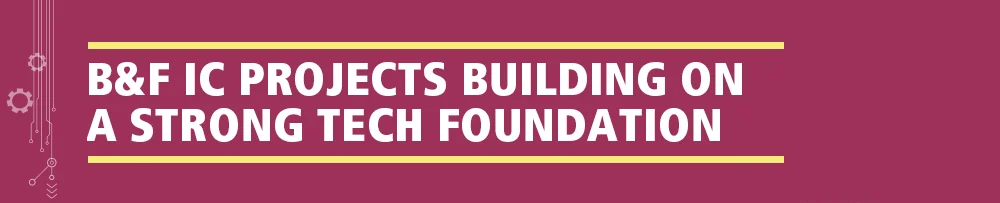
CIDCO sites on top of the tech transformation
The CIDCO Project, a massive undertaking involving the construction of over 30,000 dwelling units across 4 Navi Mumbai’s locations of Bamandongri, Kharkopar, Taloja, and Navade, has set new benchmarks in construction and leads in its deployment of tech solutions. The adept use of advanced precast technology, aluminum formwork, and a host of digital applications has won the project numerous accolades, including the prestigious PI Award, Technology Innovation of the Year 2023, and the FICCI Smart Urban Innovation Award 2023. A standout achievement was ‘Mission-96’, completing 96 flats in just 96 days!
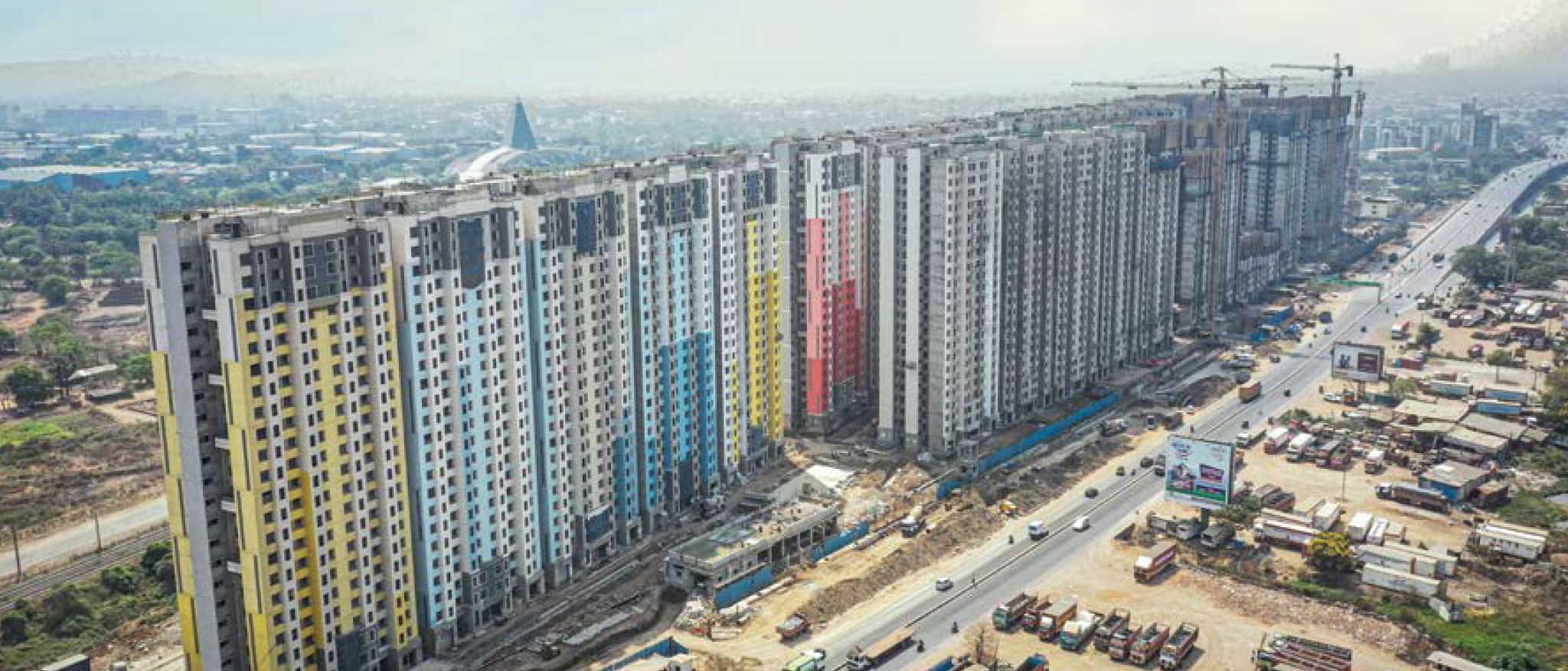
Top-driven transformation is showing the numbers
Shaik Nawaz Shareef, Project Director, CIDCO Housing Projects & TFL Head, attributes their tech success to a vibrant team of Digital Ambassadors. “To bring any change at a mass scale, the first step is awareness creation. We created an ecosystem for Digital awareness and further fueled it through certified Digital Ambassadors. As on date 100+ Digital Ambassadors have been certified at CIDCO and the idea is to have the entire project team certified,” he points out.
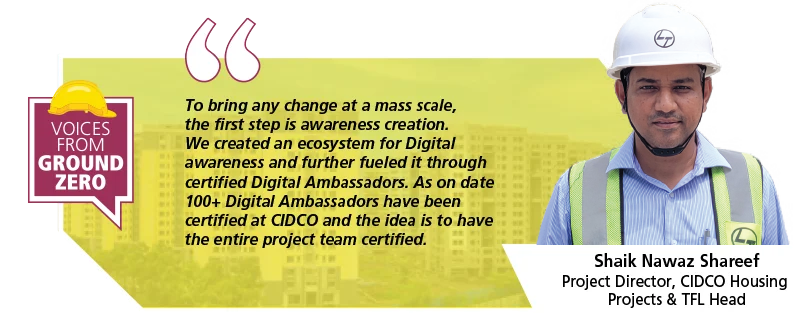
Among the team’s several innovations is the Digital Scoreboard, a compact 25 parameter metric monitoring system to track the implementation and usage levels of digital Apps, keep their varied efforts on track and sustain healthy competition among different project sites. For efficient project management, the team has developed a series of Power BI Dashboards that reveal real time insights into various aspects of the project, such as finishing, procurement allocation & invoicing, and progress monitoring. Nawaz is delighted that these have improved transparency & collaboration across teams, resulting in more streamlined operations along with continuous improvement.
“With 16 different technology solutions implemented to improve safety, quality, equipment management, and execution, the productivity gains are substantial,” exults O V Divakaran (OVD), Vice President & Head – Residential BU, and happily for him, the numbers are showing. “While concrete wastage has dropped from 1.5% to 0.2%, indent booking takes just 20 minutes instead of 20 days and workmen induction time has reduced from 15 hours to less than 3 hours at CIDCO.” Post-implementation of IB4U, inspection delays have decreased from 75% to less than 5%, and average NCR aging time has reduced from 7 days to less than 4 days.
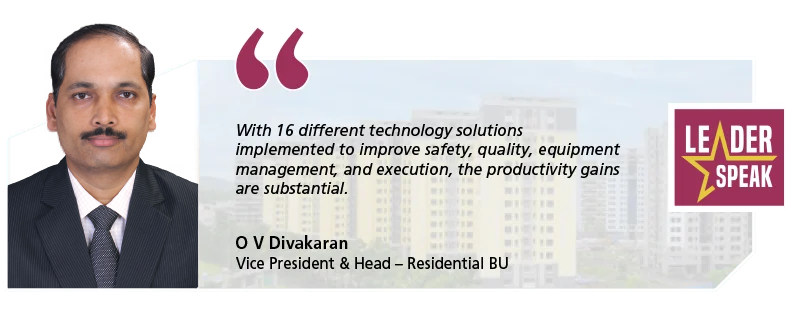
With technology implementation being top driven, the transformation has been continuous with hybrid roles assigned to the Virtual Digital Champions to ensure that they remain connected to their core domains, all the while driving digital implementation.
Impressive statistics!
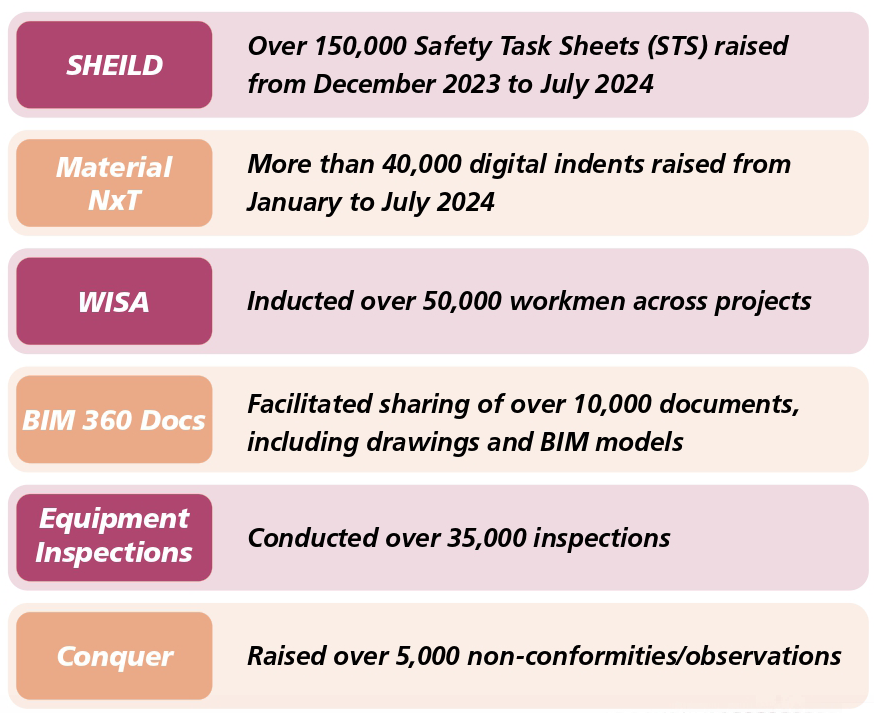
A safety third eye to keep everyone on their toes
In expansive construction sites that involves a lot of working at height, EHS is top priority for the site leadership and strengthening their arm is the Digital Scorecard at CIDCO sites, a real-time monitoring tool that tracks various EHS metrics across 12 key areas, including safety incidents, near misses, environmental compliance, and adherence to safety protocols. “Apart from promoting transparency and accountability, our Digital Scorecard makes EHS performance visible to all stakeholders, right from our workers to top management, that invokes a sense of responsibility,” elaborates Gopi Krishnan, EHS Cluster Head. “This is akin to speed cameras on roads that force motorists to drive safely,” he smiles at his analogy. “Both supervisors and workers are acutely aware that their actions are being monitored and evaluated in real time.”
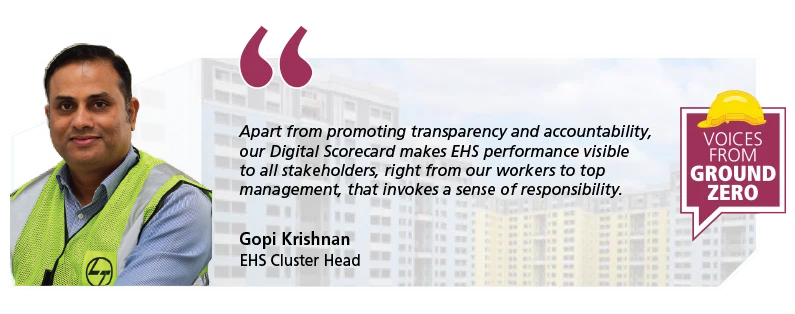
The scorecard’s data aggregation provides EHS managers with a comprehensive overview of each site’s safety performance, enabling them to identify trends, potential hazards, and areas that require immediate attention.
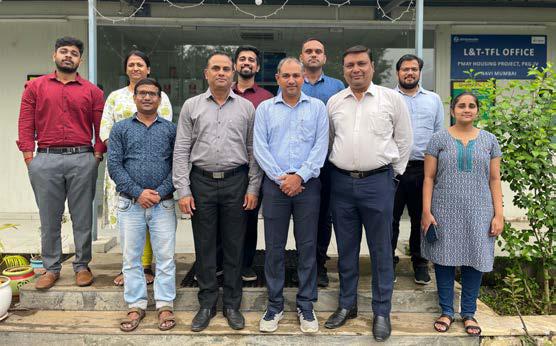
More innovations, more visibility, more savings
The Mobile Automation System or MOBA, implemented at the Kharkopar and Taloja sites to monitor fuel usage and prevent theft has already started to make its presence felt by detecting fuel theft in transit mixers and trailers, enabling the team to take corrective actions and make significant cost savings. Their site surveys have been revolutionized thanks to the Trimble SX-12 scanning technology with its 1” angular accuracy and 1.5 mm scan range noise at 200 m, enabling As-Built to Design Deviation Analysis, Floor Inspections, and Cadastral Scans. The Trimble SX-12 was piloted at CIDCO Kharkopar and is planned for full-fledged implementation at CIDCO Navade.
“The Tile Tracking Dashboard at CIDCO Taloja tracks tile utilization and wastage on a unit-by-unit basis, providing comparative data on scope quantity versus issued quantity,” shares Project Manager, Suryawanshi Sachin Shankarrao. “By analyzing utilization patterns, the team can identify areas to reduce wastage, driving efficiency and sustainability.”
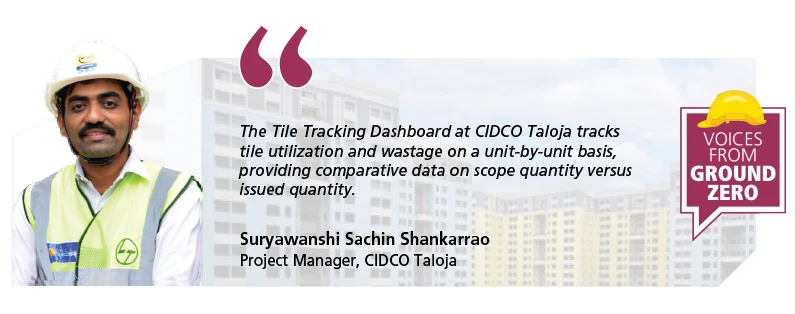
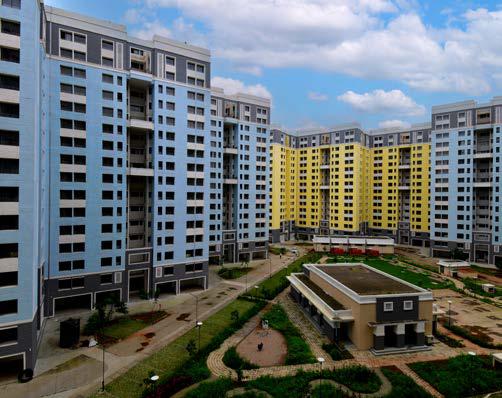
Digicast, tracking precast elements with precision
Precasting brings in speed & precision but managing the life cycle from mould preparation to final erection can be challenging. “Our specifically designed solution to this challenge is Digicast,” quips Karunanithi R, Project Manager at CIDCO Kharkopar. Its pilot implementation at the Kharkopar Precast Yard has already shown promising results, and plans are underway to fully implement it at the Navade site. “Digicast has brought in a new level of transparency to our operations,” Karunanithi explains. “We are now able to monitor each stage of the precast process in real time, ensuring that every element meets quality standards before being installed and trace each precast element back to its origin, helping us to maintain quality and address any issues immediately.”
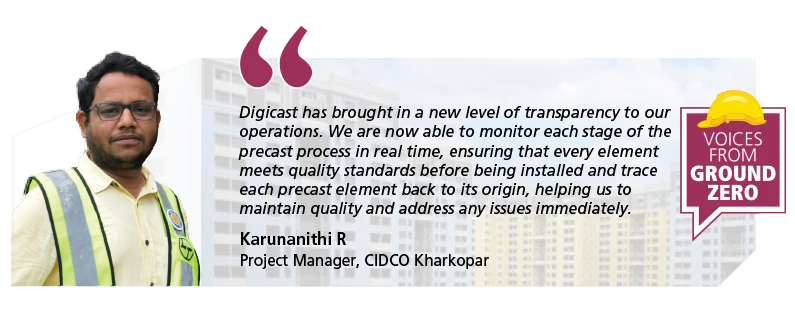
Ensuring quick, prompt responses to queries
In a dynamic environment like a construction site, addressing issues swiftly is crucial and the CIDCO team’s QR-Based Feedback System ensures that any digital application-related query or issue is swiftly resolved. It is easy to use too: users only need to scan QR codes, strategically placed across sites, to directly send their feedback to the Digital Champion of their respective site. This system has significantly reduced the time to resolve issues, ensure that digital tools are always functioning optimally and that site operations are not disrupted.
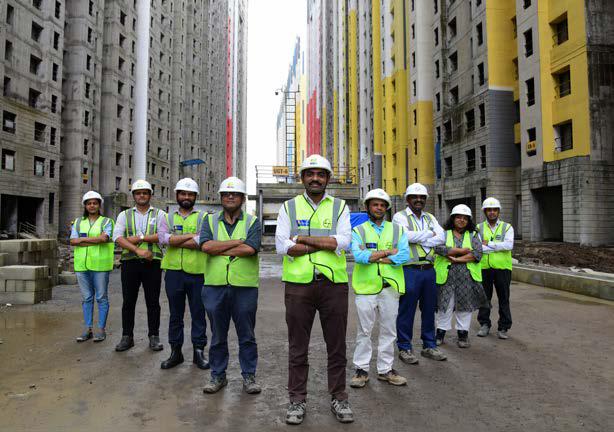
Automated mix design expiry notifications
“Quality is another one of our top priorities and with the automated mix design expiry notifications, we have taken proactive steps to maintain it,” highlights Krishna Kumar Telikicherla, Digital Officer. “Using Power Automate, the system sends mail notifications to Quality In-charges about the impending expiry of mix designs, prompting them to take necessary actions well in advance,” he adds. This automation has minimized the risk of using expired mixes thereby avoiding contractual and operational issues.

“We will be the first B&F project to implement the Quality Sanyog application,” says a proud Niraj Kumar Mishra, Project Manager at CIDCO Navade, underscoring the site’s efforts to drive Quality.
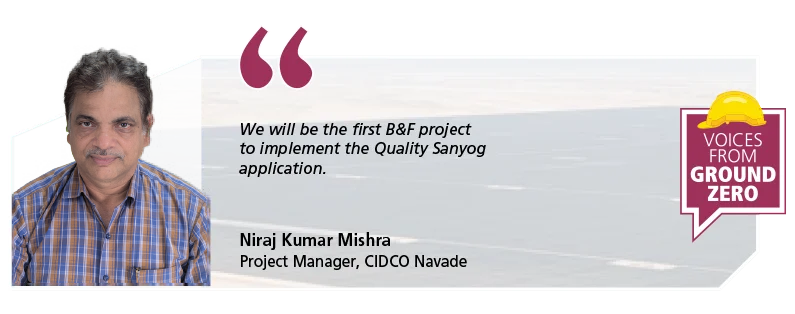
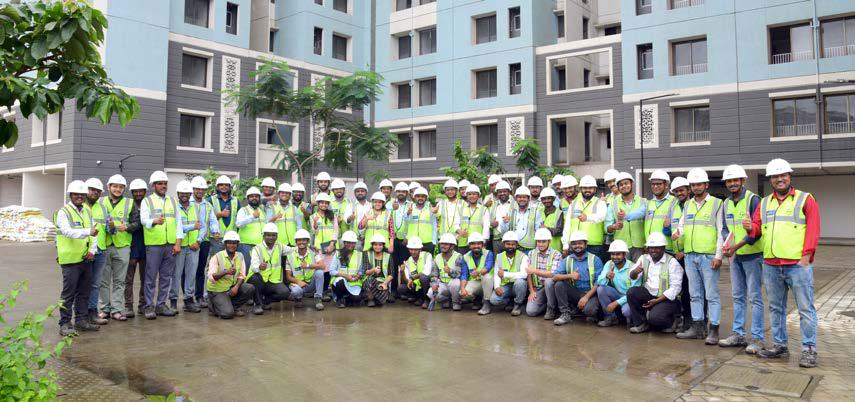
Collaboration and BIM integration
“BIM has already helped us avert potential losses by detecting clashes in pipe routing,” says an impressed Bibhas Belel, Project Manager at CIDCO Bamandongri. “MEP quantity extraction and client certification have been streamlined through BIM, and as-built drawings are readily accepted by architects, PMC, and clients. Additionally, progress meetings, delay analysis, and execution plans are all monitored via BIM, with 3D models integrated into the Primavera schedule for comprehensive project visualization,” he adds sagely.
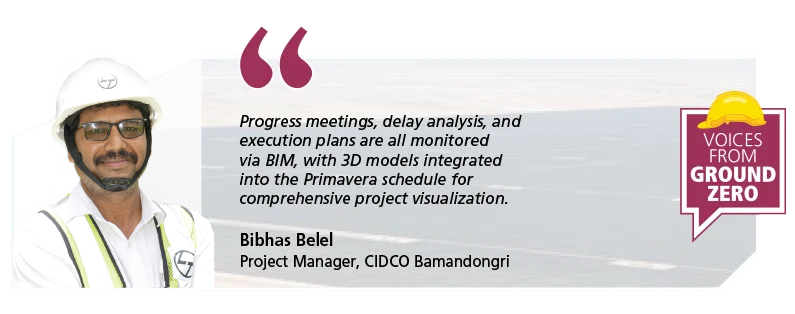
Well-deserved recognition
The digital initiatives at CIDCO have not gone unnoticed, with the project receiving numerous awards, including the British Safety Council’s Sword of Honour, NSCI Safety Award, RoSPA Award, and the CIDC Vishwakarma Award 2023. Internally, the project has been honoured with the Corporate & IC Digital & BIM Awards.
As the CIDCO projects continue to push the boundaries of digital innovation, their success serves as a blueprint for new sites like Navade, to implement the takeaways from technologies piloted at Bamandongri, Kharkopar, Taloja, and demonstrate the transformative power of technology.
Digitalization ‘central’ to everything that we do!
A major office development initiative undertaken by the Government of India, the Common Central Secretariat (CCS) Integrated Buildings project is in Central Delhi’s historic Lutyens Zone, spanning three buildings with a cumulative built-up area of 48.11 lakh square feet, including a basement of 1,23,074 square meters. The buildings, with their two basements, ground & upper ground floors, and six storeys, will soon buzz with governmental activities.
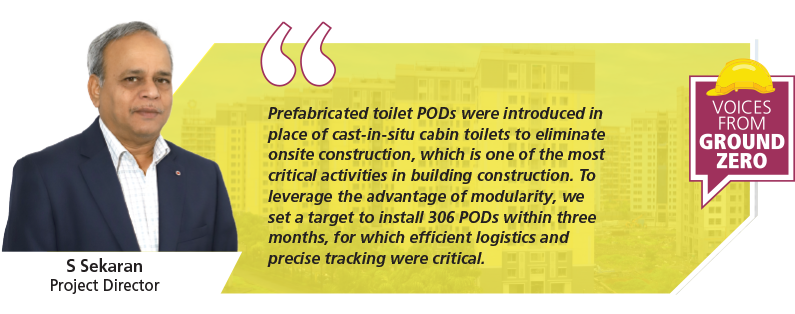
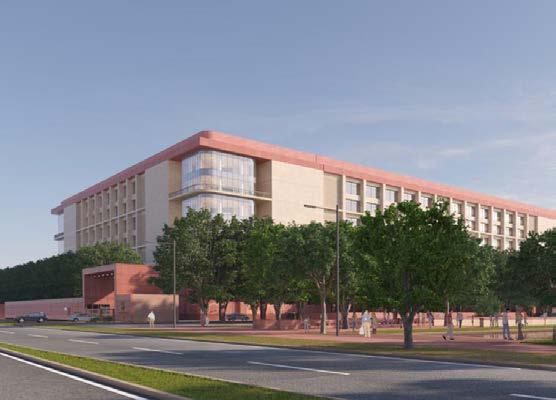
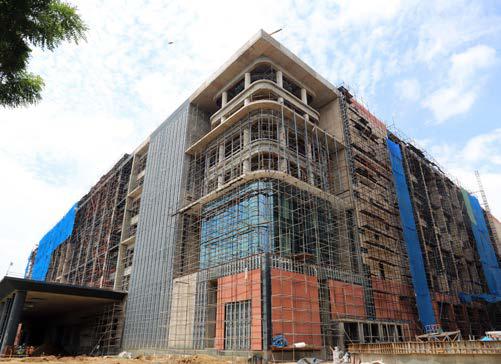
“Technology is at the core of our strategy,” states Amit Kumar Jain, Head of Project Controls, looking over his site, mentioning that the project’s extensive scope involves construction, mechanical, electrical, plumbing work, as well as operation and maintenance for five years. “Looking at our progress, digital solutions have certainly helped us to navigate the complexities and enhance efficiency,” he adds, nodding vigorously.
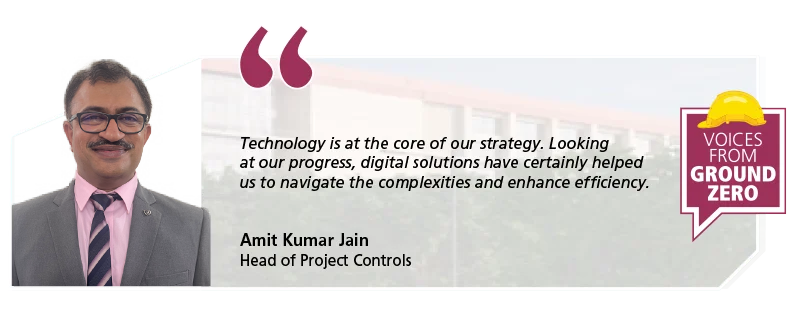
An App to track PODs
One of the team’s standout digital initiatives is implementing a mobile-compatible web application to track prefabricated Toilet PODs. “Prefabricated toilet PODs were introduced in place of cast-in-situ cabin toilets to eliminate onsite construction, which is one of the most critical activities in building construction,” points out Project Director, S Sekaran. “To leverage the advantage of modularity, we set a target to install 306 PODs within three months, for which efficient logistics and precise tracking were critical.”
A web application tracks various stages from production to dispatch, delivery, and commissioning, ensuring timely completion. It streamlines the installation process, provides real-time updates, minimizes delays and improves coordination among teams. “The result is that we completed toilet construction in just 20 days offsite and 3 days onsite work instead of the typical 60 days onsite work,” says Sekaran, with a quick smile.
Laser scanning for accurate execution
Laser scanning technology is proving to be an able ally for the team to achieve accurate finishing, facade and services activities. “With Trimble, we can detect deviations as low as 1mm in structure works between the design and executed work,” shares Tarit Jain, Digital Officer, with energy. “It enables us to take corrective actions to deliver the final product as per design intents. Of course, laser scanning has significantly reduced errors and rework, and significantly improved our finishing, façade and services works.”
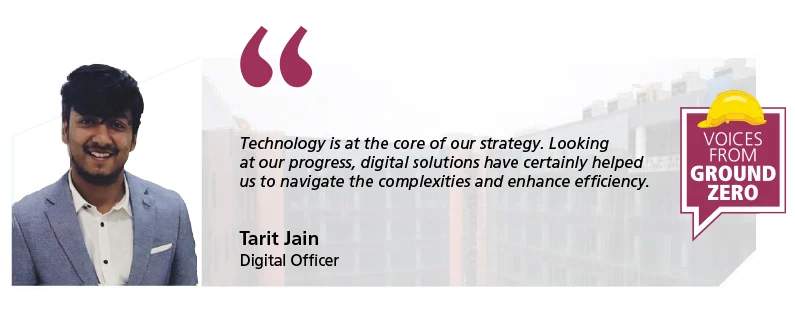
RFID-based fuel management system beating down costs & theft
Fuel theft from P&M assets is a common source of concern for large-scale construction projects and CCS is no exception. The answer is an RFID-based fuel management system. RFID sensors installed in the P&M assets track fuel levels and detect sudden drops, triggering automatic alerts to the respective teams. The system reduces fuel theft and ensures optimal fuel usage. The benefits are already showing in terms of cost savings by reducing average fuel consumption to 2.5 LPH from 3.5 LPH. With improved operational efficiency, Sekaran has one more reason to smile.

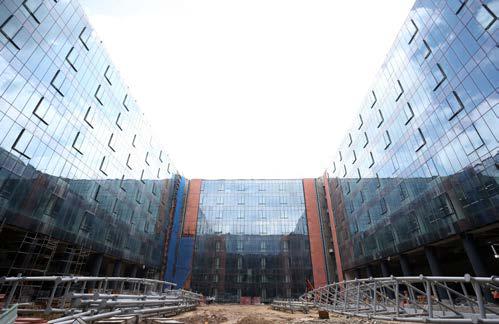
Expertly managing logistics
At the project’s peak activity, 300+ heavy vehicles were moving daily to and from the site making logistics planning a nightmare for the team, also because of the site’s location in the Lutyens Zone. “Working within high-security zones, with stringent access controls and restricted logistical space, demands inventive and adept logistics solutions,” observes Planning Head, Abhishek Jain. A dashboard, developed using the existing weighbridge, tracked the in-time and out-time of vehicles resulting in timely loading and unloading, preventing bottlenecks and ensuring smooth logistics operations. “We reduced the total turnaround time from an average of 6-8 hours to just 3 hours which is a significant time saving,” Abhishek says triumphantly.
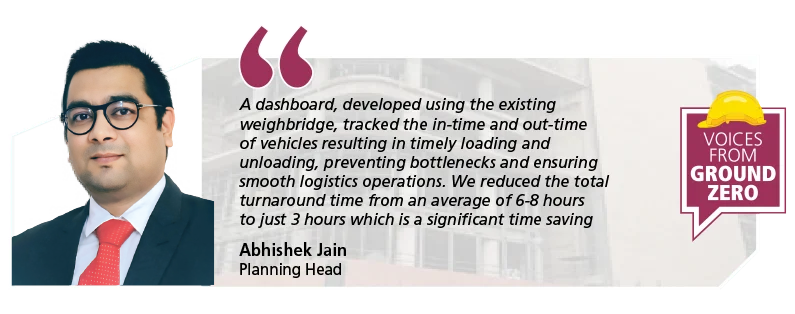
As the project progresses, it stands as a model for future government infrastructure projects, showcasing the potential of digital innovation in driving large-scale development.
We ‘HAD’ a vision!
B&F IC’s Himank Air Dispatch Unit (HAD) project in Chandigarh, commissioned by the Indian Army’s Border Roads Organisation (BRO) is a mixed-use development spanning a built-up area of 1 lakh sq feet in a G+2 configuration, featuring six building blocks, of which five have been constructed using advanced 3D Concrete Printing Technology, and the other has been precast. The HAD project redefines construction methodologies, and at the same time, integrates digital technologies.
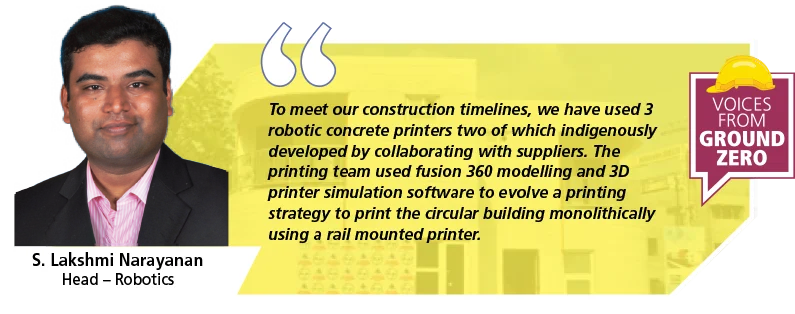
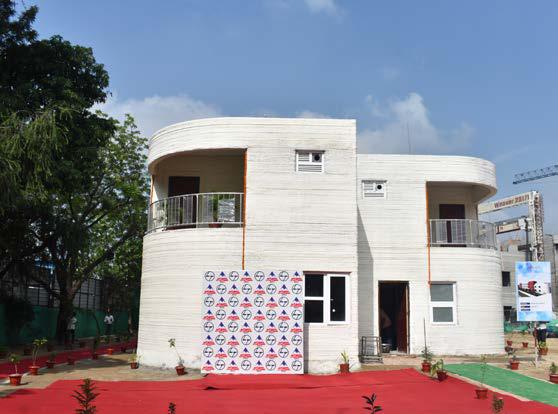
Revolutionizing construction with digital technologies
Robotic 3D concrete printers
At the heart of the HAD project is the use of robotic 3D concrete printing technology, a cutting-edge method that constructs building walls layer by layer, eliminating the need for supporting formwork systems. Robotic printers automate the wall construction process, significantly reducing the need for manual labour and supervision. “The architectural form has been crafted by leveraging the dynamism of 3D Printing technology which provides designers with unprecedented freedom to create innovative and non-geometrical building shapes that would otherwise have been challenging using conventional construction methods,” shares Rajkumar Murali, Chief Architect. The iconic administrative block with its eccentric circular design reflecting Chandigarh’s urban fabric and the BRO’s logo colours brings to life Rajkumar’s statements.
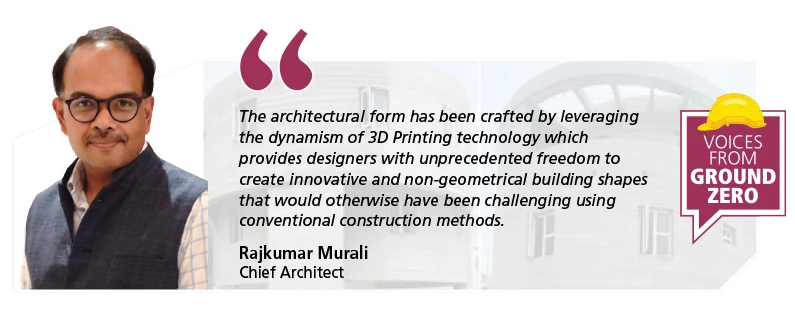
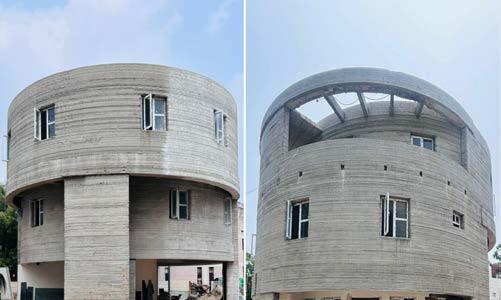
“To meet our construction timelines, we have used 3 robotic concrete printers two of which indigenously developed by collaborating with suppliers,” informs S. Lakshmi Narayanan (SLN), Head Robotics. “The admin block, an 18 m dia, excentric circular building with cantilever slabs, was challenging in terms of structural design and execution. The printing team used fusion 360 modelling and 3D printer simulation software to evolve a printing strategy to print the circular building monolithically using a rail mounted printer.” His expression reflects his sense of triumph.
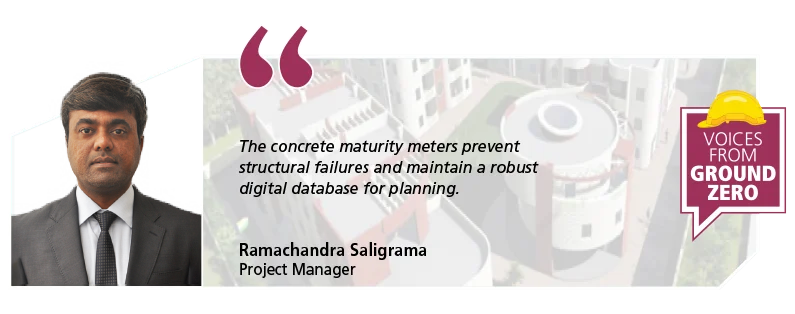
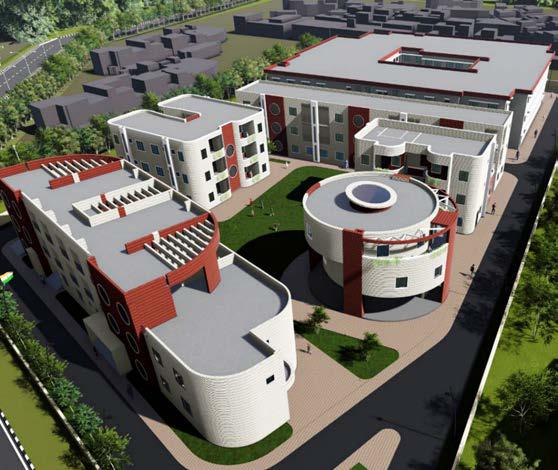
Seamless digital information flow
The seamless digital transition from concept to construction is another highlight of the HAD project with the design team developing drawings in 3D AutoCAD format, that were converted into machine g-codes using a printer slicing software. “This digital construction methodology has eliminated manual intervention and rework,” explains SLN, “for once the g-codes are fed into the printer and initial reference coordinates set via a total station, the printer autonomously manages the construction, accurately and efficiently.”
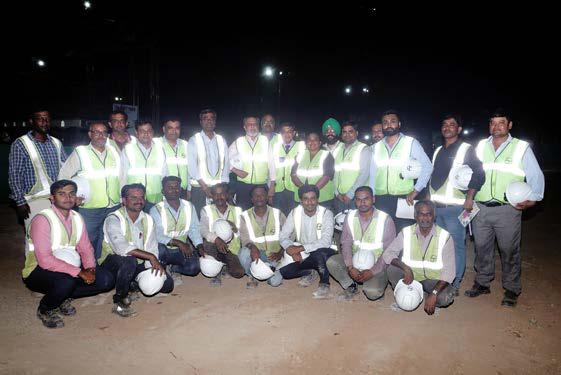
Ensuring structural integrity with concrete maturity meters
Since the concrete is 3D printed in layers without reinforcements, it is imperative to monitor the strength of the concrete for which the HAD team employed concrete maturity meters, to measure real-time concrete strength through embedded sensors. This data is used to adjust the printing speed, ensuring that each layer has sufficient compressive strength before the next layer is added. “This technology prevents structural failures and maintains a robust digital database for planning,” remarks Ramachandra Saligrama, Project Manager.
Integration of concrete chain equipment
The seamless integration of concrete production, pumping, and printing is another hallmark of the HAD project. An on-site batching plant ensures continuous supply of 3D printable concrete, which is pumped directly into the printers, that is managed digitally, with concrete level sensors ensuring efficient and uninterrupted construction. The integrated system minimizes the requirement for labor and enhances operational efficiency.
The successful integration of digital workflows and robotic systems has streamlined the construction process, opened new avenues for architectural creativity, and set a new standard for structural efficiency.
“The success of the HAD project underscores the transformative potential of 3D concrete printing technology for large-scale construction,” smiles SLN, with a punched fist.