
Redefining speed & scale
A 6-decade-old phenomenon, high-speed rail operations were first rolled out in Japan in 1964, and soon gathering speed, ran across several European countries like Italy, France, Germany & Spain, though presently China leads accounting for almost 70% of the world’s high-speed network with 40,000+ km of high-speed railway lines. India is getting ready to jump on to the bandwagon with the Mumbai–Ahmedabad High-Speed Rail Project (MAHSR), a dream project of the Honourable Prime Minister, envisioned to be a 508-km long corridor running through the states of Gujarat, Maharashtra and the Union Territories of Dadar & Nagar Haveli. The first package for the project, C4, the country’s largest EPC contract ever, to construct a 237-km stretch, was awarded to L&T in November 2020 through a competitive bidding process.
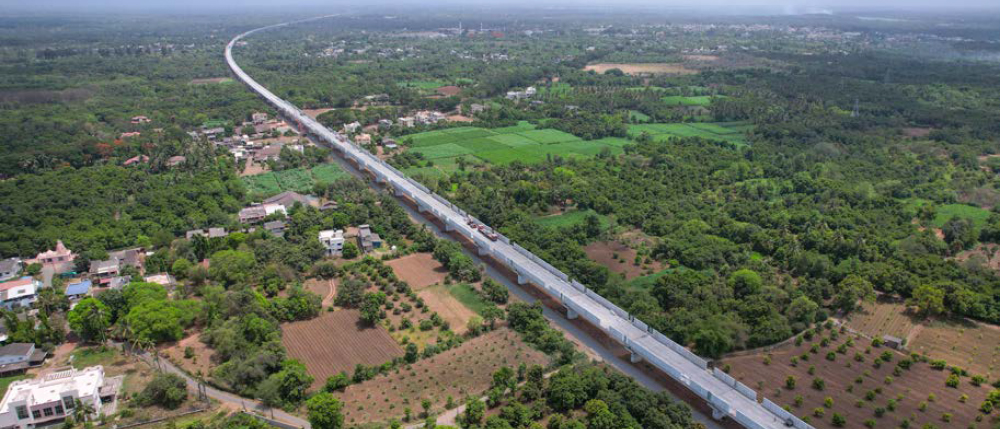
“Apart from the impact of the pandemic, one of our primary considerations initially was how to maintain the intended speed of construction, hitherto not achieved in the Indian construction industry to construct 237 km of elevated viaduct in just
42 months,” recalls the phlegmatic Executive Vice President & Task Force Leader – MAHSR C4, G. Vinod, characteristically rubbing his bald pate. Just as a point of reference: 350 km of the Delhi Metro has been constructed over a period of
25 years, though in phases. “Full-span construction methods that are 8–10 times faster than conventional segmental construction gave us a head start, and thereafter by adopting Japanese technology, efficiently & digitally managing humongous volumes of men, material & equipment, and with various other technology interventions, we are keeping our project on track,” he smiles tightly.
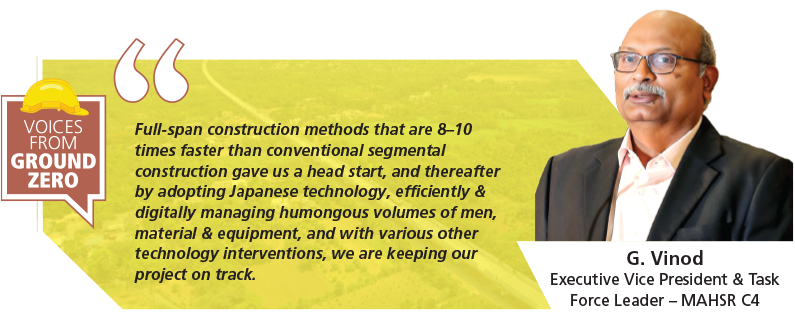
“At the C4 package, we are progressing at ~9 km a month, pouring more than 2 lakh cum of concrete and producing more than 4.5 lakh MT of aggregates in-house,” informs Navneet Kaul (Head-Technical Services, MAHSR C4), matter-of-factly and the general understanding among the project leadership is that C4 is not just about managing a complex gigaproject but a saga of transforming blueprint into reality, redefining the concepts of speed & scale.
With a broad framework in place, the project team hit the ground running planning, gathering geological, geotechnical, & survey data and mobilizing.
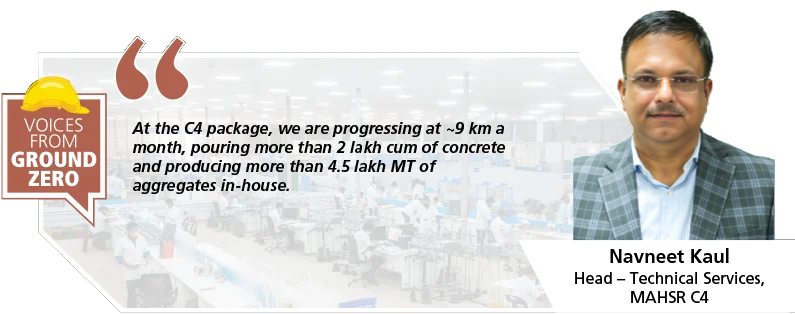
LiDAR reduces survey time from 60 to just 15 days
Approximately 118.55 sq. km was topographically surveyed in just 15 days (10 for actual survey and 5 for data processing) using Aerial LiDAR (Light Detection and Ranging) technology, with lasers mounted on a fixed wing aircraft. “This survey would have taken at least 60 days with conventional methods,” points out Rakesh Kumar Jha (Project Director, Section-01). “This Geospatial technology has several benefits: pinpoint accuracy, fast acquisition, minimum human dependence, weather independence, high data density, widespread accessibility and cost efficiency.” A 500-m corridor, 250 m on either side of alignment was surveyed in clear, cloud free weather conditions, free of fog, smog, haze, or cloud shadows.
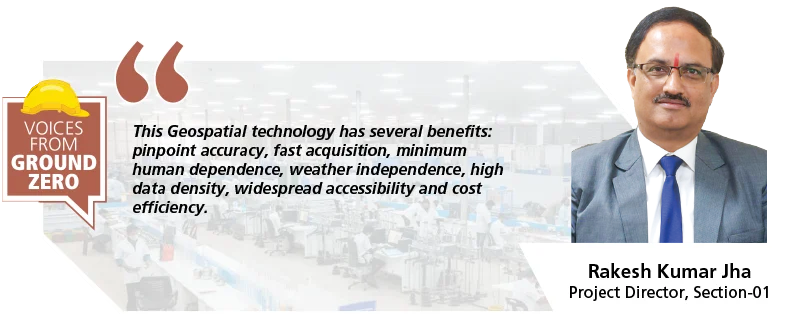
In LiDAR a laser throws a light pulse, and a sensor detects the return of the pulse, to calculate the ‘Time of flight’ as the speed of light is constant to the distance of the point. It is supported by precise GPS and INS (Inertial Navigation System). The point cloud data was captured at intervals of 0.5 m to derive the contours and topographic features, apart from deriving DEM (Digital Elevation model) and DSM (Digital Surface Model) for a better understanding of the 237 km stretch. Adopted for the first time for a railway project in India, it is environment friendly too.
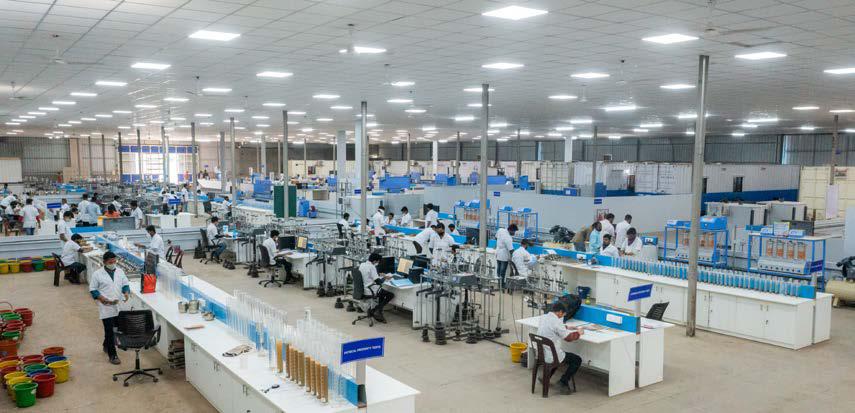
Investigations at Asia’s largest onsite GeoTech lab
Being a greenfield project of almost unimaginable scale, understanding the terrain was the first task for the team who were mandated to investigate 2,454 borehole locations at every 100 m intervals of average depths of 40 m & 70–80 m on riverbeds, all along 237 km, the largest ever on-field geotechnical investigation to be undertaken in India. It translated into some 100,000 soil/rock samples to be tested in 12 months.
As per the Employer requirements, the field investigation had to conducted by deploying standard mechanized drilling rigs with semi-automatic/automatic trip hammers, capable of extracting undisturbed samples at great depths to be used for drilling and Energy ratio of the machine used for Standard Penetration Tests (SPT) shall be more than or equal to 67%. Such machines were unavailable in India and importing them, hugely time-consuming. Further, to ensure accuracy and reliability, all testing had to be conducted at Government Approved/ Accreditation Board for Calibration and Testing of Laboratories (NABL) accredited labs and although there were some 20+ in the vicinity, only a few possessed the necessary resources and none could meet the extensive testing demands.
The team’s strategic response was to set up a central geotechnical testing facility, bringing in-house all the testing and evaluation activities. “We streamlined the testing process, to ensure quality and adhere to project schedules,” smiles
K Ganesh Iyer (Chief Consultant, L&T IEL). Established over an area of 58,000 sq. ft in the outskirts of Surat, the GeoTech lab is equipped with state-of-the-art automatic and digital testing equipment with accuracies meeting all the codal provisions. To conduct 484,624 soil index property tests and 13,576 engineering property tests within 18 months, 190 specially trained technicians test 400 samples a day for index properties, 25 samples a day for engineering properties amounting to some 3,500 tests per day while 20 qualified geotechnical engineers evaluate, interpret & report data to ensure correctness, accuracy & reliability. Completing about 94,000 running meters of GTI work within 12 months is a record-breaking volume for any single project in India.
Managing loads of logistics
The C4 Package calls for detailed logistic planning to manage some 70 lakhs cum concrete, 1.45 crore MT of aggregate production and 8 lacs MT of reinforcement. To implement full-span construction, it was imperative to have the casting yards adjoining or in proximity to the project alignment. “It was double RoW,” chuckles VV Ramana Murty (Project Director, Section-03), “first the client had to procure RoW for the alignment and then we had to for the casting yards and access routes along the entire 237 km alignment.”
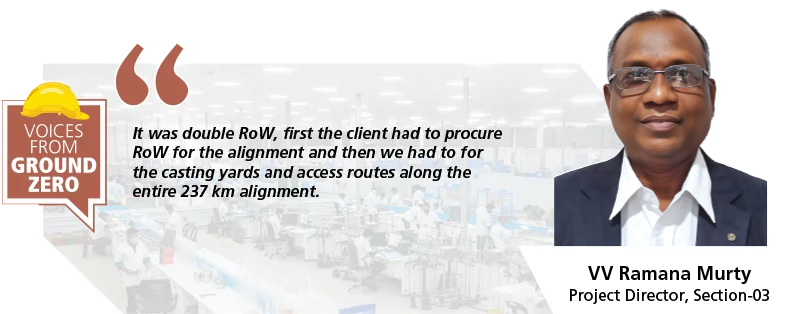
Identifying lands at desired locations, bringing multiple owners on one platform, convincing unwilling parties to lease out their lands and finally formalising the lease rental agreements was no mean task. “It was a humongous task to finalise lease agreements for 1000 acres of land (as much as entire ROW area) spread over 20 locations for setting up the casting yards,” exclaims D. Vijayakumar (Head – FAA, MAHSR C4).
With ~40% of the concrete volume being for superstructure precasting, 33 (at 2,520 cum./hr) batching plants are strategically located for the least possible lead for the major quantum of concrete. 14 crushers produce aggregates (achieving a peak of 6 lacs MT in one month), located close to quarry locations to minimise lead to the crushers. With limitations on the temporary permits for quarrying operations, the existing quarry owners / lease holders had to be convinced to supply boulders to the crusher plants. The locations were carefully chosen considering environmental impact and regulatory compliance to avoid legal issues.
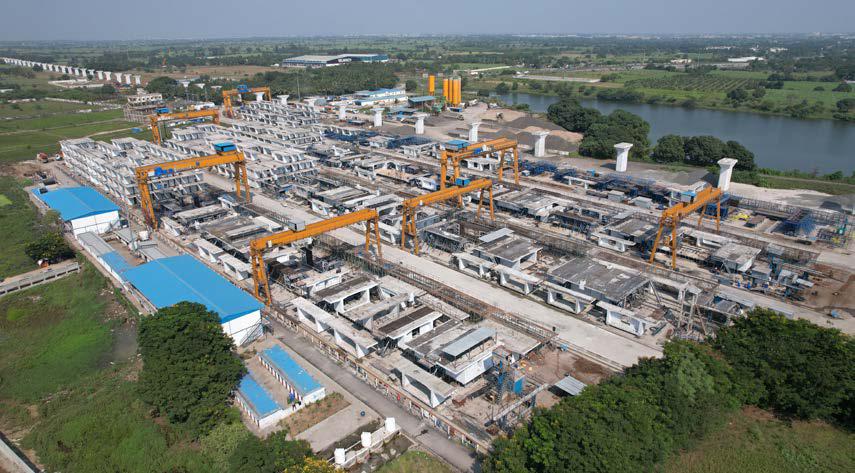
Ensuring flow of aggregates from the local suppliers was a major risk to achieve planned progress for the team that was mitigated by setting up their own crushers while in-house production maintained high quality standards at lower unit rates. 20,000 MT of aggregates are transported every day to various casting yard locations, their quality maintained by controlling the production process. 6 Reinforcement C&B plants (with a total capacity of 20,000 MT/month) located at various casting yards across the project ensure timely reinforcement requirement.
“We could adjust production rates based on project needs, ensuring that materials were available exactly when required and our ability to produce high-quality materials in-house gave us a strategic advantage in terms of cost, quality, and reliability,” expresses Laxmee Narayana (Head – Quarry & Crusher, MAHSR C4).
FSLM helps to keep up to the crushing construction schedule
The Full Span Launching Method (FLSM) has brought about a paradigm shift to the speed of construction of bridges and viaducts, along with additional benefits including less labour, better quality and increased competitiveness of prestressed concrete bridges over embankments. “FSLM involves a full-span box girder of 30–40 m, cast in the casting yard, transported to site and lifted onto the piers,” explains Zamshed Ali (Project Director, Section-02), “with the help of imposing Straddle Carriers, Girder Transporters, Bridge Gantries & Launching Girders.”
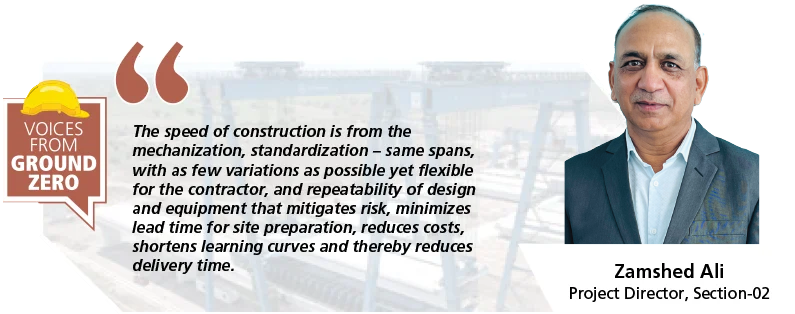
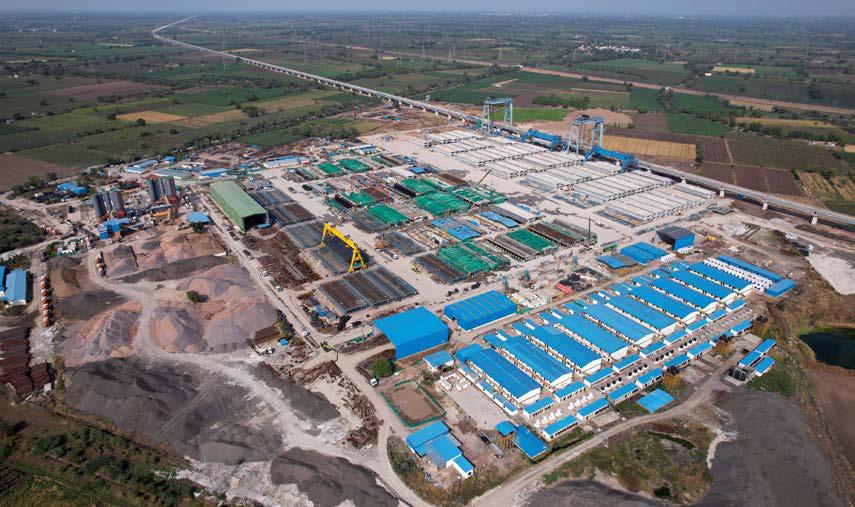
“The speed of construction is from the mechanization, standardization – same spans, with as few variations as possible yet flexible for the contractor, and repeatability of design,” he elaborates, “and equipment that mitigates risk, minimizes lead time for site preparation, reduces costs, shortens learning curves and thereby reduces delivery time.” Since casting is in factory-like conditions, quality is maintained, and erection continues all year-round in almost any weather conditions.
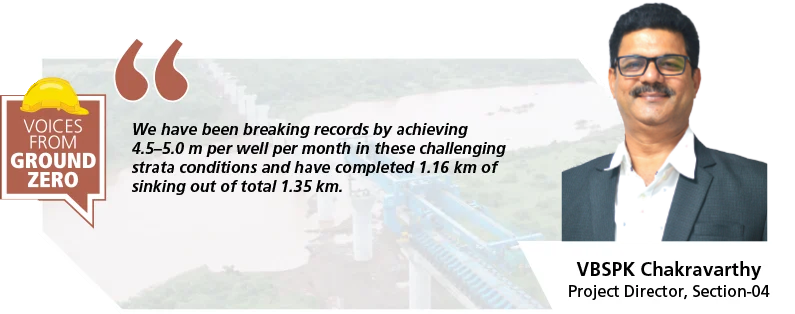
While the casting moulds produce 5–6 spans a month from each set, each casting yard is equipped with facilities like jigs for making rebar cages, casting beds with hydraulically operated prefabricated moulds, batching plants, aggregate stacking areas, cement silos, and labour camps to meet the tall requirement of superstructure casting & erection. “Presently, 9 sets of FSLM equipment have been deployed at C4 with which we manage to achieve the asking rate of ~9 Km. superstructure erection/month,” shares Sudhir Kumar Srivastava (Head-Erection, MAHSR C4).
Bridging rivers at high speed
Previously, each river bridge was treated as a separate project, often taking years to complete due to the complexities and challenges involved but with FSLM, the task has become elatively easier for the C4 team. “Out of 11 river bridges supported by pile/open foundations, the superstructure for 6 of them have been completed and the sub-structure completed for another 4,” updates VBSPK Chakravarthy (Project Director, Section-04). The technology minimizes the need for extensive scaffolding and support structures in the river, reducing environmental impact and disruption to the river flow.
The C4 alignment traverses the Tapi River supported by 13 wells and the Narmada River, supported by 22 well foundations that have been designed to depths ranging from 50 to 80 m stretching across 0.72 km and 1.26 km, respectively. “The construction challenge lies in penetrating a series of ‘sandwich layers’ of stiff to medium clay and sandy strata,” explains Sunil Kalliath (Head – Engineering and Construction Methods, MAHSR C4), “and these are arguably some of the deepest constructed well foundations in recent history of bridge construction in India, demanding exceptional engineering solutions.” To ensure precise and vertical well placement, the team has adopted four approaches: the two conventional approaches of self-sinking well foundation and the Kentledge method. Two others adopted are the Jack Down method using gripper rods and the innovative Jack Down method using the Macalloy Bar Method.
Bridging the Narmada has been the toughest as the team must remain ever alert to its erratic nature and sudden tidal shifts & currents, especially during the rainy season. There are several other technical challenges too to maintain the stability and verticality of the wells, largely due to unstable soil conditions. “We have been breaking records by achieving 4.5–5.0 m per well per month in these challenging strata conditions and have completed 1.16 km of sinking out of total 1.35 km,” rounds off an upbeat VBSPK.
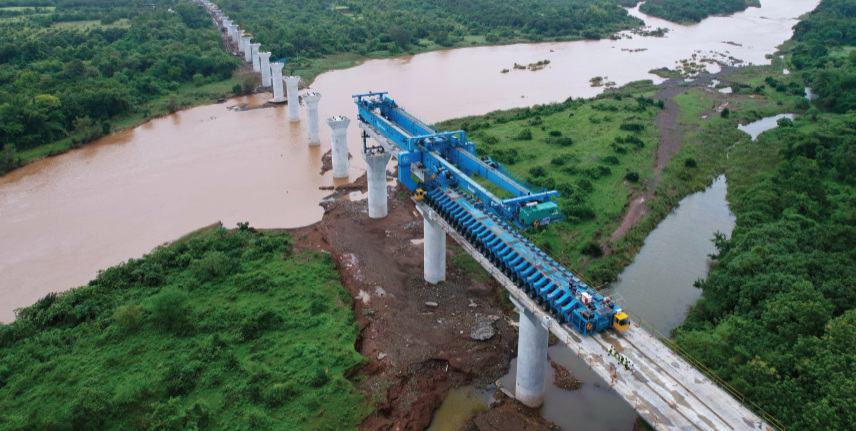
Fuelling profit by managing fuel
Having to manage a distributed fleet of 2,200+ assets over 237 km is not only arduous but expensive too reflected in the monthly consumption of approximately 25 lakh litres of high-speed diesel, following the conventional method of using a large fleet of bowsers with hired vendors dispensing fuel to the various assets, over which the team had little control.
The bowser operator used to maintain a manual register, relying entirely on manual entries and paper documents. “We had no clue as to how much fuel was being consumed and only an approximation of its value,” says Biren Modi (Head-Administration, MAHSR C4), seeking a process without human intervention that provided real time, accurate & actionable data.
The answer lay in a cost-effective, robust, user-friendly system with minimal architectural complexity that gathered data from a variety of sources like Liquid Level Sensors, RFIDs, magneto restrictive level probes & automatic fuel dispensers to calculate fuel usage. “For the first time in L&T, we had a comprehensive fuel monitoring system covering the entire fuel value chain from procurement from vendors to distribution to consumption,” points out D. Chandra Sekhar (Head – Plant & Machinery, MAHSR C4), who is more than pleased with the results:
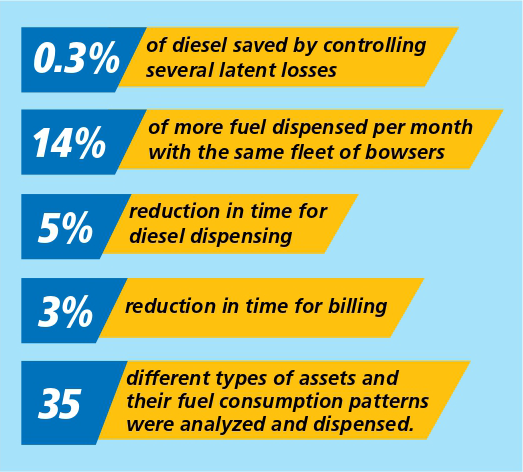
Developing precast Noise Barriers & a Cable Duct production hub
The 237 km viaduct must be fitted with precast noise barriers & cable ducts as deck furnishing that requires a huge quantity of precast elements to be produced and delivered within 24 months. “The challenges for production of the precast elements were 3D eccentric C shapes for the noise barrier, huge number of elements and a short timeframe to supply 20 lakh elements in 2 years,” informs Yogesh Sudheer Pande (Head – Construction Services, MAHSR C4). Both the barrier & duct have several design & manufacturing complexities.
Since no vendor had thus far developed automated moulds for such a 3-dimensional complex shape element and to meet the steep asking rate of production, the team developed an automated and robust manufacturing hub in-house, for the first time in India, with minimal human interface and designed to achieve 1.5 cycles per day. The 150 m x 75 m hub is equipped with an automated concrete supply system, overhead cranes, two batching plants (30cum./hr and 60 cum./ hr capacity), a chiller plant, boiler house, GAS bank, stacking yard, and an adequate drainage system. “We can now cast complex
3-dimensional shaped noise barriers with each machine designed to cast 12 elements at a time, while the automated mould shapes the complex cable duct,” says a joyous Soman Narayanan (Head – Precast, MAHSR C4). “We also have a steam curing system, element transport runoff trucks to shift finished elements to stacking yard with the help of overhead cranes and vacuum lifters.”
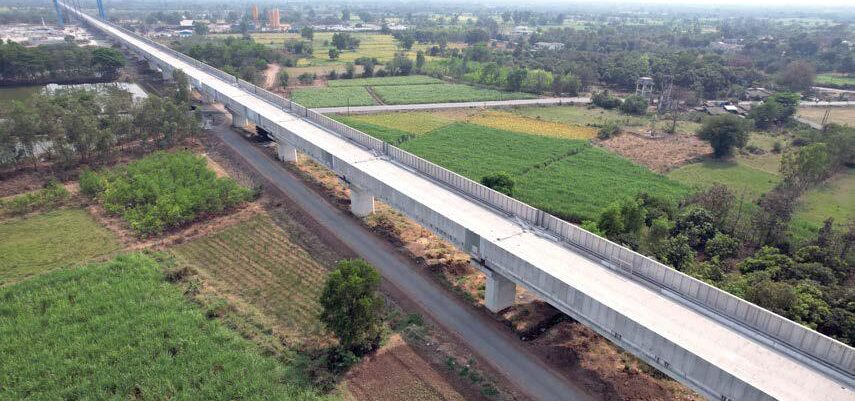
Their efforts have certainly borne fruit:
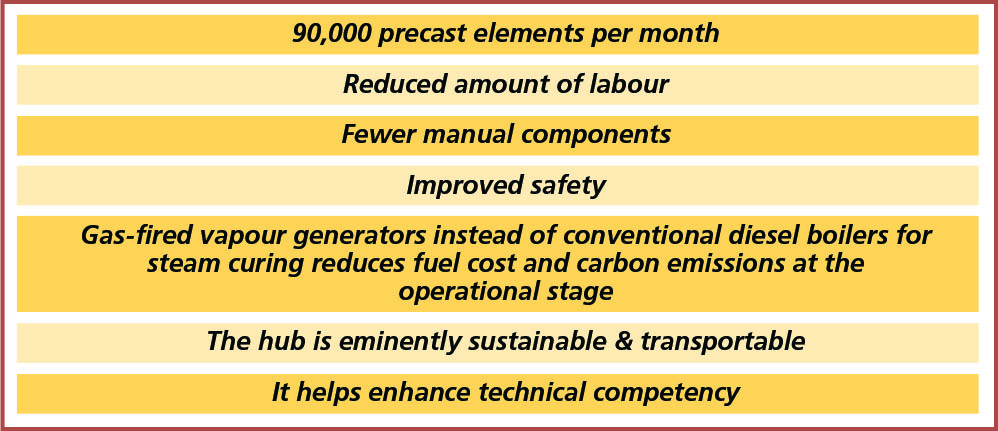
Make in India initiative: Adopting technology
Considering the magnitude and relevance of this nation-building effort, it is an ideal platform to showcase ‘Make in India’ that has found expression in building FSLM equipment in-house at L&T’s M&M SBG, Kolkata & Kancheepuram, and LTCEL, Bangalore, after importing the first 3 sets from China. Six sets of FSLM equipment weighing more than 11,000 MT have been indigenously designed and manufactured at the Kanchipuram Works, in partnership with 55 Micro-Small Medium Enterprises (MSMEs), joining a select group of countries like Italy, Norway, Korea, and China.
Recognizing the potential to manufacture locally, L&T supported Winsteel, a long-standing fabrication associate from Surat, to develop the capability to fabricate these moulds domestically that involved technology transfer, capacity building, and for the project, cost effectiveness and value creation. “This collaboration created numerous job opportunities, both directly in manufacturing and indirectly through the supply chain, contributing to skill development too,” notes S. Ramesh (Head – QA/QC, MAHSR C4).
The adoption of Japanese technology to develop seismic stoppers, critical components installed between the girder and the pier cap of a bridge to maintain stability under seismic forces, has both reduced the dependency on foreign suppliers and enhanced local manufacturing capabilities. The requirement for C4 & C6 Packages is 35,714 seismic stoppers, with a peak requirement 2,000 stoppers per month. “With only two Japanese vendors possessing the production know-how and local suppliers lacking the experience and capability to produce seismic stoppers to Japanese standards, we were in a spot,” recalls Navneet. In response, the team first identified LTPC at Hazira having facilities capable of high-quality fabrication and Hevea Rubber Technologies Pvt Ltd to manufacture the rubber sleeves. “We overcame the issue of foreign dependency and, at the same time, established L&T as a prime manufacturer of seismic stoppers, achieving substantial cost reductions and securing additional project packages,” smiles a satisfied C. Sivakumar (Project Director, Section-05).
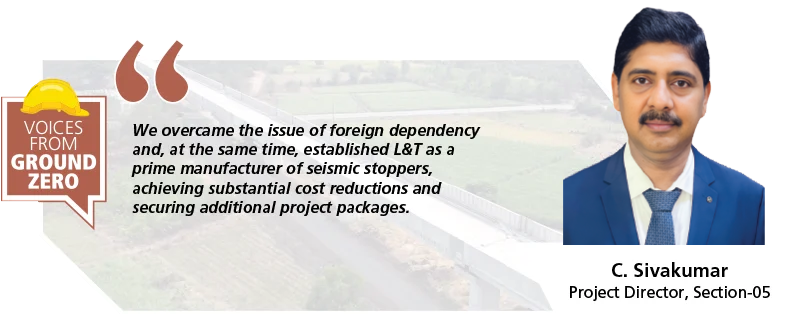
Going digiTALL
Managing Men: On the EHS front, the SHIELD App updates prestart forms, near misses, permits, unsafe acts & conditions, EHS observations & checklists. The team’s 3-stage escalation matrix ensures accountability. Through WMS, till date nearly 150,000 workers have been inducted and about 18,000 VR training sessions have thus far been conducted under different modules. The project has benefited enormously from the transfer of technology & skills, with Japanese experts training engineers & workers to improve skills. “The economic impactis profound too, with 15,000+ workers busy at site with the potential to create nearly 100,000 new jobs going forward”, expresses Ashish Chandra (Head – EHS, MAHSR C4).
With 2,000+ staff at C4, Badshah Juned (Head – Human Resources, MAHSR C4) clarifies that “Proper staff management ensures that every team member understands his or her role, responsibilities, and the project’s goals, which are essential to maintain high standards of safety, quality, and efficiency. The success of a mega project hinges on the ability to manage human resources effectively,” he adds wisely.
Managing Material: With the ConEase App, the team handles a scope of ~70 lakh cum of concrete, 20 times the volume used to construct the Burj Khalifa while Rebar Pro is a user-friendly App to manage the 8 lakh MT of rebar. The Material NXT App smoothens indent creation & issue while IOT & LLS installed in the assets monitor utilization & fuel consumption, all available on the Asset Insight portal.
Managing Machines: The production data of each of the 31 batching plants is extracted from the SCADA system and made available on the Asset Insight portal. The Weighbridge management application is a standalone application, connected to the cloud, that stores every transaction and weighment data, with the facility to update the PO/WO, helping the billing team. “For the first time in the construction industry, we have developed an advanced analytics-based recommender system to decide on hiring, de hiring and redeploying assets based on past utilisation patterns and seasonality,” mentions S Mohanbabu (Digital Officer, MAHSR C4). The IB4U tool monitors inspections & maintenance of assets.
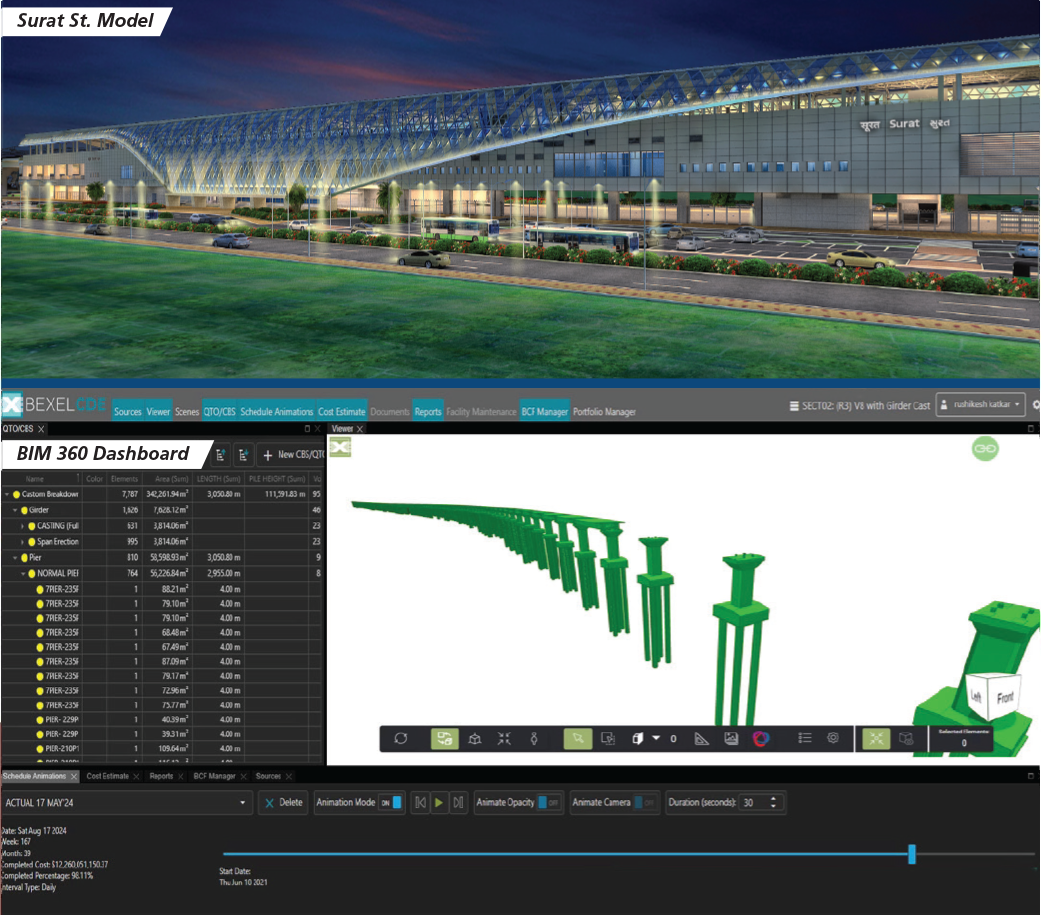
Managing Methods: Procube helps the team to manage an average of 10,000 cum. of concrete a day. Through BIM, a comprehensive 3D model of the entire stretch & 4 station buildings has been created using Revit/Dynamo that can be reviewed through VR & the BIM 360 platform. “We have integrated 3D model with P6 schedule using the Bexel Manager BIM Integration platform for project tracking and quantification,” elaborates Sumendu Dutta (Head – Projects Control, MAHSR C4). “Monthly progress reviews have been automated and integrated with Power-BI, facilitating seamless data transfer from the BIM model to the Power-BI dashboard.” 5D BIM implementation for real-time cost flow monitoring is an ongoing initiative.
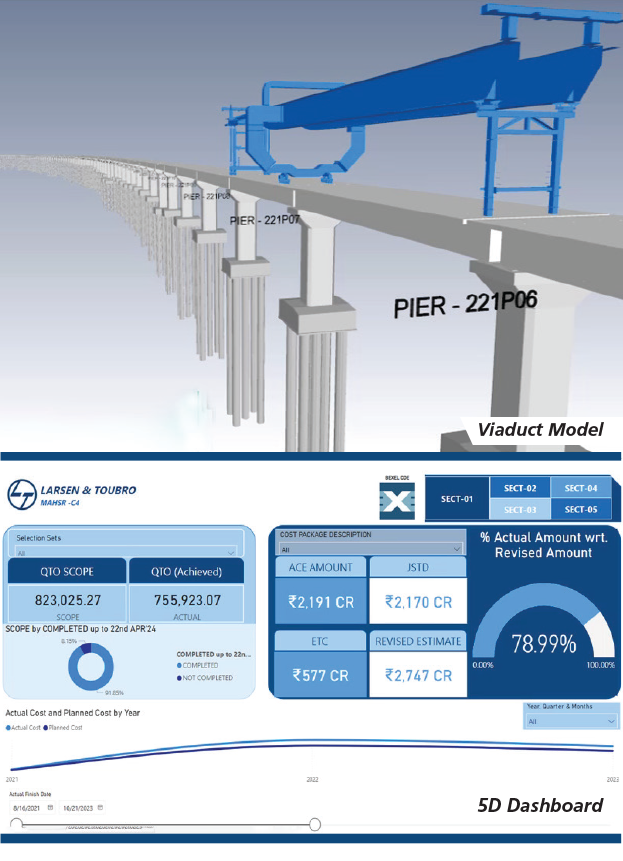
TSRM Srinivas (Head – Coordination) delves into the criticality of project management for such a project of this size. “It is not just intricate planning, but also about translating plans into actionable tasks, orchestrating complexity, mitigating risk, aligning stakeholders, adapting strategies, maintaining quality and safety, meeting deadlines and keeping the wheels turning.”
Connectivity was a major issue across the 237 km stretch and when efforts to establish a network through multiple service providers failed due to high costs and prolonged set up times, the team decided to establish their own network. “We have successfully implemented a centralized real-time monitoring system, an intercom facility with over 500 connections across all our establishments and internet routing through this network to ensure continuity in case of failure at any establishment,” voices Ranjan Kumar Sahoo (Head – ISD, MAHSR C4), happy that the solution is cost-effective and eliminates their dependency on
external providers.
15 Quality laboratories generate nearly 350 quality test reports per day per lab at different frequencies for different materials including IMIR, FAT, and about 5,000 third-party Quality tests and reports per day with a projected 7.02 crore tests are shared via the Quality Management App. It provides different types of tests on concrete, cement, aggregates, reinforcement, soil, HT strands, FATs (Factory Acceptance Tests), and IMIRs (Incoming Material Inspection Reports).
A Precast Activity Tracker App studies the time and motion of each activity in the casting and erection process to determine cycle time & identify critical path. This App is being expanded to SBS and being developed for I&T girders.
Governance Model
Dividing the C4 package into 5 sections and further subdividing it into 33 stretches, ranging from 1.2 km to 12.2 km, have significantly enhanced its efficiency and effectiveness by splitting operational factors such as scope of work, timelines, structures, and milestones, leaving teams to concentrate and deliver on the big tasks. Granular precise planning and execution, clearly defined roles and responsibilities are some of the advantages apart from speedier decision-making, sense of responsibility and accountability among the team.
A High-Power Steering Committee comprising key stakeholders including S. V. Desai (Whole-Time Director & Senior EVP (Civil Infrastructure)), A. L. Sekar (Advisor – Heavy Civil Infrastructure), Karthikeyan T. V. (EVP & Head – FAA, L&T Construction), and K. Bhavani (EVP & Head – Urban Transit SBG) streamline the approval process, with regular reviews to facilitate smooth decision-making, timely approvals, and effective project management.
With over 130 km of superstructure erection already completed and approximately another 100 km to be constructed, the High-Speed Rail Project is speeding to put India on the high-speed rail map.