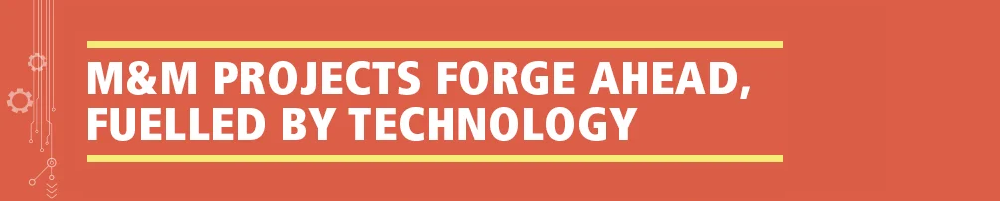
COB project for Tata Steel, Kalinganagar –
Tracking brick by brick
“Our project is truly technology driven, having deployed digital initiatives in planning, execution, and monitoring,” says Project Manager, Prasanta Tikadar, quite dramatically, having to overcome challenges in the refractory works in the Coke Oven. “We use 3D and 4D BIM (using Synchro Pro Software) modelling for the refractory store and refractory supply chain management, have developed a QR code and GPRS-based storing and tracking system, are developing skilled manpower to handle end-to-end refractory logistics, and have mechanized refractory handling.”
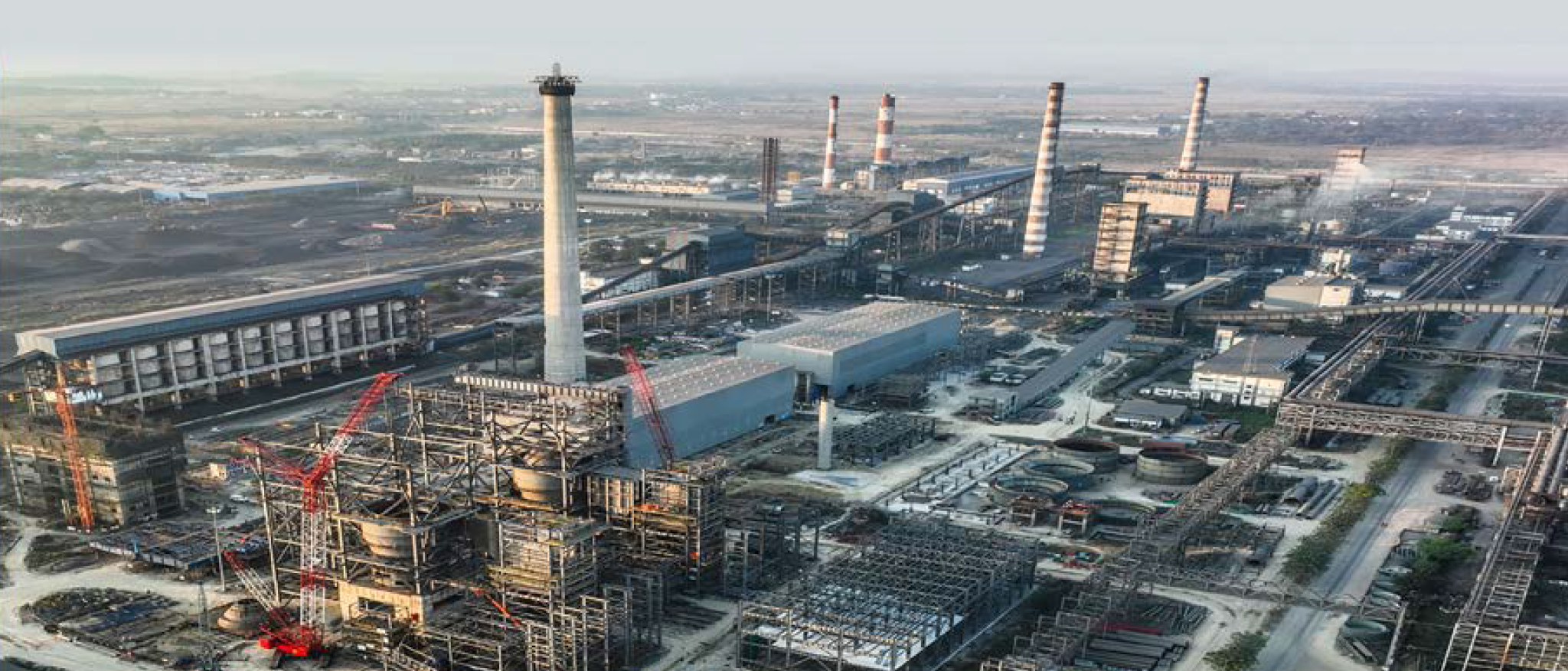
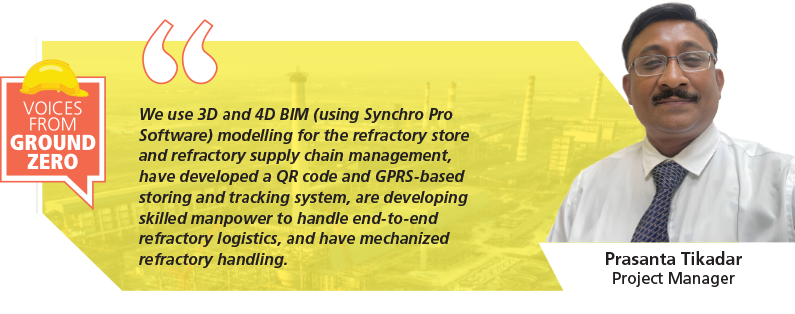
A brick of a problem to resolve
One of the team’s major challenges is to handle 35 lakh bricks per battery and 783 different shapes to manage in each battery, with the brick pallets to be unloaded & stacked in 5 different locations. One can well imagine the complexity of identifying and retrieving the required bricks, in the prescribed shape in the specified time to keep the process of brick lining flowing smoothly.
“The refractory 3D model was prepared using Revit software based on the 2D AutoCAD drawings provided by the client,” informs Planning Manager, Subhashish Sarkar. “On selecting a brick, its name and dimension can be viewed along with the layer in which it has to be placed.”
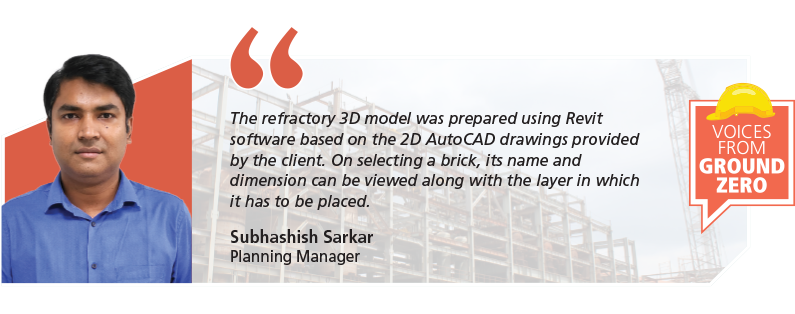
Digitizing project monitoring
“A 3D model of the Coke Oven refractory has been incorporated into the Synchro Pro software for 4D modelling and analysis,” apprises Deputy General Manager (MECH), Sanjay Mitra. “A layer-wise job completion schedule has been prepared in Primavera software which has been incorporated and linked with this 3D model. Thanks to this linking of schedule with the 3D model forms, the 4D analysis reveals planned progress versus actual progress visually.”
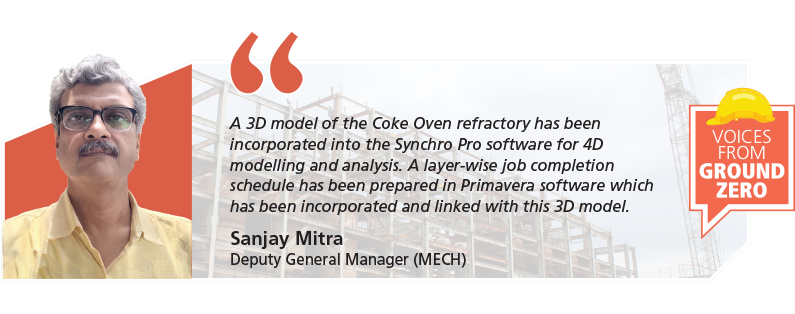
Refractory material handling & storage made simple
Having to unload, re-handle, and feed 140,000 MT of refractories is a tall order, added to tracking & handling 90,000 pallets, storing, tracking, & retrieving 1,375 varieties of bricks & other material, protecting 40,000 pallets containing highly hydroscopic bricks that must be prevented from moistening, and of course, keeping the supply line ticking 24×7. Having understood the magnitude of their task, the team got down to evolving a plan of action.
In their storage plan, they calculated the requirement for covered & open storage and then demarked the land for each location, marking the items to their respective zones/ bays. When the vehicle arrives with the load, it is directed to the designated shed, documents verified, and unloaded only after the client’s clearance. The data is immediately uploaded in EPC Proman. The load is stored in the designated zone/bay after the pallet is checked for any repair. Materials are verified as per the documents using the QR code & GPS. On receipt of confirmation of material at site, it is issued in EPC Proman. All material is tracked with a QR code that can furnish all information regarding location (displayed on Google Maps), transport, where stored and erected.
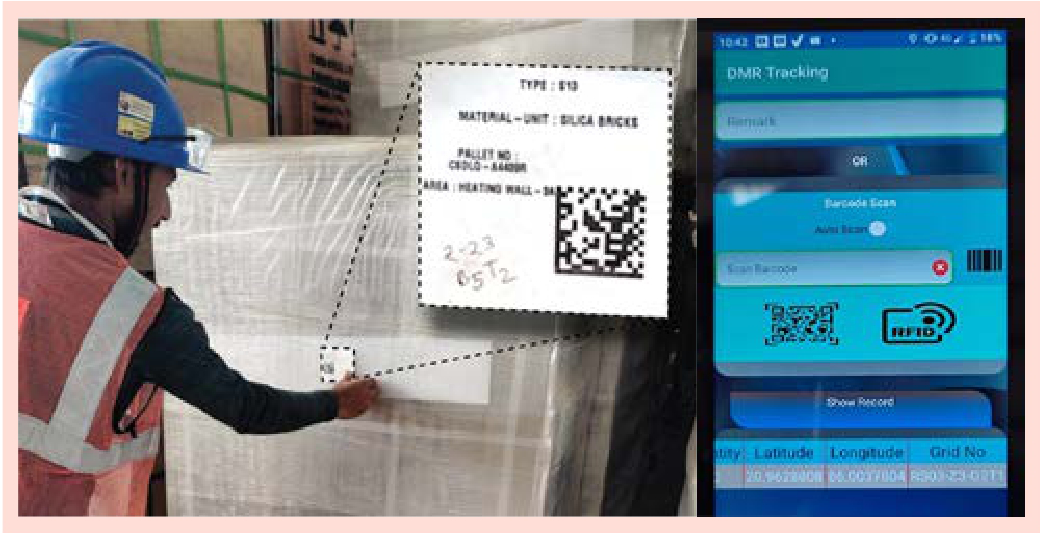
While Prasanta is pleased with the level of tech adoption at his site, like good leaders he is thirsting for more to ensure that they successfully deliver their project to time and quality.
Vedanta Alumina Refinery, Lanjigarh – Towards completing an incomplete project
Having set up a 2 MTPA Alumina Refinery, with an associated 75 MW captive power plant at Lanjigarh, Odisha, Vedanta Limited are keen to boost its capacity to 5 MPTA. An M&M team is executing the associated civil, structural, and piping work on an item rate basis along with commissioning assistance. The scope for Project Manager, Sanjay Saha, and team involves 50,000 MT of structures, 31 lakh IM of piping, 15,000 MT of equipment, and the onerous task of completing 118 tanks (diameters ranging from 3 m to 18 m & heights varying from 3 m to 37 m).
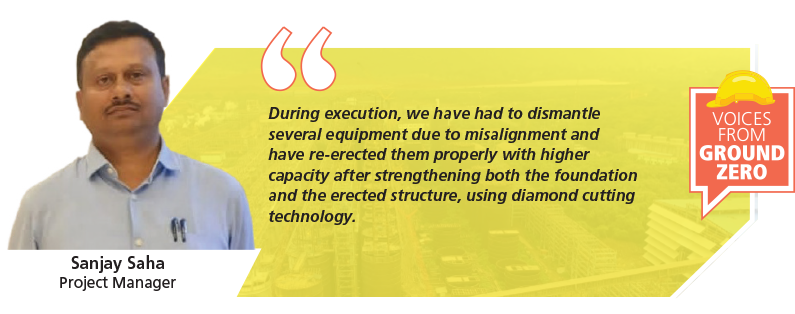
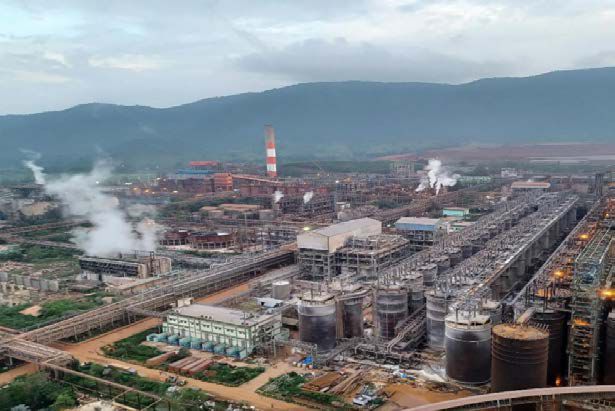
The project has a bit of a history. Initiated in 2007–08, it stalled in August 2010 after 50% completion due to environmental issues; restarted in 2017, it ran aground again in March 2018 and has been given a fresh lease of life in 2020 with M/s Worley, Australia, as the new technology partners.
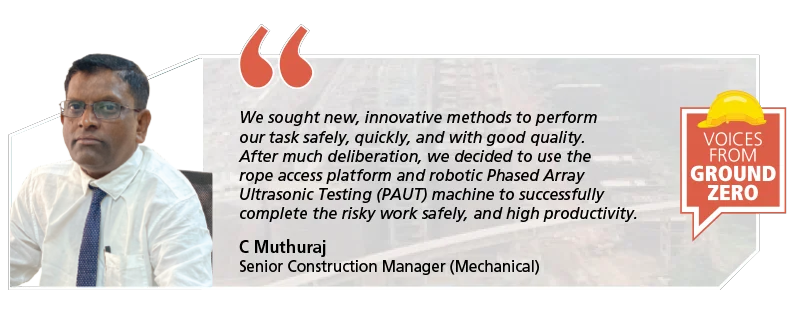
“Making changes to a half-done design is perhaps most difficult in construction,” sighs Sanjay. “During execution, we have had to dismantle several equipment due to misalignment and have re-erected them properly with higher capacity after strengthening both the foundation and the erected structure, using diamond cutting technology.” In some cases, he adds, the entire foundation was broken and re-constructed.
Addressing the matter of 118 tanks
Every welding joint in all the 118 tanks had to be ultrasonically tested, according to Senior Construction Manager (Mechanical), C Muthuraj. “We sought new, innovative methods to perform our task safely, quickly, and with good quality,” he says. “After much deliberation, we decided to use the rope access platform and robotic Phased Array Ultrasonic Testing (PAUT) machine to successfully complete the risky work safely, and high productivity.”
The entire testing process would have required a huge amount of scaffolding to provide approaches for the grinders and UT technicians, but the team’s methodology obviated the need for scaffolding. “The customer was initially sceptical about our approach, seriously doubting the safety of the workmen involved in the process, but we stuck to our guns and finally convinced them to accept our recommendation,” says a determined Muthuraj.
Rope access is an advanced system to access difficult-to-reach areas. Originally based on climbing and caving techniques, the system uses specialized harnesses and ropes to ensure that the tasks are carried out safely with minimum disruption. “All the rope access teams are capable of self-rescue, for the technicians only place themselves in positions where they can be rescued by their team, if necessary,” assures Bharath Kumar, Manager – Mechanical. “To avoid dangerous situations, the rope access crew conducts mock-ups and prepares method statements, risk assessments, rescue plans, & JSAs to ensure that all hazards are identified and mitigated.”
Weld inspections are often a major component of a large company’s non-destructive testing (NDT) programme. The sheer volume of welds, and their presence in critical, no-fail applications, requires companies to invest significant time & resources to test and maintain them. Ultrasonic scanning is the most effective NDT method to ascertain weld integrity. “In this method, high-frequency sonic pulses are transmitted into the welds, and by analysing the reflectance or transmittance of the sound, ultrasonic instruments can quickly locate and identify internal, invisible flaws and defects to ascertain if a weld is safe to remain in service,” explains M Barkat Hussain, Manager – QA/QC.
PAUT is so much better
“PAUT has several advantages over older, standard ultrasonic testing methods. It is faster with a larger coverage area than single-probe methods, allows technicians to scan more at once, reducing the time for inspections,” notes Arnab Das, Assistant Manager – QA/QC. “It is also simple, although the technology involved is complex. The most advanced PAUT equipment is simpler for technicians to use, fully integrated, easy to set up and certainly more efficient with superior test reliability. It gives us peace of mind that our welds will hold,” laughs Barkat.
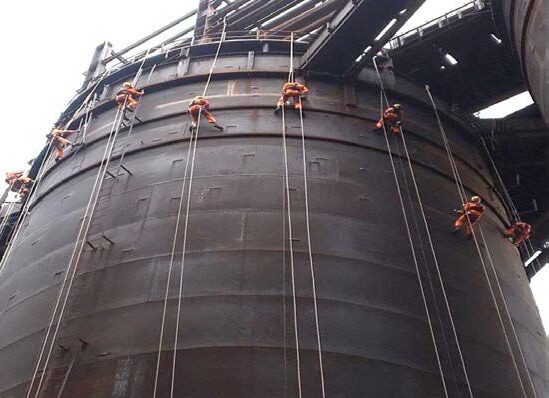
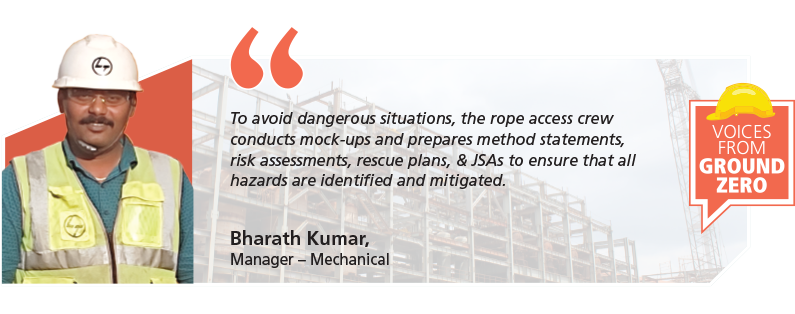
As-built 3D model
Another technology highlight of the Lanjigarh Project is the use of accurate data from an as-built 3D BIM model for engineering and new construction. The advantages are several, as Sanjay ticks off: better construction planning & management, time & cost saving, minimal shutdowns, and enhanced sustainability & safety.
The team is doing more than their bit and, with the help of technology, should soon be able to put finishing touches to a long-delayed project.
AMNS Beam Automation Shop, Hazira – Boosting structural activity
M&M’s project at AMNS, Hazira, has an Automation Workshop that includes an automated CNC cutting machine, CNC drilling, beam fit-up & welding stations, with the mandate to boost structural fabrication activity. Task Force Head, R Suresh Kumar, & team have increased conversion of beams from 3 MT/man-month to 25 MT/man-month, and while one beam was taking 3 days using conventional methods, thanks to automation it is now taking only 0.3 days. “Automation has pushed our production to 750 MT of beams in a single month, which facilitated the speed for completing the Fabricated Structure with less workmen and better quality,” says a pleased Suresh. “Where small items like stiffeners, gussets, and profile plates take very long when cut by hand, automation has speeded up production and that too without any hand marking on the plates,” says Rajesh Sharma, Head – In-house Fabrication, while lauding the efforts of the team of Parminder, Arnab, Sridhar, Zulfikar, Manjali, Atul, Prabakaran, Arunasree, and Abdus to resolve bottlenecks, streamline process and improve productivity.
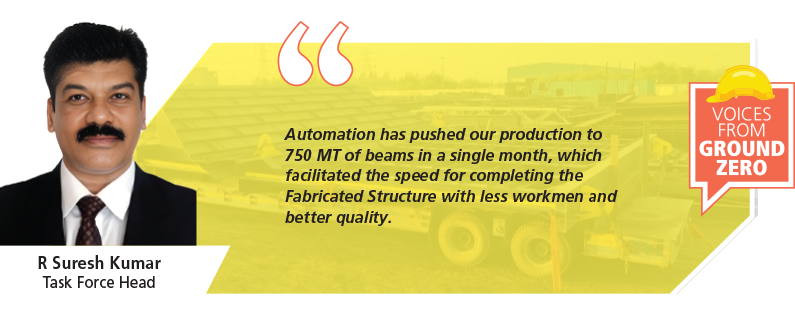
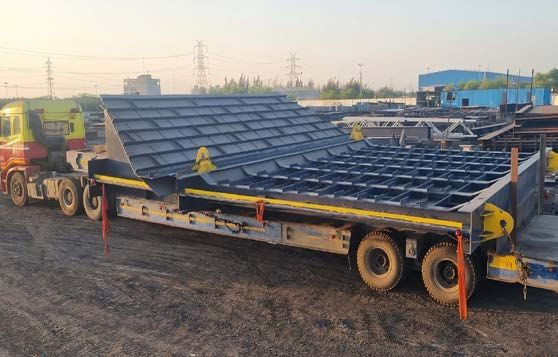
Bunker Girder (8.5 × 8.9 × 3.8 m) (weight: 140 MT)
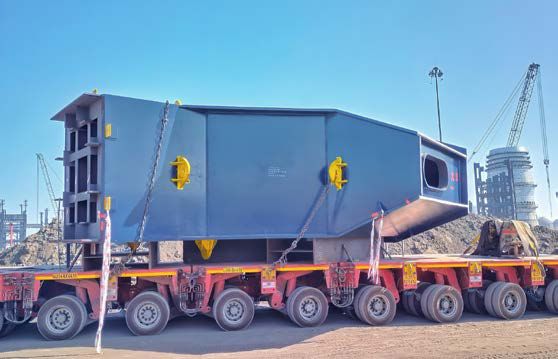
Tower Structure (weight: 80 MT)
Less human effort thanks to Digitalization
“Software like +2D and Pro-Nest help to nest the plates, reducing the time taken by fitters to mark them, for these are directly converted from the AutoCAD .DXF files into .NC files that can be directly put into the CNC machine to cut the profile plates,” describes Rajesh Sharma. With cutting profile and base plates also made easy, the contractor’s time is saved, and the rate of production has increased with the CNC cutting machine cutting 30 MT/day.
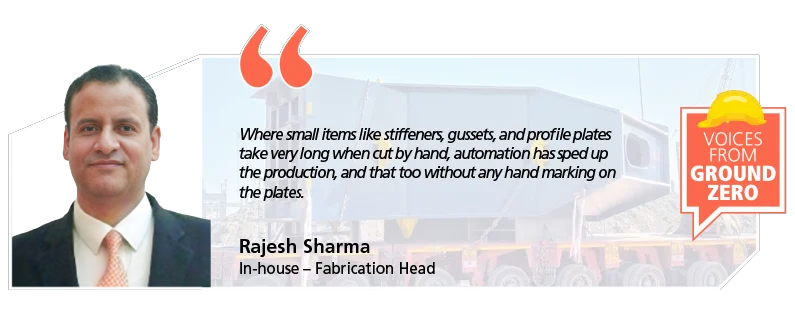
Two CNC cutting machines, installed in the workshop, each possessing both Arc and Plasma facilities and 6 strip cutting nozzles, are used to straight cut the shaft plates or long plates. “Replacing the LPG-based gas cutting sets with portable plasma cutting devices has been one of our standout carbon neutrality initiatives,” observes a satisfied Planning Manager, Sridhar B. “We have two such machines at the Hazira fabrication yard that reduces the use of LPG too.”
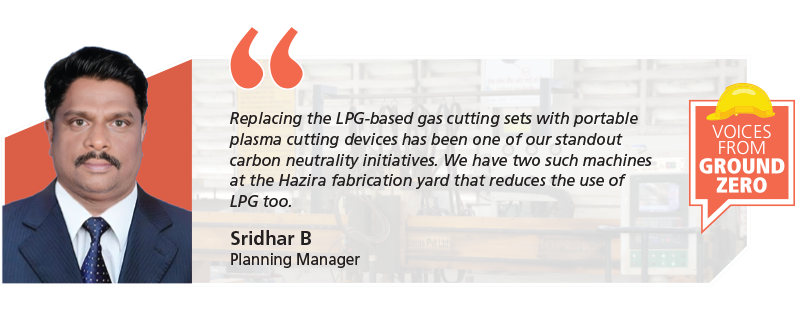
CNC machines also help to convert I-Section beams for columns, tie and floor beams, and smaller profile plates for hoppers and bunkers, which significantly reduces time for cutting and fabrication. In a single month, 1,000 MT of cutting is done by both the CNC machines.
Beam fit-up stations improving productivity
After the plates are straight cut by the CNC machines, they are put in the Beam Fit-Up Station where I-Sections are made. By increasing the number of conversions, presently the team has touched 130 fit-ups a month, with less time taken for loading and unloading that in turn improves shaft production. “Quality improves, human effort reduces, as also arching time for the tilting time,” points out Sridhar. At the start of the project, only a single machine was operational; now there are two Beam Fit-Up Stations that have increased shaft production from 5 beams/day to 12 beams/day.
Beam welding station
The AMNS automation workshop has two beam welding stations. These beam welding machines with 4 tilters of 3,000 × 12,000 mm size can weld long 12 m shafts. Normally, it takes 2 hours & 40 minutes to weld one beam, with about 6 welded from both stations. Now, with the tilting & roller facilities reducing loading and unloading time, 750 MT beams are being welded in a single month, which has helped production to zoom.
With technology playing the lead role, the speed of the fabrication has commendably improved with good quality.