
Meerut–Aligarh–Ghaziabad Road Project
– Acing Mission 100 in 100
Breaking the record to lay 112.5 lane km of the Ghaziabad to Aligarh Road in just 100 hours using 51,896 MT of bituminous concrete (BC), the largest quantity ever used, and surpass the previous records set by other Indian construction firms, is a matter of immense pride for Project Manager, Neeraj Kumar Garg and his team at the Meerut–Aligarh–Ghaziabad Road Project.
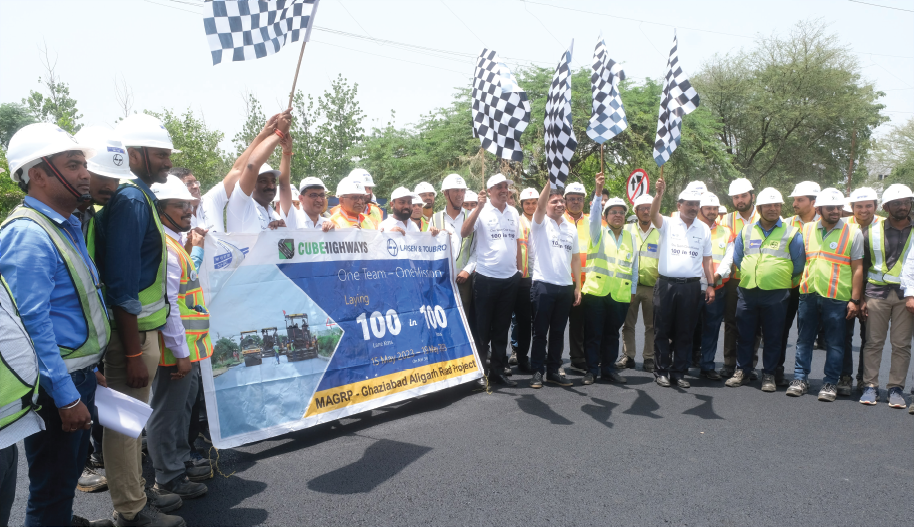
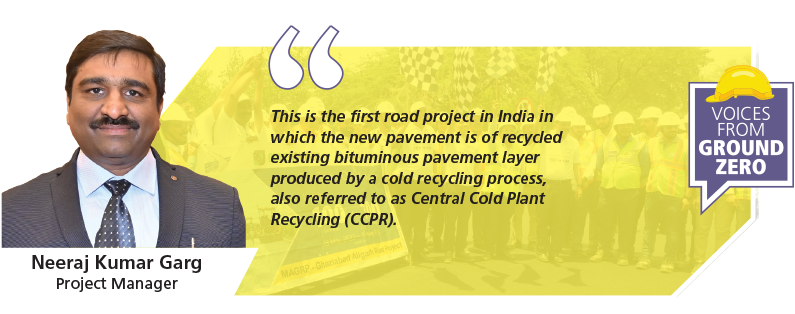
“Our ‘Mission 100 in 100’ started at 10 am on 15th May 2023 and completing at 2 pm on 19th May, maintaining a laying rate of roughly 1 lane km per hour,” shares Neeraj, reliving his sense of achievement. Interestingly, although the set target of 100 lane km was surpassed by the 85th hour itself, the team went on to complete 112.5 lane km by the 100th hour. Even in laying BC, they exceeded their initial target of 44,606 MT.
To achieve an extremely challenging task that involved producing asphalt at six different hot mix plants installed at various locations, transporting the asphalt mix to the various sites and laying it simultaneously at four different locations, was helped in no small measure by technological interventions. Neeraj is thankful too to his team of 250 engineers and 1,900 workmen who worked round-the-clock using 53 specialised road construction equipment to achieve this feat.
The MAGRP up close: Awarded to M/s. Cube Highways & Infrastructure Pvt. Ltd., a Singapore-based developer, the project involves strengthening & widening 126 km from Ghaziabad to Aligarh, an overlay of 119.20 km, widening 83.5 km, developing 15 major & 90 minor junctions and other allied works. A vital road link between the two densely populated cities, the Ghaziabad-Aligarh section of NH-34 is a critical trade route to move goods and connect industrial areas, agricultural belts, and educational zones. The road traverses through several places in Uttar Pradesh, including Dadri, Gautam Buddh Nagar, Sikandrabad, Bulandshahr, and Khurja.
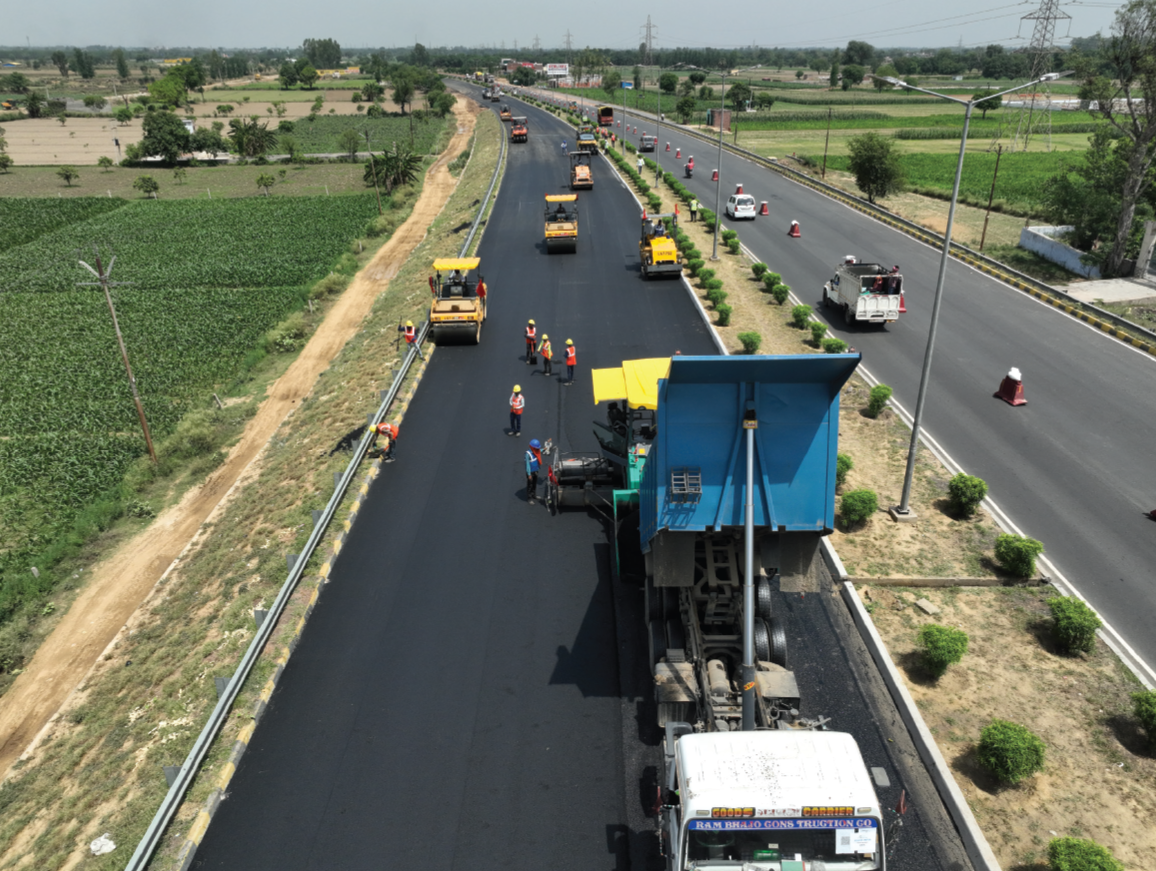
“Apart from being the second project that L&T is executing for Cube Highways, this is the first road project in India in which the new pavement is of recycled existing bituminous pavement layer produced by a cold recycling process, also referred to as Central Cold Plant Recycling (CCPR),” informs Neeraj. The total recycled quantity used is around 5.48 lakh MT, that has reduced emissions to the extent of 12,700 T of carbon dioxide.
Gunning for 100 in 100
It was evident to the team right from the outset that the secret to their success lay in efficiently managing and coordinating resources. After multiple brainstorming sessions involving the senior leadership of TI IC – RBF SBG and the project team, they came alive to the key role that the available digital tools and technologies could play to integrate all the resources for real time monitoring and decision making. “We strategically planned the entire mission and identified 4 key focus areas: Single point contact & coordination, Real time production and site laying progress, Live tracking, monitoring and controlling the fleet of dumpers and Laying status of asphalt mix & allocation plan, with subject matter experts to integrate them digitally,” explains Naveen Kanojia, Planning & Operations Head.
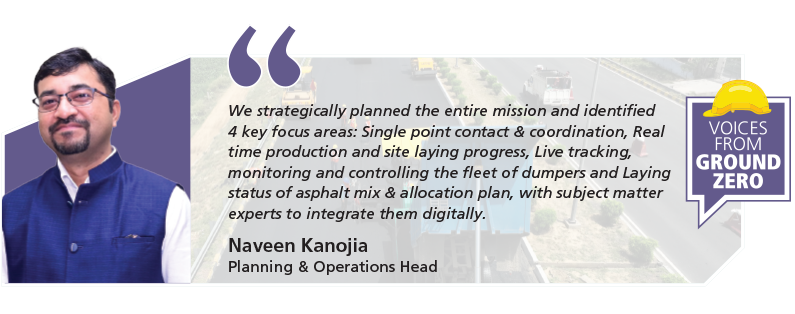
Single point contact & coordination: A Central Control Room or War Room was digitally equipped to track and monitor progress in real time. The four aspects being tracked were production at the various plants, status of the transportation of the mix, status of laying & status of planned v/s achieved.
Real time production & site laying progress was achieved with an App developed on the Power BI dashboard. A QR code, integrated into the App, monitored production. “Specific QR codes were generated and affixed on the individual dumpers,” informs Mohammed Arshun, Manager – Planning. “The Production Engineer scanned the vehicle through his mobile App to enter the quantity of material despatched from the plant and after the vehicle reached the designated site, the Site Engineer scanned the vehicle to report receipt and downloading of the material at site.” All the data captured through mobiles was integrated onto the dashboard.
With this tracking, the team was aware of the material dispatched, how much was unloaded and the quantity laid, all in real time. This digital tool even helped the team to shuffle the dumpers among the laying sites to ensure continuous material feed to all the 4 paving locations.
Live tracking, monitoring & controlling the fleet of dumpers: Live locations, running speeds, ignition status, stoppage time and more of each dumper were tracked real time with GPS technology. “This was not as easy as it sounds for the hot bituminous mix had to be laid within 3 hours from production,” Neeraj shakes his head, recalling those hectic mission days. “Two of the production plants were 65 km away from the laying site and therefore our logistics had to be clockwork to avoid material wastage.”
A dedicated tracking portal ‘Spotrack’ was created, all the vehicles were tagged with their respective production plants and the route patrolling team monitored and controlled every vehicle. The War Room, along with the patrolling team, ensured that the vehicle only took the planned path during transit and any breakdown or hold was promptly attended.
Laying status of the asphalt mix & allocation plan: The App, dashboard, GPS & CCTV on the pavers were all monitored and analysed from the War Room to ensure seamless progress to take decisions on such matters like the maintenance hours for the production plants, shuffling dumpers between the various laying sites and catch-up planning if there were
any slippages.
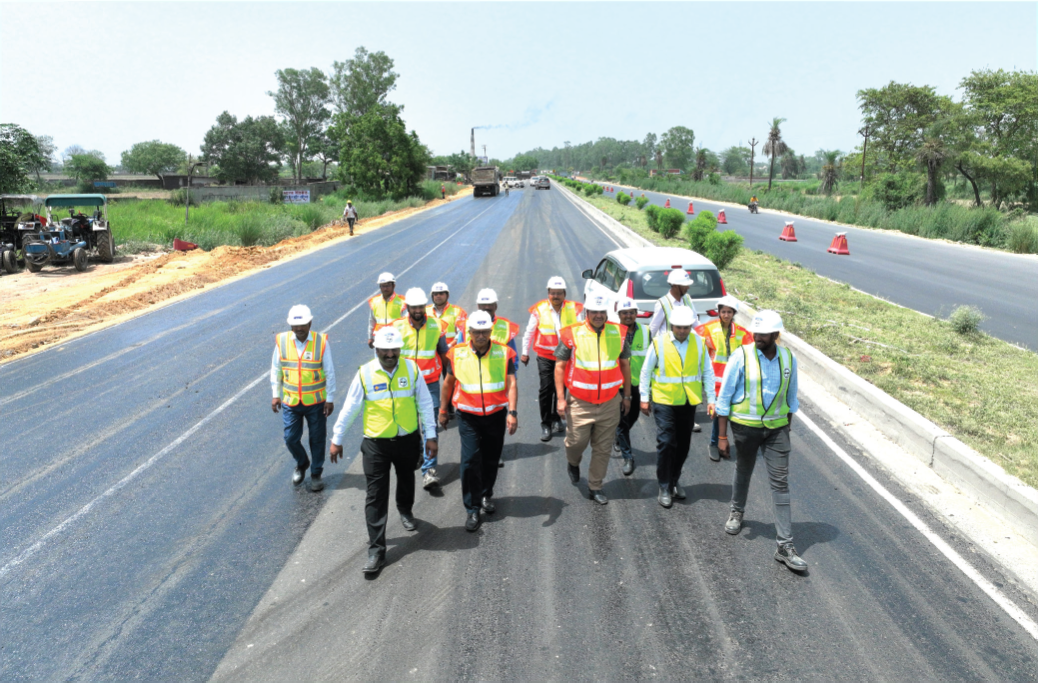
Recognition from all quarters: Achieved in the presence of representatives from the National Highway Authority of India and Cube Highways, the team’s amazing feat drew applause from the Hon’ble Prime Minister Shri Narendra Modi, who tweeted, A notable accomplishment on a very important highway route. It manifests the importance given to both speed and embracing modern methods for better infrastructure.
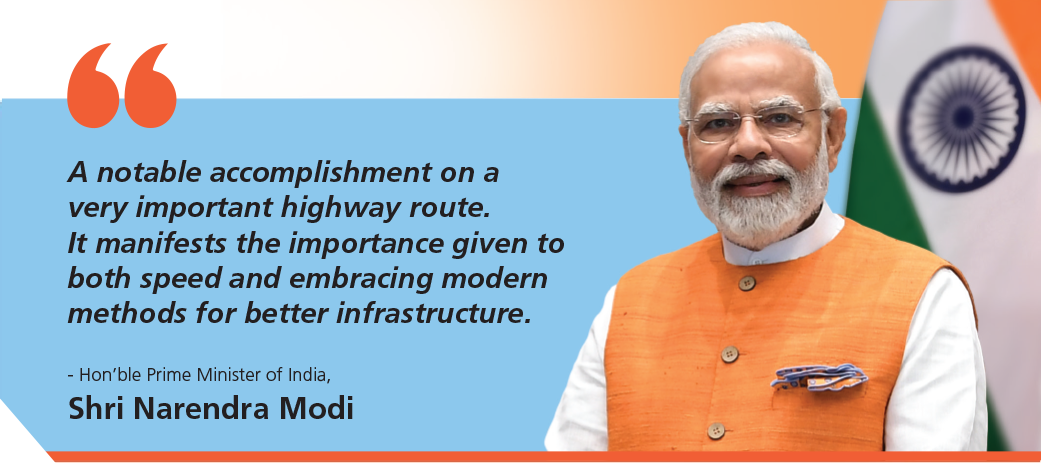
Union Minister of Road Transport & Highways, Shri Nitin Gadkari, too took to X (formerly Twitter): Proud moment for the entire nation! … This accomplishment highlights the dedication and ingenuity of India’s road infrastructure industry. I extend my congratulations to the exceptional teams of Cube Highways, L&T, and Ghaziabad Aligarh Expressway Pvt Ltd for their outstanding achievement.
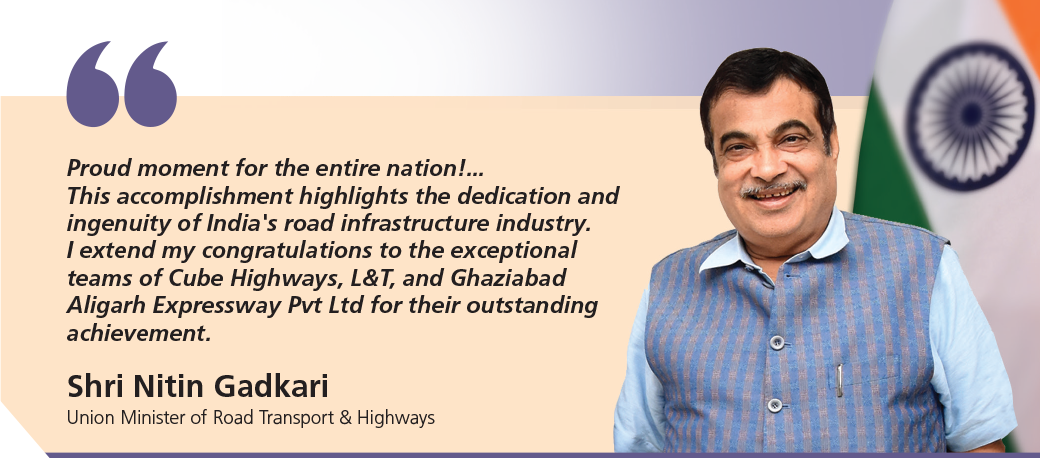
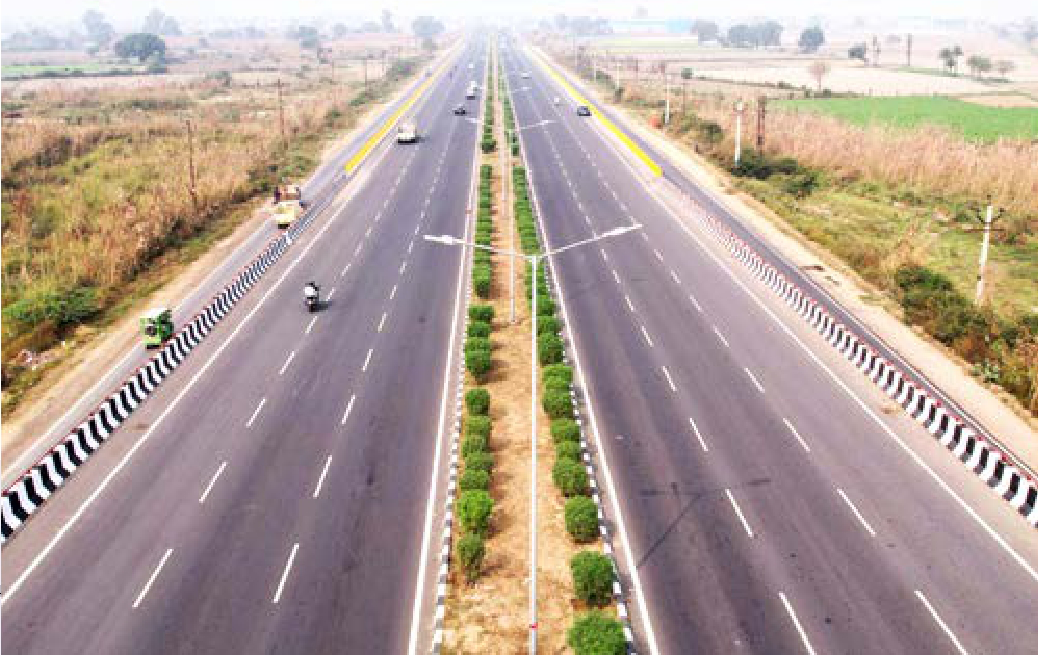
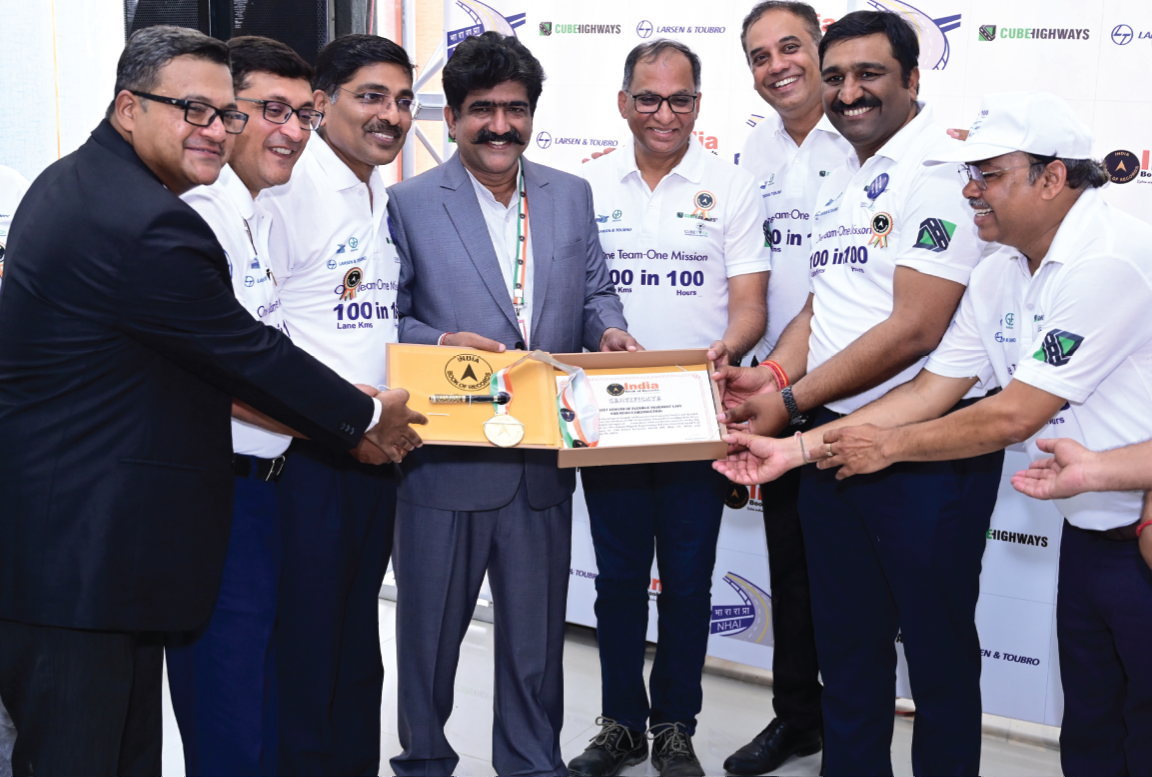
Chairman & Managing Director, Mr S N Subrahmanyan, was lavish with his praise too: “It’s a matter of pride that L&T’s RREC team has achieved this record milestone. It is yet another example of L&T’s crucial role in nation-building. We do things to speed and scale and this achievement is great example of that,” he said.
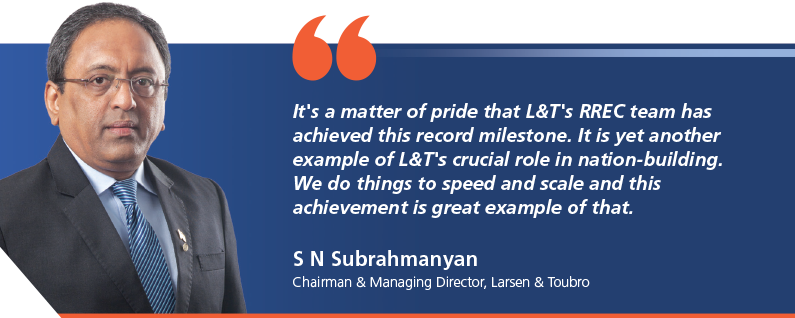
For the project team it was a significant learning from the mission: apart from creating two outstanding records, the team got an opportunity to execute the highest ever recycling of existing reclaimed Asphalt in the form of CCPR. CCPR is an innovative technology that not only utilises recycled aggregate but is also energy efficient when compared with conventional hot mix material for road construction. “This has enabled us to keep pace with the ever-evolving technological advancements that too sustainably,” smiles Neeraj.
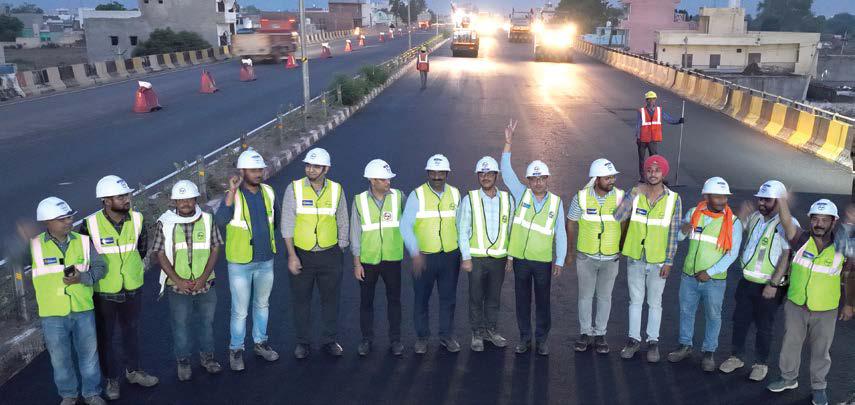
The Project has won various recognitions for the CCPR initiative like the National Environment Award at the GSS Conference – 2022, the Global Sustainability Award by Energy & Environment Foundation – 2023, & the Green Highway Award of the year, by Global Green Foundation – 2024.
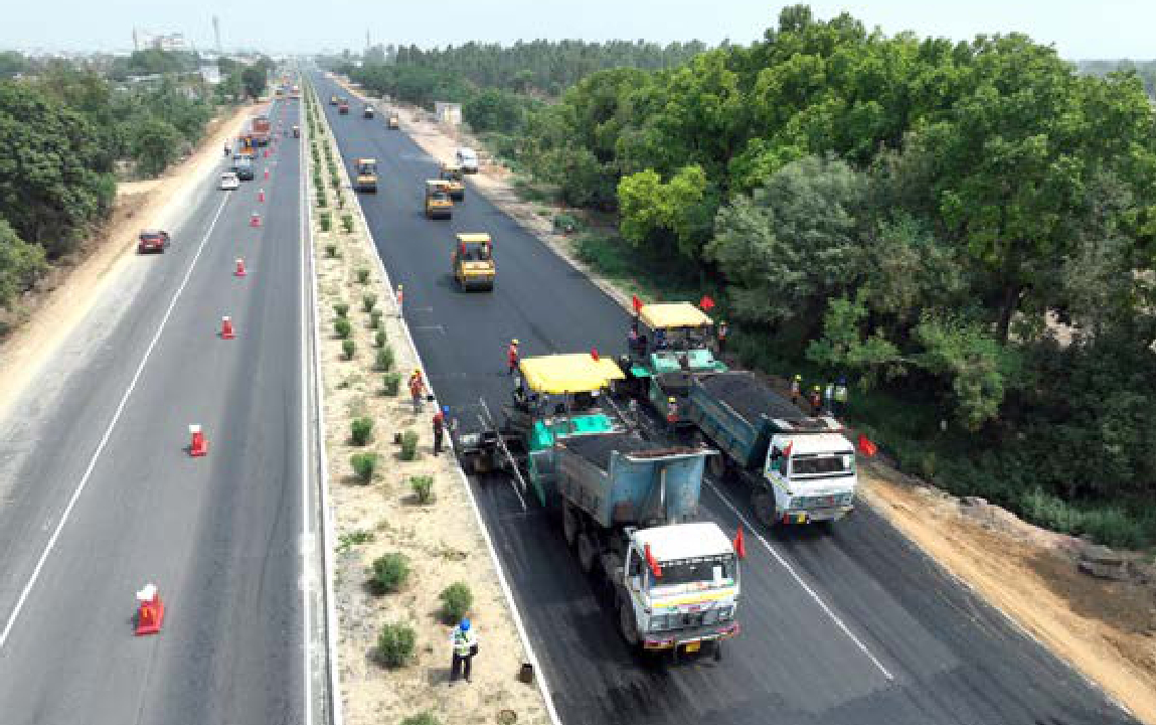
Overcoming several challenges, the MAGRP team completed original scope of works within the stipulated time, after which the client has awarded additional work to widen one of the bypasses, which has also been completed by the project team in accordance with the agreed additional time. They are now preparing for even bigger challenges ahead.
Navi Mumbai International Airport Project
Strategically located in the heart of the fast-developing satellite city of New Mumbai, the eagerly awaited Navi Mumbai International Airport is expected to meet Mumbai’s air travel demands that are reaching sky high. Envisioned as a greenfield airport, L&T is executing the Main Works of the airport on an EPC basis that will augment Mumbai’s aviation capacity, as the second airport to the already existing Mumbai International Airport.
Eventually to handle 90 million passengers, after completing Phase 1, the airport will be able to handle 20 million passengers annually, which is 40% of the existing Mumbai Airport’s total capacity.
Although L&T are the foremost builders of airport infrastructure with 12 airports under its belt, Project Manager, Arvind Kumar Jha, and his project team must still buckle down to construct a complex infrastructure project along with simultaneous land development work involving blasting. “It demands seamless integration and management of multiple domains, all of which must operate or be constructed in synchronization,” he points out. “This intricate coordination can only be accomplished effectively by adopting innovative digital solutions that facilitate precise and efficient management of various project aspects, right from design and planning to construction and operations.”
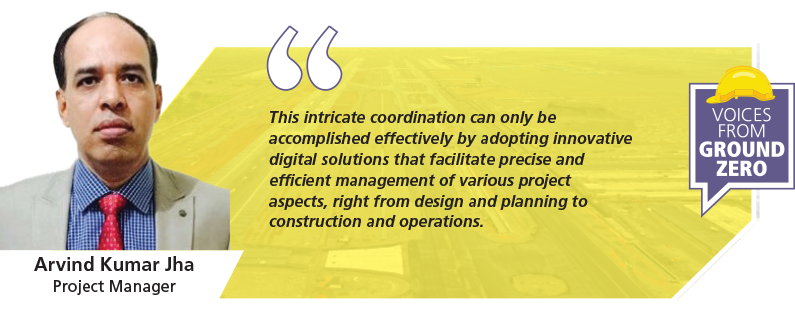
True to his word, Arvind has been spearheading the introduction of several digital initiatives that are improving coordination, productivity & efficiency. Planning In-charge Abhinav Agarwal emphasizes the crucial role of digital initiatives in closely monitoring project progress. “The project is on track for completion and timely hand over,” he asserts. “Considering the extensive scope of work and interfacing with multiple facilities, the digital initiatives implemented at the site have significantly benefited us.”
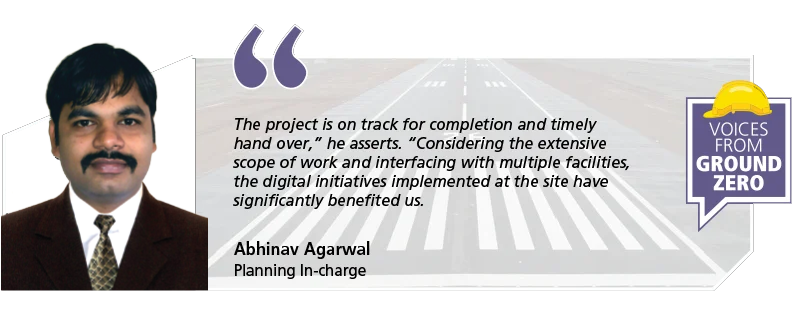
Building Information Modelling (BIM): A detailed 3D modelling of the entire airport infrastructure through BIM has given the team better visualization, helping enormously in its planning, much to the delight of Aniket Kulkarni, BIM Modeller, EDRC, and Shashank Kashyap, Design Co-ordinator, whose responsibility is to ensure clash-free designing for the infrastructure & airside works. “BIM helps us to detect clashes and manage construction activities, ensuring that all our stakeholders have a comprehensive understanding of the project’s progress,” they chorus.
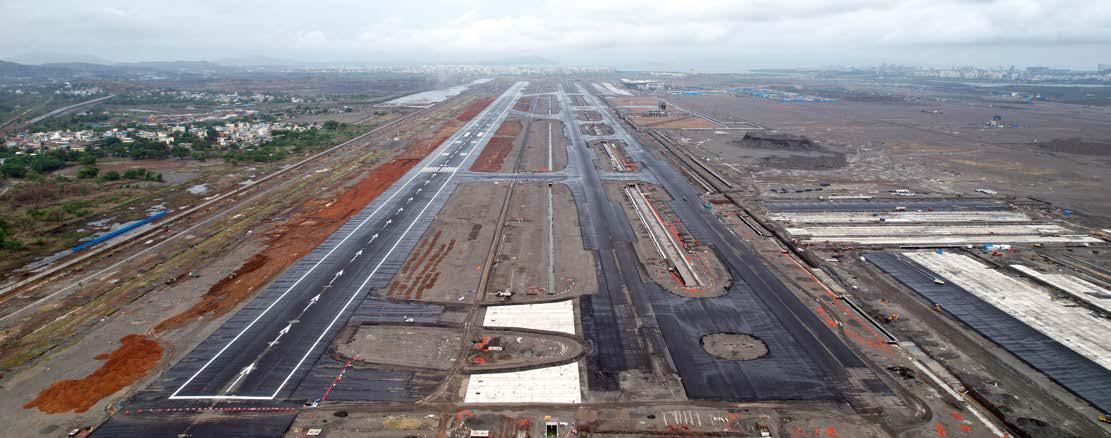
Project Management Software: Advanced project management tools such as server-based Primavera P6 expertly schedule tasks and monitor progress while progress reporting is on a mobile input-based software developed to ensure dynamic reporting. “These digital tools provide a centralized platform for various teams to collaborate, ensuring accurate and timely progress monitoring and reporting.” remarks Prathamesh Dingorkar, Assistant Construction Manager (Civil), who leads implementation of digital initiatives at site.
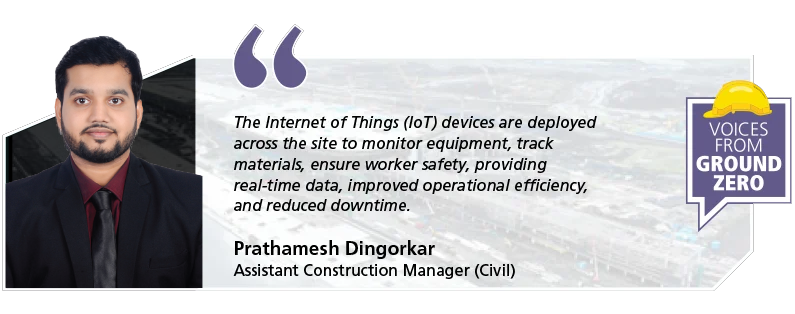
Internet of Things (IoT): “The Internet of Things (IoT) devices are deployed across the site to monitor equipment, track materials, ensure worker safety, provide real-time data, improved operational efficiency, and reduced downtime,” highlights Prathamesh. Digital tools such as MOBA Fuel Dispensing Management System (FDMS), SpotTrack Asset Utilisation Monitoring are being efficiently utilised at site to monitor resources better. “All our batching plants as well as weighbridges are connected to IoT ensuring effective utilisation,” adds Arvind, already reaping the rewards of technology interventions.
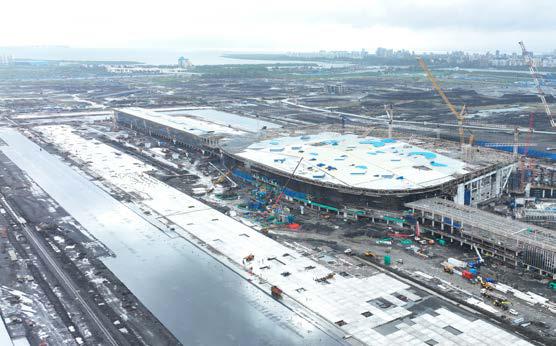
Trimble Grade Controller System, an advanced system, has been deployed to automate motor grader operations to enhance the precision and efficiency of subgrade works. This connects to a base station to ensure seamless communication and data transfer. Describing how the system works, Sai Krishna, Engineer (P&M) explains: “The finalized pavement section design, along with its coordinates, is uploaded into the 3D Grade Controller system, that appears on the controller’s display, providing a visual guide for the operator. When the motor grader enters the designated location, the system accurately displays the specific elevation levels and grading information for that area.” This precise level control is user-friendly for the operators, ensures accuracy, reduces wastages, significantly boosts the grader’s productivity, and saves time.
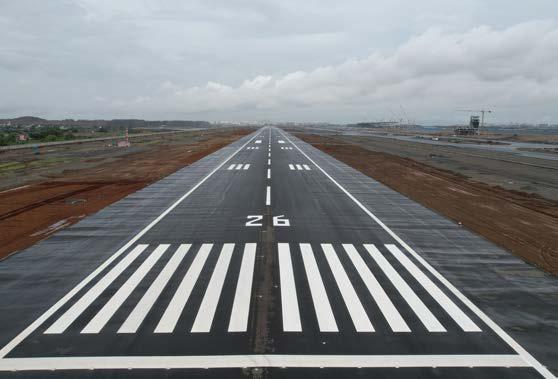
Other digital solutions
AR & VR: Augmented Reality & Virtual Reality technologies are used for immersive training, site inspections, and design reviews. These provide an interactive experience, for stakeholders to explore the construction site virtually and make informed decisions.
Drones are used for aerial surveys and inspections, providing high-resolution images and videos of the construction site that help to monitor, identify potential issues, measure stock, and ensure quality control.
Cloud-based platforms store and share project data securely, enabling remote access and collaboration among stakeholders and all the team members access the latest information, regardless of their location and platforms for
dynamic updates.
Meerut–Hapur–Ganga Expressway Project
– Ticking all the technology boxes
Project Manager, Shashikanta Tripathy, and his team’s mandate at the greenfield Meerut–Hapur–Ganga Expressway Project is to construct a 62.1 km access-controlled 6-lane expressway from Group 1A km 07+900 in Meerut district to km 70-000 in Amroha district, Uttar Pradesh, for the Uttar Pradesh Expressways Industrial Development Authority. “Our project is a part of the prestigious Ganga Expressway project that will ultimately link Greater Noida to the eastern and western boundaries of UP to give trade, commerce and movement of people a huge fillip,” remarks Shashikanta, underscoring the strategic relevance of his project. “We started work on 12 October 2022, and aim to hand over as per our contract on 11 October 2025,” he says with steely determination.
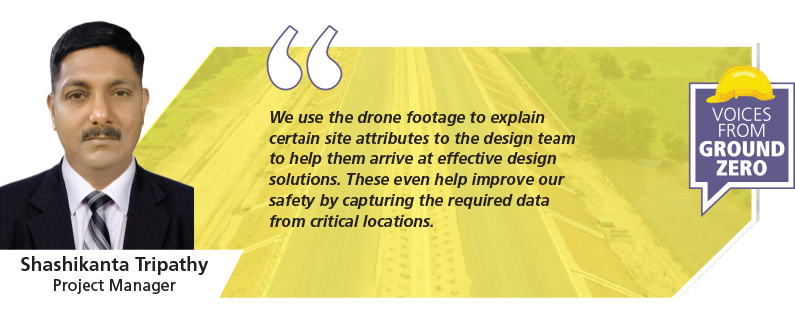
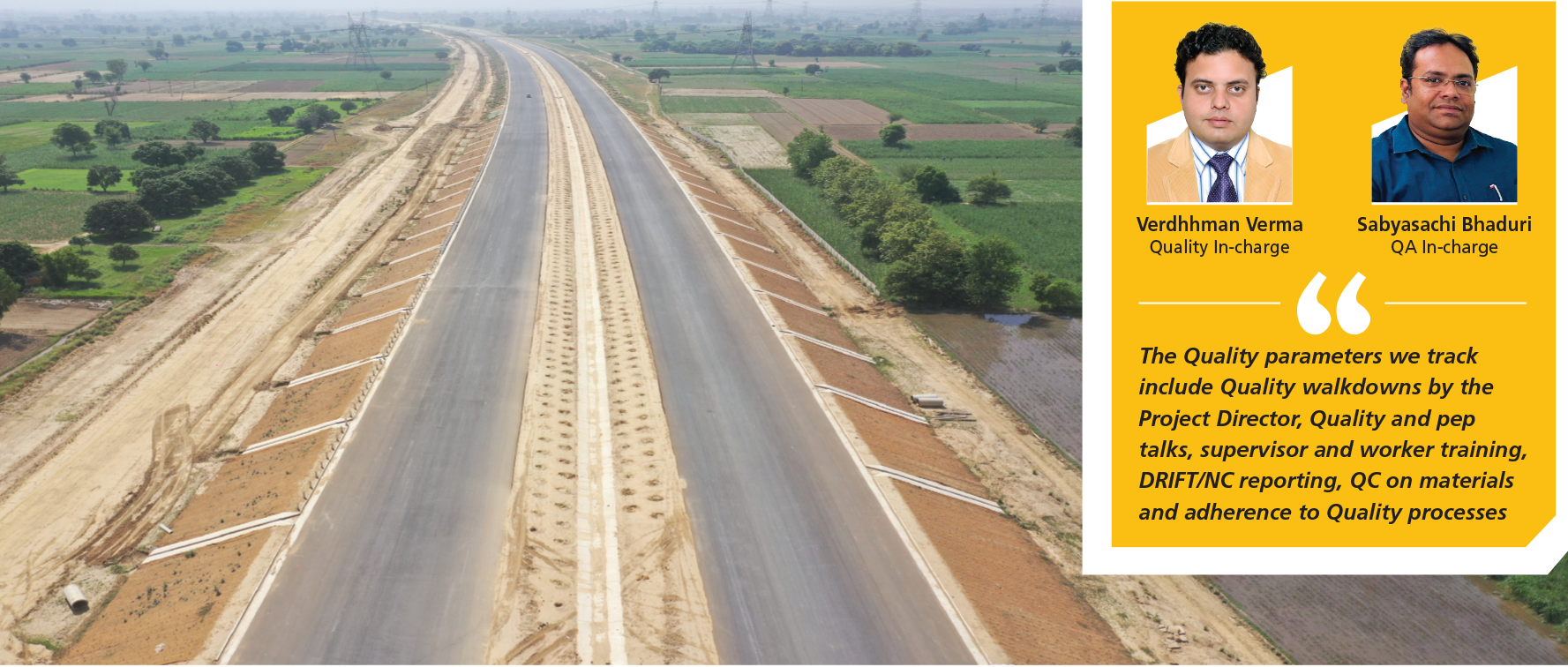
Technology leading the way
“As a team, we appreciate the benefits of digitalization and therefore our technology adoption has been robust, widespread and is paying us rich dividends,” smiles Aneesh Kumar Sharma, Senior Construction Manager (Civil), happy with the results that are helping him and the project team to stay in step with the asking rate. “We have analysed every aspect of the construction process and found several solutions to improve productivity, reduce wastage, cut costs and overall improve
our delivery.”
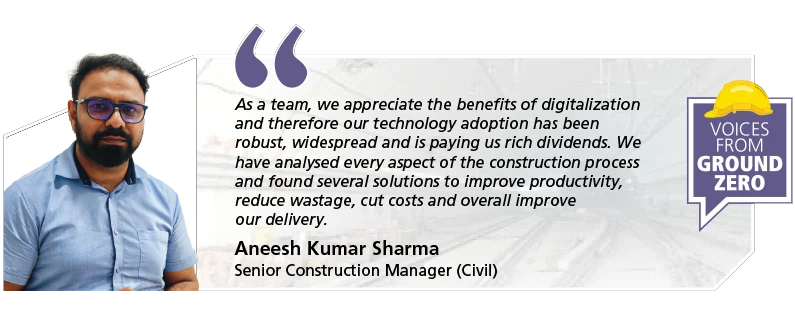
SHEILD: 100% adoption of the SHEILD App translates into usage that is as high as 95% to measure EHS parameters. EHS In-charge, Suraj Eknath Kolhatkar, is delighted with the results. “Since inception, 14,465 RTRs have been assigned, 6,244 instances of Unsafe Act/Unsafe Condition have been submitted and 25 e-TICS have been raised and complied to,” he shares with satisfaction. Their rigorous adoption has ensured that the project has recorded no LTIs, having clocked 12.57 safe million manhours till date.
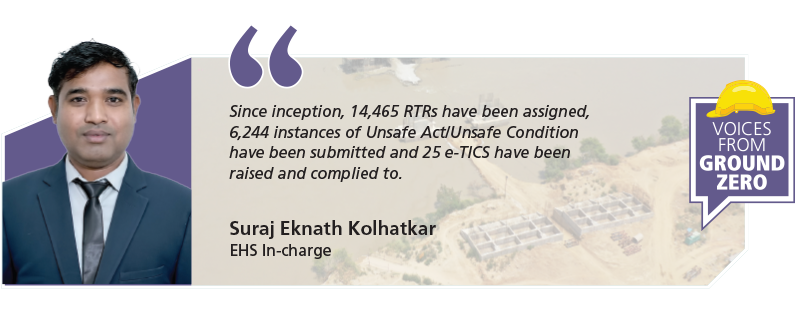
QUALITY: Quality In-charge Verddhman Verma’s and QA In-charge Sabyasachi Bhaduri’s lives have become easier with the deployment of the Quality App, an in-house developed digital solution in Power Apps. “The Quality parameters we track include Quality walkdowns by the Project Director, Quality and pep talks, supervisor and worker training, DRIFT/ NC reporting, QC on materials and adherence to Quality processes.”
WMS 4.0: The team uses WMS 4.0 (a new, improved version f the erstwhile WISA) to onboard & manage workers, maintain their attendance through biometrics and track their demographics. As of date, some 8,000 workers have been onboarded through WMS 4.0 that additionally captures data on the number of unique subcontractors engaged, number of unique subcontractors with workers exceeding 25 numbers, average gang sizes, average daily worker strength and more.
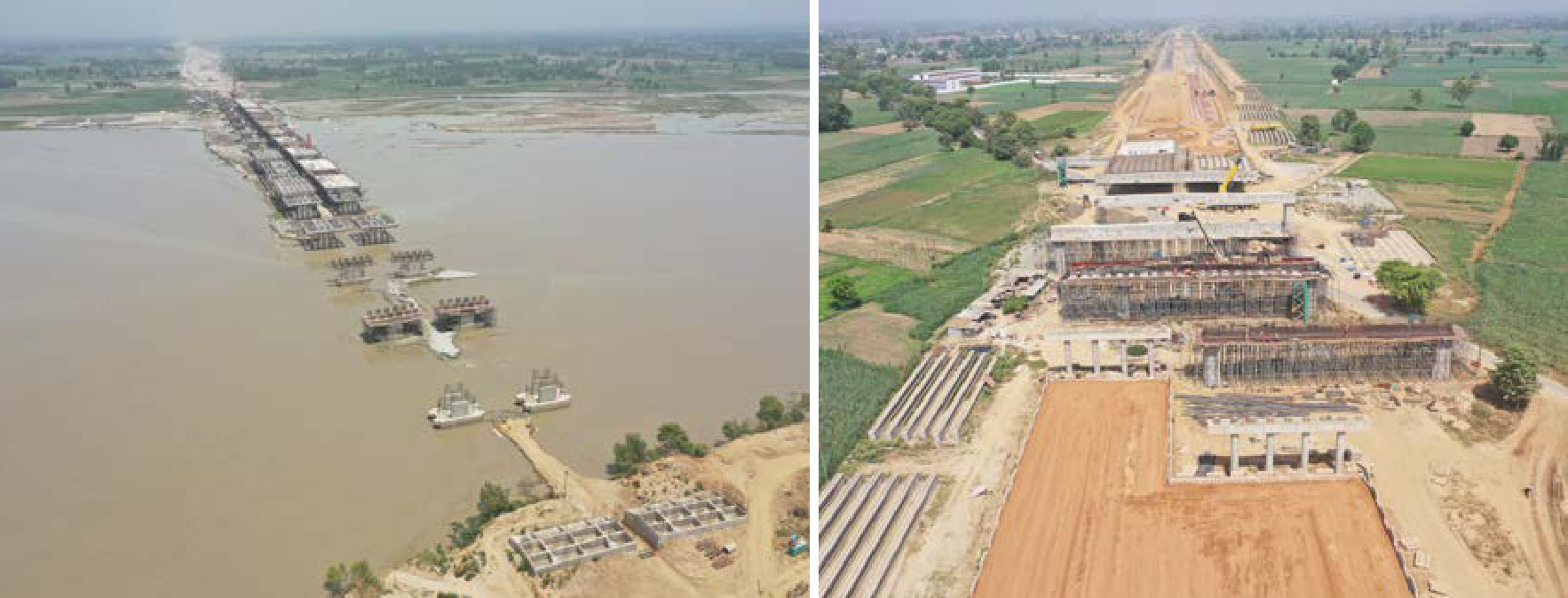
ASSET-INSIGHT: Material tracking is what can give a Planning Engineer sleepless nights but with the digital solution, Asset-Insight, Planning In-charge, Aneesh Kumar Sharma, can at least breathe easy. “With the weighbridge system, we access and track material transactions real time, monitor open, or open and faulty transactions and track material quantities real time,” he says with purpose. With the GPS-based ‘Spotrack’, the team tracks & monitors productivity and status of major equipment in real time enabling easy identification of status.
“As of date, we have tracked, connected and onboarded 254 major equipment,” adds Aneesh.
MOBA-RFID: At an organizational level, fuel tracking has been identified as a key focus area to improve productivity and Shashikanta has not taken his eyes of the ball, using the MOBA-RFID digital App with fuel sensors to track & monitor fuel status, consumption & distribution. “With FDMS, we have kept a strict check over HSD distribution and fuel pilferage at site,” he remarks.
Although linear, the site is under the constant surveillance of 102 CCTV cameras installed in the camp, plant, weighbridge & crushers for remote monitoring, improved security, better EHS & to prevent or at least discourage pilferage & theft at site. Overhead drones record progress showing the diverse features of construction that are then collated into monthly reports for the Client & senior management. “We use the drone footage to explain certain site attributes to the design team to help them arrive at effective design solutions,” remarks Shashikanta. “These even help improve our safety by capturing the required data from critical locations,” he nods.
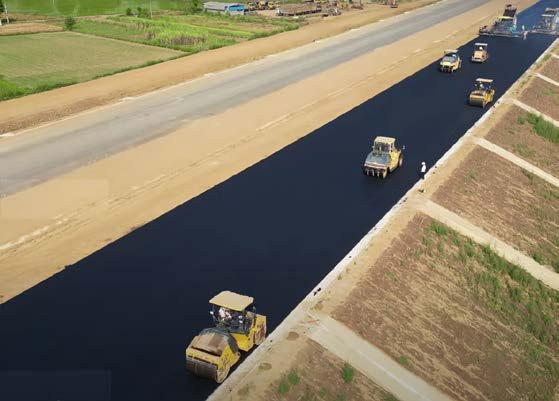
Monthly aggregate stock measurements are taken at the camps & stockyards using the DGPS survey control system that aids to accurately and timely reconcile bulk material.
With just over a year to go to handover, Shashikanta and team are focused to execute their project in time to quality and if they continue their robust technology adoption, we can rest assured that they will deliver as promised.