
WDFC CTP-14 –
A triumph of collaboration
It is a matter of pride for Project Director, Chintan Kumar Parikh, and his team at the WDFC CTP-14 Project for successfully handing over the only integrated freight corridor project that links the Eastern with the Western Dedicated Freight Corridors. Running linear for 128 km across the three states of Haryana, Rajasthan, and Uttar Pradesh, the project is a triumph of detailed planning, tackling each day as a new challenge, closely monitoring progress, and optimizing resources with regular interface to address issues and find solutions.
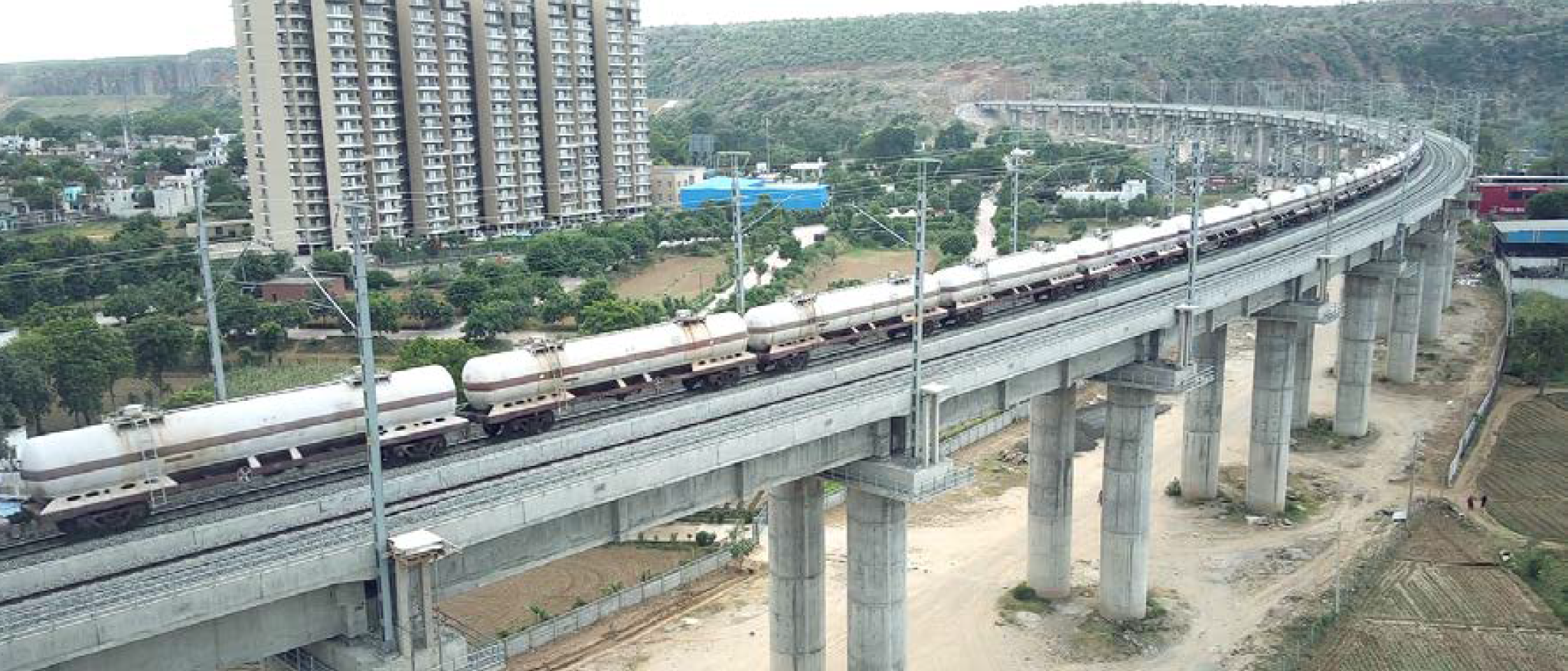
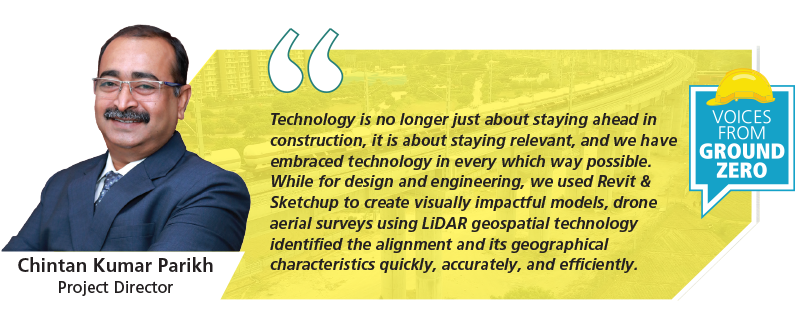
Technology at every station
“Technology is no longer just about staying ahead in construction, it is about staying relevant, and we have embraced technology in every which way possible,” remarks Chintan, astutely. “While for design and engineering, we used Revit & Sketchup to create visually impactful models, drone aerial surveys using LiDAR geospatial technology identified the alignment and its geographical characteristics quickly, accurately, and efficiently.” Later, drones came in handy to periodically film the alignment paving the way for the team to analyse site conditions, plan their activities and understand interdependencies to collaboratively arrive at solutions. Primavera served as the ideal solution to schedule and monitor progress against targets on the three main parameters of planning: Cost, Resources, and Time. It also aided in resource management and levelling.
Understanding interdependencies resulted in efficient multi-tasking Sushil Kumar, Head – Contracts, explains. “While on one side we rushed to utilize ready embankments for track laying, on the other, we hurried to gather teams and wiring equipment for overhead connection after completing ballast laying. At the same time, we could neither overlook signalling and telecom connectivity to ensure precise timing nor allow for any delay in bridge construction along the alignment, at the risk of disrupting NTC availability.”
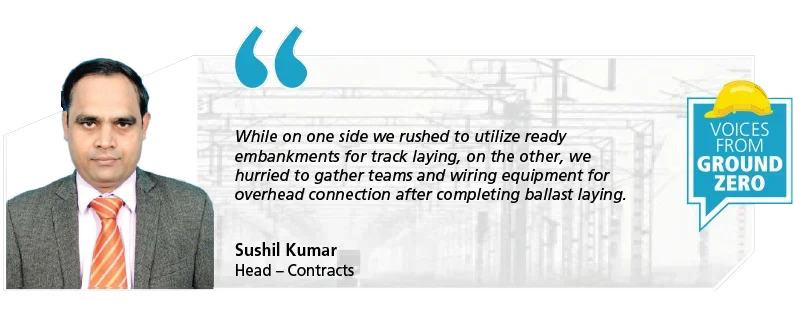
Considering the amount of material, machinery, and equipment like sleeper plants, crushing plants, batching plants, and more that Chintan’s team had to manage, they recognized technology as their able ally. “E4 sensors with GPS, CCTV cameras and the ConEase App significantly reduced theft and wastage,” he remarks. TMS & SCADA, a Train Monitoring System and Supervisory Control and Data Acquisition system for precise monitoring, control, and command from a centralized Operation Control Centre (OCC) established connectivity with other WDFC packages while the WISA App for workers attendance cultivated and maintained discipline in the ranks.
Chintan is proud that his was the first fully automated integrated project for the Indian Railways that required several advanced tech solutions to address numerous existing challenges like implementing the Global System for Mobile Communications in Railways (GSMR) for seamless wireless communication across the entire stretch. “To achieve operational efficiency, we have installed Video Display Units (VDUs) in the Station Masters’ rooms, which provide a comprehensive graphical layout of the yard, depicting real-time status of signals, point machines, track movements, and other signalling and telecommunication devices,” explains Saurabh Sharma, Construction Manager (S&T). A Signalling and Diagnostics (S&D) system comprising subsystems and processes to monitor, analyse and diagnose the performance and condition of the signalling equipment and communication networks ensured reliability, safety, and efficiency of the railway signalling systems by promptly detecting and addressing faults, failures, or abnormalities. A centralized operation control centre ensured reliable systems at individual stations for safe train operations, adhering to established signalling and telecommunication standards.
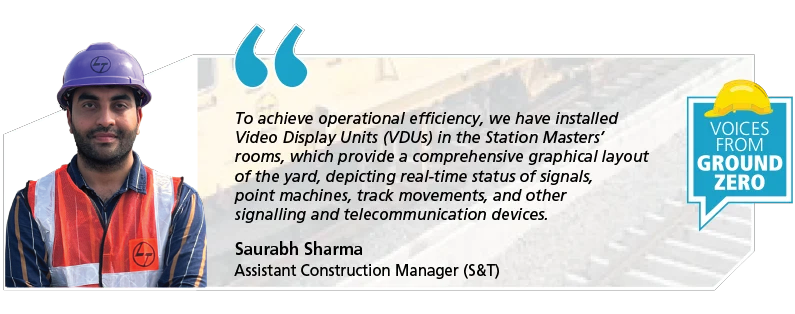
“Conceptualizing and adopting new methods such as the AMT linking method has given us a lead to complete the track linking work. Close coordination and meticulous planning has further helped in achieving completion of the post track works simultaneously with OHE works,” explains Vikas Niwad, Construction Manager (Tracks). These VDUs help Station Masters to easily identify any discrepancies and promptly issue commands to the computer-based interlocking system. Additionally, it coordinates with the Electronic Interlocking (EI) system to enact the required responses to maintain operational integrity. The digital App, TILOS, proved invaluable aiding the team to find quick solutions to maintain progress.
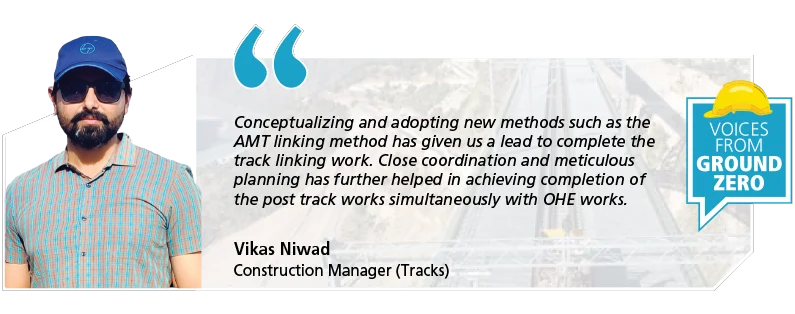
A sophisticated system to control railway traffic, the EI system unlike traditional mechanical interlocking systems which rely on physical levers and rods, uses computerized control units to manage railway points and signals, incorporating safety logic algorithms to prevent conflicting movements of trains, prevent collisions and address other safety hazards with real-time monitoring and integrating with other railway control systems, such as train detection systems, and communication networks.
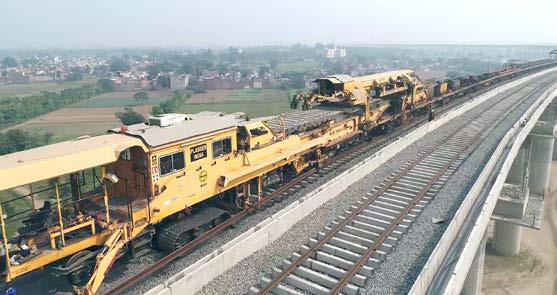
There is no project without challenges
Chintan reminds that project success is a result of overcoming numerous obstacles encountered during the construction phase. “Our challenges included dealing with different teams for various tasks and understanding their interdependencies such as formation, bridges, buildings, tracks, Overhead Equipment, power supply installations, signalling, and telecom and, most critically, aligning all these elements,” he shares. FAA Head, Nabeen Padia, adds, “Our collective commitment to foster a positive and inclusive culture made this journey not only productive but enjoyable as well and helped to navigate numerous challenges, including commercial and financial hurdles.”
Executing in the Aravalli hills posed huge geographical and terrain challenges, remarks Jaspreet Singh Gill, Project Manager (Formation & Structures), with a shake of his head, mentioning the difficulties of maintaining slope stability when working between a 28 m deep area on one side and an equally elevated embankment zone on the other.
“Of course, there was the small matter of interacting with various authorities for live highway diversions, working metro lines, shifting gas pipelines, which added several layers of complexity to our task,” he laughs.
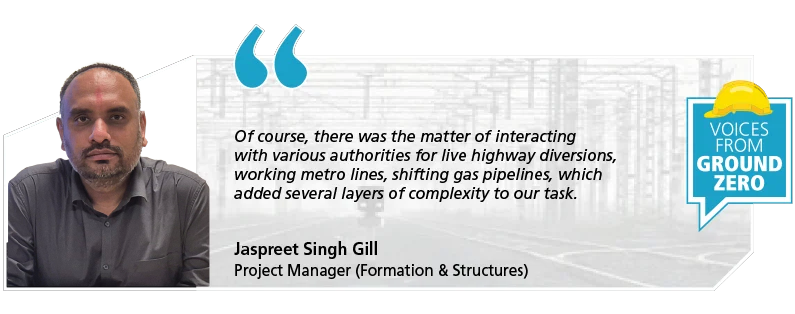
SPARSH, VR & AR training modules helped achieve ‘Mission Zero Harm’, much to EHS Head, Bhimasen Shukla’s delight. The SHELD platform ensured systematic implementation of safe practices by organizing pre-work assessment through checklists prior to commencement of the job, identifying and notifying unsafe acts/unsafe conditions through EHS observations.
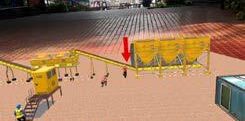
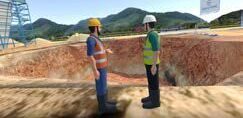
Describing its complexity, Amalanshu Maity, Project Manager (PSI), says that it involved civil, track, E&M, and S&T, all in a single package. “The E&M works were challenging including various step components procured from overseas and engaging with multiple vendors and sub-contractors to deliver as per the Contract and within the timeline. Strategic planning and coordinating with the Client and Consultants were critical to achieve our milestones and a pleasure to work with such a wonderful team,” he enthuses.
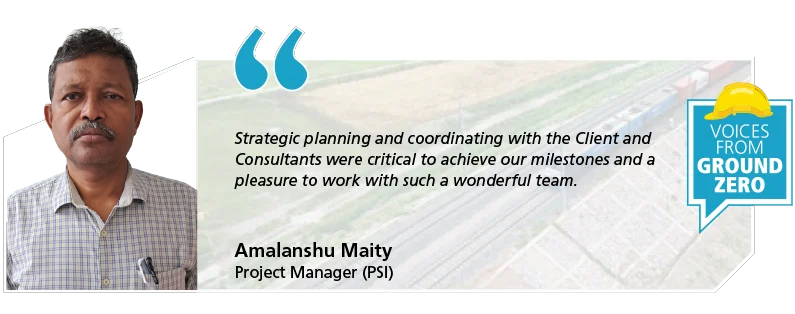
Jaishankar Batra, Construction Manager, Formation & Structures found CTP-14 a great proving ground. “We got the opportunity to work on double container tunnels with 2 tracks, the longest viaduct of 2.75 kms, hill viaducts ranging from 25 to 30 m, top-down construction in deep cut ROBs constructed using the latest civil engineering techniques such as jump forms, pier caps with brackets, full span girder launching by tandem lifting, and more.”
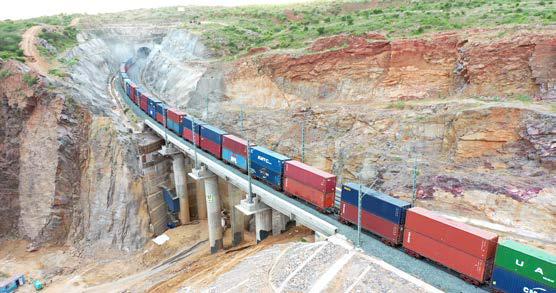
Interdependencies of various works is one of the crucial challenges in this project which further leads to resource constraints, according to Senior Construction Manager (Formation & Structures), Ram Suresh. “Yet, with meticulous planning and effective communication, we centralized our efforts, meeting the challenge of resource management with creativity and adaptability, ensuring that no obstacle hindered our progress. This accomplishment stands as a testament to our team’s cohesion and resilience in the face of adversity.”
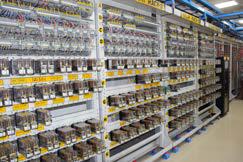
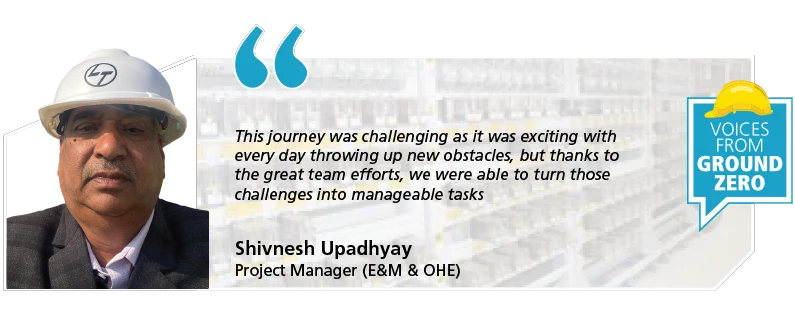
“This journey was challenging as it was exciting with every day throwing up new obstacles, but thanks to the great team efforts, we were able to turn those challenges into manageable tasks,” exclaims Shivnesh Upadhyay, Project Manager (E&M & OHE). “Be it problems related to execution or local issues, we successfully faced them all together.”
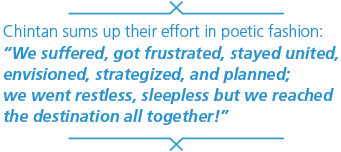
KRCL Katra–Dharam Railway Electrification Project
– Overcoming Himalayan challenges with technology
The Katra–Dharam Railway Electrification project, part of the ambitious Udhampur– Srinagar–Baramulla Rail Link Project, envisions to connect Kashmir with the rest of the country’s railway network. Running almost entirely through the Himalayan ranges, 62 km of the total 72 km long project stretch are tunnels; additionally featuring two special major bridges – the Chenab (world’s highest railway) Bridge and the Anji (first cable-stayed railway) Bridge.
L&T is executing railway electrification (rigid overhead catenary system (ROCS) type OHE) in this section for the Konkan Railway Corporation Limited (KRCL), at altitudes of 750 m to 1,500 m where temperatures vary from −2° to 45° Celsius, overcoming varied challenges of unapproachable routes for site access and working along with other agencies like civil, track, & signalling contractors.
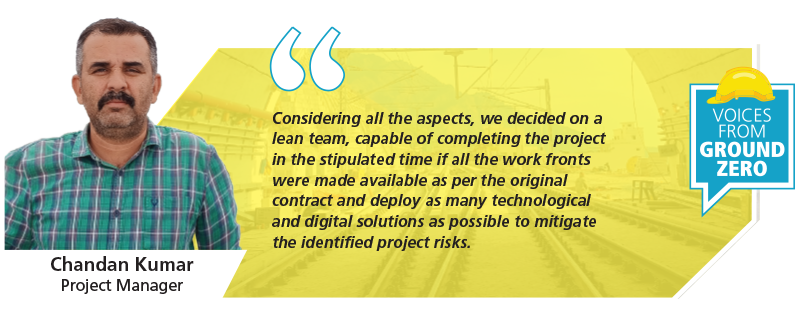
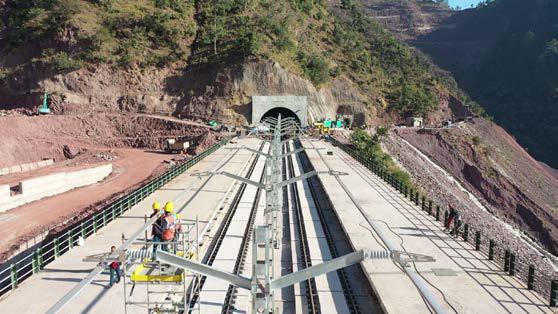
India’s first mainline electrification project using the Rigid Overhead Conductor System (ROCS)
L&T is spearheading the railway electrification in India’s strategic Jammu–Baramulla line through electrification of the Katra–Dharam sections for Northern Railway. The project encompasses 25 kV electrification of 80 TKM including ROCS (Furrer + Frey, Switzerland) for significant stretches, associated power supply systems, and SCADA.
Apart from the terrain and temperatures, another initial headache for Project Manager, Chandan Kumar was the non-availability of most of the tunnels when L&T signed the Contract with KRCL, raising the question as to how to plan resources for optimum utilization. “Considering all the aspects, we decided on a lean team, capable of completing the project in the stipulated time if all the work fronts were made available as per the original contract,” he avers, “and deploy as many technological and digital solutions as possible to mitigate the identified project risks.” Riding on the wholehearted support from the management, Chandan is glad that their technology adoption is of a high order, even comparable to some
global companies.

Out-of-the-box solutions to drive progress
The team was struggling to design the Drop Tubes for the tunnels that holds the overall ROCS system due to the non-availability of the tunnel cross sections making it difficult to determine the specific parameters for each location. Manually measuring the height of the tunnel and track angles at the anchoring locations was an option, but with other agencies working and restricted access, it would have been extremely time-consuming.
“To overcome this problem, we adopted a new technology to get the required data to design the Drop Tubes called the OHE Height-Stagger Gauge,” shares Planning Manager, Gourav Bhattacharya, with an air of triumph. The device has a Hilti Laser Range Machine with a Digital Spirit Level at the base, that can be placed on the railway track to measure the height of the tunnel as well as the cant of the track to determine the length and angle of the drop tubes. When placed on the track, the gauge throws up the angle of the tracks, the tunnel crown height and other important parameters. “We saved a lot of time in the process and were able to procure material before the fronts were made available to us,” sighs a relieved Gourav.
Adopting this technology has been hugely beneficial for Chandan and his team as Planning Engineer, Souvik Das, adds with a grin, “We were no longer dependent on the client for the tunnel’s cross sections and could proactively procure the Drop Tubes that won appreciation from KRCL for prompt delivery of the material.”
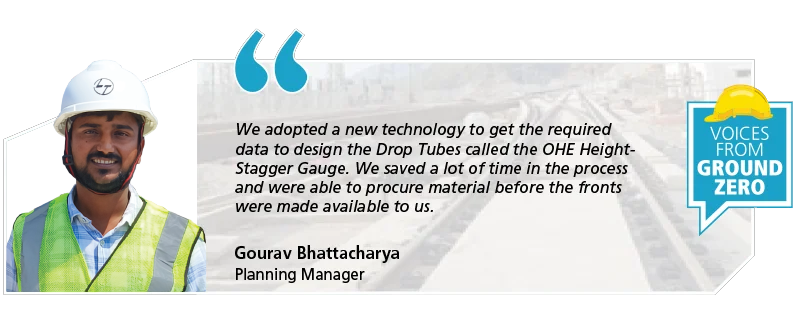
Shielded from harm
Given the terrain, the altitudes, the temperatures and the gruelling nature of work, EHS is non-negotiable. The team therefore has consciously implemented a transparent & robust digital system to drive safety with the SHEILD Safety App with the observation module to recognize unsafe acts/conditions and eliminate them, using suggested corrective measures for a safer workplace. “We have developed safety checklists specifically for this project for work like structure foundations, mast and boom erection, working at height and all PSI activities, that are integrated in this App,” says Senior Engineer – EHS, Swapneshwar Nayak, “to monitor timely compliance of EHS observations too.” It is a ritual for every Site Engineer to update the App every day, once before and then after work.
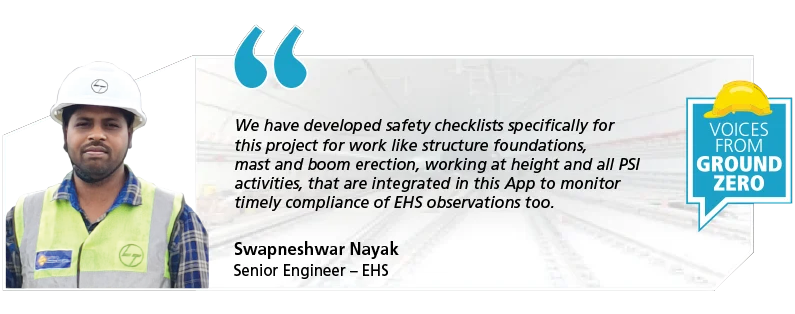
Safety is a critical consideration especially for a team that is executing in various locations that are prone to landslides, working at heights on the Chenab Bridge, transporting men & material and working in the 11 km long tunnel. “We encourage near-miss reporting and vigorously examine lead indicators for risk identification, assessment, mitigation and monitoring,” stresses Chandan. “We continually assess progress and output by identifying and addressing deviations, if any, from the desired quality and client-approved method statements, conducting comprehensive reviews through root-cause analysis for corrective and preventive actions to avoid recurring issues.”
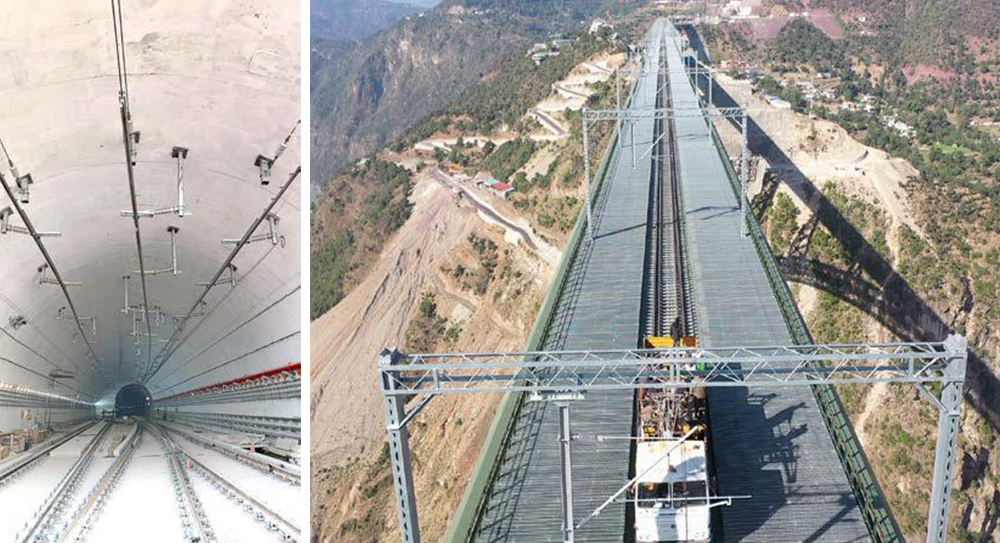
Electrification in Katra–Dharam sections in Jammu–Baramulla Railway on the iconic Chenab Bridge
MS Project keeps the project on track
In this project more than in others, the onus of getting it right first time is critical, for which the team strictly implements MS Project to plan their work, with significant benefits. “With its features and capabilities, we have optimized our project planning, resource allocation and project status monitoring,” states Gourav. “To start with, all the major tasks in each section were identified and a core project structure created and then the sub tasks under each major tasks created with resources.”
Thereafter, based on the site conditions and access related inputs from KRCL, the duration for each activity is set and linked logically. It is important to note that the team maintained multiple baselines in the same programme, for future references at the time of request for extension of time. “Utmost importance has been given to activities in the critical path to ensure timely completion and we review variations and float reports on monthly resources to effectively utilize resources without impacting the critical path,” elaborates Chandan, adding with a chuckle, “Due to a lean site team, we are collaborating with HQ for a shared resource to update schedules monthly.”
All project correspondences are on SharePoint. “We have developed a template to assign categories and sub-categories to each document that are mapped to each related activity in MS Project,” explains Souvik. In case of any delay from the client, the documents supporting the start & end of the cause for delay is mapped and monitored by HQ’s Contract Management team. “With up-to-date documentation of all events, we can analyse time impact in-house to ascertain the delay liabilities,” he adds. The team shares the summary of these analysis in their Monthly Progress Reports to the client for necessary action that have helped them receive a first extension of time without any delay damages.
Summing up their technology interventions, Chandan says, “In our project, the stringent requirements and working conditions have motivated us to leverage the power of technology to overcome challenges and implementing them has benefited us greatly to achieve our business goal,” he signs off, buffeted by strong winds atop the Chenab Bridge.
Agra Metro Electrification Project
– Several ‘First’s, including tech adoption
A 29.6 km urban Mass Rapid Transit System (MRTS) with 2 corridors and 28 stations, the Agra Metro Electrification Project involves electrification through a 750 V DC Third Rail Traction system, and it is the first project to be executed by L&T (RBG of TI IC) with this system. That it is India’s first DC metro system to successfully commission an inverter system to reuse regenerative braking energy is yet another of the project’s claim to fame.
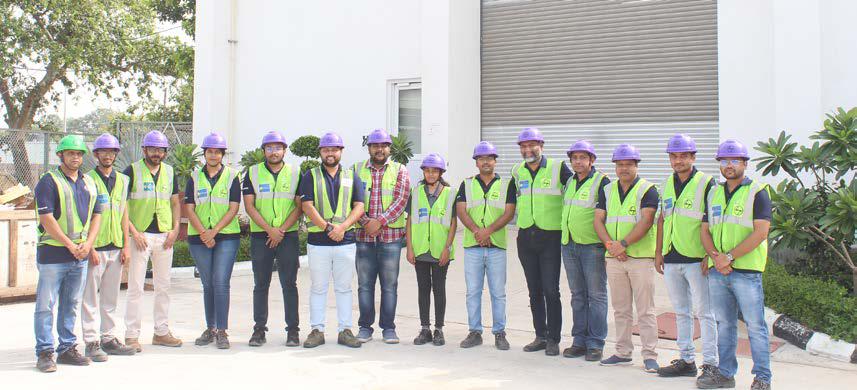
A 6 km priority section with 3 elevated and 3 underground stations between Taj East Gate and Mankameshwar section of Corridor 1, strategically selected around the heritage sites of Taj Mahal, Agra Fort, Mankameshwar Temple and Jama Masjid for the benefit of tourists, was officially opened on 7 March 2024 by the Hon’ble Prime Minister of India, Shri Narendra Modi, through video conferencing, with the Hon’ble Chief Minister of Uttar Pradesh Shri Yogi Adityanath, physically present at Agra.
Managing stringent timelines
Awarded in March 2022 and with the team mobilized by May 2022, Planning Manager, Animesh Kumar – who is presently leading the project under the direction & guidance of Prashant Soni, Cluster Manager (West), MT BU – says that their priority was to address the stringent phase-wise target set by the client, Uttar Pradesh Metro Rail Corporation (UPMRC), for the priority section starting with the commissioning of the Receiving Substation (RSS), Traction Substation (TSS) & Depot by March 2023, the elevated section by July 2023 and the complete the priority section including the underground section by March 2024, along with the mandatory CMRS inspections.
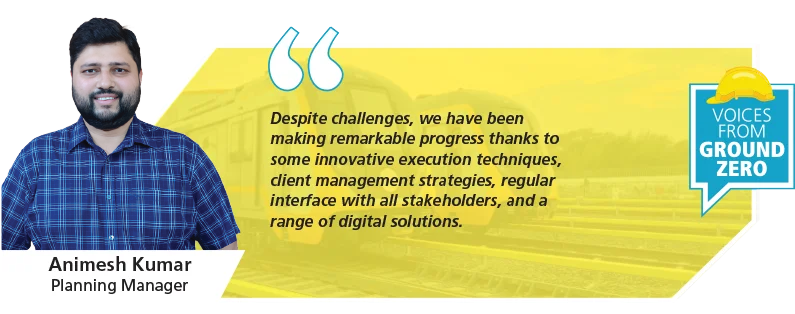
“Our milestones were extremely challenging as the civil and track works by other agencies were in progress at the same pace as ours and all the work had to be completed simultaneously,” remarks Animesh with a grimace, that called for meticulous interface and clarity of planning among the contractors. “Since this was our first third rail metro electrification job, it was difficult for us to anticipate unknown execution risks,” he adds.
“Despite challenges,” Animesh smiles, “we have been making remarkable progress thanks to some innovative execution techniques, client management strategies, regular interface with all stakeholders, and a range of digital solutions.”
Simulation of the 750 V DC Third Rail Traction System during design stage: The 750 V DC Third Rail Traction System with a 3-car configuration is a relatively new technology & configuration for the Indian Metro Industry. Understandably, therefore, UPMRC had serious reservations during the design stage about the third rail alignment and bridging gaps based on their past experiences that was delaying approvals of the third rail drawings. To address this, with the support of the Railways SBG’s EDRC team, the site team, simulated different cases with worst conditions using AutoCAD, providing customized location specific solutions to overcome the challenges which are as on date installed at site with precision. “We not only won our client’s confidence with these simulations, but could accelerate the remaining design process,” shares a happy Third Rail Expert, S Venkatesan. “Currently, along with our EDRC team we are preparing to automate the third rail layout based on inputs to further speed up the design process and automatically generate BOM based on the layout plans.”
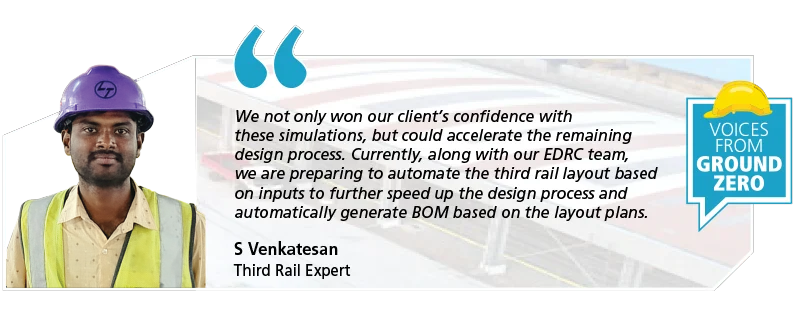
TILOS for project scheduling & interface: Proper planning & scheduling of activities as per site access, utilizing optimum resources and manpower are key to on time delivery. A cause for worry for Animesh was that their materials for the priority section were scheduled to be delivered only by January 2023 giving the team very little time to commission their first milestones. “What helped us to meticulously plan the sequence of activities along with constrains from other stakeholders easily was the scheduling tool ‘TILOS’,” says a relieved Planning Engineer, Prachee Acharya. “We can identify potential conflicts, manage dependencies, streamline workflows and optimize resource allocation far more efficiently.”
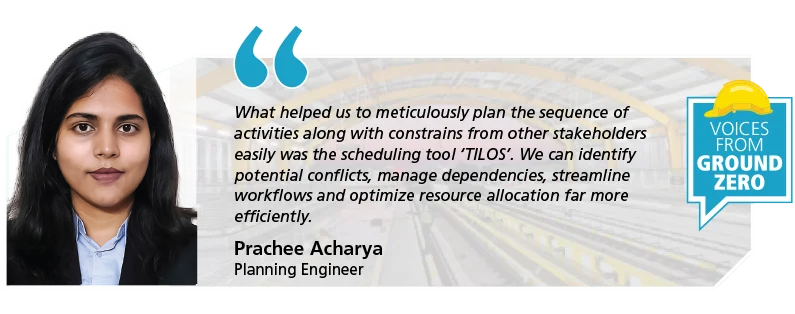
During execution, TILOS, along with a strip chart is updated daily to monitor daily progress of each activity with issues highlighted to the concerned stakeholders for prompt resolution. To keep everyone informed and on the same page, the updated TILOS schedule and strip charts are shared every morning by mail with the client, team members, and interface managers of other contractors.
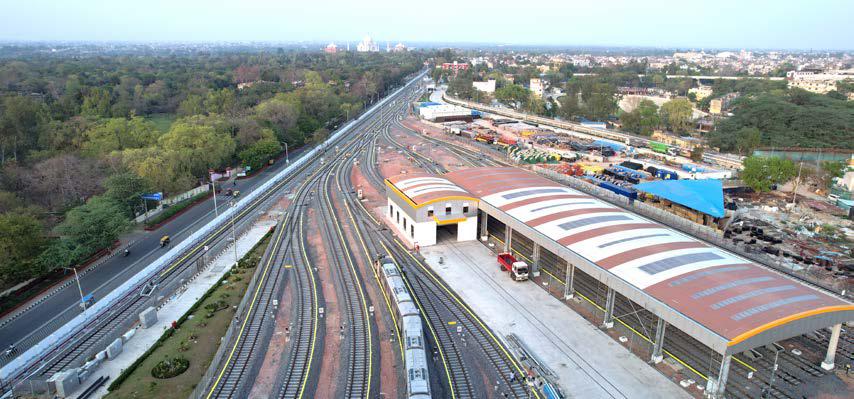
State-of-the-art depot & workshop (PAC Depot)
Real time progress monitoring with Optic Vyu: PT&D IC, executing the AC network side works for the project along with RBG team as a part of same contract, have implemented Optic Vyu App for real time progress monitoring at one of the RSS sites. “With live visual updates from site, we can view progress in a Timelapse mode. With support of the PT&D team we are planning to implement the App in all the other sections of the project,” affirms Animesh.
Establishing 24×7 connectivity in the underground sections: Portable wi-fi connections installed inside the tunnels with the help of local service providers keep the team constantly connected with the execution team in the underground sections. All information regarding progress, material availability, location of the team, problems and other critical information is being shared on real time basis.
Real-time material tracking from factory to store: Given the critical nature of timely delivery of material, a dedicated team from site is responsible to track material containers from various vendors located in the different countries, across the globe, right from dispatch from the vendor’s premises to the origin port along various sea routes to the destination port to custom clearance office in India to delivery at site stores. “Thanks to the digital advancements in the shipping industry with shipping agencies like CMA-CGM, Hapag-Lloyd, and others we can track containers real time and take proactive steps for custom clearance,” mentions TSS Expert, Amit Kumar Gupta.
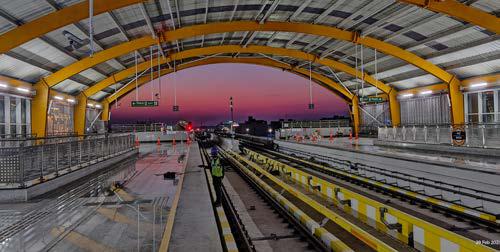
A scenic sunset at the Taj East Gate Metro Station
Pursuing Mission Zero Harm with SHEILD App & VR-based training
That the project has achieved nearly 1 million safe man hours with zero LTIs is a matter of pride for Chief Safety Manager, Shashikant Sharma. “Apart from identifying and minimizing potential risks, the SHIELD App ensures that everyone is adhering to the safety protocols and that all procedures are being followed,” he points out. All EHS observations are routed through the App with timely compliance and the team can analyse potential risks & hazards and mitigate them on its dashboard. “Recently the Railways SBG has started conducting customized Quarterly Audit Rating Score (QARS) audits through the SHEILD App for Railway projects that has standardized the audit process and created a benchmark to analyse all Railway projects under one umbrella,” informs Shashikant. Before the start of actual execution works, engineers & workers are given training in Safety using VR technology, to ensure that everyone is aware of the safety protocols.
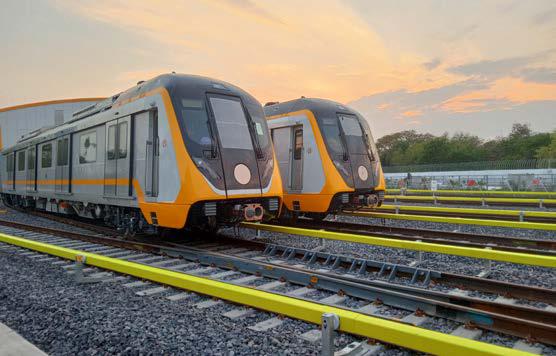
Metro using 750 V DC Traction from 3rd Rail
Vendor interface
“Recognizing the probable challenges associated with the high value imported materials, characterized by extended lead times, we decided to procure the material as soon as the project started,” informs Assistant Construction Manager (Elec), Amit Kumar Gupta, “and to speed up the process, we convinced the client officials to participate in virtual meetings with our SCM, EDRC, and vendor representatives for speedy decisions and order finalizations.”
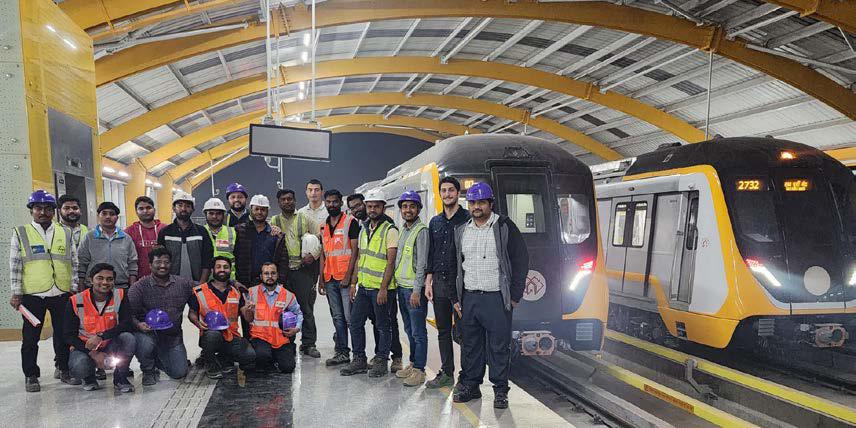
Integrated testing & commissioning works along with UPMRC, GC, OEM, and other system contractors
“Along with the TILOS schedule, prior to the initiation of work, we interfaced with contractors to create a joint construction section–wise work program for civil, tunnelling, track, electrification, signalling activities along with integrated testing of the Metro,” Animesh explains their approach. In the joint program, the expected access dates for each domain are mentioned to schedule the final commissioning date. “This program has helped us in our resource planning and to analyse and closely monitor on a weekly basis the activities that can be done in parallel with the other contractors’ teams.”
Workers are on-boarded through WISA, and with that repository of details the team can track worker attendance, mobilize & resource plan the day’s scheduled activities. Virtual Factory Acceptance Tests (FATs) are saving both time and cost in scheduling, processing, overseas travel and ensuring timely delivery of material at site, since all the major material required for Third Rail electrification comes from countries like France, Germany, the Czech Republic, Dubai, UK and others.
Digital Documentation: A dedicated document control team ensures that all the project documents and drawings are digitally stored on the cloud dataspace. Real time monitoring of design approvals speeds up designing process that are accessible to all to avoid delays in submissions and ensure timely compliances and approvals.
Currently, the project that has received ISO 45001:2018 and ISO 14001:2015 certifications from an external agency, continues to advance, with approximately 6.7 km under construction with another 17.5 km about to begin.