
Masalia Ranishwar Mega Lift Irrigation Scheme –
From parched to prosperous lands
Several districts of Jharkhand suffer from drought, leaving farmers in penury with their lands uncultivable as they solely depend on rain. The Masalia Ranishwar Mega Lift Irrigation Scheme is envisioned to transform lives by providing water to 22,283 hectares of land. The mandate to Project Manager, Srinivasakan M, and his team is to construct a 5 MCM storage reservoir with a barrage across the Siddeswari River and a lift irrigation scheme (LIS). While the barrage will feature an energy dissipation arrangement, piers, abutments, wing walls, flared out walls, barrage bays, and service & emergency stoplog gates with hoisting system of rope drum and monorail, respectively, the scope for the LIS includes approach channels, pump houses, electrical buildings, a switchyard, delivery chambers (max. capacity of 9,856 KL), and a piped irrigation network of 932 km for the 22,283 Ha of culturable command area.
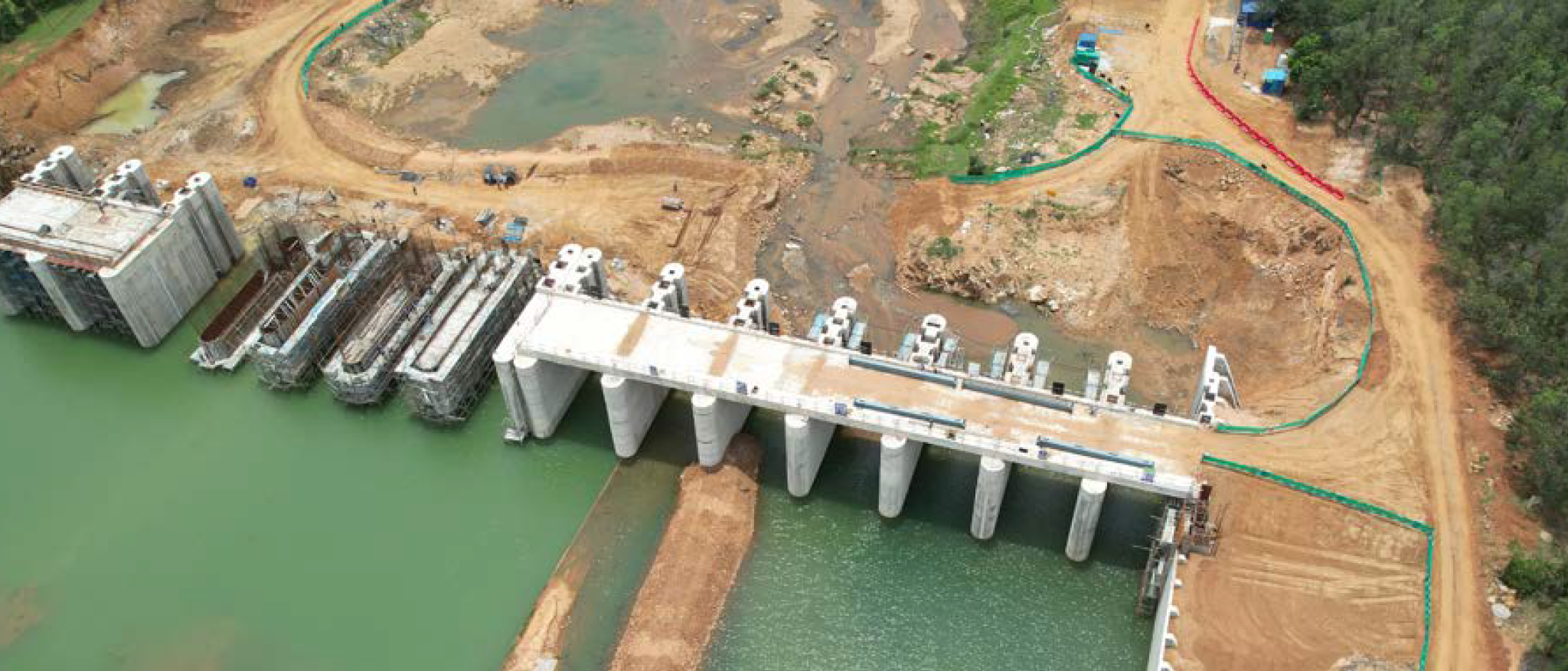
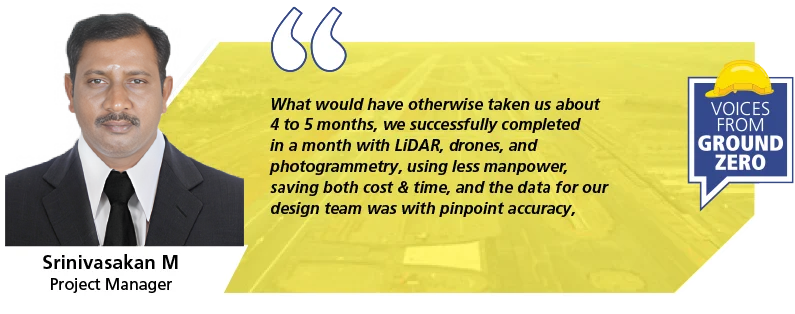
An aerial view
Surveying the entire 30,680 hectares (gross command area) with conventional methods would have been arduous, time consuming, and not entirely accurate. “A survey that otherwise would have taken us about 4 to 5 months, was successfully completed in a month with LiDAR, drones, and photogrammetry, using less manpower, saving both cost & time, with pin-point accurate data for our design team,” says Srinivasakan with a spring in his voice.
A specialized agency had pre-surveyed the environment, weather, and logistics before planning the launch sites for the
5 sq. km. flights. The flight paths and limits were fed into the RCs and managed by an experienced fleet of DGCA-approved pilots from the agency, each with over 500 hours of flying experience.
With this head start, Srinivasakan’s team forged ahead, and their progress currently stands at 67%, helped in no small measure by their several technology interventions that have even fetched them CII’s Digital Transformation Award in the Innovation category.
Fact finding
Planning Manager Vikas Vats’s primary concern is to lay a pipeline network of 932 km, with the size of pipes varying from 110 mm to 2,450 mm, traversing across multiple kinds of terrains. “To manually manage such a long network, identify gaps, and initiate immediate action would have been terribly difficult,” he shakes his head. “With the geospatial solution we have developed with LTIMindtree, and integrated, real time data is captured and readily available on dashboards; what’s more, it is easy to locate gaps and guide engineers to the exact location to resolve issues,” he smiles. All the pipelines have specific IDs that are mapped onto the dashboard.
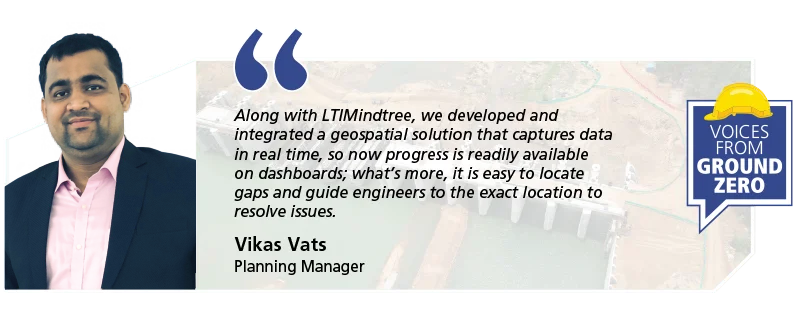
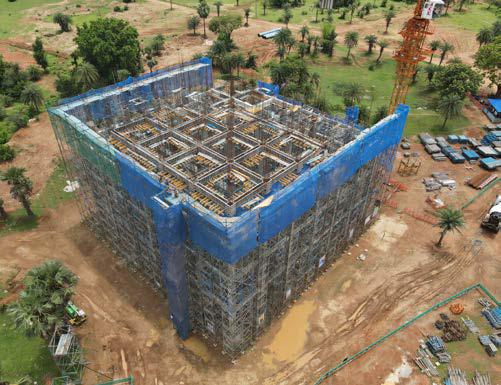
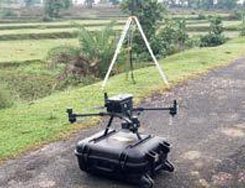
The project features 9 civil structures: 1 river barrage, 5 delivery chambers, and 3 pump houses and a batching plant, the epicentre of these 9 structures, for timely supply of concrete is critical to delivery. Traditionally, site engineers would place their requirements for concrete on WhatsApp, and as multiple requests come in from different areas of the project, the plant would find it challenging to prioritize based on need. In addition, with data being manually fed, reconciliation of production vis-à-vis supply vis-à-vis usage used to be inaccurate, with the team lacking any clear visibility of real-time progress.
“The ConPro App available to all the site engineers and the planning & project teams has changed our lives,” shares a delighted digital coordinator, Ayush Kumar Singh. “Configured to ensure need-based concrete production, it helps reduce wastage, and helps the QA/QC Manager to prioritize requests based on the real-time progress of the project.”
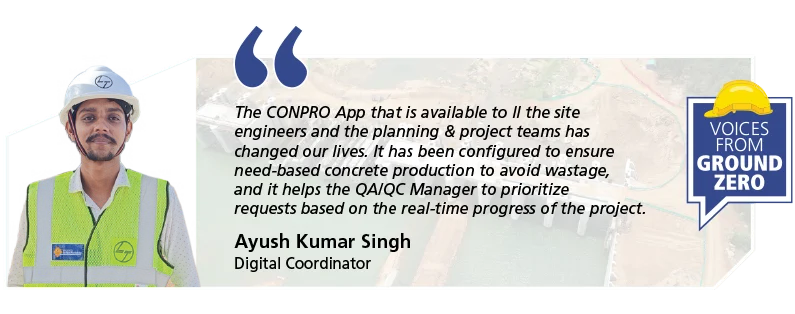
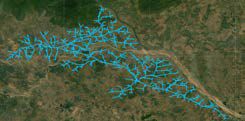
Practically, while the requirement of concrete for the barrage is enormous, that for the delivery chamber, which works only at night, is much lower. Now, with clear visibility of all the data on the ConPro dashboard, production and transportation are prioritized accordingly, reducing wastage and more efficient resource management.
Real time progress is monitored with cameras to help the team make informed interventions and decisions, saving cost, time, and resources. IoTs installed in the Plant & Machinery assets ensure their optimal utilization.
Gearing for the bountiful harvest
Srinivasakan M and team are committed to ensure that water reaches the beleaguered farmers of Jharkhand for the whole season of cultivation, and their efforts are finding new speed & vigour thanks to the technology solutions deployed.
Once commissioned, 22,283 hectares of land, which includes 17,066 hectares in the Masalia block and 5,217 hectares in the Raniswar block, should sprout paddy, pulses, and oilseeds as well as ragi and jowar-maize.
UP Tubewell Scheme – Transforming water management through digitization
Clean drinking water, so essential for quality of life, is an extremely scarce resource in several parts of rural India. Under the ambitious Jal Jeevan Mission, the Government of Uttar Pradesh (UP) aims to provide piped drinking water to over 3,300 Gram Panchayats across seven districts: Balrampur, Ghazipur, Gonda, Prayagraj, Shravasti, Sitapur, and Varanasi and one of the first projects to implement water management through automation and leveraging innovative technology to address several critical challenges in groundwater supply management.
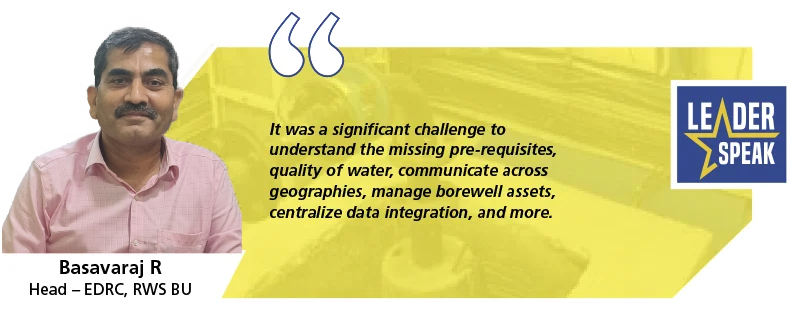
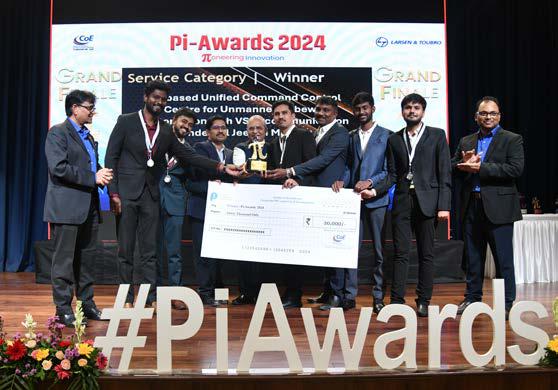
The project team at the Pi-Awards 2024
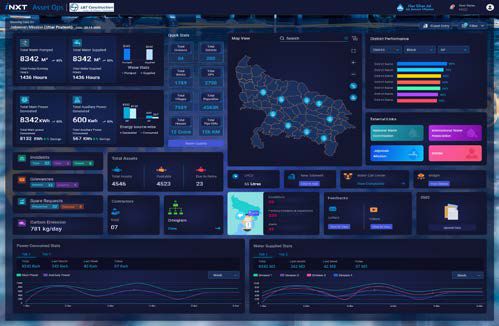
The Unified Command Control Centre (UC3 ) dashboard
Automating for efficiency
L&T has been entrusted to construct and integrate 3,000+ borewells across 7 districts of UP, including pump houses cum chlorination rooms, overhead tanks, solar plants, a RTU (Remote Terminal Unit) system, and laying the main & distribution pipeline network. “It was challenging to first understand the missing pre-requisites, quality of water, communicate across geographies, manage borewell assets, centralize data integration, and more,” prefaces Basavaraj R, Head – EDRC, RWS BU. With the number of tubewells increasing and O&M in their scope, it was imperative for the team to understand the existing supply versus demand situation.
Prathit Rameshchandra Patel, Sumit Roy, Arman Ali, Jaipal Soni, Talluri Krishna Chaitanya, Ankit Srivastava, Prateek Singh, Sailesh Kumar, and Kadhiravan from the site team are all playing pivotal roles in on-ground operations. Additionally, Murugan Babu and Devaliya Jayesh Kumar from the O&M team, under the leadership of Rajamohan K, Head – O&M, WWW SBG, ensure seamless maintenance and operations, while Srinath Badrinarayanan, Prabhakaran N, Nagendra S, Rajesh Muthuraj, and Mohd Zaid Khan from the EDRC team remain focused on design and technical integrations. Their collaborative efforts are driving the project ahead.
It called for a methodical approach involving automating tubewell operations, integrating the data using reliable technology (VSAT, or Very Small Aperture Terminal, being used for the first time) and multilevel data monitoring with a unified, AI-integrated Central Command Centre, the first such within L&T for a water project, and India’s largest groundwater automation project. Currently under construction at Lucknow, the automation is helping to monitor & control water supply from the tubewells with uninterrupted service. The hybrid data storage method leverages both on-premise servers and cloud storage to achieve optimal results.
Tech-led operations
The project integrates over 32,000 field instruments and 8.5 lakh SCADA (Supervisory Control and Data Acquisition) tags, utilizing protocols such as HART over IP, DNP3, etc. for real-time data collection. “The communication architecture, created using VSAT technology (more efficient than GPRS), MPLS, and ILL, facilitate reliable communication, remote monitoring, predictive maintenance, and data analytics,” informs R. Prasanna Venkatesh, Task Force Leader – UC3 & Dept Head – EDRC, Instrumentation – RWS North & UWWM BU.
For better control and monitoring of the Gram Panchayats, a hierarchical system has been used with operational technology and information technology, in which the system architecture is divided into five levels: 3,013 Unmanned Tubewell Control Stations, 100 Block Level Control Stations, 7 District Master Control Stations, 4 Disaster Recovery Control Stations, and a Unified Command Control Centre.
SCADA systems and real-time data management
The Supervisory Control and Data Acquisition (SCADA) systems are integrated with smart Remote Terminal Units (RTUs) at each Overhead Tank (OHT) to comprehensively monitor, detect leaks, and control the water supply system. To optimize the water flow and ensure efficient resource allocation, real-time data is collected and transmitted to the DRCS for redundancy; the data can also be viewed on tablets and smartphones.
- VSAT communication technology: VSAT takes care of reliable, long-distance data transmission, for continuous and dependable communication between the remote tubewell sites and central command centres.
- Health diagnostics and asset management: Involves health diagnostic monitoring of all electro-mechanical equipment and comprehensive asset management to improve the reliability and maintenance of the infrastructure, for prolonged operational efficiency.
- Artificial Intelligence and Machine Learning: AI and ML models are used for predictive analytics, water demand forecasting, and maintenance strategies that analyse data to derive actionable insights and optimize the functionality & sustainability of the water management system.
- Industry 4.0 and IIoT Integration: The project incorporates Industry 4.0 principles and Industrial Internet of Things (IIoT) technologies that enables smart, data-driven decision-making, and operational efficiency.
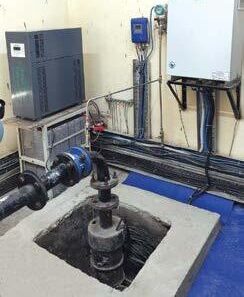
“With this seamless integration of information technology with operational technology, all that the in-charge has to do every morning is open his tab to view the dashboard and follow the processes to resolve any issue with a preventive, predictive, pre-defined, & prescriptive approach,” sums up Rajeevan K, Vice President & Chief Technology Officer – WET IC.
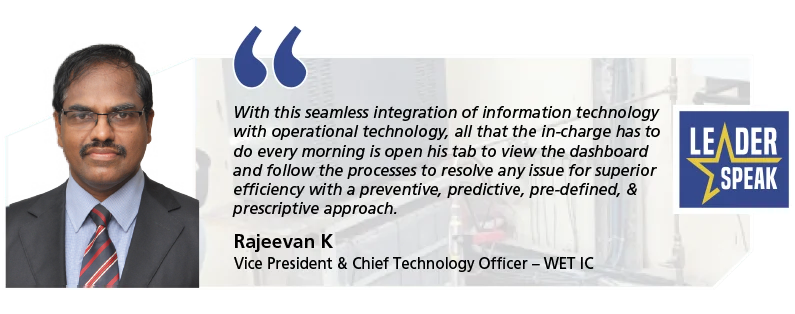
Impact and gearing-up for the future
A direct benefit of technology intervention is cost savings. “According to our data, we expect significant cost savings for the duration of the project,” opines Sudripta Misra, Head – EDRC, WWW SBG. “It will also reduce CO2 emissions by 10 lakh kilograms per year owing to a considerable reduction in transportation, apart from helping us with better water production and storage forecasting, water demand production, and water quality management.”
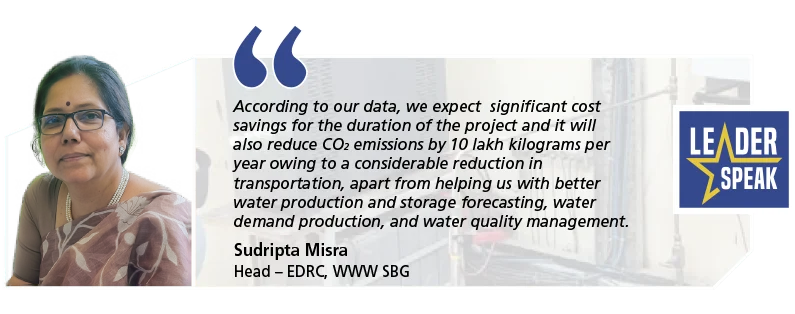
The project team has won accolades at internal Group-wide competitions like Technology Conclave IX 2023–24, Stellar Award 2024, and, most recently, the Pi-Award 2024 in the ‘Service’ category.
A sure-shot sign of its success is that the client has requested L&T to replicate the system at other water supply projects in Uttar Pradesh.
“To make our system more robust, we will be developing capabilities such as cloud server with multiple backups, integration of 75 districts’ tubewells with over 6.9 lakh field instruments, 58 lakh SCADA tags, health diagnostic monitoring of all electro-mechanical equipment, reliable wireless communication, AI integration, and a complete dashboard for Uttar Pradesh,” notes Chandraeaswaran S, Head – RWS North BU, looking ahead to a top-notch water management system of the future.
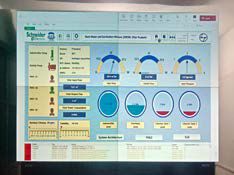
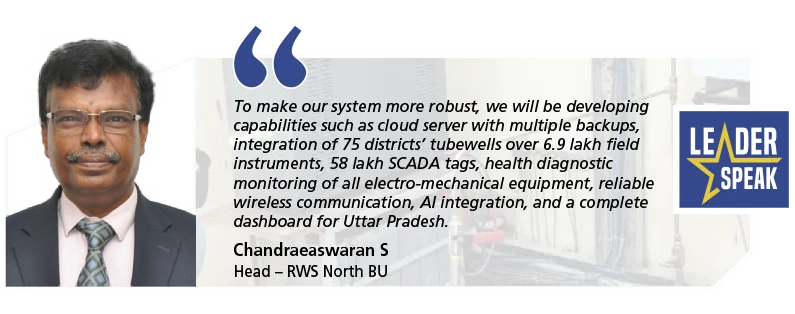
24×7 Hubballi–Dharwad DB – Transforming a complex water supply system
The Karnataka Urban Water Sector Improvement Project (KUWASIP) is a significant programme to reform Karnataka’s water and sanitation sectors, targeting Belagavi, Kalaburgi, and Hubballi–Dharwad. Since taking over on 5 December 2022, WET IC’s Operation & Maintenance (O&M) team has been implementing a range of technologies and strategies to improve the water supply system by understanding the reasons for water leakage, contamination, and irregular supply covering 1,676 km, comprising 12 municipal zones, 82 wards, and 1.4 million residents with 179,644 water house connections.
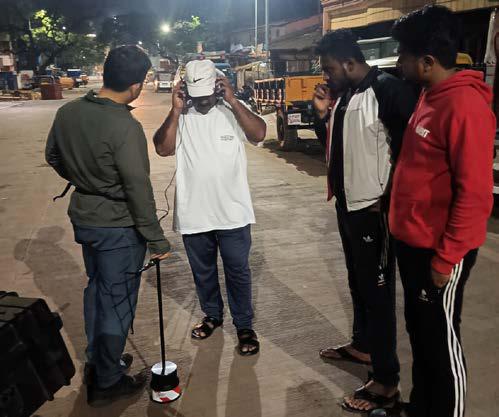
A flood of challenges
“Our job on hand is to transform the water supply system in these cities by reducing water wastage and converting the hitherto intermittent water supply (at an average of once in 7–8 days) to a more reliable and sustainable one, 24×7,” explains Hari Prasad, Project Manager.
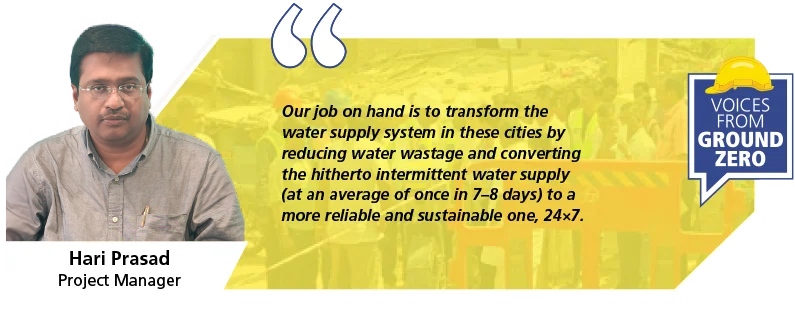
The task before Hari Prasad and team is as complex as it is challenging. Early in the piece, they realized that all the 30–40-year-old UPVC pipes had to be replaced with new ones across different regions, and that detecting leaks in the existing pipe network buried 1–2 m underground was very difficult. “Leaks often result in water contamination too with potable water mixing with the sewage or stormwater lines, so our mandate was to improve the water supply system and reduce non-revenue water – that is, water ‘lost’ before it reaches the consumer – and we are doing our best with the help of a range of technologies,” says Rajesh Kalra, Head – Non-Revenue Water.
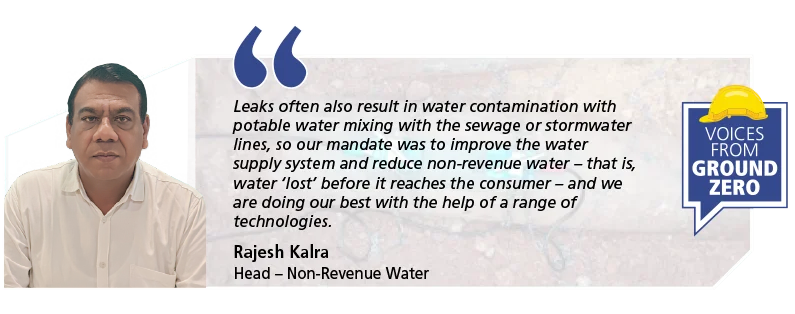
Surging ahead with technology
Portable Clamp-On Flow Metres: Ultrasonic portable clamps have been installed at regular intervals on the pipeline to identify & arrest leaks and measure the water flow & velocity at dynamic locations. “With this flexible, non-invasive device, we have thus far saved a whopping 15.62 MLD of water that is then pumped back into the system for home consumption,” shares a visibly satisfied Abhijit Das, O&M In-charge. “These plug-and-play devices can calculate water flows across pipe sizes and material,” he adds (1 MLD = 10 lakh litres of water, which can last for 7–8 months).
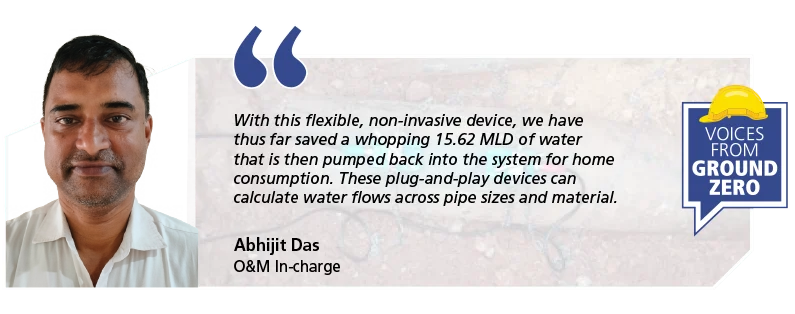
Acoustic Leak Detection Devices: Working on the method of sound, the acoustic leak detection devices travel along the pipe network to detect abnormalities by reading the sound of the water passing through the pipes. Listening sticks, ground microphones, and leak-noise correlators are installed in several parts of the pipeline where abnormlities are identified and then, after excavation, the issue identified and arrested. The team has till date saved 0.74 MLD of water in total.
Pipeline Endoscopic Camera: “Game changers in our industry, we are the first to use an endoscopic camera at site to understand the wastage and contamination problems at the Hubballi–Dharwad site better,” shares a proud Abhijeet Amnerkar, Senior Engineer. This camera goes into the pipeline to detect the exact location of and reason for a leak, and has significantly reduced water contamination. Due to the aging pipelines, many foreign bodies obstruct regular water flow which the camera detects for immediate corrective actions. “ We can detect joint damages and valve blocks, use it for micro detection in both metallic and non-metallic pipes and it has already traversed 82 km, to provide clean, potable water to about 30,000 consumers,” rounds off Abhijeet.
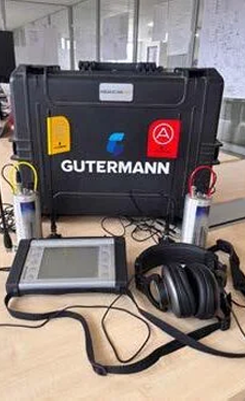
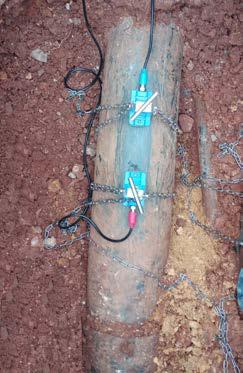
This endoscopic camera made news headlines in November 2023 when it was rushed to Uttarakhand to join the activities to save the lives of 41 miners trapped in a collapsed tunnel at the Silkyara Project. The camera was inserted into a 6-inch pipe and pushed through the collapsed rubble to establish first contact with the trapped miners after they had been trapped for 13 days. Experts refer to the introduction of the camera as perhaps the most significant step taken in the rescue act, for establishing visual contact buoyed the spirits of the trapped miners, who found new hope to hold on till they were rescued after 17 days.
Ultrasonic Level Transmitter: With the Elevated Service Reservoir (ELSR) at a height of 20 m and the container at about 5 m, pumping water up could result in overflow and wastage due to lack of visibility. “An Ultrasonic Level Transmitter installed at the ELSR alerts us when the container is filled,” informs Ramakunj Kumar, Construction Manager, “and we are now saving about 3-4 MLD water per day that was earlier being wasted.”
Online Monitoring System: Well aware of their responsibility to manage a pipe network of close to 1,800 km and ensure equitable distribution of water, the team has flow meters installed at the ELSRs, WTP inlets, outlets, and at various other identified locations to measure the quantum of water that passes through the pipes.
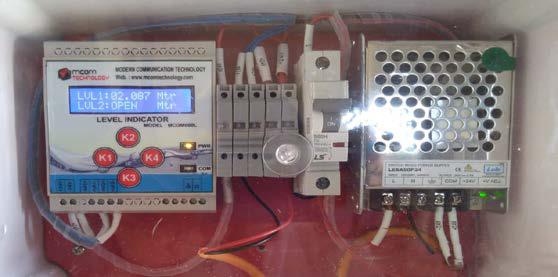
When the team took over the project, there were very few flow meters with most of them dysfunctional, making it difficult for them to assess the quanity of water passing through the pipes, a critical aspect in O&M. “Since our engineers could not travel to every location, online monitoring was the answer,” points out Syed Shahid Ali, Assistant Construction Manager. “By tracking flow and reservoir levels in real time, our downtime has reduced and operational efficiency has improved, as also our decision making.”
An example of customized action taken by using this system has been equitable water supply to the twin cities of Hubballi and Dharwad. Dharwad used to receive more supply than Hubballi, but with this system the water supply frequency has improved to 27,000+ homes across both cities, from once in 7 days to about 2 days, or daily in certain places.
Geo-Tagging and Consumer Management: This system captures the GPS coordinates of every single consumer in the twin cities to track and attend to complaints quicker. With details of all the consumers available in the system, it is easy to trace unauthorized connections, and the system has already created a database of 21,000 complaints including 42 contamination and 200 leakage-prone areas. Reading & analysing the historical pattern of the complaints is helping the team to decide and act quicker.
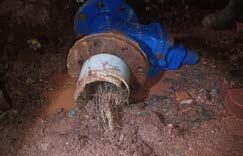
Online Customer Relationship Management (CRM) System: Rajesh agrees that keeping customers informed about the date/time of water supply or of any disruptions is a sureshot way of improving customer service. The team has captured the mobile numbers of 179,644 cosumers and fed them into the CRM to send customized bulk SMS notifications relating to maintenance or supply issues, areawise. “Consumers are now better prepared for eventualities and uncertainties,” remarks Shilpa Joshi, Customer Sevice Executive, “and they are also able to track their complaint status, manage spot billing, and make online payments using QR codes.” Additionally a 24/7 helpline number with trained personnel has been set up for consumers to reach out for any water supply–related issues. The central control room is located in Hubballi, with 3 customer care centres for Hubbali–Dharwad, Belagavi, & Kalaburgi.
Smiles for miles
Technology has certainly & significantly improved the water supply infrastructure in Hubballi–Dharwad, reflected in the smiles of the residents of the twin cities, which the team is confident will broaden as the complex project progresses to its conclusion.
360 MLD Membrane Bioreactor-Based STP, Bandra – From waste to resource
With the capacity to treat 360 million litres of sewage in a day to serve some 30 lakh people of West Mumbai, the modern Bandra Sewage Treatment Plant (STP) will be key to creating a cleaner Mumbai. India’s largest STP and located in one of the most affluent areas of Mumbai, the project team must take extra precautions to ensure low or no odour while treating the sewage. The plant will feature a rooftop garden, overlooking the spectacular Bandra–Worli Sea Link.
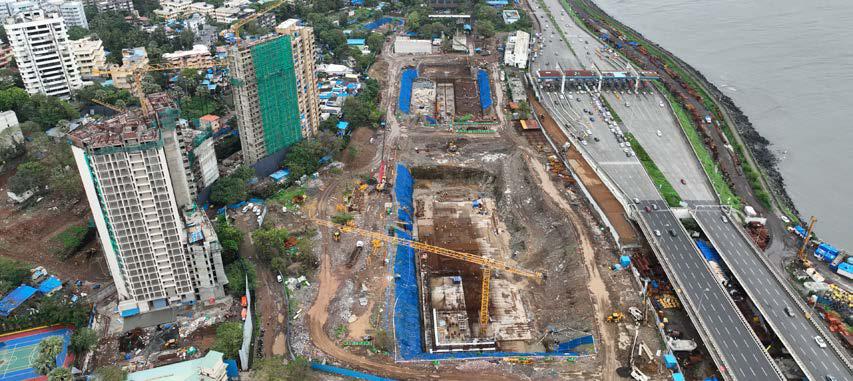
Project Director Sunirmal Pande’s objective is to produce Class A sludge that is safe for human touch and can be reused by removing the pathogens. “Our technology adoption is helping to produce quality reusable water, achieve effective sludge treatment, save energy, and optimize cost,” he remarks. “The sewage from the Mahim influent pumping station is pumped into the proposed plant and goes through various stages of preliminary, primary, biological, and sludge treatment using advanced technologies like vortex grit chambers, lamella clarifiers, Membrane Bio Filtration (MBR), UV disinfection, and TPAD (Temperature Phased Anaerobic Digestion).
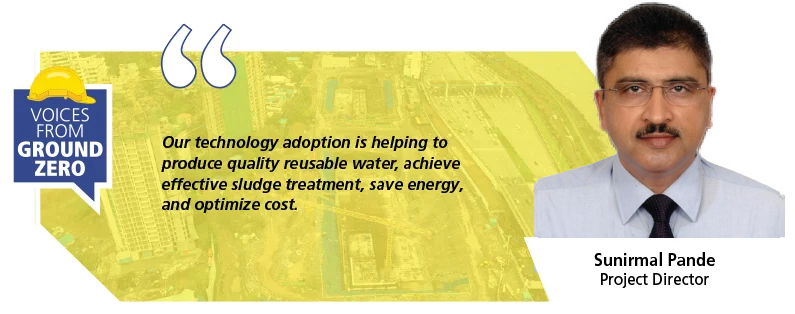
Filter and not a sponge
The sewage is first screened through the Fine Screen to remove coarse material like paper and solids above 6 mm. The screened sewage then goes to the Vortex Grit Chamber System, which consumes less energy, needs a small process footprint, and has low potential for odour. The grit tank and its inlet & outlet channels are covered and vented to the odour control unit for further treatment. The sewage that is free of sand and inorganic material then gets into the Lamella-type Primary Clarifier, where the flow rate is maintained at an optimum, and suspended solids, or sludge, settle to the bottom. This clarifier is easy to use & maintain and can absorb hydraulic shock loads. The sludge and the clarified sewage undergo further treatment through separate processes.
“Thereafter, in a bioreactor, the clarified sewage goes through anaerobic (in which phosphorus is removed), anoxic (where nitrogen is removed), and aerobic (when the BOD & COD are removed) processes,” notes Vinaya M, Chief Project Manager. “These are critical to ensure that the water is treated properly, or else green algae will start forming in the water, caused by the presence of phosphorus & nitrogen.”
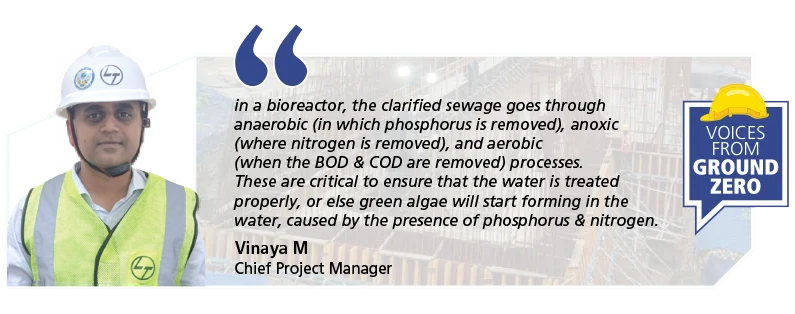
Saurabh Agrawal, Process Engineering Manager, mentions using the latest MBR technology during filtration, which has saved almost 40% space compared to a conventional reactor apart from cost. An advanced wastewater treatment technology, MBR uses low-pressure membranes to extract liquid from a suspended growth activated sludge system for high-quality, efficient, and reliable wastewater processing with a small plant footprint and economic operation.
Staying germ free
A critical step is to disinfect and free the sewage of pathogens it to be reused. “We can disinfect by chlorination, but chlorine is a hazardous chemical and storing it in the middle of a bustling city is unsafe,” points out Abhijeet N, Senior Engineering Manager. “We therefore pass the treated sewage through special UV lamps, which instantly destroys the genetic material (DNA) within the bacteria, viruses, and protozoa, eliminating their ability to reproduce and cause infection.” The UV disinfection process is chemical free, effective, safe, and environment friendly, obviating the need to transport or store it or handle toxic & corrosive chemicals. The disinfected sewage is then sent to the tanker filling station, from where the reuseable water can be transported to where it is required.
The sludge generated in the primary clarifier and MBR system is thickened through a rotary drum thickener for easy movement & downstream treatment. “To fulfil our objective of producing Class A sludge, we have in-house developed TPAD technology that uses the thermophilic and mesophilic conditions to treat the sludge,” mentions Sudhir Mishra, Senior Engineering Manager – Process Lead.
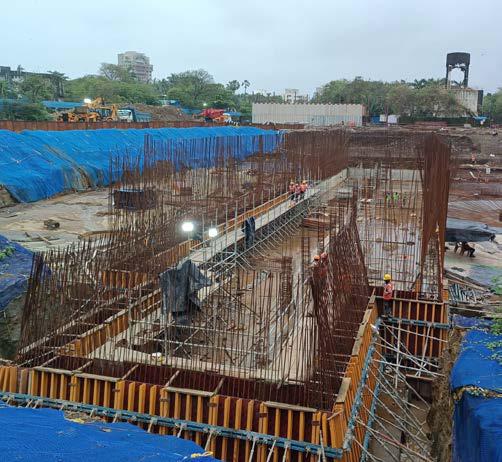
The sludge is first passed through the thermophilic digestor and treated at 55°C for 3 days to destroy all the microorganisms and pathogens. After cooling, the sludge goes into the mesophilic digestor containing mesophilic bacteria and gets treated at 35°C–40°C for a further 12 days. In the mesophilic digestor, volatile suspended solids present in the sludge get digested and biogas is generated that is further treated in the scrubber system to remove the corrosive H2S gas that can impact the life of the biogas engine if not removed. To contain the spread of odour, Odour Control Units (OCUs) are positioned at 3 strategic areas in the process, with a higher propensity of generating odour. The sludge cakes are then transported in closed tanks and disposed at an open land in Malad.
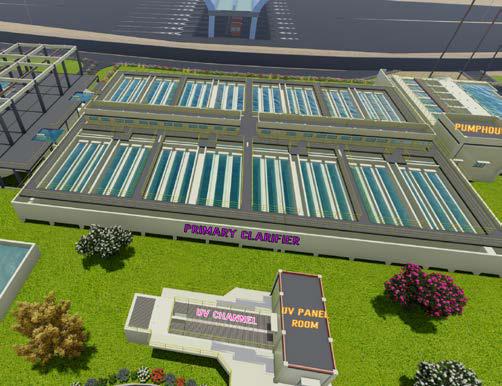
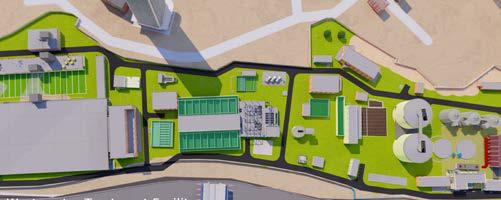
The gas generated is stored in a holder, passed through a carbon filter, and then sent to a gas engine to generate power, which will be utilized to operate the plant. Hiteshkumar Patel, Senior Manager (Chemical), smiles to reveal that 40% of the power required by the plant to operate is generated through this treatment process.
View from the top
The Bandra STP is more than just an STP plant; it is a blueprint for a cleaner Mumbai with the potential of being a knowledge hub with its fully digitalized R&D lab. Indeed, technology in WET IC is making a social and economic impact!
IOCL Gujarat Refinery, Vadodara – Towards sustainable water through recycle & reuse
Water scarcity is a major global risk due to climate change and the increasing demand from industry, agriculture, and a burgeoning population. As per a UN report, the major consumers of freshwater are agriculture (70%), industries (20%), and domestic use (12%). Globally, we consume around 4 trillion cubic metres of freshwater a year, and the demand for water is predicted to increase by 55% between 2000 and 2050. In India, consumption of freshwater by industries is predicted to be 228 billion cubic metres by 2025, which is 7%–8% of the total freshwater consumption. Water neutrality aims to reduce freshwater consumption by recycling and treating wastewater. Government initiatives promote water neutrality, requiring industries to minimize freshwater use and recycle/reuse water.
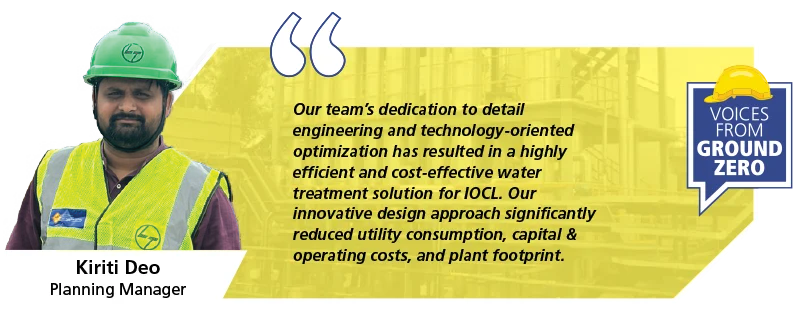
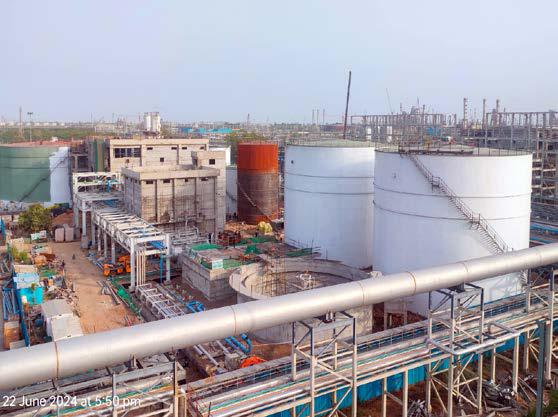
In this context, IOCL has joined hands with L&T to produce demineralized (DM) water from effluent with zero liquid discharge (ZLD) to reduce their freshwater consumption by 98%. This is L&T’s first ZLD Plant with minimum steam consumption and maximum utilization of waste generated through recycle & reuse within the plant. Balaji T K, who has recently taken over as Project Manager at the IOCL site commends the efforts of his team members Vasu K, Rajput Shivendra, and Divya S for their lead roles.
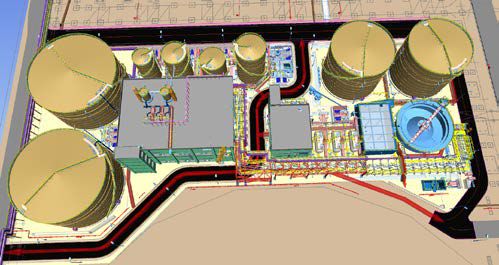
The master stroke
L&T’s winning strategy was the design optimization of the RODM (Reverse Osmosis Demineralization) and ZLD plants, to minimize power, steam, and cooling water consumption, guaranteed for a 3-year O&M period. “After extensively studying ZLD plants all over India, our process team found that most were operating at around 5 T/h/m3,” points out Divya S, Assistant Engineering Manager (Process). “We concluded that any value less than that will have the chance for competitive steam consumption. Once the strategical value was fixed, our team went all-out to get the project.”
“We prepared an extensive design in consultation with evaporator and RO membrane manufacturers and provided a steam guarantee of 4.14 T/h, which was 30% lesser compared to the competition and other bidders,” adds Rajput Shivendra Rajendra Singh, Engineering Manager (Chemical).
Feathers in the cap
This project is unique as it uses wastewater (treated effluent from ETP/cooling tower blowdown) as the source with DM water being the product that necessitates extensive pretreatment to remove contaminants like silica, TSS, TDS, hardness, BOD, and COD, that affect the performance of the system, especially the RO, evaporator, and DM water. “The team quickly came up with an idea wherein dolomite-based silica removal pretreatment & ultra-filtration system, two-pass RO, and three-stage RO recovered water up to 98%, to reduce the consumption of freshwater by 90%,” explains Shivendra. This third-stage RO was designed with maximum recovery (60%), that reduced the capacity of the ZLD plant to 23%.
Demystifying the process
RODM: In the project, the water from the cooling tower blowdown is fed to the pretreatment unit, the High-Rate Solid Contact Clarifier (HRSCC). To remove reactive silica, carbonate, and non-carbonate hardness and total suspended solids (TSS), dolomite and ferric chloride are dosed in the flash mixer before it reaches the HRSCC. The treated water from the clarifier is further sent to the DMF (a universal solvent) and ultrafiltration (UF) to remove TSS & turbidity. The UF system has a PVDF membrane with an out-in operation, to ensure good water stability. In the UF outlet, turbidity is nil and silt density index less than 3. The treated water from UF is then fed to the first-pass RO, where most of the TDS is removed and the reject water is sent to the second-stage RO system for further recovery of water.
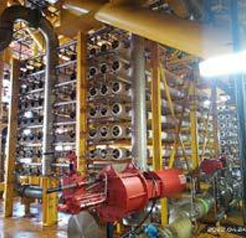
“The second-pass RO produces treated water with silica less than 0.02 ppm and TDS less than 3 ppm, and the reject is recycled back to the first-pass RO,” says Surendiran, Senior Design Engineer (Environment). Since most of the loads are removed in the RO, the product from the second-pass RO is sent to the mixed bed ion exchange to meet the required outlet DM water quality.
“The combination of UF, RO, and ion exchange treatment effectively removes the impurities, resulting in DM water of the desired quality, with silica less than 0.02 ppm and TDS less than 1 ppm,” adds Ramsankar Maji, Senior Manager (E&I) – Commissioning, who handles the critical operation automation & logic testing of the complete plant.
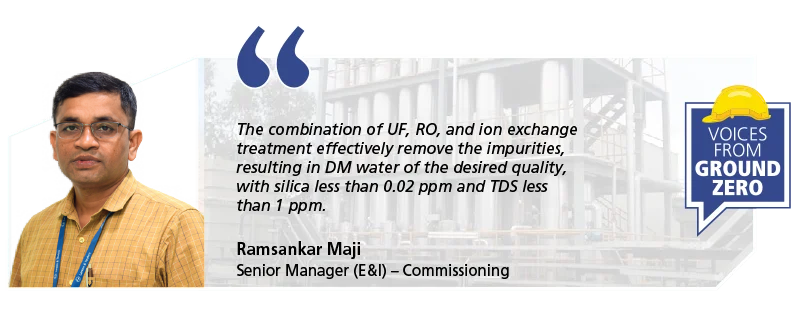
RO ZLD: TThe RO-I reject can be fed to the evaporator, but the capacity of 187 m3/h would have a cost almost equivalent to the project value. “ Our two-stage RO system with sea water membrane has reduced the evaporator feed to 24 m3/h,” remarks Shivendra, that has reduced steam consumption too, and the salt produced by the ZLD system can be further processed. For Sanjib Kumar Bhattacharya, Senior Construction Manager, the reduced area and cost of construction are reasons to smile.
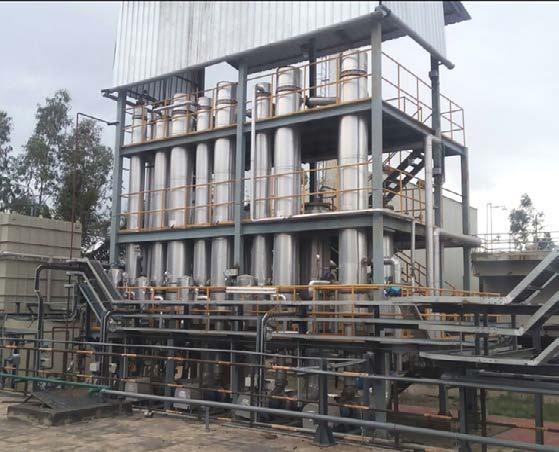
With this new process, the project team has achieved 96%–98% recovery, whereas in conventional treatment it would have been in the range of 82%–84%, according to the team of Vasu K, Senior Engineering Manager (Chemical); Prem Anand S, Chief Engineering Manager (Process); and Jaikumar K, Head – Process & Desalination.
The future beckons
“Our team’s dedication to detail engineering and technology-oriented optimization has resulted in a highly efficient and cost-effective water treatment solution for IOCL,” remarks Kiriti Deo, Planning Manager. “Our innovative design approach has significantly reduced utility consumption, capital & operating costs, and plant footprint.”
Based on this experience, the bidding team was able to provide a 2.8 t/h steam consumption for the ZLD Project for Talcher Fertilizer Limited (TFL), winning the order despite a higher capex. The ZLD technology holds immense potential for upcoming projects (Panipat, Bina, GAIL, & BPCL), with a market value estimated at around ₹1,500 crores for the financial year 2024–25.
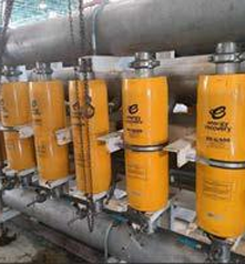
To provide the right technology to the refinery, petrochemical, textile, and fertilizer industries, a Technology Task Force (TFF) has been formed to standardize the information related to design and operations. “This project has clearly established L&T as a strong competitor in the ZLD market and positioned us well to secure future contracts in the industrial wastewater treatment sector,” signs off Kiriti with a smile.