Breaking through safely in Patna
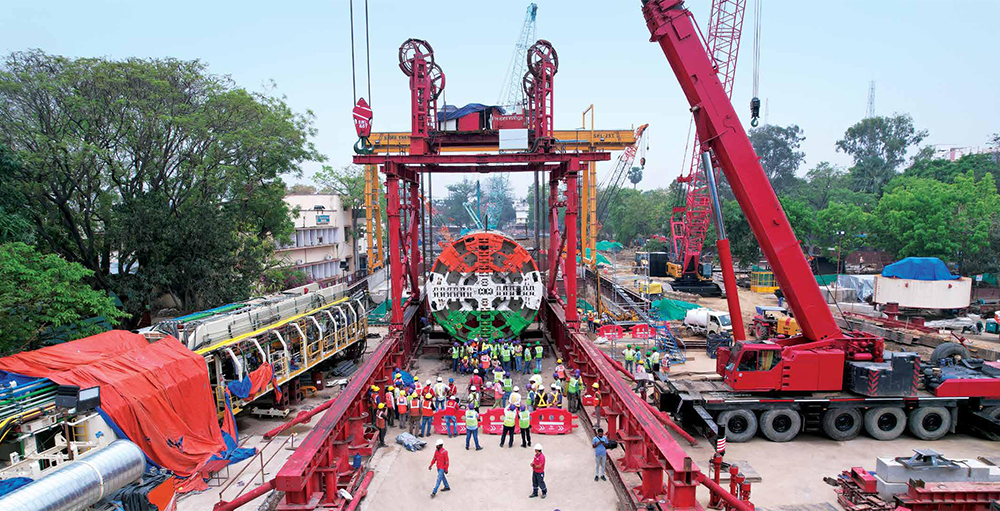
TBM erection by mega load
With space at a premium in congested cities, Metro Rail Systems are increasingly diving underground like at the Patna Metro project where L&T has been mandated to design & construct twin tunnels with Shield TBMs employing the cut-and-cover method for the client, DMRC. “The tunnels we construct play a crucial role for India’s transportation infrastructure and hence it is imperative that we prioritize safety in every aspect of tunnel construction, from planning to completion,” points out Nigel Wirtz, Head – EHS, Heavy Civil Infrastructure IC. “It is our responsibility to ensure the workers’ well-being, the smooth operation of the tunnel and careful management of the site that involves arranging various mechanical equipment, construction materials, and organizing all the necessary resources safely.”
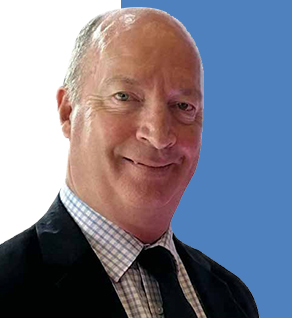
The tunnels we construct play a crucial role for India’s transportation infrastructure and hence it is imperative that we prioritize safety in every aspect of tunnel construction, from planning to completion.
Nigel Wirtz
Head – EHS, Heavy Civil Infrastructure IC
Tall challenges when digging deep
It was all systems go when work at site began in December 2021 with two TBMs in harness, but as Project Director Aloke Kumar Dey grimaces, the team encountered numerous challenges relating to the tunnel alignment. “We had to navigate around more than 900 buildings and 150 bore wells, work with loose soil strata, operate in densely populated areas that posed significant risks like working in confined spaces with high temperatures and humidity, face the threats of release of unknown hazardous gases, locomotive movement, and poor illumination.”
Perfect coordination with various teams and stakeholders ensured seamless communication and collaboration empowering the team to address any issues promptly without delays. I also oversaw compliance with regulatory requirements, quality standards, and safety protocols, to foster a culture of excellence and safety on site.
Aloke Kumar Dey
Project Director
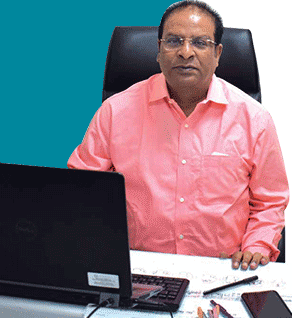
Aware of the risks involved, Aloke and his team implemented a comprehensive safe system of work, meticulously preparing work methodologies, conducting risk assessments, and developing tunnel plans that adhered to set standards and procedures for tunnel safety, such as BS6164 and applicable Indian standards. “In addition, we plugged and relocated bore wells, conducted building surveys, and installed monitoring devices along the tunnel alignment that we checked daily to ensure early detection of any potential issues,” adds Suresh Babu, Deputy Project Manager – Tunnels.
The primary task for Project EHS Head, Farid Khan, was to regularly monitor that the EHS requirements were being met throughout the tunnel construction. “To respond to any potential emergencies, we installed firefighting equipment, communication and ventilation systems on the TBMs and throughout the tunnel, apart from gas and temperature monitoring devices on them for continuous monitoring, complemented by manual checks every four hours.” Supporting his efforts was EHS Manager, Bibhuti Kumar Shukla, who conducted risk assessments, implemented safety protocols, and provided essential training to safeguard workers’ health and safety.
To respond to any potential emergencies, we installed firefighting equipment, communication and ventilation systems on the TBMs and throughout the tunnel, apart from gas and temperature monitoring devices on them for continuous monitoring, complemented by manual checks every four hours.
Farid Khan
Project EHS Head
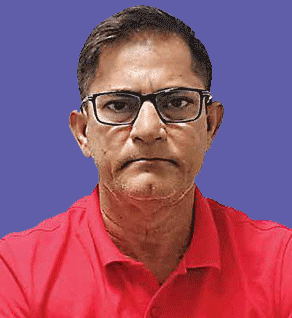
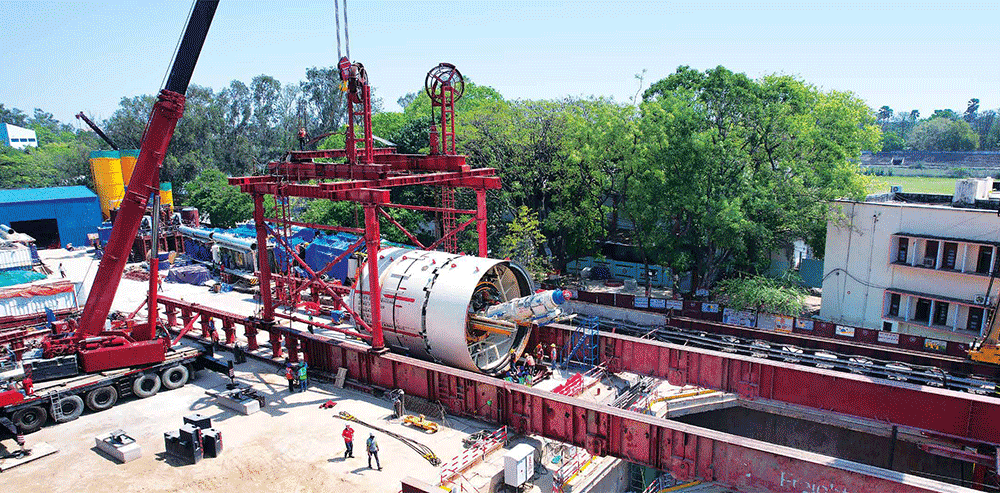
Mega load lowering tunnel boring machine
Leadership and teamwork are keys to success
There is no doubt that Aloke’s strategic direction ensured that the project goals aligned with organizational objectives helping the team stay focused, manage their resources efficiently, stay within budget and on schedule. “Perfect coordination with various teams and stakeholders ensured seamless communication and collaboration empowering the team to address any issues promptly without delays,” Aloke remarks. “I also oversaw compliance with regulatory requirements, quality standards, and safety protocols, to foster a culture of excellence and safety on site.”
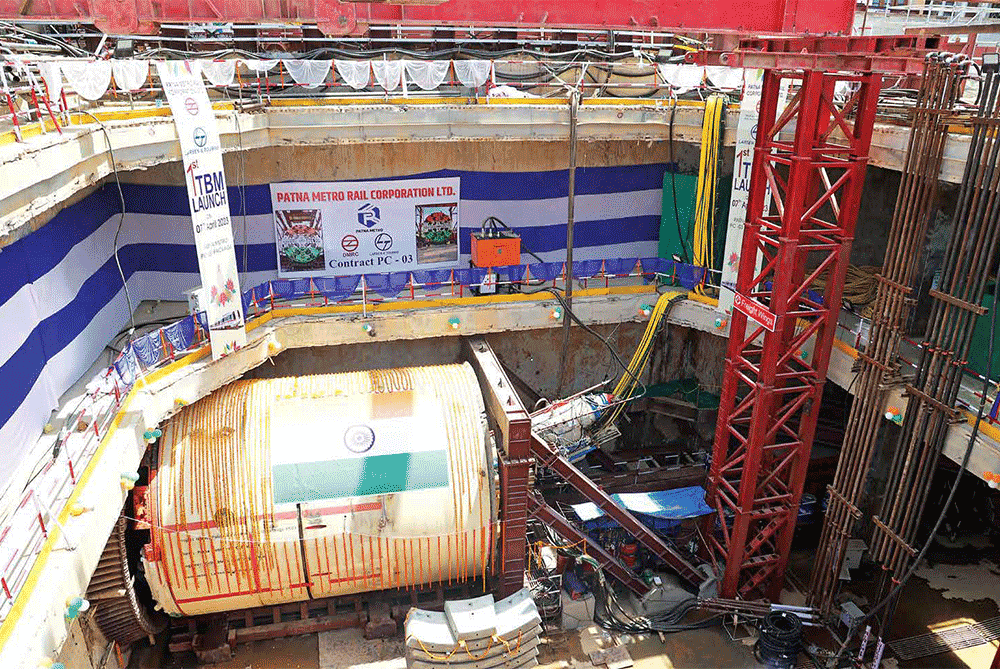
TBM launching
Suresh Babu was more granular when overseeing the implementation of detailed project plans, monitoring progress, and adhering to schedules and budgets. “Thanks to our seamless communication between the project teams, contractors, and stakeholders, we promptly addressed all issues, maintained progress, and ensured compliance with safety, quality, and regulatory standards,” he mentions.
Thanks to our seamless communication between the project teams, contractors, and stakeholders, we promptly addressed all issues, maintained progress, and ensured compliance with safety, quality, and regulatory standards.
Suresh Babu
Deputy Project Manager – Tunnels
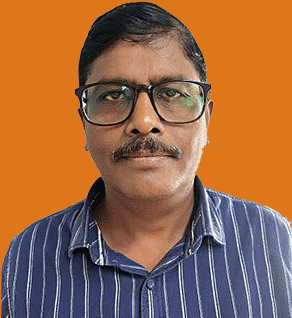
As Tunnel Operations Head, Vishnu Reddy’s responsibility was to oversee the technical and operational aspects like managing the deployment and maintenance of specialized equipment and supervising the workforce to maintain high productivity levels. “We implemented stringent safety protocols and monitored compliance to safeguard the well-being of the team and the integrity of the construction process,” he says purposefully.
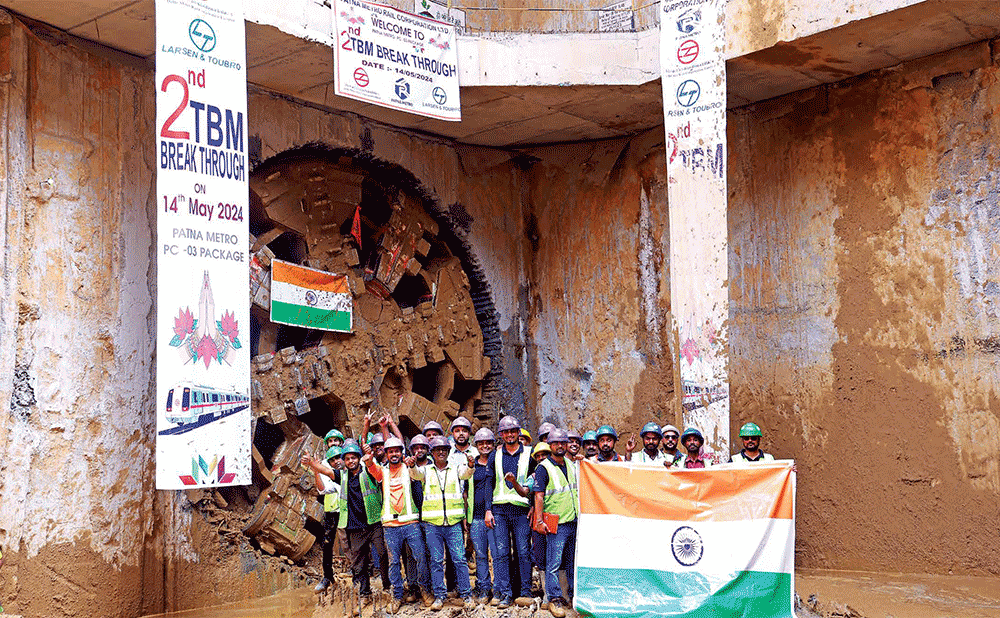
Tunnel breakthrogh
Ensuring the safety of workers
All workmen were inducted before commencing work in the tunnel undergoing thorough screening tests, pre-joining medical tests, and safety induction training including safe work procedures, tunnel safety requirements, awareness of mandatory PPEs, emergency procedures and evacuation plans, to ensure their competence and awareness of safety protocols. Farid stresses that all employees including those of the sub-contractor employed as workers, drivers, operators of lifting appliances and transport equipment were medically examined before employing. All the mandatory and job specific PPEs were ensured for the tunnel construction and the site had an occupational health centre too.
Maintaining safety as top priority
A biometric access control at the tunnel prevented unauthorized entry and the Tall Board system ensured that only those required entered the tunnel in manageable numbers, enabled head counts using a log system and was used as an emergency control room equipped with telephone, emergency contacts, first aid, etc. Hazardous gases were monitored
24 hours with inbuilt gas monitors on the TBMs in addition to manual monitoring of gas and temperature at intervals of
4 hours. Ventilation in the tunnel was through a 1.2 m dia. duct that ran throughout while return velocity was recorded by an anemometer.
To fight fire, there were extinguishers of ABC type on the TBMs, locomotives, man riders, at the bottom of the shaft, near the hoist & transformers at every 30 metres inside the tunnel. 30 m long standard hose reels were fixed at every 50 metres
(as per BS 6164-clause 13.4.2). First Aid boxes and stretchers were readily available at the bottom of the shaft, the TBM operators’ cabins, locomotives, and Tally Board. An intercom phone system was set up at every 100 metres inside the tunnel, with the emergency contact numbers displayed near them.
The movement of locomotives inside the tunnel was controlled by a Manchester Gate while an associated system with signals helped the locomotive operators, especially when two locos were running inside the tunnel. As SOP, a locomotive had to be fitted with adequate lighting, a loud, audible warning device, a braking system capable of stopping a fully loaded train, a Dead Man Switch, fire protection system, a speedometer, and a camera.
Last but certainly not least was training and briefing the workers to safely evacuate in an emergency. “Emergency layouts and evacuation procedures were displayed while a siren warned the workers to leave the workplace via the nearest escape route,” mentions Farid. “In the event of fire or heavy smoke, or gas leak or oxygen deficiency, workers could use the Self Rescuer, walk quickly or evacuate with the man rider and exit the tunnel.”
With so many safety measures in place, it is hardly surprising that Aloke and his team safely achieved TBM breakthroughs without incident; the first on 20 March 2024, followed by the second one on 14 May. With some distance to travel before completion, they have an enviable EHS reputation to protect.