Building on the power of Safety
The Paschimanchal Vidyut Vitran Nigam Limited (PVVNL) are gungho about their RDSS Saharanpur project that PT&D IC’s UPD BU is executing for they believe that with it, they can reduce AT&C losses, eliminate ACS-ARR gaps, upgrade infrastructure performance, improve consumer services, hours of supply, corporate governance, and more, in the districts of Saharanpur, Muzaffarnagar and Shamli of Uttar Pradesh.
With a lot at stake, Project Manager, Sanni Bhushan and his team’s scope of works involves armored LT cabling in high loss areas, replacing service cables, LT AB cabling works, feeder bifurcation (11 kV line), reconductoring 33 kV & 11 kV lines, AG feeder segregation, laying a new LT Line on ACSR Weasel, erecting distribution transformers, control room extension and commissioning works. “The project targets to improve operational efficiencies and financial sustainability by providing resultlinked financial assistance to DISCOMs to strengthen the power supply infrastructure,” says Sanni, highlighting the critical nature of his project.
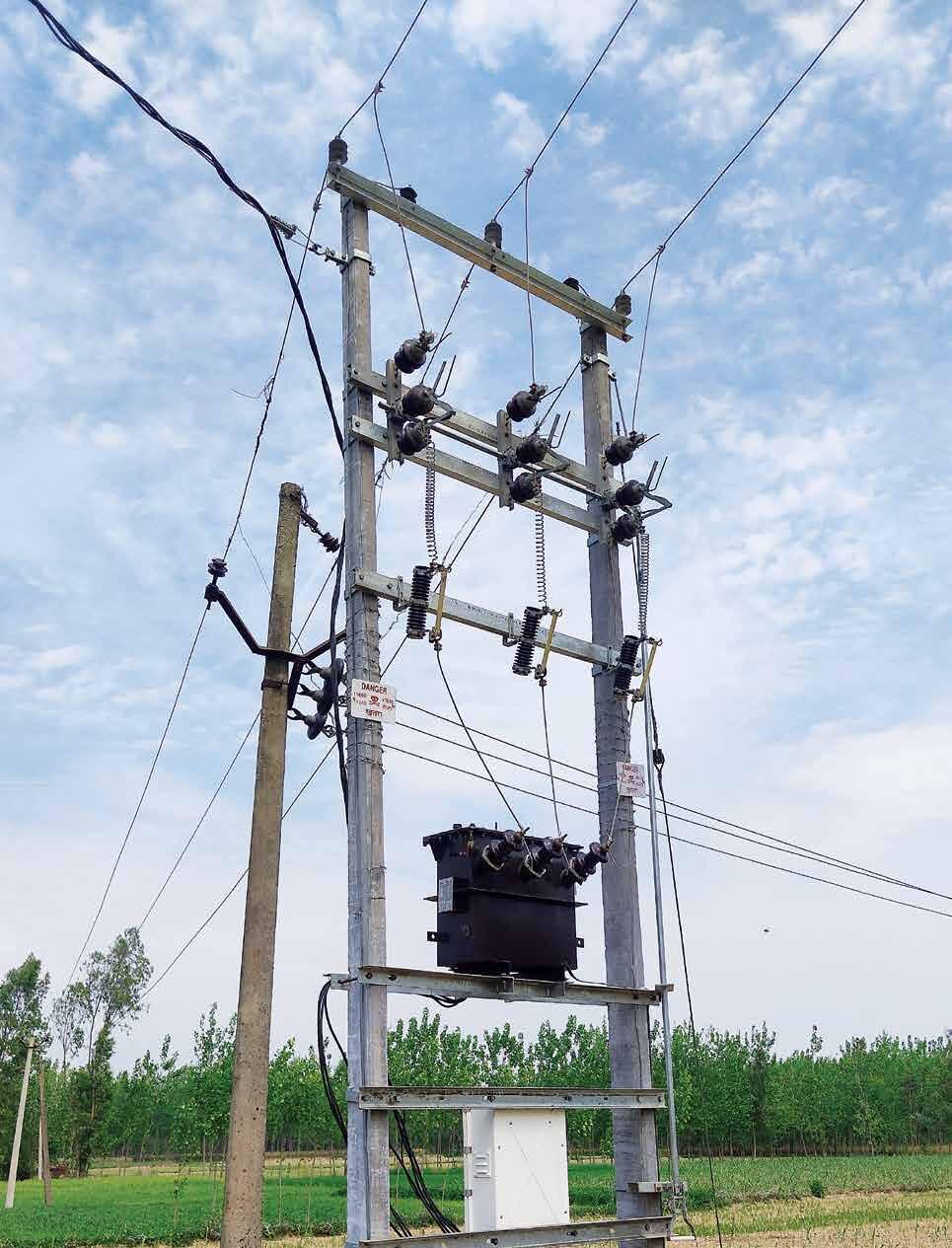
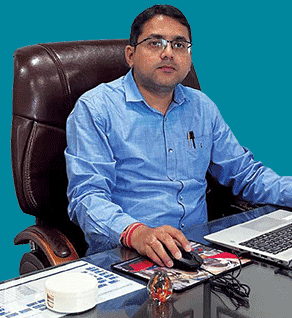
In all quarters of every financial year, we have achieved audit scores of 85%+ in all internal audits, our internal KPI score is more than 87% in each month in the last financial year and these numbers tell a story about our commitment to Mission Zero Harm.
Sanni Bhushan
Project Manager
Overcoming tall hurdles
Making sense of the complex multiple electrical circuits of the three districts was the team’s first challenge during the initial survey. “Our action plan was to understand the circuits of each of the existing feeders along with PVVNL officials before starting execution,” apprises Sanni, even as detailed survey drawings were being prepared. A complex existing overhead multiple electrical circuit running in all the three districts had to be first shut down for the team to execute, for which they implemented robust safety procedures. Daily ROW issues with landowners and local villagers remained a perennial headache too.
With the work locations scattered across the three districts and the workforce from different backgrounds with prior experience of having worked with unorganized companies or small subcontractors, the big challenge for EHS Incharge, Tarapad Pramanik, was to create awareness among his 400-odd employees and workers about safety in UPD related work. “We set up and are implementing a stringent EHS management system,” he shares with steely determination, “all new workers are thoroughly EHSinducted, they are given frequent training in Behaviour-Based Safety, and their EHS performance is monitored for us to understand their behaviour towards adopting our EHS culture.”
We set up and are implementing a stringent EHS management system. All new workers are thoroughly EHS-inducted, they are given frequent training in Behaviour-Based Safety, and their EHS performance is monitored for us to understand their behaviour towards adopting our EHS culture.
Tarapad Pramanik
EHS In-charge
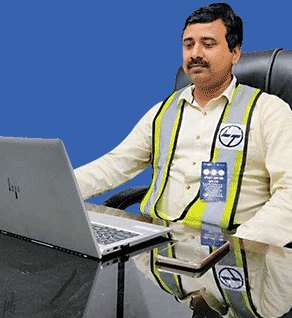
Ticking all the safety boxes
Both Sanni and Tarapad are happy that their site has already clocked 0.7 million safe manhours and all their high-risk tasks have been safely executed. Here are a few reasons for their success.
Training programmes on HIRA, SOPs of work activities, Behaviour-Based Safety, defensive driving, e‑learning trainings, VR trainings, electrical safety competency, and others are being conducted as per the training calendar after identifying training needs of individuals, including HIRA for each work activity.
Pre-Task Plan (PTP) is strictly implemented for Shutdown and NonShutdown works. For shutdown works, line survey and preparation of PTP is done 60 hours prior to execution and for non-shutdown works, 18 hours prior to execution, that are then uploaded in the SHEILD App by the Site Engineer for the Section In-charge’s and EHS In-charge’s approval. Anticipating sudden client pressure to urgently complete a critical task, the team has evolved Emergency Shutdown and Non-Shutdown Pretask plans. “We have implemented and are following dedicated Permit to Work (PTW) systems too,” adds Tarapad.
Several recent technologies have been introduced to protect workers from electrocution like HMIT, pen type induction testers, HV testers, 11 kV grade rubber gloves, FRP ladders, LOTO at main isolation points, LOTO of MCBs at the consumer’s premises, shorting and earthing of existing HT & LT UG cables and HT & LT bushing of existing distribution transformers using heavy duty shorting clips to prevent back feed. “In addition, we are putting extra discharge rods near the work area and on metal structures of GOS & DTR to leak current to the ground in our safe work zone,” mentions Tarapad, adding that the team has completed 5100+ safe shutdowns in the project and a newly introduced OTP system gives the team control over unauthorized shutdowns.
Apart from prompt distribution of appropriate PPEs & safety gadgets, the team follows a four-color token system for their workers, depending on job skills: Red for workers at height during shutdown; Blue for those on the ground during shutdown; Green for workers at height during non-shutdown; and Yellow for those on the ground during non-shutdown.
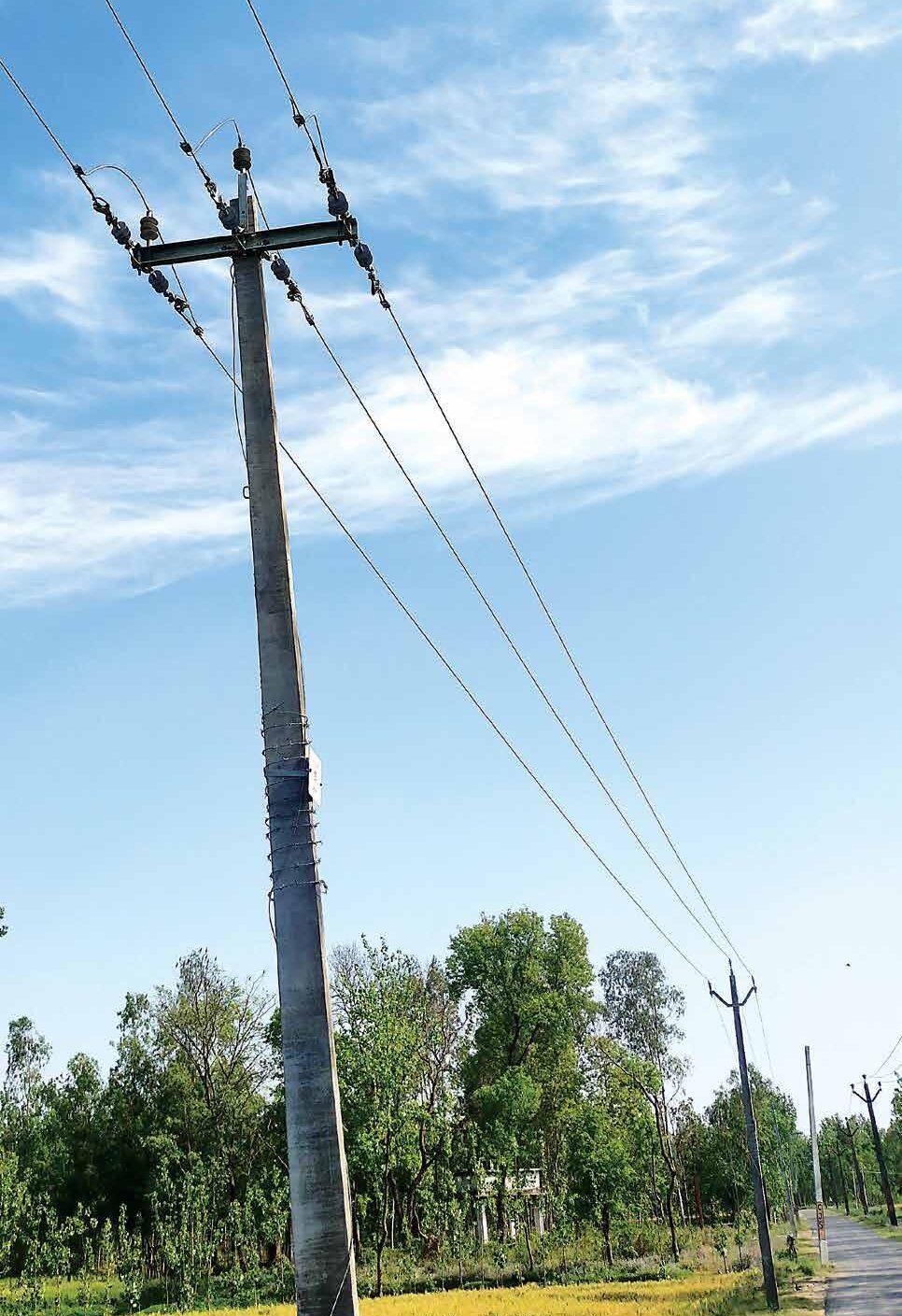
Reporting: The team’s Daily EHS Reports comprise all the checklists, permits, attendance reports, token issuance forms, etc. that are strictly followed by the site engineers and supervisors while regular EHS audits are conducted cross BUs, internally including some surprise ones as well. “Weekly EHS walkdowns by the EHS committee and client representatives reveal the management’s commitment to safety,” asserts Sanni. “We have weekly EHS committee meetings with the project team and sub-contractors’ representatives to ensure that all are on the same page about the project’s EHS needs.”
As pole pit excavations & pole erections are executed using pole master machines fitted with augur, there are chances of workers going near the rotating augur to clear excavated soil. “To alert them, we have installed a hooter in the pole master as an engineering control to alert working gangs not to go too close to the augur when it is in operation,” explains Tarapad. “Once the augur starts rotating for pole pit excavation, the hooter will sound a siren that stops only when the augur stops.”
Driving safety through digitalization
The SHEILD App is widely used for incident reporting, Virtual Reality training for staff, supervisors & workers for 360* active learning and WISA to efficiently onboard workers. “A GPS enabled Safe Start and Safe Stop communication authorizes the site engineer to permit the sub-contractor at site to start working safely and the latter will not be allowed to work after receiving a safe to stop message,” flags off Sanni. “The GPS location helps to identify the exact location where the work is being carried out by the subcontractor’s workers.”
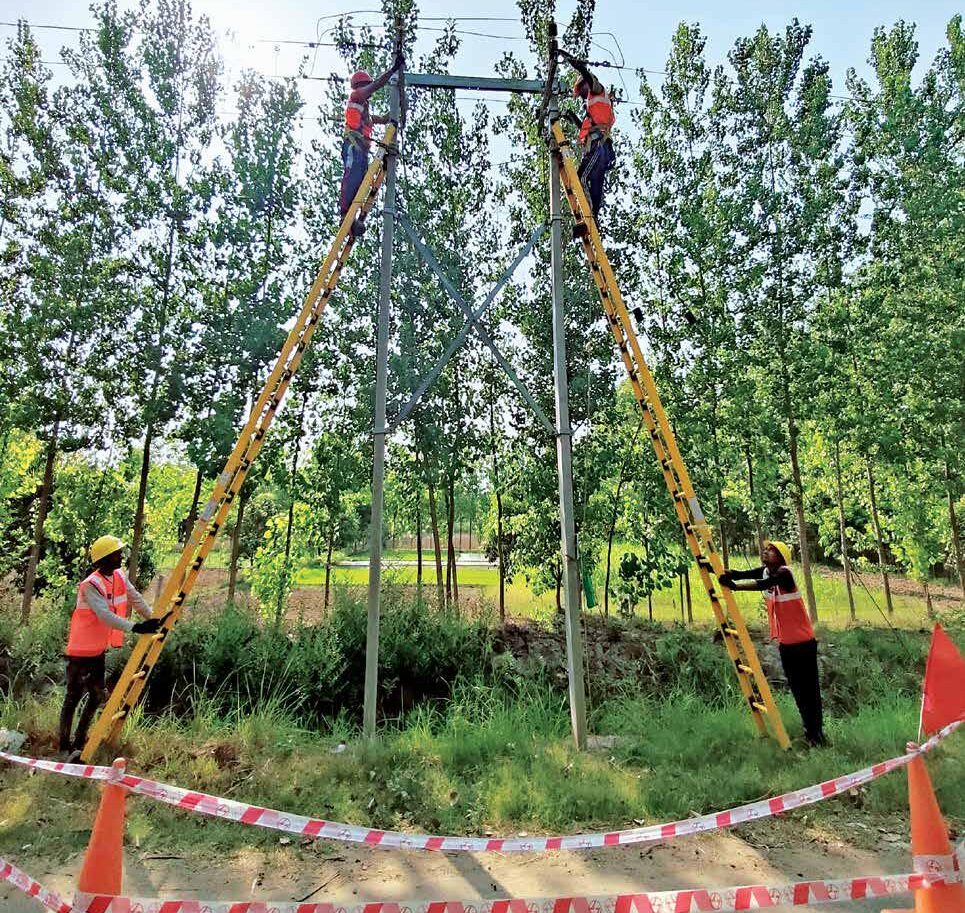
Despite facing multiple challenges like frequent pressure from the client to complete work on time, limited time to complete shutdown works, frequent changes of workers, ROW issues and more, Sanni, and Tarapad have reason to smile about their progress. “We have successfully completed 2 internal cross BU EHS audits, 2 surprise audits with minor NCRs and observations and the customer feedback has been Excellent,” enthuses Sanni. “In all quarters of every financial year, we have achieved audit scores of 85%+ in all internal audits, our internal KPI score is more than 87% in each month in the last financial year and these numbers tell a story about our commitment to Mission Zero Harm.”