Cabling safely across the world’s highest railway bridge
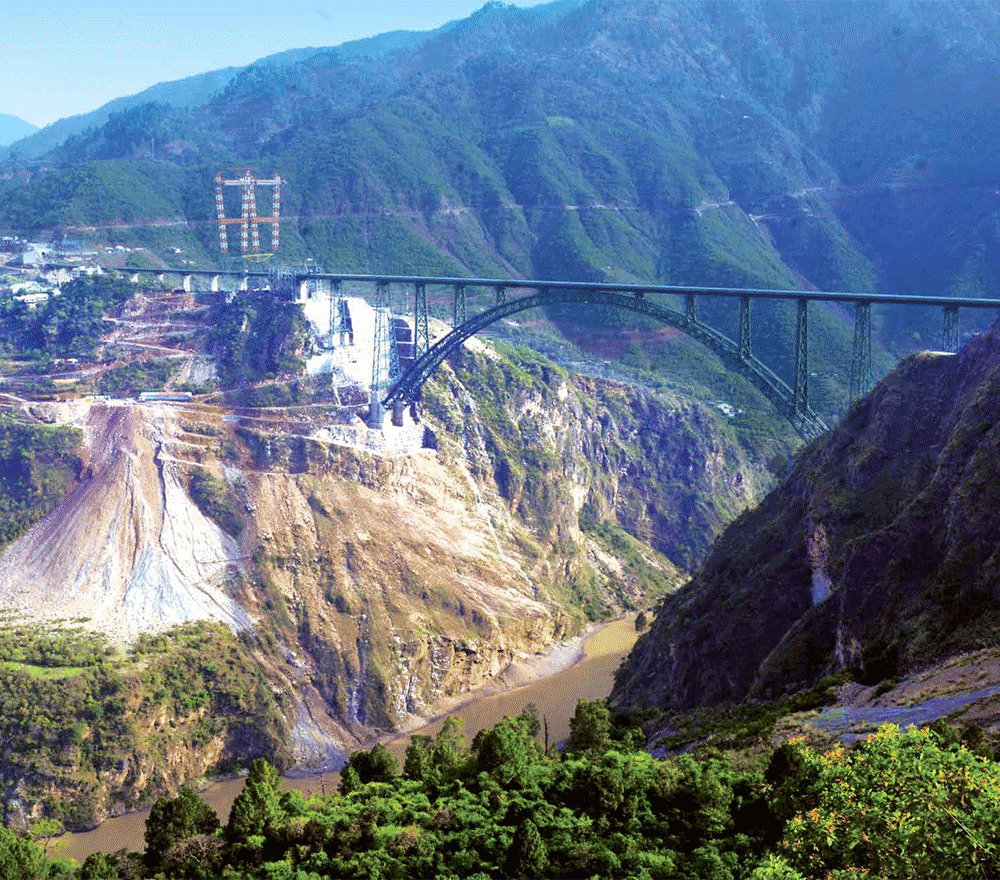
Certainly, our holistic approach to both safety and quality in every aspect of execution is our secret of success.
Nandalal Chandra
Project Manager

Perched at a height of 359 m (1,178 feet), atop the world’s highest railway bridge, the 1.3 km Chenab Bridge, also known as the Chenab Arch Bridge, spanning the Chenab River, EHS In-charge, Sanjeev Kumar has his work cut out to keep his people safe at this extremely challenging project. However, both he and his Project Manager, Nandalal Chandra, have reason to be delighted with their EHS performance, having clocked 1+ million safe manhours as of April 2024 and the slew of EHS awards they have won till date including the British Safety Council Award in 2022, the Gold Award from the World Safety Organization in 2023, the L&T Construction Quality Award and 1st Prize in PT&D IC’s Rolling Trophy competition, both in 2023.
Handrails on the walkway, guardrails on the working platform on the cable passageway, mandatory full-body harnesses, and strict supervision of all the safe work methods keep our workers safe.
Sanjeev Kumar
EHS In-charge
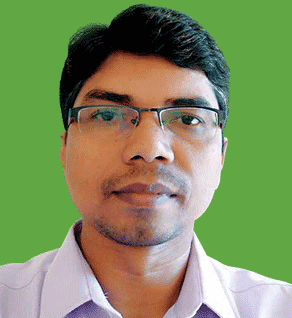
Mandated to execute Package‑3 of the Udhampur–Srinagar–Baramulla Rail Link (USBRL) for the Konkan Railway Corporation Limited (KRCL), work commenced at the remote site in August 2020, involving various tasks such as supplying, erecting, testing, and commissioning power cable networks and gas-insulated substations and, notably, laying cables across the Chenab Bridge.
A hazard known is a hazard solved
Apart from addressing the logistical hurdles of constructing on a hilly terrain, mobilizing skilled workers, maintaining communication inside tunnels, and coping with extreme weather conditions, working at height is one of Sanjeev’s chief concerns. “Handrails on the walkway, guardrails on the working platform on the cable passageway, mandatory full-body harnesses, and strict supervision of all the safe work methods keep our workers safe,” explains Sanjeev. With not enough headroom, workers are forced to crouch when working. The team’s Hazard Identification and Risk Assessment (HIRA) plan, developed by the technical team, has identified and devised strategies to mitigate potential hazards associated with work at height, handling & pulling the 33 kV cable across the bridge, and combating adverse weather conditions. Their comprehensive SOPs lay down clear instructions on equipment usage, handling of emergency protocols, and communication procedures, which are standing them in good stead in their efforts to lay cables across the cable-stayed Anji Khad Bridge, another railway bridge in the USBRL line.
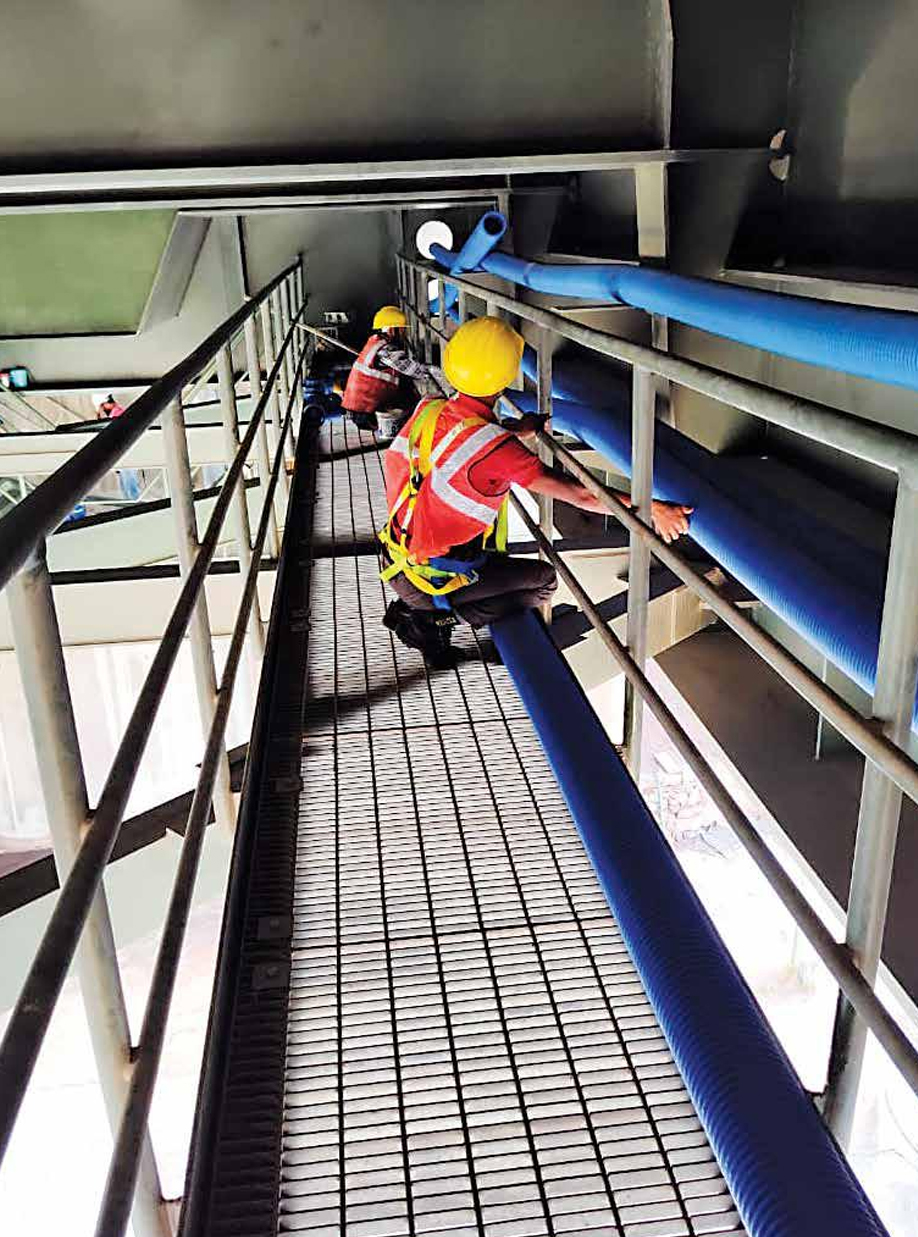
With not enough headroom, workers are forced to crouch when working
Risk factors are further mitigated by engaging workers for specialized tasks, who possess previous experience of bridge construction, while a team of engineers including the Site P&M In-charge conduct daily pep talks & specific work briefings.
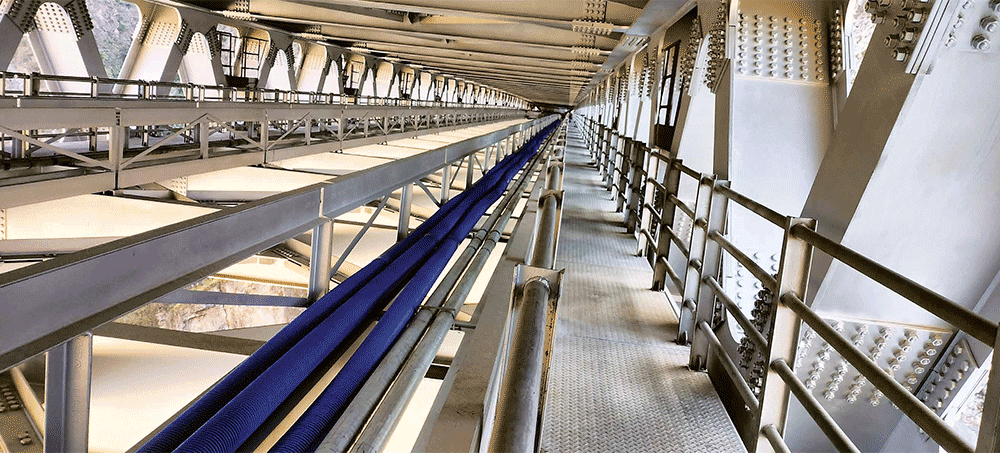
Not just height, length is a challenge too
Laying 4 km of 33 kV cable on a bridge and working inside confined spaces are not easy, as the team discovered, having to deal with drums containing 500 m length of cable that require a 1.5 km long winch rope placed in the double wall corrugated (DWC) pipe several times by using a cable duct roller. “Since traditional winch machines could not fit into the limited space, we used a portable 5‑ton capacity winch machine that had to be manually moved part by part inside the bridge,” Sanjeev shares. Since the portable machine could not be permanently fixed to the bridge structure, the team ensured the stability of the winch by using a channel and angle-bolting the machine to the structure of the bridge.
Transporting the necessary equipment and the 33 kV cable drum that weighed almost 10 tons (cable dia. 106 mm, with a weight of 18 kg per metre) was another challenge considering the rugged ground conditions and the unpredictable weather. The team’s practical solution was to earmark a specialized location to dump the cable drums near the bridge point to streamline operations and ensure smooth progress. Sanjeev adds that the drums were transported on a hired vehicle that was modified as per the drum size with a proper locking system driven by qualified drivers, strictly following all P&M SOPs.
Training sessions constantly keep workers aware of safe working procedures. Nandalal mentions the deployment of digital apps like SHEILD for real-time analytics and monitoring EHS performance. “Through the digital dashboard, we can quickly identify and address potential hazards, which is helping us maintain a safe work environment and improve productivity,” he remarks.
The challenges are tall for Nandalal, Sanjeev, and their team, but made of stern stuff, they are more than prepared to deliver as committed. “Certainly, our holistic approach to both safety and quality in every aspect of execution is our secret of success,” smiles a proud Nandalal.