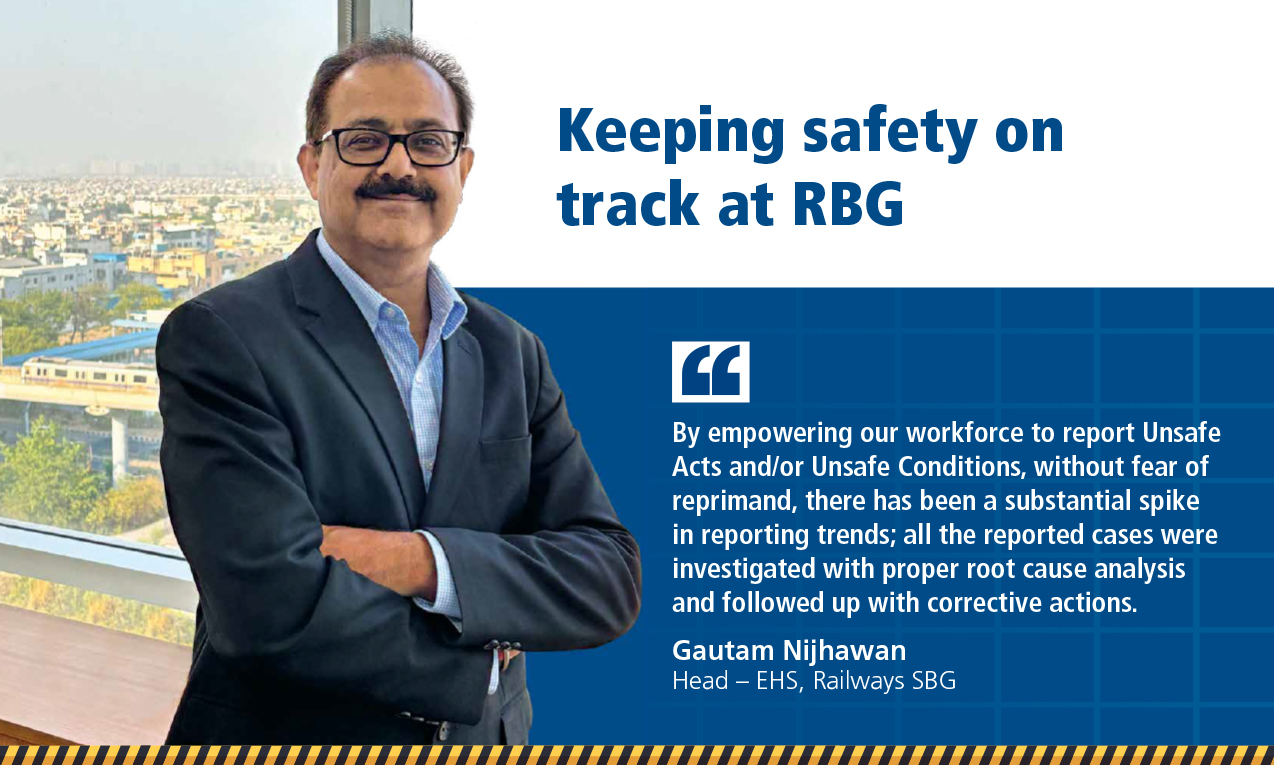
To achieve ‘Mission Zero Harm’ at the Railway Business Group (RBG), our collective efforts, driven strongly by our leadership, are aimed to significantly change our EHS management & culture and emphasize that all incidents / accidents are preventable. Our proactive approach, focusing on leading indicators like Hazard Identification & Risk Assessment (HIRA), hazard communication, near miss reporting, capacity building programmes and more have helped prevent incidents. By empowering our workforce to report Unsafe Acts and/ or Unsafe Conditions, without fear of reprimand, there has been a substantial spike in reporting trends; all the reported cases were investigated with proper root cause analysis and followed up with corrective actions.
Some of our key processes and practices to achieve Mission Zero Harm:
The 10 Life Saving Rules
Evolved to address critical activities within RBG projects, the 10 Life Saving Rules outline and define 10 essential EHS requirements that, if not adhered to, can pose significant risk to the life and health of individuals. Compliance with these rules is mandatory. A Standard Operating Procedure (SOP) along with a Consequence Management System have been developed and implemented. Violations, if any, are thoroughly investigated, actions of both the individual and supervisor are scrutinized to determine the cause for violation, with severe consequences, including potential termination from the project.
STARRT or Safety Task Analysis and Risk Reduction Talk
STARRT acts as a guide for workplace safety planning through pictorial representation of critical tasks with mitigation measures. Every employee, or work team, assigned a specific job must complete a STARRT meeting prior to the commencement of each task. The daily (pre-work) STARRT briefing is the final checkpoint to verify the safety preparedness of the workforce.
The STARRT discussion must verify:
- Basic requirements for the job with its control measures
- Tools and machinery brought to the work area are in good condition and properly equipped with safeguards
- Confirm that all employees are adequately trained
- System configuration is safe to perform work scope e.g. Lockout/Tag-out.
- Atmospheric monitors, respiratory protection, and other personal protective equipment brought to the jobsite are in safe, operable condition
- The necessary first aid or medical provisions are readily available; emergency call numbers known to the crew
It considers the hazards likely to be encountered during the shift, with mitigation methods based on the HIRA/ work method statement for the specific works. In case of interaction between different trades or work groups, separate cards must be completed for each craft and task. STARRT cards must be completed at the workplace in the environment where the work is executed.
Upon completion of a STARRT process, the task Engineer/Supervisor reviews the requirements noted on the card with employees performing the work and the latter must sign the card to verify their understanding and agreement to job requirements and hazard controls to be implemented. The task Engineer/ Supervisor discusses the risks associated with the Scope of Work with the employees and compiles the information necessary to complete the STARRT Card.
Implementation of Learning from Incident (LFI)
After investigating Reportable Loss Time Incidents, or critical and high potential near misses, ‘Learning from Incident’ (LFI) has been developed, which includes description of the incident; direct, underlying, & root causes; and corrective measures to prevent similar incidents in the future. At the project level, a stand down meeting is conducted at site in the presence of the department head, EHS head, site engineer & supervisors to detail the cause of incident and corrective actions are explained to the workforce with on time compliance. Refresher training is conducted for the workmen and supervisors associated with the incident too. In addition, LFI is translated into local languages & displayed at site as well as circulated across RBG projects.
Driving Safety through Digitalization
To identify and report unsafe acts and conditions at project sites, RBG has developed an EHS Observation module in the SHEILD App that features immediate multi-level push mail notifications and a robust compliance tracking mechanism. The Pre-Work Assessment and checklist module ensure that work is executed in accordance with safety norms.
A unique digital initiative at RBG is the QARS 2.O audit module, which benchmarks EHS performance of projects, generating quarterly audits conducted by a cross-functional EHS team, evaluating 20 RBG-specific safety parameters to comprehensively assess and improve EHS performance. The QARS 2.O audit helps foster a positive EHS culture, clearly defines roles, responsibilities, and accountability of four departments, i.e. EHS, Execution, P&M, and Admin & Stores to maximize site EHS compliance. Root cause analyses are conducted to address deficiencies, using an objective scoring approach to minimize auditor subjectivity, and promote environmental initiatives such as Reduce, Reuse, and Recycle (3R) across projects to enhance ESG compliance.
The way forward
We are closely working on a few futuristic EHS initiatives to improve our EHS efforts:
- Online EHS stats module – a single platform to collate all EHS data with predictive trend analysis,
- Incident Management Module in the SHEILD App to report near miss cases, first aid cases & other incidents,
- Develop RBG activity specific Virtual Reality modules to cover associated risk & control measures
In essence, through our proactive measures, commitment to continuous improvement, and empowerment of our workforce, we are helping ensure a safer and more sustainable future for all.