Navigating new waters with safety at the helm
After a long 2.5‑hour flight from Chennai to Indore followed by an early-morning 4‑hour drive, we finally reach PT&D’s 90 MW (AC) Floating Solar Project site in Omkareshwar, Madhya Pradesh. Stepping out of the car is like stepping into a furnace, and EHS In-charge Daniel Jeffrin smiles at our reaction as he quickly ushers us into the site office. Soon, suitably refreshed, hydrated, and wearing appropriate PPE after the visitor safety induction, we are ready for a site tour, on boats fitted with roofs to save us from sunburn, heatstroke, and longterm skin damage.
The Omkareshwar Dam is a gravity dam on the Narmada River upstream of Mandhata in MP’s Khandwa district. With an overall capacity of 600 MW, the first phase of the floating solar plant contains 288 MW, of which L&T has been awarded 90 MW by M/s SJVNL Green Energy Limited, with our scope involving design, engineering, supply, installation, testing & commissioning, and operation & maintenance for 3 years. There are over 2.19 lakh mono crystalline bi-facial PV modules and 4.2 lakh HDPE floats being floated on the reservoir, spread across 2.12 sq. km.
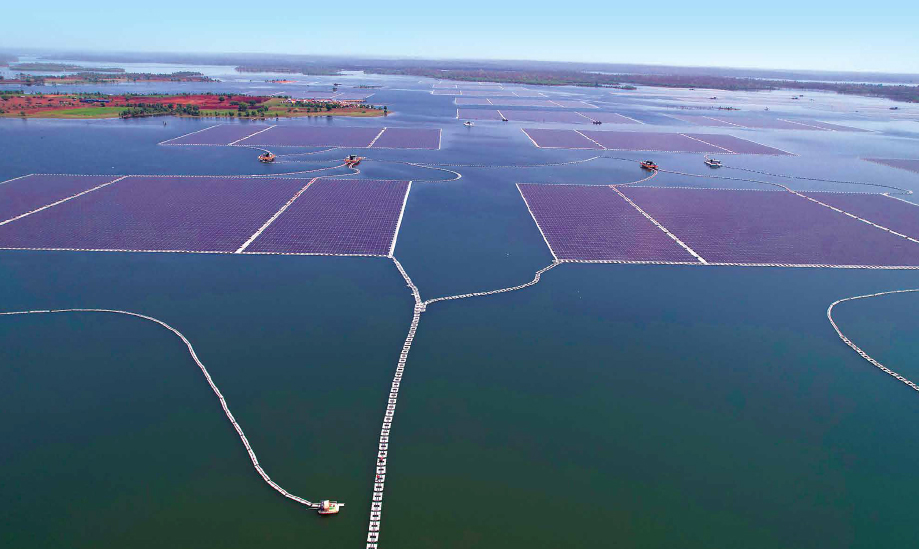
Remaining buoyant
The driver of the boat steers us to one of the 14 solar PV arrays, stopping parallel to the first row of floats. “Ours being a first-of-its-kind floating solar PV power project, we have enjoyed huge opportunities to learn and develop robust solutions, paving the way for future such projects,” remarks Lawrence Dhanaraj, Project Manager.
Ours being a first-of-its-kind floating solar PV power project, we have enjoyed huge opportunities to learn and develop robust solutions, paving the way for future such projects.
Lawrence Dhanaraj
Project Manager
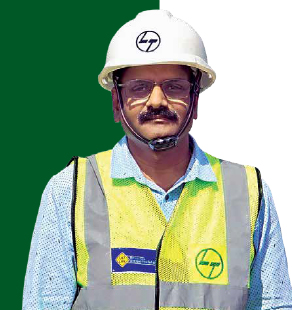
The floats work on the buoyancy principle: their weight should be equal to the buoyant force applied from the downward direction; if the float’s weight is more than the force, it will sink. Manufactured by the firm M/s Ciel & Terre, the floats are made of high-density polyethylene (HDPE) with masterbatch and designed with UV-protection and anti-slippery properties for people to walk on them firmly.
Each array or ‘solar island’ is spread across 300 × 200 sqm (equal to 15 football grounds) on the water surface, anchored at 186 to 193 points with helical or rock-bolt anchoring methodology and connected with arrays (mooring) using PVC-jacketed steel rope, polyester rope, and GI chain link in series to hold the island in position against variations in the water level. The solar panels on the arrays are connected to Inverter Floating Barges (IFBs) that have been moulded using fibre-reinforced plastic (FRP) pontoons with structural supports and Ferro Cement Barges.
Entering uncharted waters
Developing and maintaining a strong safety culture among the workmen has been challenging, according to Saravanan S, Senior Construction Manager (Electrical). “With no previous data available with us, we proactively developed SOPs on the activities involved. Our detailed HIRAs and elaborate emergency response plan have helped us achieve 0.4 million safe manhours to date, and an 85+% score in internal audits and in external audits conducted by Bureau Veritas.”
A temporary jetty, constructed by the team for boat operations and material shifting, is fitted with proper barricades and steps with handrails to ensure safety when entering or exiting the boats. More than 300 workmen have received activity-based training at site, and their induction process covers specific hazards pertaining to working at a floating solar plant. Mock rescue drills on drowning, snake/insect bites and fire drills are regularly conducted.
A deep dive indeed!
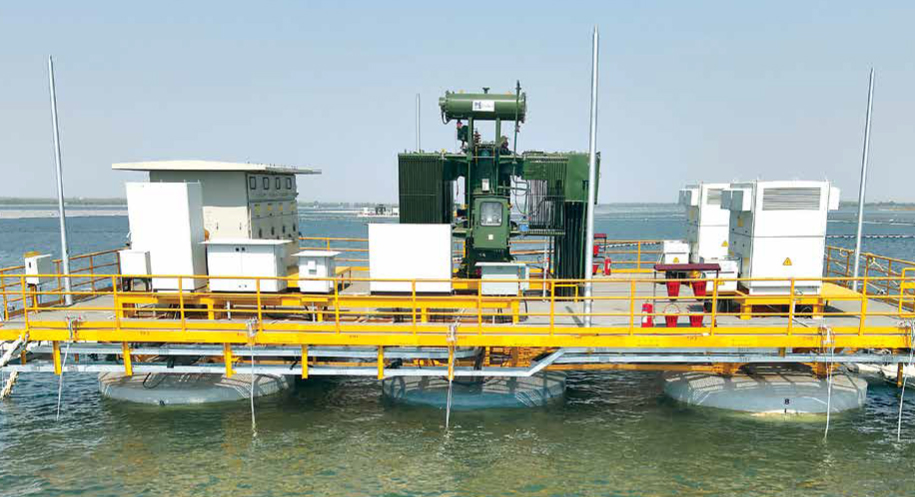
We notice lifebuoys in all boats, an emergency evacuation plan with route maps, an observer with binoculars, a flag man, breath analyser tests for operators and divers, and warning signages & barricades at the water area. Certainly, Lawrence and team have left no stone unturned to keep safety top priority!
A specially trained team of divers carried out the arduous task of anchoring & mooring the solar arrays and IFBs, working in unprecedented weather conditions and water level variations. They had to also remove dead trees and remnants of electric poles, lying submerged since the dam was constructed, under the supervision of a former naval officer. Lawrence explains about the bathymetry and topography surveys they conducted to gauge the depth of the waterbed with reference to the datum level using an echo sounder, which revealed that the water depth varied between 1.4 m and 25 m with respect to the maximum drawdown limit of 193.54 m. The stores and project office are safely located at a higher elevation that is above the maximum flood level of the dam.
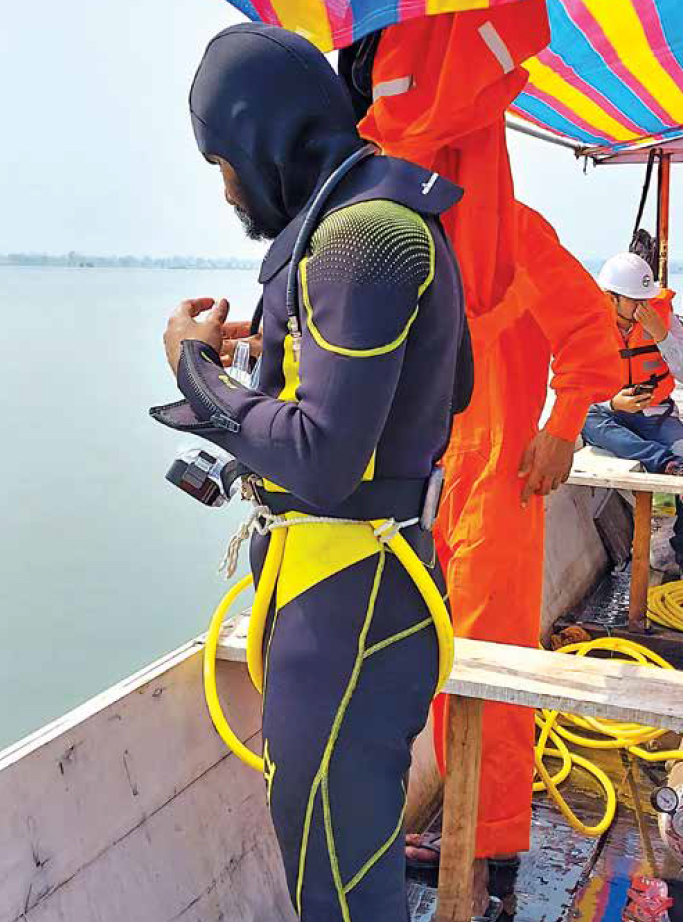
The client had handed over the area of an abandoned village to the project team. Lawrence narrates, “Our priority was to From day one at this location, we found huge scope for environmental protection, but at the same time, we were committed not to harm the environment in any way with our construction activities. Daniel Jeffrin EHS In-charge safely demolish the leftover broken mud walls, remove the bushes, and develop the area. In the process, we encountered small wild animals, snakes, and birds, for which we provided adequate safety training to excavator operators, workmen, and other stakeholders.”
While all divers were equipped with diving suits with life support, all personnel traversing the waters have to mandatorily wear life jackets with whistles, like us. “We deployed tailormade hydraulic underwater drilling equipment to drive the helical and rock-bolt anchors into the reservoir bed, mounted on the steel pontoons,” explains Saravanan. “In addition, we follow a token system for all workmen engaged in the anchoring activity.”
ESG at the fore
“From day one at this location, we found huge scope for environmental protection, but at the same time, we were committed not to harm the environment in any way with our construction activities,” remarks Daniel. Initially, the team prepared and implemented a client-approved environmental and social management & monitoring plan. “A third-party agency monitored the aquatic ecology like phytoplankton, zooplankton, and fishes on a monthly basis. In fact, we find that the number of fish breeds have increased!” he grins.
From day one at this location, we found huge scope for environmental protection, but at the same time, we were committed not to harm the environment in any way with our construction activities.
Daniel Jeffrin
EHS In-charge

Apart from aquatic life, wind speed, noise, surface water, ground water, soil quality, terrestrial biodiversity, waste management, and habitat modification are all regularly monitored. Daniel and team have planted 2,200 trees around the project area, with a 90% survival rate.
Digitalization driving safety
“We extensively use the work permit system through the SHEILD app, capturing leading indicators, which has helped us analyse and take proactive action to drive safety,” Saravanan notes gratefully. The WISA app captures daily attendance digitally, while a QR-based token system keeps tab on all movement on the dam waters. “The ‘DiGi Tokens’ capture the details of all individuals entering the water body along with their in & out times, for real-time monitoring, enabling prompt identification and response to unauthorized entries or emergencies,” he adds. “The detailed digital records facilitate swift action in case of incidents, with precise logs of all personnel present.”
The ‘DiGi Tokens’ capture the details of all individuals entering the water body along with their in & out times, for real-time monitoring, enabling prompt identification and response to unauthorized entries or emergencies.
Saravanan S
Senior Construction Manager (Electrical)
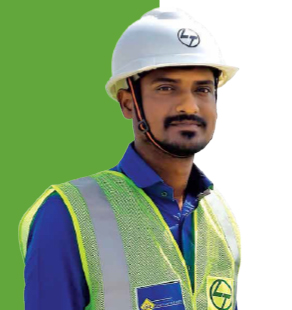
Monthly motivational awards to site engineers, supervisors, subcontractors, workmen, and operators are for keeping everyone safety conscious at site.
With meticulous SOPs and checklists developed for every activity from boat patrols & diving suit inspections to installing underwater anchors & floating inverter barges, the Omkareshwar Floating Solar Project team is well on its way to safely hand over the plant to the client by the end of June. “And we aim to do it with the Safety flag flying high!” says Lawrence with an emphatic thumbs-up, as we start our long drive back into the sunset.