SURYA REGIONAL BULK WATER SUPPLY SCHEME
On top of the EHS game!
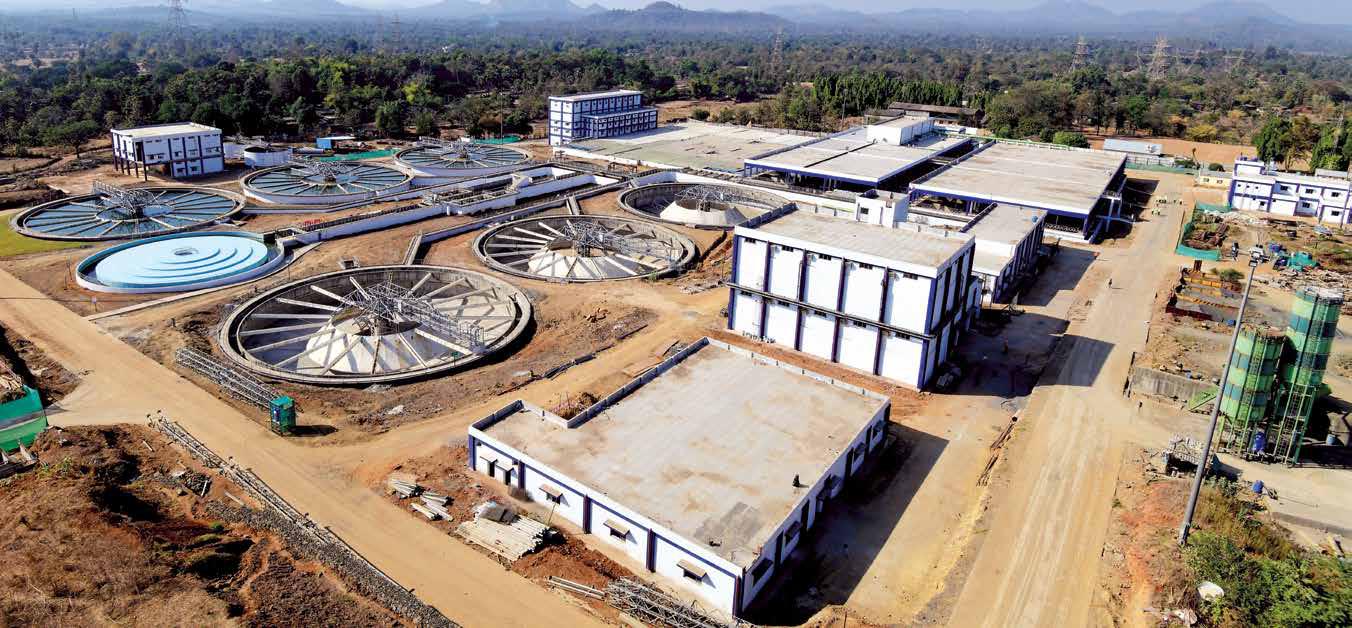
For Project Director, Colin Nonis and his team at the Surya Water Supply Scheme, the most challenging task was to construct two tunnels – the 4.6 km Tungareshwar and the 1.7 km Mendhwankhind tunnels, using TBMs, attempted for the first time by a project from WET IC. To have completed both the tunnels perfectly and bagged L&T Construction’s Safety & Quality Awards, for the first time since the awards were instituted, is a matter of immense pride for the team. “This is certainly a huge boost to the team,” grins a delighted Colin, “and as we sprint to the finish line to complete the project in a few months, we will strive to set more benchmarks and continue to maintain our robust EHS and Quality culture.”
As we sprint to the finish line to complete the project in a few months, we will strive to set more benchmarks and continue to maintain our robust EHS and Quality culture.
Colin Nonis
Project Director
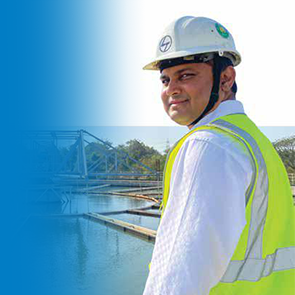
The project involves the construction of a 707 MLD Intake Well, a 418 MLD Water Treatment Plant, and 45 & 35 ML Master Balancing Reservoirs. The MS pipeline of 81 km includes a Water Segmental Tunnel of 6.3 km & a Micro Tunnel of 1.3 km.
Inculcating and maintaining a safety mindset
“Our strategy involves preplanning, introduction of new engineering control measures & adoption of Safe Operating Procedures,” shares EHS In-charge, Abijith K S, “and through our robust EHS plan, we have ensured safety standards through consistent teamwork, collaboration, early anticipation, and resolution of problems by using various digital technologies, mechanized working, and constant learning from the incidents/near-miss reports of similar projects.”
We have ensured safety standards through consistent teamwork, collaboration, early anticipation, and resolution of problems by using various digital technologies, mechanized working, and constant learning from the incidents/nearmiss reports of similar projects.
Abijith K S
EHS In-charge
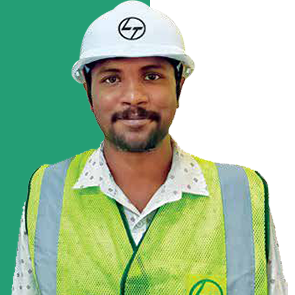
EHS induction is a norm for the staff and workmen, engaged right from the initial stages of the project, while activity-specific training schedules have been developed and certified by professionals engaged for specialized skill requirements, such as tunnelspecific training.
A Workforce Management Centre, EHS Induction Room & Training Van have been set up for staff & workmen and on successfully completing the Skill Authorization Procedure, competent workmen and staff are issued a Skill Authorization Pass (SAP) for identified activities like excavation, WAH, work in confined spaces, electrical work, and material handling. The staff also undergo several levels of EHS training like Safe Execution Engineers (SEE) training, first aid certification courses, behaviourbased safety training and more.
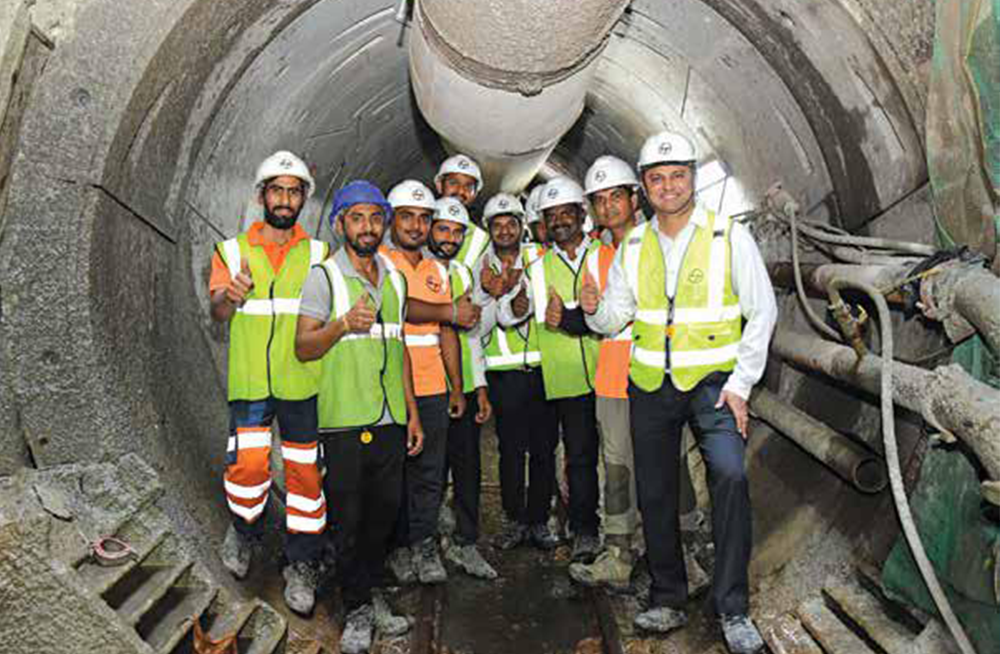
Tunneling safely
Tunnel construction involves complex and specialized tasks, requiring a high level of skill and precision and Colin mentions the deployment of skilled workmen through various processes of pre-deployment, medical, & skill tests to execute the work safely. During the shaft preparation for the tunnel, several engineering & administrative control measures were adopted to maintain safety. While EDRC designed a suspended working platform for shotcreting & rock bolting, a blasting cap was designed to prevent flying rock during blasting inside the shaf area, proving beneficial especially as all shafts were in the vicinity of a National Highway.
Pre-deployment certification & monthly inspections ensured safety in P&M operations, preventing accidents, injuries, and damage to equipment. Material handling was one of the major operations through a gantry crane. Third-party inspections were carried out for the lifting tools to ensure that lifting gears & appliances worked properly.
To ensure the tunnel site was safe and the tunnelling incident-free, a centralized control centre observed multiple locations through CCTV. A tally board system monitored safe access to the tunnel as well as for emergencies. A passenger hoist based on a rack-and-pinion gear with limit switches was installed, while an EDRCapproved man basket that could carry up to 10 workmen was arranged at the surface level to evacuate the workforce in case the passenger hoist failed.
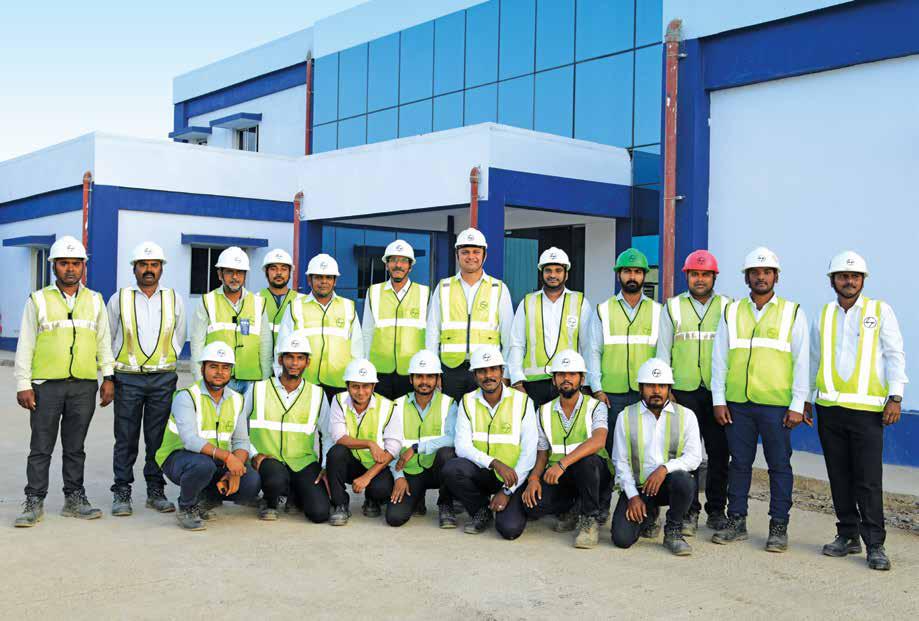
The gas levels in the tunnels were constantly monitored to ensure that there was no build up of gases underground, posing health and safety hazards, apart from a well-designed ventilation system. “We continuously checked oxygen levels on an hourly basis with multi gas detectors and mini-Oximeters, placed inside the TBM machine,” points out Abijith. “Noise, illumination, and temperature levels were also being monitored every hour.”
Emergency preparedness & leadership involvement
The team implemented a comprehensive monthly ERP plan with several mock drills conducted at site & offices for anticipated emergencies such as medical, fire, evacuation, toppling of construction machinery, drowning, chemical spillage & release of hazardous gases.
Involvement of the top management set the tone for a strong safety culture with the IC Head, BU Head, EHS Head & several other Department Heads conducting regular EHS walkthroughs, offering continuous feedback. An EHS Champion & EHS Ambassador, identified from each work location based on their participation and effectiveness to promote a positive EHS environment, are empowered to raise incidents of non-compliance and felicitated by the senior management.
The team can access and manage all kinds of inspections & training records, raise UAs/UCs/UBs, etc., digitally, giving them a one-point easy access to all records and comprehensive analyses for continuous improvement. Even the SEC & work permits were implemented through View EHS.
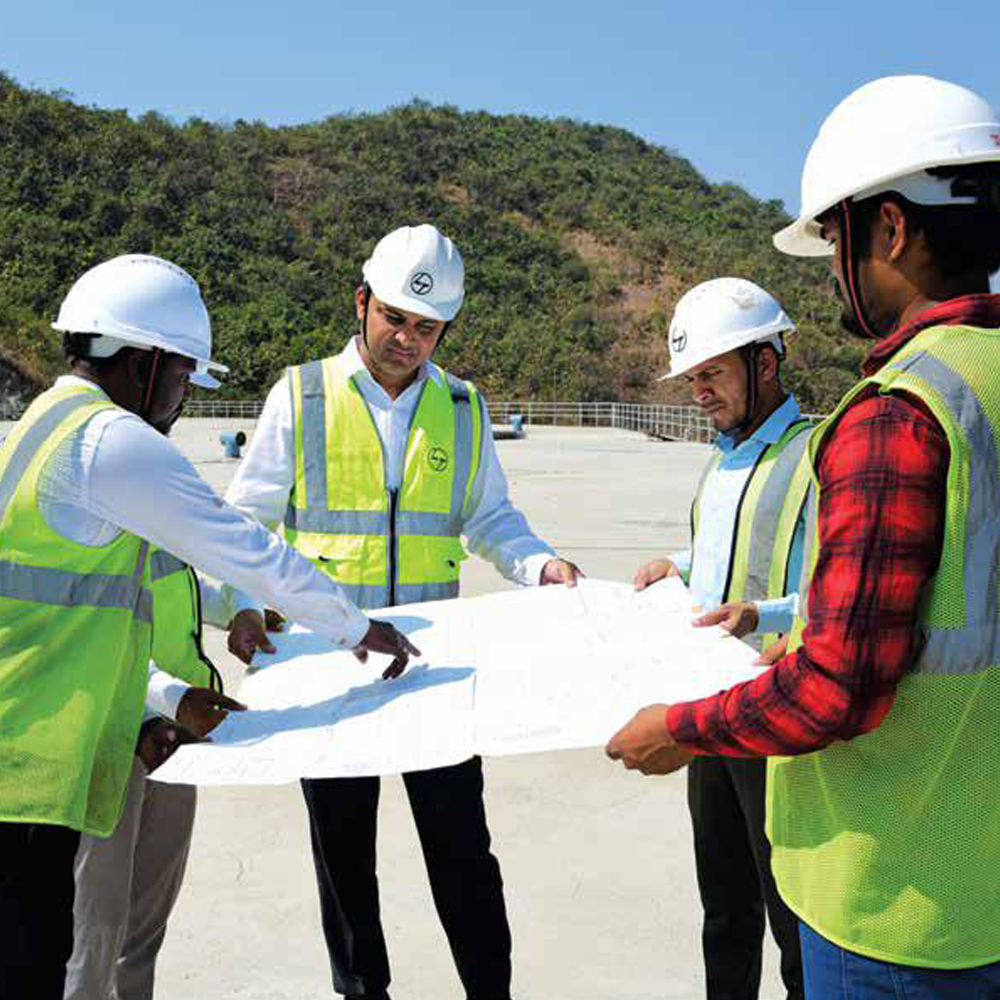
Minimizing the environmental impact
To minimize the negative impact of site activity on the environment, the project team planted 146,000 saplings across Palghar, Raigarh & Thane districts. Solar lights have been installed at the workmen habitat, and the excavated material from the tunnels was reused to prepare an approach road to the site. As a ‘Go Green’ initiative, plastic & paper waste is recycled.
The project team implemented WE CARE (Workforce and Environment Protection Program), which integrates strategies and practices that prioritize the well-being of the workforce while minimizing the environmental impact of operations.
Colin is aware that his project team has set some lofty EHS benchmarks, and the onus is on him, Abijith, and the Surya WSS team to maintain and even surpass them. They have the right strategy in place, and a team that is committed to keeping their EHS performance top-notch, come what may.