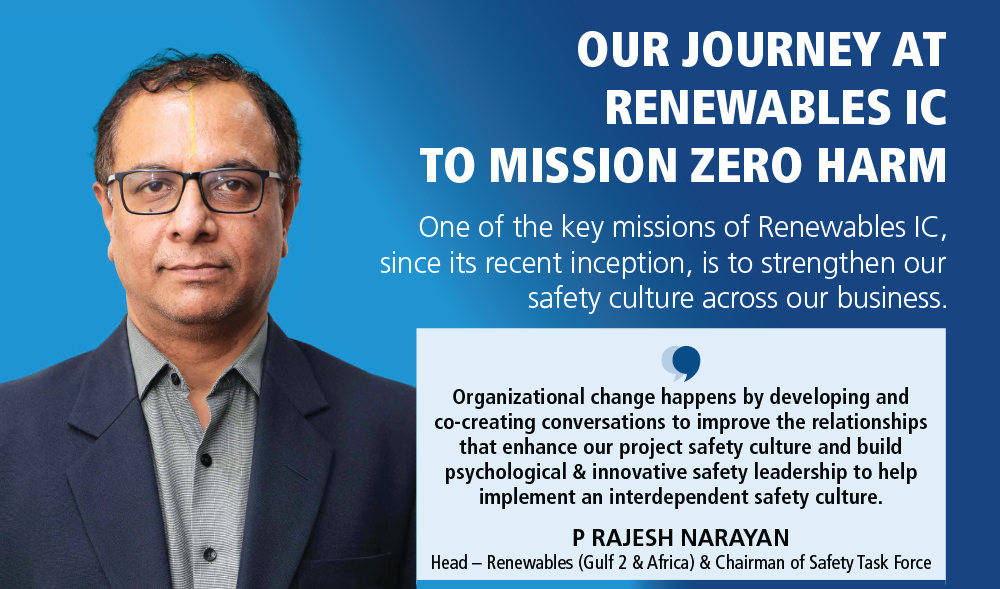
Safety is always critical to L&T. Our overall safety record is strong; however, as we grow and continue to deliver at scale, we see a need to boost our safety engagements and compliance across project sites and offices for consistent delivery and to assure our project leaders, team members, and partners that we are focused on getting results safely, the right way, in accordance with our beliefs, values, and attitudes.
To successfully drive this, our new EHS strategy rolled out in early 2025 is founded on 5 pillars: Leadership & Employee Participation, Risk Management, Business Partners Engagement, Learning & Competencies, and Compliance & Continual Improvement.
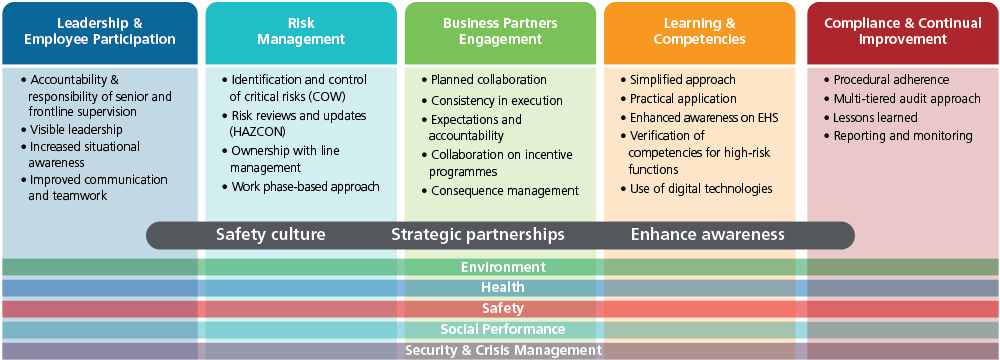
The Safety Task Force
A strong safety culture helps maintain safe and efficient operations with everyone, from workers to managers, taking safety seriously, remaining vigilant, and avoiding compromises. A Safety Task Force drives our new EHS strategy, comprising operational and functional leadership as well as members of the EHS department, to act as a vehicle to promote new ideas, roll out new initiatives, and drive consistency in EHS execution across the business. In addition to its efforts to improve existing and develop new EHS standards and protocols, the Safety Task Force has already rolled out several initiatives:
- Safety Hour initiative to highlight the importance of leadership visibility, enhance compliance with safety requirements and, indirectly, increase time on tools for the projects
- Form and standardize EHS Steering Committees across projects
- Mobile Phone Policy to reduce distractions at the workplace
- Formal Go-No-Go process to ensure readiness for specific work activities
- HAZCON approach in Risk Management
- Use of digital platforms for information sharing, lessons learned, data collection, and trend analysis
Safety Culture
Organizational change happens by developing and co-creating conversations to improve the relationships that enhance our project safety culture and build psychological & innovative safety leadership to help implement an interdependent safety culture.
At the Sudair and Al Kahfah projects in KSA, our mission was to go above and beyond our typical compliance to safety – to shift from a ‘calculative’ level of safety culture, where we acknowledge that systems are in place and hazards are managed, to a ‘proactive’ and ‘progressive’ level where safety leadership drives continual improvement and EHS becomes a way of life, self-regulation, and mindfulness.
“Through joint efforts, hard work, and uncompromising commitment to safety of all stakeholders, we have managed to not only achieve a recordable incident-free workplace at both projects but also received BSC’s 5‑Star Safety Performance recognition and the Sudair project has won the Sword of Honour. We are also working closely with other Renewables projects to undergo similar processes to drive a consistent EHS approach across the business,” said Pradeepkumar R, EHS Head, NEOM and Gulf 1 BU.
EHS is closely interlinked with a number of our functions, and alignment with our HR processes is of utmost importance as our people are the core of what we do, and we want them to reach back home safely. Learning & Development is an important pillar of the EHS strategy to enhance not only EHS competencies but also leadership and other skills of our staff and workforce, generating talent that will be second to none in the industry. Virtual reality trainings, hands-on practical Safety Park training grounds, and EHS Boot Camps for midlevel management are just a few of our initiatives.
Business Partners Engagement
Setting clear EHS expectations for our business partners, sharing best practices and lessons learned, and ensuring continual progress of the safety culture throughout our organization, and to those we work with on our projects, is critical for our overall success. EHS management is a critical component in our supply chain ecosystem, a license to operate and cornerstone our vision to deliver best-in-class service for our customers. We are instituting a multitier EHS process to select our business partners (subcontractors) focused on planning, pre-qualifications, premobilization & execution checks, performance evaluations at set intervals, demobilization, and final closeout.
The Renewables IC projects in Uzbekistan, Samarkand I and II, will be the first ones to implement an 8‑step subcontractor management process aimed at improving L&T and subcontractors’ EHS performance.
Security, Crisis Management, and Digital Technologies
Over time, our sites have shaped a security culture focused on improving awareness, prevention, preparedness, and response to changes in risk conditions. Security programmes are clearly articulated in site procedures and practices.
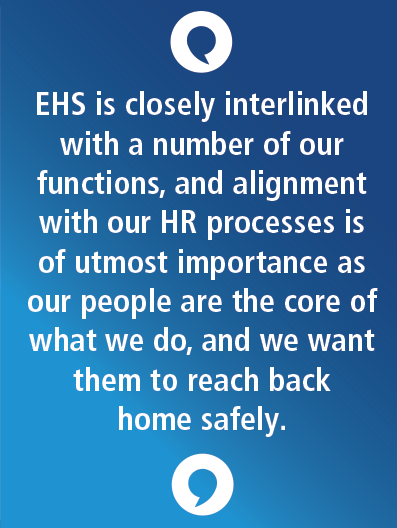
Various security initiatives have been developed at the DEWA Phase VI project by integrating project needs with digital means that include electronic access control systems, RFID capabilities, biometrics, and facial recognition systems at labour camps linked to site access control systems to ensure accurate ‘personnel on board’ data for emergency preparedness at camps and sites, enhancing accountability of the workforce.
“Our most recent process improvement using digital technology is implementing the Guard Tour System to organize, log, and execute guard rotations and patrols across their assets, while confirming that the officers have accomplished their tasks within the predefined time intervals,” noted Ms. Elif Eslek, DEWA VI Project, EHS Head. “This process ensures that all areas are monitored, in addition to the traditional CCTV concept, to solidify our efforts to Deter, Detect, and Respond to potential security events.”
Behaviour-Based Safety
Our business in India has been a role model in the implementation of several initiatives, from various applications on the SHEILD platform to behaviour-based safety programmes, developing strategies to connect with people emotionally and influence their mindset. This goes beyond a technical challenge that can be resolved using prior information and experiences; it is a challenge to make people feel their best. We are developing a programme that will go beyond trainings and workshops to focus on responsibility and accountability of all stakeholders and their share in creating and sustaining Zero Harm across all our projects.
We understand that there is no one solution when it comes to EHS excellence. It’s a myriad of different things and it starts with commitment at all levels and a shared responsibility to generate commitments and action plans that are consistent with the elimination of injuries.
EHS excellence – meaning protection of our employees, customers, suppliers, and our environment – is my core value. Safety is an individual and corporate value, not a priority, and must be treated as such, as the priorities change but values do not.
To achieve our Mission Zero Harm and create a workplace free of injuries and other incidents, we must work together, and only TOGETHER can we succeed.