Zero tolerance to anything unsafe;
100% compliance to sustainability.
The Agra Metro Electrification Project
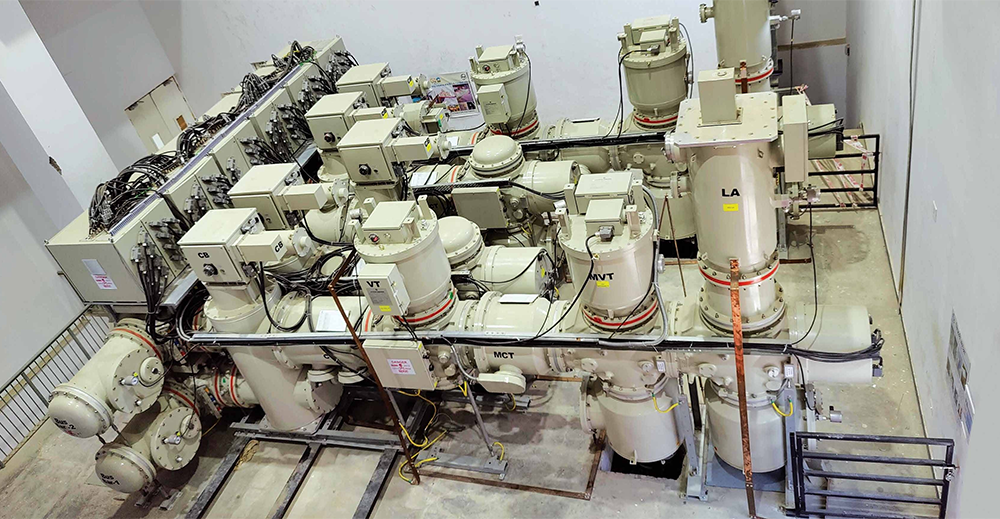
GIS
A PT&D IC team is busy executing the Agra Metro Electrification project for the Uttar Pradesh Metro Rail Limited, facing and overcoming all the challenges of building complex power infrastructure in the heart of one of India’s leading tourist locations.
At the heart of the project lie three crucial 132/33 kV Receiving Substations (RSS), strategically located at PAC Depot, ISBT, and Kalindi Vihar, which will be the metro’s energy system and are in turn intricately linked by an underground network of 132 kV double circuit cables, stretching for 20 km beneath the city. From these powerful RSSs, the pulse of 33 kV electricity will radiate outwards, reaching 27 (20 elevated and 7 underground) Auxiliary Substations (ASS) scattered across the entire metro network. Connecting them all is an impressive 250 km of 33 kV cabling. Beyond the cables and substations, the mandate for Project Manager Nitin Tiwari and his team includes supply and installation of 33 kV GIS/AIS, auxiliary transformers, lighting systems, power sockets, and bracket supports throughout the sprawling viaducts.
“The true nerve centre for this entire power infrastructure is the Supervisory Control and Data Acquisition (SCADA) system,” points out Planning Manager Mohammad Athar Ansari, “which will provide constant station-level monitoring and centralized control, managing from three control centres: an Operational Control Centre (OCC), a Backup Control Centre (BCC), and a Centralized Control Centre located all the way in Lucknow. This multilayered control will ensure that the metro’s power supply remains robust and responsive, no matter what,” affirms Mohammad.
There is no second chance with safety and everyone deserves to go home safe. Regular inspections crucially identify training needs, spot hazards early, reinforce safety protocols, and foster a culture of shared responsibility.
Nitin Tiwari
Project Manager
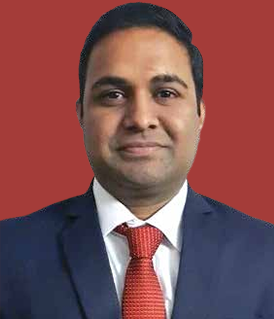
Safety: Not a guideline but a philosophy
“From day one, we have adopted a ‘Zero Tolerance’ approach to safety and environmental compliance,” emphasizes EHS Officer Ramya Ranjan Bhuyan, “which is not merely a guideline but a deeply ingrained philosophy and has been holding us in great stead, especially during the intricate 132 kV cabling work.”
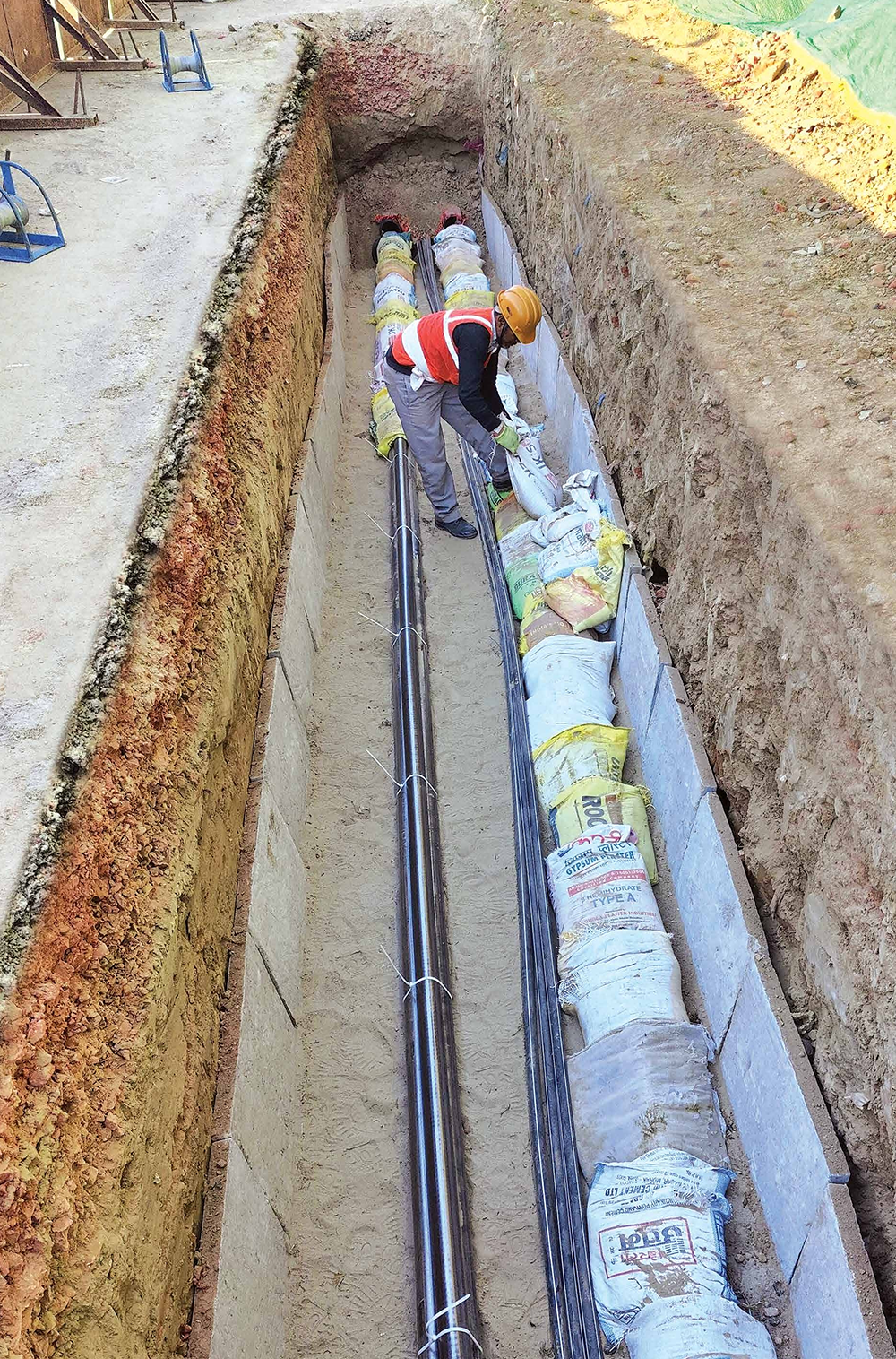
132 kV cabling work
Before a single shovel touches the ground for the 132 kV cabling, the first critical step is a thorough Ground Penetrating Radar (GPR) survey to ascertain two critical aspects: to understand the subsurface conditions to determine the safest excavation method, whether manual, mechanical, or Horizontal Directional Drilling (HDD), and secondly, to prevent any accidental damage to existing underground utilities, a network of gas lines, water pipes, and power cables that lie hidden beneath. Following the survey, a formal notification letter is dispatched to all relevant utility authorities, ensuring that everyone is on the same page and prepared.
Before commencing any mechanical excavation, a manual ‘trial pit’ is dug in the proposed work area to accurately verify the location, depth, and type of the existing underground utilities to prevent any accidental damage, ensure worker safety, and guide the team on the most appropriate excavation technique to be adopted. To prevent unauthorized entry and keep pedestrians safe, every span of the excavated area is securely barricaded with hard boards, adequately lit, and traffic-controlled with strategically placed solar-powered blinkers and rope lights.
Excavator operators are armed with an ‘Operator Competency Certificate’ and allowed to work only after successfully completing a comprehensive training programme and passing a rigorous competency assessment test conducted by an approved third-party agency, ensuring that only authorized and proficient individuals operate machinery for trench preparation.
Furthermore, every P&M used for excavation is rigorously inspected and certified by a competent third-party inspector, with approval status indicated by affixing a green flag. For precise HDD, the equipment itself is inspected and certified by a competent third party, and the drilling is meticulously tracked to ensure that the drill pipe is accurately guided along the approved route and at the correct depth.
“We have an additional layer of accountability with third-party monitoring to verify that all construction and site activities strictly adhere to environmental regulations and approved environmental management plans,” reminds Nitin. Beyond internal training, external certification programmes are actively pursued, equipping personnel with specialized knowledge in first aid, fire prevention and control, rigging, and crane safety, further strengthening the project’s safety net.
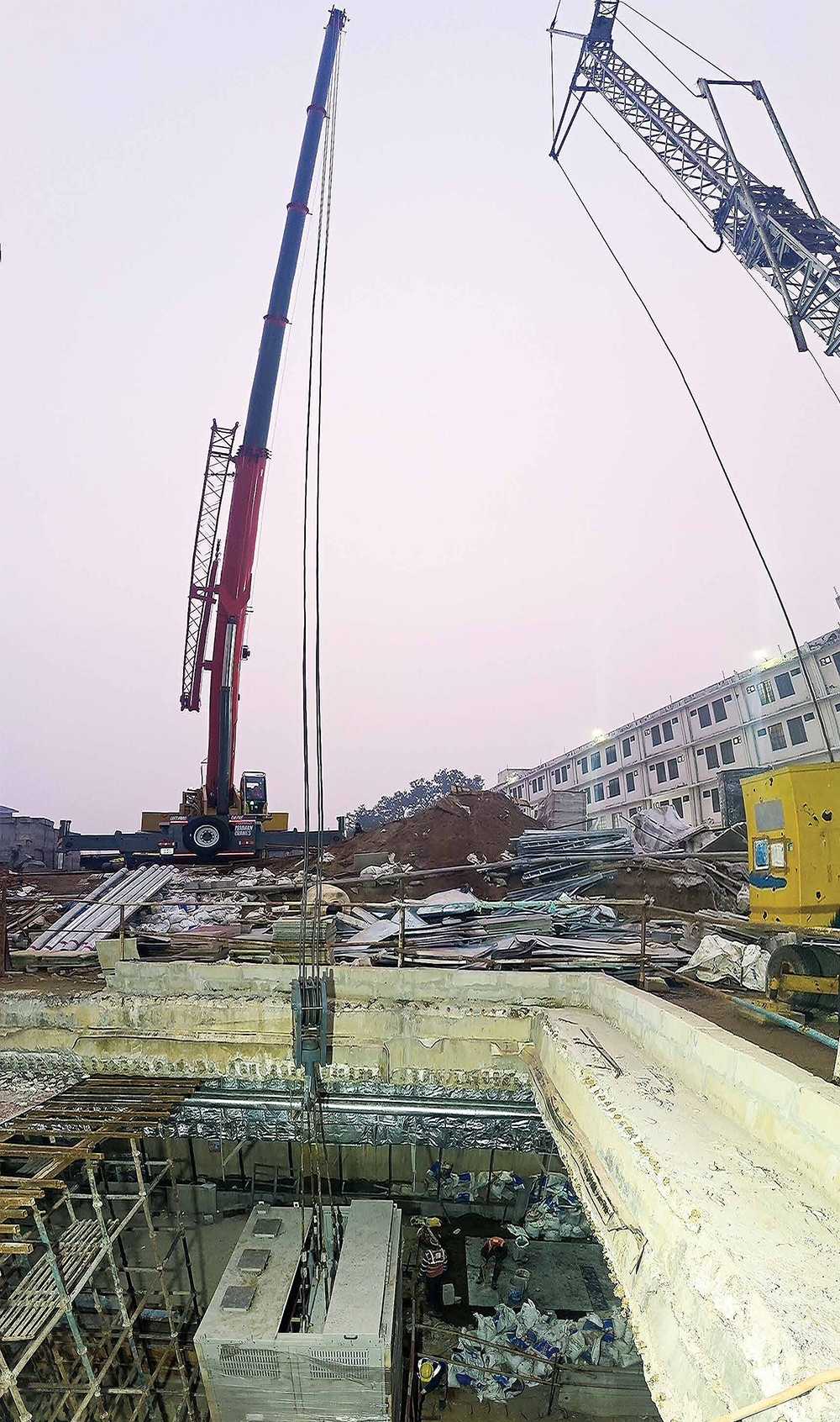
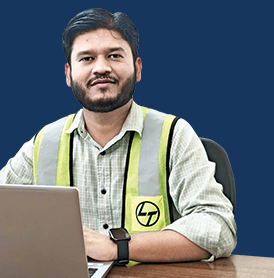
The detailed lifting plan specifying the Safe Working Load is rigorously reviewed and approved by a competent person or the designated authority, ensuring strict adherence to safety standards.
Mohammad Athar Ansari
Planning Manager
Navigating the underground, safely
The process of lowering and shifting heavy electrical equipment like transformers, panels, and cable drums into the ASS rooms within the underground metro stations presented its own unique set of complex logistical and safety challenges, often originating as early as the station box design phase, typically handled by a separate civil contractor. It was vital to communicate the size, weight, and handling requirements of all major electrical equipment during the initial design and drawing finalization stages.
“Failure to incorporate appropriate cutouts or access provisions at this point can make the lowering process incredibly difficult or even impossible without extensive rework,” cautions Nitin. These challenges are further amplified by partial clearances from the principal civil contractor, the inherent space constraints within the station structures, and tight execution schedules. “Therefore, early coordination, precise planning, and continuous interface management between the electrical and civil teams is essential for safe, timely, and efficient installation in the underground environment,” he adds.
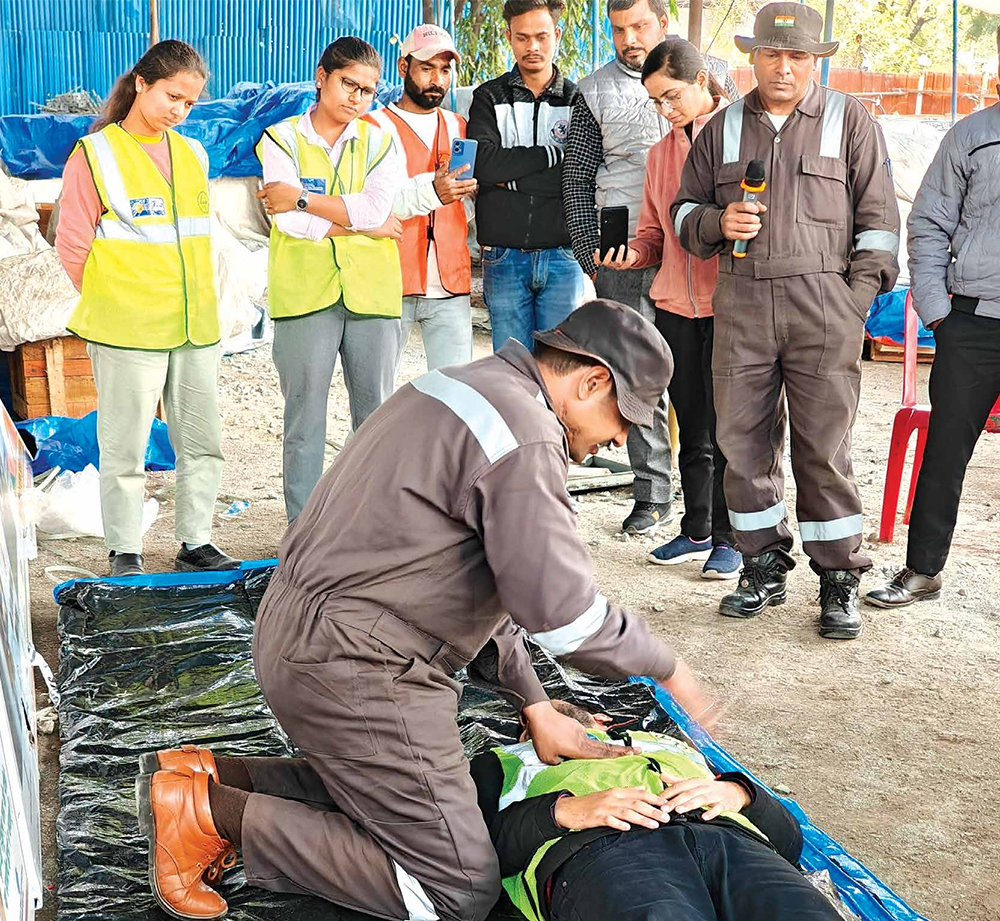
First aid training
All lifting activities commence with a detailed lifting plan that specifies the Safe Working Load (SWL) for all lifting equipment and accessories, directly correlating to the actual weight of the electrical equipment. “This plan is rigorously reviewed and approved by a competent person or the designated authority, ensuring strict adherence to safety standards ‚” explains Mohammad.
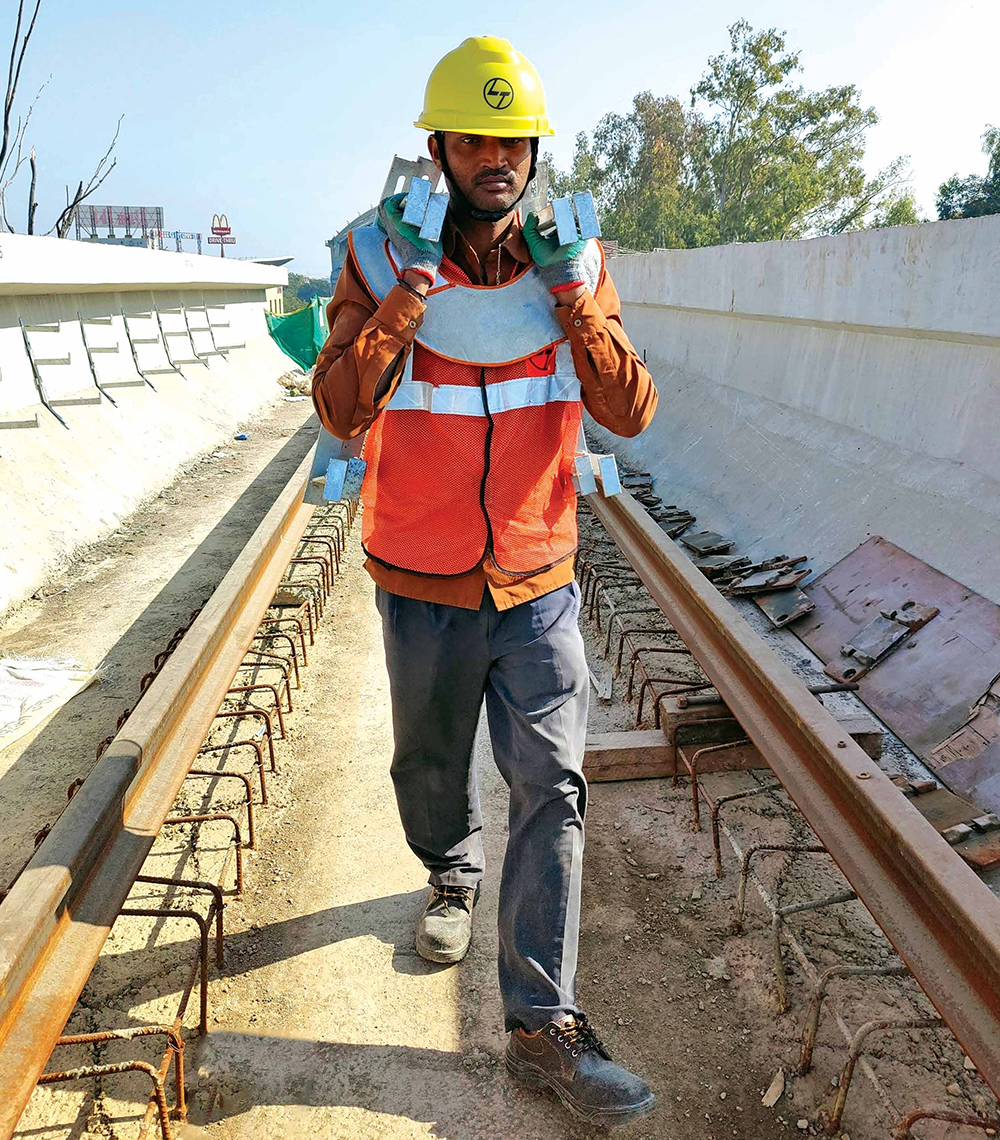
Shoulder safety pad
It is the responsibility of a dedicated Emergency Task Force to safely lower and shift materials within tight deadlines. This specialized team undergoes certified training in rigging and crane safety that empowers them to plan and execute high-risk activities with precision and efficiency, mitigating potential hazards and avoiding delays.
Apart from adequately lighting up underground stations to maintain a safe and efficient working environment, the project has embraced advanced material handling technologies, deploying panel shifting trolleys, specially fabricated custom platform-type ladders during the installation and coupling process, and custom rigging solutions for safer and more efficient movement of heavy equipment through restricted spaces. These are carried out in strict adherence to customer safety standards, continuously monitored and in full compliance with EHS protocols.
A critical contractual requirement is to maintain a pristine, dust-free, and visually clean environment along the main roads of Agra. To combat dust, and uphold the city’s ecological and aesthetic standards, green nets are used to cover loose soil and reduce fugitive dust emissions, in addition to regularly spraying water.
We have a simple but profound mantra: Observe more; Comply more and we encourage every team member to be vigilant and proactive in maintaining a safe work environment.
Ramya Ranjan Bhuyan
EHS Officer
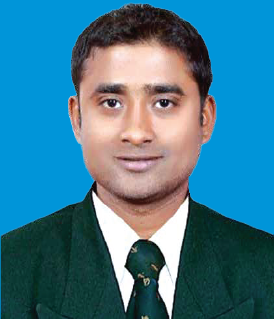
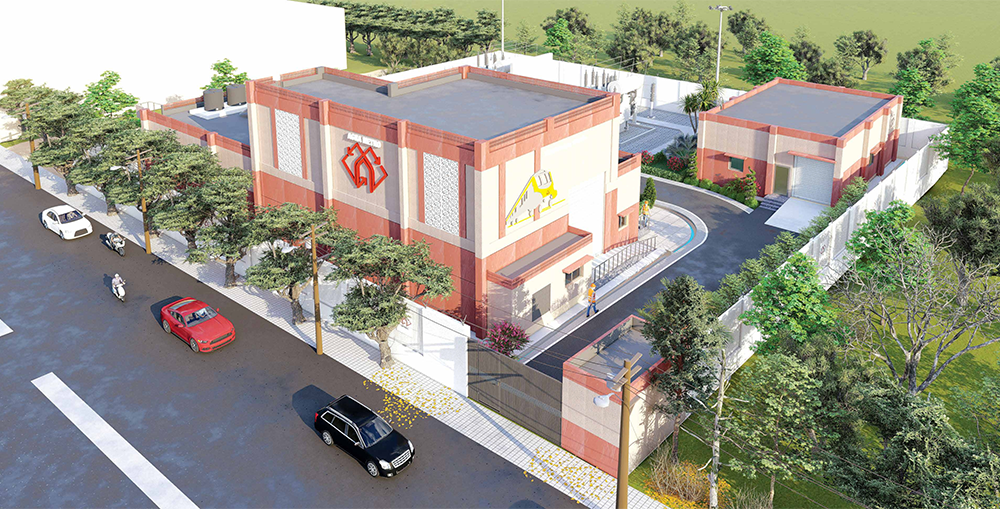
Forging a culture of safety, sustainability, and empowerment
“We have a simple but profound mantra: Observe more; Comply more,” says Ramya, “and we encourage every team member to be vigilant and proactive in maintaining a safe work environment. By consistently observing their surroundings – be it equipment, work practices, or site conditions – they can identify potential hazards early, allowing for corrective actions before they escalate into incidents.” Thankfully, this mantra has translated into a culture where risk prevention has become second nature, ultimately creating a safer and more responsible workplace for everyone.
For Nitin, it is all about an uncompromising attitude towards safety, for as he says, “there is no second chance with safety and everyone deserves to go home safe.” All execution engineers are accountable for maintaining the highest safety standards on-site, with weekly safety walkdowns sustaining safe manhours. Nitin points out that with the involvement of multiple agencies on site, the occasional behavioural challenges related to safety compliance, particularly concerning housekeeping in ASS rooms and stations, have been detected. “These regular inspections crucially identify training needs, spot hazards early, reinforce safety protocols, and foster a culture of shared responsibility.”
Beyond safety, the project has embraced sustainable and environmentally responsible construction as a core value, committed to social responsibility, public health, and long-term urban resilience. Nitin is especially proud of promoting women’s empowerment, with women actively working on site as independent Site In-charges, successfully leading critical activities, including 132 kV EHV cabling works, 33 kV cabling at underground stations, equipment installation, and testing. “They have been demonstrating strong leadership and technical expertise,” avers Nitin.
The project’s exceptional commitment to safety has been widely recognized, having won a RoSPA Gold, BSC Merit, and NSC certificates, among others. “We have received commendations from the customer for our safe work and the safe completion of Precast JB and Precast GIS roof slabs,” chips in a delighted Ramya, mentioning their various internal praise awards too.
There are still miles to go, but we are convinced that Nitin and his Agra Metro team will not rest until they have delivered their project and stayed true to their commitment to a safer, greener, and more inclusive future for one of India’s most iconic cities.