Crossing the mountains without crossing safety limits
400 kV Double Circuit Kishanpur to Dulhasti Transmission Line Project
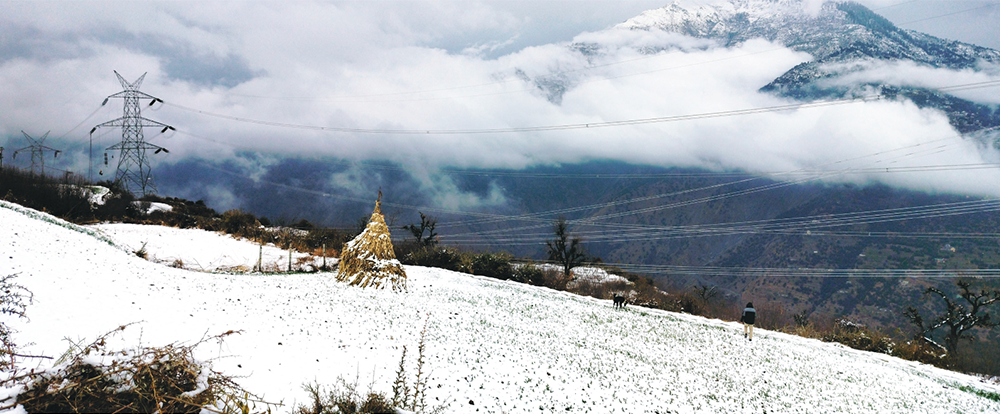
Jammu & Kashmir is everyone’s dream holiday destination with its lush, green valleys and snowcapped peaks, but talk to anyone who is working there, like the PT&D team who are executing a transmission line project, and they will share an entirely different story. They will speak of the extremely difficult terrain, the unforgiving weather, the unstableness of the ground beneath and the unpredictability of landslides or snowfall that can suddenly and without warning block all approach roads.
These are some of the challenges that Project Manager, A Mohan Kumar, and his team face as they strain muscle & sinew to erect a 400 kV transmission line from Dulhasti, near Kishtwar, traversing the Himalayas to Kishanpur, to evacuate power generated from the Hydro Electric Projects (HEPs) in J&K’s Chenab Valley. Their scope of work is spread across four packages, with a special focus on stringing the second circuit along the existing 400 kV line, in addition to foundation work and tower erection in some extremely challenging terrains and hard rock strata.
We must continuously think innovatively, be it live line stringing with the first circuit in a charged condition, crossing distribution lines without shutdown, optimizing the head loading process, or even improving material handling, with safety always at the forefront.
A Mohan Kumar
Project Manager
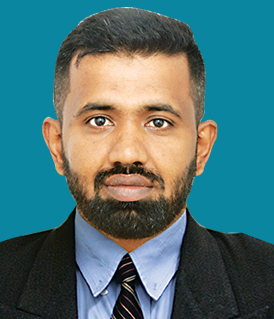
Overcoming some tall & taller challenges
Working at height is certainly one of the team’s major challenges when executing at such high altitudes, but as Mohan explains, there are several other hurdles that they must cross. “We face huge logistical issues to construct on hilly and remote terrains, mobilize skilled workers as our work demands special skill sets, ensure the safe transport of personnel to high-altitude locations, and of course, manage the extreme weather,” he says with a grim smile.
The supply of material from remote locations to the site using the nearest approach roads adds another layer of complexity to Planning Manager, Dave Kaushal Parag’s life, for sometimes they must negotiate an elevation difference of 600 m from the nearest motorable road. “Head loading of conductors, hardware fittings, construction materials, tools, and the like require a different set of skills compared to the specialized labour needed for the core activities of the project,” he points out. Coordinating and synchronizing the efforts of these two teams, coming from distinct geographical and skill backgrounds, is yet another challenge for the site team.
Head loading of conductors, hardware fittings, construction materials, tools, and the like require a different set of skills compared to the specialized labour needed for the core activities of the project.
Dave Kaushal Parag
Planning Manager
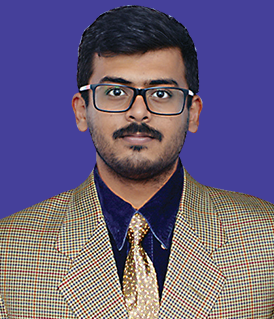
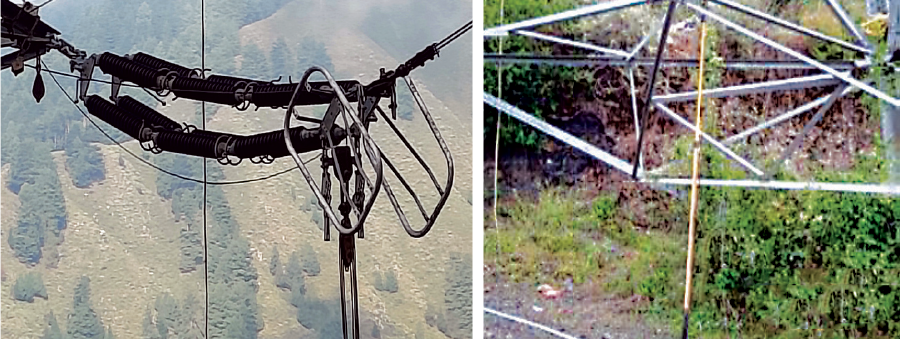
Grounding of conductors and tower using discharge rods
Adding to all these has been the issue of getting shutdowns to work safely. Since the first circuit of the line was already connected to the Dulhasti Hydro Power Plant, the Regional Load Dispatch Centre (RLDC) has often denied granting shutdowns to the team due to the increased demand for power during the summer season and increased water inflow from melting snow.
With their challenges well defined & understood, the team had to seek and find proactive methods to overcome these hurdles like completing the lion’s share of the work during favourable weather conditions and engaging with select suppliers to secure special tools capable of reducing the induction current from the ‘live’ first circuit. “After extensive consultations with our management, we prepared a detailed safe work methodology, which was approved by both competent authorities and the client,” apprises Parag.
Working smart. Working safe.
“We must continuously think innovatively, be it live line stringing with the first circuit in a charged condition, crossing distribution lines without shutdown, optimizing the head loading process, or even improving material handling, with safety always at the forefront,” comments Mohan. “We have implemented a live-line stringing methodology, grounding of tower members, aluminium conductors, and diesel operated winch machines by discharge rods to eliminate induction current.”
The team has deployed specialized safety gears such as dielectric safety belts (to protect workmen from electrical shock), webbing-type retractable fall arrestors, & specialized discharge rods. In addition, administrative control measures such as Daily Work Plans in the SHEILD App, filling working at height checklists before starting daily work, issuing height work tokens to height work fitters and registering their names in height work registers ensure discipline & safety. Daily work plans are closed at the end of every day.
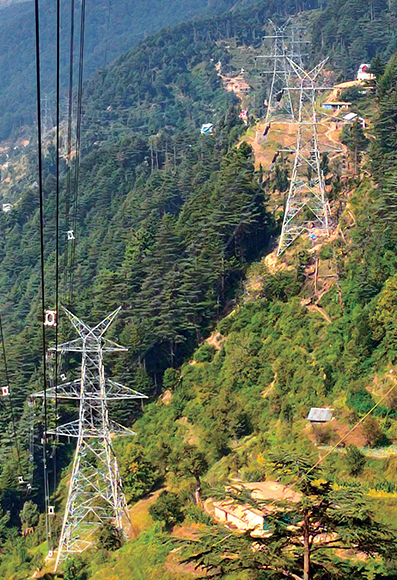
Given the challenging terrain, manual work was inevitable, and hence the team ensures that workers are trained in ergonomic lifting techniques, using safety equipment properly, and strictly adhering to safety guidelines to avoid accidents and ensure a safe working environment. To ensure that the right people are doing the right work, height work fitters are selected based on acrophobia tests using the vertigo tower at the store. Pre-employment medical checks are conducted too.
One can only imagine the pressure on EHS In-charge, Nihar Ranjan Das, to keep men & material safe in such challenging conditions, but his approach is methodical and measured. “We started with a detailed plan, including site analysis, terrain challenges, material logistics and risk assessments to identify and mitigate potential hazards before they arise,” he states wisely. “Our teams are well-trained, and we prioritize clear communication at every level. Each team member knows their role and understands the importance of following safety protocols. Collaboration and teamwork ensure that all tasks are completed efficiently and safely.”
We started with a detailed plan, including site analysis, terrain challenges, material logistics and risk assessments to identify and mitigate potential hazards before they arise.
Nihar Ranjan Das
EHS In-charge
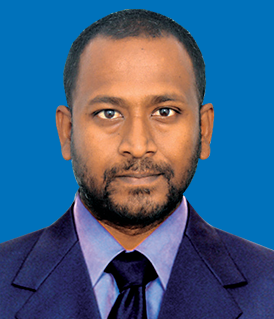
Ensuring that site staff arrive on time is critical to implement all the necessary safety measures. Timely access to these high-elevation sites enables the team to conduct thorough safety inspections and prepare the work area, thereby minimizing risks and ensuring compliance with safety protocols before operations commence.
Communication is vital in the terrains they are operating to disseminate training materials and safety protocols for the specialized equipment and techniques the team has adopted. By keeping their team members well trained & well informed about the safety measures, risks associated with working at heights and in hazardous weather conditions have been minimized to the extent possible.
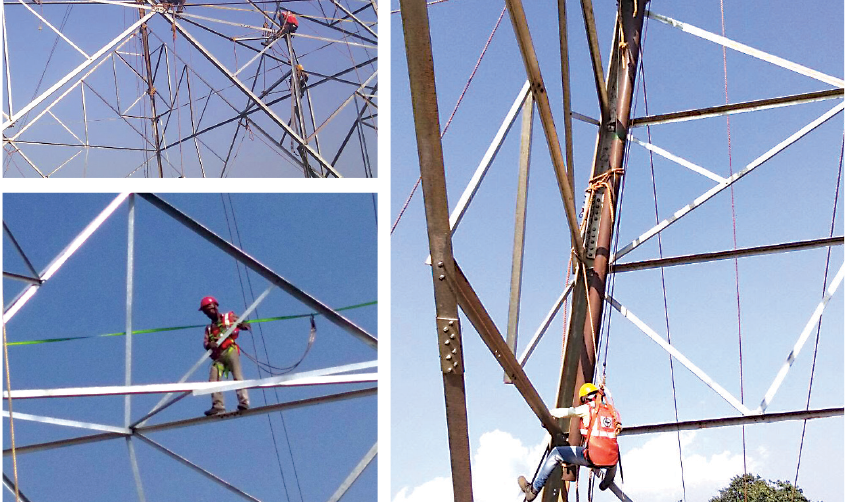
Using vertical lifelines and rope grab type fall arresters by fitters
Feedback is just as vital for engineers & workers to share their insights and challenges with the management, to facilitate continuous improvement. “This feedback is crucial to refine our safe work methodologies and ensure that they meet the demands of the project environment,” adds Nihar, who is delighted that the KDTL Project has already clocked 0.5 million safe manhours and won a RoSPA Gold to boot. Another matter of pride for the team is the Quality Trophy they have won in the Special Category.
“At times, we face critical RoW issues resulting in idling of gangs and disruptions to distribution lines, but despite all these uphill struggles, we have completed 35 km of live line stringing without interrupting the national grid or power supply across the country,” shares an extremely pleased Mohan. “What’s more, our client is enthusiastic about our adaptability and effective resource management.” The challenge before Mohan and his hardy team is to keep their clean record intact and deliver the project in time, maintaining the best standards of safety & quality.