Defusing the threat of chlorine
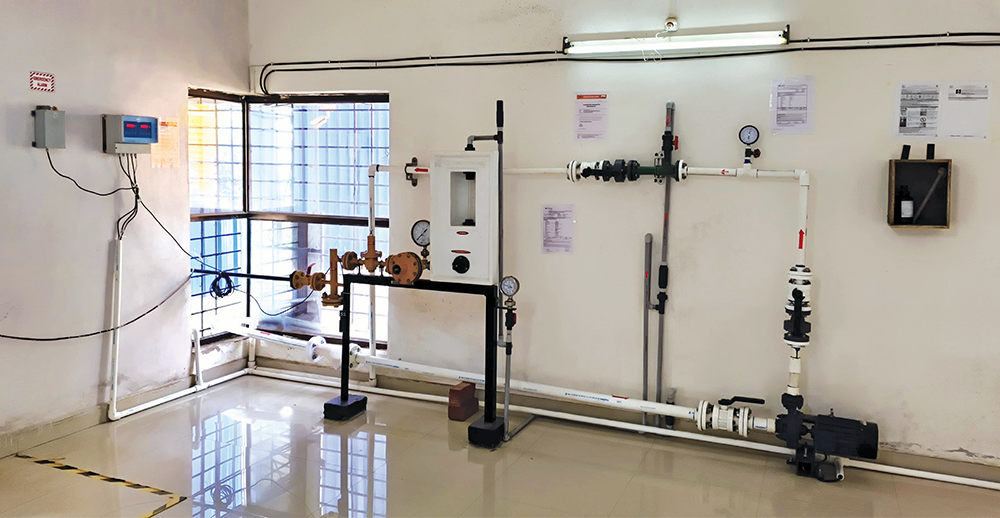
Vacuum feed gas chlorinator
Project Manager, Dheeraj K Ubhayakar, and his team are in the middle of executing WET IC’s 24×7 Belagavi DB O&M project that envisages cost-effective and sustainable upscaling of continuous (24×7) pressurized water supply to designated households in the city. Even as he and his EHS Officers, Dinesh S & Prasanna, focus on keeping their people & communities safe, one of their critical considerations is to ensure that the chlorine they use for its powerful disinfection properties to eliminate harmful pathogens is handled with care.
Keeping the risks associated with material handling in mind, we have prevented manual handling of tonner cylinders and installed a 2 T EOT crane to efficiently lift the 900 kg tonners.
Dheeraj K Ubhayakar
Project Manager
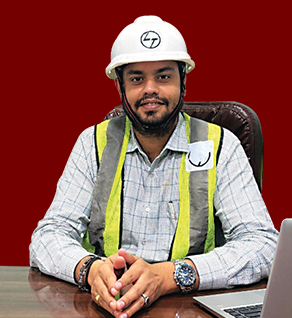
Another of Dheeraj’s counterparts, Project Manager, Hari Prasad, executing the 24×7 Hubballi Dharwad DB O&M that aims for 24×7 continuous water supply service delivery by revamping the water supply system with the introduction of water meters, payments of tariffs to generate revenue for municipal water service, conserving water and simultaneously improving service quality, faces the same pressure to prevent accidental chlorine leaks that can result in severe health hazards for all around. The onus therefore on Dheeraj, Hari Prasad and other project leaders is to establish & maintain stringent safety measures to prevent any chlroine-related mishaps.
Handle with care
Careful storage of chlorine is key, with proper ventilation, away from direct sunlight and incompatible substances like ammonia and hydrocarbons. Chlorine tonners and cylinders require careful inspection, adherence to detailed checklists, and specialized equipment to ensure safe movement and placement, always placed upright, and handled only by qualified personnel.
“Keeping the risks associated with material handling in mind, we have prevented manual handling of tonner cylinders and installed a 2 T EOT crane to efficiently lift the 900 kg tonners,” explains Dheeraj, adding that the crane is attached with spreader beams for stable lifting.
As per legal requirements and the Gas Cylinder Rules, a license from PESO is required to store more than 5 cylinders / tonners. “A factory license for WTP operations as per Factories Rules and TPI Certificate for the EOT crane have been obtained,” informs EHSO, S Dinesh, from Belagavi. The crane is inspected every six months by competent authorities who approve pressure instruments with calibration certificates.
The use of SCBA, crowd management techniques, formation of citadel, implementation of wind sock for measuring wind speed, direction, humidity, and chlorine dispersion highlight our proactive approach.
K Sudheesh Kumar
Head EHS, WET IC
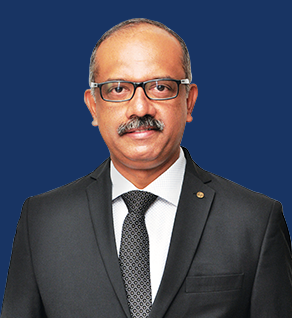
Effectively troubleshooting
Detecting and controlling chlorine leaks is critical for the safety of water treatment plants, for which chlorine safety systems are deployed across that include scrubber units and neutralization pits. While the former efficiently scrub chlorine gas from the air, using chemical reactions to neutralize harmful emissions before releasing clean air, neutralization pits placed near the chlorination site and chlorine storage areas are designed with a sloped surface to allow defective chlorine cylinders or tonners to quickly roll into an alkali solution, fully immersing them to neutralize the chlorine.
These systems alert personnel and activate emergency services, and the rapid response is critical in areas that are not continuously staffed. Chlorine detectors are designed to function both during operations and when the chlorination process is offline. “If a leak is detected, the system immediately triggers alarms, engages mechanical ventilation, and even shuts off the isolation valves, if installed,” points out K Sudheesh Kumar, Head – EHS, WET IC. “These detectors are supplemented by periodic manual tests like the ammonia torch and silver nitrate tests.”
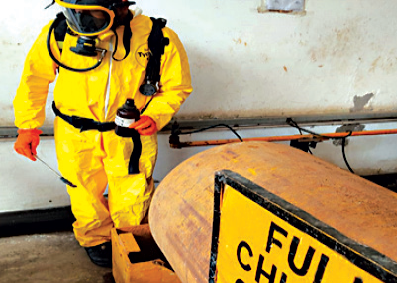
Ammonia torch test
Project Manager, Sandeep Manglik, at the Bhagirathi Water Treatment Plant ensures that all safety arrangements are in place to meet any chlorine-related eventuality, which includes an on-site emergency plan, took kits, leak detectors, self-contained breathing apparatus (SCBA), a neutralization pit, scrubber, siren & communication systems, a tagging system for equipment, first aid, & exhaust fans. “We have facilities to test pressure vessels, chlorine lines, etc.,” he adds to his growing list, “conduct regular training and mock drills, provide protective hoods for ton-containers, have fire extinguishers, windsock and cautionary placards in the local language.”
Chlorine safety is a top priority and our comprehensive Emergency Evacuation Procedure is led by a dedicated Emergency Response Committee (ERC) involving swift coordination between the Emergency Controller, EHS Officer, and Fire Chief.
Sandeep Manglik
Project Manager
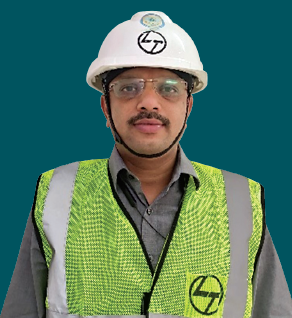
A Vacuum Feed Chlorine Dosing System has been deployed at the Belagavi site to feed chlorine into the water system, replacing the older methods.
The emergency evacuation strategy
“Chlorine safety is a top priority,” reminds Sandeep, “and our comprehensive Emergency Evacuation Procedure is led by a dedicated Emergency Response Committee (ERC) involving swift coordination between the Emergency Controller, EHS Officer, and Fire Chief.”
A key feature of this strategy is the mobile Command Post (CP), strategically positioned based on the wind direction to monitor operations safely. “The use of SCBA, crowd management techniques, formation of citadel, implementation of wind sock for measuring wind speed, direction, humidity, and chlorine dispersion, highlight our proactive approach,” elaborates Sudheesh. Rescue operations are conducted exclusively by trained professionals, ensuring that affected personnel are decontaminated and given prompt medical attention.
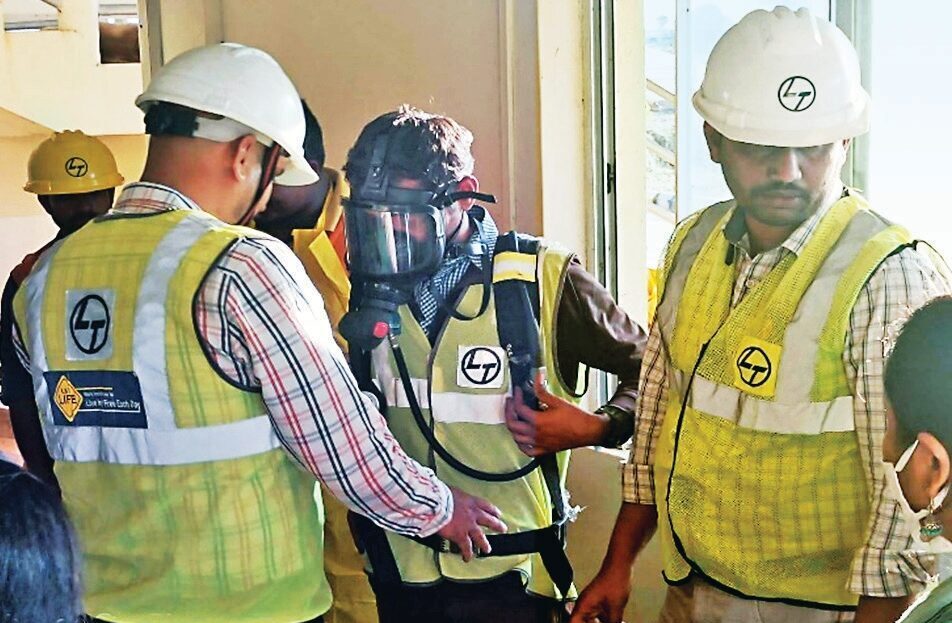
Training on proper usage of SCBA
With no known antidote for chlorine exposure, quick first aid is a critical response to remove the chlorine from the body and provide supportive medical care. Dheeraj’s list of preventive measures includes compressed oxygen, forced-oxygen masks, soap, water, saline, and specialized solutions like D5W (a dextrose solution), Ringer’s lactate, and sodium bicarbonate.

Training on chlorine storage & handling safety imparted to site staff by a certified expert
Both Sandeep & Dheeraj underline the proper use of PPE to prevent exposure. All operators are equipped with individually fitted full-sight gas masks with airtight sealed chlorine-specific filters. Operations involving chlorine containers are further safeguarded with protective suits paired with compressedair respirators, always ensuring that a minimum of two suits are readily available at any facility handling large quantities of chlorine. Stored outside chlorine rooms, all the protective gear is easily accessible, in dust- and moisture-protected areas.
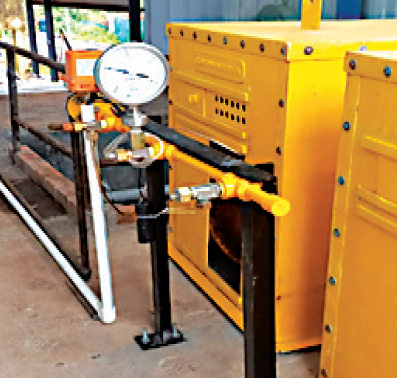
Chlorine gas leakage detector
Additionally, eyes and face must be protected by chemical safety goggles and, where necessary, face shields. Skin protection is equally important, with chemical-resistant gloves, aprons, and boots, while high-risk operations call for full-body encapsulating suits and SCBA. The choice of materials, such as butyl and neoprene rubber, further enhances the effectiveness of this protective equipment.
By addressing the gaps, providing proper equipment, training, and safety protocols, Sudheesh is breathing easy that adequate steps have been taken to keep WTP operations free of chlorinerelated. “More than just preventing incidents, we have fostered a strong safety culture that should stand us in good stead to promote our operational efficiency too,” he sums up.