Executing in the desert, without compromising on safety
RDSS Bikaner Project
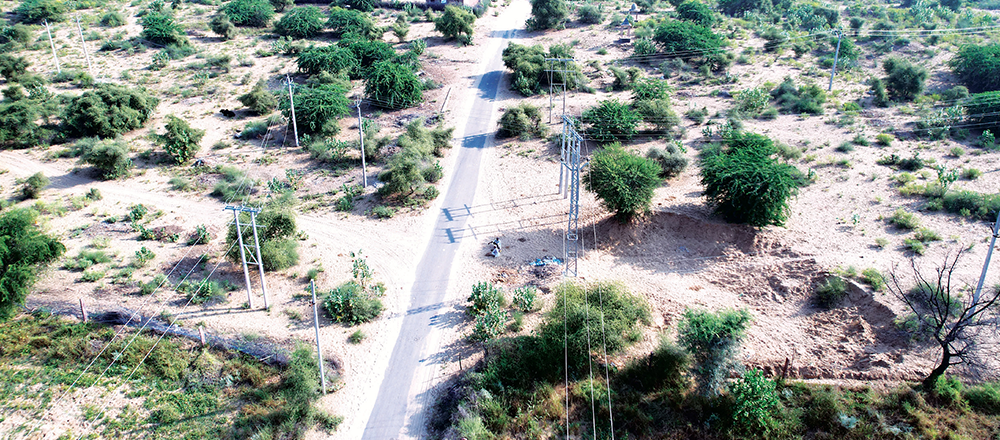
Awarded by the Jodhpur Vidyut Vitran Nigam Limited, the RDSS Bikaner Project being executed by PT&D focuses on the development of distribution infrastructure on a turnkey basis aimed to reduce loss, enhance operational efficiency, and promote financial sustainability in Rajasthan’s Bikaner district. The team’s scope includes constructing fifteen 33/11 kV Gantry Substations, 33 & 11 kV feeder lines involving 3,611 circuit km & 94,545 pole erections, 123 km of underground cabling, 444 km of LT AN cabling, 5 EV charging stations, 1,486 DTR installations & 410 circuit km of LT line apart from 1,170 shutdowns.
Prepared to succeed whatever it takes
Constructing in Rajasthan’s fourth-largest district with a desert area of 30,247 sq.km, Project Manager, Santosh Dhara and team are working in desert-like conditions: intense heat and cold, sandstorms, and a sand dune terrain that makes it difficult to navigate & manage worksites. Apart from their site being scattered, they work with the persistent danger of being close to high voltage lines, having to manage frequent shutdowns, handle Right of Way issues and suffer labour pains caused both by the rapid churn of workers and the lack of skilled labour.
Managing the safety of our approximately 300 employees and workers across such a widespread site calls for meticulous planning, constant monitoring, and strict enforcement of safety protocols to ensure the safe execution of the various activities, for which we have established and maintain a comprehensive safety procedure.
Santosh Dhara
Project Manager
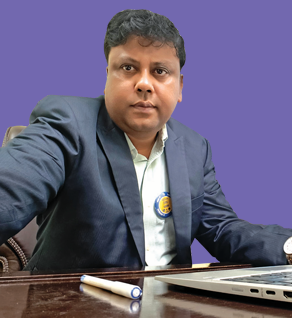
“Managing the safety of our approximately 300 employees and workers across such a widespread site calls for meticulous planning, constant monitoring, and strict enforcement of safety protocols to ensure the safe execution of the various activities, or which we have established and maintain a comprehensive safety procedure,” says a stern-faced Santosh. “We ensure 100% EHS induction and frequent Behaviour-Based Safety (BBS) training sessions to familiarize all the new workers with our safety protocols.”
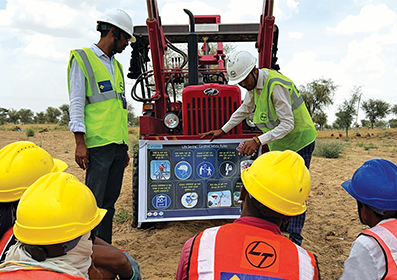
Adjusted work hours and hydration protocols help people tolerate the harsh weather, while special attention is given to keep workers safe from the hazards associated with high-voltage lines. “Our operational complexities are compounded due to the high turnover of subcontractor workers, making it extremely difficult for us to adhere to the strict SOPs while managing multiple electrical sources,” Santosh shakes his head. “Ensuring that all workers, particularly those from subcontractors, comply with our safety protocols is a constant struggle,” he grimaces.
One of EHS In-charge, Mukesh Kumar’s main challenges is to convert workers who are indifferent towards EHS into strong advocates. “My task is tougher owing to the scattered locations and the diversity of the workforce, which includes many workers from unorganized companies or small subcontractors who lack prior safety training,” he informs. “This requires continuous engagement and negotiation, adding another layer of complexity to our operational efforts.”
We have established and adhere to a dedicated Permit to Work (PTW) system, which includes Shutdown Clearance Permits, permits for work between site engineers and subcontractor supervisors, Hot Work Permits, Work at Height Permits, and Excavation Clearance Permits.
Mukesh Kumar
EHS In-charge
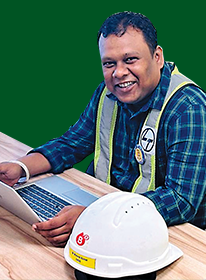
One way to overcome the issue of constantly inducting new workers is to keep training & re-training them, and the team has made available training programmes on HIRA, work activity SOPs, training in BBS, defensive driving, e-learning, with VR sessions conducted according to the training calendar after assessing individual training needs. HIRA has been performed for all work activities of the project.
250+ shutdowns negotiated safely
By its very nature, shutdown & non-shutdown activities are integral to the RDSS Bikaner Project. For shutdown tasks, the line survey and PTP preparation are completed 60 hours before execution, and 18 hours in advance for non-shutdown tasks. The Pre-Task Plan is then uploaded to the SHEILD App by the Site Engineer for the approval of the Section In-charge and EHS In-charge. “Anticipating client pressure to complete critical tasks urgently, we have developed an Emergency Shutdown and an Emergency Non-Shutdown Pre-Task Plan,” states Santosh, who is thankful that the client supports him to ensure proper power isolation to create a safe battery limit area. In the SHEILD App, the Cluster Operations Head/ Chief Project Manager serves as the final approver for emergency shutdown work plans, while the Project Manager holds final approval authority for emergency non-shutdown work plans before execution.
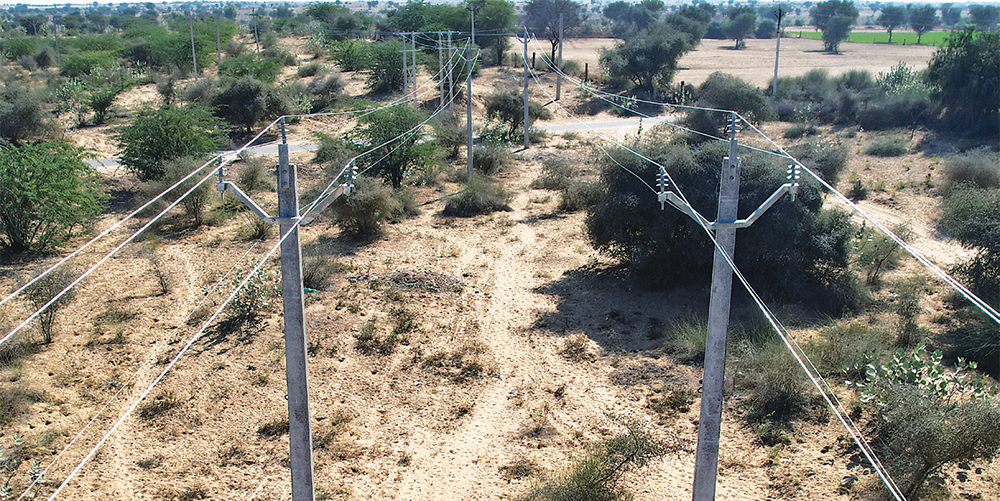
“We have established and adhere to a dedicated Permit to Work (PTW) system, which includes Shutdown Clearance Permits, permits for work between site engineers and subcontractor supervisors, Hot Work Permits, Work at Height Permits, and Excavation Clearance Permits,” informs Mukesh. To protect the workers from the danger of electrocution, the team has deployed measures like HMIT, Pen-Type Induction Testers, HV testers, 11 kV grade rubber gloves, FRP ladders and Lockout/Tagout (LOTO) procedures at the main isolation points. A hooter in the pole master is an engineering control to alert the working gang not to go near the augur when it is in operation. The siren will start hooting once the augur starts rotating for pole pit excavation and stops when the augur stops.
“Additionally, we short-circuit and earth existing HT and LT underground cables and the HT and LT bushings of distribution transformers using heavy-duty shorting clips to prevent back feed,” explains Mukesh. “We also place extra discharge rods near work areas and on metal structures of GOS and DTR to ground any leakage current within our safe work zone.” He is pleased that since the start of the project, they have successfully completed over 250 safe shutdowns, and to prevent unauthorized shutdowns, have implemented a One-Time Password (OTP) system.
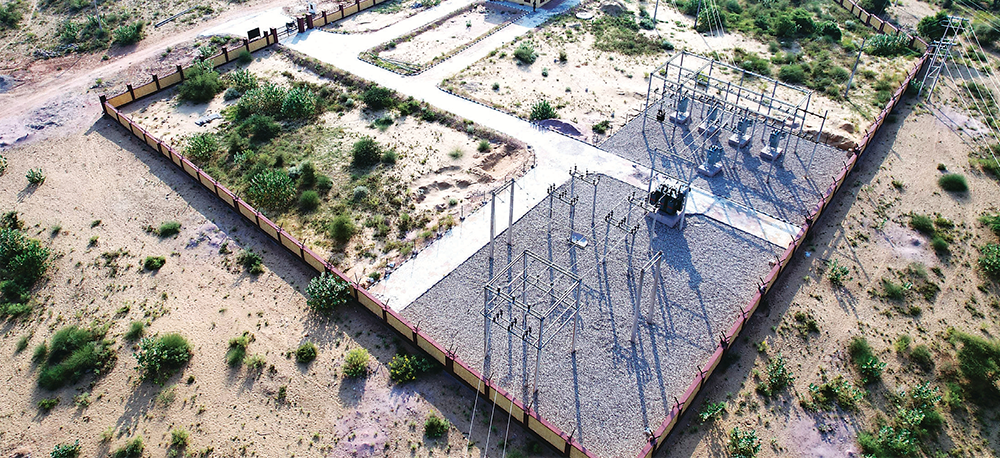
Ticking all the other safety boxes
By accurately forecasting job requirements & manpower deployment, the team is ready with sufficient supplies of PPE & safety equipment and follow a 4-colour system to categorize workers. The team’s Daily EHS Report includes all the necessary checklists, permits, attendance records, and token issuance forms. Regular EHS audits, including cross-BU EHS audits, internal audits, and surprise inspections are conducted across business units, and based on the findings, corrective actions are implemented.
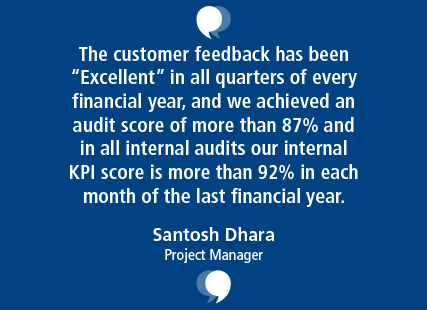
The project EHS committee and client representatives conduct weekly EHS walkdowns to demonstrate the management’s commitment to safety, while weekly meetings are held by the project EHS committee, bringing together committee members, the project team and subcontractor representatives. “This forum allows them to discuss and address all EHS-related topics, enhancing their understanding of the project’s EHS management system requirements,” adds Santosh. The WISA App has streamlined worker screening, induction & attendance tracking and the GPS-enabled Safe Start and Safe Stop communication system allows site engineers to grant permission for safe work commencement to subcontractors, who are prohibited to proceed if they receive a ‘Safe to Stop’ message.
Santosh, Mukesh and team are delighted that despite all these huge hurdles, they have held firm to clock 0.34 safe million manhours since inception. “We have successfully completed two internal cross-BU EHS audits, two surprise audits with minor NCRs and observations,” says Santosh in conclusion. “The customer feedback has been ‘Excellent’ in all quarters of every financial year, and we achieved an audit score of more than 87% and in all internal audits our internal KPI score is more than 92% in each month of the last financial year. The numbers do tell a story in our effort to achieve our goal of Mission Zero Harm,” he signs off rousingly.