Greening many extra miles
The Meerut–Aligarh–Ghaziabad Road Project
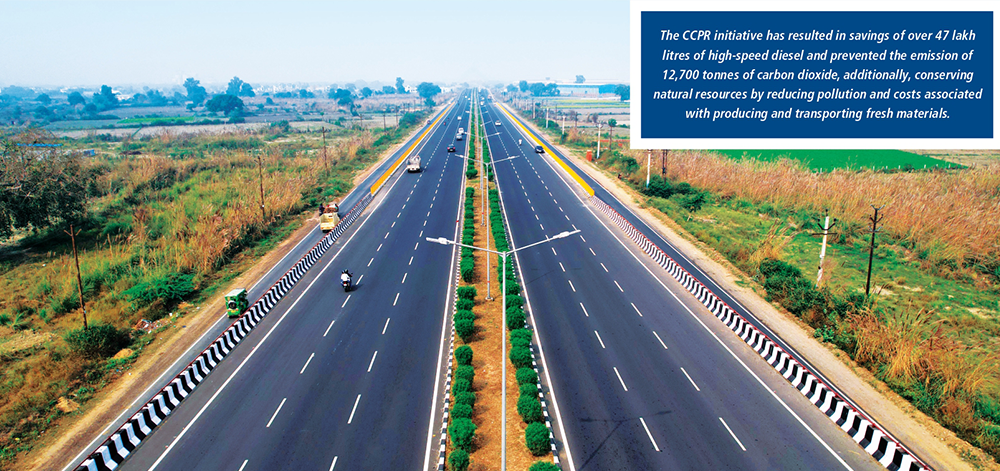
L&T’s ESG framework focuses on three critical areas: environmental stewardship, social responsibility, and governance excellence, and by integrating these principles into their core operations, the Meerut–Aligarh– Ghaziabad Road Project team have ensured that they not only meet regulatory requirements but go beyond to set industry benchmarks.
In June 2022, TI IC secured a contract from M/s Cube Highways to expand the existing four-lane GhaziabadAligarh section of NH-34 in Uttar Pradesh to six lanes. Traditionally, road construction in India relies entirely on the hot-mix method, which involves producing bituminous mixes by heating fresh aggregates and bitumen to high temperatures – an energy-intensive and environmentally unfriendly process. However, by using Cold Central Plant Recycling (CCPR), the team has significantly reduced the reliance on hot-mix bituminous material and considerably mitigated ecological damage.
“The CCPR technology is a sustainable approach to asphalt pavement rehabilitation and one of the standout features of our project,” beams Project Manager, Neeraj Kumar Garg, who is still basking in the glory of acing Mission 100 in 100 and setting a World Record in the process. “This innovative technique involves the reuse of existing pavement materials, which are processed and treated on-site to create a high-quality base layer for the new pavement,” he explains. By significantly reducing the need for new raw materials, it conserves natural resources and helps reduce the overall carbon footprint of the project. “What’s more, it enhances the structural integrity and lifespan of the road, to withstand the demanding traffic conditions expected on this route,” Neeraj adds.
The CCPR technology is a sustainable approach to asphalt pavement rehabilitation and one of the standout features of our project. This innovative technique involves the reuse of existing pavement materials, which are processed and treated on-site to create a high-quality base layer for the new pavement.
Neeraj Kumar Garg
Project Manager
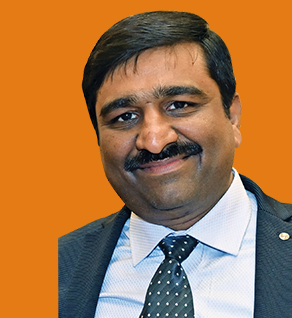
Elaborating on the CCPR process, Planning & Operations Head, Naveen Kumar Kanojia, says that the existing road aggregates are reclaimed, milled, screened into smaller fractions, and fed into CCPR plants set up along the project route. “We add supplementary new aggregates, water, cement, and bituminous emulsion to the reclaimed material to produce the cold mix, which is laid on a prepared surface and compacted to the required density.” After a three-day curing period, a dense bituminous macadam and bituminous concrete layer is laid over the CCPR layer, which considerably reduces the overall demand for hot-mix bituminous material. “Using CCPR, we have constructed approximately 87 km of highway, utilizing 90% reclaimed aggregates (about 5.48 lakh metric tonnes) from the existing road, while only 10% comprised fresh aggregates,” smiles a delighted Naveen.
Using CCPR, we have constructed approximately 87 km of highway, utilizing 90% reclaimed aggregates (about 5.48 lakh metric tonnes) from the existing road, while only 10% comprised fresh aggregates.
Naveen Kumar Kanojia
Planning & Operations Head
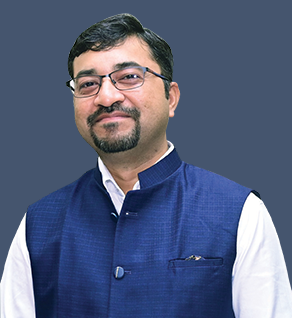
The CCPR initiative has resulted in savings of over 47 lakh litres of high-speed diesel and prevented the emission of 12,700 tonnes of carbon dioxide, additionally conserving natural resources by reducing pollution and costs associated with producing and transporting fresh materials.

Scalable, replicable, and sustainable, this pioneering effort by Neeraj and his team earned them the National Environment Award from the Global Safety Summit in 2022 and the Global Sustainability Award 2023 from the Energy and Environment Foundation, India. The constructed six-lane highway has also been declared the Green Highway of the Year by Progression Global, India, in 2024.
Salient features
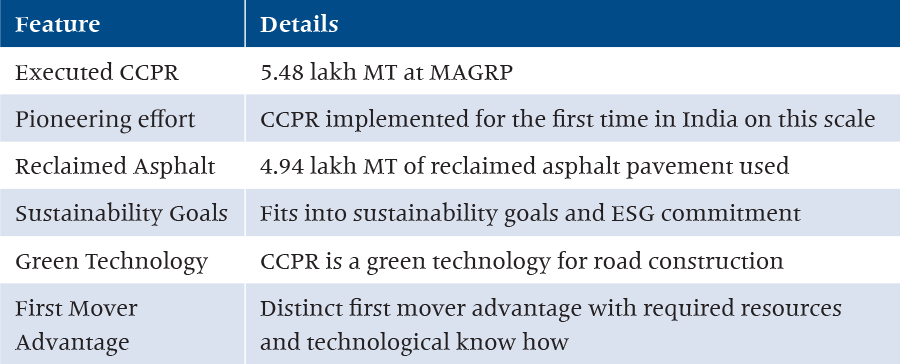
L&T’s ongoing commitment to sustainability is not just a strategic choice but a reflection of our values and dedication to creating a better world for future generations.