Operational Control Procedures (OCPs) ushering in a new EHS order
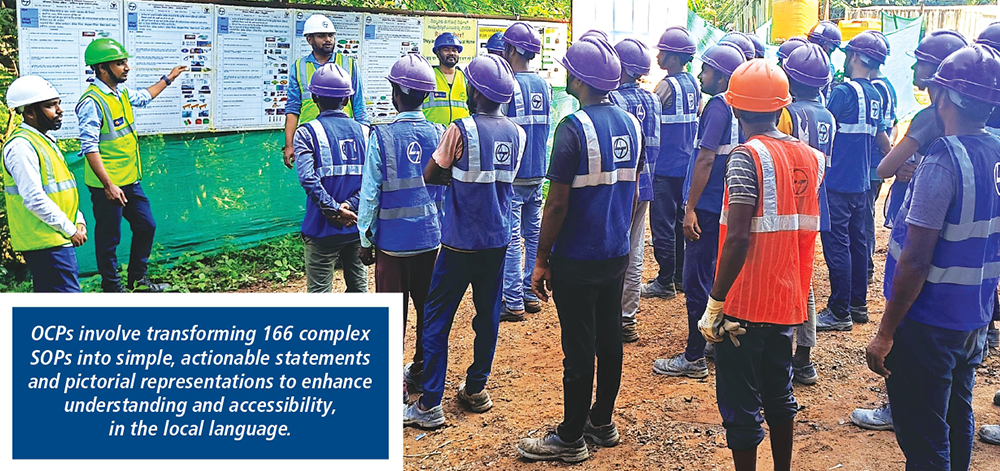
Unsafe acts & conditions at the workplace endanger the workforce and adversely impact productivity & morale too, which demands a thorough analysis of site conditions and a structured approach to mitigate risks by establishing clear procedures and behavioural guidelines. Enter Operational Control Procedures (OCPs) that aim to not only improve Safety at sites but also help maintain a strong EHS culture.
Evolving & rolling out OCPs
“To begin with, we arrived at a comprehensive set of 81 OCPs after analysing 10 years of observations using ML/NLP technique for designing minimum engineering and procedural control measures tailored to the unique needs of our workforce,” explains K Sudheesh Kumar, Head – EHS, WET IC. OCPs involve transforming 166 complex SOPs into simple, actionable statements and pictorial representations to enhance understanding and accessibility, in the local language to communicate better. “Additionally, our training sessions about OCPs include behaviour-based safety (BBS) training to encourage safe practices,” he adds. Once OCPs are rolled out across project sites and employees & workers are armed with the communication material in their preferred language, it is imperative to monitor the effectiveness of the effort.
The success of OCPs lies primarily in the monitoring that paves the way for continuous improvement, reassessment of training needs based on data analysis and employee feedback, and the recognition programme that rewards individuals who demonstrate safe practices. It is certainly a win-win situation.
K Sudheesh Kumar
Head EHS, WET IC
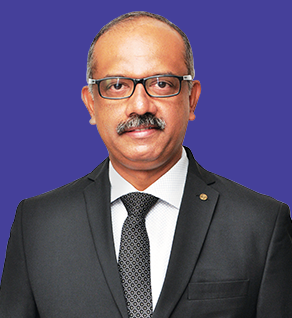
“There are acts with little or no danger, almost never resulting in injury, for the known risks are controlled and easily observed like driving with one’s hands on the steering wheel and eyes focused on the road,” points out Sudheesh. “Such behaviour should be positively reinforced.” However, there are dangerous acts that often result in injuries and can be identified with common sense and experience that are categorized as ‘unsafe’, with high probability to have a negative outcome (i.e., injury) with high severity potential. “Like taking one’s eyes off the road to check the mobile when diving fast. Such behaviour should be stopped,” he asserts.
The well-defined roll-out process starts with specifying the task/activity to be performed, identifying its location, drawing up a list of the expected safe behaviour (acts/conditions) to be followed, calculating the percentage of safe/unsafe behaviour and notifying them. Execution activities completed with 100% OCP implementations without any deviations/observations during & till completion are identified as safe behaviour, and one of the indicators to identify a Safety Cha mpion Worker or an EHS Ambassador Site Engineer. Unsafe behaviour is when there are deviations, and the extent of risk potential is captured for corrective action.
Sudheesh says that the critical next step is to discuss with the worker or gang about their unsafe behaviour and resume work only after it is rectified. Training is equally important, with coaching, refresher courses and BBS training.
Proof of delivery
“OCPs bridge the language gap between engineers, supervisors, and workers with visual aids that ensure that everyone understands the task at hand, including any hazards and associated risks,” says a pleased Dheeraj K Ubhayakar, Project Manager, 24×7 Belagavi DB Project. “OCPs promote safety, reduce unsafe acts and conditions, ensure that everyone follows proper safety protocols, leading to a safer and more efficient work environment.”
OCPs bridge the language gap between engineers, supervisors, and workers with visual aids that ensure that everyone understands the task at hand, including any hazards and associated risks.
Dheeraj K Ubhayakar
Project Manager, 24×7 Belagavi DB
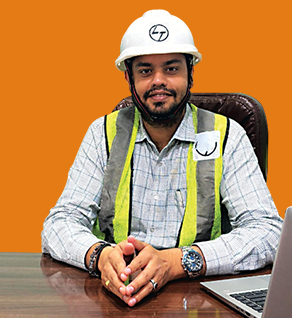
Life is easier now for G. Soma Sundaram, Project Manager, Rehab Works at Colombo, for instead of repeatedly returning to SOPs, OCPs are a quick reference tool to follow and implement all the EHS requirements. “Apart from the workforce getting a clear understanding of the step-by-step EHS requirements, the IM-34-E Behaviour reports are crucial monitoring tools to control unsafe behaviour,” adds his Senior EHS Manager, Goura Chandra Pradhan, who is obviously enjoying the fruits of OCP implementation.
By leveraging IM-34-E reports to monitor safe and unsafe behaviours, Rohit Sahay, Project Manager, at the SilautaMustakil and Chandi-Bangar WSS project has gained valuable insights into workforce practices. “OCPs are helping us identify areas requiring behavioural improvements and implement targeted training and corrective actions,” he points out. “This behavioural monitoring can be further enhanced through Gemba Walks conducted by Project Leaders from other sites and by directly observing work activities,” highlights Ashif Eqbal, EHS Manager, at the same site. “Leaders can assess behaviours firsthand, reinforce OCP adherence, and address unsafe practices immediately, and this active involvement not only ensures real-time corrective actions but also deepens their understanding of on-ground safety challenges.”
OCPs are helping us identify areas requiring behavioural improvements and implement targeted training and corrective actions.
Rohit Sahay
Project Manager, Silauta-Mustakil and
Chandi-Bangar WSS
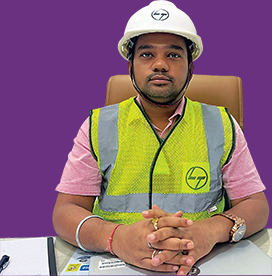
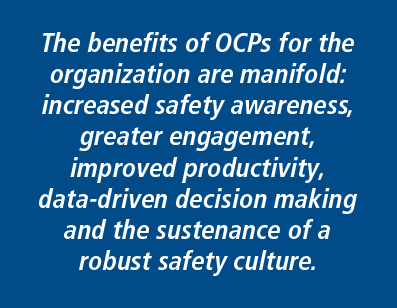
“The success of OCPs lies primarily in the monitoring that paves the way for continuous improvement, reassessment of training needs based on data analysis and employee feedback, and the recognition programme that rewards individuals who demonstrate safe practices,” summarizes Sudheesh. The benefits of OCPs for the organization are manifold: increased safety awareness, greater engagement, improved productivity, data-driven decision making and the sustenance of a robust safety culture. “It is certainly a win-win situation,” smiles Sudheesh, delighted with the new EHS order that OCPs are ushering in.