PT&D IC USHERS IN A NEW FORM OF REMOTE TESTING TO EXCEED CUSTOMER EXPECTATIONS
COVID-19 has disrupted global supply chains and brought about a paradigm shift in the way we do things. Even simple activities like taking a walk is now within confined spaces taking precautions never thought necessary before. In business, it has been all about adapting to the right mix of technologies to improve customer service and experience with minimum physical interactions and in the days to come, such channels of interfacing will be regular features in the ‘new normal.’
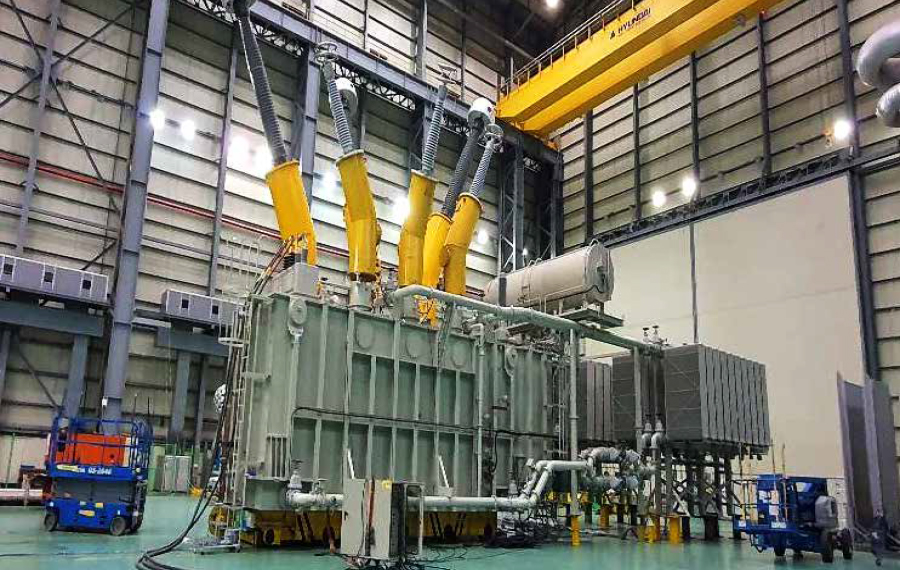
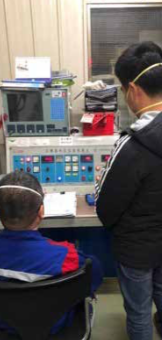
Ensuring productivity through connectivity
The Power Transmission & Distribution (PT&D) IC, the ‘COLOMBUS’ of L&T, with projects across various geographies, has developed some timely innovations for remote inspections at some of its ASEAN, Africa and Middle East projects during the lockdown. The Remote Factory Acceptance Test (RFAT) is a first-of-its-kind approach in the EPC segment with significant value advantages of zero cost, enhanced safety, transparency and flexibility and a considerable reduction in delivery time. Overall, the RFAT initiative has reinforced PT&D’s credentials as a leading EPC player with superior project management capabilities.
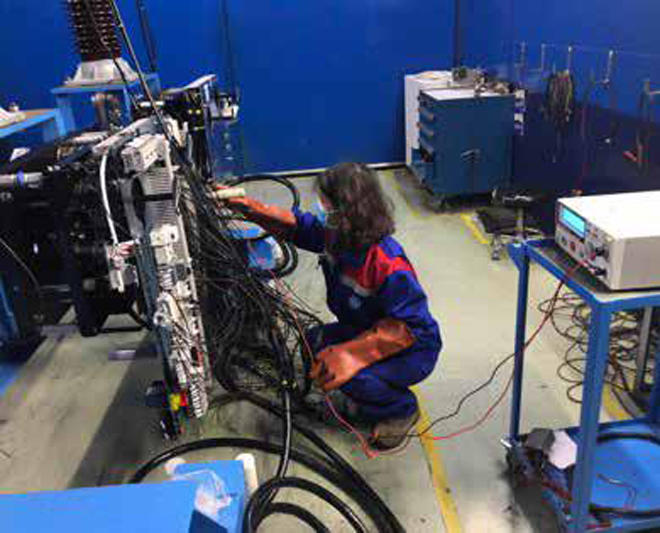
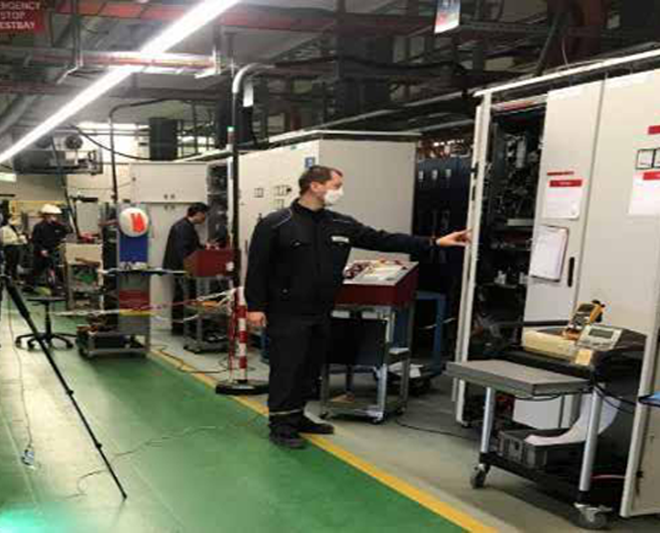
Synchronizing remote testing
J. Stalin Babu, Head ASEAN Cluster I, along with his digital team of Nikhil, Ajay and Kasiraj, have successfully completed 4 inspections and with their momentum, he is confident of repeating the feat, “We initially began RFAT for the Medamid to Lawas Town 275 kV transmission line project in Sawark, Malaysia. Having delivered significant power infrastructure projects in recent times, we had built credibility with the client, Sarawak Energy Bhd, and were able to convince them to opt for remote inspections. ” PT&D’s scope covered supply, erection, testing & commissioning of 131 km of double circuit line which involved raising 381 towers, supplying ACSR drake conductors, 6600 t of steel structures, 272 km of OPGW along with 130,000 toughened glass insulators and installing other accessories. The project had to be completed within a stringent timeline of 30 months given the undulated terrain traversing through a national forest reserve and along numerous villages with untitled lands.
“We initially began RFAT for the Medamid to Lawas Town 275 kV transmission line project in Sawark, Malaysia. A check list on the various tasks was prepared taking on board the OEM and the client before conducting the remote test. Once the sequence was finalized, the whole testing was completed seamlessly with a saving of 3 days!”
J. Stalin Babu
Head ASEAN Cluster I
With some catching up to do on the project front and the lockdown slowing down process, RFAT was a feasible option and a win-win situation for the client. “With our TLT factory in Puducherry as the inspection location, all fronts were covered, and we lined up the sequence and went through the process seamlessly to achieve a saving of 12 days.” Elaborating on the remote platform, Stalin informs, that it is like the connectivity of MS Team and depending on the OEM’s preference, the digital communication platform is finalized. A fixed number of cameras with laptops are installed to cover the activity while the approval is recorded from L&T’s side, keeping the client representative logged in.
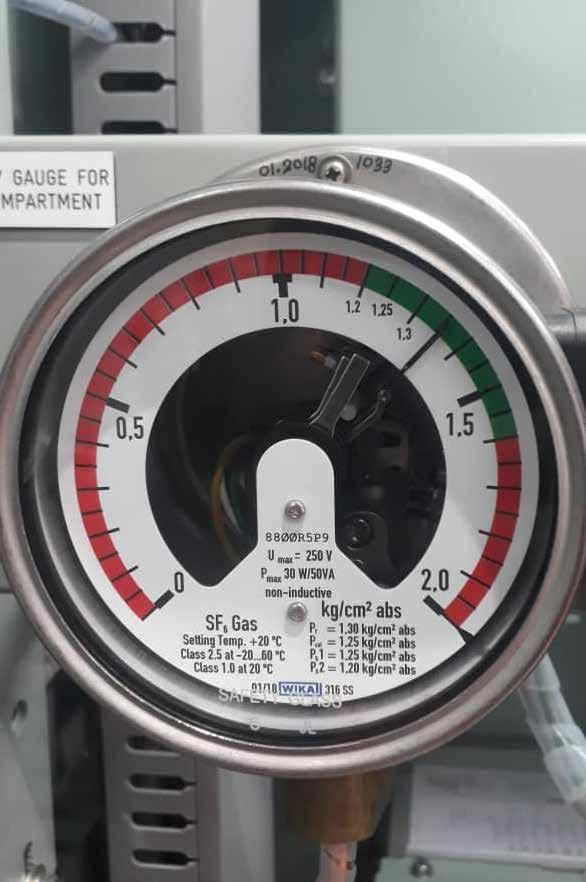
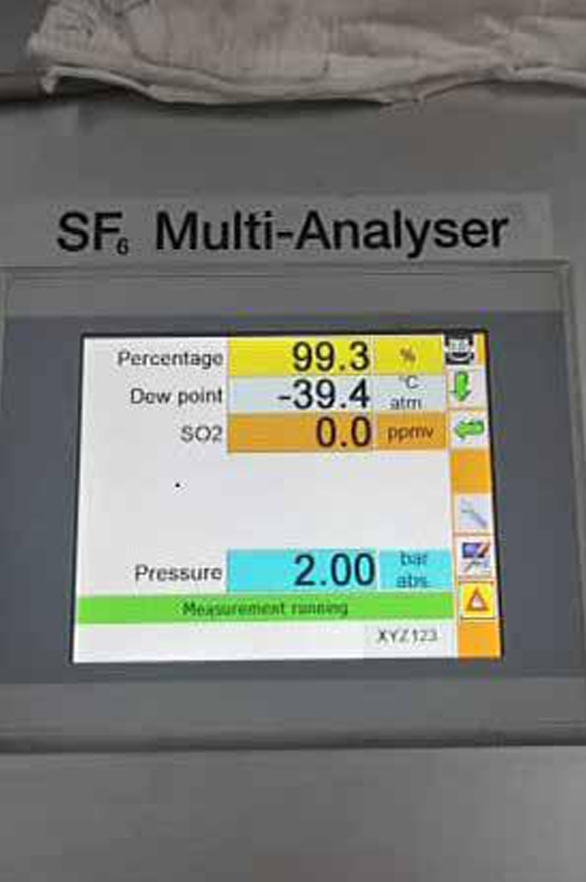
“Taking this initiative further, TLT Kancheepuram factory, successfully completed the proto structural inspection for
7 structures of the 275 kV Medamit to Lawas Transmission line -Malaysia through MS Teams,” shares Debasish Mukherjee, Head, TLT Factory, Kancheepuram.
While the tower testing was in control, the challenge was to clear the OPGW test with a vendor based at China’s Jiangsu Province. “The client was apprehensive as to how we could remotely test with the pandemic raging across China,” mentions Stalin. “Getting into specifics was the key and we quickly formed a team to connect with the vendor, ZTT International, who assured that despite the lockdown, their factory was secure and accessible. A check list on the various tasks was prepared taking on board the OEM and the client before conducting the remote test. Once the sequence was finalized, the whole testing was completed seamlessly with a saving of 3 days!”
“TLT Kancheepuram factory, successfully completed the proto structural inspection for 7 structures of the 275 kV Medamit to Lawas Transmission line.”
Debasish Mukherjee
Head, TLT Factory, Kancheepuram
Scaling up the process
Having made the initial breakthrough, Stalin and team were confident of scaling up the process for an elite project: the Matang 275/132/33 kV Substation at Kuching, Sarawak in East Malaysia. The client, Sarawak Energy, had reposed faith in L&T for the good work done in this region by awarding the fourth consecutive substation project within a span of four years since the inception of the ASEAN BU. L&T’s scope involved design, procurement, installation, testing & commissioning of the AIS substation with 275 kV & 132 kV outdoor air insulated switchgear units with double busbar arrangement, 2X240 MVA auto transformers, 275 kV cabling works, 33 kV cabling works, 33 kV GIS, complete 275 kV, 132 kV & 33 kV protection, control and communication system along with AC & DC system, retrofitting works related with 2X120 MVA power transformer and reactors and other accessories to undertake emerging load capacity in addition to the existing load of the old substation. The advantage here was that the factory was in Selangor, Malaysia and the 33 kV GIS material was tested within a day. However, the 275 kV and 132 kV Circuit Breakers were remote tested at the OEM’s premise in Suzhou, China, ensuring a saving of 5 days.
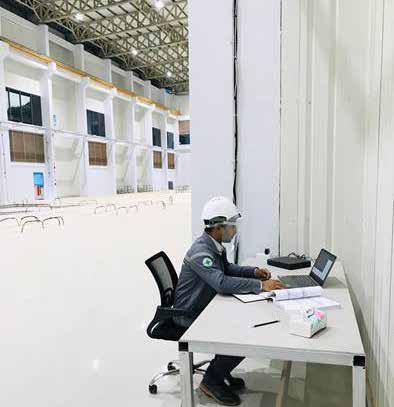
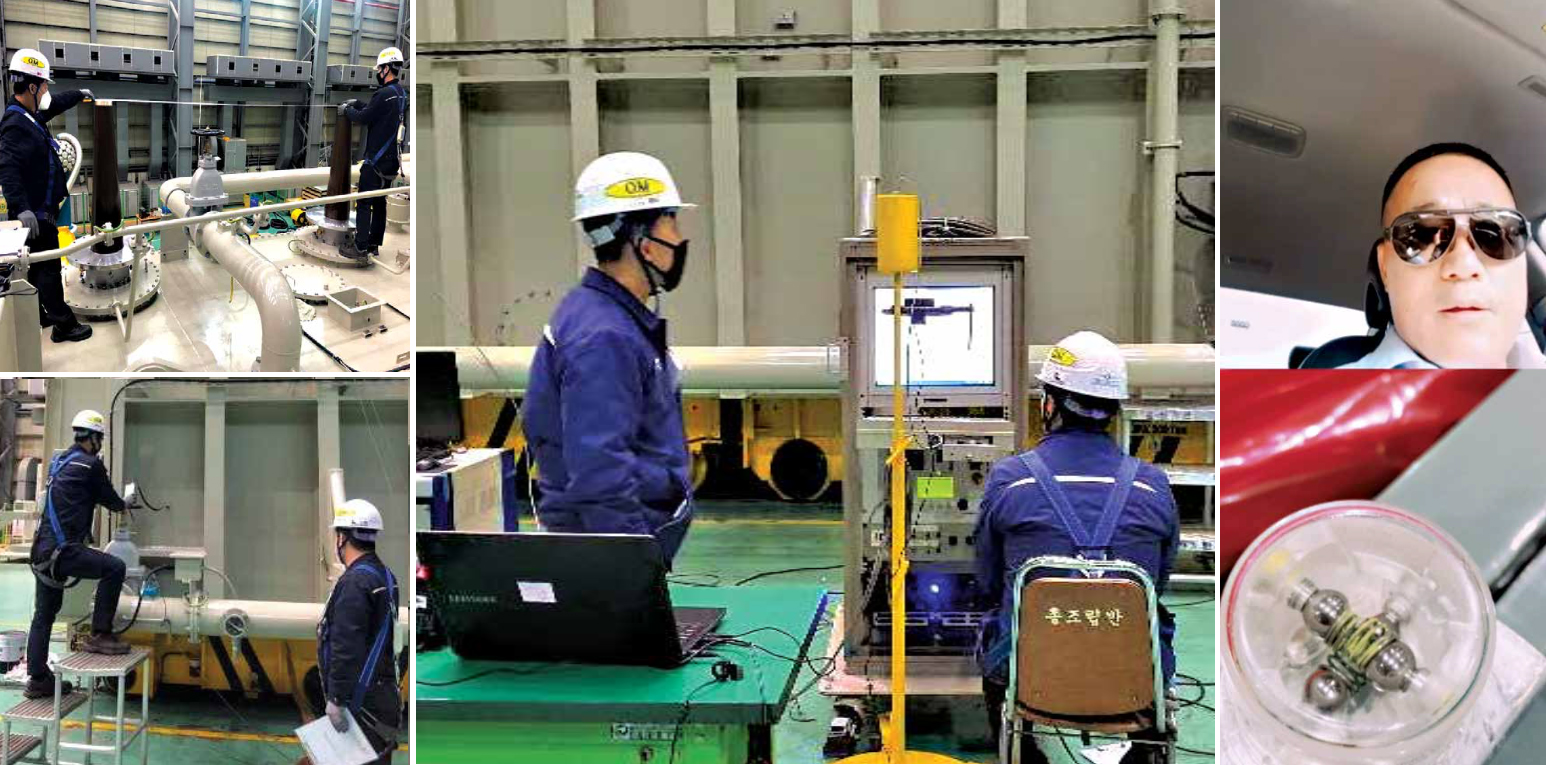
Raising the bar
Installing the 500 kV GIS was a critical milestone for the Surat Thani 2 Substation, mentions S. Suresh, Head ASEAN BU Cluster II. “When commissioned, it will be the largest transmission system in Thailand’s southern province and a key power hub in the national electricity grid. It is also the first 500 kV GIS project awarded to L&T outside India. ”It is the norm worldwide that the installation of GIS is undertaken only in the physical presence of an OEM supervisor, informs Suresh. “However, as the Korea-based OEM could not make it due to the travel restrictions, we needed an alternative plan to mitigate the delay. Moreover, since Thailand did not have a lockdown, our construction work proceeded in full swing taking all precautions.” Project Manager, B. Santhanam and his team, led by Anil Tomar, developed an alternative method for the Korean supervisor to inspect the works by formulating a SOP that covered the norms of setting up a virtual room with CCTV cameras, laptops and other essentials that could broadcast the feed to multiple locations.
“Remote Supervision of 500 kV GIS installation by the OEM has never been done in L&T and now with the SOP defined, up to 30% of the works can be completed through remote supervision while we eagerly await the shipment,” shares S. Suresh. “All through the process, our client, EGAT, has been very supportive.”
“Remote Supervision of 500 kV GIS installation by the OEM has never been done in L&T and now with the SOP defined, up to 30% of the works can be completed through remote supervision.”
S. Suresh
Head ASEAN BU Cluster II
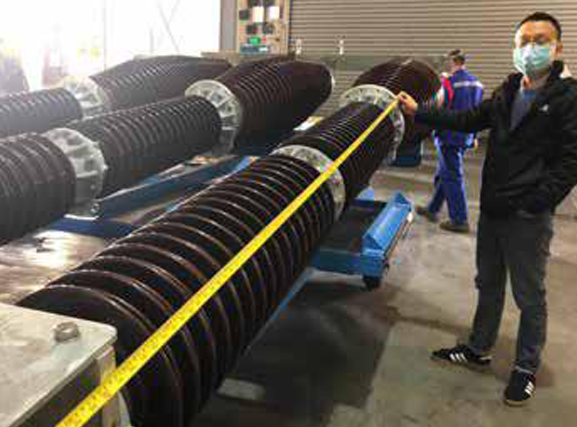
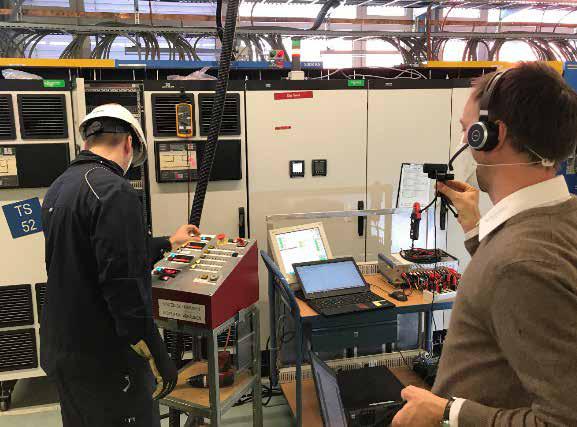
“Going forward, the client has issued a circular stating that all factory based testing should be through RFAT which is an acknowledgement of the value addition that L&T has created during these challenging times.”
Haroon Ali Kamal Mustafa
Engineering Manager, PT&D Middle East
Bridging the time factor
The process worked perfectly since the ASEAN region and China were in close proximity but the team anticipated challenges when operating from considerably different time zones involving larger equipment as was the case with the Middle East team for the remote testing of a 500 MVA Inter Connecting Transformer (ICT) for a 400/132 kV Substation at Dubai for DEWA. Taking us through the process, Haroon Ali Kamal Mustafa, Engineering Manager, explains, “Our Korea-based OEM was 5 hours ahead of Dubai and to sync the testing, we had to login by 4 am. It was a tough proposition but then there were no other options and the client was keen to complete the task. For the next nine days, the process continued with close to 32 schedules taken up according to priority.” From the OEM’s side, a CISCO communication platform facilitated the assessment with provision of 20-member logins and cameras fixed at the respective factory locations connected to the laptops while the off-field process was captured on mobile phones. “As our equipment was an ICT, there were many threshold tests conducted for various parameters and with the client onboard for the entire testing, this has been a highly successful initiative,” shares Haroon Ali Kamal Mustafa. “Going forward, the client has issued a circular stating that all factory-based testing should be through RFAT which is an acknowledgement of the value addition that L&T has made during these challenging times”.
“We completed tests at two remote locations in Switzerland and France connecting from HQ Chennai. Perhaps, this could be one of the longest remote factory tests undertaken with stakeholders participating from different regions. ”
S. Sankaravel
Chief Engineering Manager, (Electrical), EDRC
Going beyond boundaries
Adding might to the RFAT process are a few more milestones achieved across the African BU for Rehabilitation of Hassi Berkine Basin Project in Algeria. “We completed tests at two remote locations in Switzerland and France connecting from HQ Chennai,” informs S. Sankaravel, Chief Engineering Manager, (Electrical), “Perhaps, this could be one of the longest remote factory tests undertaken with stakeholders participating from different regions. From HQ EDRC, K. Ramachandar and T. Savithri, led one of the initiatives that involved testing of 4 DC batteries and charges over 4 days while the SCADA equipment testing for Central Control Station at GE’s factory was remotely monitored by A. Shankar over 3 days.”
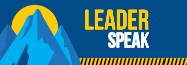
T. MADHAVA DAS
Senior Vice President & Head, Power Transmission & Distribution IC
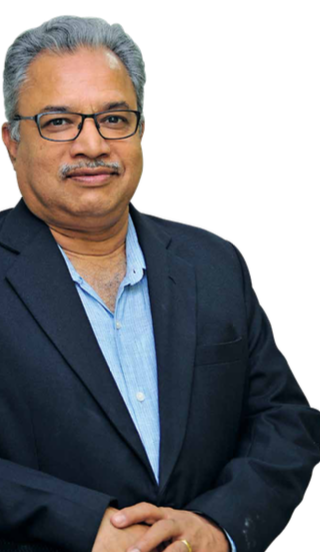
Maintaining customer relationships during such a crisis is always a challenge as in-person meetings do not happen. However, since customer centricity is deeply engrained in our culture, we overcame these challenges in our own way. As a digital frontrunner, we have done remote FATs and enabled remote project monitoring for our customers demonstrating that Digitalization is in our DNA and Result Orientation is in our RNA. Especially, since PT&D, is a supply intensive business with key projects, plants, partners, and players spread wide across the globe, these sort of initiatives are of great significance as customer experience truly gets elevated to the next level. They see us differently vis a vis our competitors and we are back to billing in quick time. And these are not one-time wonders. We are institutionalizing such practices to reap cost benefits. After all, it reverberates with our solution focus on Positivity, Profitability and Productivity during these testing times.