WET IC NAVIGATES ON A SAFE MODE ACROSS FRONTS
With several WET IC projects spread across states and districts, the challenges to mitigate the risks as the pandemic spread were unique. While the overarching need for all projects was to reinforce their safety environment, some required diverse safety strategies considering several local factors, as they focused on phase wise resumption of operations and also in continuing the essential services of delivering water to millions of people across the country.
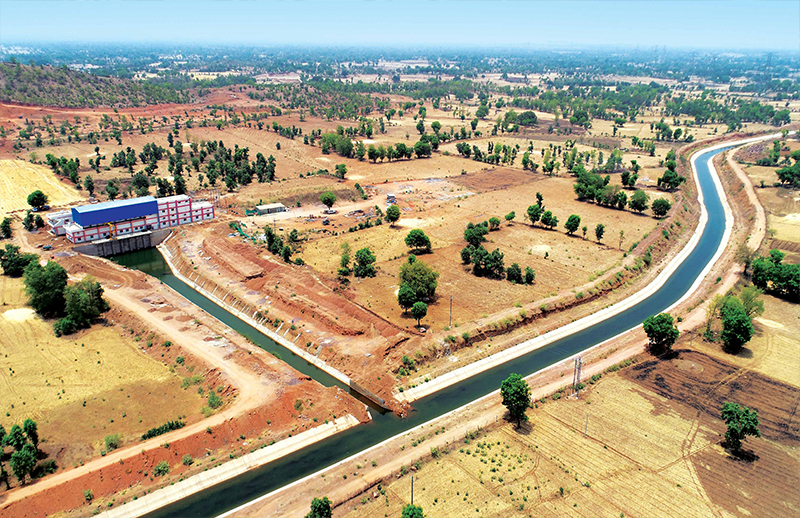
At the heart of a green channel
Several lift irrigation projects are at significant stages of execution and when completed will become game changers transforming arid zones into agrarian tracts. One such mega project is the ISP Kalisindh Phase 1 Micro Lift Irrigation Project where the onus on Project Director, S. Kumerasan, is to keep 1300 workmen and 84 employees safe and engaged across 5 districts. “Considering the spread of the project, we formed clusters with designated area wise in-charges to align to the SOPs and MHA guidelines ensuring that the requisite number of PPEs, hygiene kits were available across the camps. Teams led by S N Bhar – HeadAccounts & Admin, S G A Rizvi Head – IR, L Murugan Head – EHS along with Departmental /Section Heads have been at the forefront of this critical mission.”
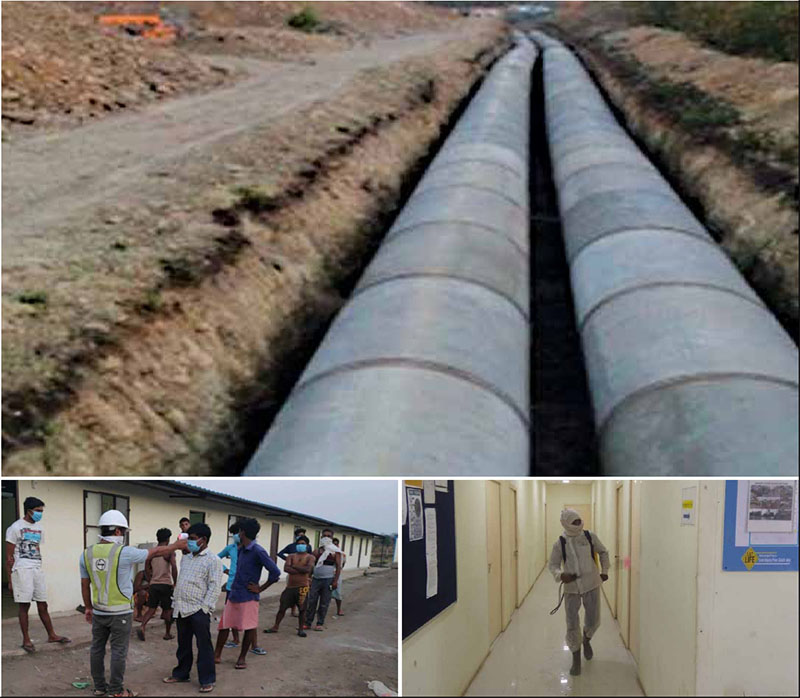
Thermal scanning of body temperature at workmen camp
One of their immediate concerns was to find a way to move across various zones to reach food and essential materials to the workmen camps. “With 21 locations to cover, movement was an issue due to the lockdown, but thanks to our networking with external stakeholders, timely permissions were obtained, and our core team members took up the task of delivery.” Kumaresan’s sense of achievement is evident. Apart from the core team, an Emergency Rescue Team served as a back-up unit to take care of the medical and other requirements of the staff and workmen. “Our success is attributable to the active participation of all our employees,” he highlights.
“With 21 locations to cover, movement was an issue due to the lockdown, but thanks to our networking with external stakeholders, timely permissions were obtained, and our core team members took up the task of delivery.”
S. Kumerasan
Project Director, ISP Kalisindh Phase 1 Micro Lift Irrigation Project
“As ours is a public infrastructure project, we often reach out to help the surrounding areas as part of our community initiatives that worked to our advantage during these challenging times,” he remarks. “We provided our vehicles to the SDM of Tehsil for their visits to the villages to make announcements and distribute food to those quarantined. Our team distributed sanitizers, gloves, and masks at the SDM office, police station and other government offices under the project area.” The team’s outreach efforts won the hearts of the local community as some farmers close to the pipe manufacturing facilities at Punjapura and Vikupura villages permitted the workmen to take fresh vegetables from their farms. “It was heartening to hear them acknowledge L&T’s effort towards building a green channel for their benefit,” shares Kumaresan.
The team had a strategy to deploy resources across various zones once the lockdown was eased and with the resumption of site operations, Kumaresan and team are continuing the battle, keeping a comprehensive safety vigil.
Being on the right track at the right bank
Another significant lift irrigation project is the Kundalia Right Bank Scheme in Madhya Pradesh. “With 764 workmen engaged across fronts, work was proceeding seamlessly but with the lockdown some firm decisions had to be taken quickly and early on,” says Project Manager, Dinesh Kharbanda. “At our first meeting on 20th March, an Emergency Response Team was formed and the ERT members went into action from day one as approvals had to be processed for vehicle movement to deliver essential requirements. It was only after 3 days of continuous follow-up that we received the passes but considering the regulations, it was empowerment at the right time for us to move on.”
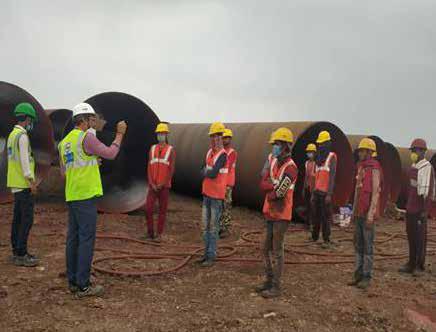
Pep talk before taking up a critical activity
“To the workmen, we conveyed a strong message of ‘We Care’ while our networking helped us to assess the situation, take proactive decisions and deal with various situations effectively.”
Dinesh Kharbanda
Project Manager, Kundalia Right Bank Scheme
With all essentials stocked at the camp, a dedicated team looked into the needs of the workmen, another networked with the bureaucracy that included the newly appointed District Collector to obtain various approvals while yet another team remained in constant touch with the police and village panchayats. “To the workmen, we conveyed a strong message of ‘We Care’ while our networking helped us to assess the situation, take proactive decisions and deal with various situations effectively.” Pep talks, awareness communication, regular medical check-ups kept the workmen healthy and in a positive frame of mind. Having safely sailed through the crisis, Dinesh and team resumed site operations on 23rd April with the District Collector’s approval with 55 staff and 400 workmen across select fronts and are hopeful that their workforce will grow as lockdown norms ease further.
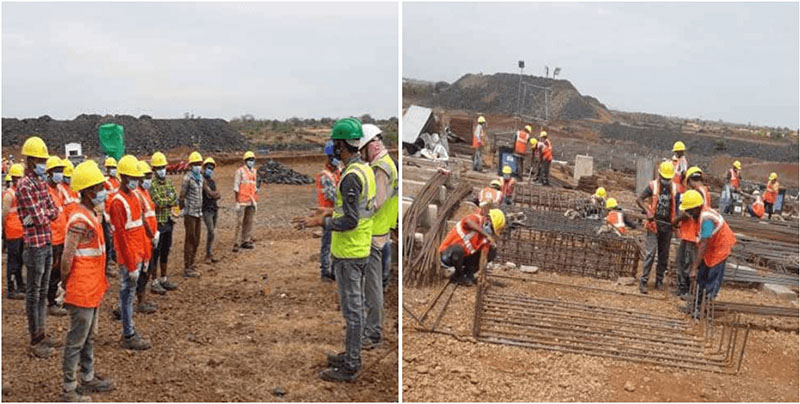
SOPs being briefed to workmen
But as the lockdown progressed, Srinivas started to sense signs of unrest. “Our workmen were from 14 different states and started to voice their concerns: “Kaam do nahi toh ghar janne do’. We assured them that we were confident of getting permissions to resume operations since our works were at a critical stage and project completion was going to benefit farmers in the coming Kharif season. To motivate the workforce, we also showed videos of the struggle faced by migrant workmen returning to their native places and requested them not to panic.”
“Thanks to our initiatives during the non-working period, we had the requisite manpower and resources to accelerate work across the balance 28 km of the canal. The good work has enabled us to collect payment for the work executed after resumption.”
S. Devanand
Project Director, Mega Lift Irrigation Scheme, Indravati Region
With the Ministry of Home Affairs granting permission to resume operations across major irrigation projects, the site commenced works from 20th April 2020. “Thanks to our initiatives during the non-working period, we had the requisite manpower and resources to accelerate work across the balance 28 km of the canal, well aware that the monsoon was just a couple of months away. The team is ensuring that execution is as per the SOPs and guidelines laid down by Government. Social distancing is being strictly implemented at all the site locations. In spite of all hurdles, the team has executed 37056 cum of canal excavation, 1781 cum of CC canal lining, 554 cum of concreting in the in lined canal structures and 17 km of distribution pipe laying in the first week after resuming site activities. The good work has enabled us to collect payment for the work executed after resumption.” For Devanand, it is another opportunity to be proud!
Taking control of a 900 sq.km area
S.S. Mani, Project Manager, at the twin projects, Clusters IX and XII in Sundergarh District, had to make quick inroads as the lockdown began, to ensure access to the 17 camps spread across locations. “We discussed the matter with the District Collector on 25th March 2020 for vehicle passes to support delivery of essentials to the workmen which was approved within 12 hours.”
After gaining access, the core team members, Sayyed Ali Ansari, Shashi Kant Singh and Hrudananda Mishra, swung into the action to address various workmen issues. “In addition to establishing a safe environment, it was important to work on their mindset to remove apprehensions and to a large extent we succeeded,” says Mani.
“When work resumed, the site team faced another unique issue as most of the access roads were either blocked or dug up. We therefore took the issue right up to the District Collector level and police authorities and were able to make phased headway.”
S.S. Mani
Project Manager, Clusters IX and XII
Although their internal strategy was working to perfection, an external storm was brewing for Mani and team. “Tension was building up among the villagers, wanting our workmen to be removed as the pandemic was spreading. With a mitigation plan evolved with the IR & Admin personnel, we sought the Tashildar’s Block Development Office and Village Sarpanch support to lead our reconciliation efforts. A series of awareness campaigns on the pandemic, do’s, and don’ts along with precautionary measures taken at the camps assured the villagers of our concentrated efforts and helped defuse the situation.”
When work resumed, the site team faced another unique issue as most of the access roads were either blocked or dug up. Reaching out to the local authorities did not help much. “We therefore took the issue right up to the District Collector level and police authorities and were able to make phased headway. By April 25th, the complete road clearance was secured,” shares a battle-hardened Mani.
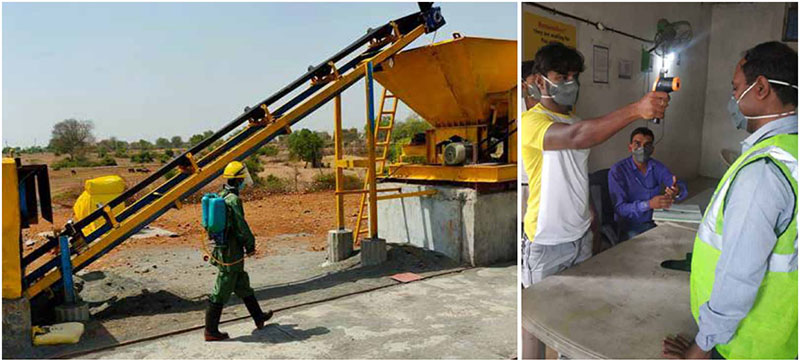
Fumigation of Plant & Machinery
Resuming operations in a hotspot zone
Down south in Karnataka at Bagalkot District, where WET IC is involved in building a vital infrastructure for Karnataka Power Corporation, timely decisions by Project Manager, Ganeshmani, ensured that all 160 odd workmen were grouped and shifted to a common camp. “It was easier and safer for us as we could monitor the base station, provide round the clock security with the back-up of a CCTV system.” Further, a committee with IR Head, Mangala Sreekanth and Accountant, Anup Nemani focused on providing all the essentials and ensuring hygiene at the camp which was appreciated by the Chief Engineer during one of his visits. A tie up with the local doctor for regular health check-ups ensured the wellbeing of the workmen. “All our initiatives kept the workmen calm and in good health that helped us to resume operations on 21st April.
“State wise leaders were assigned to address workmen for better connect. We were able to secure permission and commence works in a phased manner after gaining the confidence of the workmen.”
Colin Nonis
Project Director, Surya Water Supply Project
Working out an internal and an external plan
At Palghar, Project Director Colin Nonis’s Surya Water Supply Project is strategically placed with the alignment traversing through many villages along NH8 that presented him with a spate of issues during the lockdown. “The tribal villages in Palghar went into a shell, being overly protective, demanding the removal of migrant workmen based in camps near their villages and even trying to prevent the use of our offices. The workmen, understandably so, were all in panic, wanting to return home.”
Communication and networking worked best for Colin. “Thanks to our Accountant, Sajeev, we achieved a breakthrough after discussing with the District Collector. We quickly put in place a SOP with EHS Manager, Ganesh Balu Divekar driving the initiatives along with team member Nalini Krishna. At the camps, we adopted a straightforward approach with Assistant Manager, IR – Masum Ali, and his team members, Dhanshyam and Amit based at the labour camps to implement SOPs, ensure hygiene, provisions and importantly security. In addition, state wise leaders were assigned to address workmen for better connect. After about a month, we were able to secure permission and commence works in a phased manner after gaining the confidence of the workmen.” Colin’s relief is evident.
“That we have stood by the workman during these times and have done whatever best was possible is paying us back as we are now in position to take up works and accelerate.”
Mrityunjoy Santra
Project Manager, The Ranchi Water Supply Project
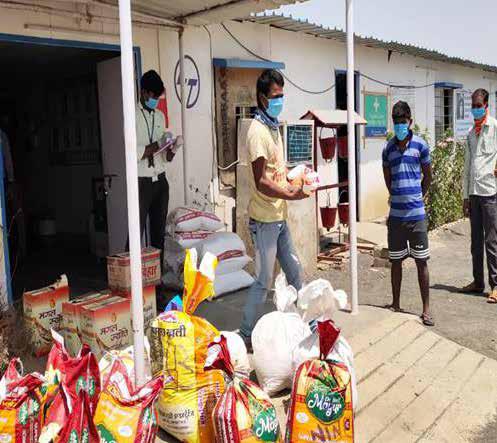
Grocery distribution to workmen
Gaining a safe edge with timely decisions
The Ranchi Water Supply Project team led by Project Manager, Mrityunjoy Santra, along with Construction Manager, Vipin P, were quick to implement control measures since 14th March, to keep 158 members safe at site. “That we have stood by them during these times and have done whatever best was possible is paying us back as we are now in position to take up works and accelerate,” shares Mrityunjoy, attributing his success to teamwork. He mentions some of his key members:
Md. Gulam Ali Hassan, Accounts & Admin who was instrumental in getting the BOCW benefits for the workmen and ESHO, A. Srinivas for ensuring the provision of essentials at the camps, conducting medical camps and awareness campaigns.
“The pandemic crisis forced us to act fast, ensuring minimum interface while moving our workmen to safer zones.”
Vipin Kumar Tyagi
Project Manager, Udaipur Integrated Infrastructure Project
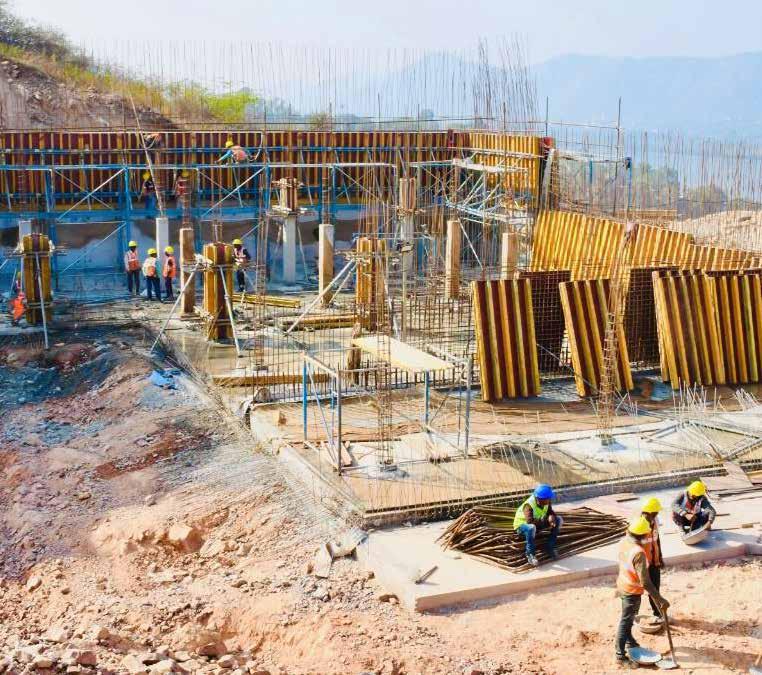
Construction of a WTP over a hill at Udaipur Integrated Infrastructure Project
Mitigating an urban challenge
Just before the lockdown there were around 1200 workmen at the Udaipur Integrated Infrastructure Project with most of the works happening across narrow roads and by-lanes. “We always had to strive for a safe access way,” mentions Vipin Kumar Tyagi, Project Manager, “The pandemic crisis forced us to act fast, ensuring minimum interface while moving our workmen to safer zones.” Precise communication by the EHS team led by Yagana Khan conveyed the right message to the workmen that staying at their camps was safer than taking the risk of travelling to their hometowns.
After the easing of restrictions, the project team recommenced works across all fronts taking up a slew of tasks comprising micro tunnelling, pipe bursting, CIPP activity, open cut pipeline work, cable laying and WTP structure works. The core team involving Vipin Kumar, Ankush Bansal, Vikram Singh, SB Pathak, Pawan Pandey, Surendra Singh, worked out a secure way forward, aligning to the precautionary SOPs with 500+ workmen. “With proper planning and monitoring, we arranged work passes for staff, workmen, and P&M equipment, mobilized subcontractor workmen and machinery and got the ‘work resumption’ letter from the local authorities.”
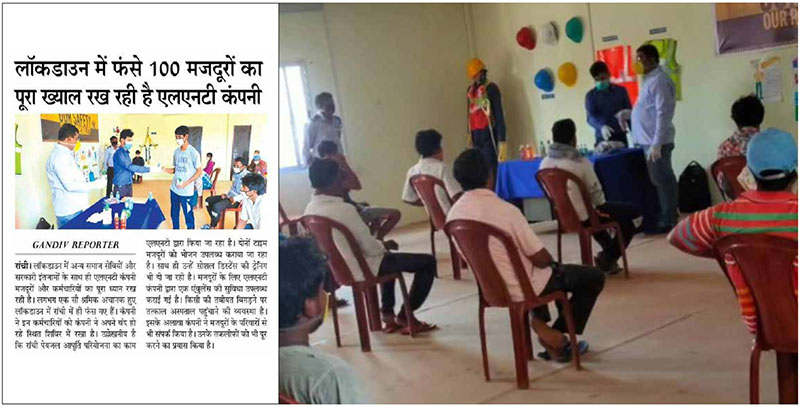
Holding together in the capital city
In Delhi, WET IC is executing one of the largest STPs in India, the 318 MLD WWTP Coronation Pillar Project at Mukundpur. As soon as the first case of COVID-19 was detected in the first week of March, Project Manager, Vinod Kumar, initiated a site level meeting to implement control measures at site, guest houses and workmen habitations. “To ensure the safety of 700 plus workmen at site, an action team comprising execution personnel, EHS, Admin and IR members, was formed to drive precautionary measures. As restrictions eased, site operations resumed with around 80 workmen taking up works in a phased manner. Presently, concreting works are underway and with situation in Delhi still sensitive, work is progressing with utmost caution.”
“We focused to keep site activities ticking safely without any disruption by working in two shifts. Formulating a ground zero safe work policy was something that we did even before there were any work resumption videos made and that provided the right direction in these most challenging times.”
S. Vishal
Project Manager, Industrial Area Sewage Treatment Works –
Phase III A, Qatar
On a safe working mission in Qatar
Unlike India, Qatar, decided against a total lockdown which increased the responsibilities on S. Vishal, Project Manager at the Industrial Area Sewage Treatment Works – Phase III A Project. “We focused to keep site activities ticking safely without any disruption by working in two shifts,” he shares, “although the bigger challenge was to ensure the wellbeing of workmen across various zones starting from their quarters, during commute and at site.”
Effective communication was Vishal’s prime driver. “Monitoring across various fronts was another crucial factor. We broke down the safety process into action points and key members of the team took up specific initiatives. Formulating a ground zero safe work policy was something that we did even before there were any work resumption videos made and that provided the right direction in these most challenging times as we continue to surge forward.”
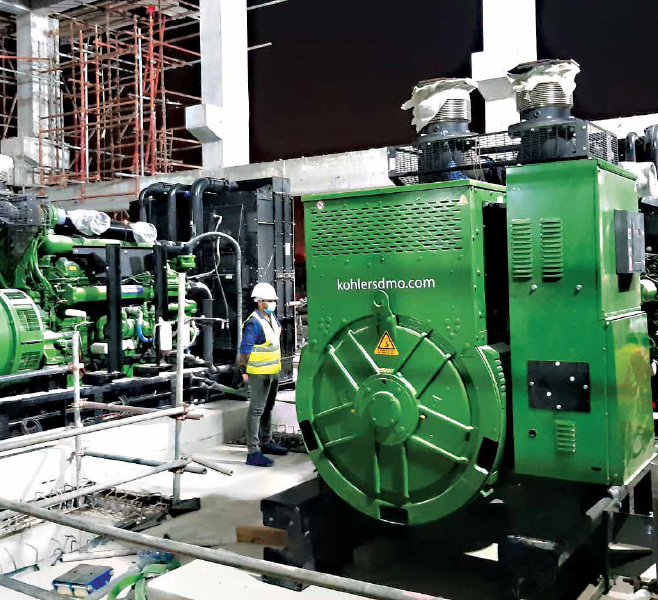
Operations & Maintenance at the Industrial Area Sewage Treatment Plant, Qatar
A CRITICAL SERVICE THAT IS ALWAYS ON
“Today, 68 of our Operations & Maintenance (O&M) stations across 14 States are delivering 3108 MLD of potable water every day,” shares K. Asok Kumar, Executive Vice President & Head Water & Effluent Treatment Business. “Lockdown or no, the O&M functions continue as they are considered ‘essential services,’ the only difference is that during these times it is even more challenging.” WET IC has effectively managed services across the states of Andhra Pradesh, Delhi, Gujarat, Jharkhand, Karnataka, Maharashtra, Madhya Pradesh, Odisha, Punjab, Rajasthan, Telangana, Tamil Nadu, Uttar Pradesh, and West Bengal.
“With a span spread out across 96 km, we had to keep the green channel flowing with close to 600 MLD of water delivered to around 1600 villages including meeting the needs of Jaipur city too.”
Smit Shah
Plant In-charge, Bisalpur-Jaipur Water Supply Station
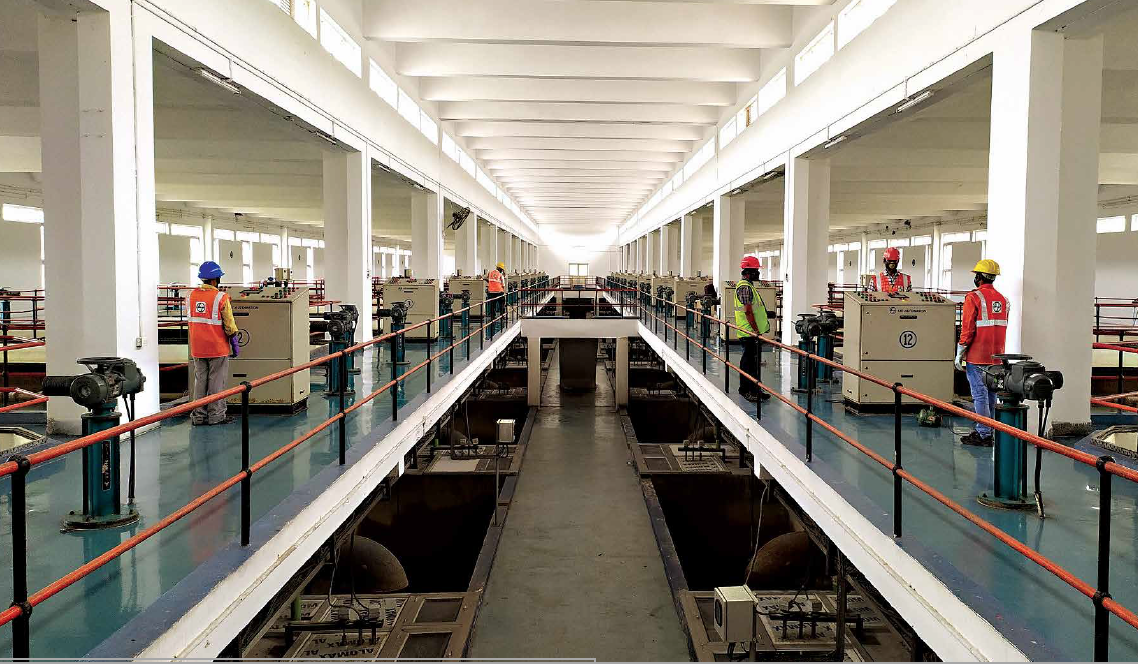
O&M team enabling the operations at the filter house in Bhagirathi WTP, New Delhi
Working out specific continuity plans
During the lockdown, the responsibilities for the 165 L&T-ites based across these O&M stations doubled as the ploy involved charting a secure way forward for the 4250 workmen while aligning to the plant SOPs and MHA directives. Some common initiatives evolved across locations included arranging special passes for the movement of workmen, transporting chemicals required for the treatment process from other states, scheduling operational shifts, enhancing awareness on the do’s and don’ts, ensuring wellbeing of the workmen and the wellness of the plant, all the while maintaining high standards of safety and quality.
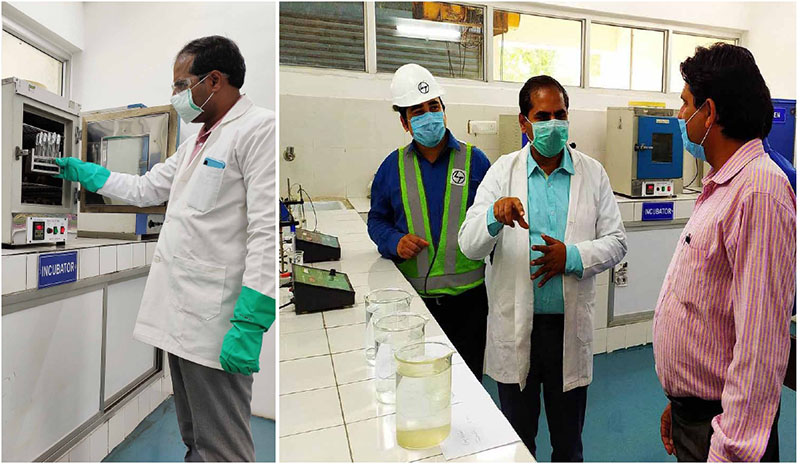
O&M team enabling the operations at the filter house in Bhagirathi WTP, New Delhi
At the Bisalpur-Jaipur Water Supply Station, one of India’s largest integrated water infrastructure projects, Smit Shah, Plant In-charge, had the task of keeping the O&M functioning with the pandemic spreading across Rajasthan, “We reviewed just before the lockdown and reduced our workmen strength from 156 to around 15 operators. This was important to ensure their safety and wellbeing,” informs Smit Shah. “With a span spread out across 96 km, we had to keep the green channel flowing with close to 600 MLD of water delivered to around 1600 villages including meeting the needs of Jaipur city too. It is commendable to note that despite the on-ground challenges, we did not reduce the shift hours and ensured that the plant functioned seamlessly in 4 shifts.”
“We worked out an effective work mitigation plan that was put in place on the 20th of March, a few days ahead of the lockdown with a three-shift agenda to keep the plant running.”
Anoop Kumar
O&M Manager, Bhagirathi WTP
In Delhi, a Corona red zone, Anoop Kumar, O&M Manager, was on the guard early on thanks to his networking skills. “With six O&M stations and Bhagirathi WTP being a significant base, we worked out an effective work mitigation plan that was put in place on the 20th of March, a few days ahead of the lockdown with workmen segregated based on age and health conditions. After a careful assessment, about 10% of the workmen were advised quarantine while the rest were put through a secure process with a three-shift agenda to keep the plant running. As a back-up, critical spares were stocked, and an inhouse technician was stationed at the plant to attend to any unlikely repairs,” he says. During the lockdown, there were two key visits, one from the Delhi Disaster Management Team and other from the Police Department to ensure the security of the plant, being in a sensitive zone.
“The challenge was to customize delivery exclusively for the pharma companies as the overall SCADA system was designed to provide 40% treated water to all industries across domains.”
Sourabh Bhargava
Plant In-charge, 60 MLD Plant in Pithampur
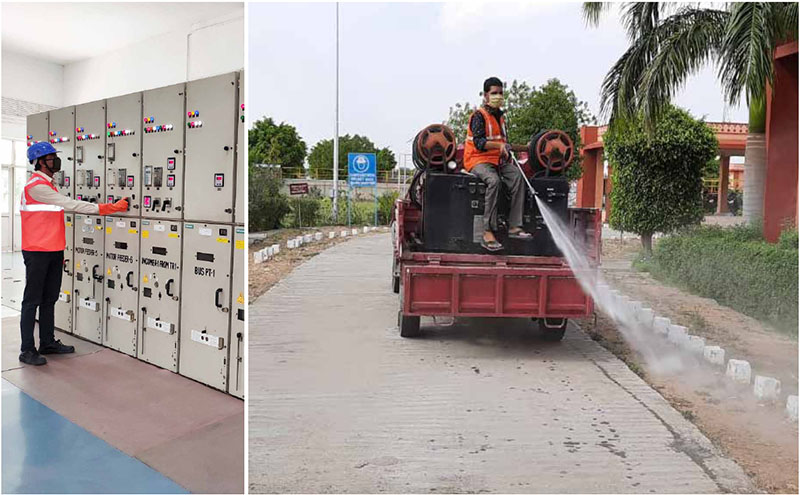
Fumigation of the campus at Bislapur-Jaipur WTP
Sourabh Bhargava, Plant In-charge, had a unique responsibility at the 60 MLD Plant in Pithampur to cater to the water requirements of the pharmaceutical industry where production is on in full swing. “The infrastructure was a mix of old and new structures comprising a 90 MLD intake facility and a 60 MLD treatment plant. There were 3 Water Treatment Plants (WTP) of 9 MLD capacity and one 27 MLD plant, with all the WTPs almost 30 years old,” informs Sourabh. “The challenge was to customize delivery exclusively for the pharma companies as the overall SCADA system was designed to provide 40% treated water to all industries across various domains.” With only the pharma companies functioning, the task was cut out for the O&M team as the valves had to be physically managed. This process was meticulously carried out and monitored throughout the lockdown.
“During this phase, we have also taken up the maintenance of Lift Irrigation Systems covering a network of more than 25,000 hectares for the upcoming Kharif crop season across 121 villages”
Shaik Shajahan
O&M Manager, Clusters III, XIV and XV projects
There was a problem, if it could be so described, of plenty at some of Odisha’s irrigation projects due to the lockdown. The surplus water is being used effectively by channelling it to the farmers for the cultivation of the Rabi crops. At the 19 pump houses in Clusters III, XIV and XV projects, Shaik Shajahan, O&M Manager, along with his four-member team have delivered water to farmers across 4500 hectares. “Our role in these projects apart from ensuring effective O&M also calls for maintaining a close rapport with the farmers. It is more than just a water supply job as the end-customer, the farmer, directly interfaces with us on several occasions. During this phase, we have also taken up the maintenance of Lift Irrigation Systems covering a network of more than 25,000 hectares for the upcoming Kharif crop season across 121 villages.”
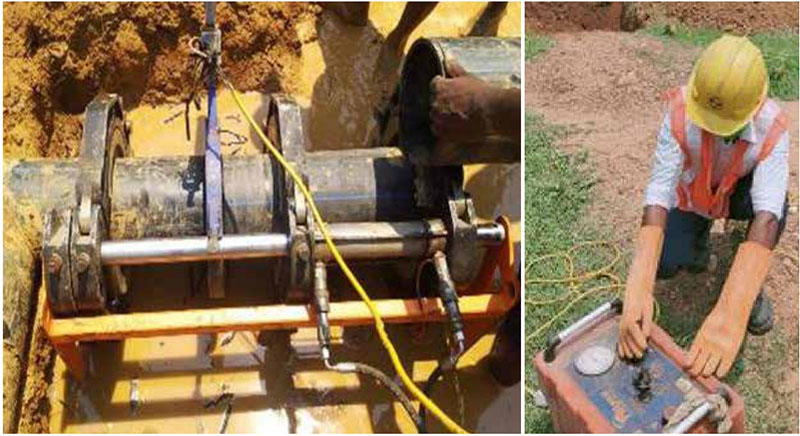
Maintenance of Lift Irrigation Network
Some of the other significant O&M stations where WET is operating 24/7 includes the 250 MLD Plant at Naguar, 236 MLD Plant at Kulpi, 227 MLD Plant at Garden Reach Water Treatment and Transmission Scheme in Kolkata and 172 MLD Vellore Package 1 for Tamil Nadu Water Supply and Drainage Board.
Across a couple of significant Sewerage Treatment Plant projects in Dubai and Sri Lanka, WET IC has been keeping critical services functioning. At the Greater Colombo Wastewater Management Project, one of the key pumping stations was operated continuously during the lockdown ensuring hygiene for the entire city. “Through our dedicated efforts, we ensure the hygiene of various organizations, government sectors & other essential service sectors including hospitals and close to 838,000 residents in these challenging times,” points out P Hari Prakash, Project Manager. “With limited manpower, we worked out a secure strategy aligning to the SOPs while keeping the plant functioning seamlessly as it was a crucial wastewater pumping facility for the entire city of Colombo,” highlights K Sivaramakrishnan – Cluster Head (WW BU, Sri Lanka).
“As an operational plant and classified under ‘Vital Sector’ by the Government of Dubai, it is of utmost importance to ensure the hygiene, safety and wellbeing of our 96 workmen, 30 foremen and 22 staff.”
S.A. Noor
Deputy Project Director, Jebel Ali STP
At UAE’s largest STP, the 375 MLD Phase-2 Jebel Ali Sewage Treatment Plant, WET IC’s Water International BU has completed the construction works and is about to begin the O&M services that will treat the daily waste created by 3.35 million inhabitants towards creating a clean, green Dubai. “As an operational plant and classified under ‘Vital Sector’ by the Government of Dubai, it is of utmost importance to ensure the hygiene, safety and wellbeing of our 96 workmen, 30 foremen and 22 staff,” informs S.A. Noor, Deputy Project Director.
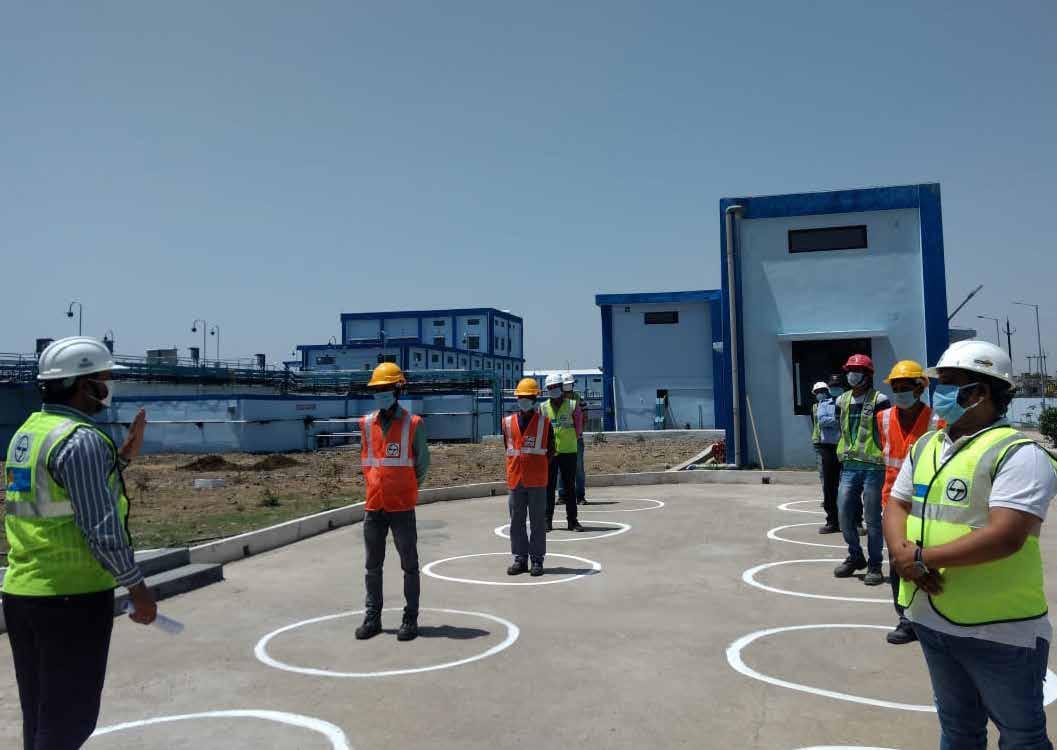
As soon as COVID-19 broke out, the L&T-BESIX JV formed a core team comprising Yves D. Rue, Project Director, Martin Cornellissens, Plant Manager and Prabal Desai, Maintenance Manager from BESIX and the L&T team led by Noor with able support from Operation Manager, Sabapathy Raja. “With the plant established at an isolated desert region, part of the workforce stayed at the site camp while rest of the crew were mobilised from different parts of the city through daily trips. As a safety measure, the workforce from outside that included subcontractors, were quickly mobilised and advised to stay at the site camps to minimise risks,” shares Sabapathy Raja.
A series of precautionary measures were put in place with the workforce including staff classified under different groups for working in shifts with the accommodation grouped likewise to ensure that groups did not get to meet either at site or at the camps that not only limited the number of workmen and staff but enhanced the availability of resources as well.
Enhancing operational efficiencies
By adapting a robust system along with building standard preventive maintenance schedules and task lists based on the OEM’s recommendations, WET IC has been able to successfully mitigate major system breakdowns. With a sizeable number of the O&M projects monitored at HQ Chennai through an integrated Computerized Maintenance Management System (CMMS), 98% of equipment availability has been ensured covering around 33,000 assets with 100% contractual compliance across all O&M projects. “CMMS gives us the edge to proactively maintain through automation with enhanced information for processing and taking actionable insights,” shares Rajmohan Head O&M. With 11 state-of-the-art technologies in operation at the various plants, maintaining a 360-degree vigil especially during these challenging times is crucial but with the back-up of technology and experienced teams, WET IC has raised the bar.
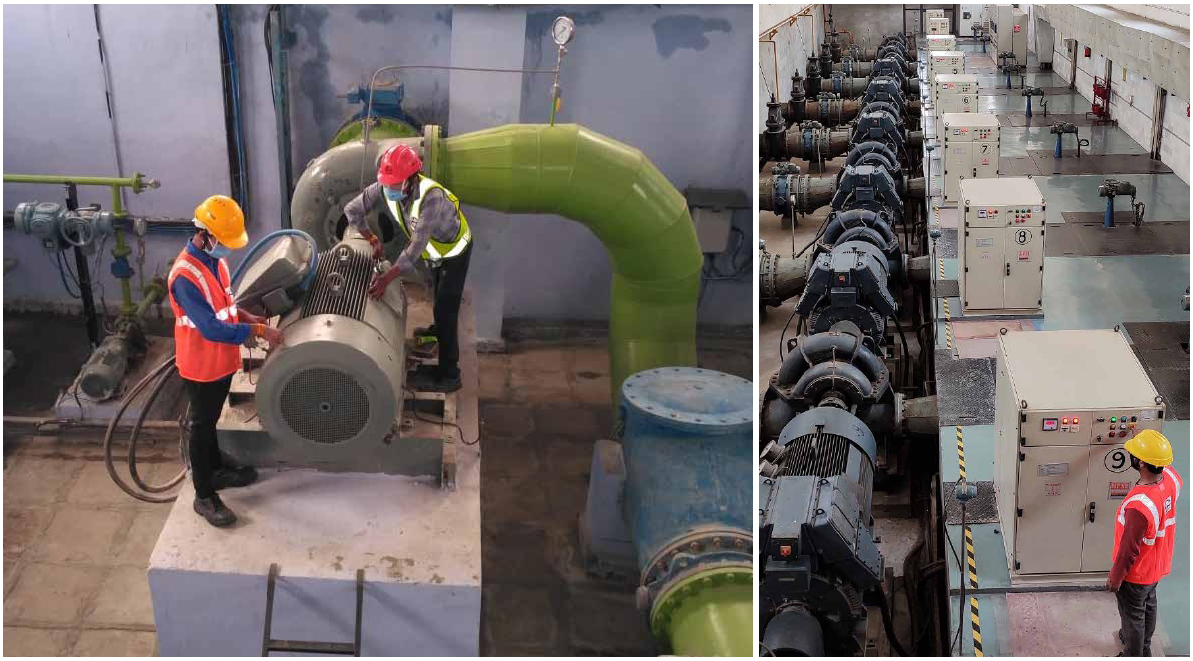
Pump maintenance at the Pithampur Industrial Water Supply Plant
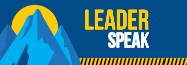
K. ASOK KUMAR
Executive Vice President & Head, Water & Effluent Treatment IC
Our safe methods have worked well across some 200 of our projects. Every project team has put their best foot forward, ensured the wellbeing of their workmen, contributed towards community initiatives and have emerged winners. The challenges were many and varied, often entirely new in nature that called for some quick, alert thinking and decision making almost on the fly. I am glad that many of our leaders have lived up to our expectations and have, at the same time, helped others down the line to act decisively and confidently. Going forward, the new normal brings us a whole new paradigm. We need to gear up to raise the bar with renewed focus, maximize our potential, consistently engage with our clients and give them the best of technology and project management services while ensuring the highest standards of safety and quality in all our endeavours.
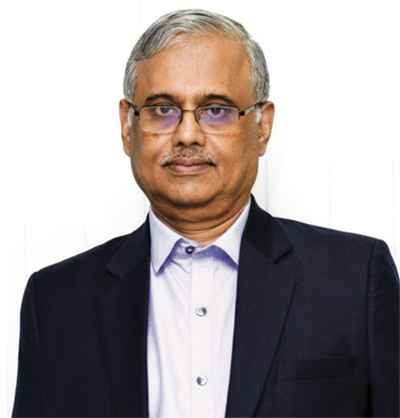