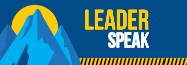
ANUPAM KUMAR
Vice President & Head (Metallurgical & Material Handling – SBG)
The ever-growing demand in EPC projects is for speed and scale, which calls for enhanced operational efficiency to deliver quality products at right time and right value. The expectations of stakeholders can be addressed by embracing digital advancements and quickly adopting to new and faster techniques, duly complemented by advanced mechanization. At MMH, operational efficiency is close interaction right from inception stage, i.e. design and detail engineering wherein the issues related to constructability are debated and duly incorporated for faster and smoother execution. The procurement process is fully digitized and synchronized with the project requirements to enable selection of the right product, undertake inhouse manufacturing and onboarding the right vendor. In execution, MMH has institutionalized several processes with the sole purpose of transforming the site activities into a safer and more productive environment thus adding value to the product being delivered.
We always endeavour improved performance across departments at micro-level, robust interface & resolution management. Coupled with this internal process efficiency, the focused efforts for external stakeholder management, involving a multitude of customers, consultants, vendors, subcontractors and workmen at various levels and locations in these challenging times is the driving factor to execute process intensive complex projects in time.
The operational excellence at MMH is driven through People, Processes and the Organization. Automation of Design and Mechanization of Construction will be the growth drivers for MMH completely changing the competitive dynamics which we are facing today to enable us to grow globally.
MMH is focussing on ‘Business Excellence’ where the ‘Leadership’ is driving focused ‘Strategy’ through its ‘People’, ‘Process’ and ‘Partnerships’ with a ‘Result’ oriented approach that will create multi-fold value to all its stakeholders.
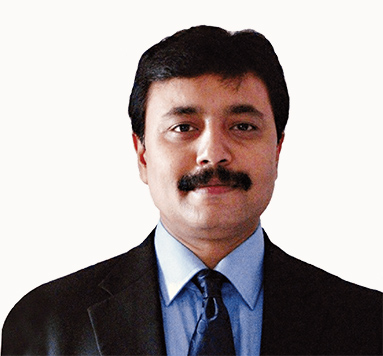
A BEST-IN-CLASS HOT STRIP MILL HAS TAKEN SHAPE!
At SAIL, Rourkela
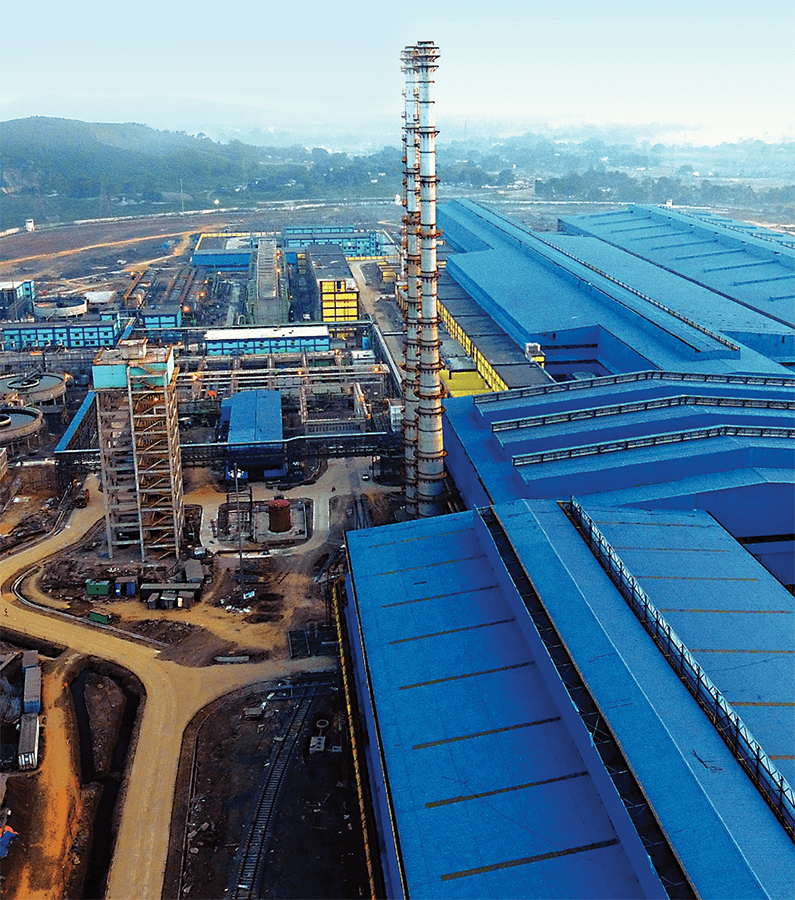
The Consortium of L&T’s Metallurgical & Material Handling (MMH) SBG and Mitsubishi Corporation, Japan, were contracted by Steel Authority of India Limited to build a 3 MPTA Hot Strip Mill (HSM) along with a 0.4 MPTA sheet shearing line on turnkey basis at Rourkela, with technology from Primetals and Hitachi of Japan. Spread over an area of 86.56 acres, the scope of this EPC project, a first for MMH, was huge: design & engineering, civil engineering work, fabrication & supply of steel structures, manufacture & supply of plant and equipment, manufacture & supply of refractories, intermediate storage, insurance & handling, erection, testing, pre-commissioning, start-up & commissioning and demonstration & establishment of performance guarantee parameters of the facilities. Critical equipment like roller tables, shearing lines, chock extractors, transfer and pallet cars were manufactured at L&T’s Kansbahal works in sync with the ‘Make in India’ theme.
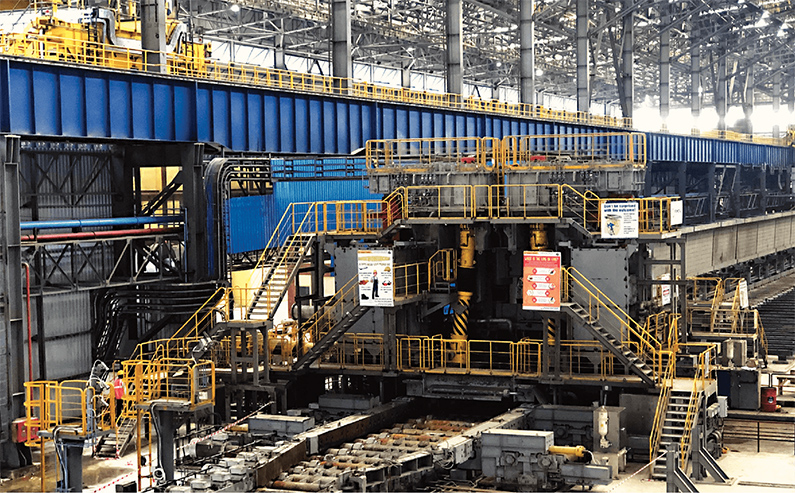
Roughing mill
After manufacturing 390 distinct pieces of equipment, buying out 3,979 distinct items procured from 155 local and overseas suppliers, 200+ customer inspections and some 40,000 inspection documents, the mill, one of the largest of its kind in India, was commissioned in January, 2020 and rolled out its first HR coil within two days of the commencement of hot trials. It is already being recognized as best-in-class and will roll out Carbon Structural Steel, HSLA, High Carbon Steel, LPG Cylinder Steel, Low Alloy Steel, API (up to X100) Pipe Steel and Auto-grade steel, to cater to high-end market segments.
“We had to overcome several challenges before successfully rolling out the first coil, within two days of the start of hot commissioning. Now, we are concentrating on fully commissioning the project for 66% of the guaranteed production capacity as per the terms of the contract.”
R Umasathiyan
Project Manager
Demystifying an HSM
Quite simply, a hot strip mill produces hot rolled coils from steel slabs that are in turn produced through a continuous casting route of charging in a reheating furnace to temperatures of up to 1,2500 C. Thereafter, the reheated slabs are sprayed with high pressure water in a descaling unit to remove the scales and then put through a roughing mill stand to reduce their thickness and correct their edges for further processing downstream. In a crop shear, their heads and tails are squared, divided into 7 numbers that in a finishing mill are converted into strips with precise 1.2 mm thickness and 25 mm flatness and then cooled to recover their steel mechanical properties. Finally, the strips are formed into two down coilers, paint marked, strapped online and transported to the coil yard via a pellet conveyor. The sheet shearing line cuts these strips into the desired lengths. The annual capacity of the shearing line is 400,000 tons capable of shearing strips of thickness ranging from 5 to 25 mm and widths ranging from 1000 to 2150 mm. The sheet bundles vary in length from 4 to 13 m and weigh up to 10 tons.
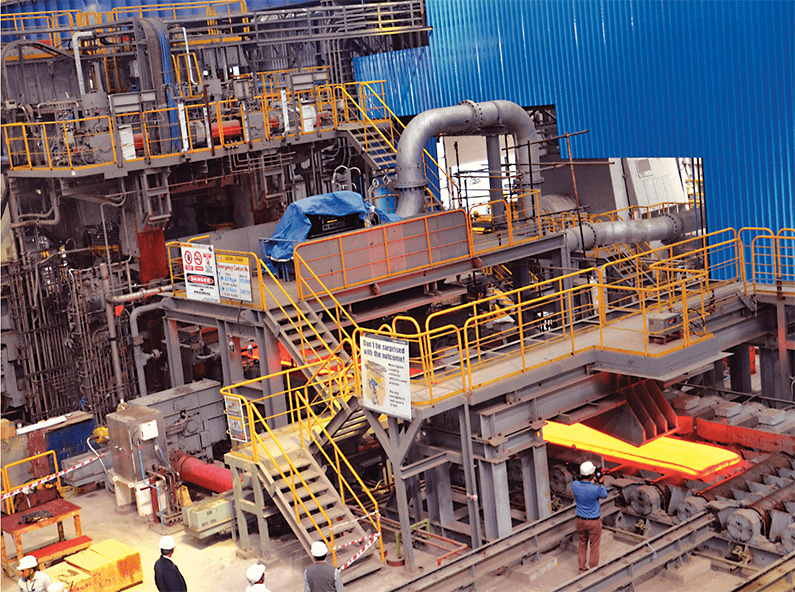
It took a lot of doing
6000 piles, 15 lakh cum of earthwork, 2.3 lakh cum of concreting, fabrication furnace oil, firefighting system. 4000
MT of refractory work, 4.2 km & 8.8 km 220kV double circuit transmission line from Tarkera grid to MSDS VII and NSPCL grid to MSDS VII of HSM respectively, 1.8km EHV cable laying, 2 km of railway track laying, 2,200 km of power / control / communication cables, HT/LT electrical panels including 220kV & 33kV GIS and 90 transformers. The HSM certainly took a lot of doing.
Other challenges were that it was being constructed on a solidified slag filled area in which structures had to go 23 m underground, with the perennial riverbed of the river Brahmani and a high water table in close proximity. “I’m proud to have lead the team to execute this project that faced several & erection of 24000 MT structures, installation of 26,000 MT mechanical equipment, 10 lakh inch-meter of piping comprising of mixed gas, water, nitrogen, steam, hydraulics & lubrication, compressed / instrument / dry air, oxygen, steam, fuel oil, LPG, challenges since inception, but due to the combined efforts of the entire team, we were able to overcome them to successful roll out the first coil within two days from the start of hot commissioning,” says R Umasathiyan, Project Manager, New Hot Strip Mill Project. With an adrenaline rush, he adds, “Now, we are concentrating on fully commissioning the project for 66% of the guaranteed production capacity as per the terms of the contract.”
“We had to negotiate and deal with as many as 550 equipment suppliers and another 145 specialized vendors for the electrical and automation works, but we managed them well.”
R. Suresh Kumar
Head – Operations, Minerals and Metals BU
Improving efficiencies
Perfect coordination: To execute a project of such complexity and scale, perfect co-ordination between Engineering, Procurement and Construction and across all disciplines like civil & structural, mechanical, electrical and automation was an imperative. “The good news is that all our teams worked in tandem,” shares T. Kumaresan, Head – Minerals and Metals BU, “information was readily shared and we seamlessly coordinated during the design and execution stages which is primarily why we were able to deliver the project against an extremely aggressive time line.” Dealing with vendors and suppliers is normally a tall order but at this project it was even taller. “We had to negotiate and deal with as many as 550 equipment suppliers and another 145 specialized vendors for the electrical and automation works,” shares R. Suresh Kumar, Head – Operations, Minerals and Metals BU, “but we managed them well!” His smile tells a tale of success.
“The good news is that all our teams worked in tandem. Information was readily shared and we had seamless coordination during the design and execution stages which is primarily why we were able to deliver the project against an extremely aggressive time line.”
T. Kumaresan
Head – Minerals and Metals BU
Going digital: “With Procube, our project progress monitoring was spot on,” shares Anton Jayanth, Digital Officer – MMH. “Our Safety app was the reason we were able to clock 38.4 million safe man hours thus far but the real digital success was the RFID system monitoring our 1,500-strong work force that significantly improved our human productivity quotient.” Supply materials were tracked through the SLIM (Smart and Liver Inventory Management) application while concrete pour cards generated using the Conquer app hastened clearances to speed up execution. All vehicles at site were tracked while the stores were always under the lens of CCTV surveillance cameras.
Mechanisation: Compensating the limited availability of skilled manpower, the project team implemented several mechanisation initiatives. “With great learnings through cross cultural interaction with foreign experts from Japan and Europe, we were able to explore various innovative approaches like the usage of a skidding arrangement to install heavy equipment like Mill Housing weighing 165 MT each, 9.5 MW Motors and levellers. This eliminated the involvement of high capacity cranes for multiple handling,” says Suman Mukherjee, Project Coordinator and Mechanical In charge “Erecting structures in modular form improved resource productivity. By applying ceramic back strap with adhesive tape inside the buffer tank and two 112 m tall steel chimneys before welding joints cut both cost and time.” The chimneys were assembled with 500 MT Demag cranes on ground with refractories and erected after which the refractory lining was done with specialized platforms and hoists designed by CMPC.
Exclusivity: “For the first time in MMH, we installed and commissioned 220 kV and 33 kV Gas Insulated Substations and 12 Mbps network speed for profibus network,” informs a delighted N Jothi Ramalingam, Incharge – Electrical, Instrumentation and Automation. “In fact, the 33 kV GIS is India’s 2nd largest single board GIS with one Sectionaliser, 2 bus couplers and 37 bays. The 12Mbps network line is exclusively used for communication of heavy-duty mill motors (IGBT drives). The plant is fully automated with complete Fibre Optics backbone catering to different sections of the plant such as the mill bay, coil storage bay, roll shop, reheating furnace, water treatment plant, MSDS VII, etc.”
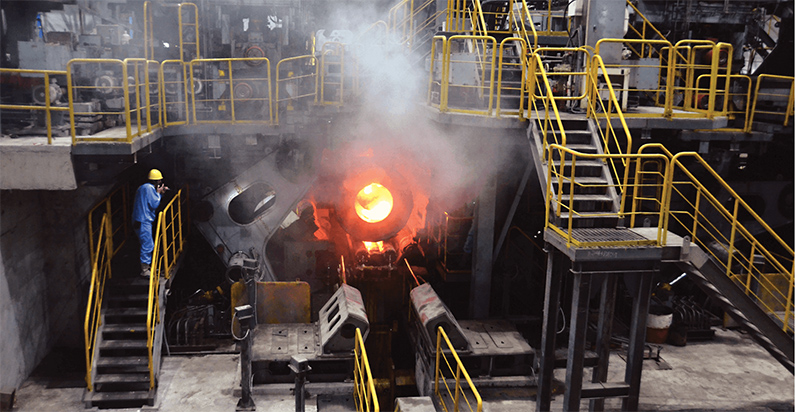
First coil produced at the down coiler
Higher the height, taller the risk!
The Ghoshpukur-Salsalabari Road Project involved several activities at critical heights such as erection of RCC, PSC and steel girders over live railway lines all of which was beside ‘live’ traffic. “Instead of a task-based approach that is usually adopted, we went for a systembased method including HIRA, SWM (Safe Work Method) and behaviourbased training to address safety,” reveals Project Manager, Niloy Mukherjee. The EHS In-charge, Tushar Gangopadhyay chips in that the EHS team involved workmen, local villagers and even the local administration in their safety regimen. “We used events like the Safety Month, Road Safety Week, Environment Day to drive EHS awareness.” Malay Kumar Mahanta – Head EHS TI IC, mentions, “Introduction of systems like the formation of an EHS Committee, the implementation of the Reverse the Risk (RtR) system, Permits to Work (PtW) and widespread safety awareness campaigns went a long way in sensitizing workmen to avoid unsafe practices and acts.”
“Every project is a fresh experience. It was no different with this one and it is kudos to our team for having pulled off such a wonderful project though the bigger concern for me was to live up to the expectations and trust reposed in us by SAIL, a long time customer of L&T, and I am delighted that we have delighted them.”
Anupam Kumar
Head – MMH
Auxiliaries: The Hot Strip Mill features vast utility systems and the water system handles 25,554 cum / hr of cooling water by three water circuits: an indirect cooling water system, a direct cooling water system and a laminar cooling system for control of metallurgical process as well as dissipation of unutilized heat. To conserve precious fresh water, water re-circulation systems recycle and reuse discharges from the mill equipment with the help of a filtration plant, thickener and filter press. These systems are also used to collect and convey scales, for drinking, sanitation, firefighting, condenser cooling of chiller units and other miscellaneous purposes.
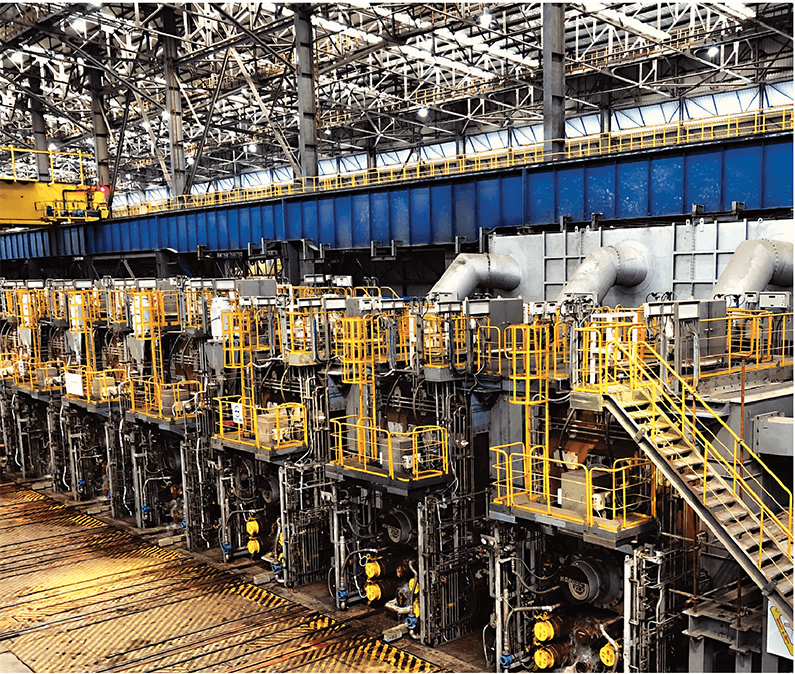
Finishing mill
Enormity: The project team built 7 major substations and 100 small buildings with all finishing works, MEP and 2.5 lakh inch-meter embedded conduits. The foundations had to be precise to cater to critical tolerance levels required for mill equipment. All major external plastering works were carried out with plaster spraying machines by a specially trained CSTI team. The plant is connected by 8 km of RCC pavements; it has a 16 km long drainage system too. “A reflection of our commitment to faster execution is that we poured more than 10,000 cum of concrete per month consecutively for 3 months with placement in 26 multiple locations with exacting quality requirements meeting the precise tolerance limits under stringent environment conditions across varying elevation from (-)23 m depth to 48 m height ”, says C V Nagaraju , Incharge – Civil works.
“With Procube, our project progress monitoring was spot on and the Safety app was the reason why we have been able to clock 38.4 million safe man hours thus far but our real digital success was the RFID system that monitored the 1,500-strong work force that significantly improved our human productivity quotient.”
Anton Jayanth
Digital Officer – MMH
For Anupam Kumar, Head – MMH, the Rourkela HSM has been yet another opportunity to prove the SBG’s mettle to execute large scale EPC projects across metallurgical units. “Every project is a fresh experience. This one was no different and kudos to our team for having pulled off such a wonderful project though the bigger concern for me was to live up to the expectations and trust reposed in us by SAIL, a long-time customer of L&T, and I am delighted that we have delighted them,” he concludes with a grin and a thumbs up, relishing the pride of L&T being the sole EPC company to have executed the majority of hot strip mills in the country.