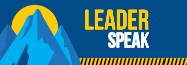
T. MADHAVA DAS
Senior Vice President & Head, PT&D IC
At a recent meeting with a developer, their CEO shared a critical piece of their interesting strategy that they endeavour to discover the lowest possible cost for all their inputs, irrespective of market pricing, by working out specific, best-fit, technically optimized solutions every time. Such a strategy has given them a success rate of two out of three tenders. Being an EPC contractor, we can truly add value to our customers not only by demanding lowest possible cost for our own inputs with our partners and giving technically optimized solutions but also by excelling in our operations.
Our predictive abilities make our plans robust that gives us an edge to manage risks better and achieve speed and scale. Thanks to our vast experience and spread, we are blessed with a huge amount of data and knowledge. We, at PT&D IC, are on a journey through a specific OPEX initiative to orchestrate the data captured by digital means and articulate organizational wisdom in a replicable manner.
We have reaped the benefits of modularization improvised to suit our own business needs, for instance, in the kitting of tower components or remote electrification items.
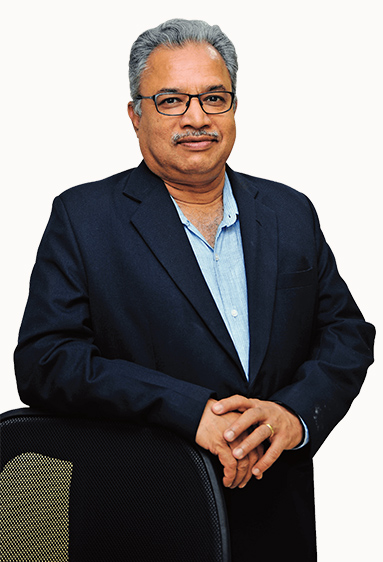
In our projects, the elimination of inefficiency starts early at the planning stage itself. For example, in the way we sequence our project tasks and assign work packages for our subcontractors. At our manufacturing set ups, our Industry 4.0 journey has gained momentum with marked improvement in the Overall Equipment Efficiency (OEE) of our equipment.
At the core of such initiatives is the centralized facilitator set up named PRAPTI – Planning, Reviewing and Assisting Projects to Improve – that equips the site team with the requisite tools and analytics to improve productivity. Productivity improvement reveals itself in project duration, like in the reduction of the number of days for our civil works to achieve clean room access in GIS projects. Be aware that timely completion is a panacea this will ultimately reflect in our profitability.
Finally, process simplification needs no emphasis. As Tiger Woods put it, “There is always stuff to work on. You’re never there.”
By getting better each day, we ensure a greater tomorrow for all of us!
GAINING A DECISIVE EDGE THROUGH COST LEADERSHIP
Driving process changes at PT&D
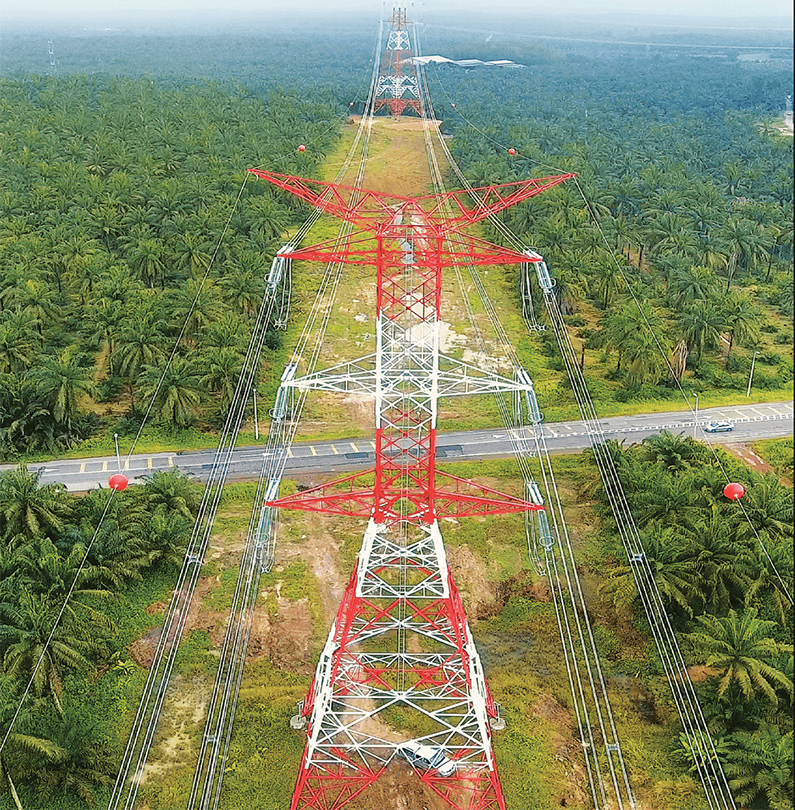
For a business that operates across multiple geographies and in some of the harshest terrains, the Power Transmission & Distribution (PT&D) IC has always banked on robust processes to achieve excellence across its operations both at sites and production centres. In recent years, the IC has successfully executed mega power transmission and distribution projects within stringent timelines thanks largely to its Operational Excellence (OPEX) initiatives.
“We have driven OPEX with the primary focus on Cost Leadership across all operations,” declares T. Madhava Das (TMD), Senior Vice President & Head, PT&D IC. “Our success factor is attributable to the total commitment of our senior management to continuously drive the change process, to evolve solutions best suited to cross-country/geographically widespread projects where execution is always a challenge and to monitor remote locations where accessibility is an issue.”
“We have driven OPEX with the primary focus on Cost Leadership across all operations, focused on Productivity Improvement, Cost Optimization and Process Time Reduction to gain a competitive advantage in the industry.”
T. Madhava Das
Senior Vice President & Head, PT&D IC
In sync with LAKSHYA goals
Aligned to the business goals and LAKSHYA 2021 plans, the OPEX initiatives are focused on Productivity Improvement, Cost Optimization and Process Time Reduction to gain a competitive advantage in the industry, reveals TMD, “to achieve which, we introduced various initiatives at the functional level driven directly by the BU heads through specific OPEX coordinators and Cluster Operating heads to effectively implement across factories and sites. Each OPEX initiative is driven by an OPEX Champion, supported by a small team working in close coordination with the OPEX team at L&T Powai to monitor, review and provide the necessary push to speed up implementation.
Subsequently, as the initiatives have gained momentum, we have institutionalized them across functional levels as Standard Operating Procedures.”
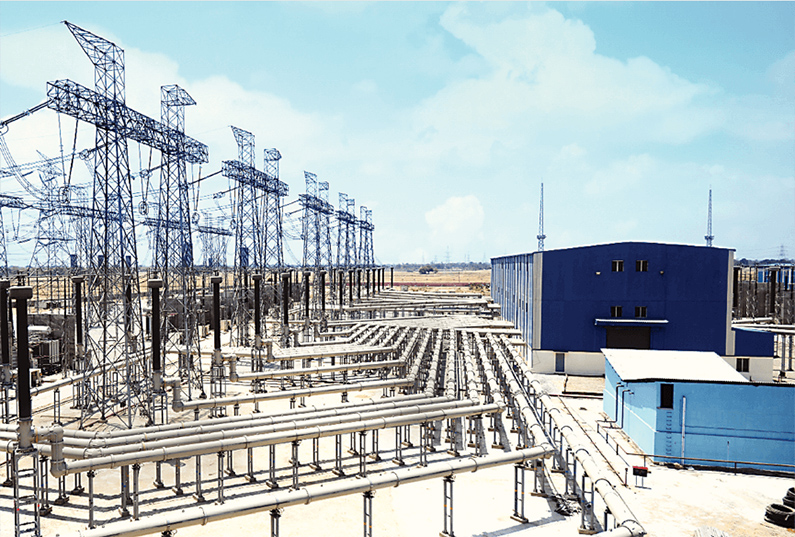
765 kV GIS at Varanasi
Realtime monitoring through PRAPTI
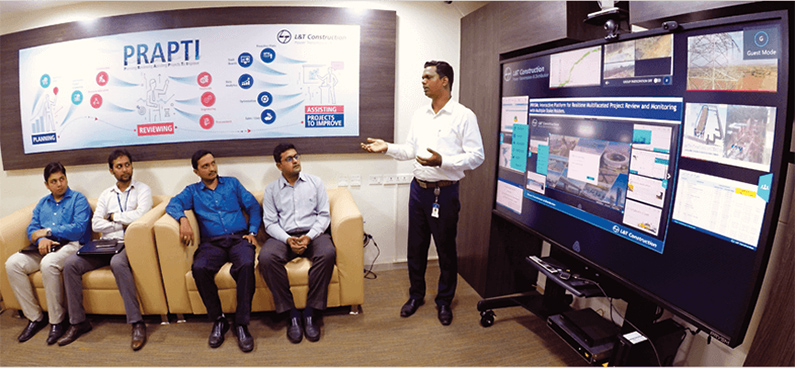
Time has always been critical for any infrastructure construction contract. However, understanding delays, determining critical tasks and forecasting completion dates have always been challenging, even more so considering the span and tough terrains of PT&D projects.
The need of the hour was a platform with the right insights to mitigate time variations and cost claims. A 4-member task force team worked with a stringent timeline of one year to develop and implement a first-of-its-kind digital tool in the construction industry for Planning, Reviewing and Assisting Projects to Improve. “Called ‘PRAPTI’, we developed this digital intervention,” shares Jerome Johnson, one of the digital champions, “to integrate a real time decision support system that uses a detailed integrated plan, by involving all the disciplines (Engineering, Procurement & Construction) in a single schedule to subsequently, with the help of analytics models, indicate the department or discipline that is delaying a project.”
“PRAPTI is extremely useful during the closing stages of a project too,” adds Jerome, “when we are dealing with variation claims as delays not attributable to the contractor can be highlighted and made eligible for scope variation with the client or get additional Extension of Time (EoT) and thereby avoid legal problems.”
The team of Siva Sankaran, Vijay and Sumit briefs the editorial team on a gamut of information and about the physical progress of a transmission line project in Malaysia on an applications dashboard. Thanks to the inbuilt virtual workspace feature, an impromptu meeting is called with the stakeholders of the site team. Impressed by the insight, we quiz them about the software dynamics and are briefed that project management solutions such as EIP Execution Plan, Primavera P6, Nadhi (ALIGN), Building Information Modelling (BIM) and Geospatial technologies have been integrated into PRAPTI.
A Central Planning Cell (CPC) streamlines the plan of the respective stakeholders and establishes a consolidated base to schedule resource allocation, enable lean construction, integrate procurement and track material with all activities tagged to specific project coordinates.
Strategizing execution
To transit seamlessly from strategy to execution, PT&D has adopted a fundamentally strong, workable approach. “Our core initiatives are focused on improving execution methodologies, introducing process improvements, enhancing production capabilities, digitalization, engineering standardization, time saving and sustainable growth, that have ultimately led to customer satisfaction,” shares Deepak Nayak, Head Corporate Centre. About 26 major OPEX initiatives have given the IC comprehensive benefits across its various business.
REVIEWING PROJECT SCHEDULING
When a project to electrify 96 villages across an area of more than 47, 800 km across 9 Districts in Western Odisha was undertaken within a stringent timeline, the stakes were high for PT&D’s Utility Power Distribution Business. Especially, with a ton of challenges to be mitigated that included negotiating the elephant corridors of Sundergarh, hilly terrains of Deogarh, mines of Jharsuguda, submerged areas of Sambalpur, cultivation lands of Bargarh, tribal habitats of Nuapada, Maoist regions of Kalahandi and the searing heat of Bolangir. A detailed survey revealed that 36 out of the total 96 villages were in the vicinity of dense forests where the scope involved electrifying 1392 households ranging from 4 to 208 with an average of 36 households per village. Power had to be transmitted through 192 km of aerial bunched cables strung on 4880 steel tubular poles. 65 distribution transformers with ratings of 25 kVA, 63 kVA & 100 kVA had to be installed too.
“Our core initiatives are focused on improving execution methodologies, introducing process improvements, enhancing production capabilities, digitalization, engineering standardization, time saving and sustainable growth, that have ultimately led to customer satisfaction.”
Deepak Nayak
Head Corporate Centre
Based on initial linear scheduling, work commenced but soon the project team encountered various issues like changing customer priorities, Right of Way issues, third party delays in approval and the like that required continuous rescheduling of order of preference of villages and reallocation of resources. After carefully analyzing all the factors affecting the deployment of resources, the core project team realized that four major factors held the key to determine the project schedule – Order of Preference of Villages/Works, Customer & Political priorities, Contractor & Work Front Availability, Complexity in Materials and Accessibility. Based on this success, this approach was implemented across DDUGY and IPDS works covering 1381 villages.
TOPSIS APPROACH IMPLEMENTED ON A LARGER SCALE
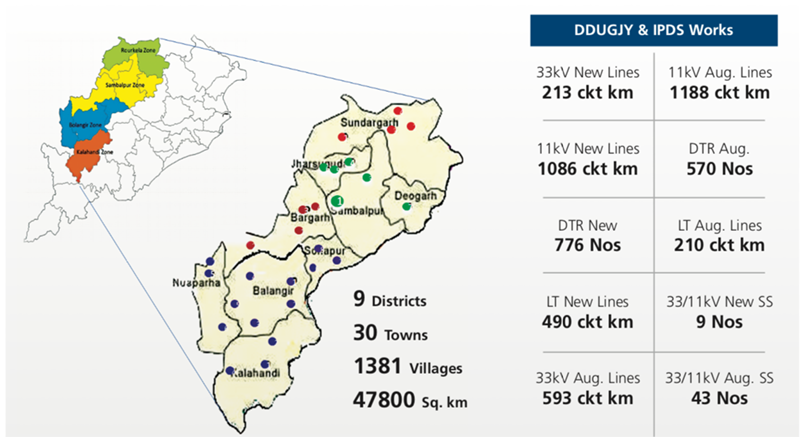
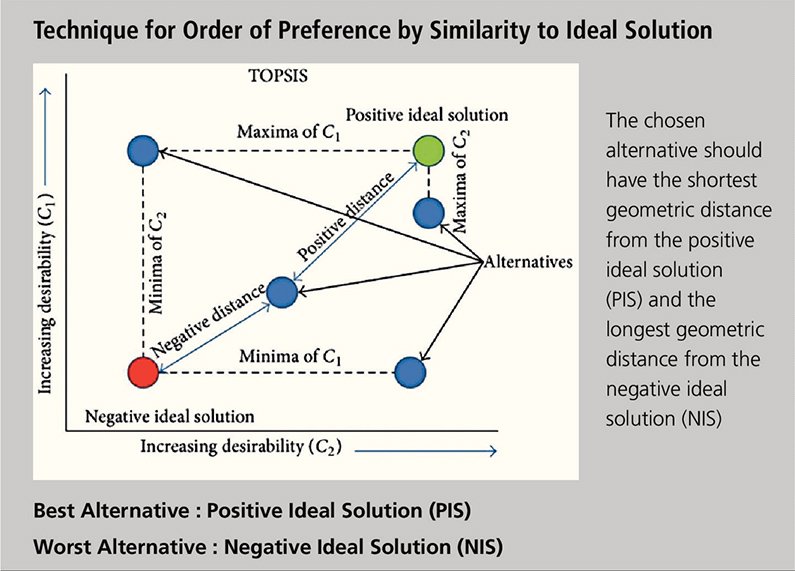
Aligning with the TOPSIS approach
For the core team of Karthik, Sandeep, Karthikeyan, Ravitej and Sahil Kumar, it was time to shift gears, and they opted for a novel scheme – Technique for Order of Preference by Similarity to Ideal Solution (TOPSIS), a multicriteria decision analysis method based on the concept that the chosen alternative should have the shortest geometric (Euclidian) distance from the Positive Ideal Solution (PIS) and the farthest geometric (Euclidian) distance from the Negative Ideal Solution (NIS). For instance, PIS maximizes benefit and minimizes cost, whereas the NIS maximizes cost and minimizes benefit assuming that each criterion needs to be either maximized or minimized. A simple and useful technique, TOPSIS ranks multiple possible alternatives according to closeness to the ideal solution. “After working out the mathematical functionality, the decision matrix was derived and then the order of preference arrived at,” elaborates Karthik. Therefore, instead of starting with 16 villages in April as originally planned, the team started with a different set of 9 villages in April and another 9 in May as per the revised schedule; the execution of 10 villages was brought forward to start in the 1st quarter that were originally scheduled for the 2nd and 3rd quarters.
“We iterated the TOPSIS approach thrice i.e. in March, June & September 2018, assigning different weightages to various criteria.”
G Karthik
Project Manager DDUGJY
Keeping tabs on influencing factors
With the schedule spread over nine months, quarterly revisions to the weightages were made considering the dynamic nature of the influencing factors. “We iterated the TOPSIS approach thrice i.e. in March, June & September 2018, assigning different weightages to various criteria,” says Karthik, with each succeeding iteration excluding the villages that were started earlier. During the initial phase of the project, i.e. March to June, there was a compulsion to start and complete those villages under the SAGY scheme and directly monitored by the local Members of Parliament. With the customer having his own list of villages to be taken up on priority basis, the criterion of ‘Customer or Political Priority’ was given more weightage during March 18 and reduced in the subsequent months. As accessibility to several of the villages reduced with the onset of monsoon during July – September, the ‘Accessibility’ criterion was given preference while the ‘Complexity in Material’ criterion gained precedence during March & September due to the limitations in procurement of the specialized structures used specifically for the UE execution works.
The gains for the project team by adopting the project schedule based on the TOPSIS approach were manifold: reduction in average cycle time to electrify villages, reduction of schedule overruns, reduction in supervision costs, improved monitoring and implementation of quality and safety resulting in lesser working capital requirements that thrilled the stake holders. After the successful implementation of the pilot project in 36 UE villages in the Sambalpur District, the scheduling approach has been applied for the entire works.
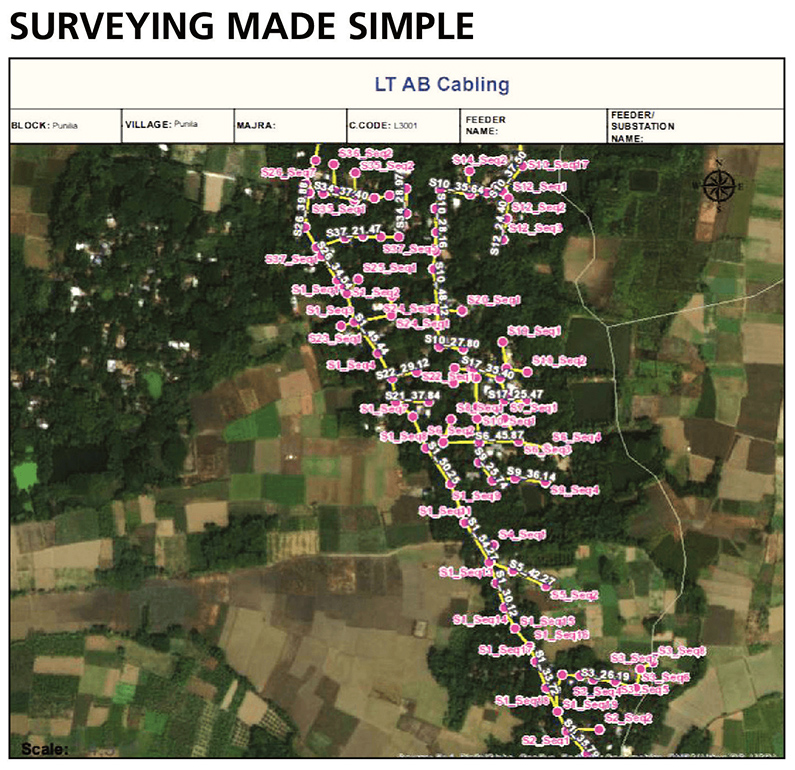
There were instances especially in UPD projects where for a 24-month project, surveying alone used to take close to 4 months. Hence there was a dire need to make surveys more efficient especially for long span projects. A 4-member task force team at UPD’s HQ office was mandated to design and develop a GIS based solution to reduce survey time and improve data collection at sites during survey and execution stages.
Within a year’s time, the team came up with ‘LMNoP+Dhruv’, a unique digital solution that combines mobile application to collect and map all equipment at field level and the web application to review and finalize field data to submit to client. The application works through a Trimble catalyst device which is a lightweightx antenna that plugs directly into an Android phone or a tablet’s USB port to take measurements.
Elaborating on the simplification of the process, the development team comprising Charan, Ajay, Kaustav and Dileep take us through the paces. The surveyor at site has only to upload the data from the catalyst device following which automatic BOM generation location wise and auto survey drawings are generated with conductor/cable lengths finalized. ‘LMNoP+Dhruv’ has enhanced productivity and improved workflow that ensures faster delivery of the final survey outputs and less chances of any cost escalation. Across UPD projects, the average cycle time for conducting surveys has reduced from 4 months to just 2.5 months!
Similar digital surveys have now become the order of the day at other projects too. At the 400 kV Chimuara -Nacala Transmission Line project in Mozambique, LiDAR was used to complete the 370 km topographical survey, where close to 100 km of the alignment passed through dense forests. Apart from time and cost savings, the crew’s safety was ensured. The site team is also using drones to capture data from various locations.
Pre-task Plans
Tower erection and stringing call for comprehensive safety and quality guidelines in transmission line projects. Though secure methods were in place, the risk of a tower collapse had to be completely removed for which a Pre-task Plan (PTP) was initiated that involved implementing motorized double-capstan winches for tower erection and aluminium final sagging bridges for final sagging activities for control and safety of workmen.
Through a centralized approach, the process at each location was defined highlighting the potential hazards that included stringing across different stretches to prevent tower collapse. Conductor drum scheduling further minimized wastages. To enhance the process, workmen gangs were oriented with activity training programmes and procedures for using winches and sag bridges safely.
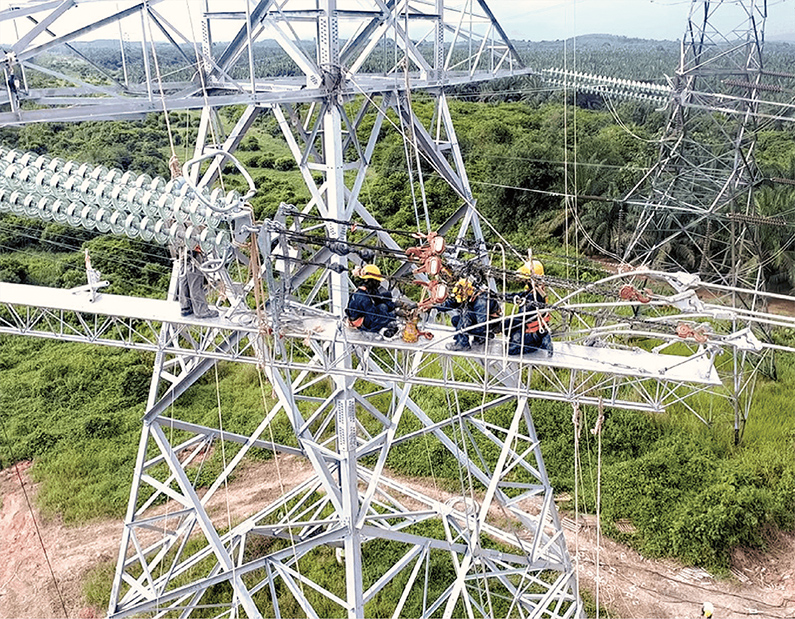
A safe platform on sag bridges for transmission tower erections
Through a centralized approach, the process at each location was defined highlighting the potential hazards that included stringing across different stretches to prevent tower collapse. Conductor drum scheduling further minimized wastages. To enhance the process, workmen gangs were oriented with activity training programmes and procedures for using winches and sag bridges safely.
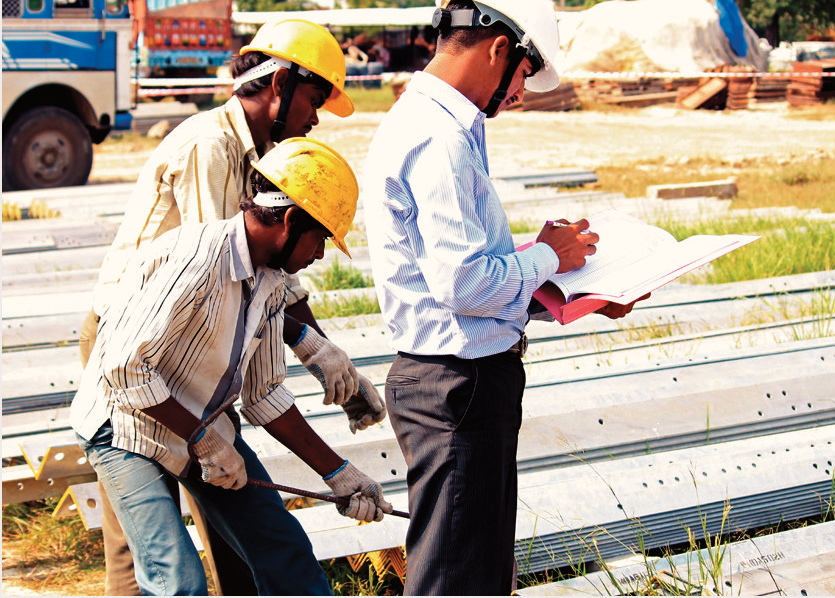
Tagging of transmission tower members
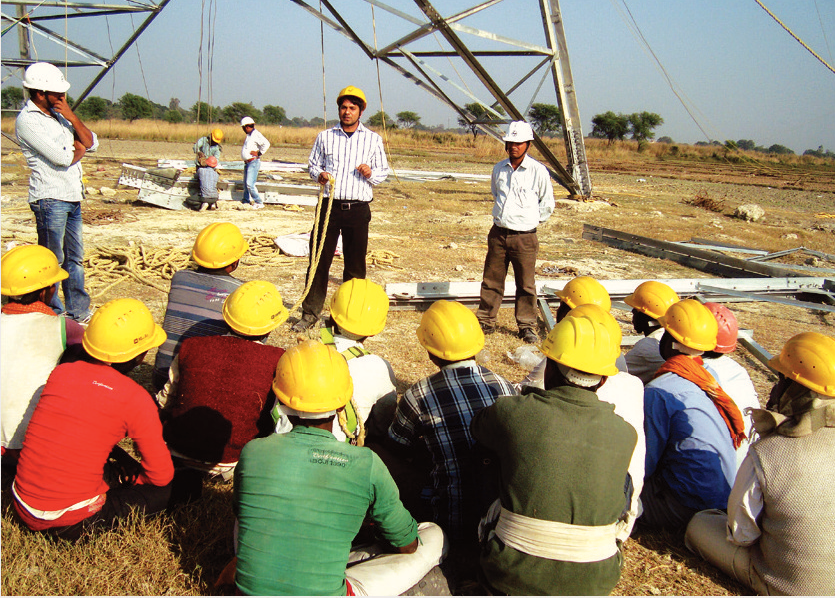
Workmen orientation
At the 500 kV DC TL stringing activities in Malaysia that had close to 160 plus towers with an average height of 60 meters running for most part of the alignment, the sag bridge played a pivotal role to ensure safety and productivity. “Introduced in West Malaysia, the sag bridge was placed parallel with the rough sag of the conductor as a platform for fitters to carry out the final works completely eliminating the hazards of working at height,” informs T.R. avichandran, Project Manager. Sag bridges can be customized as per the tower specifications as was the case in this project where a 20 m sag bridge was used to accommodate 5 m platforms in 4 parts with all tools required for final sagging placed on the bridge.
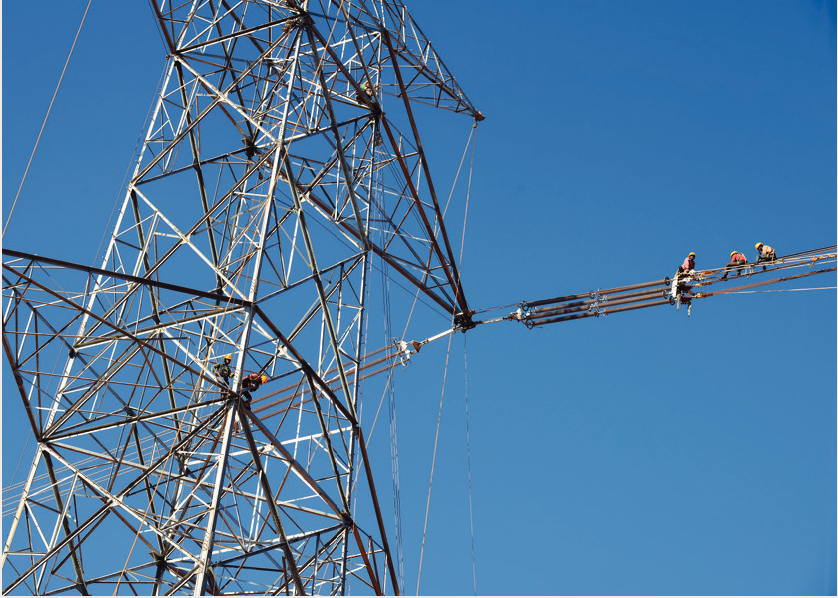
Workmen on lifelines to raise the steely tower members
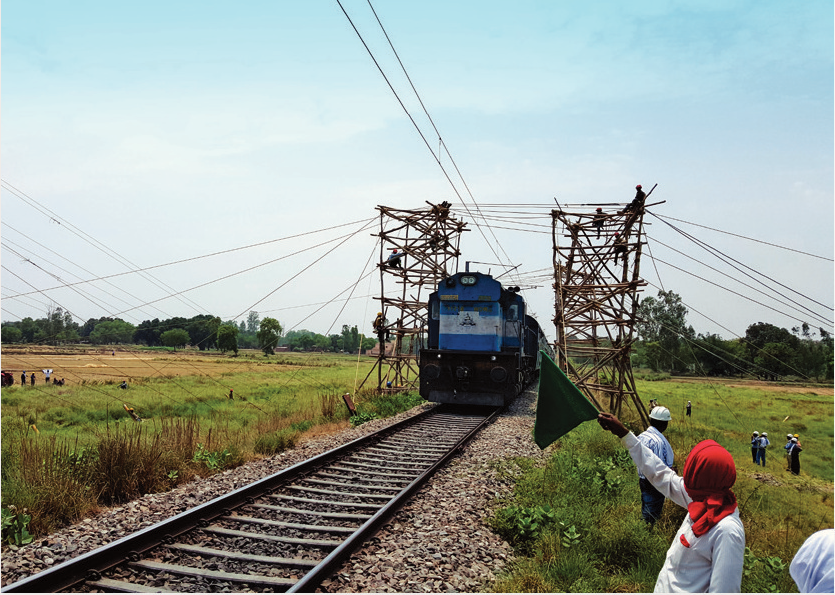
Stringing over a railway line
The success of sag bridges is translating into numbers: 15% increase in tower erection, 26.86% reduction in tools and tackles inventory, reduction of manpower by 35% during the final sagging activities and an overall reduction in the incident and fatality rates to 9.87% and 8.56% respectively during 2018-19.
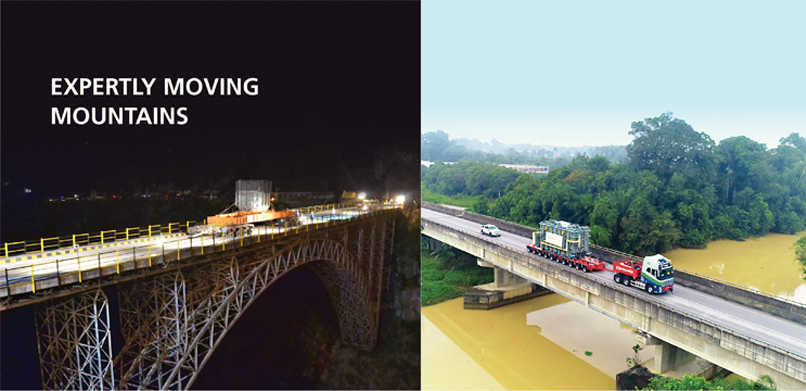
Safely moving hulking transformers to Wangtoo and Sarawak Substations
ENHANCING DELIVERY COMMITMENTS
Across PT&D’s factories in Pithampur and Puducherry, the process of production is driven through an internally developed, customized ‘PDSS 4.0 TL Tower Factory ERP’ software that monitors a range of tasks like BOM preparation, material requirement planning, cutting optimization, production planning, vendor planning, process control, QC checks, panel wise bundling and despatch. At the shop floor, the Theory of Constraint (TOC) approach is implemented to identify bottlenecks in the supply chain to streamline production processes. Considerable improvements have been made across various lines including galvanizing, beam production, fabrication of tower parts with reduced delivery lead times. Wastages in zine and binding wire consumption have also reduced. With tower wise despatches to sites, on-field teams have lead time, and cost and time are saved as there is no need for any segregation at site.
The demoulding time to produce precast poles in power distribution jobs has been brought down from 72 to 24 hours by changing the M40 mix design of concrete through admixtures that has also increased productivity and sales of poles.
Another process innovation at the 500 kV Chom-Bung Bang-Saphan 2 site in Malaysia has been a three-check point QR code that tracks elements from the factory, to the store and thence to the site through which likely shortages are immediately addressed, can be accessed any time and one can compare scope verses actually supplied tower elements.
“The transportation system was reconfigured with variable load distribution and simulated to reciprocate with the IRC Standard of the vehicle to transport without either strengthening or modifying the existing bridge.”
Sivakumar
Planning Engineer
Transporting huge, heavy-duty transformers, veritably a project within a project, have been successfully accomplished at Wangtoo in Himachal Pradesh and Sarawak in Malaysia that involved a cross-section of on-field tasks. At Wangtoo, the Special Projects and Construction Methods team stepped in to expertly move 9 of these hulking monsters across the Solding Khad and Jaypee Bailey bridges, that were the only link to the districts of Kinnaur and Lahal Spiti that are critical for army movement to the border areas. After a thorough analysis of the bridges, a customized solution was developed by reducing the self-weight of the system (without puller and trailers) and ‘skidding’ the transformers across. “To meet the bridge design requirements, the lattice girder system configuration was devised as an easy assembly and dismantlable pin connection,” shares Sivakumar, the Planning Engineer. “The transportation system was reconfigured with variable load distribution and simulated to reciprocate with the IRC Standard of the vehicle to transport without either strengthening or modifying the existing bridge.”
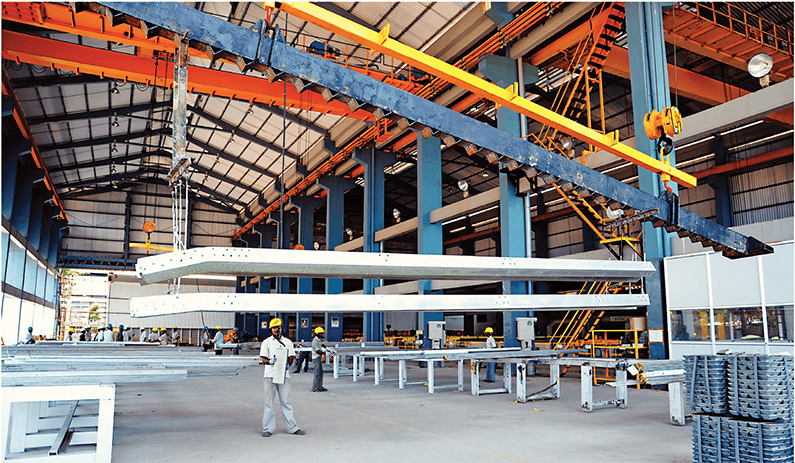
TLT factory Puducherry
At Sarawak, two 240 MVA Auto transformers with a freight weight of 143 tonnes, comprising mainly of a tank that was 9.5 meters long, 4 meters wide and 4.5 meters tall, had to be supplied to the Marudi Junction 275/132 kV substation project. It was a two-day journey from the Bintulu port to the site, the cargo moving at speeds of 5 to 20 kmph accompanied by escort vehicles. At site, the issue was to position the transformer to its plinth area along the live substation without a crane due to space constraints. “We introduced the hydraulic jacking and skidding technique for the first time in this region for the installation,” informs Mohana Dayalan, the Project Manager, and it took just 2 hours to position the transformer from the road to the plinth, perhaps the fastest and most effective skidding/Jacking method executed in this region.
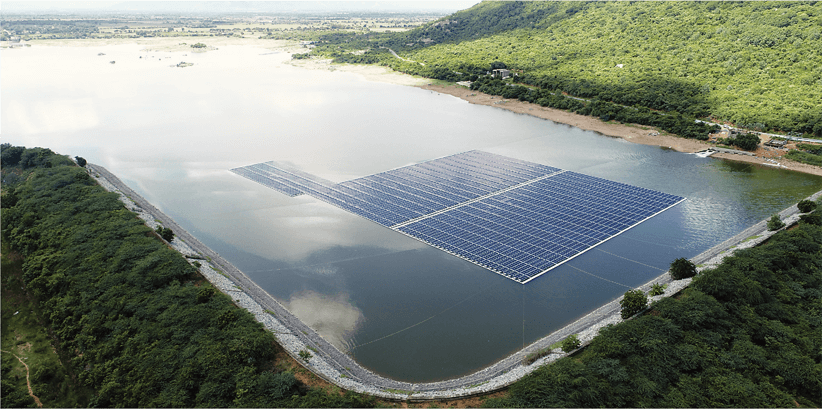
One of India’s largest floating solar plants, Tirupati
Ready for Commissioning Cell
Functioning as a nodal agency, an exclusive Ready for Commissioning (ROC) cell has been empowered to act and take decisions outside of the project team regarding any critical evaluation that calls for updates before issues are raised by the customer. Since this is an upfront evaluation before the client evaluates, the down time due to punch points have dropped drastically by 20%.
“The L&T SAHBT tracker is designed with higher structural stability and is easy to handle, assemble and maintain while its automatic, remotely controllable and unmanned operation makes it a safe solar installation.”
Shaji John
Head – Business Development & Proposals
PATENTING TECHNOLOGY
Several technological innovations have seen light of day in solar tracker and battery energy storage systems. One of the biggest by the Solar BU has been the indigenous development of the Automatic Single Axis Horizontal Bifacial Tracker with Specular Reflective Elements. “This is a high energy yielding platform with 18% more output than the horizontal single axis monofacial tracker,” mentions Shaji John, Head Solar BU. “The L&T SAHBT tracker is designed with higher structural stability and is easy to handle, assemble and maintain while its automatic, remotely controllable and unmanned operation makes it a safe solar installation.”
Since backend service is just as important in product development, the Solar BU has developed an automatic module cleaning system that reduces water and manpower requirement by a whopping 70 to 80% while increasing energy generation by 2 to 5% in comparison to conventional methods. With the technology patents to be formalised shortly, these products will be a shot in the arm and a decisive competitive edge for the Solar BU when tapping global markets.
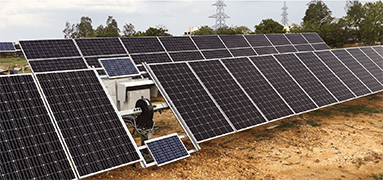
Single axis tracker block and single row tracker variants
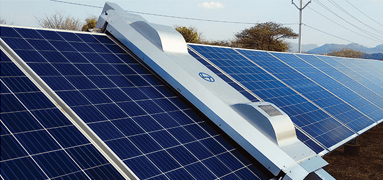
Solar automatic cleaning system
Championing OPEX
The future is all about how the OPEX initiatives are championed by bringing technology to the fore and automating processes to ultimately give customers greater value and timely delivery. “As the ‘Columbus’ of L&T and as we make inroads into newer geographies, scaling up OPEX initiatives is the way forward to achieve operational excellence,” rounds off TMD.