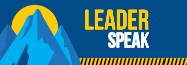
RAJEEV JYOTI
Chief Executive, Railways SBG
Railway Projects are unique in many ways. Our focus on improving operational efficiency involves a multi-faceted approach that involves a combination of strategic initiatives, expert project planning, and innovative methods to execute speedily and cost-effectively.
Some of the these aspects include :
- Large scale deployment of mechanized construction techniques for rapid progress of both Trackwork and OHE projects and monitoring of turnaround time of all P&M through GPS based digital technologies. This includes New Track Construction (NTC) machines for trackwork along with a multitude of other track finishing machines. On the OHE front, besides mechanized OHE wiring, multiple mechanized methods are followed for Cylindrical Auger foundations and OHE mast erection as well.
- Our pioneering venture to implement Linear Project Management tools like ‘TILOS’ is to effectively visualize and plan mega linear projects across domains.
- We are harnessing Digital technology for Supply Chain Management by developing various apps that drive ‘Store to Site’ planning in OHE and S&T works.
- Leveraging strengths on the Design and Engineering fronts across multiple domains like track alignment, traction power simulations, interface design, ballastless track works, signaling design through state-of-the-art design software and BIM.
- Strong focus on safe work practices leveraged through digital technologies viz; Virtual Reality based training for workmen to emphasize the criticality of working along ‘live’ tracks.
- Nurturing an innovative culture for Operational Efficiency through institution of awards – Digital implementation, Energy Optimization, Large Scale Reuse of / Waste, Time Reduction, Advancements (DELTA Awards)
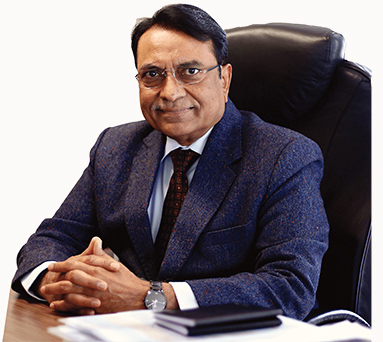
LAYING TRACKS OF GROWTH…EFFICIENTLY
The Railway SBG story
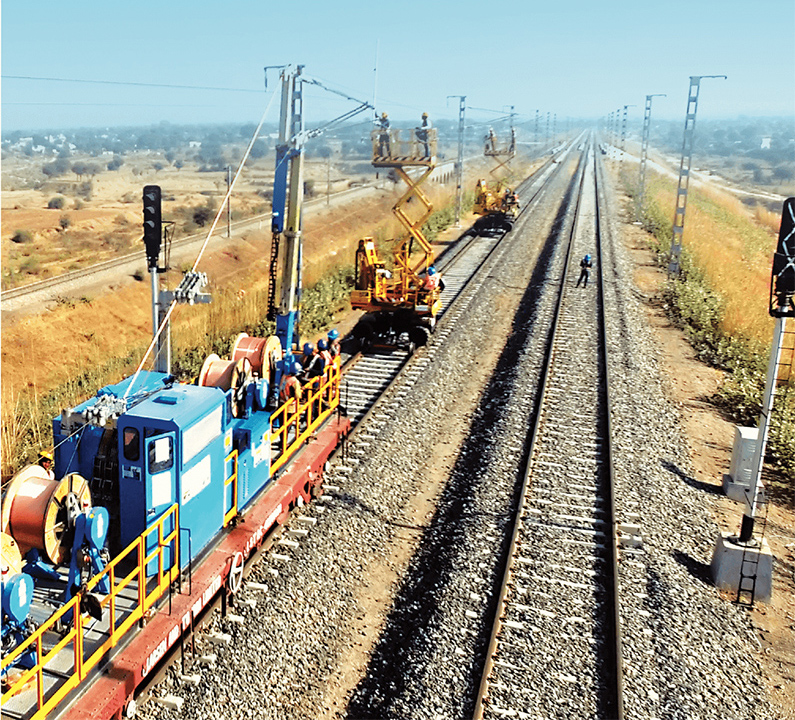
The Railways business is unique and railway projects are unique in many ways. A case in point is a major project in the Western Ghats that requires OHE installations in 70+ tunnels and 125 bridges over a stretch of 428 km, 90% of which is single line. A project of this complexity throws up a welter of challenges: of working amidst highly restrictive ‘block sections’ involving significant material handling and extraordinary erection ethodologies. Unique challenges require unique solutions, like in this case, installing OHE using gantry structures without impeding normal train movements, with minimal dependence on ‘traffic block’, developing ‘quick transfer containers’ to shift OHE foundation material to difficult locations and such like. This ability to think on their feet and evolve clever strategies, has transformed the Railway business from a simple EPC player into a large-scale Rail Systems Integrator. Proof of pudding is an order book that has grown 5 times along with revenues and profits.
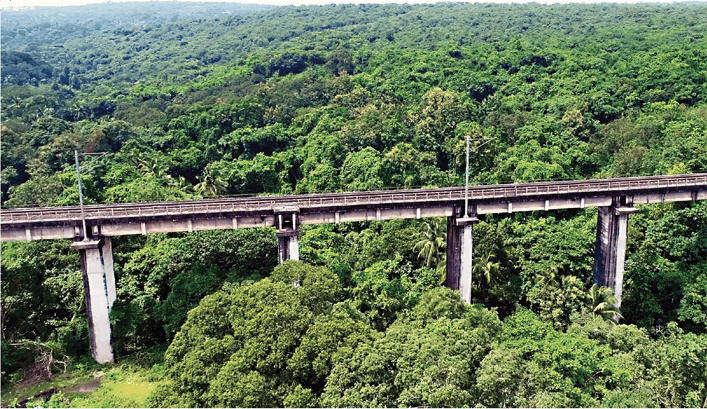
“Apart from a paradigm shift in our execution, our focus has been to improve our operational efficiency through a combination of strategic initiatives, expert project planning, innovative methods to execute speedily and cost-effectively,” shares Rajeev Jyoti, Chief Executive, Railways SBG, “but what has really helped us is a culture of efficiency that we have created and perpetuated within our business.”
The Dedicated Freight Corridor (DFC) projects have radically changed the way the Indian Railways approach projects and, at the same time, as rail systems integrators, the Railways business has continuously morphed itself to meet new and more exacting demands.
“Apart from a paradigm shift in our execution, our focus has been to improve our operational efficiency through a combination of strategic initiatives, expert project planning, innovative methods to execute speedily and cost-effectively, but what has really helped us is a culture of efficiency that we have created and perpetuated within our business.”
Rajeev Jyoti
Chief Executive, Railways SBG
Stretching efficiency over hundreds of kms
DFC projects are primarily mega civil & track works involving multiple linear activities spread across hundreds of km featuring numerous minor and major bridges. These require location design and construction activities that must be visualized and conceptualized in planning to optimally utilize resources and movement of heavy track equipment like the NTC machines and tamping and ballast regulating machines. In response, the SBG was amongst the first to introduce Linear Project Management tools like ‘TILOS’ – to effectively visualize and plan mega linear projects across domains. Driven by a dedicated ‘Track Planning Cell’, this strategic initiative facilitates centralized planning of not only civil & track projects but mega OHE projects as well.
Excellence in logistics and P&M turnaround time
The NTC machine is truly a workhorse for DFC projects. This ‘over a km long machine train’ carries about 2,000 precast sleepers and 250 m long welded rail panels to lay 1.5 tkm. “We need to optimize the movement of the NTC machine as it spreads the sleepers and lays tracks at the rate of some 2 km a day,” says S.Ramkumar – VP & Head Mainline BU, “of course there are issues to be solved,” he adds, “RoW and incomplete sections can seriously impact productivity but through TILOS we are able to visualize the overall project in a snapshot and plan critical activities like NTC machine movement months ahead.” Timely refurbishment of rakes carrying sleepers and rails is yet another logistic challenge the team faces to ensure that the NTC machine functions optimally. Besides, a large battery of Ballast hoppers is digitally monitored to optimize ‘Hopper Turnaround’ time.
On the OHE front, simultaneous stringing of contact wire and catenaries under tension reduce both operational costs and execution time.
Besides wiring, multiple mechanized methods are followed for Cylindrical Auger foundations based on site conditions that includes Auger on Crawler based RRV and tractor/trolley mounted Auger. A similar multipronged approach is followed for mast erection as well.
Self Sufficiency in OHE structures
“Our association with the Railways has leapt from about 7,500 tkm of OHE a decade ago to over 16,000 tkm now with the advent of the DFC and other large EPC projects from the Indian Railways mainline,” points out Rajeev that has, at the same time, increased his requirement for OHE structures including 13 m high rise masts for double stack containers. Managing the existing vendor base and insulating the business from price spikes are critical considerations for Rajeev that has led to the establishment of a new OHE
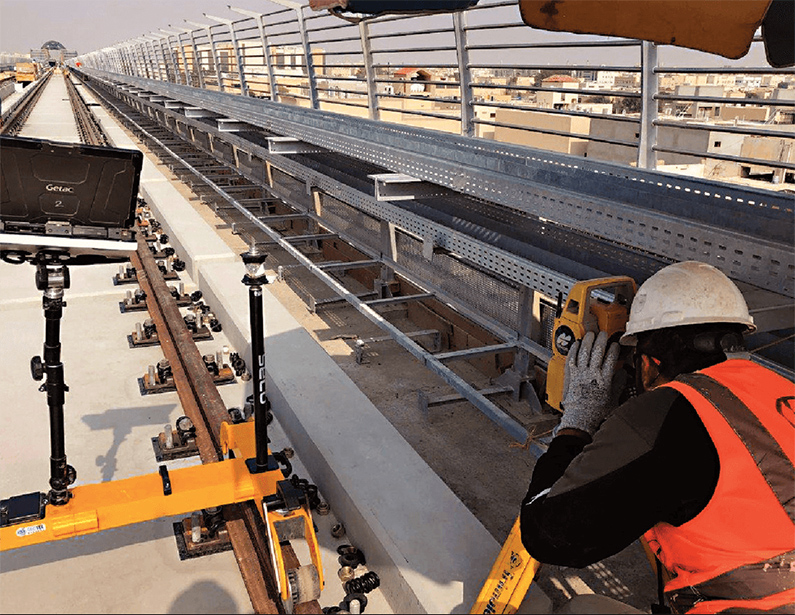
Riyadh metro track work
“We need to optimize the movement of the NTC machine as it spreads the sleepers and lays tracks at the rate of some 2 km a day. Through TILOS we are able to visualize the overall project in a snapshot and plan critical activities like NTC machine movement months ahead.”
S. Ramkumar
VP & Head Mainline BU
fabrication and galvanizing facility at TL factory, Pithampura with a capacity of 36,000 MT/annum. “Our sense of urgency is reflected in the fact that the fabrication facility was set up and fully functional in double quick time,” smiles Ramkumar
Driving efficiency along several tracks
A first-of-its-kind GPS-based ‘Central Command Centre’ was deployed by the WDFC project team to monitor and track a multitude of high value and specialized track and OHE construction machines, provide track linking completion status updates, trigger collision warning alerts to both the driver and LC gate operator when approaching LC gates.
‘eM Track’ drives ‘Store to Site’ planning and is specific to OHE and S&T works. With numerous components involved, the non-availability of even one component can throw productivity off the rails. By promoting inter store and store-site interaction, ‘eM Track’ significantly reduces working capital requirements without compromising project progress and since railway activities are linear, most of these applications are mobile based.
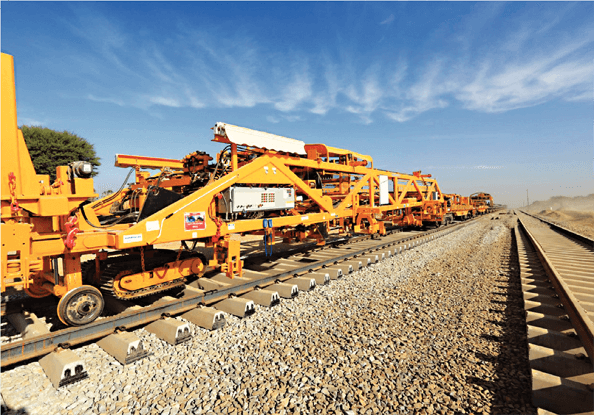
New track construction machine
Making the engine room more efficient
On the engineering and design fronts, the business has assimilated in house talent across multiple railway domains like track alignment, traction power simulations, interface design, ballastless track works, signalling design and much more. “For Track and OHE designs, we use advanced design software like Bentley; STAAD Pro to generate Alignment Designs, Engineering Scale Plans, Layout Plans (LoP), and Signal Interlock Plans (SIP) to name a few,” informs Shiv Gupta – Head EDRC Railway SBG , ‘and we are moving towards simultaneous linking of track ESP (Engineering Scale Plan) with LoP and SIP leading to BIM.”
“Safety is a critical consideration and more so in linear railway projects, for which we have been leveraging digital technologies viz; Virtual Reality based training for workmen to emphasize the criticality of working along ‘live’ tracks.”
Alok Sharma
Head Safety
Harnessing the benefits of digitalization across domains
“Safety is a critical consideration and more so in linear railway projects,” says Alok Sharma – Head Safety, “for which we have been leveraging digital technologies viz; Virtual Reality based training for workmen to emphasize the criticality of working along ‘live’ tracks.”
The implementation of PROCUBE across all railway projects has given top management comprehensive daily overview snapshots of projects, supported by periodic drone-based video capture. SPEED is another initiative to improve Site Productivity Efficiency and Excellence through Digital means while ‘Asset Insight’ tracks and efficiently monitors P&M.
“We have developed and implemented a QR Code system at site for effective control of drawings,” adds Shiv Gupta. An app-based solution to raise, approve and monitor RFIs (Request for Inspection) too.
RACE initiatives have been adopted to benchmark cost and a structured process to benchmark suppliers on multiple parameters has already resulted in significant savings on big-ticket system vendors. RACE has ushered in a greater degree of understanding that has triggered the creation of a significant database and increased partnership with specific stake holders both locally and globally.
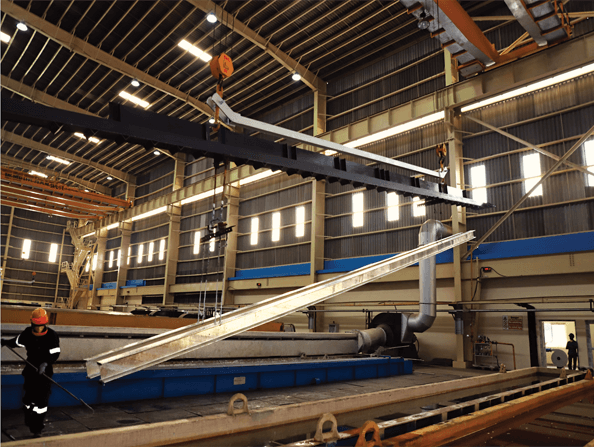
OHE fabrication and galvanizing facility at TL factory, Pithampur
Enhancing skilled manpower base
More ‘Front Line Supervisors’ are coming through the Competency Centre in Kanchipuram, one of the finest and first amongst Indian private companies to train manpower in the railway domain, with the requisite theoretical and practical on-the-job training to address Track and OHE requirements.
“The business is extremely challenging and very often we are treading challenging terrains, but I guess that is the thrill of meeting these challenges head on and driving the business forward to new frontiers.”
Rajeev Jyoti
Chief Executive, Railways SBG
Nurturing an innovative culture for Operational Efficiency
At the end of the day, for Rajeev and his senior management team to drive productivity, it is imperative to create and nurture an innovative culture and one step in that direction has been the institution of the DELTA Awards – Digital implementation, Energy Optimization, Large Scale Reuse of / Waste, Time Reduction, Advancements (Innovation) Awards that attracted as many as 89 implemented entries from across the Railway SBG.
“The business is extremely challenging and very often we are treading challenging terrains,” says Rajeev with a serious and piercing look, “but I guess that is the thrill of meeting these challenges head on and driving the business forward to new frontiers.”