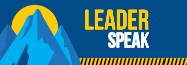
Rajeev Jyoti,
Chief Executive (Railway SBG – TIIC)
At Railway SBG, Safe work practices are paramount to our business.
Railways projects, being linear in nature, are typically spread across hundreds of km with a multitude of discrete risks that are both location and task specific. Therefore, risk identification and mitigation is a continuous process involving multiple teams across various stretches of the project. Safety is a key priority for the leadership team and the project organization structure has been evolved to provide significant autonomy to the function of Safety.
Across projects, EHS methodologies are monitored and improved through regimented protocols and systems through Quarterly Audit Rating Score (QARS) – a 20-point comprehensive process to evaluate EHS performance and identify thrust areas that are further benchmarked through cross project reviews during periodic Safety Conclaves. Such methods allow us to update project specific requirements To mention, one of our projects in the Western Ghats involves OHE installation in over 70 tunnels and 125 bridges over a stretch of 428 km (90% single line) that brings in numerous challenges in the implementation of safe work practices while working amidst highly restrictive ‘block sections’ involving significant material handling and unique erection methodologies.
Our projects have won top category awards from National Safety Council of India – four year in a row including the prestigious ‘Golden Trophy Award’ in the Construction Segment twice in the last 4 years. Besides, we continue to be at the forefront in harnessing Digital technologies to evolve innovatives solutions towards mitigating Safety challenges.
Irrespective of the huge challenges, as a SBG, we remain committed a high level of Safety awareness and to improve our safety performance – towards ‘Mission Zero Harm.’
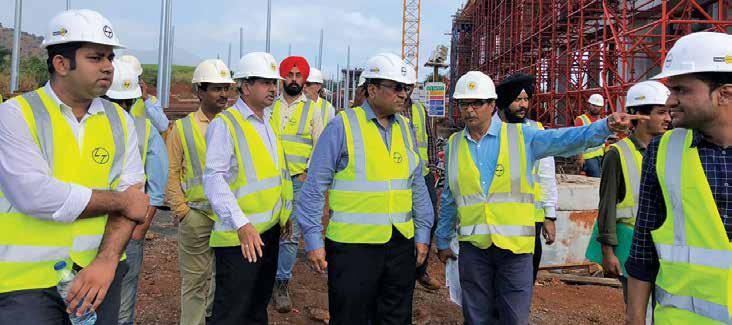
SAFELY DIGITAL!
As the digitalization wave sweeps across the organization, its enormous benefits are gradually becoming evident to improve productivity, reduce waste, cut costs, quicken execution time and thereby enhance overall efficiencies. Multiple spheres are enjoying the positive impact of digitalization, none more than the realm of Safety.
“Our digital approach to safety is four-pronged,” begins Chief Digital Officer, L&T, S Anantha Sayana, doodling on his favourite white board. “Our primary focus is on awareness building and education featuring immersive learning with Virtual, Augmented and, in some cases, Mixed Reality. Next comes process compliance involving mobile apps to capture check lists, work permits, manage EHSMS and EHS inspection processes, SOPs, and so on. Workmen tracking is another area of implementation with alerts on entering ‘no-go’ or hazardous zones, to mark attendance, measure productivity. Finally, we have sensors, beacons, fatigue detection devices, gas detectors that stream ‘live’ data.”
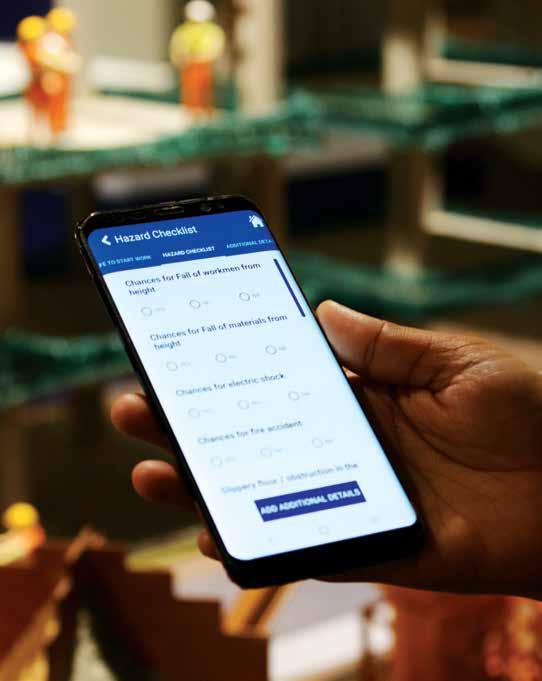
Safety app in action
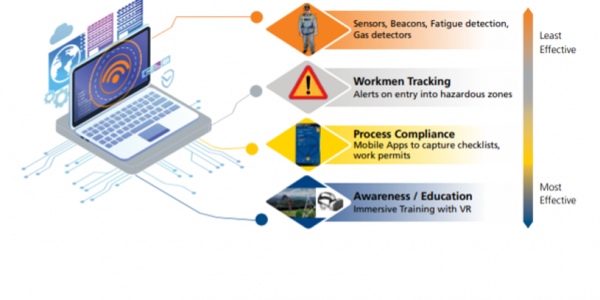
Digital reality checks
Safety training through immersive VR gives workmen and employees a ‘real life’ feel of situations. “We have developed around 40 modules, trained over 30,000 workmen across 5 of our businesses,” informs Krithika Venkatesh, Senior Manager – Digital. The VR training modules cover a wide range of situations that are IC-specific: fall from temporary platforms, fall from lift shafts, vehicles parked on slopes, being B&F specific; fall from height when working next to water in a marine environment and fall from height when working on a cable stay bridge relevant for both B&F & Heavy Civil; excavation for TI; power tools operation, working over ladder mobile scaffold working platforms, panel shifting and erection equipment installation, soil collapse foundation activities, horizontal movement on towers, dead-man anchoring and tower back stay specific to PT&D while fall from height straddles almost all verticals.
“We have developed around 40 modules, trained over 30,000 workmen across 5 of our businesses.”
– Krithika Venkatesh
Senior Manager – Digital
“We have been the early adopters to use Virtual Reality modules for our safety training of workmen,” informs Digital Officer, PT&D – Ashok Varadhan P, “and the response from workmen has been extremely positive. In fact, some of them became very emotional after the VR experience and commented that the experience had helped them realise the importance of safety. Another mentioned that henceforth he would think of his family every time he climbed a transmission line tower. This impact has motivated us to develop more such modules and today we have covered all the critical activities involved in our TL, UPD and substation businesses using VR.”
“We have been the early adopters to use Virtual Reality modules for our safety training of workmen and the response from workmen has been extremely positive.”
– Ashok Varadhan P
Digital Officer, PT&D
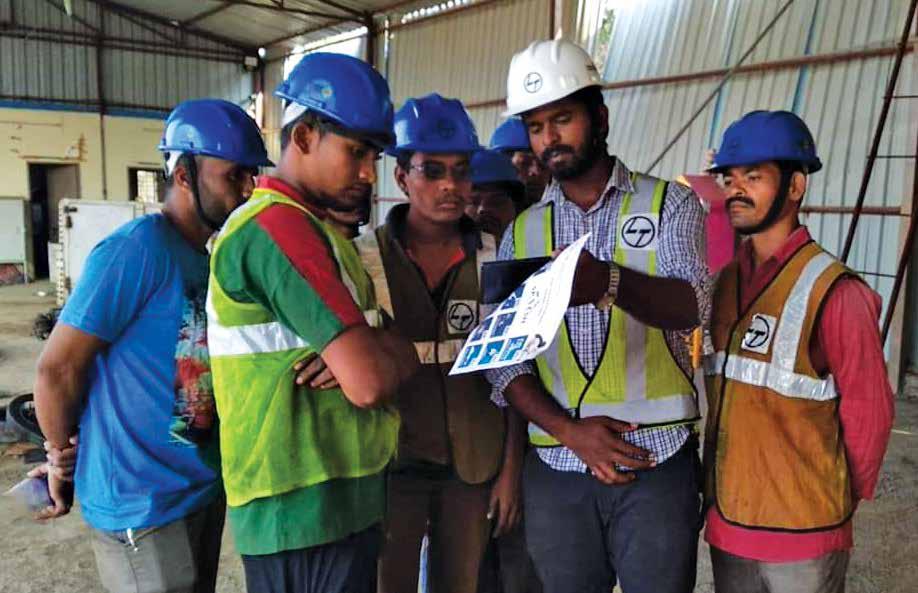
Pep talk
Apart from adopting Virtual Reality for Safety training, Digital Officer of TI IC, Utkarsh Desai shares that an app named SPARSH (Standard Precautions Using AR for Safety & Health) is under development and he looks forward to the opportunity of using this AR app to train workmen at his sites.
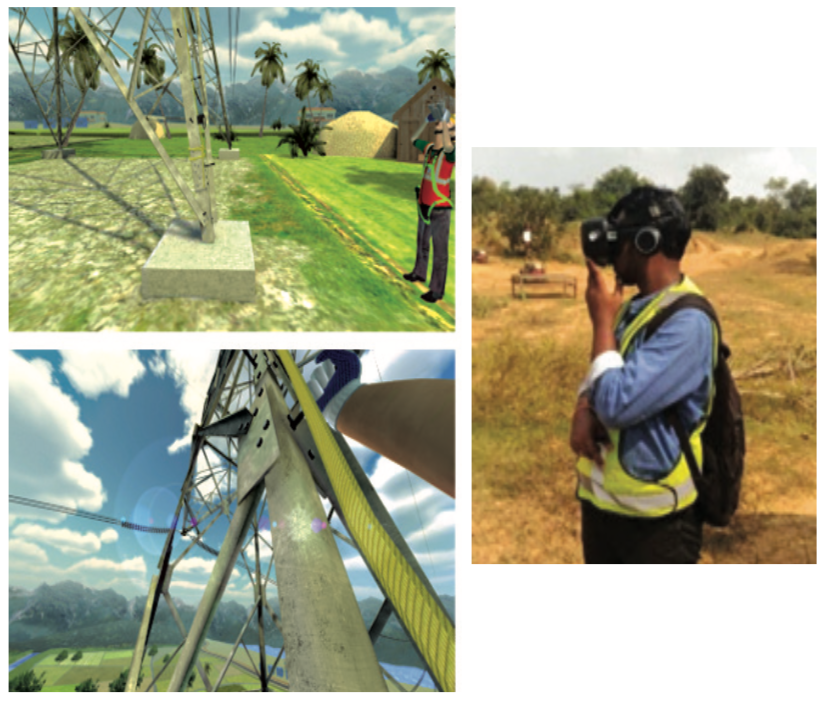
Snapshot of a virtual reality module
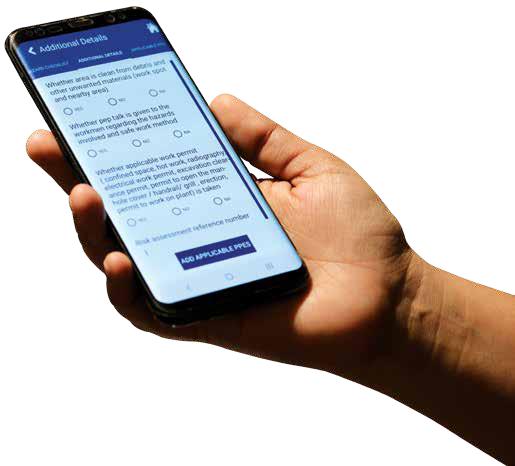
“Apart from adopting Virtual Reality for Safety training, an app named SPARSH (Standard Precautions Using AR for Safety & Health) is under development.”
– Utkarsh Desai
Digital Officer of TI IC
The Safety Innovation School (SIS) located in Kanchipuram is something very close to EHS Advisor, B&F IC M Kamarajan’s (MK) heart as he holds forth with passion, “we are in the process of putting together the building blocks to offer an engaging experience to participants that will include interactive AR content on a mobile app, immersive VR experience using Oculus Rift for fire safety, safety when working in confined spaces and gas cutting.” The app will provide participants real-time engagement for pre-visit, onsite and post-training activities, take up online tests and give feedback. “We will also use existing VR modules through Oculus and Procus and soon SIS is set to make a marked difference to the efficiency of individuals who undergo sessions here,” he says confidently.
“We will also use existing VR modules through Oculus and Procus and soon SIS is set to make a marked difference to the efficiency of individuals who undergo sessions here.”
– M Kamarajan
EHS Advisor, B&F IC
“Without doubt, this initiative (Safety App) of ours has the highest adoption, B&F IC has been both the early adopters and the most comprehensive users covering almost all the developed applications.”
– Krithika Venkatesh
Senior Manager – Digital
Safety reporting made simple
Launched in November 2016, the mobile Safety App has been a runaway hit with 16,000+ users, covering some 550 projects cumulatively raising 1.5 lakh forms per month. ‘Without doubt, this initiative of ours has the highest adoption,” enthuses Krithika. “B&F IC has been both the early adopters and the most comprehensive users covering almost all the developed applications. The modules that have already been rolled out include pre-start, work permits, safety improvements, near miss reporting, EHS violation memos, EHS observations, escalations for non-compliance, audit modules with mailers and escalation, CAT module with mailers and escalation, inspection checklists and executive feedback.”
The safety app assists site engineers and managers to update site workers on safety rules at the mere tap of a screen. “It works like a perfect interactive communication medium,” shares Mohan Babu, Digital Officer, HCI, “it reduces physical interactions and has made documenting workplace safety incidents extremely easy. Upload of photographs as evidence to the pre-start form has helped us to improve the efficiency of our safety staff.” Apart from enhancing site efficiency, documents are now available anytime, anywhere on the cloud.
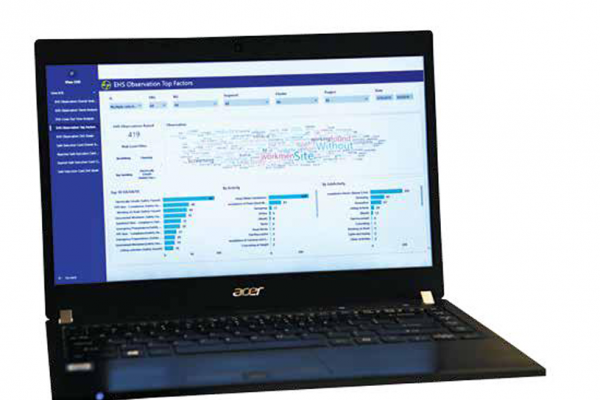
EHS observation dashboard on PowerBI
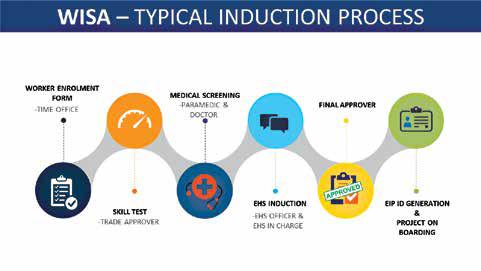
“It works like a perfect interactive communication medium, it reduces physical interactions and has made documenting workplace safety incidents extremely easy.”
– Mohan Babu
Digital Officer, HCI IC
What’s your safety score?
Welcome ‘ViewEHS’, a revolutionary and one-of-its-kind digital solution, that captures all EHS data, compares them with baseline data and assigns KPI scores to analyse EHS performance of all sites in real time. “It has brought in unprecedented transparency in overall site EHS assessment with minimal human intervention,” for Head – EHS, WET IC & SWC BU, K S Sudheesh Kumar and a matter of great relief too which is why he has promptly implemented ‘ViewEHS’ across all sites in both WET IC and SWC BU.
The ‘ViewEHS’ platform comprises 37 objectives clubbed under ‘5 Arms of EHS’ to monitor day to day EHS implementation. The five areas being Proactive Measures, Audit Inspection Outcomes and Compliances, Incident Communication, Investigation and Corrective Action, Training & EHS reviews and IMS Implementation & Documentation. All the activities and sub-activities in WET and SWC have been mapped comprehensively with their respective hazards, risks, SOPs, checklists and permits.
Sudheesh declares proudly that “We received the copyright for ‘SafeArmz’, the earlier version of ViewEHS, so this is surely a world-class digital EHS management solution and we plan to go a step further and apply for patent rights as we believe no such solution exists right now across the EPC Industry.”
“The mobile app features asset registration, online and offline inspection of assets and ready reports while the web app enables user and project on-boarding, QR code generation and dynamic report generation.”
– Prabhu V
Senior DGM – Digital
Ib4U aka Inspect before Use
Periodic safety inspection of assets and facilities is now possible with Ib4U, that has both a “a mobile and a web avatar,” informs V Prabhu, Senior DGM – Digital. “The mobile app features asset registration, online and offline inspection of assets and ready reports while the web app enables user and project on-boarding, QR code generation and dynamic report generation.”
Canteens, offices, stores and workmen habitats have been on-boarded while some of the P&M assets on-boarded include tower cranes, DG sets, passenger hoists, plants, supplier vehicles, rope suspended platforms, vehicle & earth moving equipment, RCCB and power tools. Fire extinguishers, ladders, safety harnesses and scaffolds are other aspects that can also be inspected with Ib4U.
Knowing your workman up close and personal!
WISA or Workforce Induction & Skills Application is an end-to-end worker information system that comprises a complete induction process including a digital health screening kit. A QR-coded worker ID can be generated for all onboarded workers, which in turn can be used to capture worker attendance at work site, view his details, training records, site passes, etc. The mobile interface can record observations, appreciations and make behaviour notes. “All sites are constantly struggling with the lack of skilled manpower but once you find this rare commodity, we will go a long way to have the right man for the right job,” says Balaji Kasiram, Head Digital – Technical, “WISA is a repository of information of workmen that are relevant for sites especially at the point of deployment and execution.”
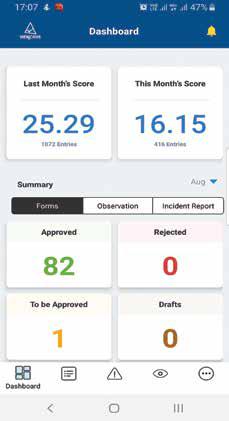
ViewEHS – Performance scorecard
“All sites are constantly struggling with the lack of skilled manpower but once you find this rare commodity, we will go a long way to have the right man for the right job.”
– Balaji Kasiram
Head Digital – Technical
Face recognition is possible in WISA using a reference image uploaded at the time of induction. The worker is captured on camera at site through a mobile app and identified using an AI engine. WISA is therefore ideal to find out attendance or to just observe the behaviour of a particular workman.
“WISA has helped us improve our worker on-boarding process at several B&F sites,” shares S. Suresh Kumar – DGM – Site Administration & IR, B&F IC. “We feel WISA has huge potential to transform our interface with workers and contractors in a big way.”
“WISA has helped us improve our worker on-boarding process at several B&F sites. We feel WISA has huge potential to transform our interface with workers and contractors in a big way.”
– S. Suresh Kumar
DGM – Site Administration & IR, B&F IC
How healthy are you?
The VinCense Health Screening process is about making occupational health screening oh-so-easy. When a workman arrives, he is registered as a new person following which his vitals like blood pressure, glucose, weight, pulse rate, etc. are screened using the VinCense HSP. This data is updated real time into the WISA platform which is then made available to the doctor on the platform during physical examination. “The entire screening process takes only about 4-5 minutes per person,” says Krithika, “saving time to the tune of some 77% from our erstwhile processes. Induction is so much easier,” she laughs.
Alchemy – turning data into insight
In olden times, alchemy was considered the science of turning base metals into gold. The role of the ‘Alchemy’ analytics platform for the Digital team is almost as crucial as it ingests data from multiple sources and derives insights by capturing patterns and trends from the data. It sources data every month from P&M, IoT devices, Procube, Safety and Quality solutions and presents them as business intelligence dashboards with the capability to perform – descriptive, diagnostic, predictive and prescriptive analytics. In the realm of Safety, Alchemy processes approximately 1 TB a month from 1.5 lakh forms to provide safety performance dashboards such as submission time analysis for permits, rejection analysis of permits, types of observations recorded, time analysis for closure of observations, and so on.
“We capitalised on this opportunity and were able to build the ML model based on the rich data generated from the forms submitted during 2017.”
– P S Rajkumar
Digital Officer – B&F
Machine Learning (ML) models have been next on the Digital team’s agenda, developed to mine insights from the textual data generated from the various forms submitted through the Safety App like reasons for rejection, classification for permits and EHS observation classifications. Digital Officer – B&F, P S Rajkumar traces the IC’s digital journey from 2016. “We capitalised on this opportunity and were able to build the ML model based on the rich data generated from the forms submitted during 2017. For example, we were able to unearth the major categories for rejection of permits based on the type of project and prioritise focussed training interventions for the site staff.”
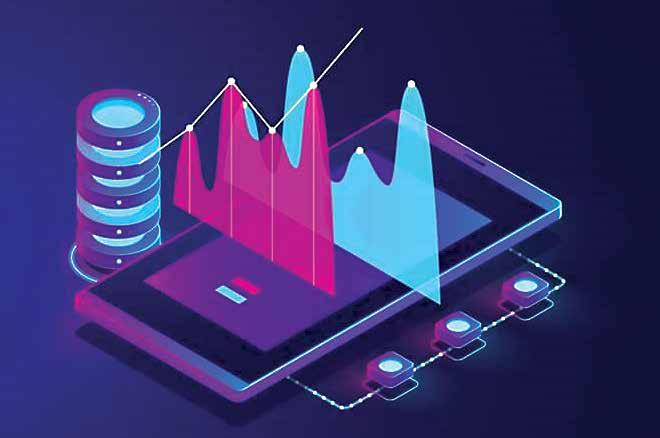
Matters have progressed a fair bit, emphasizes Ashwin VK, Senior Manager – Analytics. “Currently, we are analysing events before and after an observation submission, correlating findings with work permits and their rejections and are able to predict potential hazards that could lead to near misses. After we develop the model, we believe, that we will able to predict unsafe practices and give prescriptions to prevent such incidents.”
“Currently, we are analysing events before and after an observation submission, correlating findings with work permits and their rejections and are able to predict potential hazards that could lead to near misses.”
– Ashwin VK
Senior Manager – Analytics
AI is already making safety A1
Artificial Intelligence (AI) has opened a huge new vista of intervention in construction and safety is a big gainer. “The versatility of AI is what makes it a game-changer,” is how Anantha Sayana describes the veritable AI invasion. “A typical construction site covers a large area, multiple zones and varied activities, posing a challenge to the safety staff at site to maintain safety controls. AI aids our staff to detect unsafe acts and conditions through live video feed from CCTV cameras.”
For example, computer vision (CV, a branch of AI) can detect unsafe acts like not wearing a helmet or harness, working at edges without a harness or working without safety shoes. It can detect unsafe conditions like missing barricades, absent safety nets or sense loose material around edges. AI can also answer questions like “How many workmen are on site at a given point in time,” “How many machines are at work,” “What is the current stock of material at site?” or even a question relating to whether it is safe to walk on a platform or not.
Apart from CV, AI can churn out safety form texts into meaningful insights using Natural Language Processing (NLP) and the two together can provide a comprehensive view of safety risk levels and hazards for the site, enabling site personnel to take proactive measures and controls.
At present, AI predicts exciting times ahead!
“We see our AI and other digital tools to soon play the role of a Man Friday for the EHS Head, giving him timely alerts and prompting action that enables immediate decision-making and, most importantly, saves his time. The future is almost here!”
– S Anantha Sayana
Chief Digital Officer, L&T
Enter the digital Man Friday!
A common sight at construction sites is of EHS managers constantly running around attending to a variety of never ending issues. An equally common complaint from EHS personnel is that they are forced to be too action-orientated with very little time to think and contribute strategically. This situation could undergo a sea change soon thanks to digitalization.
Imagine a scene circa 2022. An EHS Head, just starting from home for work, checks his mobile and finds all the designated tasks for the various sites under him, across geographies. The AI tool alerts him of a non-compliance at a residential site: a workman is on a top floor without full body harness. He can immediately alert the EHS Incharge to rectify the situation. Another ping: another alert; an unsafe activity has just commenced at another site without proper sanctions. Depending on the severity of the issue, the EHS Head can act. By the time he reaches his site office, all the immediate issues have been tackled. He is now free to settle down and think beyond.
“We see our AI and other digital tools to soon play the role of a Man Friday for the EHS Head, giving him timely alerts and prompting action that enables immediate decision-making and, most importantly, saves his time. The future is almost here!” Anantha and his merry band are preparing to usher it in sooner rather than later!