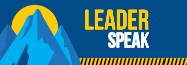
S. Rajavel,
Senior Vice President & Head (Water, Smart World & Communication)
Over the years, we, at WET IC, have institutionalised the culture of responsibility and accountability towards EHS at all levels of the Management. Transparency in reporting of all Unsafe Acts, Unsafe Conditions and Unsafe Behaviour and implementation of various safe to-start systems through online and digital have brought an unprecedented level of safety and productivity improvement at the sites.
This is further exemplified by the fact that WET IC reported ZERO FATAL INCIDENTS in the financial year 2018-19. With the business growing exponentially and huge influx of skilled and unskilled workforce at our sites, we must gear up to ensure that the management of EHS policies, procedures, objectives and digital systems are practiced and implemented at all our sites through training and awareness programs.
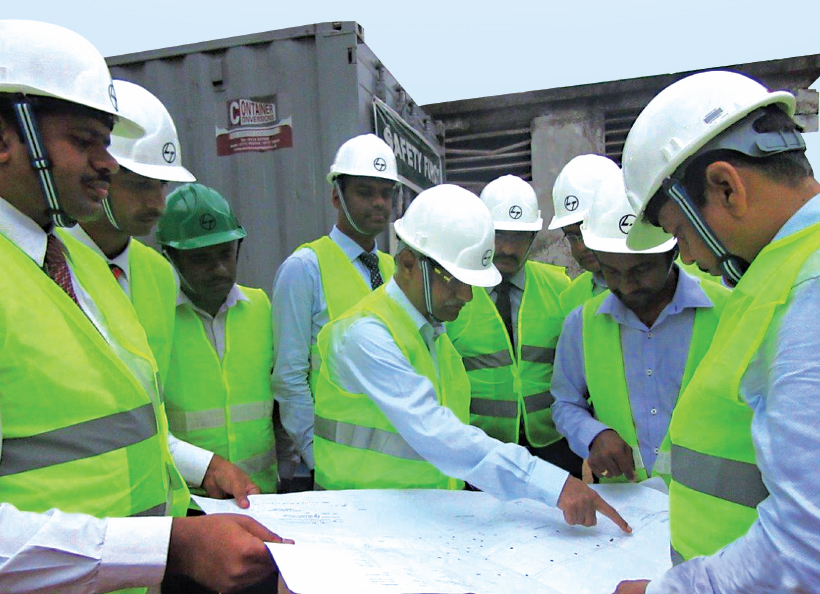
MAKING EVERY DROP COUNT
Strategizing safe methods for building defining water infrastructure
When you turn on your tap, have you ever given a thought as to how water is flowing from it? It is in fact a long journey from the delivery end to the tapping point, a complex maze of conduit network, building which is an engineering challenge. Every water infrastructure project is fraught with many risk factors though for L&T Construction’s Water & Effluent Treatment IC, it would be familiar ground with the experience of having constructed over 5 lakh+ km of channelized water & wastewater network, more than 7100 MLD of water, wastewater and effluent treatment plants and irrigated 7.3 lakh hectares of land. With over 20 million people benefiting from these various water infrastructure projects, there is a lot to share on how we make every drop count!
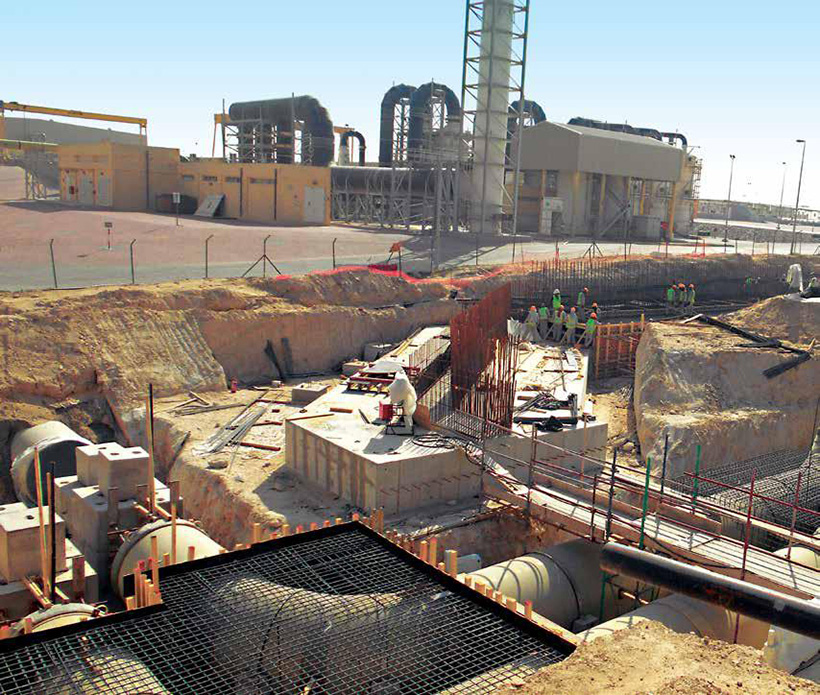
Deploying a safe zone work policy at the Jebel Ali STP
Prioritising critical civil works
While pipelines are the arteries of water projects, the critical structures are the heart of the system that tap and treat water from its sources. Raising such structures calls for a detailed safe approach as the scope largely involves precise civil and mechanical works as Project Director, Syed Abdul Noor, and team at the 375 MLD Sewage Treatment Plant in Jebel Ali found out. “This is probably the largest STP that we have constructed covering an area of 4 km X 1 Km comprising 54 major civil structures with 12 large diameter clarifiers, 6 anaerobic digester tanks, 77 tank clusters and other building structures. There are 20 pre-sedimentation tanks to capture the settable solids and 16 aeration tanks in which oxygen breaks down the contaminants. All these structures are interconnected by an impressive network of large diameter pipes to move 375,000 tons of water for treatment, 24/7, all year long.”
“With excavation as deep as 12 m and the water table around 6 to 8 m, it was critical to first stabilize the soil to prevent collapse of equipment in the trenches,” shares K.A. Muralidharan, the EHS Incharge. “We conducted necessary soil testing prior to execution and engaged a dewatering specialist to implement continuous dewatering and necessary slope protection.”
“We implemented a zoning system with the entire project divided into 7 control areas by breaking down the construction activities to align each activity with individual targets that were monitored daily through the Time Quality Report (TQR).”
– Syed Abdul Noor
Project Director – Jebel Ali STP
To make work secure, “We implemented a zoning system with the entire project divided into 7 control areas by breaking down the construction activities to align each activity with individual targets that were monitored daily through the Time Quality Report (TQR),” shares Noor adding that a timetested safe methodology with on-field improvisations was largely instrumental for success. “Mapping the activities through TQR helped to add thrust wherever required with additional manpower for lagging tasks. During peak operations the site looked more like a heavy civil job with 21 tower cranes operating between 45 to 65 m boom lengths whose safe manoeuvring was backed by a 32-channel communication system comprising 123 radio sets among operators, riggers and supervisors.”
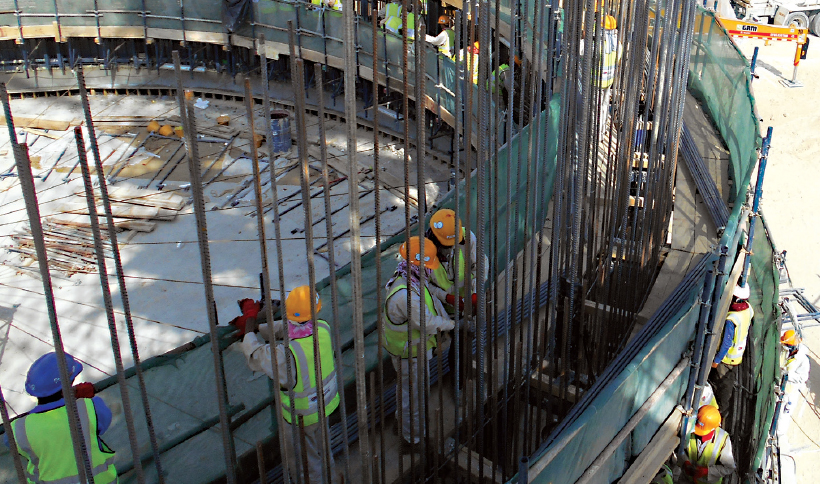
Creating a secure staging system
A tall order of constructing 179 structures across more than 40 locations at the Adilabad Water Supply Scheme, was brought down to 125, thanks to the team’s strategic review of the alignment. “Whenever we hit a road block, we brainstormed a lot and ideas just flowed,” quips R.K. Subramani, Project Manager, “Our plan to do precast chambers over the conventional mode fast tracked the entire process across the hilly segment with 90% of chambers casted in a yard thereby facilitating seamless transportation and erection. With close to 10,335 valves under our scope, we raised the bar to ensure that the butterfly and sluice valves were preassembled in a centralized yard to safely meet the delivery schedules.”
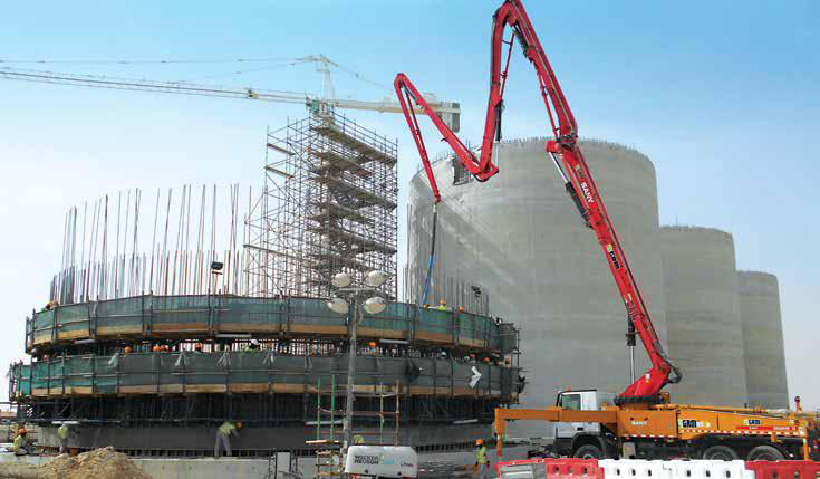
Raising critical structures the safe way
Banking on inherent strengths
L&T’s innovative formwork schemes always give us a safe edge especially when it comes to building complex structures like the anaerobic digesters, at the Jebel Ali Plant, that involved the construction of 22 m tall, 21 m dia tanks in confined spaces through an automatic climbing scaffolding system with three hanging platforms addressing different layers of work.
Elaborating on the scheme, Muralidharan, shares, “While the topmost platform catered to the reinforcement work, the middle focussed on continuous concreting and the bottom bench on finishing. This way, we achieved phase wise finishing by putting close to 150 workmen per shift and completing the entire activity in just about 5 days with utmost safety.” Likewise, doing the 3-level tertiary filter beds needed process innovation, highlights Noor, “It was too risky at the lower levels because of the confined space, so we used a thermocol block as a dead bed for the base slab to align the sequence of works as per the schedule.”
“For the construction of anaerobic digesters, we achieved phase wise finishing by putting close to 150 workmen per shift and completing the entire activity in just about 5 days with utmost safety.”
– K.A. Muralidharan
EHS In-charge – Jebel Ali STP
While executing Asia’s largest microfiltration plant at Raichur, our expertise to customize a suitable formwork scheme came in handy to build the settling tank, a 3-part structure partly below and partly above ground with the walls tapering from 550 mm to 200 mm at the top along with a counterfort at 4 m intervals. The chemical house was another structure that needed precision planning during construction as it comprised RCC chemical tanks inside the first floor which was taken up only after completing the entire structure and roof works. Special care was taken to insulate the floor and tank with acid resistant tiles as the UPVC pipeline carries the chemical up to the stilling chamber, CMB ETP and centrifuge.
The project team at Kharkai Barrage came up with a suitable scheme to construct the flared-out wall of 80 to 90 m length and height of 18.5 m, both upstream and downstream along both banks of the barrage due to the varying slope, ranging between 90 degrees at the beginning to 26 at the end. “As close to 30 percent of the total concrete work was in this section, a novel formwork scheme for hinging the structure from the inside was developed using reinforcements and only the working platform was provided from the outside,” mentions Dinesh Kharbhanda, Project Manager – Kharkai Barrage. For lifting the piers and abutment, a triangular shaped 1.5 m long climbing bracket system was used which was fixed to the bottom of the pier lift above which the lifting was done. The entire shuttering formwork was placed over this climbing bracket system and fastened from the inside using tie rods with supports provided from the outside. Adopting the bracket system prolonged the working season and mitigated the risk of flash floods during the pre-monsoon period.
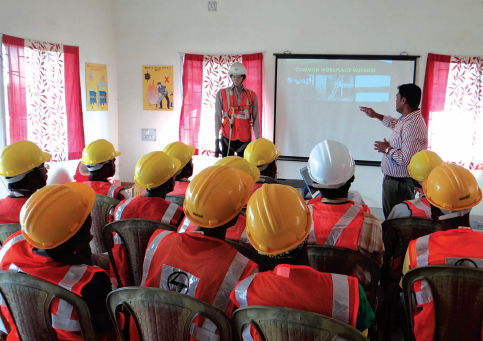
Training session for workmen
At the Pokaran-Falsoond-Balotra Siwana Lift Water Supply Project, a major portion of the scope comprised construction of civil structures that included 34 elevated service reservoirs ranging from 20 to 25 m in height with storage capacities of 100 KL to 1250 KL across remote locations on the top of 40 m high sand dunes. The team accessed the work spot by making approach ramps that facilitated safe movement of materials. Geo-technical investigations revealed that the soil had chloride content and hence had to be treated before taking up the civil works. The team implemented a secure staging process with fall arrestors and the task was monitored by an EHS official and subjected to timely inspections during phases of construction.
“We were spot on to ensure that safety and quality were stringently adhered to at site by having two construction managers assigned across both banks with another senior construction manager exclusively reviewing the entire activities through daily and weekly meetings with the on-field teams.”
– Dinesh Kharbhanda
Project Manager – Kharkai Barrage
Engineering secure methods around wet wickets
In the realm of water supply and lift irrigation projects, there are plenty of insights about how to safely raise critical structures. At the Upper Indravati Lift Canal project, EDRC stepped in to evolve a secure execution strategy to build the intake structure, highlights Project Manager, Udayagiri Srinivas. “The scope involved diverting the flow of running water through a tail race channel and constructing a 16 m deep coffer dam for the fore bay channel. Necessary silt protection measures were taken to prevent its entry as the design encompassed an open fore bay allowing water to be pumped directly to the suction chambers.” From the safety front, we had it all covered, says Sujit Panda, EHS In-charge. “Appropriate sloping and benching methods were worked out along with additional protection such as safety nets to contain the earth. Other support elements included hard barricading with colour coding, signage boards with safety messages while access to work spots was allowed only through authorized approvals backed with MS ladders supported by intermediate landing platforms for safe working.”
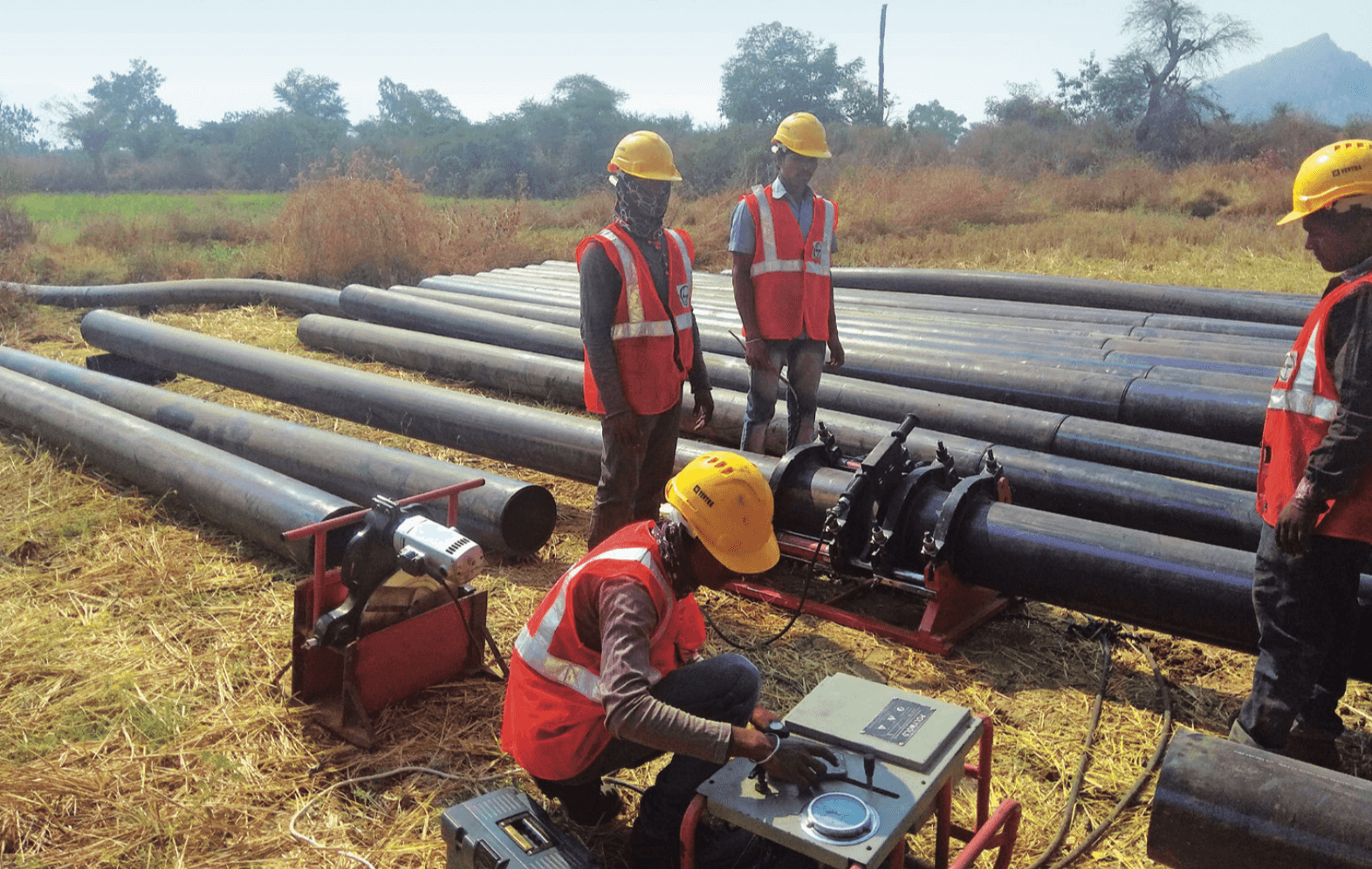
Testing the conduits
The Kharkhai Barrage and TWAD Vellore water supply projects are unique in that the risks were high as a large part of the core works was along perineal waters. One of the most critical tasks at the TWAD Vellore project was the construction of head and intake works on an island-like mass (600 m wide) surrounded by the waters of river Cauvery and the surplus water from Mettur dam within a mean shutdown period of 32 days which was critically monitored by the farmers. A secure work strategy was formulated with a conventional method of earth replacement for accessing the land mass to mitigate a water level of 8 m around the channel by progressively laying well-gravelled soil over the slush to prevent sinking and seepage. An economic design enabled the construction of the entire structure within a limited space of 8.6 acres with provisions for future enhancement. Since the intake well was adjacent to the water column, coffer dams were constructed to arrest the seepage of water during execution and as the depth of the well increased, the bund sizes were enhanced accordingly. Excavation was carried out by the progressive earth shifting method with multiple excavators simultaneously engaged at different levels. The entire substructure was raised adopting the sequential dewatering and concreting method. The raw water pumping main for conveying water from head works to the proposed treatment plant runs to about 100 m.
“Necessary silt protection measures were taken to prevent the entry of running water as the structural design encompassed an open fore bay allowing water to be pumped directly to the suction chambers.”
– Udayagiri Srinivas
Project Manager – Upper Indravati Lift Canal Project
Concreting formed the bulk of the works comprising close to 227,000, cu.m along with associated tasks such as 109,000 sq.m of shuttering and 5800 t of reinforcement at Kharkai Barrage. “This was not a plain pour forward task as we had only 8 to 9 months a year to work in the middle of a flowing river and our asking rate for concreting was more than 10,000 cum per month,” highlights Dinesh Kharbhanda. Keeping vigil and having the right men at strategic locations made work safer he assures, “We were spot on to ensure that safety and quality were stringently adhered to at site by having two construction managers assigned across both banks with another senior construction manager exclusively reviewing the entire activities through daily and weekly meetings with the on-field teams.”
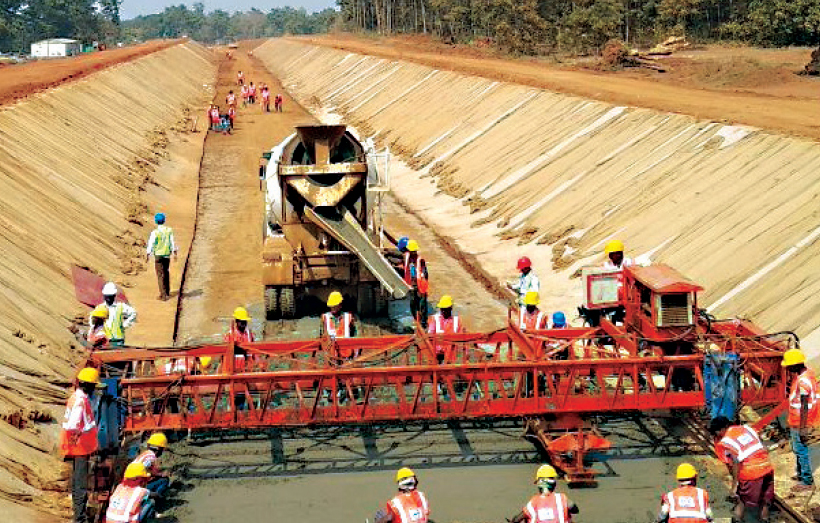
Building a water life line canal with secure sloping and benching methods
Integrating water lifelines with precision
Integrating water transmission mains is always a challenge of channelizing safe zones with the alignment that run across habitations, villages and cities. The risk factors associated in such tasks are directly related to the size of conduits and limitations along the route. At times, things can get further complicated when there are different services especially in a plant water system as was the case at Jebel Ali where the scope involved close to 120 km of pipe laying, 24 km of yard piping, 11.5 km of GRE piping, 6 km of fibre optic cables, 54 km of LV and MV cables, 2 km of HDPE, 21 km of street lighting along with CCTV cables and MEP services. Streamlining was the key, highlights Noor, “It was critical to finish the milestones synchronizing with the various services within the site. By recruiting a MEICA coordinator, we were able to merge all the different service drawings to mitigate the risks and clashes on the spot.” Today, Jebel Ali stands safely having clocked more than 10 million safe-manhours, a feat that Noor largely attributes to the ‘Lookahead Planning meetings’ that removed constraints and ensured safety across work fronts.
“Appropriate sloping and benching methods were worked out along with additional protection such as safety nets to contain the earth.”
– Sujit Panda
EHS In-charge – Upper Indravati Lift Canal Project
Zoning resources along strategic sections of the alignment is something that most WET projects have perfected according to site needs. In projects such as Adilabad and Nagaur-Bikaner Water Supply Schemes where the piping scope was close to 3000 km, a feasible and safe tactic was implemented. “We divided the span across 4 zones – Asifabad, Kaghaznagar, Bellampally and Utnoor – so that close to 2700 km of pipes were unloaded at strategic locations along the alignment. For certain tough terrain sections, a feasible round about routing was worked out taking into consideration the safety of the logistics,” mentions Planning Engineer, Kaushal.
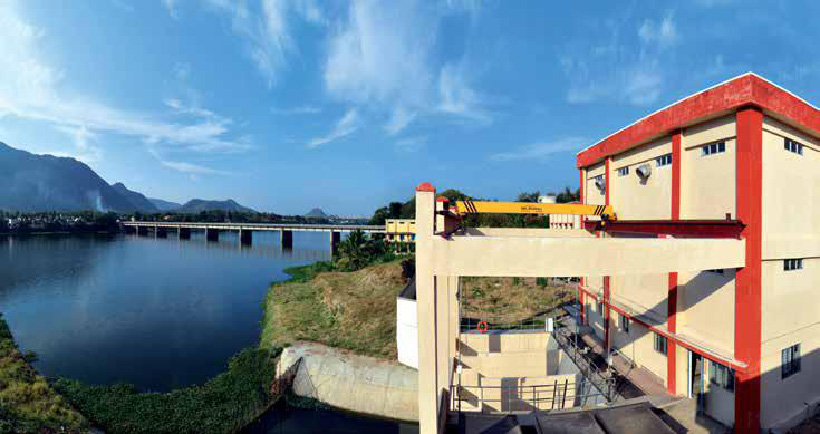
Head and intake works for TWAD Vellore
A major portion of L&T’s scope of work at the Sauni Yojana Link 3&4 comprised manufacturing and laying of 83801 RMT pipes of 3000 mm dia with each unit weighing close to 17 t with a plate thickness of 17.5 mm. To facilitate safe handling of the heavy pipes, the project team conducted a survey by coordinating with the local electricity department and strategized a secure mode of transport for the pipes on trailers by either increasing the height of the electrical conductors or by shifting the poles. To ensure that the special coating on the pipes remained intact, the team made a provision to unload the pipes onto sandbags to maintain both a minimum clearance from ground level and safe distances between the units to facilitate the lifting process.
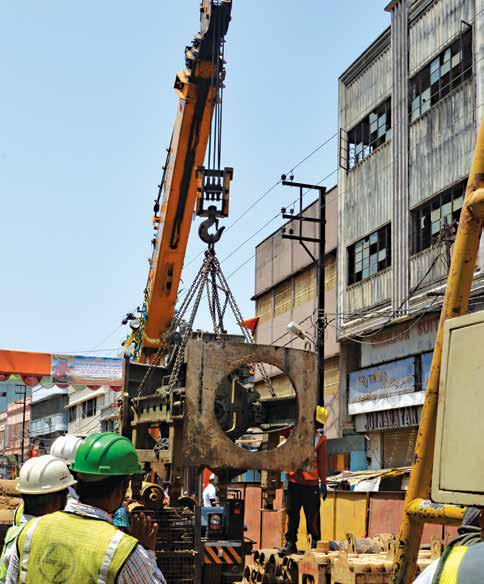
Precast duct installed at a sewage pipeline project
“For certain tough terrain sections, a feasible round about routing was worked out taking into consideration the safety of the logistics.”
– Kaushal
Planning Engineer – Adilabad and Nagaur-Bikaner, WSS Project
Putting together the water transmission main across 256 km for the NagaurBikaner Water Supply Scheme was tricky for Project Director, Shaik Yesdani Ahmed, and team. “Since we were dealing with close to 1,20,000 t of pipes in the scope, we chose a vendor who put up a plant that worked very well for it gave us a safe edge in costing, production and delivery.”
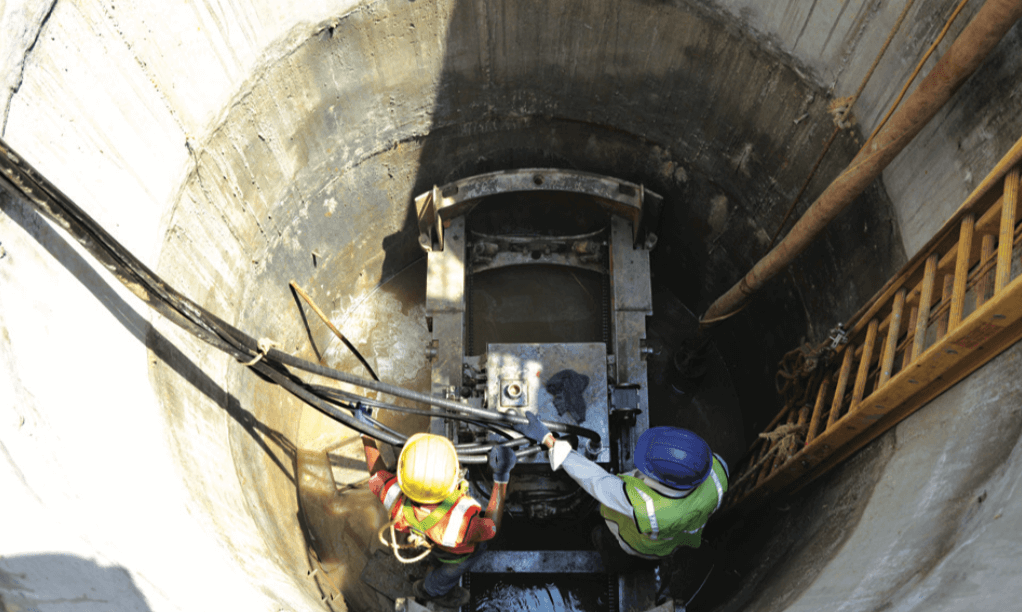
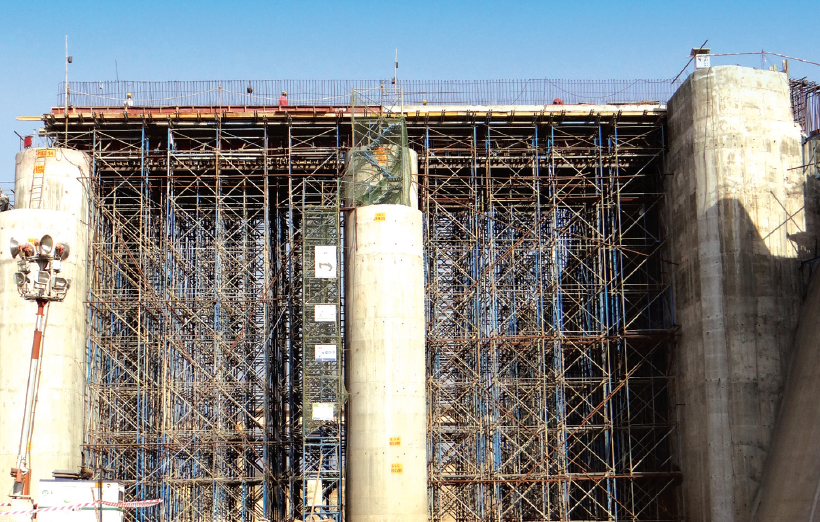
Scaffolding when building the Kharkai Barrage
Perfecting the art of trenching and cross overs
It’s never easy to make headway while laying pipes when the alignment runs across different zones. Safety is paramount both while breaking ground and making headway considering the dangers of unknown utilities. While modern digital tools like LiDAR has made life considerably easier, you still need to adopt a cautious approach.
While each site has its own risk mitigation measures there are a few significant projects like the Sauni Yojana lift irrigation scheme that saw some of the largest dia pipes handled across Asia where a range of measures were implemented that are now a benchmark in safe methods. To ensure hassle-free execution, the project team adhered to a maximum of 100 m long trenching activity wherein 8 pipes were laid in a single line. Welding of the pipe joints was a precision task for which the project team adopted an innovative method of creating a weld pit inside the pipe trench for the jointing works carried out by skilled welders using the Shielded Metal Arc Welding (SMAW) process.
“Since we were dealing with close to 1,20,000 t of pipes in the scope, we chose a vendor who put up a plant that worked very well for it gave us a safe edge in costing, production and delivery.”
– Shaik Yesdani Ahmed
Project Director – Nagaur-Bikaner WSS
There were, in addition, a slew of critical cross overs with more than 120 high tension electrical lines crossing the alignment which called for utmost care while handling the pipes during excavation, blasting and particularly when operating cranes. The entire works were completed successfully by adhering to the highest safety standards by implementing SOPs such as lowering the ground profile which facilitated gradual excavation, adjusting the position of the crane and ensuring timely shutdowns.
A major crossover successfully negotiated by the team was across 10 m under an existing crude oil pipeline. Mock-ups were made to illustrate the possible hazards which enabled the workforce to master the precise procedures to be adopted. The project team made cautious headway manually excavating, as blasting was prohibited, around 200 m as per the safety guidelines, but always maintaining a 1 m clearance from the crude oil line throughout the trenching activity. The process involved 7400 cu.m of hard rock excavation: 85% of the strata using rock breakers and manual excavation of 400 cu.m using electric rock breakers. A MS casing pipe of 3.4 m ID was installed to ‘push’ and lay the pipes at the rate of 2.5 m per week. To make the system fool proof, the rising main was encased for 25 m on each side of the crossing with concrete and equipped with turbulence measurement sensors that assessed the water current vibration and automatically triggered alert messages to the oil and water.
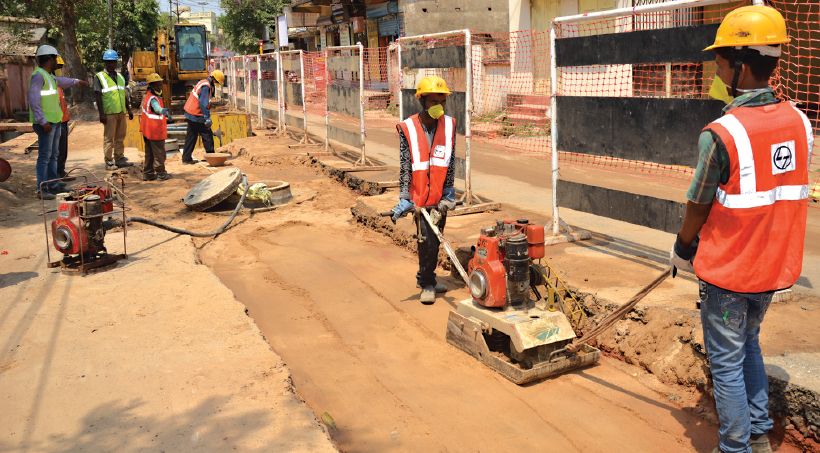
Road restoration work
Ensuring safe promises continue
The WET IC teams remain connected with their projects even after commissioning as most water infrastructure schemes have an operations and maintenance phase. It is then up to the O&M Department to continue the good work with appropriate hands-on training to the clients’ teams as the onus with water projects is always about how safely water is delivered to the public at large.