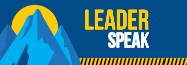
M V SATISH
Whole Time Director & Senior Executive Vice President
(Buildings, Minerals & Metals)
At B&F, we have driven operational efficiency through value engineering and adopting best practises to avoid rework, reduce repetitive work as well as cost for improved productivity. The advent and widespread adoption of precast engineering has brought with it several advantages including speedier execution, better standardization, reduced dependency on in-situ construction and better quality. The stadiums at both Al Rayyan and Motera are classic examples. Industrial prefabricated construction technology ensures 30-40% reduction in construction time and 10-15% reduction in cost apart from improving the workmen productivity in a factory environment by 40-50%.
A lot of our construction takes place at heights on high rises and to improve our efficiency at heights, we indigenously developed and implemented the Gallow ACS system, for the first time in the history of Indian construction, at the ICC Towers Project, Mumbai. This helped to optimise resource requirement and achieve a continuous cycle time of just 6 days. The use of travelling slab formwork for electrical trenching at Prestige Smart City, Bengaluru and aluminium slab formwork for the non-tower areas at Prestige Jindal City project, Bengaluru have both significantly reduced cycle time.
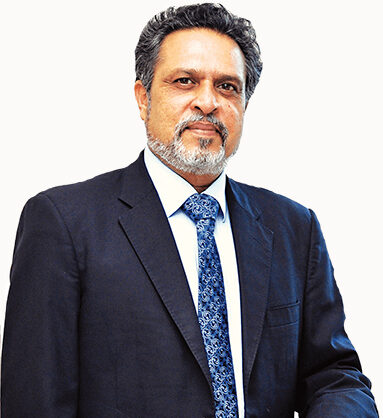
Digitalization has aided our journey to achieve operational efficiency. Our new P&M Central Monitoring Cell has facilitated the use of IoT for P&M strategic assets that drives P&M Life Cycle management by continuously tracking and analysing the data derived to improve overall P&M performance that has already accrued some handsome savings. Steps have also been initiated to reduce material wastages at site. While digital concrete requisition and engineer wise pour cards have reduced concrete wastage, a BBS automation tool to reduce and optimise offcuts have reduced rebar wastages.
Due importance has been given to improve workmen productivity at project sites. Continuous monitoring of the workmen biometry along with digital applications like WISA & Procube now track workmen availability at project locations and thereby improve their productivity.
Having said all that, operational efficiency is a continuous process and sky is the limit!
The MANY FACES OF OPERATIONAL EFFICIENCY AT B&F
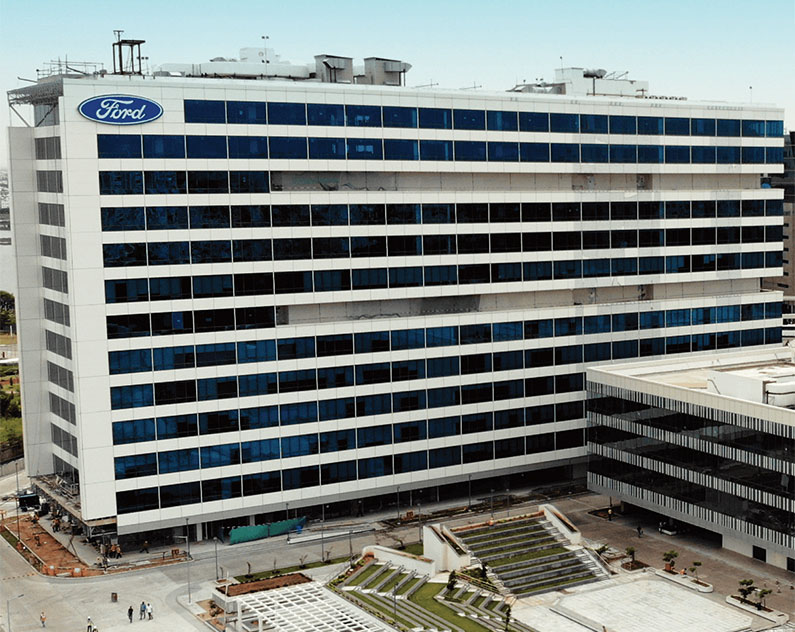
The unpredictability that is infrastructure projects was felt keenly by B&F’s Al Rayyan project team when an adverse socio-political scenario forced them to alter operating procedures without the luxury of changing either the requirements or delivery schedules. “We had to immediately go into action-mode and literally push boundaries to quickly evolve alternate procurement strategies to source material from friendly countries that in many cases were new markets for us,” shares Vijay Venkatesh, Head – Quality & EHS. “All our processes had to be requirements and to ensure that our product specs were maintained. We introduced micro quality checks to achieve zero rejections and we succeeded!” His sense of triumph is obvious. Although this was a situation created by factors beyond their control, other B&F project teams across other geographies, are striving to improve productivity despite challenges to remain profitable.
Precasting success
Like Al Rayyan, the Motera stadium, in Ahmedabad, that was recently in the news filled to the rafters for the ‘Namaste Trump’ event and already the world’s largest cricket stadium, is another example of speedy execution using precast technology that has standardized delivery, enhanced quality, maintained aesthetics, improved safety and, in the process, achieved a high degree of operational efficiency.
“We had to immediately go into action-mode and literally push boundaries to quickly evolve alternate procurement strategies to source material from friendly countries that in many cases were new markets for us. All our processes had to be remodelled to suit these fresh requirements and to ensure that our product specs were maintained. We introduced micro quality checks to achieve zero rejections and we succeeded!”
Vijay Venkatesh
Head – Quality & EHS, Al Rayyan Stadium
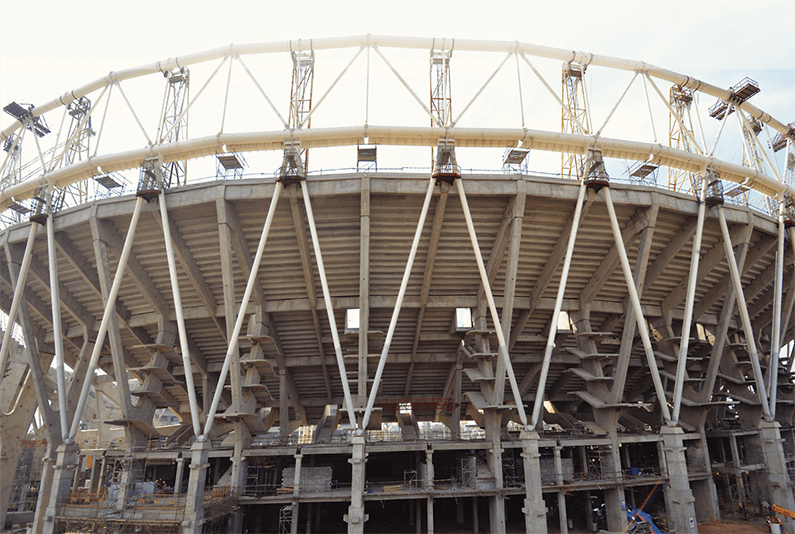
GY and HY precast columns erected at Motera Stadium
The task of erecting the huge GY and HY columns with as many as 178 structural connections, was giving the Motera team sleepless days and nights with the added threat of a knock-on effect on the project’s costs and delivery. Thinking out-ofthe oval, as it were, Project Director, Subrata Dutta (SD) and his team evolved an engineering solution to erect these columns as single elements with special lifting arrangements. “Each of the HY columns was 36 m in height i.e. approximately as tall as a 12-storied building, 15 m wide, a metre in depth, weighing in excess of 250 tonnes,” shares SD, “and these had to be first precast in steel moulds, then transported from the yard to site on self-propelled modular trailers with 3 sets of hydraulic axles, with a combined capacity of 400 MT.” During transportation, turn table arrangements were used to negotiate sharp turns in Bolster mode. The team chose a main lifting point that was just 2 feet above the centre of gravity and the special lifting arrangement included lifting clamps with a trunnion arrangement and a ‘C’ link. The expertise of N Srinivasan – Head Special Projects and his team was crucial in planning and executing the entire activity. “We were able to significantly reduce overall cycle time,” smiles a satisfied SD through his trim goatee, “the GY column by 5 days that is about 42% and the HY column by 7 days or 38% and since we cast these huge columns in one piece we were saved the bother of several multiple tough lifts,” he adds. There were more benefits that accrued to the team – reduced dependency on manpower, improved safe working conditions and a positive impact on cost, time and quality.
“We were able to significantly reduce overall cycle time of the GY column by 5 days that is about 42% and the HY column by 7 days or 38% and since we cast these huge columns in one piece we were saved the bother of several multiple tough lifts.”
Subrata Dutta
Project Director
Elsewhere, 3 m wide and 2 m deep drains at the HST NATRAX project, drains, drain covers and manholes at both NATRAX and New Delhi’s India International Convention & Expo Centre (IICC) project sites and bleachers for seating areas at IICC are all quickly and aesthetically taking shape thanks to precast technology.
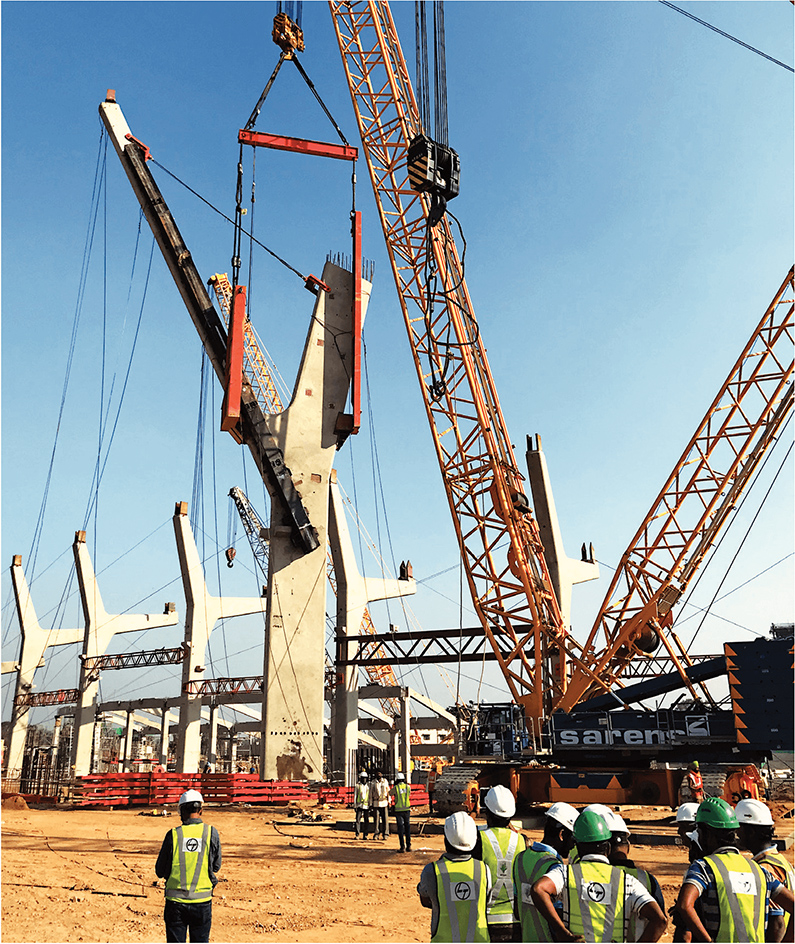
Precast wall panels for MEP shafts: The usual practice is to construct a brick/block wall after installing the MEP services inside the shaft that usually take about 55 days in total for wall construction, curing, plastering, another round of curing, drying and painting. This does not allow plaster and paint for the internal surface as there is no space to work. M Balasubramanian (Bala), Head – Quality, B&F shares that at the ITC Colombo site, the execution team used precast wall panels that were given a coat of paint prior to installation. “Once the MEP services were installed and the green signal was given for civil works, the team got cracking and completed the entire process in 12 days flat! If there is an example of improving operational efficiency, this is it!” says Bala with a thumbs up.
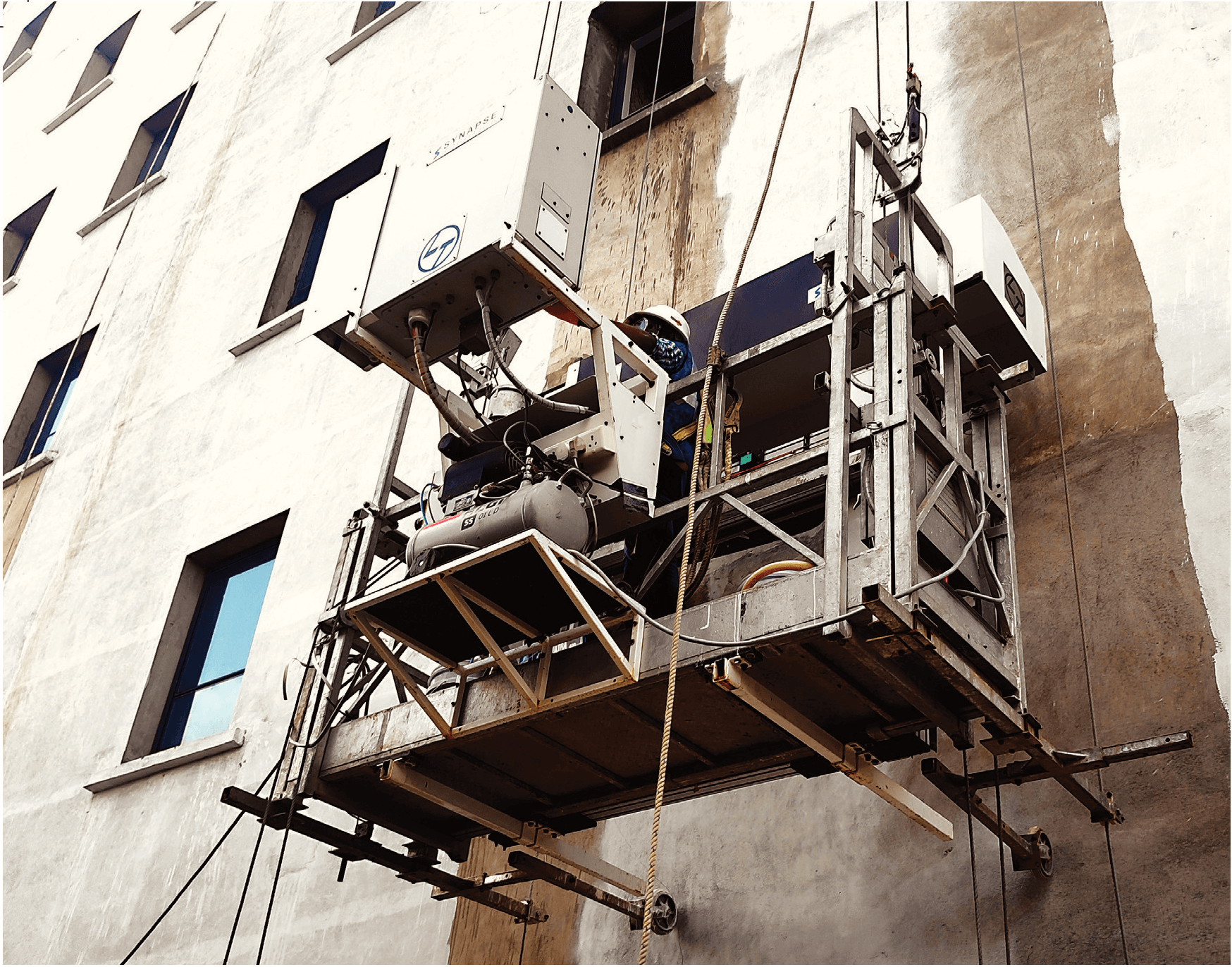
External wall robotic painting
Painting robotically
Efficiency in painting has risen several notches with the introduction of Robotic Painting, a revolutionary new painting technology as the S Vadivazhagan, Project Manager of Commerzone Raheja, in Chennai has found out to his delight. “Painting has suddenly become a far more controlled activity,” he shares enthusiastically, “the robot precisely identifies the area to be painted, almost totally eliminates wastage and rework, and at the end of the day, our efficiency improves multi-fold.”
Digitally tracking aluminium formwork
Perhaps for the first time in L&T Construction, the CMPC Team of B&F’s Residential Business Unit set out to find a digital solution to track aluminium formwork by eliminating human intervention as scheme preparation and data management were turning out to be far too time-consuming. The developed app helps to identify the usage pattern of panels thereby bringing in traceability and accountability at sites. It is now possible to record the physical stock available, the number of repetitions and the age of panels. The initiative is already ‘live’ across 17 project sites since August 2018.
Improving efficiency at heights
As B&F’s reputation of constructing high-rise towers grows and projects increase, project teams are constantly seeking construction methods to enhance productivity when working at heights. The Rebar Reinforcement Cage is one such that is helping their cause and a host of projects like DLF Crest, IKEA, DMIACC, CAPFIMS and Ford among others will vouch for it. “The advantages from rebar cages are manifold,” shares Bala. “Enhanced construction sequence, improved manpower productivity, significantly reduced overall cycle time of achieving concrete works per floor and, most importantly, improved quality.”
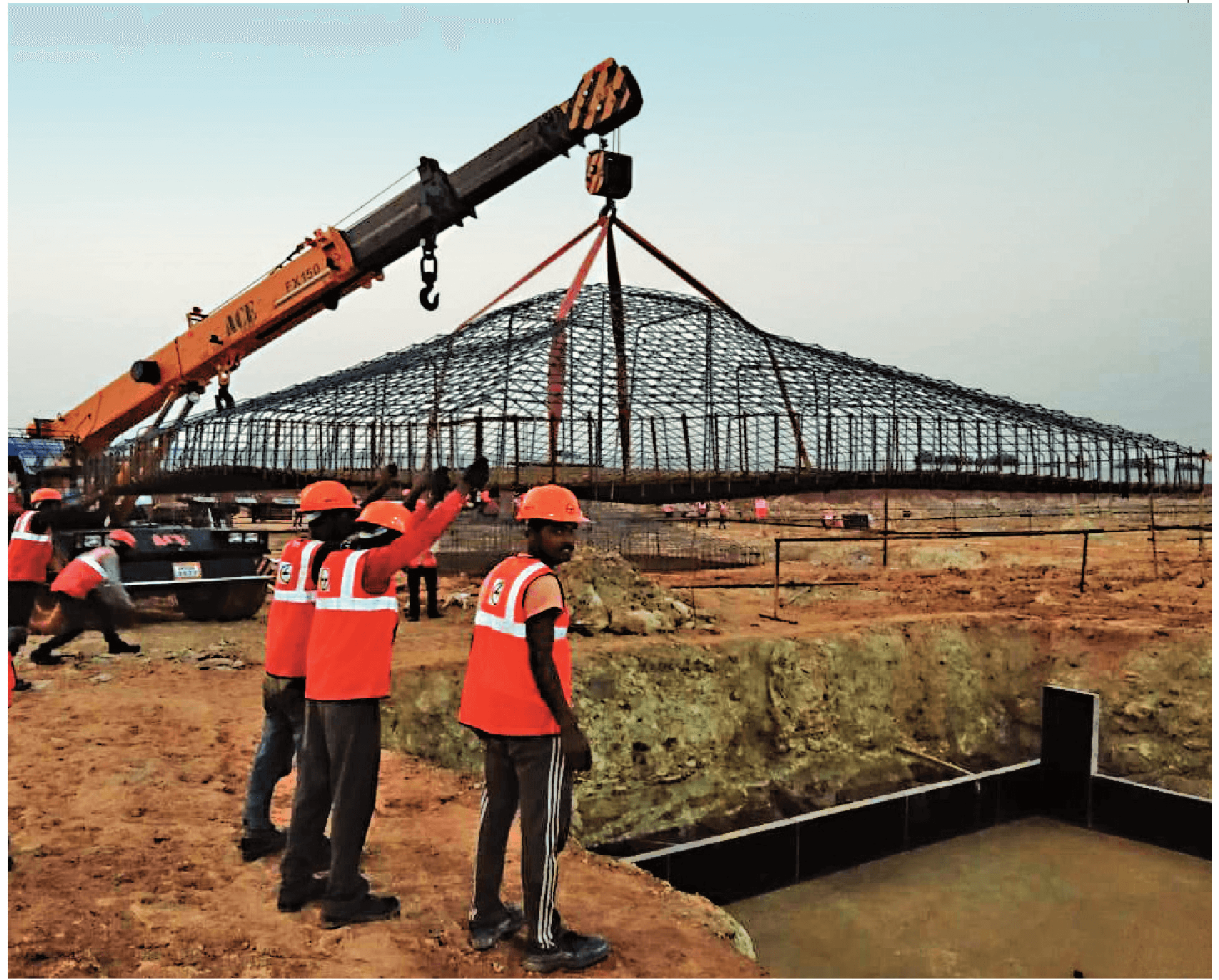
Rebar Reinforcement Cage
“Painting has suddenly become a far more controlled activity. The robot precisely identifies the area to be painted, almost totally eliminates wastage and rework, and at the end of the day, our efficiency improves multi-fold.”
S Vadivazhagan
Project Manager of Commerzone Raheja
Reinforcement cages are prefabricated virtually like columns at site except that the stirrups are not tied at the lapping zone and since they are prefabricated, it reduces the need to issue separate material like straight bars, rings and stirrups onto the working platform that in turn reduces housekeeping headaches. “These cages provide an excellent guide system to accurately place concrete,” says Santosh Kumar Shukla, Senior Construction Manager (QA/QC), DLF Crest project, “they are economical to use and have fewer labour requirements thereby positively impacting our project costs.”
C Prasad, Head – Formwork Competence Cell, B&F IC shares about the innovative Gallow ACS system implemented perhaps for the first time in the history of Indian construction at the ICC Towers project in Mumbai. “The am was to optimise resource requirement and improve cycle time by creating a safe zone of working for the workmen at heights,” he says and adds with a winning smile, “we have executed the project without a single incident.” Prasad and team have also successfully worked at heights of up to 260 m with the Safety Screen system that was introduced to protect perimeters with an automatic climbing system that improved both labour productivity as workmen felt safe even at great heights.
“Fly Table System helped us achieve a cycle time of 15 days from floor to floor of 5.5 m or above, has reduced our dependency on labour, reduced our rate of shuttering and importantly increased our productivity from 2 sqm/md to a minimum of 8 sqm/md.”
Jaydeep Sengupta
Project Manager – Ranchi Convention Centre
The efficiency of the Fly Table system
Project teams at BIAL and IKEA are singing praises of the simple but clever Fly Table system that has, according to Project Manager Jaydeep Sengupta, at the Ranchi Convention Centre project, helped us achieve a cycle time of 15 days from floor to floor of 5.5 m or above, has reduced our dependency on labour, reduced our rate of shuttering and importantly increased our productivity from 2 sqm/md to a minimum of 8 sqm/md.”
Prasad informs that the Large Area Table formwork system is used the world over for the flat slab format, “whereas in India we use the slab & beam combination in structural design, so we successfully modified the LAT system to suit our specific requirements and it has been hugely successful.”
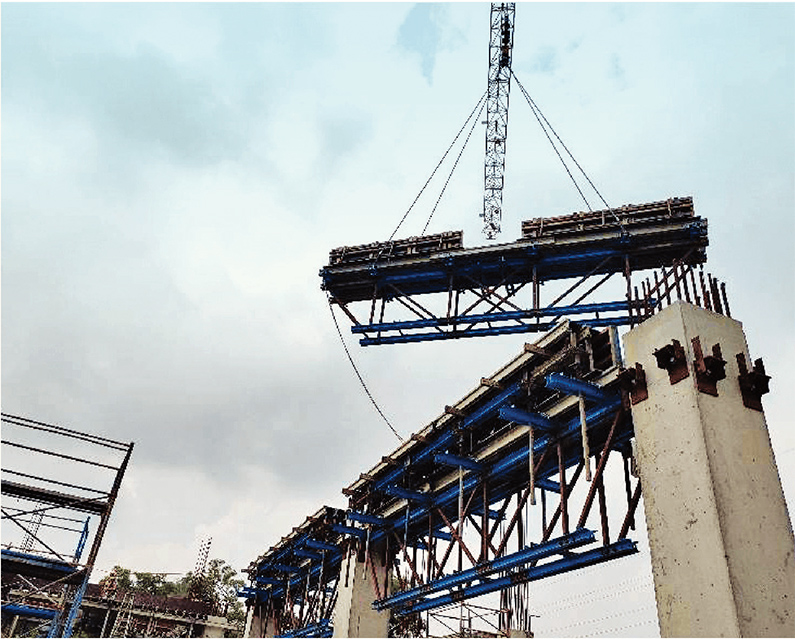
Fly table erection
“The advantages from rebar cages are manifold. Enhanced construction sequence, improved manpower productivity, significantly reduced overall cycle time of achieving concrete works per floor and, most importantly, improved quality.”
M Balasubramanian
Head – Quality, B&F
Towards more efficient P&M Life Cycle management
J Raveendran (JR), Head – P&M, (CB&A), B&F IC has been busy setting up the P&M Central Monitoring Cell (CMC) to drive P&M Life Cycle management by, as he shares, “ensuring 100% digital implementation, continuously tracking data derived from IoT and analysing it to improve overall P&M performance. All the involved stakeholders connect every week to crunch the data to optimise performance and this initiative has already yielded us cost savings to the tune of INR 10 Crores by improving P&M productivity at sites, demobilizing hired equipment, reducing fuel and energy consumption.” A satisfied JR adds, “during FY 19-20, the team has safely and successfully executed 1400+ critical activities.”
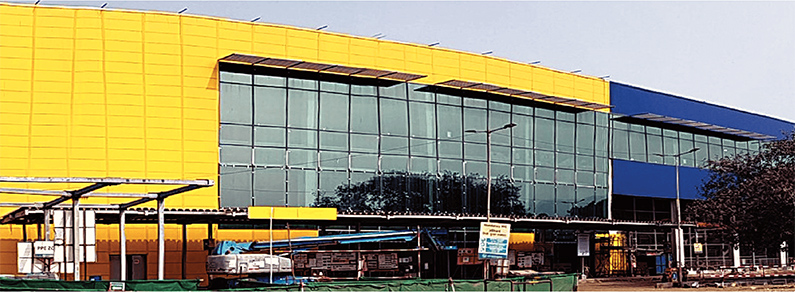
IKEA Retail Store Project, Mumbai
A bouquet of other initiatives driving productivity
Speedier connect through mmGPS systems: At the NATRAX project, mmGPS systems have increased the alignment between project site teams and the client across layers where previously the client had to check approximately 1,75,000 points. Now, through the mmGPS system, at least 5,000 points can be crosschecked by both the site team and the client in a single day that translates into huge saving of time and costs! Traditionally, this exercise would have taken at least five total stations and 5 auto level teams to complete revealing the efficiency of the system that has, at the same time, eliminated the possibility of human error during execution.
Introducing efficiency to formwork material: Formwork plays a key role at the IIT, Hyderabad project as most of the buildings have an Exposed Concrete Surface finish. After a detailed study, the project team identified the most optimal use of formwork material with maximum possible repetitions. Formwork movement was also effectively planned as per the building handing over dates. By using prefabricated or pre-erected scaffolds for columns, the team impressively saved on time, involved less labor, saved on costs and a Cup-lock system used for slabs proved faster and more productive than the conventional HD/flex systems.
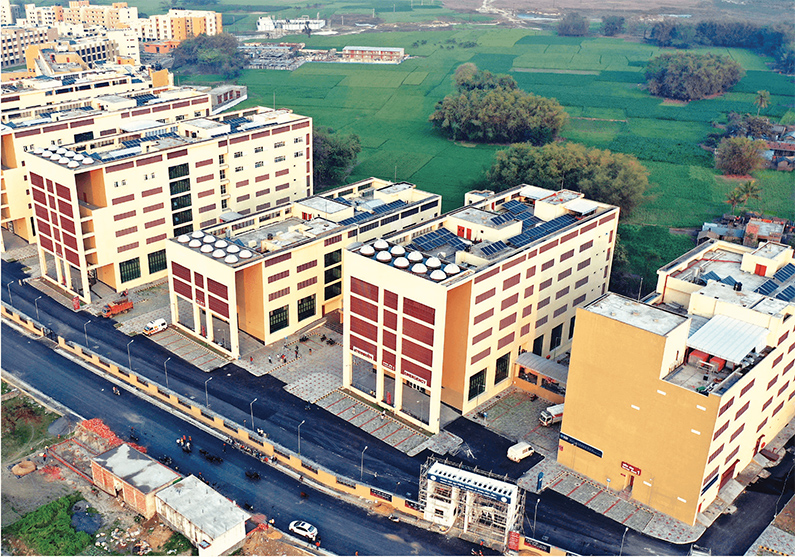
Government Medical College, Madhepur
Reducing bulk material waste: IIT Hyderabad was selected as a pilot project to implement Bulk Material
Wastage (BMW) optimization by introducing the Real Cut 1D, a steel optimizer software, that automatically
generates optimum cutting plans by ensuring the inventory of offcuts to be used and updating the inventory before running a fresh cutting plan. “As part of this initiative, a user form was shared along with the pour card that automatically calculates wastage according to the mode of concreting,” shares Project Manager H.S.P. Shukla. The software gives the site engineer the option to choose the quantity against the theoretical quantity of his/her pour. “Although, the analysis is still manual, the reduction in wastage has been very significant,” Shukla shares with a thumbs up.
“Value engineering is nothing but analyzing your construction methods to find new, better and more efficient ways to build. I am delighted that a number of teams have successfully introduced so many efficiency enhancing initiatives but there is still a long way and I urge all to continue this process, to keep thinking out of the box because ultimately all these will work best for our wonderful organization.”
M V Satish
Whole Time Director & Senior
Executive Vice President
(Buildings, Minerals & Metals)
Use of Plywood Arrangement Scheme Drawings: is an initiative by the Government Medical College & Hospital Project team in Madhepura, Bihar to use a plywood arrangement scheme drawing for the plywood used for slab shuttering. It involves placing the plywood as per the arrangement used in the previous slab to avoid cutting plywood pieces, increasing the repetition of plywood, reducing scrap and thereby saving plywood cost. This practice is recommended for all sites to dramatically reduce the cost of plywood.
Use of shuttering oil sprayer: Instead of the conventional method of applying shuttering oil on the plywood surface with a waste cloth or paint brush, the project team at the Government Medical College & Hospital project introduced a shuttering oil sprayer. The area of coverage has increased dramatically from around 8-10 SqM / litre to a whooping 40-45 SqM / Litre.
“Value engineering is nothing but analyzing your construction methods to find new, better and more efficient ways to build,” shares M V Satish, Whole Time Director & Senior Executive Vice President (Buildings, Minerals & Metals) and Head B&F IC. “I am delighted that a number of teams have successfully introduced so many efficiency enhancing initiatives but there is still a long way and I urge all to continue this process, to keep thinking out of the box because ultimately all these will work best for our wonderful organization,” he concludes with a positive air.
SOUTH ASIA’S LARGEST,
2000 MT SKY BRIDGE LIFTED TO 95M
at ITC One Colombo Project
Colombo’s Galle beach skyline was transformed on 15th December 2019, when a spectacular sky bridge ‘Ahasa One’ (‘Sky’ in Sinhalese), weighing 2000 MT, measuring 55 m longtitudinally and features a restaurant and a jazz bar with two infinity pools on the top overlooking the Indian Ocean one side and Beira Lake, on the other and is the high point of colombo’s Galle beach face where the President of Sri Lanka hoists the National flag every year on the Independence Day.
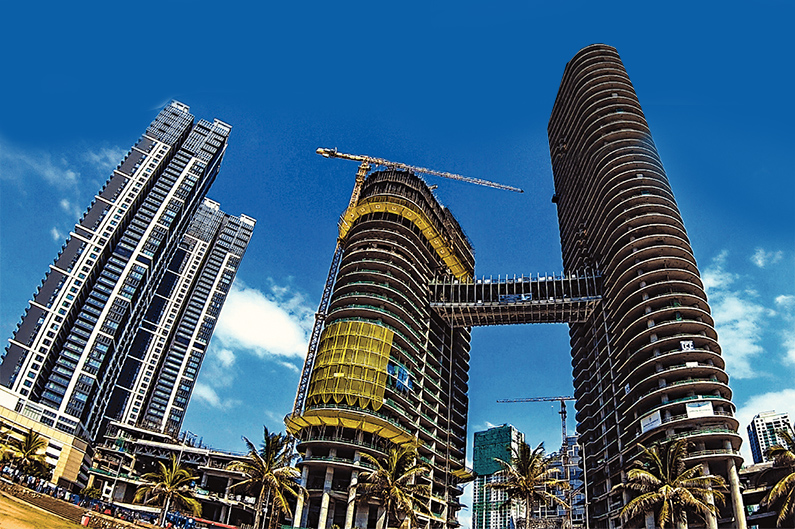
Enabling constructability with value engineering
Tracing the making of this milestone, Kasiraja, General Manager, Special Projects & Construction Methods (SPCM), highlights, “Considering the span, the ITC Project and SPCM teams worked out a phased fabrication schedule starting from October 2018 at L&T’s LTEW Workshop in Kancheepuram. The connection of the main spine, which was proposed as a welded connection, was converted to an 100% bolted one for easy assembly and dismantling during load test and final assembly at project site.” A modular production scheme was lined up to fabricate the steel elements considering the transportable size from Kanchipuram to Colombo and the assembly crane available at Sri Lanka.
“The fabrication involved critical welding of plates and sections up to a thickness of 150 mm in a restrained environment,” shares P. Dinesh Kumar Head – LTEW- Kancheepuram Works. “We ensured that all the components including the splice plates were properly tagged during despatch for ease of erection at site.” A total of 17,800 fasteners was used to connect about 1300 components. Top-notch fabrication at LTEW ensured seamless integration of the elements with the joints and quick assembly at project site, “as we couldn’t afford the risk of even a minor misfit,” adds Dinesh.
“Considering the span, the ITC Project and SPCM teams worked out a phased fabrication schedule starting from October 2018 at L&T’s LTEW Workshop in Kancheepuram. The connection of the main spine, which was proposed as a welded connection, was converted to an 100% bolted one for easy assembly and dismantling during load test and final assembly at project site.”
Kasiraja
General Manager, Special Projects & Construction Methods (SPCM)
Guaranteeing the performance of the Skybridge
A load test of this magnitude and scale had never been attempted at L&T and with seemingly no other alternative, the challenge for Kasiraja and team were to try and accomplish the impossible. “An innovative load test method was developed by the SPCM team to support the 3000 MT bridge at two ends with the available loading facilities at Kancheepuram – two 50 MT gantry cranes, without any heavy lift cranes,” he explains. “We opted for a secure ground level test in line with the overall requirement of 3000 MT to ascertain the amount of deflection without any lifting system.” The load spread for 1500 MT on each supporting end was distributed by placing the available steel mats on top of the shop floor of the fabrication yard, which had a SBC of 20 MT per sqm. After a successful load test, the bridge elements were dismantled and transported to Colombo by ship with the maximum weight of a single element being 100 MT.
“The fabrication involved critical welding of plates and sections up to a thickness of 150 mm in a restrained environment. We ensured that all the components including the splice plates were properly tagged during despatch for ease of erection at site.”
P. Dinesh Kumar
Head – LTEW – Kancheepuram Works
Piecing together the elements
On site, the components of the skybridge were preassembled at ground level in an open space in front of the podium building, some 40 m from the final lift-off location. Effortless movement of the skybridge spine assembly was possible by deploying an indigenously developed skidding system taking advantage of a low coefficient of friction between the stainless steel and the Tefloncoated launch pads. Automated remote-controlled push pull jacks were used for this movement. On reaching the final lift-off position, the spine assembly was hooked-up to the strand jacks and subsequently, the skybridge attachments were loaded in five stages with the skybridge hanging from the strand jacks all the time. The strand jacks were supported by a temporary RCC deep wall between the 24th and 25th floors simulating the final structural support requirements between the 20th and 21st floors, that resulted in substantial savings in the cost of structural steel. A thorough survey was also conducted to decide the positioning of the jacks as the operating space for the jacks to raise the bridge between the towers on either side was only about 50 mm.
“From the initial 750 MT, the weight of the sky bridge increased in phases, reaching its maximum load of 2000 MT with the addition of elements such as the concrete of three floors, facades, bearings, resting brackets ACP & BMU.”
N. Srinivasan
VP & Head – P&M and SPCM
Raising the bar
Heavy lifts are always critical, exclaims N. Srinivasan, VP & Head -P&M and SPCM and when it is dynamic as in this case, it is all the more complex, “From the initial 750 MT, the weight of the sky bridge increased in phases, reaching its maximum load of 2000 MT with the addition of elements such as the concrete of three floors, facades, bearings, resting brackets ACP & BMU.”
Sunday. 5.20 am. Even before the sun had risen, the lifting process commenced after a traditional pooja and reached its final position at 1:25 pm, smoothly and safely negotiating 95 m in approximately 8 hours. The fully dressed sky bridge module was lifted using 8 strand jacks, each with a capacity of 300 MT, mounted at the 25th floor level and operated in a synchronized manner. The whole process that was digitally controlled using a customized Smart Computer Control System, was carefully planned and executed as the sky bridge structure was not symmetrical and curved on all three axis, and precise alignment of strand jacks position was critical for the lift to succeed.
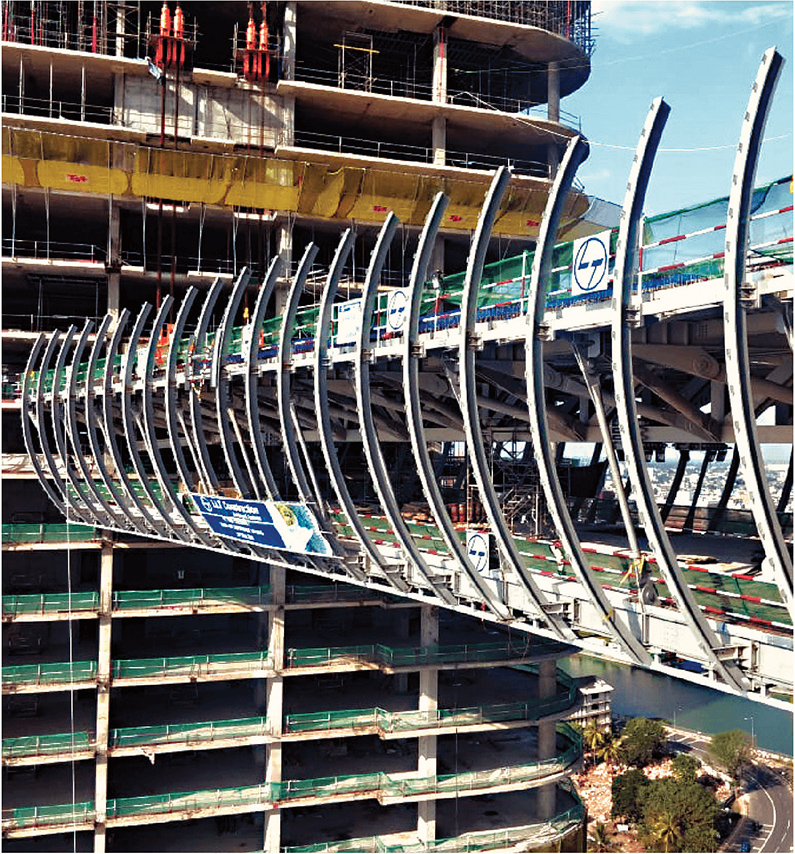
A triumph of collaboration
“In every challenge, the team work among the various stake holders beyond their roles made all the difference. For the first time the client openly appreciated the efforts by LTSP,” says Natarajan Namachivayam, Project Director.
Sri Lanka’s entire engineering fraternity were present at the grand heavy lift event. The clients and consultants were unequivocal in their praise for L&T’s innovative first-of-its-kind method that was the project’s 5th critical milestone. There are two more remaining. For team L&T, it was a triumph of collaboration, a feat executed entirelyin-house, involving the B&F IC’s project team, EDRC, L&T Engineering Works, Kanchipuram and L&T Special Projects & Construction Methods department of Divisional Corporate.
“Team work among the various stake holders beyond their roles made all the difference. For the first time the client openly appreciated the efforts by LTSP.”
Natarajan Namachivayam
Project Director
MASSIVE ROOF STRUCTURE ERECTED
at Hyderabad International Airport Project
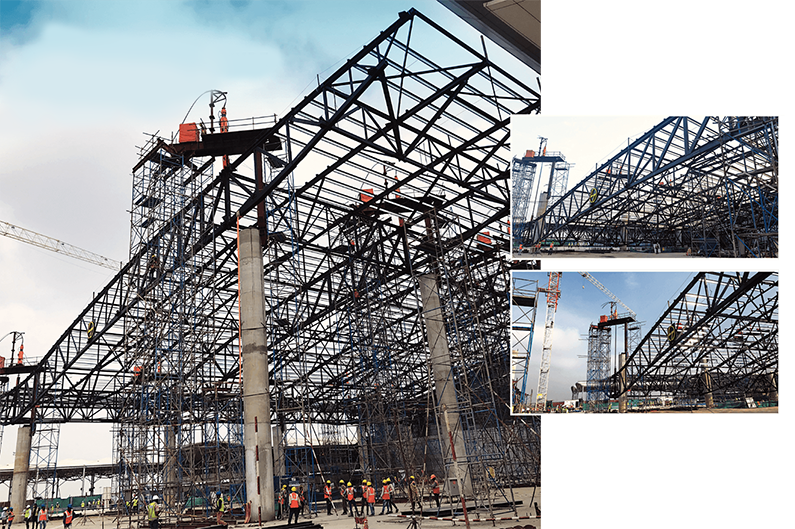
A massive roof trust spanning 70×77 m (equivalent to the size of a football ground) and weighing 450 t was erected at the Hyderabad International Airport through a strand jack system on 6th Jan 2020. Being a brown field project, this remarkable achievement was engineered by the Special Projects & Construction Methods Department of Divisional Corporate along with the HIAL project team.
The lifting system comprised ten 185 t strand jacks mounted on portals supported by Doka towers on one side and a permanent column on the other. The consumption of enabling steel was kept to the bare minimum and reusable for subsequent roof modules at HIAL.
The roof module was lifted above the 17 m tall column from the assembly level and skidded 1500 mm diagonally to reach the final installation position. Hollow hydraulic jacks with mac-alloy bars were used for horizontal skidding.