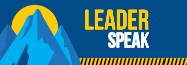
R Srinivasan,
Executive Vice President & Head (Smart World & Communications)
Digitalisation is an important tool to achieve our goal of zero incident and safe environment. Amongst the main advantages, three things stand out: i) With our constantly expanding workforce and resources, it is extremely important to bring the new entrants and trainees to the level of safety being practiced at the company level and meet L&T benchmarks and digitalization that provide the answer through standardisation of processes. ii) Any near miss or potential hazard cases at any site and learnings thereof must be transmitted to all the sites instantly so that the entire operation is in sync. & iii) With live monitoring, emergency responses and expert advice as and when required, quick turnaround is possible. Digital tools like VR, AR and AI are already providing us with additional ammunition for us to achieve our goal of zero incident.
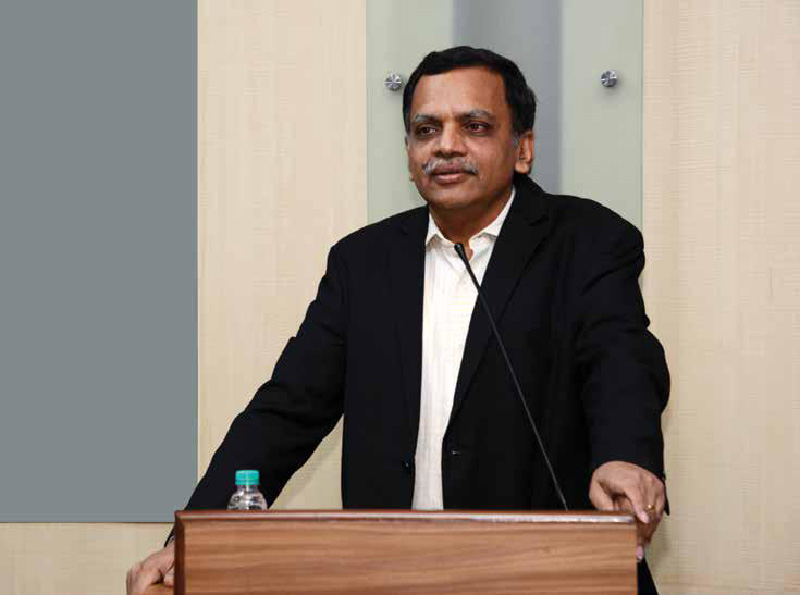
BUILDING INFRASTRUCTURE IN THE HEARTS OF CITIES
Understanding the hazards of constructing in congested cities
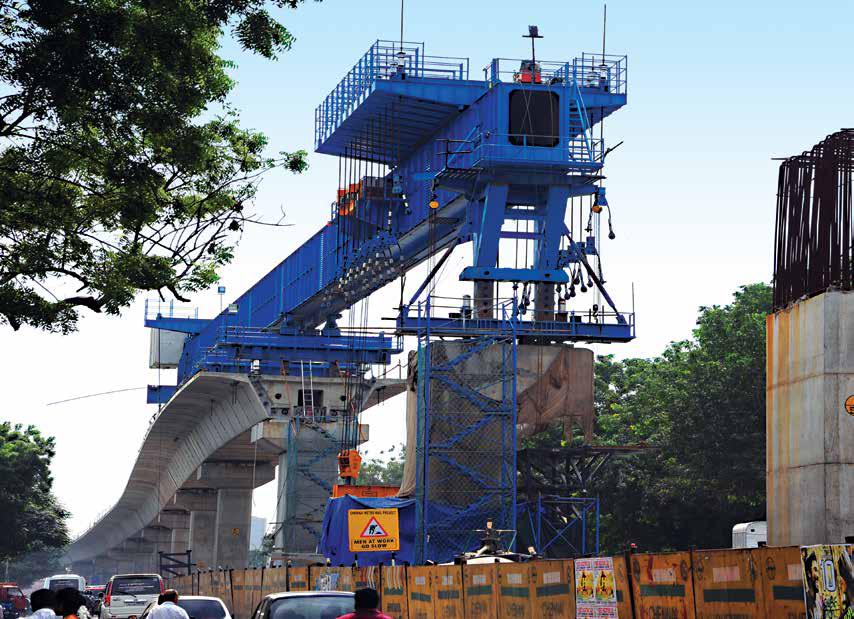
Girder erection across a busy junction
P R Kumar, Cluster Head, Smart World & Communications (SW&C) business unit has a lot to share about his project team’s difficulties to execute India’s largest surveillance network in Mumbai city. “There were challenges for us both above the ground and below,” recalls Kumar, with his usual vigour. “Over ground, we had to avoid high-density traffic areas but then the whole of Mumbai is one big high-density traffic area,” he laughs. “Space constraints in pedestrian areas was another headache and then there were power lines, dish cables, even clothes lines. Once we started to dig, we had to be extra careful not to damage any of the utilities lines running underground but that was only after we had received the necessary clearances and approvals from the Municipality and other local authorities.”
Almost all IC and BU teams building urban infrastructure within the narrow confines of congested cities face similar challenges as Kumar be it constructing a high-rise residential tower or a sewerage network; a metro rail system or a deep basement car park. The two phases of the Lucknow Metro, for example, constructed by teams from the Heavy Civil Infrastructure IC and Railway SBG of Transportation Infrastructure IC are arguably the fastest built metro systems in India! One can well imagine their stress to build so fast, yet maintaining high standards of quality and safety and this article is about how Project and EHS Heads achieve this tall order.
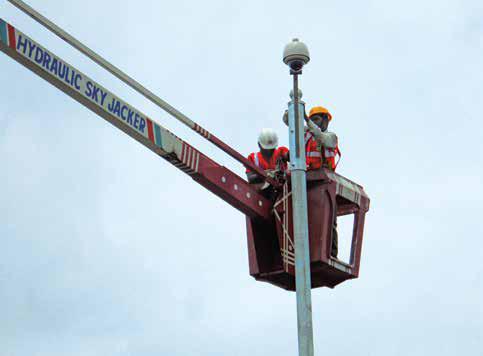
Workmen fixing a surveillance camera
Look before you leap
Before they begin excavations, construction teams must first ascertain what lies beneath. Very few cities have well chartered and documented evidence of public utilities and therefore as K S Sudheesh Kumar, Head – EHS, WET IC shares, “It is a discovery process and many a time the discoveries are not very pleasant. It is almost a jungle down there and no one has any clue what they are, how old or in what condition they are but if anything goes wrong, which it is bound to, we have to face everyone’s wrath.”
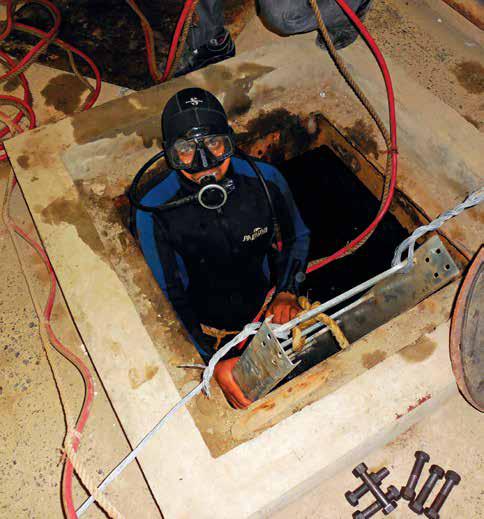
A diver accessing a storage tank
There are water lines, power lines, gas lines, telephone lines, sewerage lines, all jumbled up without any colour coding or markings whatsoever. “Therefore, first we need to make sense of this jumble, identify the nature of the lines, mark and map them and then carefully handle them so that there are no disruptions. In fact, after most L&T projects, one big gain for the concerned municipality is that all their underground public utilities will be clearly chartered but we don’t get paid for this extra service,” adds Sudheesh with a sad smile.
“It is a discovery process and many a time the discoveries are not very pleasant. It is almost a jungle down there and no one has any clue what they are, how old or in what condition they are but if anything goes wrong, which it is bound to, we have to face everyone’s wrath.”
– K S Sudheesh Kumar
Head – EHS, WET IC
Gas lines are a huge concern when executing in cities like Bengaluru. Sudheesh recalls an incident at the WSF to Bommanahalli Project, when excavating on the main road after taking permissions from GAIL, in the presence of GAIL engineers. “Unfortunately, a gas line was damaged. We isolated the area in no time for an hour to attend to the leak, considering public safety in a heavy traffic area.” All such excavation works in such areas must be carried out in the presence of authorised personnel with Emergency Preparedness Plans and other arrangements. Assistant EHS Manager, Abhijit Rout adds that digging into an old network without updated drawings and plans is only asking for trouble.
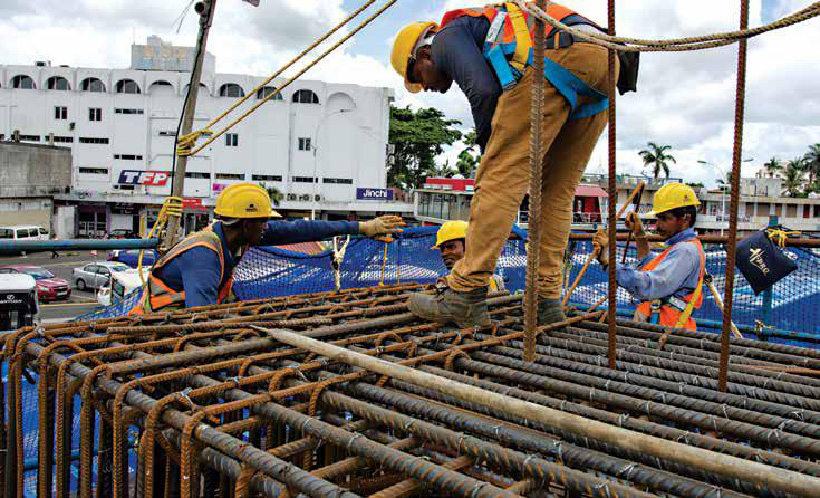
Rebar works
The situation is not very different overseas as EHS Manager, R Palanikumar at the Mauritius Metro site deals with an old network and non-updated drawings and plans. “It is time consuming,” he laments, “and often we have to repair some of the damaged pipes that are over half a century old. The public do not understand our difficulties therefore managing their grievances is yet another issue.”
At times, there are several endusers involved that project teams are forced to approach for the necessary approvals. Kumar perks up, “We faced this situation both in Ahmedabad and Mumbai. The reality is that we have a non-negotiable delivery deadline which these authorities will never appreciate; at the same time, we cannot ‘push’ too hard either because then things could backfire, so it is quite a tightrope walk!”
The depth and extent of excavations are dictated by the condition of the soil. K P Ravinath, Head – EHS, L&T GeoSTructure offers valuable insights. “Crews are often briefed not to go below the level of existing foundations and if deeply embedded structures are encountered, work should proceed only after thorough review and provision of supports.” Debris removal and backfilling are related functions which if not taken up and completed quickly and efficiently, can, as Kumar jokes, “literally cause a stink!” More than a stink, it can lead to unsavoury situations that a WET team had to encounter at a project in Moradabad, UP where the incomplete backfilling work by the concerned authorities led to a fatality due to flooding of open pits that were also not safe barricaded. Executing open cut excavation is normally carried out by SBH shoring box (German technology for shielding & shoring) and other approved shoring systems from EDRC in congested or narrow areas with all safety requirements.
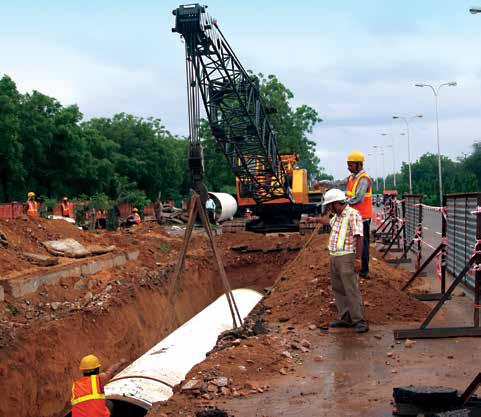
Workmen busy laying pipes under the watchful eyes of supervisors in a well barricaded zone
“It is time consuming and often we have to repair some of the damaged pipes that are over half a century old. The public do not understand our difficulties therefore managing their grievances is yet another issue.”
– R Palanikumar
EHS Manager – Mauritius Metro
It is an ordeal for our WET IC teams to excavate, tunnel or carry out trenchless cuttings to lay pipes in the middle of crowded marketplaces or on roads with heavy traffic. “The hazards and risks need expert assessment and control measures implemented through a hierarchy of controls,” cautions Sudheesh. At the same time, they must consider options of alternate routing, coordination, permissions, timing of activities, compliance to statutory requirements, restriction of the public, diversions or alternate traffic routes and traffic management. “We even consider updated technologies like Diamond Rock Cutting.”
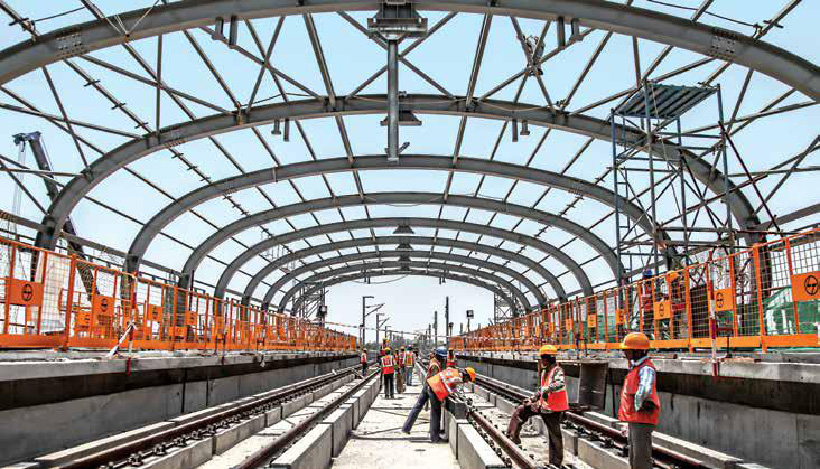
Track laying
Consider all these factors when constructing in a teeming city like Kolkata and one can understand Cluster Head, Waste Water, KKCO (WET IC) Business Unit, M M Jaiswal’s task of executing a sewerage pipe line network in Barrackpore city. “This is one of the most crowded places with multiple local railway station gates adding to the mess. We had to safely construct a lifting structure and a STP with pipe networking both above and below the ground. We managed,” grins a relieved Jaiswal.
Public interface is unavoidable but needs to be handled with kid gloves as incidents involving the public can get nasty, warns Sudeesh. “There are potential risks of public agitations, mobs, media and sometimes national attention, stakeholders’ dilemma, company reputation, brand image and other issues.”
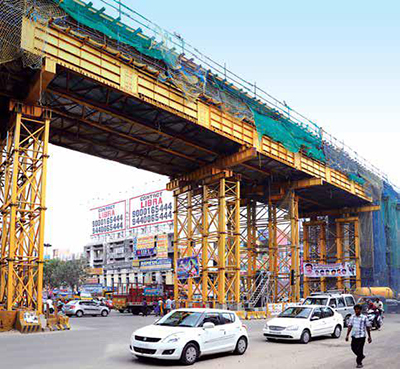
Putting safety first for a steel girder erection across a busy traffic junction
Apart from controlling external factors like traffic and public, project teams must be equally vigilant of internal factors within a site – the huge quantum of men and material entering or exiting a site that require close monitoring. Normally, safe access and exit points are clearly identified and demarcated and as Brij Mohan Sharma, Chief Project Manager, Lucknow Metro, TI IC, adds, “Prior to start of any work, the EHS & execution teams conduct safety walk downs to ensure safe access and egress.”
Flooding is another issue that several cities experience during the monsoons and it is imperative for teams to be always prepared with a clearly laid out de-watering plan and equipment.
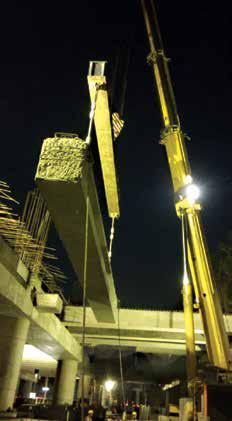
Lifting of girders in the middle of the night
Moving mountains
With excavations, come the onerous task of manoeuvring the large, heavy earth moving equipment into place. “This is tricky,” cautions Stephen Storey, Head – EHS, Heavy Civil Infrastructure, “because it involves large vehicles like tippers to remove the debris and while most of this activity is planned for the night, it can still cause traffic snarls, irate pedestrians and even residents cross with us for spoiling their sleep with the din we create.”
Gigantic precast elements like piers, pier caps and girders used in the construction of metro rail systems need to be transported from the casting yard to the site for insitu erection. “Normally, these are transported on large flatbed trailers that are then manoeuvred in extremely confined spaces into position from where the precast elements are lifted and erected all during a small window that we are given. So,” continues Stephen ticks off on his fingers, “we have to work fast, quietly and super efficiently.” Logistics and safe movement planning are critical; even the most minute aspect needs to be considered and factored in. Often big tasks come undone because of some small, seemingly insignificant error of planning or judgement. “Some of these are trickier as what we have to erect are off centre of gravity (CG),” adds Stephen, miming the tilt.
Lifting, shifting of heavy equipment like transformers, cable drums, masts and other big equipment warrants a well-thought-out and meticulous traffic management plan that is usually drawn up in consultation with various stakeholders: client, local authorities and other contractors. “We created an Interface Committee,” Brij Mohan of LKM informs, “and our plan included prior approvals of road diversions, traffic blocks from local authorities, the deployment of traffic marshals and installation of blinkers.”
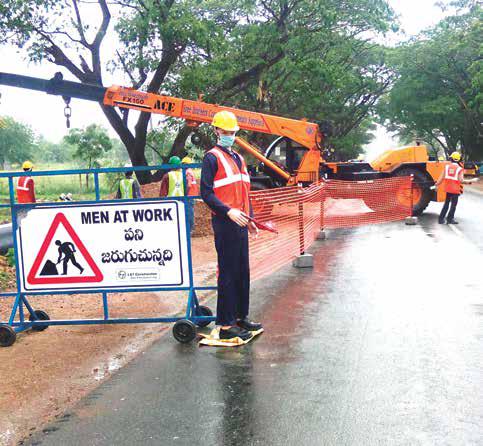
Mannequins as flagmen to avoid putting people in danger
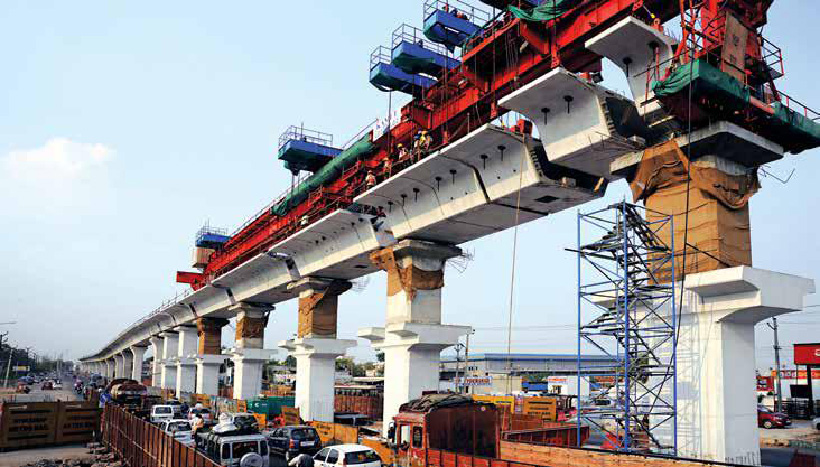
Girder erection using push launch technique with a marked secure zone for vehicle transit
Sanjay of Lucknow Metro, mentions a TRAP system that was implemented to ensure comprehensive safety at work especially along some of the sensitive places of Lucknow. At instances, where traffic cannot be fully restricted, hard barricading and reflective caution signs isolate the work area from public movement.
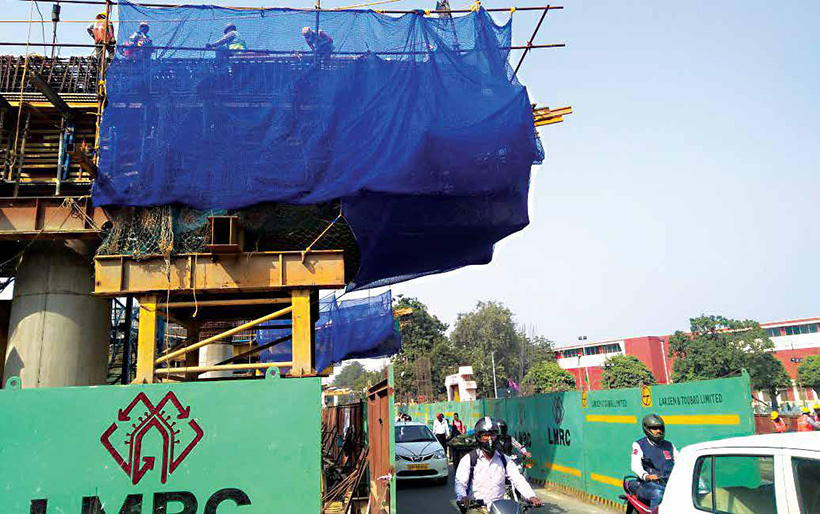
Providing complete cover with safety nets and barricading for an elevated metro corridor construction
Careful and meticulous material handling is another key to success. “After a reassessment of the risk factors, lifting plans/permits are drawn up and shared with the client for approval and concurrence,” informs G Divakar, Senior Manager EHS, Heavy Civil IC. “All applicable risk assessments and method statements are reviewed before undertaking any heavy material handling activity and, as a matter of SOP, the condition of plant and machinery such as cranes, lifting accessories are regularly checked by the EHS department and by third parties to ensure safe usage.”
“All applicable risk assessments and method statements are reviewed before undertaking any heavy material handling activity and, as a matter of SOP, the condition of plant and machinery such as cranes, lifting accessories are regularly checked by the EHS department and by third parties to ensure safe usage.”
– G Divakar
Manager EHS – HCI IC
Fitness of equipment is another critical consideration. Meticulous prestart checks certify that equipment is good to go like as Sanjay adds, “Cranes were specially checked for their safety and warning devices.” Wherever required, the lifting area is cordoned off, barricaded and manned by traffic marshals. “Often, it is not human error but machine error that can spoil our day,” remarks Divakar though for Palanikumar, the roadblock was of a different nature. “To get a 35 m man lift to work at the river bridge was a struggle because man baskets are not legally allowed in Mauritius and therefore finding the optimized medium to execute works at height within the Mauritian legal framework was a challenge.”
For Sanjay and team, the heart of their project was a 177 m cantilever bridge across the Gomti River connecting old and new Lucknow including an engineeringly challenging 85 m long central span at a height of 13 m without any pillar in between. “We also had to erect a 60 m ROB within 5 days across a 25000-volt railway powerline that called for a lot of detailing and microplanning right from fabrication of steel structures, logistics and preparing the lift scheme,” remarks Sanjay.
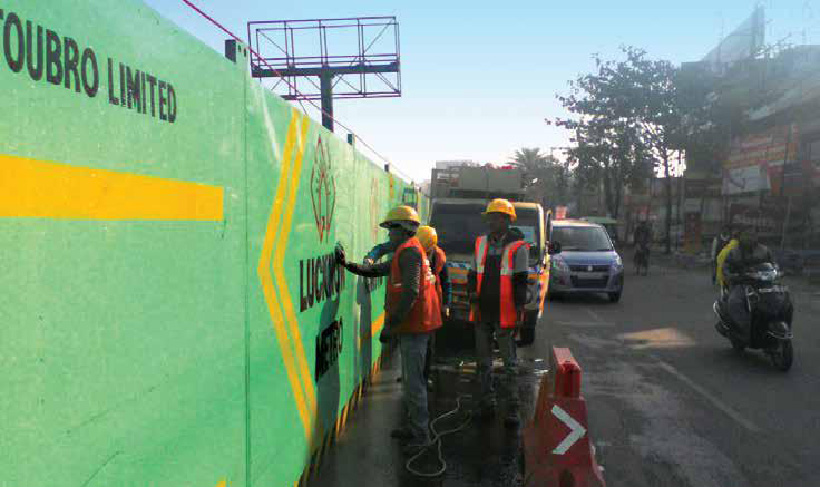
Communicating the message of safety
Working at height and at night in cities
Lucknow Metro had multiple erections of bridges, large spans, portals across roads and over live railway lines at height. “The first task is to carefully choose suitable contractors and then put all workmen, ours and theirs, through a rigorous EHS training including compulsorily undergoing the Acrophobia Test (suitability for height work),” informs Sanjay.
A thoughtful departure from the standard use of ladders was the introduction of Rail cum Road Vehicles (RRV) which are elevated work platforms enclosed from four sides for OHE works like installation of insulators, cantilevers, droppers, stringing of catenary and contact wires, etc. Subhamoy Maitra, says that “Group risk assessments define the best control measures which are “so far Reasonably Practicable” and such control measures are implemented.” At the SW&C site at Ahmedabad, a dual level working platform equipped with knee roll handrails and toe guards was devised to accommodate workmen with materials.
“The first task is to carefully choose suitable contractors and then put all workmen, ours and theirs, through a rigorous EHS training including compulsorily undergoing the Acrophobia Test (suitability for height work).”
– Sanjay Singh Gangwar
Project Manager – Lucknow Metro
The hazards of working at night are darkness, fatigue and sleep, lack of alertness and workmen indulging in alcohol. The Chennai Metro project team recall a bad accident that occurred a couple of years ago because some of these boxes were not ticked.
The most basic requirement is a well-lit site. An illumination level of minimum 50 lux, certified before start of work, is normally used at sites to ensure that speed of execution does not slacken at night. At WET IC, the P&M department has ensured that all equipment at site have reverse horn and delayed start mechanisms to alert workmen. Sudheesh adds that they have implemented human proximity sensors to ensure public safety.
“Group risk assessments define the best control measures which are “so far Reasonably Practicable” and such control measures are implemented.”
– Subhamoy Maitra
RREC – EHS Head
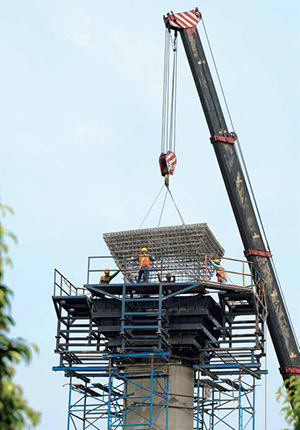
Banking on staging and a secure lift method
When dealing with high voltages, OHE charging is decided only after consulting with clients and procuring permits. “It’s critical that everyone should be alerted of the charging,” warns Subhamoy, “Induction current, if any, from the OHE wire or from any nearby power lines, should be first neutralized with discharge rods, the continuity of circuits checked for any faults by competent licensed electricians to ensure earthing.” Lineman are deployed at all access points to restrict unauthorized entry into the charging zone.
Life in most cities are fast-paced and as builders of infrastructure, we are often hindrances, causing disruptions, throwing their wellplanned lives out of gear. As planners, we need to be cognizant of that and ensure that they suffer least pain for the big gain that we are constructing for them.