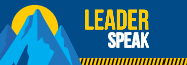
S V DESAI
Senior Vice President & Head Heavy Civil IC
If the Heavy Civil IC has been successfuly delivering mega projects to quality, safety and timelines, it has been largely thanks to our ability to provide ‘tailormade’ solutions to suit the specific requirements of our customers which presupposes a clear understanding of customer requirements and expectations. Often, the challenges we face at our various sites are unique, without precedent that calls for quick appreciation of ground realities, understanding the true nature of the issue at hand and thinking on one’s feet to evolve mitigation strategies. We, as a team, have been able to think out-of-the-box to overcome many of these challenges.
Be it massive concrete pour record of 16,722 cum in a single day at Medigadda Barrage project, or launching girders cycle time of 2 days per span at Riyadh metro, or record casting a 16 m tall RCC wall in a single pour using system formwork, or custom P&M solutions to meet stringent environmental requirements such as Rock Splitters and Hydraulic Auger cleaners at Mumbai Metro UGC-01 project, Innovation, has been one of the chief enablers to achieve these benchmarks that are on par with international norms.
In addition, our digitally ‘connected sites’ supported by various applications help us monitor the projects closely and ensure optimal use of 3M (Materials, Machine & Men) at every step of the progress enabling continuous improvement and setting productivity benchmarks.
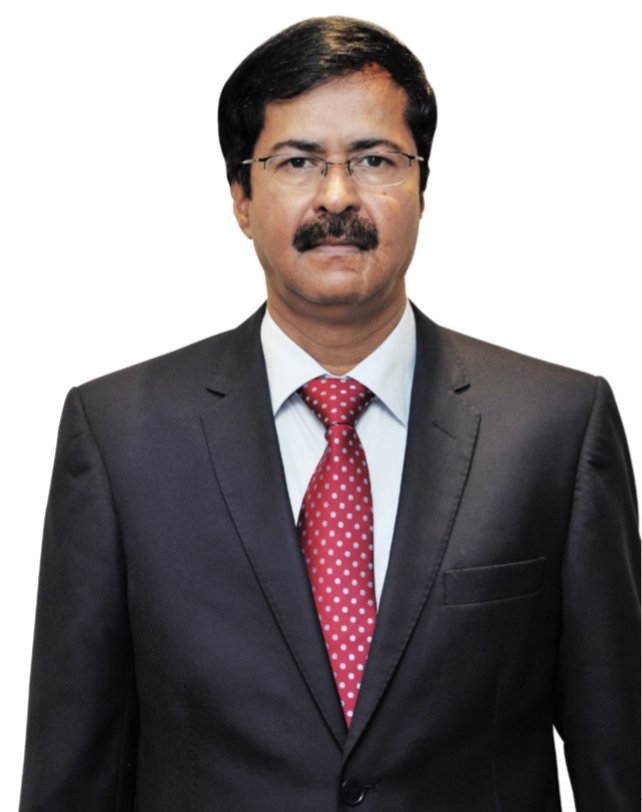
Innovations can be big or small but our focus, as a team, will always remain to constantly seek ways to enhance productivity, improve cycle times, reduce execution time, cut costs that will, at the end of the day, translate into superior operational efficiency and more satisfied customers.
INNOVATIONS THAT BRIDGE THE FUTURE
Achieving operational efficiency at Heavy Civil
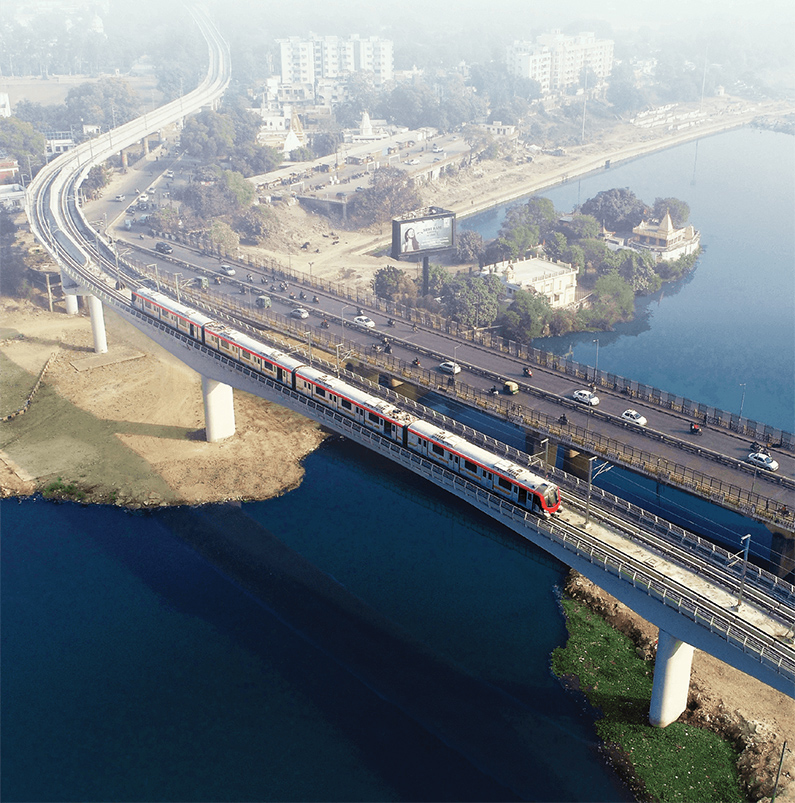
Perhaps, the most defining aspect of the Heavy Civil IC has been, as the name suggests, constructing projects of huge size and scale and as projects become bigger and more complex, the need for best practices and more efficient construction methods to enhance overall efficiencies and complete projects within stipulated timelines is greater.
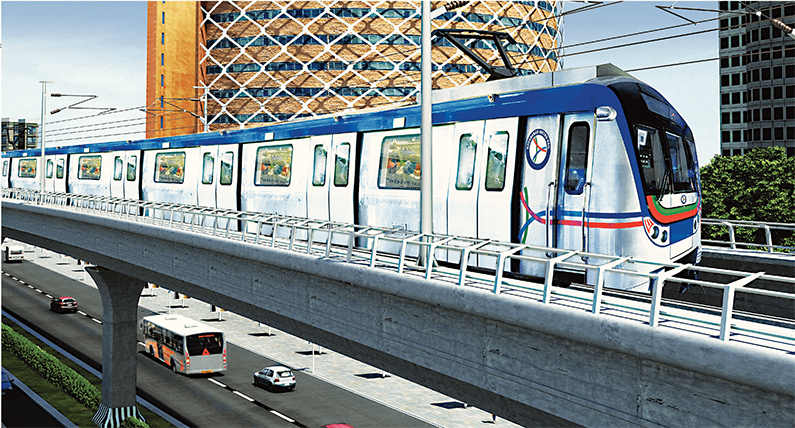
Hyderabad Metro Rail
Introducing some chief enablers
Enabling structures are the lifeline of Heavy Civil projects, to build imposing and permanent structures that are interdependent, as their design and details govern that of permanent structures and vice versa. The construction methodology decided during the tender stage, can have major consequences if changed mid-way through the project. Right selection, effective planning, design and operation of enabling structures are imperatives for success.
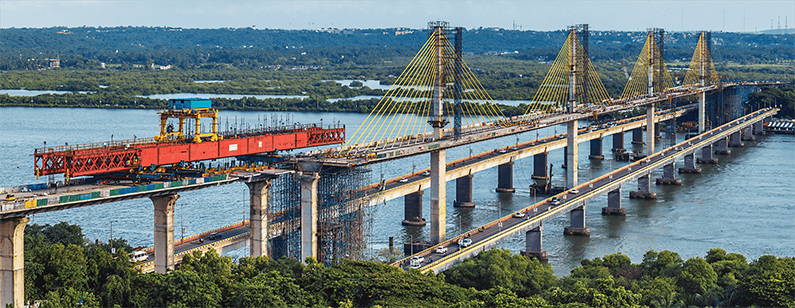
Launching Girders: With precasting technologies dominating the construction industry, precast segment erection has formed the backbone of infrastructure projects that are more equipment intensive than labour driven. In this realm, the Launching Girder (LG) has assumed prime importance. Huge precast segments were erected in challenging projects like the Hyderabad Metro by purpose-made erection machines called ‘1st Gen LGs.’ These 2-lane LGs are designed considering sharp curvatures in the alignment, capable of achieving a cycle time of 3 days per segment and a lifting capacity of 520 MT. Other types of LGs deployed at the Hyderabad Metro project included the underslung, the movable winch and the hinged LGs, all improvements on the 2-lane LG. Hinged LGs are preferred in the confined spaces of congested cities as these can be scaled to erect spans ranging from 19 m to 31 m with 128 m Radius of Curvature and a lifting capacity of 450 MT to achieve cycle times of 6 days per span. “The Movable Winch LG was developed to address the sharp curvatures of Hyderabad’s roads,” elaborates T Vijayakumar, Head – CPMC, Heavy Civil, “that were designed to erect spans of 31 m and 34 m with a Radii of Curvature of 128.1 m and 150.2m respectively with a rear segment feeding provision. The Hyderabad Metro project holds the record for the highest productivity in India in the erection of box girder superstructures (15 spans / LG month) as published in www.ice.org.uk,” he mentions proudly,
“The Hyderabad Metro project holds the record for the highest productivity in India in the erection of box girder superstructures (15 spans / LG month) as published in www.ice.org.uk.”
T Vijayakumar
Head – CPMC, Heavy Civil
The capability and productivity of LGs were further enhanced in the construction of Goa’s 3rd Mandovi Bridge with the design and development of the Twin Box Launching Gantry to leverage hydraulic power. Hydraulic circuit systems were developed and deployed to improve operations, such as the remote operated segment positioning system, semi-automated side shifting system, and the support shifting system with a lifting capacity of 1500 MT that helped achieve cycle times of 6-10 days per span compared to other launching girders and, as a competitor to international brands.
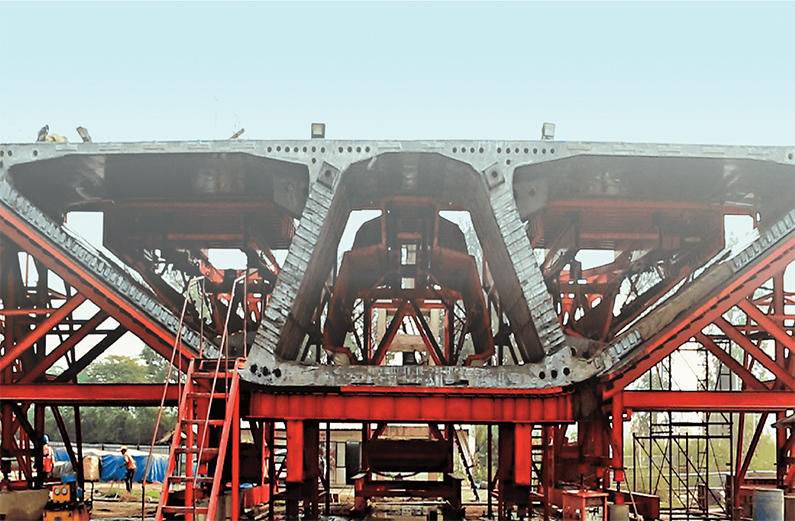
Semi automated mould, Barapullah
Bridge Builders: Segments weighing up to 65 MT can now be erected using winches for erection and hydraulic jacks for movement with the specially designed, semi-automatic Bridge Builders (BB) that have revolutionized ROB construction. ‘Weighing about 120 MT, a pair of BBs can erect straight segments as well those with sharp curvatures of up to 128 m radius,” explains TVK, “and with a lifting capacity of 60 MT, we can achieve a cycle time of 2 days per segment.” First engineered for the Hyderabad Metro, BB set a world record for the fastest segmental span erection at Mandovi Bridge and an Indian record by constructing a 30 m span of the Malakpet ROB in just 25 days. BBs have accelerated the progress of special bridge projects as well like the 3rd Narmada Bridge, 3rd Mandovi Bridge, the Barapullah Extra Dosed Bridge, and the Durgam Cheruvu Bridge. “BBs have positively impacted productivity, cost, delivery, safety, quality and improved cycle times,” vouches V R Saravanakumar, Project Manager, HMRL.
“Our initiative to cast the full height of the wall from raft, top to bottom of the roof slab in a single pour with the L&T formwork system addressed the lack of skilled manpower and shortage of trade workers in carpentry.”
Roy George
Head – Formwork, Heavy Civil
Form travellers: Designed for cantilevered concrete girder construction at the Lucknow Metro project, each form traveller can cast 12 segments with an average cycle time of 12 days per segment against the industry norm of 16 days. “In fact, this special cantilever bridge holds the record for the fastest balanced cantilever construction in India,” enthuses Sanjay Singh Gangwar, Project Manager, Lucknow Metro.
Semi-Automated Short Line Moulds: were used for the segment casting at the Barapullah Extradosed Bridge project. The hydraulically controlled operations in an automated mould set a record in the casting schedule achieving 3.5 days per segment to match international standards. “The compact, scalable, and versatile system suits all blisters, eliminating human intervention and hydraulics improves accuracy, quality of segment profile and finish,” shares Shubendhu Bose, the Project Manager.
Casting Gantry: was designed to cast I-Girders on a large scale that reduced the total time required for casting I-Girders at the Ishwar Gupta Project from 836 man-hours to just 514 manhours! “A moving frame to carry and guide the formwork during moulding and de-moulding operations was certainly a leap towards automation,” says an excited Sandip De, Project Manager, Iswar Gupta Setu.
Marine construction: CMPC had the opportunity to prove their mettle in marine constructions by designing a 5-span, continuous (9.6 m per span) Temporary Modular Access (TAB) bridge at the Mumbai Trans Harbour Link Project, Package-1 suitable to march 150 MT capacity crawler cranes of 8 m width, floating batching plants, material barges, storage barges (aggregate, cement & reinforcement) etc., that has enabled round the clock operations.
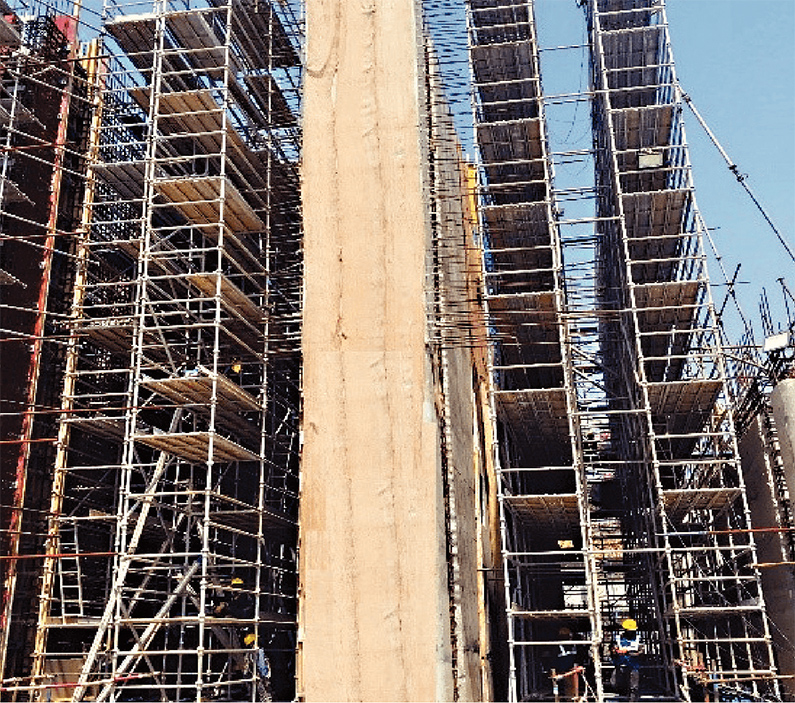
16-meter tall formwork system for Kudankulam Nuclear Power Plant
Larger pour, Lesser resources, Higher productivity
The KKNPP–HTS Phase II project achieved a milestone in the Construction Industry by casting a 16 m high RCC wall concreting in a single pour using a 16-meter tall Formwork System. Head – Formwork, Heavy Civil, Roy George explains, “Our initiative to cast the full height of the wall from raft, top to bottom of the roof slab in a single pour with the L&T formwork system addressed the lack of skilled manpower and shortage of trade workers in carpentry.”
Shutter panels weighing about 3.5 MT were handled using heavy duty tower cranes to cover the work area of the pump house. Adopting the tremie method, concreting was planned to reach the bottom level with two intermediate platforms positioned at 5 & 10 m levels to carry out the concreting and vibration works. “Special mechanisms were designed and used to lift and tilt the shutter panels to either position them on the raft or move them safely from one place to other,” explains Anup Kumar Anupam, DGM, Formwork – KKNPP HTS Phase II Project. Shutter panels were so designed that the alignment and erection required minimum manpower and less time with the shuttering crew engaged on both sides of the walls to continuously monitor and record the supports, tie rods and maintain verticality of the shutters during concreting. The mechanical crew were also vigilant to monitor the displacement of embedded parts during concreting. The initiative was appreciated by the client, NPCIL, who acknowledged it as a one-of-its-kind in their history.
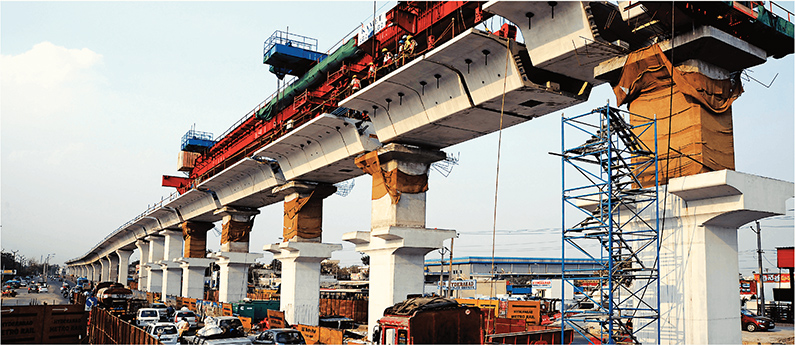
Girder erection at Hyderabad Metro Rail Project
Vizag Vessels Project – a hot bed of innovations
While this naval project is veiled in secrecy due to obvious reasons, there are several interesting snippets that have emerged that reveal the agile, active, engineering minds working on this project.
Mating the parts to make a whole: In vessel construction, mating two mammoth sections involves huge labour, time and cost and is traditionally carried out by a trial and rectification method, entirely dependent on the skill sets of the workmen involved, resources available, accuracy of inspections at every stage, etc.
In addition, several repeated activities adversely impact manpower productivity and resources. Erstwhile, the process involved shifting the sections to site, aligning them on the saddle post, two sets of trials followed by green trimming and WEP of the sections before final set up. The attendant hazards were many: multiple erection and removal of scaffolds, working at heights, crane availability for repeated trials, movement of the CMM (Coordinate Measuring Machine) while taking profile readings, multiple movements of sections via trolleys amongst others.
“To reduce cycle time and increase productivity, we brainstormed and came up with a digital solution to introduce a FARO Laser Tracker,” shares E Kranthi Kumar Reddy (Senior Engineer, Vizag Vessel IV), “that digitally captures profile readings, superimposes the readings after taking a common reference point, analyses the data to arrive at the green trim line and projects it onto both sections.”
The result was better than the team anticipated: significant reduction in hazard levels, reduction of cycle time from 21 to 9 days (!) along with huge saving in time, cost and labour.
4D modelling using Synchro: Manual project monitoring involves engineers forced to spend lots of their precious time to complete a host of non-valueadding activities which Raaj Kumar G (Senior Engineer, Vizag Vessel III) and team wanted to eliminate to improve productivity and quality of the project.
“The answer lay in introducing 4D Modelling using the Synchro BIM 360 software platform,” he shares, “that drastically reduced manual work, saved time, made monitoring, tracking of the entire project life cycle, material tracking and reconciliation simple and easy!”
4D BIM includes project schedule, costing and with the data posted on cloud, it can be accessed by allconcerned anytime, anywhere, that helps the team keep track of progress, closely monitor critical paths, detect clashes, manage payments, avoid rework, evaluate different scenarios, derive insights and compare & contrast alternative construction strategies. Certainly, a great asset for Raaj Kumar and team.
Passing the hydro pressure and leak tests with flying colours: M Arun Kumar (Engineer – Mech, Vizag Vessel) and team, in normal course conduct hydro pressure tests (1.5 times of working pressure) on more than 10,000 spools and leak tests (1.25 times of working pressure) on 25,000 spools of detachable joints. During the process, leaks occur invariably due to hoses and adaptors and the time spent to check, detect and rectify these leaks, a drain on the project. “In fact, our FTR (First Time Right) was below 60%,” laments Arun Kumar, “primarily because of improper tightening, frequent opening and tightening of the hoses and lack of standard enabling items.”
To address these issues, the team introduced a Quick Release Coupling that cut the time to make one connection from 5 minutes to just 15 seconds, reduced wear and tear, the chances of thread misalignment and eliminated failures in the Go/No Go gauge tests. “Our FTR has jumped to 92%!” rejoices Arun Kumar.
Moving from 2D to 3D to improve productivity: Laying cables in extremely confined spaces is one of the biggest challenges for teams working on vessels and Pritam Bose (Construction Manager, Vizag Vessel III) and team had only about 15,000 of them to lay maintaining stringent quality norms without interfering with other adjacent elements like pipes, internal structures, equipment, etc.
“It was a tedious process as we had to keep referring back time and again to the drawings and spec sheets to match them to the actual situation at site,” he explains. “Chances of errors were high as every change conducted, big or small had to be captured.”
By replacing all 2D auto cad drawings and spec sheets with a single 3D PDF, life has changed dramatically for Pritam. “It has improved our productivity, we enjoy better visualization, there is less rework, we are able to manage change better and, most importantly, it has improved our FTRC (First Time Right Clearance),” he grins happily.
Towards operational efficiency in Supply Chain Management
Creating a SOP for SCM was a revolutionary first step taken by the team that captures all the systems, processes and digital initiatives being followed making it easy for even a novice to hit the board running. Big data and analytics are the new order and the introduction of ‘Lattice’, a module to manage data in the EDMS (Electronic Document Management System) has been a huge step in the right direction. “We can track activities real time,” shares Prasanta Gupta, Head – SCM, Heavy Civil IC, “starting with the procurement plan, updates of various procurement packages, identify bottlenecks, target dates, people responsible and the like. Monthly activity progress keeps us abreast of savings over ACE/ JCR/ baseline costing, cycle time, vendor database, locators and cost sheets are readily available to refer saving us lots of time.” ‘Lattice’ has made everything paperless including new vendor registrations, RFQs, offer documents, comparison statements, scrap declarations and e-auctions.
“With Electronic Document Management System, we can track activities real time starting with the procurement plan, updates of various procurement packages, identify bottlenecks, target dates, people responsible and the like.”
Prasanta Gupta
Head – SCM, Heavy Civil IC
Skill set mapping to specific categories: Based on spend trends over the past 3 years, 63 major categories have been identified and mapped with the skill sets of team members to ensure that the right person is assigned the right procurement as category specialist.
Creating healthy competition to improve performance: The PUGH Matrix decision making tool is one such idea that is handy when several parameters are not at par and it has paid rich dividends for the organization in the use of TBM at the Bengaluru Metro project.
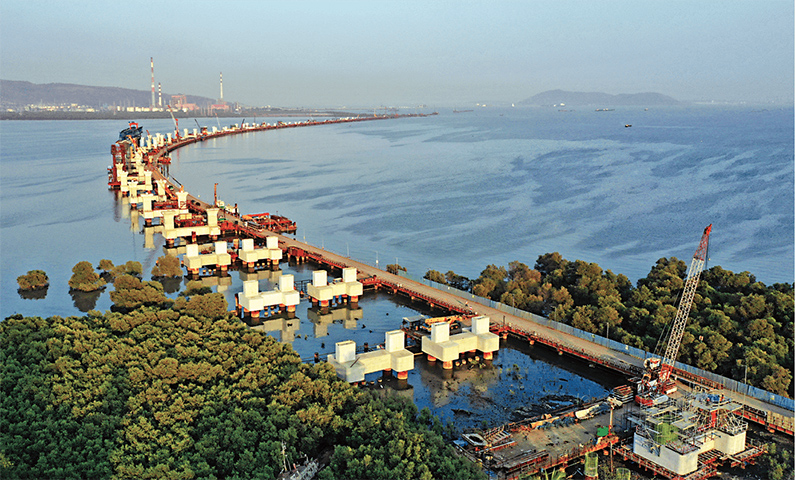
Bridging the sea at the Mumbai Trans-Harbour Link project
Innovations at the front line
Operational Efficiency through Lean techniques: Lean Construction Methodology has sharpened day to day tracking, smoothened work planning, improved standards of house-keeping and reduced cycle time of activities for the Mumbai Metro UGC-07 project team. Value adding and non-value adding activities have been identified with efforts taken to eliminate nonvalue adding tasks. The lean tools implemented are the last planner system, work sampling, value stream mapping, 5S, BIM Big Room Meeting, WS, VSM and LBMS.
“The project won the 1st Prize for Lean Implementation at the ‘Lean Construction Training and Implementation Programme 2018’ organized jointly by IIT-M, IIT-B and ILCE (Institute for Lean Construction Excellence) after 9 months of continuous evaluation,” shares a proud Jayarama H, Project Director, MMRC UGC-07. The award was won against tough competition among 8 sites (3 from L&T Construction and 5 from other companies).
“The Mumbai Metro project won the 1st Prize for Lean Implementation at the ‘Lean Construction Training and Implementation Programme 2018’ organized jointly by IIT-M, IIT-B and ILCE (Institute for Lean Construction Excellence) after 9 months of continuous evaluation.”
Jayarama H
Project Director, MMRC UGC-07
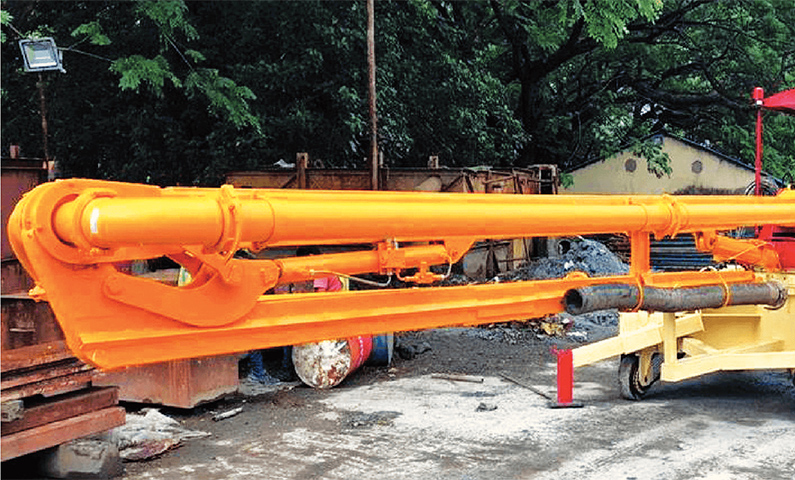
Spider boom placer
P&M Innovations: The P&M team of the MMRC UGC-01 project innovated a ‘Spider Boom Placer,’ a smaller version of the boom placer with automatic boom extension and swinging operation. “When using conventional concrete pumps in concreting works, our main concern was the enormous amount of time taken and manpower required to fix pipeline works apart from the delay in clearing the concrete from the choked pipes,” points out Avdhesh Kumar Mishra, P&M – MMRC UGC-01. “For a mere INR 4 lakhs, we developed the Spider Boom Placer that is smaller, more economical than other boom placers commercially available with OEMs that carry a tag of approximately INR 40 Lakhs plus.”
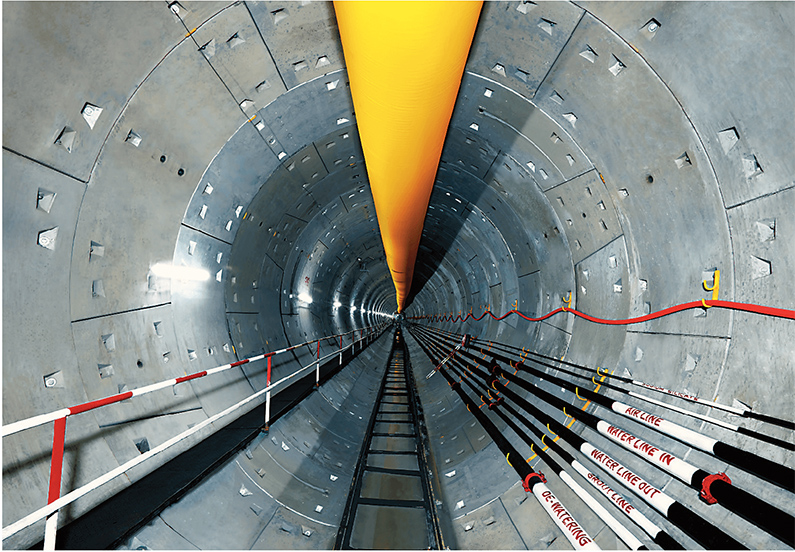
One of the underground tunnels for Mumbai Metro
With the hard rock ground strata at UGC-01 impeding excavation productivity, the P&M team innovated two solutions to address the issue. Rock Splitter: that works on the hydraulic principle and depending on the rock strength, applies 60-100 MT load on the wedge which when inserted into the pre-drilled hole of suitable diameter, splits the rock which is then easily removed by excavators. Rock Buster: is a compact and user-friendly hydraulic device in which the drilled holes in rock are expanded and pushed outwards towards free face by applying 70-150 MT load directly on the rock surface.
“Since the size of projects we execute are so huge, the challenges we face are just as huge that call for innovative and out-of-the-box thinking at almost every step,” says SVD. “In fact, our very survival depends on our ability to stay ahead of the curve and we are committed to do so,” he sums up confidently.
4 HOURS TO BUILD A RAILWAY BRIDGE OVER FOUR ‘LIVE’ RAILWAY LINES
A milestone for L&T; a’first’ for the Indian Railways
On a cold and foggy night in New Delhi on January 26th, when the country was still awake to welcome India’s 71st Republic Day, two L&T teams, one from the WDFCC CTP 15 C project of nuclear & Special Bridges BU, Heavy Civil IC led by Project Manager, M Kannan and the Special Projects & Construction Methods (SPCM) team, attached to Divisional Coporate were in the last stages of preparations to launch one of the two steel griders weighing 160 MT across a 48.5 m span over four ‘live’ lines on the busy New Delhi-Mathura sector, at Asoati in Palwal near Faridabad.
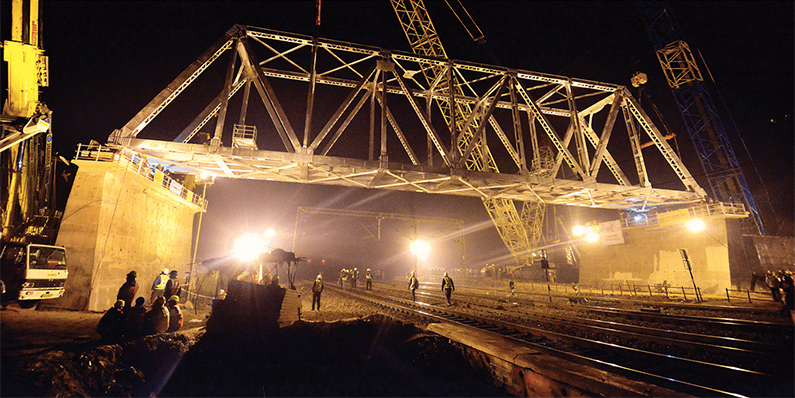
“Normally, we would have used the ‘push launch’ method for such an erection,” points out V Kasiraja, General Manager, SPCM who was one of the prime movers of this operation. “We would have done it in stages with supports, a long-drawn process that would have taken at least a month, and when the work was in progress, the trains would have to move slowly which was not acceptable to the Indian Railways.” That prompted the team to develop an innovative method to launch the long span girders from one end of the RFO using crawler cranes in tandem. “The bridges were handled below the centre of gravity since the cross girder of the bottom chord was stronger, the rigging gears were designed accordingly to ensure stability. For us it was a normal erection but for them,” chuckles Kasiraja, “Rapid bridge construction.”
“Tougher than the actual erection was convincing the authorities at the Indian Railways that what we were suggesting was feasible because they had not seen anything like this before. Our approval sheet carries 30 signatures of various railway officials!”
V Kasiraja
General Manager, SPCM
Preparing the ground for launch
Preparation is key to the success of such an operation. “Tougher than the actual erection was convincing the authorities at the Indian Railways that what we were suggesting was feasible because they had not seen anything like this before,” shares Kasiraja. “In fact, our approval sheet carries 30 signatures of various railway officials!” To address their reservations, a mock lift was arranged and executed post which the teams were given the go ahead.
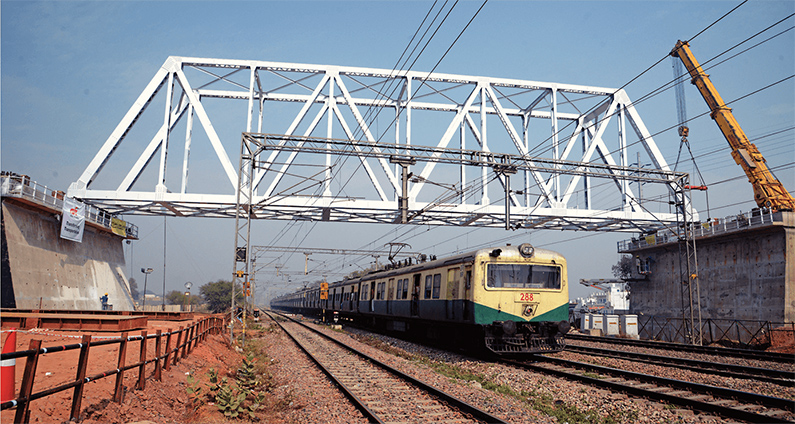
Their first task was to literally prepare the ground for the launch. With paddy fields adjoining the tracks where the super heavy-duty crawler cranes had to be positioned, the project team had to ‘borrow’ the land from the owners, prepare hard stands and lay steel mats on which the cranes were placed. Although only two cranes were used for the erection, another 3 were on standby.
All the elements of the bridge were first assembled on the ground that comprised of two Open Web Structural Steel Girders of 48.5 m span with 7.0 m x 10.9 m cross sections weighing 160 MT each. After assembly, they were torqued, painted and then with the cranes and the super lift counterweights ready, the team waited for the go ahead from the railway authorities to commence operations.
The complete launching activity was executed in a best-of-class manner that is chiefly attributable to the meticulous planning and coordination between DFCCIL, Indian Railways, PMC-2R and L&T.
Anurag Sachan
Managing Director, DFCCIL
Get. Set. Push …
They received the green signal at 12.40 am and had a tight 4-hour window till 4.40 am to complete the erection. It was therefore all systems go.
The bridge was first lifted from the assembly bed with two 600 MT capacity Demag CC2800-1 cranes. While the rear crane marched the entire length of the bridge, the front crane marched only till the railway line barricading and since further movement was not possible, super lift counterweights of 250 MT were added to enhance the capacity before lowering and reaching the other end (radius of 40 m).
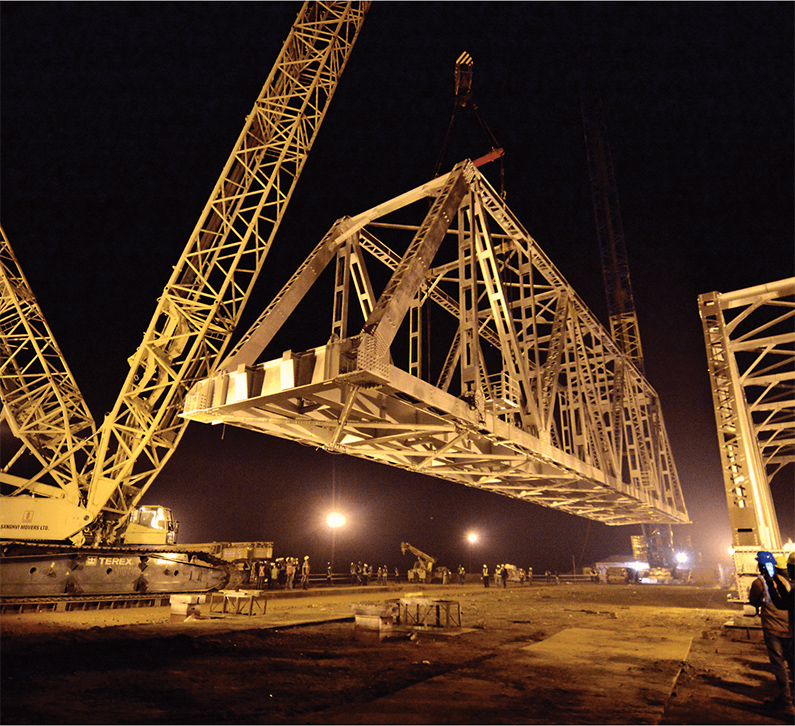
The erection was successfully completed almost an hour before the cut off time to the delight of the railway officials in attendance, watching the entire exercise with bated breath, that included Mr. Anurag Sachan, Managing Director, DFCCIL, who was effusive in his praise of the operation in a letter to Mr. S N Subrahmanyan, CEO & Managing Director, L&T. “The complete launching activity was executed in a best-of-class manner that is chiefly attributable to the meticulous planning and coordination between DFCCIL, Indian Railways, PMC-2R and L&T,” he wrote, further expressing his appreciation of the team’s precautionary and emergency standby arrangements and for maintaining the highest levels of safety throughout the operation.
“Our method has now been adopted by the Indian Railways as a standard operating procedure for all such erections!.”
M. Kannan
Project Manager
Having perfected the act, the teams launched the second girder on the night of January 28th with equal alacrity, efficiency and success. For Kasiraja and team, the success is even more satisfying because as Kannan remarks with pride, “our method has now been adopted by the Indian Railways as a standard operating procedure for all such erections!”
RIYADH METRO –
BULDING VIADUCTS EFFICIENTLY!
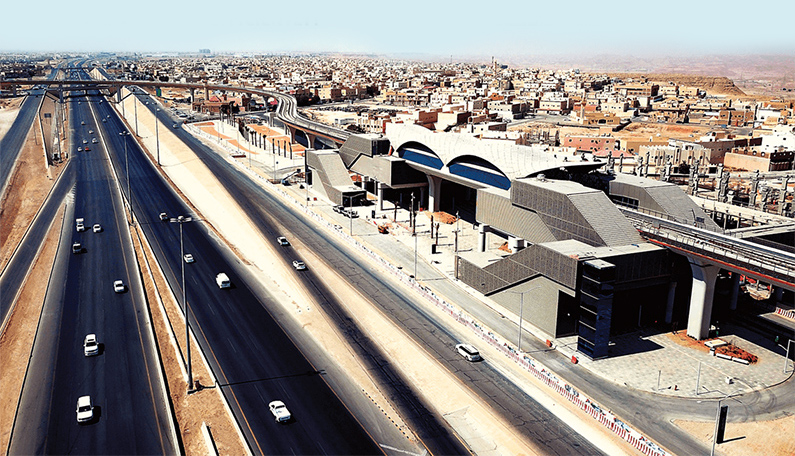
6 lines, 176 kms long Riyadh Metro network is being built by some of the biggest names in the global construction industry. 41 km of line 3 is being constructed by L&T as a major partner in the ArRiyadh New Mobility consortium. Running from west to east, 25.7 km of the line is elevated,with underground sections in the middle and the remaining portion at grade. The line features 20 stations, 2 iconic stations and 2 depots at either end.
Shaping the Viaduct: The viaduct has been designed to optimally accommodate a double track and a maintenance/emergency steel walkway on both sides that also carry the cables trays throughout the route. The structural arrangement is a 3 celled box girder with a sleek, aerodynamic fish belly bottom. For greater efficiency, the entire elevated portion is precast, executed as precast segmental decks with match-cast segments. The deck is supported over a single pier located over the central median for most of the stretches. There are over portals straddling the road when the alignment is away from the central median.
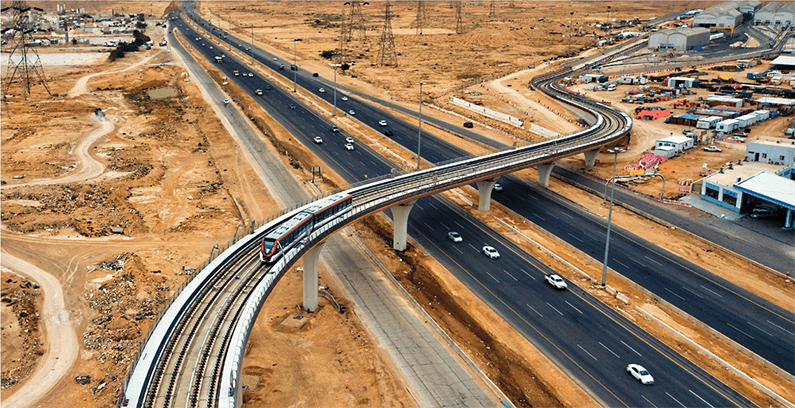
Standardisation is key: Though there are varying requirements for changing the superstructure, the profile is standardised to fit the basic fish belly shape to give a uniform band across the entire viaduct.
To accommodate road crossings of up to 50 m, 3-span continuous hyperstatic superstructures have been adopted with the same standard profile. A similar continuous superstructure arrangement is used to deal with sharp curvatures of up to 150 m and steep gradients of up to 5.5%. For larger road crossing spans (maximum is 95 m), the central cell depth alone is increased gradually from the centre to the supports, maintaining the end cell shape and the uniform band effect and constructed using balanced cantilever construction techniques.
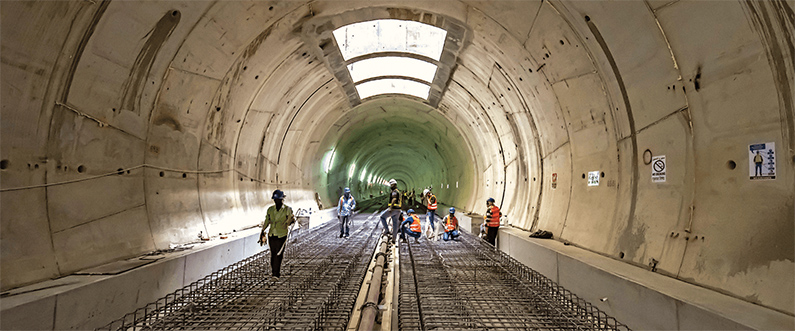
Station in the stride: Completing the stations was a huge bottle neck in the construction of the elevated metro. At stations, in addition to the tracks, platforms need to be incorporated. Conventionally, the station spans are constructed either in-situ or with a different erection technique which interrupts the erection methodology of the viaducts. To overcome this delay, the team came up with a brilliant idea to integrate the viaduct with the platform and precast 17 m wide structures and erected them continuously thus taking station construction in their stride using the same launching girders.
Enter the versatile Universal Launching Girder (ULG): Considering the variety of the construction involved – typical, continuous and stations spans – and the tight schedule, the team decided to deploy 7 ULGs that were versatile enough to handle the different size of spans, dimensions and weights. To use the same launching gantry, continuous spans were carried out in two phases – first the mini cantilever portions near the central piers and then the infills and end spans. The station segments were different, 17 m in width (wider because of the innovative design), 3 m long and weighing up to 130 tons. As the station and continuous spans were designed with precast segments to be erected by the ULG, the erection of the viaduct and station spans / continuous spans could continue uninterrupted without dismantling and re-erecting the ULG near stations.
Challenges & solutions
There were challenges for superstructure erection pertaining to terrain, alignment and traffic diversions but these were pre-empted and considered when finalizing the specifications for the ULG with respect to loads and the design.
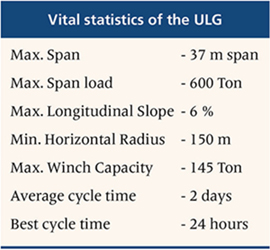
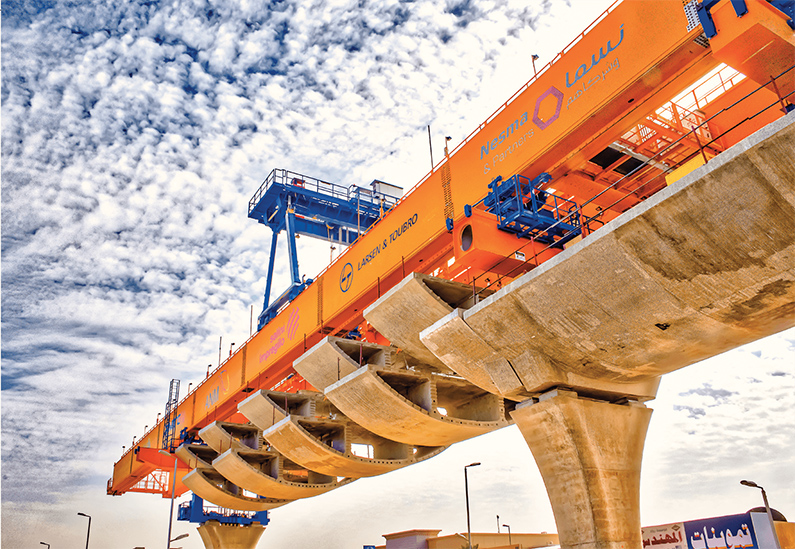
Launching Girder
Speeding across an expressway: The ULG successfully launched a particularly challenging span with a sharp curvature of 150 m radius and a high gradient of 5.6% over the Jeddah Road, one of the busiest expressways, with only a small window of time open for erection. Not once but twice across the expressway to accommodate a station across the other side of expressway.
“Meticulous planning, precise detailing of construction stages and design enabling structures helped us to deliver,” explains Design Head, K. Senthilnathan (KSN). “There were about 58 stages (584 steps) required to complete this complex erection activity and each stage was analysed, and detailed drawings prepared. Our team from the technical office monitored the stages at site to ensure that the erection was safely carried out across the expressway with heavy traffic running all the while below.”
“Meticulous planning, precise detailing of construction stages and design enabling structures helped us to deliver. There were about 58 stages (584 steps) required to complete this complex erection activity and each stage was analysed, and detailed drawings prepared.”
K. Senthilnathan
Design Head
For G. Vinod, Head Elevated Section, this was the first major challenge to prove the efficacy of the launching girders of handling erection over a live expressway within a very restricted four hour window per night. “We had to move the elements and lift them,” he shares enthusiastically, “but this is a major milestone receiving continuous accolades from both client and consultants.”

“Literally, thinking on our feet, we devised a new plan to advance the construction of superstructure as a tie element by integrating the inclined pier to provide a robust structural connection by introducing a closed frame action. The LG was moved over the station in 3 days and we achieved it with detailed construction method planning, immense design support and perfect logistic coordination between the 5 stakeholders involved.”
G. Vinod
Head Elevated Section
Straddling the hurdle: MVS Rao, Viaduct Head, recalls that a huge challenge for his team was to lift the ULG above the architectural piers supporting the sprawling iconic landmark station. KSN points out, “Designing these piers to support the launching girder was both costly and risky as the height of the piers from the station basement is approximately 20 m plus there were the sharp 150 m curvatures of the approach spans to consider that required special tie- downs.” Since the station platform was not being erected by a launching girder, the original plan was to dismantle and re-erect the LG at location that would interrupt work on the station. “Literally, thinking on our feet, we devised a new plan to advance the construction of superstructure as a tie element by integrating the inclined pier to provide a robust structural connection by introducing a closed frame action,” recounts G Vinod. The entire system was conceptualized and devised in-house by the technical department and the detailed design verification was carried out by the design consultant, without any major modification to the available design and in very quick time. “Finally, the LG was moved over the station in 3 days,” says an extremely satisfied G. Vinod, “and we achieved it with detailed construction method planning, immense design support and perfect logistic coordination between the 5 stakeholders involved.”
“Client appreciation for Line-3 Viaduct is a testimony of our team efforts, and credit goes to the entire team for their efforts to leave a legacy viaduct structure in Riyadh and build L&T’s brand image in the Kingdom of Saudi Arabia.”
T. Srinivasan
Head Riyadh Metro
“Client appreciation for Line-3 Viaduct is a testimony of our team efforts,” T. Srinivasan, Head Riyadh Metro summarises, “and credit goes to the entire team for their efforts to leave a legacy viaduct structure in Riyadh and build L&T’s brand image in the Kingdom of Saudi Arabia.”