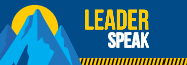
S V Desai,
Senior Vice President & Head (Heavy Civil Infrastructure)
In the construction industry, ensuring production and keeping lives and assets safe are two faces of a coin. These factors have been the pillars on which the entire organization is established and reasons for our glory. Embedding this philosophy within ourselves, we not only learn from our own experiences but also continuously look at our peers to improve our practices and adapt ourselves to changing business scenarios. It is the need of the time to think out of the box to keep our workforce safe and sound, protect and conserve nature and bring smiles to all the stakeholders. The accolades earned speak for the standards that we uphold; the smile brought within the family when an employee returns home safely is our real reward.
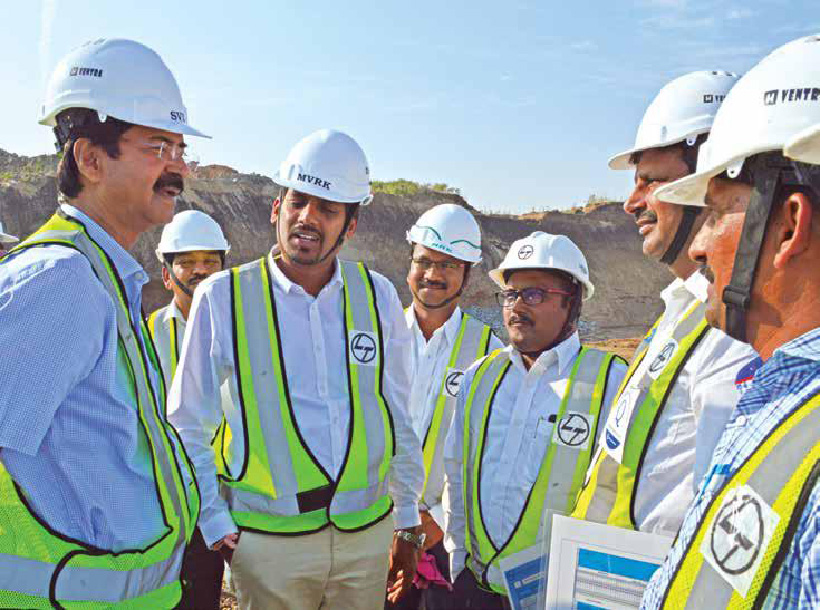
COMBATING THE PERILS OF
THE UNDERGROUND
Keeping safe during tunnelling operations
Starved of space, infrastructure development in recent years is increasingly going underground, as it were. The establishment of L&T’s Tunnelling Excellence Academy in Kanchipuram by the Heavy Civil Infra IC is an important initiative to create and build in-house efficiencies in tunnelling. Several metro projects that L&T is currently executing at Doha, Riyadh, Mumbai and Ahmedabad, to name a few, involve substantial work underground.
Tunnelling is involved in three spheres of infrastructure development: for underground sections of metro projects, tunnelling is normally at a depth of 20-30 m to lay tracks and construct underground stations while in hydel power projects, tunnelling depths can go even up to 1,500 m. In public utility laying projects, sewerage lines normally lie at depths of about 15 m, while others like water lines, telephone lines, power lines or even trenches for laying roads and highways, micro-tunnelling is normally at a depth of 3-5 M.
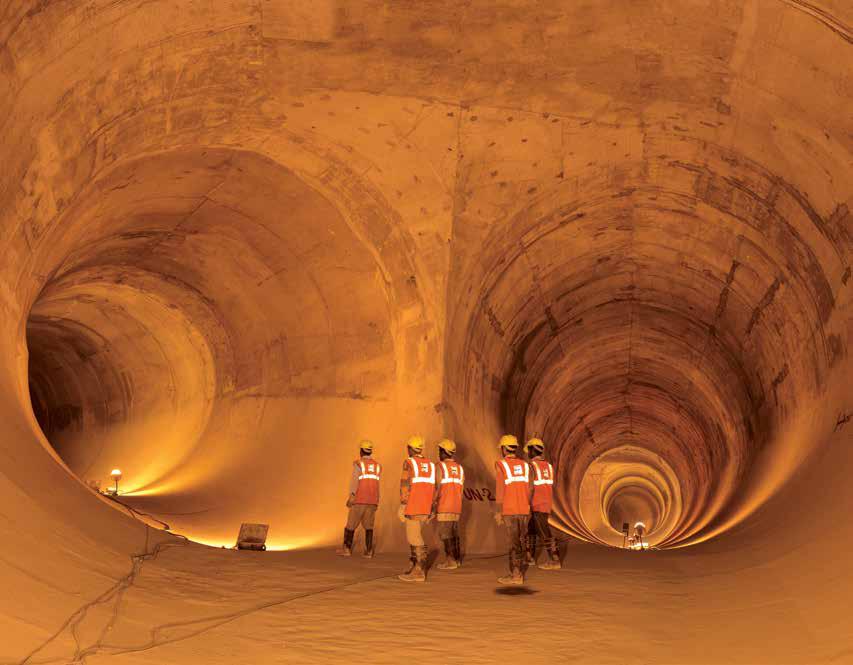
Safe access chambers to the Punatsangchhu HEP
“Often, maps are absent, utility lines are rarely well mapped or is there available data on the strength of foundations of structures so in some cases it is a bit like groping in the dark,” Stephen Phillip Storey, EHS Head, Heavy Civil IC shares some travails about tunnelling, “but modern day geotechnical studies are certainly making our lives a whole lot easier.”
“Often, maps are absent, utility lines are rarely well mapped or is there available data on the strength of foundations of structures so in some cases it is a bit like groping in the dark, but modern day geotechnical studies are certainly making our lives a whole lot easier.”
– Stephen Phillip Storey
EHS Head – HCI IC
As work proceeds in top gear at the Mumbai Metro, a huge issue that Michael William Sanderson, EHS – Incharge, Mumbai Metro – UGC 01 must be ever mindful off is the inadvertent weakening of existing structures or buildings adjacent to the alignment. Adjusting his helmet, Michael glances at some old, heritage-looking buildings of South Mumbai and remarks, “We are monitoring the behaviour of some of these buildings to ensure that there is no movement or weakening of their foundations due to our tunnelling and TBM activity.”
Ahmedabad is India’s first Heritage City of India as declared by UNESCO and therefore the onus on Yadavalli Vn Sarma, Project Manager, Ahmedabad Metro is even greater. “We have had to align our tunnel to keep the mandatory distance of 100 metres from heritage structures like the world-famous Relief Road Heritage Commercial Area which has resulted in many curves in our tunnel that has made both tunnel construction and loco operation inside the tunnels quite challenging.” During tunnelling, the team is constantly faced with old, long unused wells inside residential buildings that no one has any clue about.
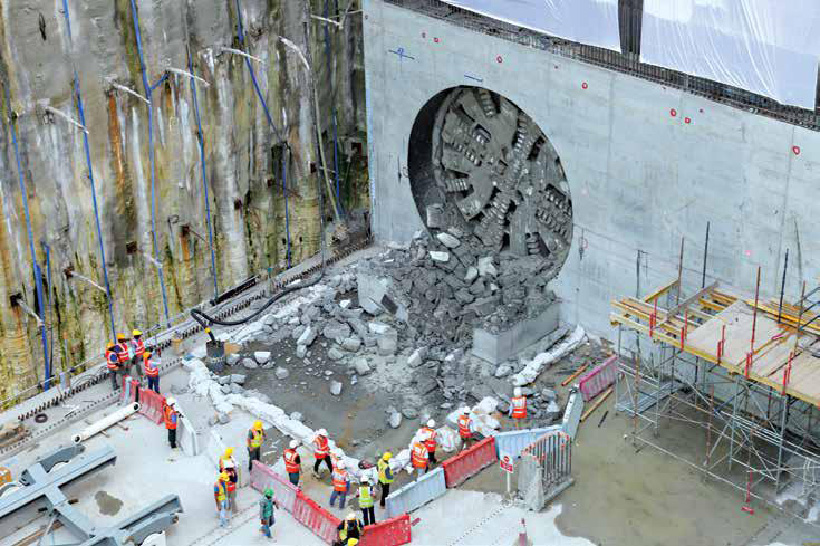
TBM (Tunnel Boring Machine) in action at Riyadh
Dust, heat, fire, TBM, confined spaces – a deadly combination
Digging, blasting, grout mixing, short concreting can all create copious amounts of dust which, if inhaled, can lead to ailments while repeated trimming, corking and working in poorly ventilated spaces can cause thermal discomfort due to the high temperatures and heat stress. “Noise, vibration, toxic fumes and gases are problems that we have to face,” says, Yadavalli, “In some cases, on this stretch, the sandy soil is so unstable that we have to be always ready to face the threat of the soil collapsing.”
“We have had to align our tunnel to keep the mandatory distance of 100 metres from heritage structures like the world-famous Relief Road Heritage Commercial Area which has resulted in many curves in our tunnel that has made both tunnel construction and loco operation inside the tunnels quite challenging.”
– Yadavalli Vn Sarma
Project Manager – Ahmedabad Metro
Workmen can easily be trapped or injured in dark tunnels or hit by loco movement while fire is another ever present danger that could be triggered by either faulty electrical installations, grouping of cables, electric motors, lighting, cables, switchgear, transformers, overheating of power units or even a short circuit in the TBM.
The TBM presents challenges as big as its size and complexity of operations. “Repairing and cleaning the TBM cutter-head or changing the cutter discs are dangerous exercises because it is very easy to slip, fall and get injured in the process,” remarks Michael, whose last words are drowned out by the din as TBM operations re-start.
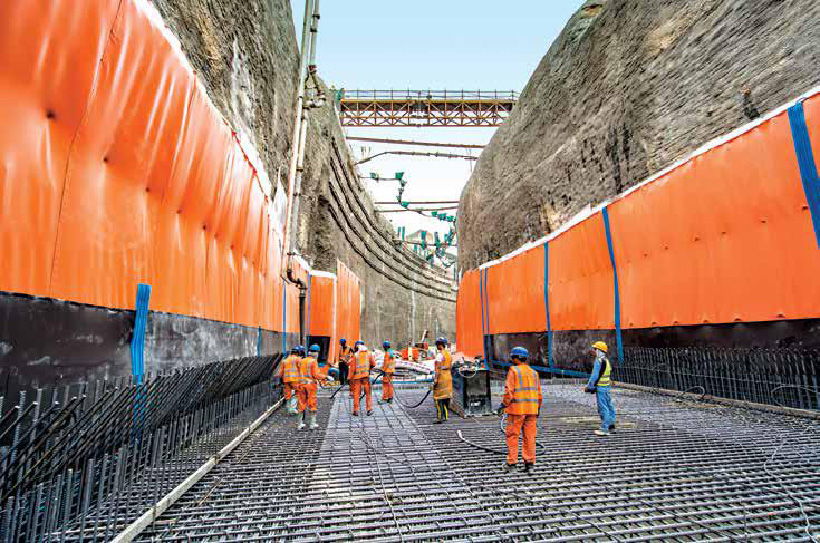
Cut and cover work in progress for underground station building
Remaining safe underground
Although the risks are many and varied, Stephen feels that proper designing, planning and caution are imperatives to keeping manpower safe underground. “The design is critical following which a competent tunnelling supervisor or engineer should prepare a method statement for the excavation of the underground services incorporating all the requirements along with a detailed sequence operation. The method of shoring must be part of the design and temporary or makeshift shoring is a definite no no!” An emergency rescue plan should be in place that is shared with the workforce and adequate number of well-marked, well-lit escape routes, fire-fighting equipment, such as extinguishers & fire reel hoses with suppression systems designed into the TBM, to quickly fight fire and prevent it from spreading and creating smoke. Regular fire drills are a must during which the emergency arrangements can be tested to ensure that they are robust and working to exit the tunnel workspace.
Safe to start:
Work in any tunnel should only start after a thorough inspection of the site and certification that all equipment is fit for use. This is an imperative especially during adverse weather conditions.
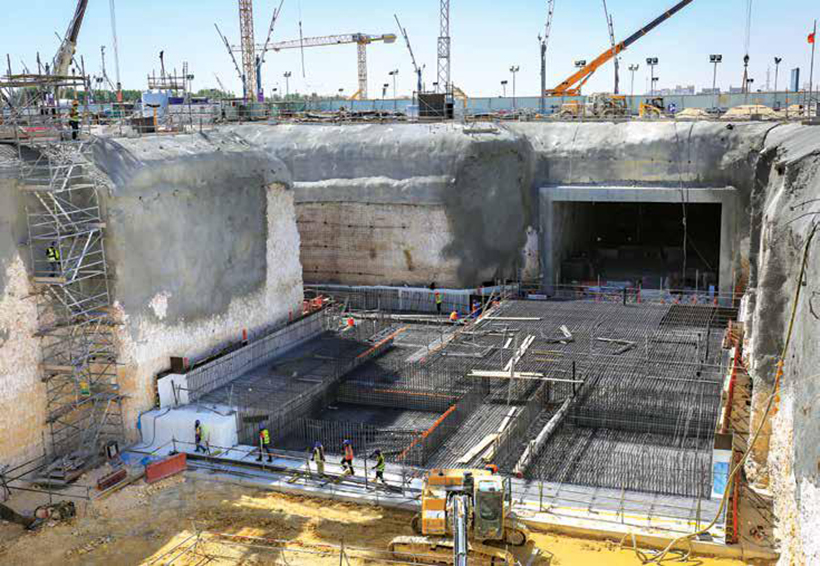
Base slab work in progress
Plan for water:
De-watering systems should be planned based on ground water table levels and soil strata; where the water pressure is high, a total dewatering method is the answer. For Michael, the Mumbai monsoons are posing some stern questions. “We have already had several spells of heavy rain and flooding, but our plans and systems have stood up to the test,” he says with a tight grin. “We require a provision for continuous dewatering pumps with standby pumps and be ever prepared for night operations,” warns Rajesh K Bhandary, EHS Incharge, Mumbai Metro – UGC 07.
The Doha Metro team relates a harrowing experience when a bore hole installed for dewatering accidentally connected with an aquifer due to soil movement releasing water at enormous speeds that inundated the entire station box to about 3 m. All the excavation equipment was lifted in the nick of time to the surface avoiding material damage. Precision drilling into the source and extensive cement grouting for three days brought the situation under control but the station depth had to be consequently reduced by 3 m that in turn affected the vertical alignment between connecting tunnels at both ends of the station forcing necessary alterations.
“We require a provision for continuous dewatering pumps with standby pumps and be ever prepared for night operations.”
– Rajesh K Bhandary
EHS In-charge, Mumbai Metro – UGC 07
Controlling noise and vibration levels:
While acoustic enclosures are provided in some equipment to control noise levels, frequently used plant, tools and equipment across projects sites are assessed for noise and then either corrective action is taken and/or warning signage posted. It is advisable for workmen exposed to continuous noise in excess of 85dB to wear hearing protection of at least SNR (sound noise reduction) +30, or more if national regulations or client requirements stipulate. Workers at risk of ‘vibration white finger’ for using jack hammers for long periods should ideally reduce such use and frequently medically checked. Apart from task rotation, normally low-vibration tools are specified during the procurement phase.
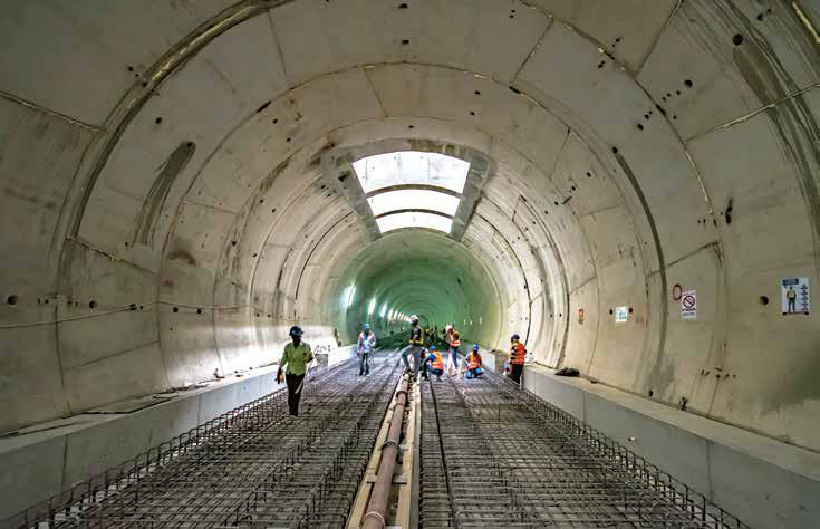
Building safe portals of connectivity
Dressed to stay safe:
In tunnels, overall protective clothing include safety helmets, safety boots, hivisibility vests, gloves, hearing protection devices & face masks are a must along with appropriate respiratory protection.
To breathe easy:
Air quality in tunnels is periodically tested with a multi gas monitor to ensure acceptable levels of oxygen, lower flammable limits, carbon monoxide, hydrogen sulphide and methane. Alarms trigger emergency procedures for all personnel who are trained to exit the tunnel quickly and safely using an Emergency Escape Breathing Device, a lifesaving appliance to escape from hazardous conditions such as fire, smoke, poisonous gases, etc. It is critical to maintain tunnel ventilation by ensuring movement of fresh air in and out of the tunnels and all carbon burning fuel plant & equipment such as generators, excavators and parked vehicles etc. are never placed adjacent to deep excavations as exhaust fumes are likely to settle in the excavation zone.
“The moment we encounter any sign of water, we have to stop, because there is no way to ascertain how big is the water accumulation. The only way forward is to dig a way around it.”
– R Anbalagan
Vice President & Head – Hydel, Tunnels, Nuclear & Special Bridges
Keeping P&M safe:
It is imperative to follow an EHS Code of Practice for the safe movement of vehicles at project sites along dedicated and well-maintained routes separate for people and vehicles. Transportation of P&M, maintenance, repairs, inspections are conducted only by competent and trained persons and there are dedicated banksmen for loco movements who are in constant radio contact with the loco driver. As far as possible, entry of vehicles into a tunnel should be avoided; ideally concrete, for example, should be pumped into the tunnel using concrete pump lines and compressor pumps. “Tunnels are usually one way IN and same way OUT which make things very challenging,” shares G Divakar, Senior Manager EHS, Heavy Civil Infrastructure, “requiring deep thinking and frequent assessment of our ‘emergency preparedness’. We have harnessed digital technology at the Tunnel Access Controller and Emergency Control Room to keep count in real time the number of people inside each tunnel.”
Burrowing into the side of a mountain
The challenges of digging into a mountain are of a different magnitude all together. “We face challenging geologies in most of our projects in the Himalayan region,” shares R Anbalagan (RA), Vice President & Head – Hydel, Tunnels, Nuclear & Special Bridges. “The Himalayas are known as the New Fold mountains that are less mature and stable when compared to other older mountain ranges like the Alps and both our major hydel projects – Punatsangshu in Bhutan and Singoli Bhatwara in Himachal Pradesh – face similar issues.”
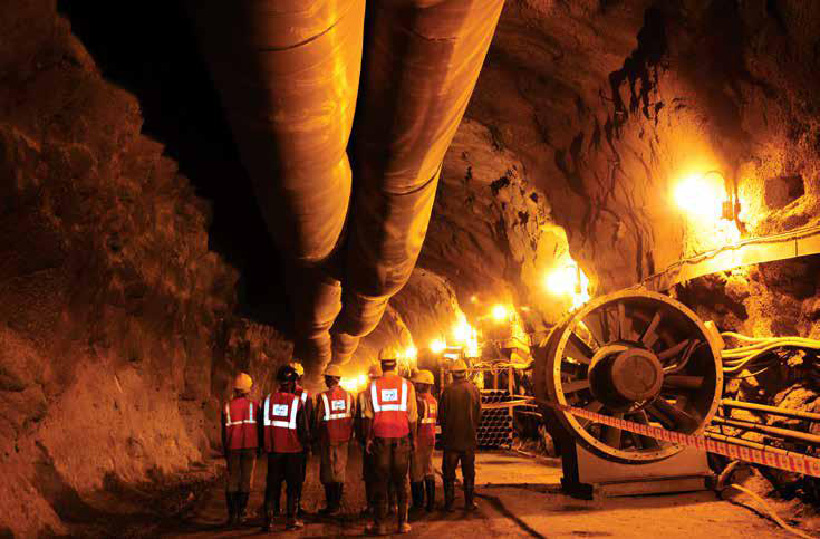
A secure underground work zone with ventilation vents and appropriate lighting
Keeping things dry:
Water is perhaps the biggest threat and project teams must be constantly on the alert for any sign of seepage when tunnelling. “The moment we encounter any sign of water, we have to stop,” cautions RA, “because there is no way to ascertain how big is the water accumulation. The only way forward is to dig a way around it.” Teams are always ready to carry out dewatering whenever required that entails the establishment of a clear de-watering system that is clearly communicated to the workmen, drivers, employees and even the client, special training for the workmen, adequate illumination in the tunnel and all arrangements for emergency rescue.
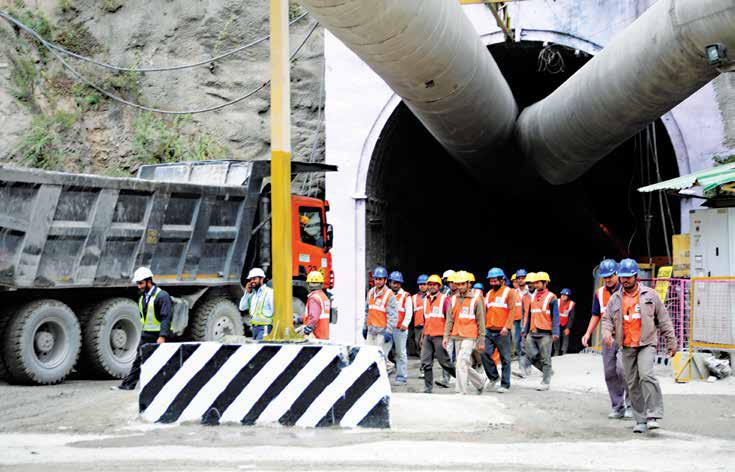
Gearing up for a safe day at work
Handling explosives:
Blasting is an unavoidable exercise in tunnelling and along with it comes the dangerous task of handling, transporting, storing, charging and using explosives which gives Arindam Maity, EHS Manager, Punatsangshu Hydel Project, sleepless nights. “Explosives have to be transported carefully in enclosed, leakproof vehicles, with double locking, properly insulated electrical wiring and driven by a licensed driver,” he says. “When handling, explosives should not be dragged, dropped, kept away from metal tools to avoid sparks and should not be handled during a thunderstorm.” The charging and blasting are carried out meticulously with proper permits and evacuation plans. “In the case of misfires, the place needs to be immediately barricaded, flushed with water and monitored till the situation is under control,” he adds.
“When handling, explosives should not be dragged, dropped, kept away from metal tools to avoid sparks and should not be handled during a thunderstorm.”
– Arindam Maity
EHS Manager – Punatsangshu Hydel Project
Geological weaknesses:
These regions are prone to natural disasters like heavy rains, earthquakes, landslides that can trigger tunnel collapses or mass sliding like experienced by the Punatsangshu team who found their concrete trusses twisted out of shape one morning. While it is impossible to plan for disasters, it pays to be well prepared which is what Arindam ensures. “We follow a tally board system, carry out emergency mock drills regularly, conduct regular surveys to check for any displacement, have inductions for all who enter the tunnel, intercoms for instant communication and wellilluminated emergency exits.”
“Yes, the dangers are many, varied and sometimes, quite unexpected,” nods Stephen, “but it is possible to overcome all these with proper planning, preparedness and a positive mindset,” he concludes.