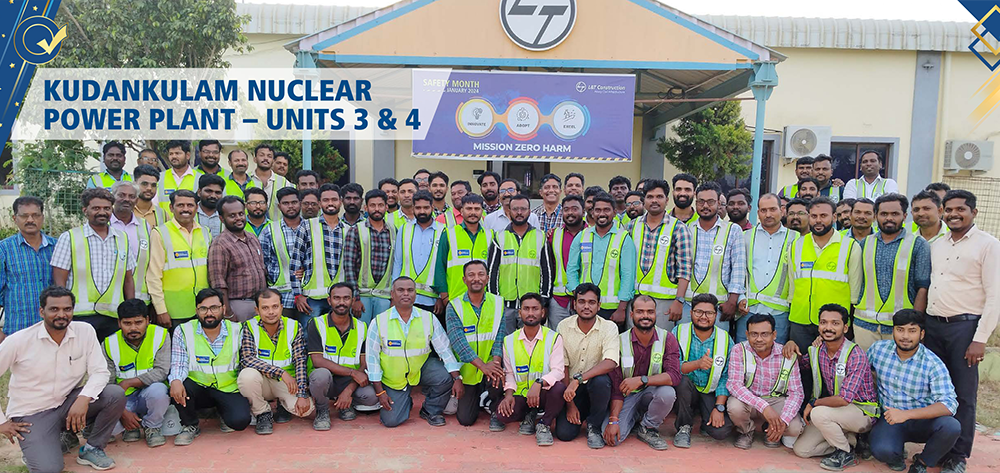
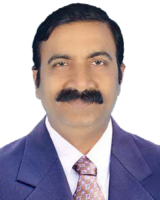
K Suresh
Project Head


One of our primary tasks was to get acquainted with the KKS coding, understand Russian standards and specifications, and manage stringent inspections and strict design tolerances.
Quality is a shared responsibility
TFL Head, S A Subramaniyan; Project Head, K Suresh; Project Manager, A Rajamanickam; and team have a tall order on their hands to build Units 3 & 4 of the Kudankulam Nuclear Power Plant (KKNPP) involving the construction of the Reactor Building, the Reactor Auxiliary Building, Turbine Building, Diesel Generator Building, and other Safety-related structures.


Constructing intricate structures in densely arranged reinforcement configurations along with positioning the critical embedded parts to support the process system leads to several interfaces, but we have made each member of our team responsible for high-quality execution and delivery.
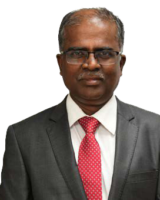
S A Subramaniyan
TFL Head
“Constructing intricate structures in densely arranged reinforcement configurations along with positioning the critical embedded parts to support the process system leads to several interfaces,” points out Subramaniyan, “but we have made each member of our team responsible for high-quality execution and delivery.” That is precisely the reason why the project has won L&T Construction’s Quality Award – 2023.
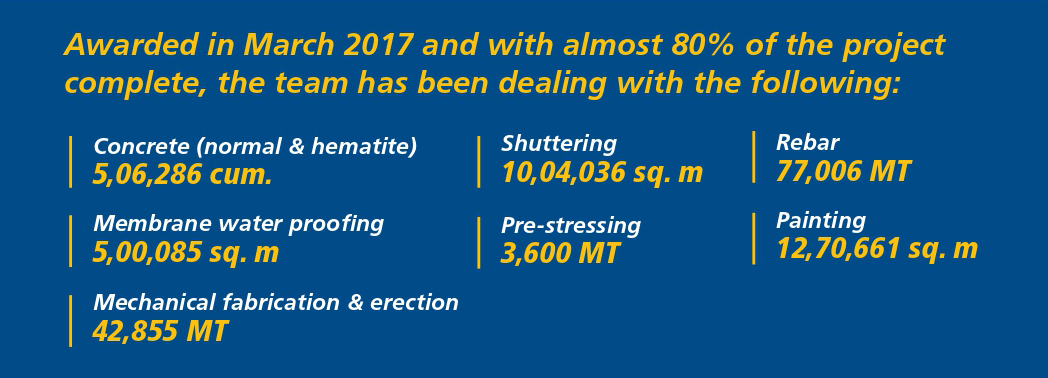
Keeping up to Russian standards
“One of our primary tasks was to get acquainted with the KKS coding, understand Russian standards and specifications, and manage stringent inspections and strict design tolerances,” remarks Suresh. His other concerns included mobilizing & retaining skilled manpower at site and quickly adopting and implementing design changes.
He is understandably proud of several ‘firsts’ that the project has to its credit, some of which, he qualifies, have not been implemented even by the Principal Designer, M/s Rosatom, of the Russia Federation at their previous projects. Concrete was poured at a height of 5.8 m for the inner containment wall in Unit 3 for the first time, a practice that has since been institutionalized. Without changing the primary design, precast methodology has been implemented in process trestles, this is again for the first time.
Concrete was poured at a height of 5.8 m for the inner containment wall in
Unit 3 for the first time, a practice that has since been institutionalized.
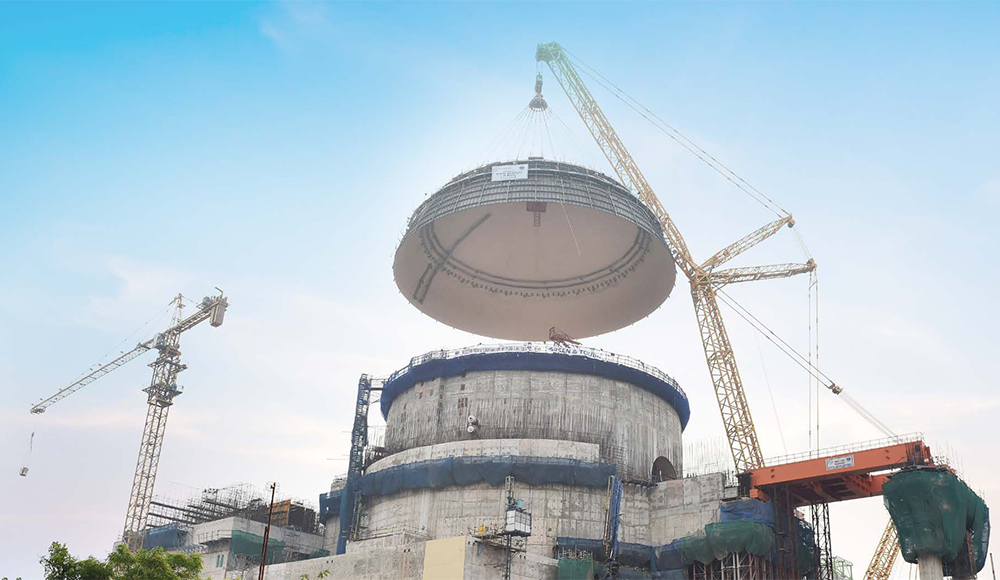
The 16 m tall Inner Containment Dome liner assembly with a diameter of 44 m and weighing 305 MT was fabricated and assembled at ground level and thereafter lifted and erected at a height of El+48m as a single unit. The 190 MT transport portal beam was fabricated & erected into position at a height of El+28m as a single unit as also was the ventilation stack of diameter 6 m & 3.2 m, height 67 m and weighing 127 MT, that was fabricated, assembled, welded, and erected into position at a height of El+33m, again as a single unit.
A proud Rajamanickam adds, “We assembled, welded, and erected critical reactor core components like the truss cantilever, dry shield with heat treatment, support, and thrust trusses, all within a stringent tolerance of 2 mm, a noteworthy achievement which was recognized and published in the World Nuclear News magazine.”
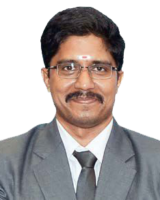
A Rajamanickam
Project Manager


We assembled, welded, and erected critical reactor core components like the truss cantilever, dry shield with heat treatment, support, and thrust trusses, all within a stringent tolerance of 2 mm. which was recognized and published in the World Nuclear News magazine.
A total of 72 polar crane brackets weighing some 310 MT have been fabricated, assembled, and successfully erected in the Reactor Buildings in both Units 3 & 4, along with intercontinental liners to the required radius and planarity, well within the tolerance as prescribed by the Russian standards. Suresh adds that the 45 m span turbine roof truss, weighing 60 MT and each assembly cumulatively weighing 300 MT was fabricated, assembled, and erected at a height of EL+39 m.
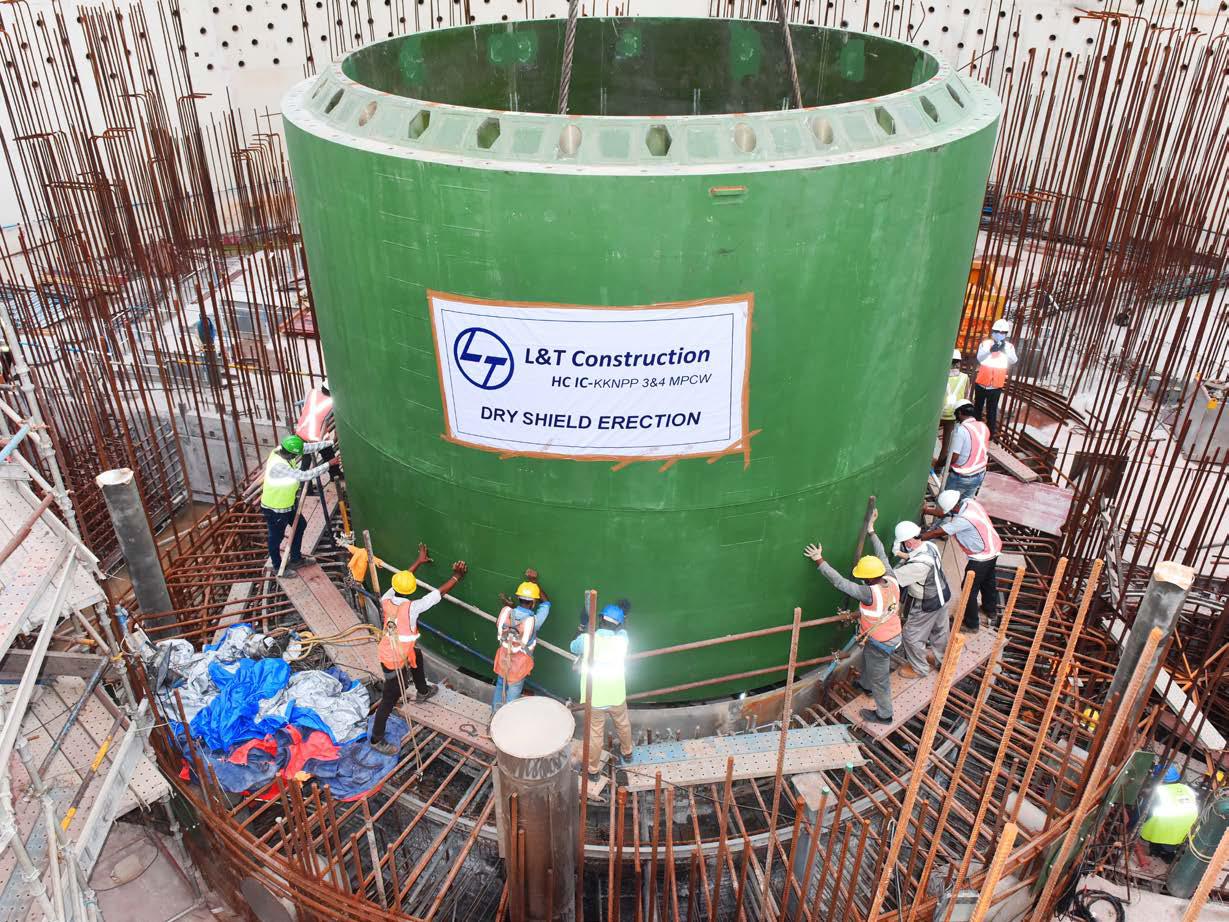
Dry Shield Erection
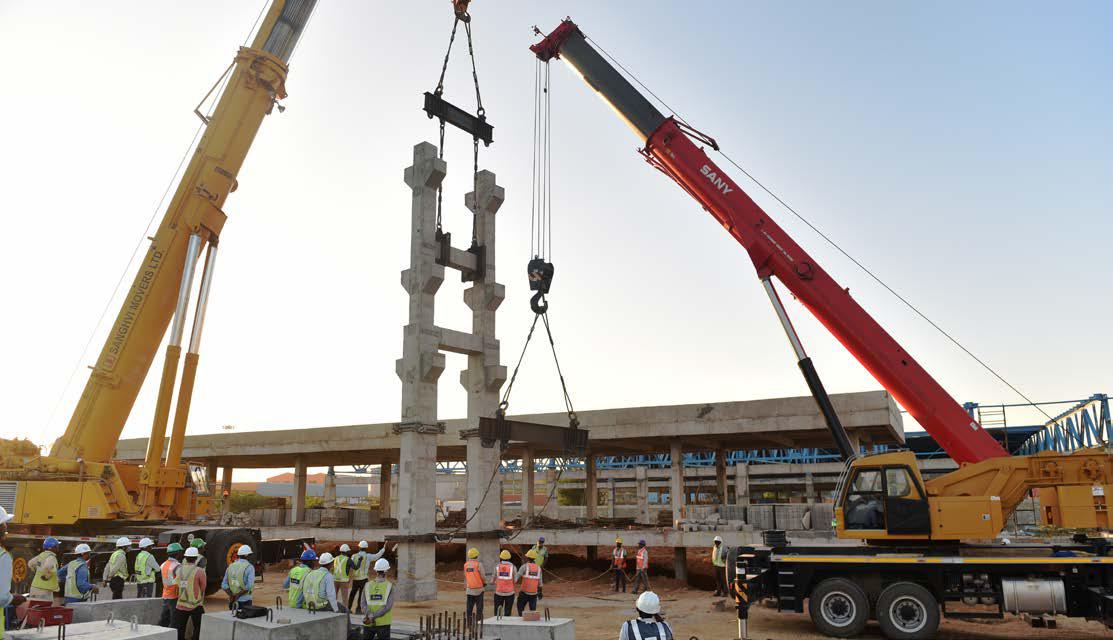
Precast Erection
Building a strong Quality culture
The task for Quality Head, S Ponnappan, has been to create and sustain a culture of getting it right the first time at every level. “To streamline construction and to ensure conformity to the highest quality standards, we prepared a detailed construction methodology right at the start that has established clear work procedures, quality plans, instructions, and JHA before commencing any new task, fostering a shared understanding within the team to align efforts with customer requirements,” he says, with a definite sense of purpose.
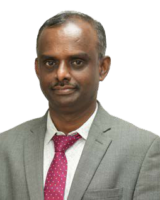
S Ponnappan
Quality Head


To streamline construction and to ensure conformity to the highest quality standards, we prepared a detailed construction methodology right at the start fostering a shared understanding within the team to align efforts with customer requirements.
Processes have been simplified to have a well-trained & authorized workforce and minimize rejection rates, while jobspecific training to workmen & employees incorporate practical demonstrations to enhance their skills and overall productivity. Regular mock-ups for critical works and finishing activities are conducted to set benchmarks and maintain excellence in processes. “At all stages, and especially for final inspections, we actively involve QA/QC personnel to conduct root-cause analyses and implement corrective actions based on internal inspection findings,” Ponnappan affirms.
It would have been extremely surprising if this project team had not won the L&T Construction Quality Award – 2023 considering their all-round and all-out effort to drive Quality. Congratulations!