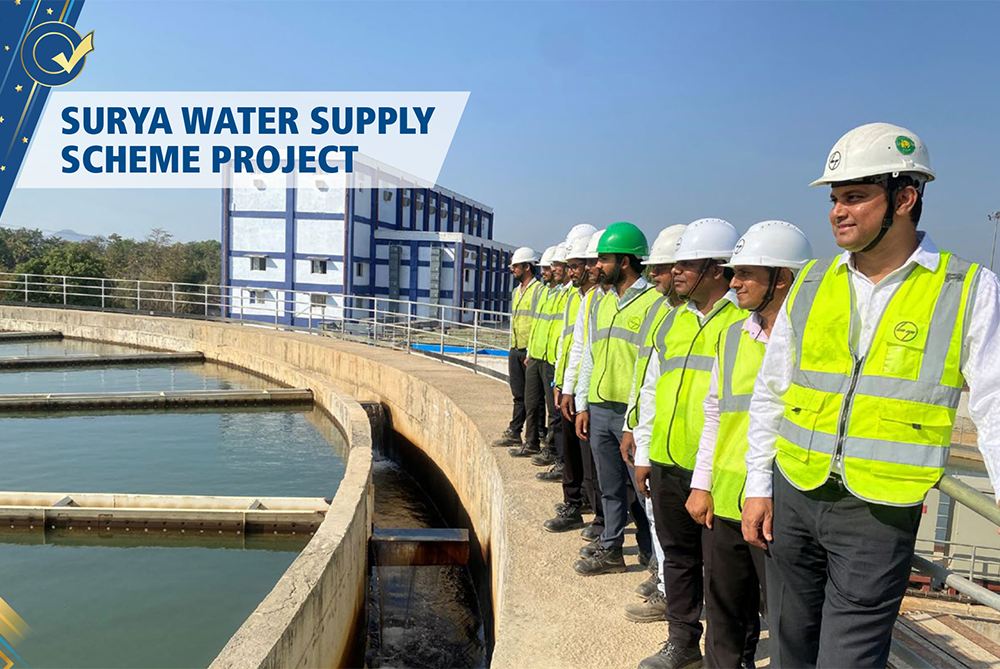
Where Quality is a success mantra
Project Director, Colin Nonis, and team at the Surya Water Supply scheme have achieved a Grand Prix, as it were, winning both L&T Construction’s Safety & Quality Awards 2023. It is the first time a project has managed to do so since the Awards were instituted. “Our comprehensive quality assurance plans are aligned to client requirements and industry standards that include outlining quality objectives, procedures, and responsibilities,” says Colin, putting context to his team’s pursuit of excellence in Quality.


Our comprehensive quality assurance plans are aligned to client requirements and industry standards that include outlining quality objectives, procedures, and responsibilities.
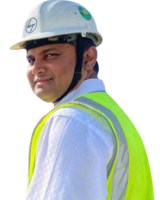
Colin Nonis
Project Director
Quality is all-encompassing that impacts everything including rigorous assessment and qualification of vendors and suppliers for high-quality materials, standardized procedures & workflows to ensure consistency and repeatability in pipe laying activities, regular audits and assessments to monitor compliance with QA standards, fastidious processes during tunnelling, the works.
“Proactive identification, assessment, and mitigation of project risks prevent quality issues and delays,” remarks Quality In-Charge, Muralidharan S “while regular reviews and analysis of project performance data help us to identify areas for improvement, fostering a culture of continuous improvement.” Effective communication channels established with stakeholders ensure alignment of expectations and prompt resolution of quality-related issues.
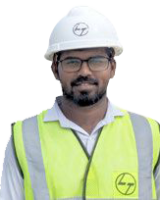
Muralidharan S
Quality In-Charge


The Request for Inspection (RFI) process is a significant leap in our quality control practices, that has dramatically improved our inspection request management and efficiency. Automated data capture has improved accuracy, minimized errors, and made the inspection data more reliable.
Quality fuelled by digitalization
The team’s quality agenda is being powered by digital tools and Muralidharan informs that the Request for Inspection (RFI) process has been digitalized using the Perform Flow Addon since the inception of the project. “This strategic initiative is a significant leap in our quality control practices, that has dramatically improved our inspection request management and efficiency,” he says. They have transitioned from paper-based forms to digital platforms, workflow management is smoother, and turnaround times quicker. “Automated data capture has improved accuracy, minimized errors, and made the inspection data more reliable,” he adds, apart from better collaboration amongst the various stakeholders. “With real-time visibility into the status of inspection requests, teams can now align their efforts resulting in project cohesion, better communication, more prompt decision-making, and problem resolution,” smiles Colin.
Ensuring quality in the supply chain
For a quality project, all the stakeholders have to espouse it with the same verve and a vital link in the chain is supply chain and the team has instituted a rigorous evaluation & selection process. Potential suppliers are evaluated and assessed against predefined criteria such as quality certifications, manufacturing capabilities, and past performance, followed by a rigorous qualification process, that involves audits, evaluation of their quality systems, and inspection of samples. Comprehensive quality agreements are then drawn up that clearly delineate quality requirements, responsibilities, and performance benchmarks. The team regularly monitors & assesses their processes using performance metrics, statistical analyses, and on-site evaluations. Nonconformance attracts swift corrective & preventive actions.
All incoming components are meticulously inspected and tested to validate adherence to established specifications and standards and suppliers are mandated to institute robust process control measures.
The performance of the suppliers is periodically evaluated based on predefined criteria of quality, delivery timeliness, responsiveness, and dependability. Performance metrics and scorecards serve as objective tools to gauge performance, identify strengths, and pinpoint areas for improvement. “Our Supplier Quality Assurance Plan serves as a roadmap to maintain quality standards and reliability,” remarks Colin.
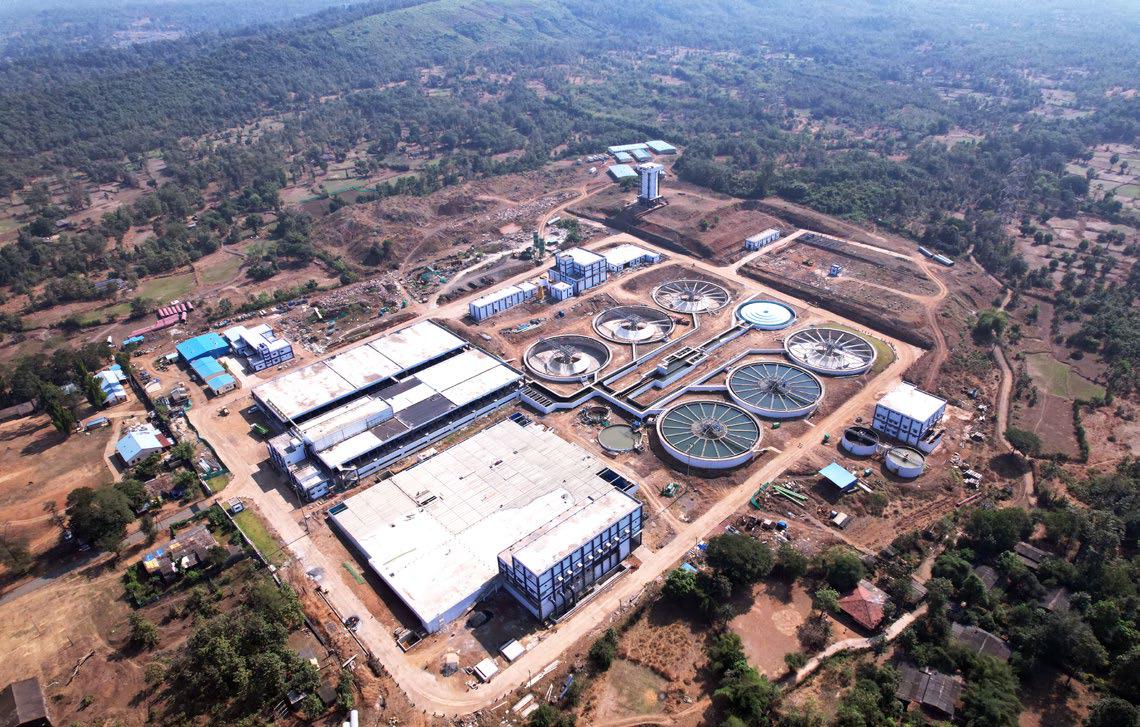
Ensuring quality in MS pipe laying
With mild steel (MS) pipelaying works a critical activity, the project team’s robust Quality Assurance/Quality Control (QA/QC) program covers various stages of the process including bedding, compaction, fit-up, welding, inspection, coating application, backfilling, and hydrotesting.
Before laying the MS pipes, the bedding material is thoroughly inspected to ensure uniformity and compatibility with the pipeline. Sieved material with a particle size of 10 mm is utilized to ensure proper support and alignment, facilitated by a sieving bucket attached to an excavator, that has improved productivity and reduced project timelines. Bedding material is compacted using Baby Rollers to achieve the required density and stability. Extra care is taken to ensure proper alignment and joint integrity during the fit-up of the MS pipes. Welding is performed by qualified welders and the joints are visually inspected prior to welding. All weld joints are ultrasonically tested to ensure weld quality, and select welds, are even radiographic tested, then heat shrinkage coated to ward off corrosion and preserve insulation.
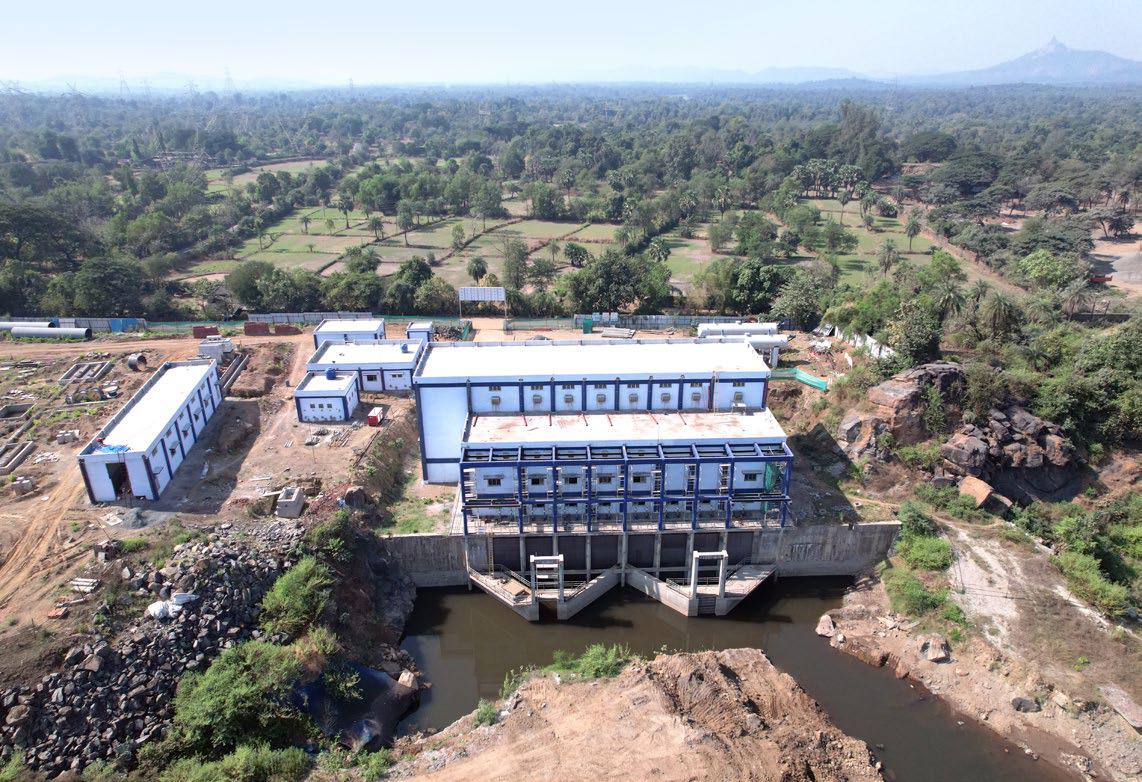
Ensuring quality during cement mortar lining
The cement, aggregates, and water are first thoroughly inspected and then mixed in the approved proportions for consistency and homogeneity of the mortar mixture which is then applied ensuring proper thickness, coverage, and compaction, before which the surface is prepared to receive it. The thickness of the applied mortar lining is regularly measured to maintain uniformity and meet design requirements, The work is finally visually inspected for cracks, voids, or delamination. The entire process is meticulously documented.
Ensuring quality during tunnelling
Tunnelling was being done for the first time in WET IC that called for extra vigilance and care to complete the two tunnels safely and to quality. It began with comprehensive geotechnical investigations using techniques such as borehole drilling, geophysical surveys, and laboratory testing to accurately characterize the ground properties. “When precasting the segments, we carefully monitored the concrete mix design, casting moulds, reinforcement placement, and curing conditions to achieve the desired strength and durability,” remarks Muralidharan. Regular inspections and testing of precast segments ensured dimensional accuracy, concrete quality, and surface finish.
Precast segment erection was another critical activity during which the team had to take care of alignment, orientation, and support of precast segments within the tunnel bore.
The segment joint profiles, gasket placements, and grout pockets were verified, and precision measurement tools helped maintain alignment tolerances and prevent misalignments. During grouting, grout mix proportions, injection pressures, flow rates, and distribution patterns were closely monitored. Again, everything is captured and documented.
“We have implemented a Project Quality Index for a comprehensive measure of project quality across various parameters,” sums up Colin, “that involves quantifiable metrics and evaluation criteria to assess the quality of project deliverables, processes, and outcomes.”