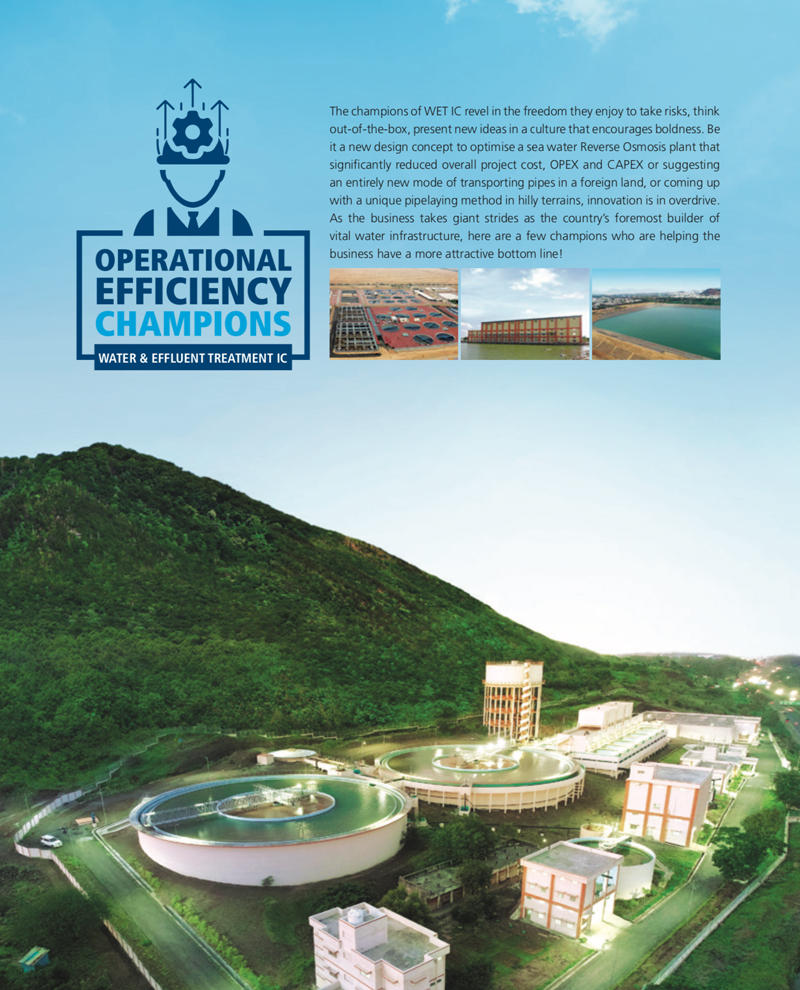
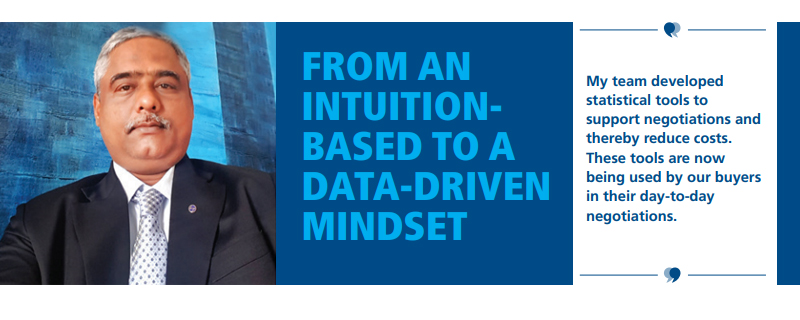
P Jaganathan,
Senior DGM – Mechanical, SCM, WET IC
Supply Chain Management (SCM) plays as important a role as any other function in the world of project management and P Jaganathan’s primary objective is, as he states, “to improve the efficiency of the supply chain to support our water business.” An import from MMH SBG where he was part of ‘Operation Excel’, Jaganathan feels that one of his main tasks is to convert his mates at SCM to move from “an intuition-based mindset to one that is data-driven. This is important,” he stresses, “because everything depends on one’s mindset to accept the new.”
In a competitive scenario, Jaganathan’s mandate was to maintain the double-digit margins of the business and, to begin with, he had to overcome some major roadblocks. “There were several delays in ordering, supplies and there was huge pressure on costs.” The usual challenges for a SCM professional, one might say.
Wasting no time, Jaganathan rolled up his sleeves and got to work with a series of steps to address these issues. “Firstly, by adopting a systematic approach to procurement, we were able to reduce the ordering time,” he shares, warming up to a subject that is obviously close to his heart. By identifying the issues they were facing in their functioning, Jaganathan and his team provided inputs to the digital team to develop a comprehensive digital solution in the form of a material supply tracker. “My team developed statistical tools to support negotiations and thereby reduce costs. These tools are now being used by our buyers in their day-to-day negotiations,” he says, with a sense of achievement.
“We have developed a standalone file management system, loaded on EIP Vidhya, that helps balance workloads among buyers. There is an in-built cut off time for files based on age to trigger immediate attention,” he briefs further mentioning that “there are category specific estimation templates too based on statistical data.”
For a person who’s entire work depends on systems and procedures, he advocates that these should be simplified at L&T, “without losing the intended controls,” he is quick to add and believes that operational efficiency is being driven by the bright, young minds at L&T Construction.
On his personal front, Jaganathan’s native place is Chennai. “My wife, J Sumithra, is a homemaker and we have one daughter, J Varshini,” he shares with an obvious softening of his features. “I love visiting temples during my free time, and I recall with a lot of love the time I spent with my father,” he says about his most memorable moments.
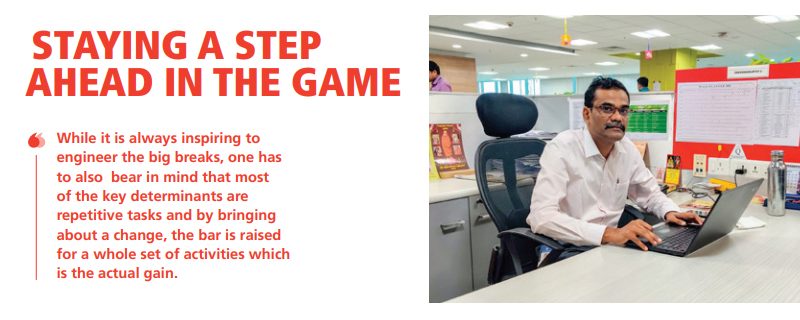
V. Dakshinamurthy,
In-charge, Operations Support, WET IC
Engineering innovative methods and processes to drive timely delivery across projects keeps V. Dakshinamurthy, In-charge, Operations Support for Wastewater BU, a step ahead in the game. “Strategizing is always a fulfilling exercise as it is all about enhancing quality, safety and fast-tracking project execution,” mentions Dakshinamurthy. “At WET IC, we have engineered some amazing breakthroughs that have redefined project management. Take for instance, the Dusk to Dawn construction method, more popularly known as D2D, the brainchild of WW BUH, that has bridged a 3 to 28-day activity to merely a 12-hour job.”
Achieving operational efficiency is a two-pronged approach for Dakshinamurthy, “While it is always inspiring to engineer the big breaks, one has to also bear in mind that most of the key determinants are repetitive tasks and by bringing about a change, the bar is raised for a whole set of activities which is the actual gain.” D2D is a step in this direction, he affirms, “Initially we started with a 100 m stretch at Jhunjhunu in Rajasthan with various digital and process improvement techniques amalgamated including a remotely operated time lapse camera for real time monitoring and laser level monitoring with a Geo-tag enabled GIS App.” Recounting the milestone in a feverish tone, he says, “For all of us, October 3, 2019, is a special day as we rolled out this initiative which had its own natural flavour with a 90 minute rain delay,” but he assures, “We finished well in time before 8 am the next morning and it was a proud moment for the entire project team with overwhelming appreciation from the locals as they were surprised to see their roads in as was is condition.”
Through digitalization we have enhanced operational efficiency several notches as site progress monitoring has become real-time with impactful intervention, shares Dakshinamurthy, “Initiatives such as the development of pneumatic tubular formwork for cast-in-situ construction of top cover slabs of RCC drains at the Vijayawada Storm Water Drainage project, standardization of precast elements for chambers, development of centralized issue register dashboards have all radically transformed the way we work at projects.” Going ahead, he affirms, “I would like to establish a swifter AI enabled approval system integrating machine learning with artificial neural network for faster clearance of work and purchase orders by evaluating details from our vast information bank.”
The last 17 years at L&T have been extremely satisfying for Dakshinamurthy and looking back he recounts, “I still vividly remember telling the interview panel in 2003 that L&T is my dream company and I’m here to make a mark. When I successfully completed 15 years in 2018 and received the long service award from our IC Head that was my moment of pride.”
Dakshinamurthy’s hometown is Thirunallar in Puducherry where his heart is too. But he along with his wife Jayanthi and daughters Priyadarshini and Sharunethra have made Chennai their second home.
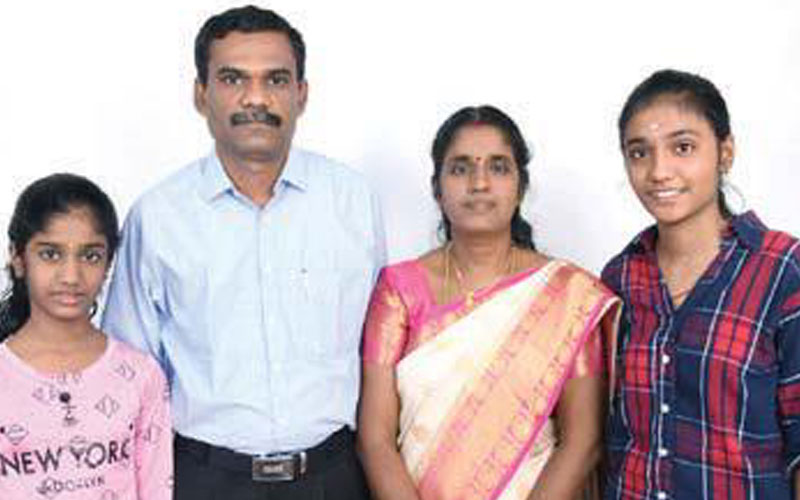
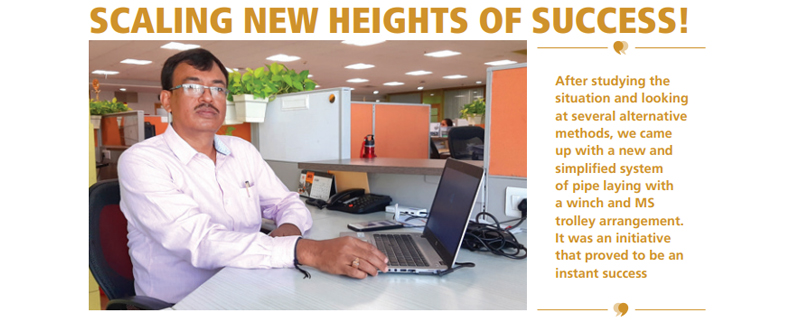
- Gopal Krishna Roy
Senior Manager – Mechanical (P&M), WET IC
At the Alirajpur site, Gopal Krishna Roy, or GKR for short, was facing an uphill problem. “We were tasked to lay 6 m long pipes of 2.8 m diameter from Pump House‑1 to Pump House‑2 in a difficult hilly terrain,” he scopes his problem. “We were facing three dimensional slopes where our conventional method of pipe laying was not possible. After studying the situation and looking at several alternative methods, we came up with a new and simplified system of pipe laying with a winch and MS trolley arrangement. It was an initiative that proved to be an instant success,” a winning smile writ large on his face.
“We were able to speed up the work and complete a long pending, unfinished task. The best thing,” he adds, “is that with its successful implementation at our site, other sites in our IC have the confidence to adopt our method to lay pipes efficiently especially in hilly terrains.” He points out that the method had another advantage of increasing safety of the workmen because they did not have to use heavy cranes. “In fact, by not having to use heavy cranes we significantly saved costs for the project too.”
Presently working at HQ as BU-Plant Manager for IWS BU, GKR has seen a lot of action at various projects during his tenure with L&T Construction including the Vizag Vijaywada Pipe Line, HPCL DHDS-Vizag, Cyber Gateway Hyderabad, Vijaywada fly over Project, Sri Satya Sai Telugu Ganga Project, Jindal Dam Raigarh, Velegonda dam, NTPC Simhadri, BF‑8 and SP3 Bhilai and the Hot Strip Mill at Rourkela. Looking back at his long association with L&T, he says, “the major challenges that we have often faced at sites are to mobilize the required assets in the required time especially in remote locations with the right kind of skilled manpower.”
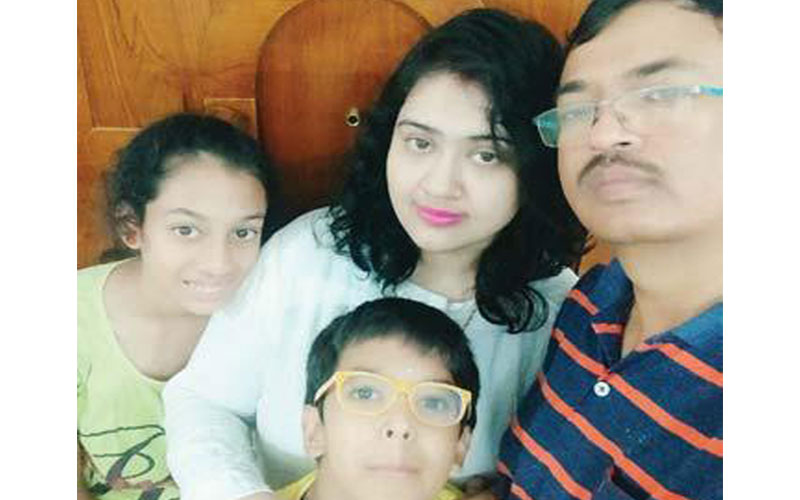
Apart from the elation of having discovered a new pipe-laying method for hilly terrains, GKR takes pleasure from other personal ‘highs’ at work. “At the HPCL DHDS site, the erection of the 300 T DHDS reactor with a 315 T capacity crane with ringer was a great success,” he shares radiantly, “as also was our erection of a 110 T BF raiser pipe top piece with a 600 T crawler crane with luffing at the BF8 project in Bhilai.”
Hailing for Kolkata, West Bengal, GKR’s better half, Irin Roy, is a homemaker and the couple are blessed with two children, 13-year-old Anushka, who is in her 7th standard and son, Rajdeep who is in his 3rd. A lover of reading and chess, GKR believes that “digitalization is enhancing our operational efficiency at L&T Construction.”
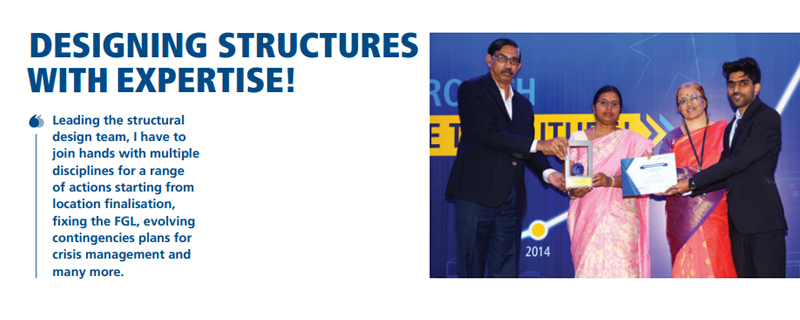
J Sakthi Chitra,
Senior Engineering Manager — EDRC, WET IC
Ever since J Sakthi Chitra began her association with L&T in 2005, armed with a post-graduation in structural engineering, as a Design Engineer in the Bulk Material Handling Unit, she has enjoyed rich, varied exposure across business segments helping her to hone her designing skills. “From 2005 till 2015, I grew to the level of Engineering Manager handling end-to end responsibility of tenders and operating jobs, basic to detail structural engineering of projects.” With this strong foundation in designing industrial projects, she took up designing material handling structures first for the TANCEM Cement plant and then a few other cement plant tenders and even contributed to a few residential projects during her tenure at B&F IC. “Since 2017, I have been a Section Head, WET ILWS BU EDRC- Civil, associated with several lift irrigation projects across different geographical areas.”
Joining the Irrigation team was both a major milestone for her and a challenge. “I was new to the field but with fruitful inputs from functional experts, department seniors and the support of my team members, I was able to perform well.”
There are several challenges in constructing an intake pump house, Sakthi explains. “Deep underground excavations, proximity to a reservoir / river, or a forest leads to issues of access, safety and land acquisition. Leading the structural design team, I have to join hands with multiple disciplines for a range of actions starting from location finalisation, fixing the FGL, evolving contingencies plans for crisis management and many more.” Driven by her passion for basic structural design DNA, Sakthi’s focuses on several OPEX initiatives: BIM implementation, standardisation & customization of design & detailing components for first time release & quick revision and complete transformation in design of deep Intake pump house with a novel alternative to the conventional U/G framed substructure by stable simple long overhang wall/deep beam.
“Detailing of all pump houses in Revit takes care of future interface issues,” says Sakthi. “We have explored RCDC for the first time in WET IC for superior design and detailing of structural elements as part of automation to increase the productivity.” Her team’s optimization effort to design the Ground Bunker Shed for the NCL Block‑B project received the NMR-2014 award in the AA category. “I thank the Operations team, Project Director and the management for their fullest support, motivation and for empowering me and my team to implement our new ideas,” says a visibly moved Sakthi.
Currently pursuing a doctorate in structural engineering from IIT, Madras, Sakthi also runs her family. Her husband, K Senthilvelu — Nanotechnologist, works for an Automobile OEM and the couple are blessed with two children, son, Kavinesh and daughter, Mohitakalai. She has a long list of moments that are memorable, top of pops among them being the birth of her son & daughter and her team winning the Best Innovation Award in WET EDRC — 2020.
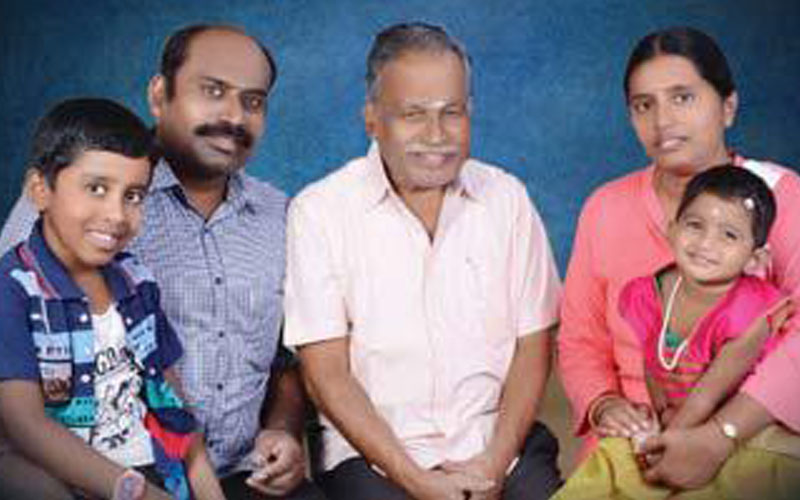
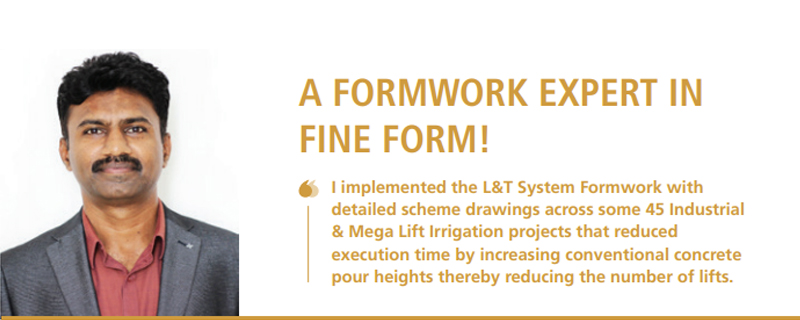
- N Subramanian
Senior Construction Manager — Civil,
Industrial & Large Water Systems BU, WET IC
“I am responsible and accountable, as an owner, for the formwork operations of the Industrial & Large Water Systems BU, WET IC,” declares N Subramanian, very seriously adding that during a 3‑year stint with MMH SBG, “I was a Core Team Leader of ‘Project ETA — an Operational Excellence Program’ along with consulting partner Accenture, aimed to improve operations through standardization, streamlining and innovation to deliver an enhanced bottomline.” His ambit of responsibilities included implementing and institutionalizing OPEXCEL initiatives across projects to ensure targeted outcomes & benefits and design new initiatives to reduce costs, optimize execution timelines and improve quality of execution.
With this rich background, Subramanian is now lending his expertise to his BU and proudly shares, “I implemented the L&T System Formwork with detailed scheme drawings across some 45 Industrial & Mega Lift Irrigation projects that reduced execution time by increasing conventional concrete pour heights thereby reducing the number of lifts.” He shares his knowledge through theoretical and practical sessions on the L&T System Formwork to his colleagues across WET IC, with an average effectiveness rating of >95%. “I have introduced operational efficiency in formwork by ensuring identification, usage, safe erection & dismantling of System Formwork components especially among our frontline employees.”
Subramanian has more triumphs to share about his OPEX initiatives. “I introduced in the WET IC a higher concrete pour / lift height of 3.6 m for RCC walls & 5.4 m for columns that enabled speedy execution, ensuring safety and quality standards. I also initiated the execution of reinforced cement concrete delivery chambers, break pressure tanks and raw water sump structures using the Slipform technique, again for the first time in WET IC, that saved us execution time of such water retaining structures without construction joints and without compromising on safety.” Almost predictably, he mentions initiating the preparation of Formwork Schemes in 3D Model (BIM) for quick and correct understanding of schemes, accurate detailing and multi-dimensional views to understand execution steps.
Being selected to the OPEXCEL team was one of the highpoints in Subramanian’s career as was the appreciation he received from personnel at KPMG for developing an ATL Course on L&T Formwork and for initiatives undertaken to transform WET IC’s formwork operations, “but nothing can describe my feeling when I held my new-born daughter for the first time.” He calls his daughter, Shashini as his “princess’ and son, Shaarav as his “prince.” His better half is Sivagami, whom Subramanian describes as, “a home maker and an entrepreneur!”
“The freedom we have to express our views, execute and take decisions to achieve our business goals, the continuous training and development and our data-driven culture is what is working well for L&T Construction,” he sums up with total conviction.
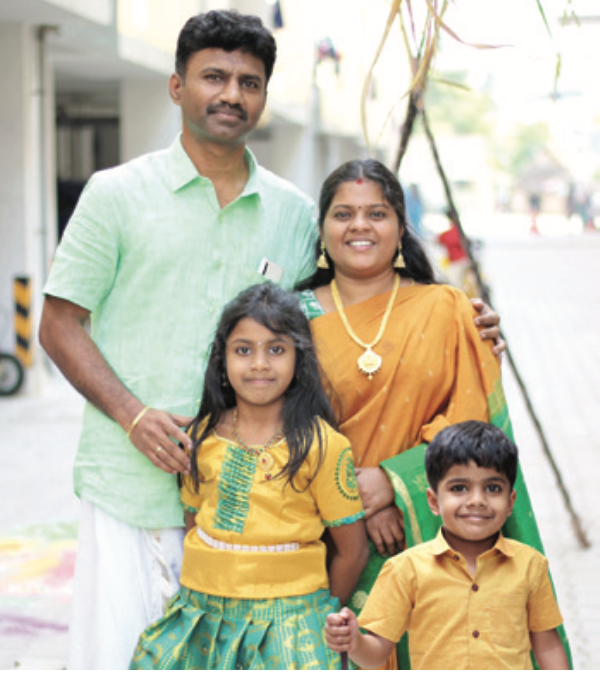
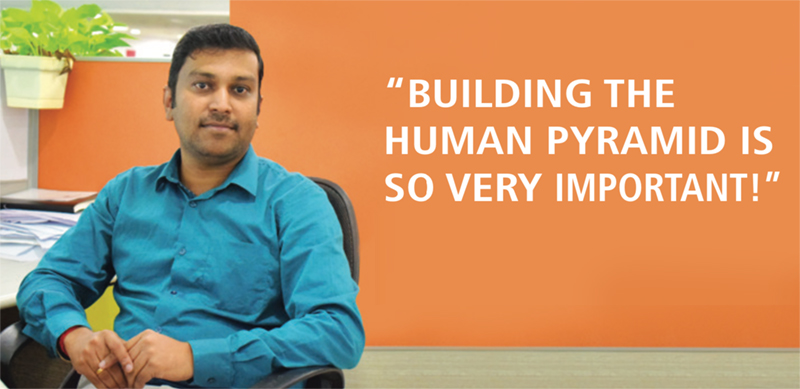
- S Prem Anand
Sr. Engineering Manager — Process, WET IC
Given the changing environment that is increasingly getting more challenging, S Prem Anand believes that L&T is at the top, “thanks largely to our well-established systems, the decision making of the management, the organizational set up, financial stability and brand value that is enhancing our operational efficiency.” However, he advocates a fairer rating system as in construction individuals cannot achieve much by themselves, it is always teamwork that triumphs. “A human pyramid is very important for success but when creating it to achieve our target everyone should have the same goal or else the pyramid will collapse.”
After a stint with a L&T Hydrocarbon offshore project for design and engineering work, Prem has been involved with a slew of WET projects across India including the 150 MLD Plant Water System for 2x800 MW Yermarus Thermal Power Station, Raichur, Karnataka, the 40 MLD CETP project at Ludhiana, the 216 MLD Makeup & Drinking water system for NMDC Limited, two CETP projects in Ahmedabad and Dholera (Effluent Recycle Plant) and the 20 MLD low salinity water package for ONGC. Presently, Prem is working on the 100 MLD Sea Water Reverse Osmosis desalination plant project in Dahej, Gujarat. “As most industrial process plants are unique in nature and since clients always require us to use new technologies, it was very challenging in the beginning when I joined L&T to introduce new technologies without benchmarks but with benchmarks and references it is much easier now,” he smiles. “At my present project, we optimized the sea water reverse osmosis system that helped to reduce the brackishness in the water, improved its pre-treatment and reduce overall operation cost.”

“Based on the site execution plan, receiving approvals for our drawings with 90% accuracy with our data base and 3D models minimizing rework at site based on the vendor’s input,” Prem flags off as standout achievements.” On the digital front, he mentions, “for designing the membrane system design we use WAVE, Hydranautics IMS Design, CADIX, TORAY, INGE Design and the 3D modelling software for ROs, ERDs, pumps and other equipment.”
Anand’s better half, Sheebha S P, is a homemaker, looking after their home and two children, daughter, Anshika and son, Anshiv. “I spend my free time watching movies, reading books and of course, with my children,” he shares, recalling a trip to Denmark as a memorable one.
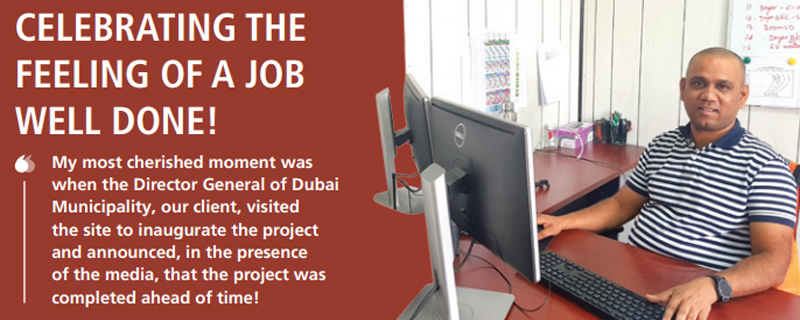
- Sabapathy Raja
Senior Construction Manager – Mechanical, WET IC
As the Process Engineering Manager of the Jebel Ali Sewage Treatment Plant (STP) (Phase 2) project, Sabapathy Raja is an extremely happy man having delivered a difficult project in a foreign land to the complete satisfaction of the client. “My most cherished moment was when the Director General of Dubai Municipality, our client, visited the site to inaugurate the project and announced, in the presence of the media, that the project was completed ahead of time!” Though his sense of achievement is obvious he is quick to admit that it wasn’t easy. “Working in a 50:50 JV environment was new for us, so we had to understand our partners’ working procedures. Civil work started from Day‑1 and it was challenging to meet the engineering demand right from identifying the resources, understanding needs of the civil team and handling the engineering and procurement with 14 engineers.”
Fresh from his previous assignments as Lead Process Engineer at the two Doha STP projects (including expansion), Sabapathy completed the automation logic testing of the entire Jebel Ali plant single-handedly and adds, “even during the operation phase, the treated effluent guaranteed parameters were met to avoid penalty, that were really tough during wet weather conditions.”
To improve operational efficiencies at site, Sabapathy mentions the adoption of the Site Document Management System as a single window for all document flow and the Kanban Card to control supply chain management. “In addition, we placed the Last Planner System, a lean construction tool, at critical zones to monitor execution of work inline with the baseline schedule.”
“As a process engineer, I conducted process design verifications through simulation model techniques that proved that the effluent parameters defined in the contract could only be guaranteed under certain treatment regimes thus displaying the pitfalls in the design assumptions in the contract. A major risk was mitigated, and improved the plant’s process efficiency.” Skill based resource planning during the engineering phase enabled the team “to manage and complete the entire plant engineering (MEICA) and procurement activities efficiently with lean organisation in line with the baseline schedule.” About digital solutions adopted at site, Sabapathy flags off a model-based (GPSx and BioWin) simulation technique to control, optimize and manage waste water treatment plants, LiDAR to map all water-retaining structures, a bar-coding system to track material, an integrated Project Management Office and “an Oracle-based computerized Maintenance Management System to conduct plant maintenance activities, plan, record, monitor and control maintenance activities.”
Sabapathy loves gardening during his free time, “whenever time permits,” he says with a laugh. Hailing from Karaikal, Puducherry, his wife, Brindha, is a homemaker and they are blessed with a daughter, Kamalini.
In parting, Sabapathy’s advice is for, “more emphasis on timely completion and employees should realize the value of time.”
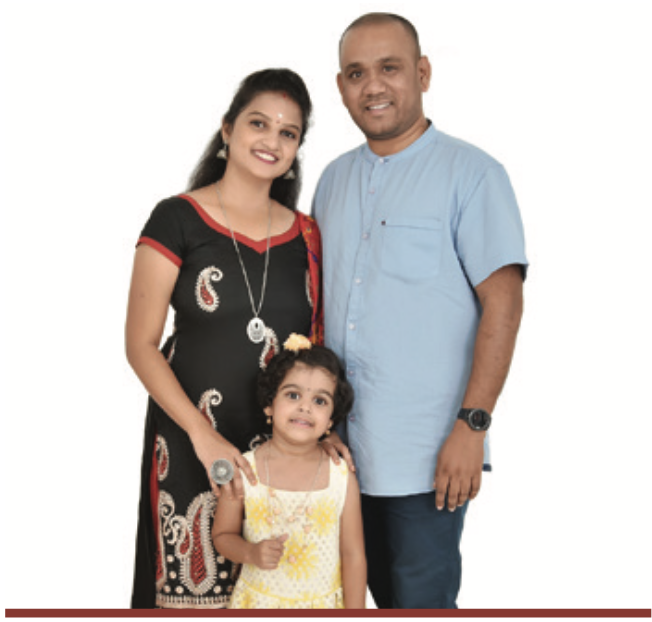
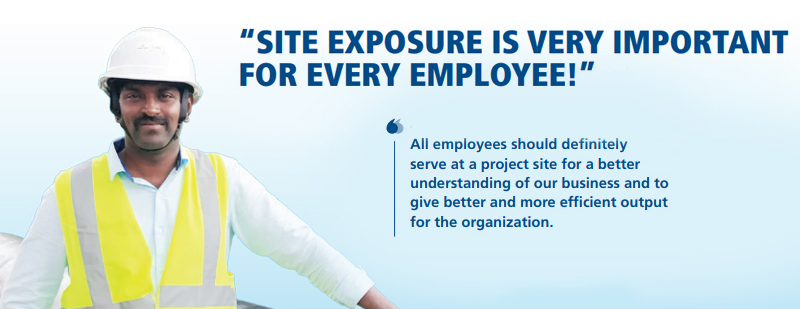
V Murali Anand,
Manager – Mechanical, QA/QC, WET IC
After handling suppliers’ plant inspection & evaluation and material inspection at the Kolkata Cluster Office, V Murali Anand is having his first taste of project life at L&T’s first in Tanzania and his experience has been so impactful that he sincerely advocates that “all employees should definitely serve at a project site for a better understanding of our business and to give better and more efficient output for the organization.” Murali’s project is aiming to provide a water lifeline to the central region of Tanzania called ‘Tabora’ by constructing water lines, distribution lines and a host of other vital water infrastructure.
In an alien land, it took time for Murali and team to first understand its unique challenges and find innovative ways to overcome them. “Initially, we followed our conventional pipe laying method but soon found the going tough,” he says. “Due to a low water table, water kept accumulating in our trenches and the need to repeatedly de-water was both time-consuming and delaying progress. There was also the danger of soil collapses.” The team was forced to additionally excavate up to 100 m for fit-up and pipe welding and moreover, the conventional method called for skilled fitters and welders too who were, not surprisingly, in short supply.
“We had to think out of the box, and came up with the S‑laying method that is normally used in offshore projects using pipes with diameters ranging from 150 mm to 300 mm,” shares Murali. “To start with, we explained the method to our site engineers, supervisors and fitters after which we procured materials for the same such as chain pulleys, lifting belts, supporting bars & fabricated A‑block structures. Then, we arranged a mock-up of the pipe laying operation for the consultant and client and it was only after its success that we started to implement this method.” The benefits of the S‑laying method were many. “It reduced the additional excavation for weld pits, we could make do by only engaging lifting equipment for pipe stringing, workmen time was utilized to the maximum cutting out idling and there was no space constraint to work. All in all, we reduced pipe laying time by 50%!”
Having tasted such success with this method, the other initiatives seem rather incidental for Murali as he mentions the use of the ‘MAPinr’ app to find and fix pipe alignment, installed on the mobiles of all site engineers.
“I am basically from Madurai, Tamil Nadu,” shares Murali about his personal front. “My wife, N Soundhara Devi, is a homemaker, and our son is M Kritik Anand.” Cooking and listening to music are his hobbies and “reaching the hilltop reservoir after crossing a stretch of 103 km without any leakage in the pipeline in this project has been my most memorable moment,” he says with a contended smile.
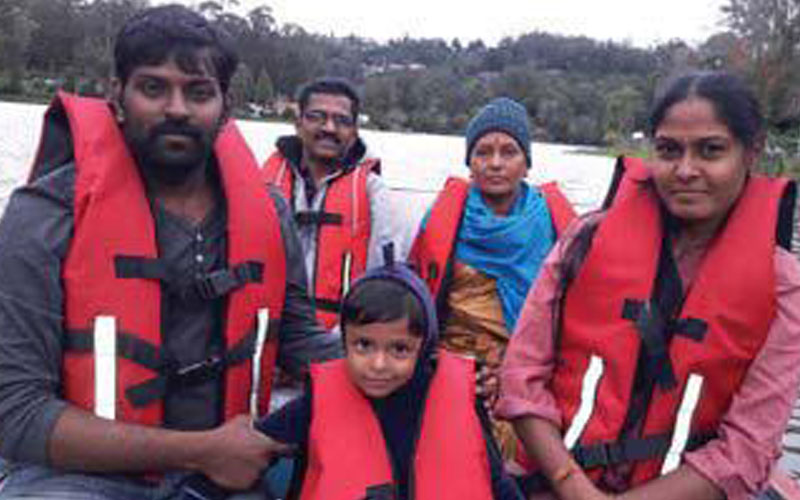
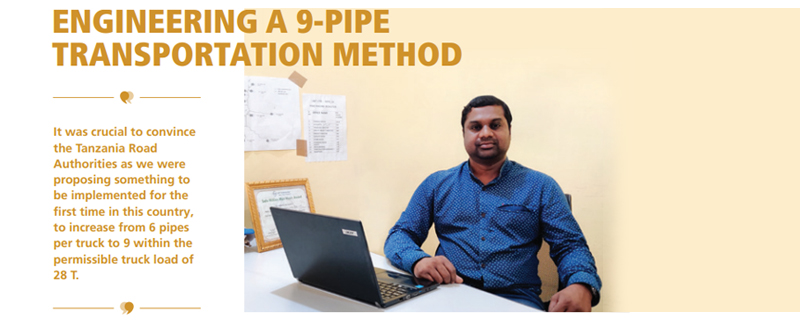
- Jayakumar Swaminathan
Manager, Electrical — SCM, WET IC
Evolving strategies to achieve excellence has been Jayakumar Swaminathan’s mainstay right from the time he stepped into L&T Construction and today, it is this quest for excellence that has driven him to come up with a key value addition at the Tabora Water Pipeline project in Tanzania where he steers Supply Chain & Logistic Management. “From an estimated 1430 trips to transport pipes, we brought down the number to 953 and the gains are not only specific to this project but across water supply and distribution jobs,” he shares elatedly.
Being his first overseas project, Jayakumar had his task cut out from the very beginning as pipes had to be transported over nearly 1000 km across 5 key check points involving statutory approvals from different nodal officers. “It was crucial to convince the Tanzania Road Authorities as we were proposing something to be implemented for the first time in this country, to increase from 6 pipes per truck to 9 within the permissible truck load of 28 T.” Safety was a top priority, insists Jayakumar, “While aligning to the mandatory precautions, we took note of the additional challenges of improper approach roads and the mountainous terrain en route.”
A sound strategy has to be supported by a lot of groundwork, mentions Jayakumar, “Saddles were specially fabricated in line with the weight of each pipe; the load dynamics and strength of the material were designed to absorb the shocks during transit backed by a 10 line safety belt for each truck.” The hard work of Jayakumar and team paid off as their 9‑pipe method was approved, “We now had permission to transport pipes of up to 180 mm oversize width on either side of the truck. The entire process is a trail blazer in the logistic handling of conduits, especially in a foreign country, with stringent operational norms and is now acknowledged as a standard operating procedure.”
Transferring the momentum is key to all OPEX initiatives, affirms Jayakumar, “The entire conduit supply chain process benefitted as we further improvised the deliverables by installing GPS on all trucks to receive real time information on fleet movement for hassle free unloading operations.” With all the pipes moved to site locations, without any incident, Jayakumar and team have stamped L&T’s signature of excellence in Tanzania and assured WET IC a head start in Africa.
On the family front, Jayakumar owes it to his wife, Purnima, for raising their two daughters Vaibhavi and Thanishka who are 7 and 2 years old respectively. Time with family for Jayakumar, means a visit to his hometown, Bengaluru that is laced with fond memories with his dad.
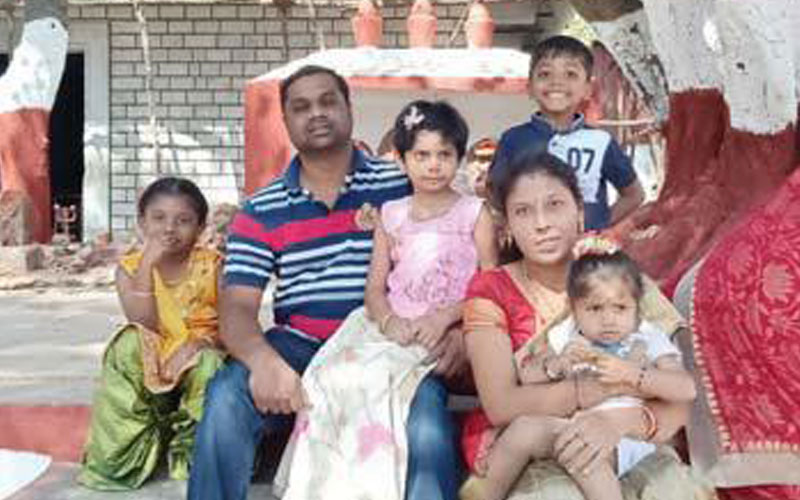
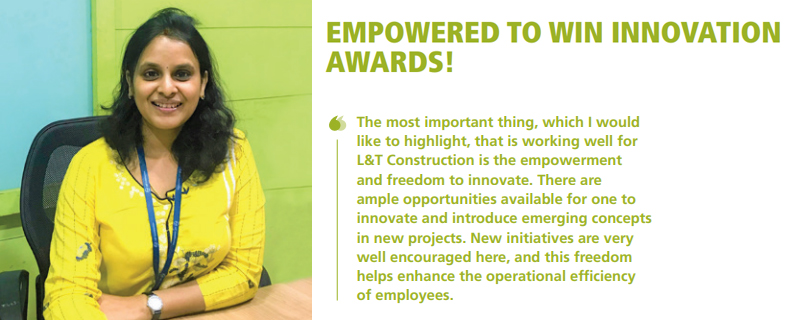
Kanika Bansal,
Asst. Engineering Manager (Chemical) — WET IC
Kanika Bansal is an extremely proud and happy young woman for winning the Best Innovation Award in 2019 for her new design concept. “It is entirely new for the Indian market,” she shares excitedly, “Though the design had already been proven in some successful installations around the world so we took learnings from those installations and made innovative modifications to the GIDC project design to suit our client’s requirements.” The design concept was to optimise the Sea Water Reverse Osmosis plant that was having a cascading effect on all downstream and upstream equipment sizing. “This concept has not only reduced our overall project cost, OPEX and CAPEX but also helped our I&LWS department (WET IC) win the project bid. The design from the software provides cost effective solutions by minimizing the size of the pre-treatment and second pass RO, that creates substantial savings on capital investments as well as in operating costs of the plant,” she elaborates. Winning that award, obviously, has been her most cherished moment. “I am most thankful to L&T Construction for having recognized my talent and given me a platform to innovate and execute,” she shares with feeling.
“The most important thing, which I would like to highlight, that is working well for L&T Construction is the empowerment and freedom to innovate.” She means every word. “There are ample opportunities available for one to innovate and introduce emerging concepts in new projects. New initiatives are very well encouraged here, and this freedom helps enhance the operational efficiency of employees.”
Presently associated with the 100 MLD Desalination project, where she introduced her award-winning concept, Kanika is involved with a couple of other projects too: detailed process engineering for the 20 MLD Low Salinity Project based on Sea Water Reverse Osmosis System for ONGC at an off-shore platform and for the Water Block (156 MLD- RWTP, 32 MLD — RO-DM, 6 MLD- CPU & Associated Facilities) at HPCL Rajasthan refinery. “I am using several design software like WAVES, IMS design, INGE design provided by the manufacturers to improve efficiency of the overall process of any treatment plant,” she shares.
If possible, Kanika would love to have her Saturdays for herself and her family. “I believe that work-life balance helps increase the motivation of employees and they feel more dedicated towards their work. My husband, Shashwat Saxena, is a business head at TVS Credit, Chennai and my daughter’s name is Shreya,” she shares with a sparkle in her eyes. Hailing from Meerut, Uttar Pradesh, Kanika’s hobbies are dancing and watching movies and, “yes, I do create time to follow them,” she adds with a laugh.
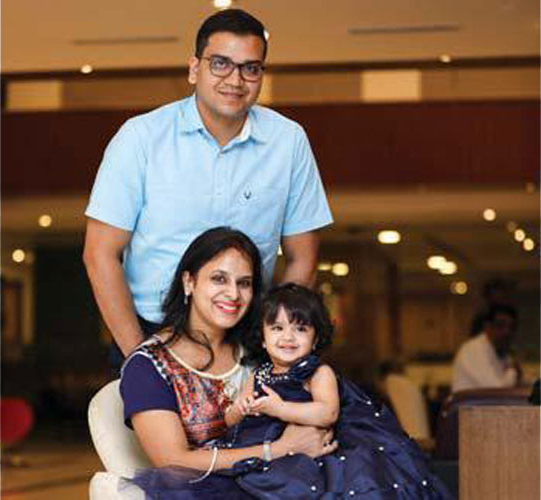
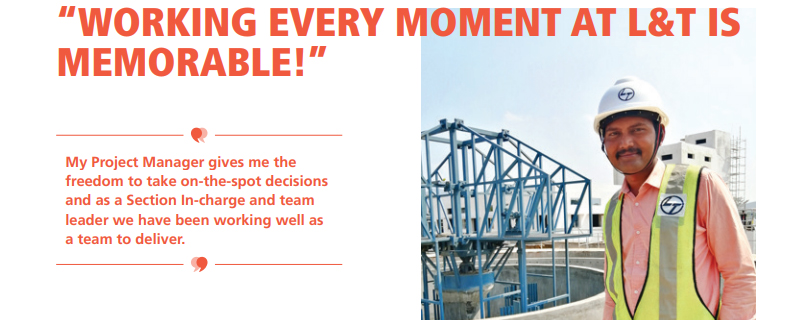
D Ramsundar,
Asst. Manager — Civil, WET IC
Being chosen as an efficiency champion has certainly been a highpoint in D Ramsundar’s career at L&T, every moment of which he describes as “memorable and a passion” filled with a long list of moments to cherish. “In the Gadag water supply project, when the site was flooded in the monsoon and the jack well was sinking into the slush, we engaged a long boom excavator to remove some 3,000 cum of slush in 30 days’ time to bring the jack well back and complete the job in time,” he shares proudly. In the same project, their decision to construct and commission the electrical buildings and switch yards in the stipulated time and erect prefabricated shutter panels for roof slabs again reduced execution time.
After stints at the Dhanbad and Gadag projects, Ramsundar is on his third, the Naupada water supply project. “We do have challenges like availability of skilled labour, the pressure to construct a number of ESRs in a short time, operate in remote locations with no network and to reach them we spend more time travelling than working,” he grins, “but my Project Manager gives me the freedom to take on-the-spot decisions and as a Section In-charge and team leader we have been working well as a team to deliver.”
As efforts to improve efficiencies at site, Ramsundar mentions the introduction of Eurex props for all beam bottoms in ESRs instead of H‑beams, wallers and universal Jacks that have improved manpower productivity and reduced formwork cost. “We erected HDT systems from tie beams to tie beams in ESRs instead of laying scaffolding from ground level to slab whereby we were able to repeat the formwork system more often and by pouring ESR wall concrete in 2 lifts of 2.4 m height instead of in 4 lifts of 1.2 m helped reduce both time and number of construction joints.”
Cognisant App, View EHS, QIR and ePragati are some of the digital solutions he reels off that are making a huge difference for Ramsundar and his team at site. “WhatsApp helps us bridge the communication gap and Google maps have helped us enormously to identify the pipeline routes since a lot of our work is happening in areas out of network. Continuous follow up with all subcontractors and all our internal departments for manpower & material mobilisation, training local sub-contractors and workmen in civil & pipeline works and making them adapt to our L&T Systems are making the difference,” he says.
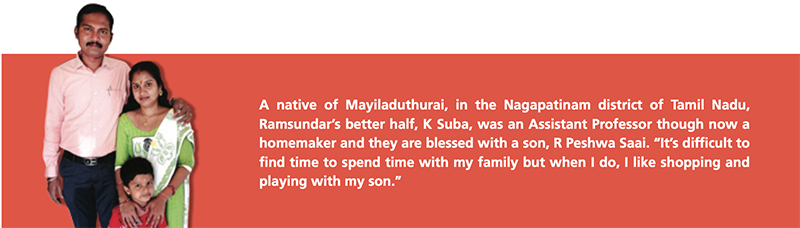
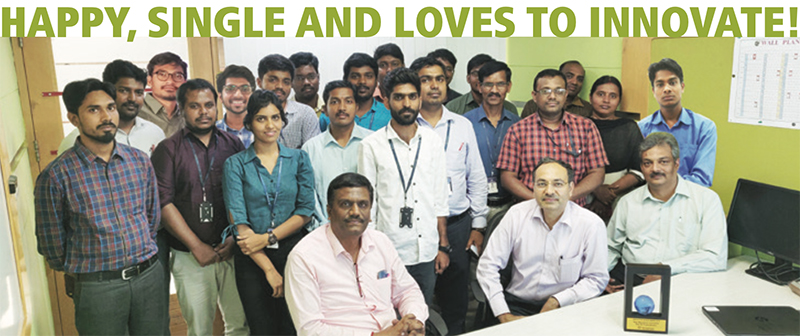
M Vinod,
Asst. Engineering Manager – Civil, EDRC — Industrial
Water Systems, WET IC
Thinking laterally, M Vinod feels that the success of an organization should not only be in terms of revenue, “but also in terms of GOH – Gross Organizational Happiness,” he opines, “which will boost an individual’s efficiency and in turn that of the organization as a whole.” A four-year-old at L&T, Vinod has already worked across a wide spectrum of projects and been involved in a range of OPEX initiatives but the one dearest to him is his novel design for the deep intake pump house that faced several execution and design challenges, he points out. “Dependence on seasonal variations in water levels adjacent to a river or lake, uncertainty in founding and berm levels to be excavated, the huge requirement of plum concrete for a level base, time consuming removal of shuttering in case of tie beams and a host of others that increased our time for resubmissions and validation of designs. To address all these uncertainties, we proposed an overhang deep beam from sump wall to rest the gantry column. A simple, out-of-the-box solution,” he grins, “but hugely successful as it has saved considerable time and cost. It also won us the award for the Best Innovative Design – 2019 in WET IC,” he shares proudly.
About some of his other OPEX initiatives, he mentions the design of switchyards for the NVDA Parvathi project, the use of RCDC and building planners in the design of beams, columns and slabs for the Athikdavu Avinashi project “to get exact drawings in reference to the detailing as exact inputs for draftsman to work effectively and efficiently and the first time use of the Ansys workbench to analyse stresses in the mass foundation of canal pumping stations with volute pumps at the SSNNL SBC PS4 & PS5 project. Complete BIM implementation for the first time in LWS BU started with the Harpanahalli Pump house which I have been a part of,” he shares with eyes alight. “I have also developed excel sheets to arrive at Sag Tension loads based on thermal and elastic elongation effects on cables for gantry tower structures, that is applicable for transmission line towers too and help to optimize the engineering design of foundations when dealing with probabilistic loads.”
Hailing from Bidar, Karnataka, Vinod is still only married to his job and his present love is his dog, Casper, “whom I have personally trained,” he smiles. “I like listening to Punjabi songs, do bhangra, collect gadgets, assemble PCs and take long rides.”
Vinod believes that being an engineering and construction giant, “L&T needs to educate the working level people (at EDRC) about project management aspects but I am happy that engineers have freedom and responsibility to take up huge tasks that creates an atmosphere to come up with innovative ideas and solutions for problems,” he signs off confidently.
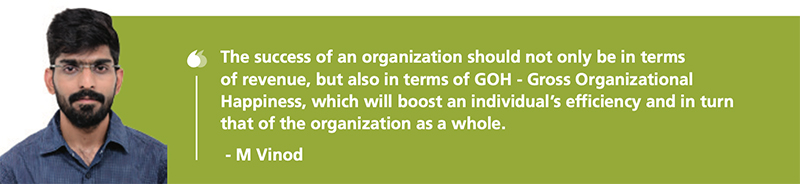