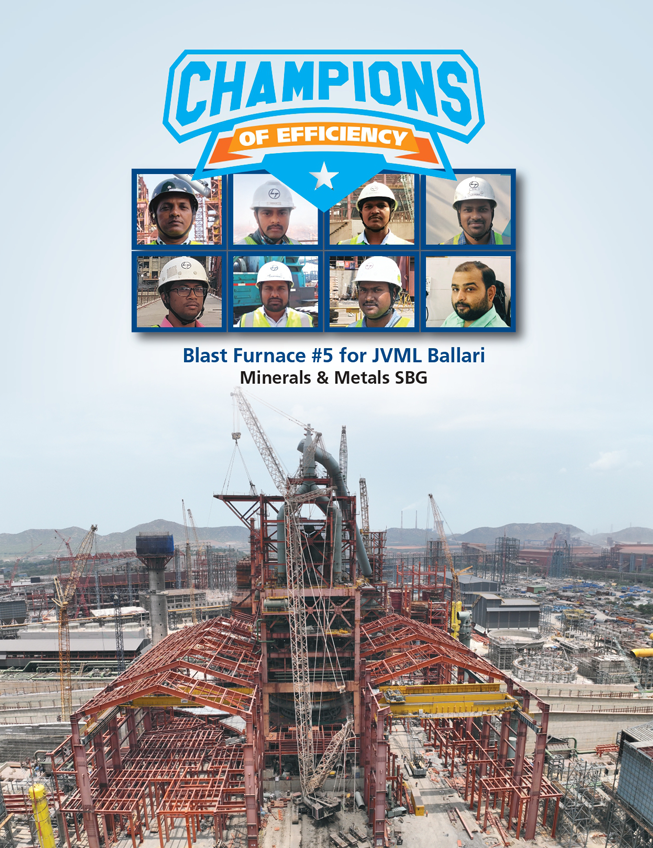
DRIVING SAFETY IN A COMPLEX,
MULTI-DIMENSIONAL PROJECT
Uttam Kumar Nandi
Senior Manager (EHS), M&M SBG
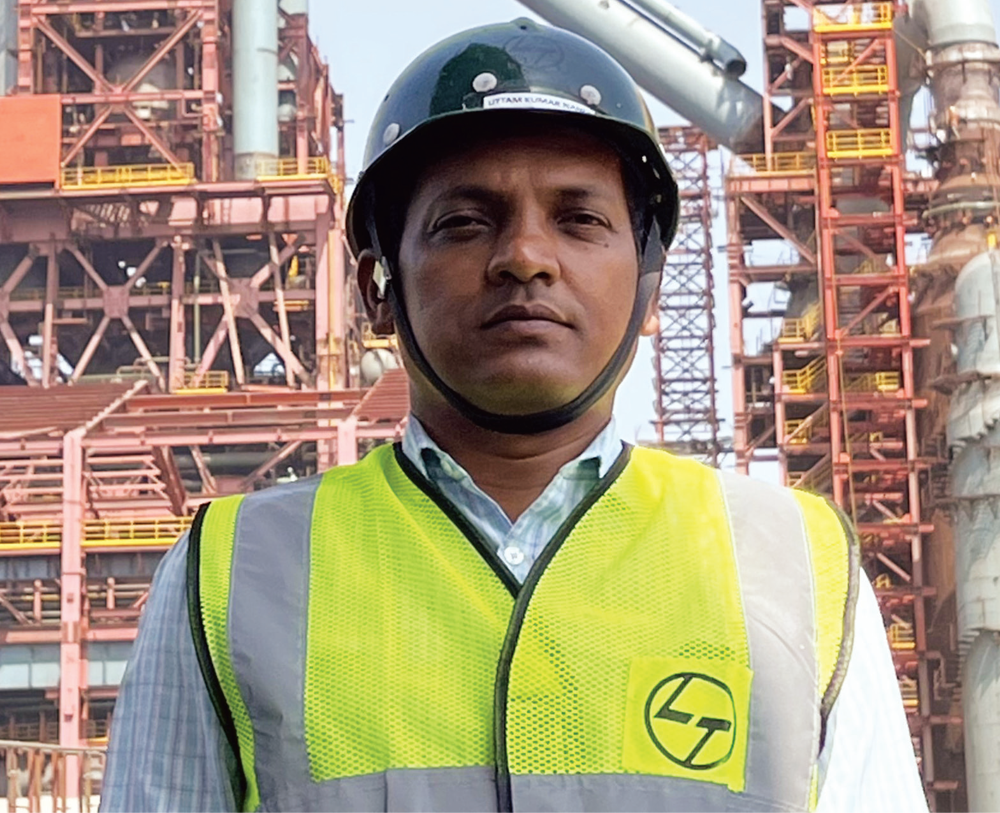
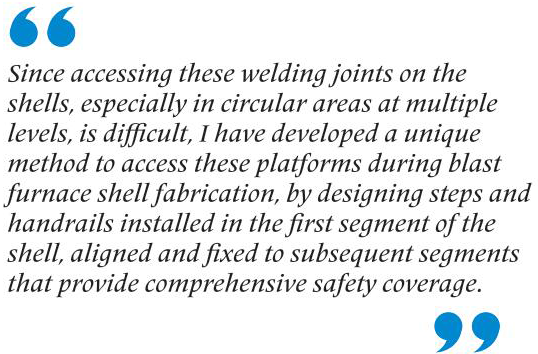
A moment of reckoning in Uttam Nandi’s life was when working at the Lower Subansiri Hydroelectric Project; heavy rains caused a huge landslide, closing the one and only mouth of the tunnel and trapping 14 personnel inside. “We successfully rescued them after 18 long hours,” he recalls, but that incident has left an indelible mark on Uttam, the EHS professional. A seasoned campaigner, already at his 8th project with L&T, he is currently working on the complex, multi-dimensional JVML Ballari project.
Blast furnace shells are fabricated on the ground in various segments and rings, which are then assembled vertically ring by ring. “Since accessing these welding joints on the shells, especially in circular areas at multiple levels, is difficult, I have developed a unique method to access these platforms during blast furnace shell fabrication,” he shares, “by designing steps and handrails installed in the first segment of the shell, aligned and fixed to subsequent segments that provide comprehensive safety coverage.” Barricades at his site are different: made of reused or waste materials like discarded or scrapped small, empty plastic drums, filled with waste or unused concrete with one-metre pipes installed as posts. “It is a cost-effective, environmentally friendly, and innovative method,” he smiles.
Having to deal with multiple agencies and activities at various elevations, Uttam has introduced administrative control permits for multiple tasks with all agencies for better coordination across the project. “Apart from safety nets, we have maximized modularization of erection lifts to avoid working at height and multilevel working risks,” he remarks. Housekeeping is another imperative for Uttam, and as part of his ‘Safe Housekeeping Model’, everyone is required to bring at least one material or thing down from a height while stepping down to the ground floor for lunch, tea break, or any other purpose. “It’s a simple but effective way to improve safety at a complex project,” he adds, with a punched fist.
“I always insist on modular erection and effectively implement the work permit system to avoid multilevel work,” he shares about his other priorities at site. “We used to maintain and monitor a wireless communication system at one of my earlier projects and use an interlocking system with passenger hoist at the entry gate apart from the inbuilt door interlock.”
About teamwork, Uttam says, “My peers, team members and subordinates have always stood by me throughout my journey, and the support and collaboration from the senior management have helped me to achieve my objectives.”
A native of Paschim Medinipur, West Bengal, Uttam is married to Sagarika, a homemaker, and they are blessed with two daughters, Shreyasi and Shrestha. When not driving his EHS agenda, he loves to work with electronic devices.
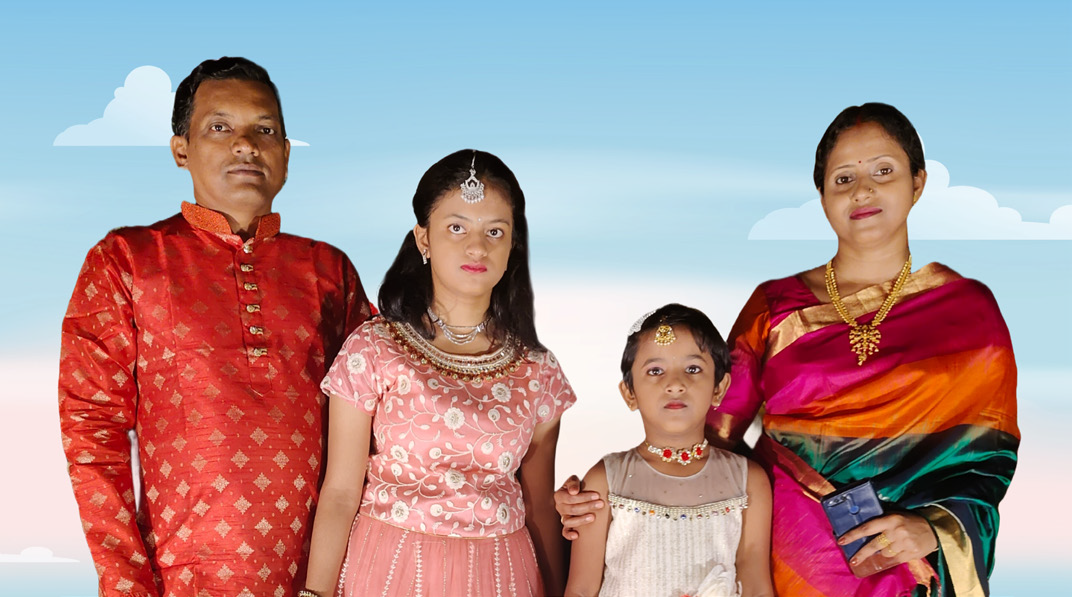
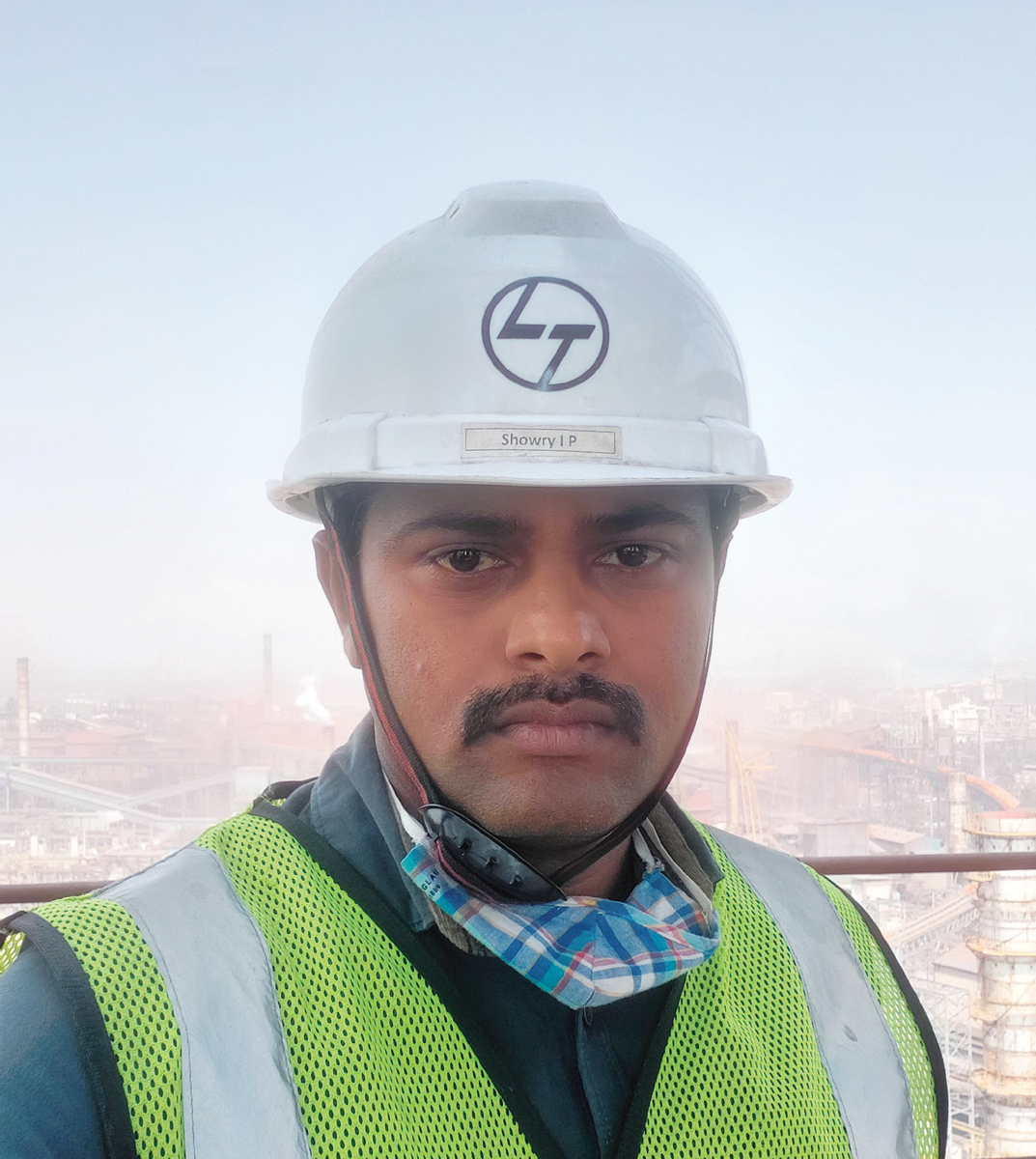
MASTER BLASTER
Showry Innaiah Pamisetty
Senior Construction Manager, M&M SBG
His experience in constructing blast furnaces across India has helped Showry Innaiah Pamisetty appreciate the importance of risk management in projects, for the construction of blast furnaces involves more than 80,000 members at the site and structures that can exceed heights of 100 m, posing serious safety concerns. Currently at the Blast Furnace #5 for JVML, at Toranagallu, Karnataka, he is bringing to play all his well-earned experience. “It is important to follow stringent safety standards to ensure safe working practices,” he remarks seriously, “so, we opted for modular erection to reduce risks by assembling the major structural components on the ground and then positioning and erecting them as a single unit at the desired location.”
Being a new method, one of the key challenges for the team was to get the workers to leave their traditional comfort zone to adopt a new technology. “To maintain consistent progress, we have ensured the timely supply of structures in the required sequence through meticulous microplanning of the tasks, identifying the key requirements, effectively communicating with the yards, and providing detailed explanations of the new technology and its benefits. The proof of the pudding is in consistent progress and timely completion of the structures with no safety hazards,” says a smiling Showry.
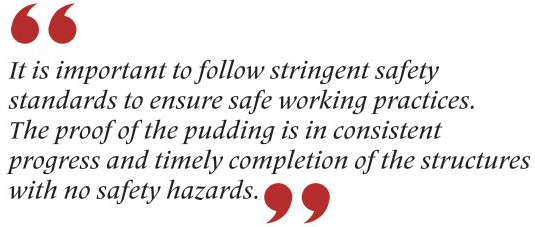
Having started his association with L&T in 2007, he has worked on a slew of major blast furnace projects and particularly recalls his work at the Blast Furnace #8 at Bhilai Steel Plant in Chhattisgarh during the pandemic. “We had issues at the Vertical Rolling Mill since the OEM experts could not make it to the site, so I took on the task and, after a thorough inspection, identified the solution and implemented it, which saved us costs and completed the project on time,” he says with a proud look.
Showry appreciates the strong support he receives from his seniors when new ideas are implemented. As an example, he quotes the shift from manual workflow to digital automation. He was instrumental in successfully implementing the semi-automated FCAW welding in Blast Furnace #5, which has since been extended into the hot blast stoves and other areas. It has reduced cycle time from 25 to 9 days, another feather in Showry’s cap.
A native of Phirangipuram, Guntur in Andhra Pradesh, Showry is married to Julian Mary Pamisetty, a home maker. He loves to take morning walks and watch movies with his son, Susanth, and daughter, Samyuktha. A moment that he cherishes is commissioning the top gas recovery turbine & oxygen PRMS plants in Bhilai.
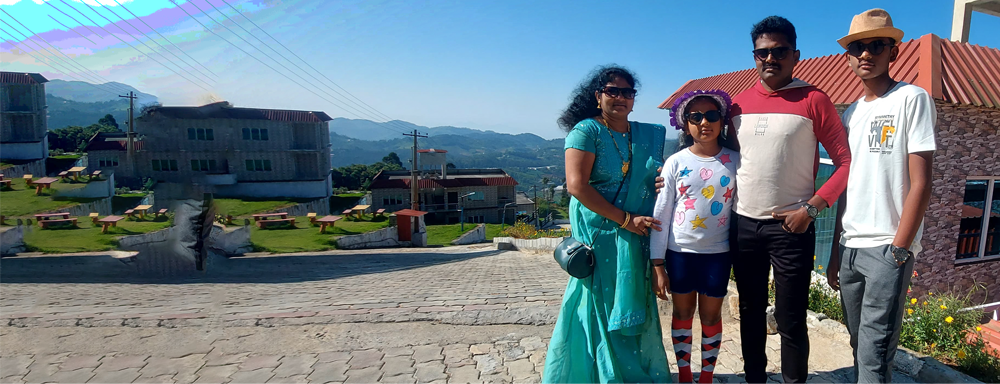
THE ‘Q’ IN QUALITY IS FOLLOWED BY YOU
S Mohammad Farooq
Manager (Mechanical – QA/QC), M&M SBG
Ever since he began his journey with L&T in 2008 at the 3.0 MTPA Blast Furnace (BF#3) Project, to construct Asia’s largest blast furnace at JSW Steel Ballari, a matter of great prestige for him, S Mohammad Farooq has made it his mission to drive quality. It is heartening too that he focuses on the vital link in the chain – the workman. “Our participation to drive quality with workmen at project sites has made them understand our design considerations, which has translated into significant improvements in efficiency levels,” he remarks purposefully. “It’s also the best way to change mindsets and behaviours towards quality.”
A veteran of 9 projects, Farooq is presently driving his Quality mission at the JVML Ballari Project, where among his several challenges is the one that, since they work on complex structures, quality inspections at the right time are most important. “We have introduced stagewise inspections to ensure that all agencies are aware of the quality systems when coordinating with them for all the activities and have maximized the modularization of structural erection inspections to avoid working at height and multilevel working risks,” he points out. Training workmen in various languages and rewarding them are other ways to sustain their quality culture.
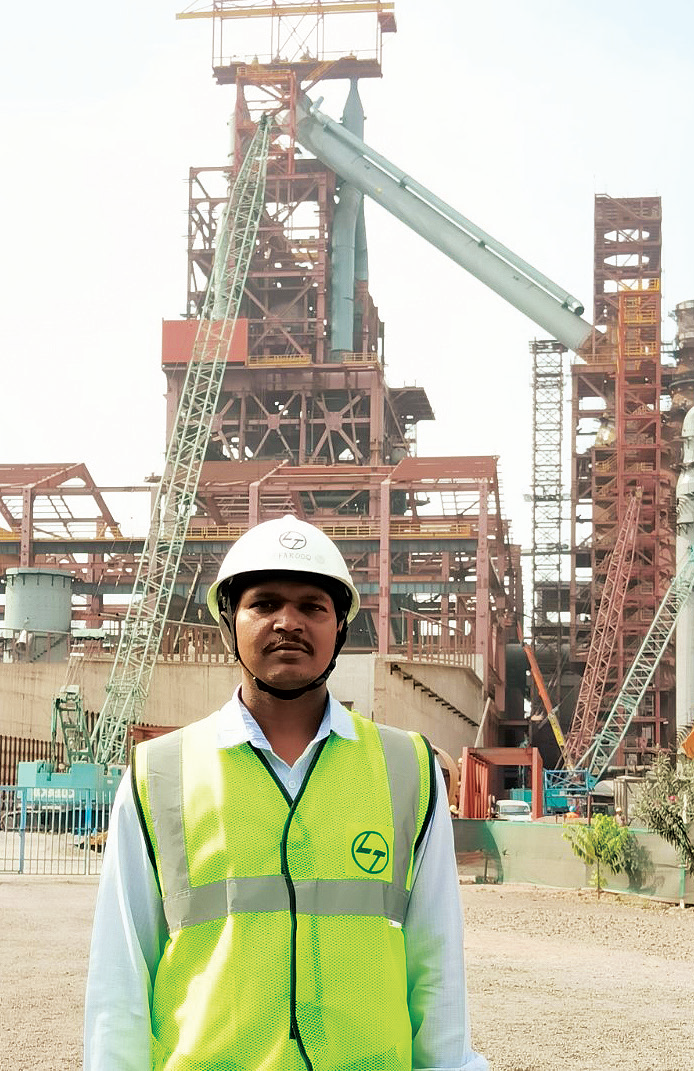
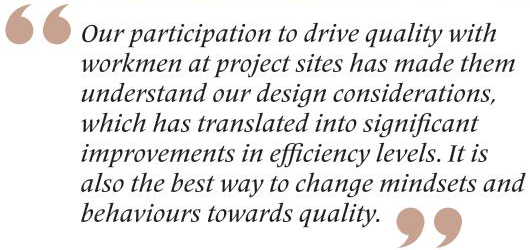
Another challenge the team faces is the scarcity of agencies for inspection, weld testing and laboratories for calibration, which leads to delays. “We have taken it upon ourselves to calibrate all our instruments at the site, with the result that 150 of our instruments were calibrated in just 3 days by an NABL calibration agency,” shares Farooq, with an air of achievement. “Test pieces are welded before the start of a job to establish welding procedures with our NABL labs and to get quick approvals from our clients.” Welder qualification is also critical for the project due to the enormous frequency of welders being qualified and for fast screening, for which welder training and qualification booths have been set up at the LRPC yard, and over 1,500 welders have thus far qualified.
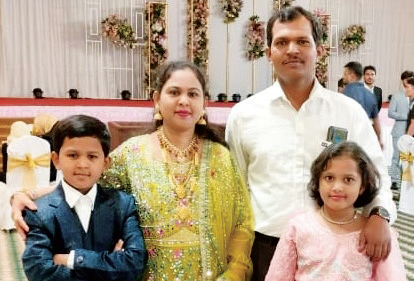
“We have developed a unique method in the blast furnace to weld high-thickness plates in large quantities,” shares Farooq. “In fact, this is the first project where ring-to-ring shells are being welded using an automatic Submerged Arc Welding Process that is saving us time, cost and dependency on welders,” he smiles.
Hailing from Ballari, in Karnataka, a city rich in iron ore, Farooq’s better half is Farheen S, a teacher, and they are blessed with two children, S. Mohammed Farhan and Aayat S. He loves to play carrom in his free time.
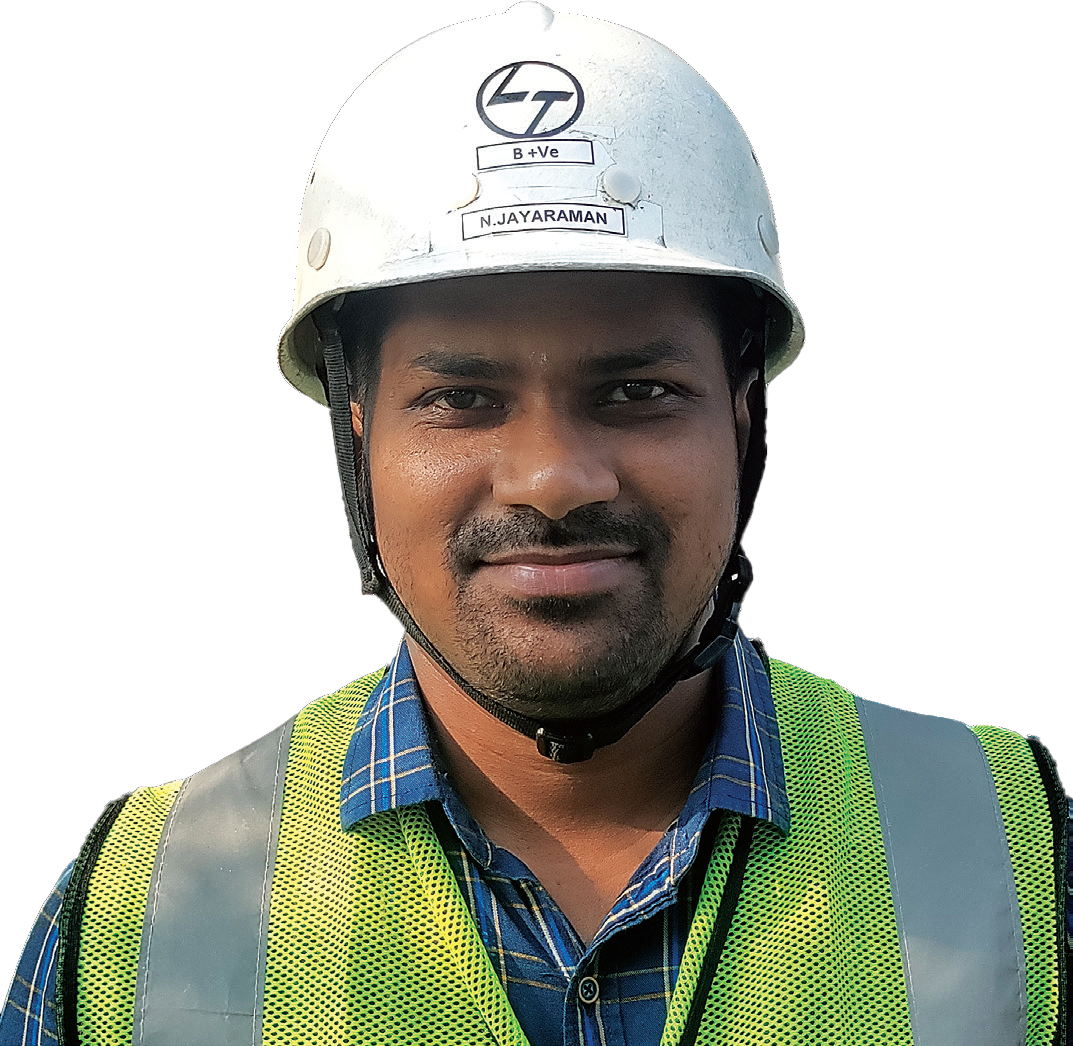
PLANNING IS KEY
N Jayaraman
Construction Manager (Mechanical), M&M SBG
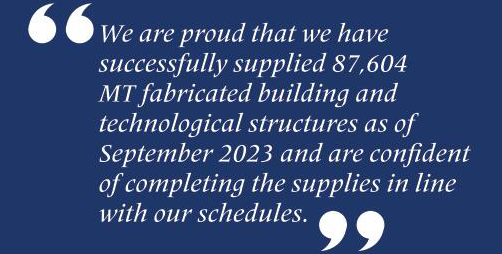
Any construction professional worth his salt will tell you that planning is key to successful execution, and N Jayaraman agrees whole-heartedly. After spending 16 years with L&T, what impresses him most about the company is the quick decision-making and the freedom to perform. Having started his innings at the NLC Mines-II Expansion Project as Erection Engineer, he is currently at the JVML Ballari Project, in charge of the fabrication yard that involves in-house fabrication, steel melt shop building and technological structures.
With 1,14,835 MT in-house structural fabrication works planned for the project, Jayaraman got busy establishing a strong fabrication and supply tracker to monitor both the fabrication yards from the perspectives of scope, drawing availability, status of steel, fabrication, and supply. “This has helped us take timely decisions based on priority and execute backup plans during material/manpower crises,” he points out. “We are proud that we have successfully supplied 87,604 MT fabricated building and technological structures as of September 2023 and are confident of completing the supplies in line with our schedules,” he says with quiet assurance.
Of course, handling more than 1.1 lakh MT of BOQ and arranging resources including raw materials, mobilizing equipment and manpower have been challenging for the team, considering that they are executing a fast-track project for a prestigious client. “Through continuous follow-up with vendors and systematically maintaining records from drawing quantification, steel reconciliation, fabrication to supply status, we have successfully arranged and managed resources to achieve a peak supply of 5,300 MT/month for both yards,” he flags off proudly.
Jayaram shares that records of the special mining equipment are being maintained systematically, helping the team to compete and award subsequent maintenance tenders with optimum cost workings. “A new software, Steel Structural System, monitors steel fabrication jobs from scope, drawing receipt, material requirement, matching steel availability, scheduling, erection priority and fabrication progress to dispatch till receipt at the site, and we are implementing this software for the first time in our SBG,” gushes Jayaraman.
Having worked on special mining equipment for 14 years, handling fabrication planning at the JVML Project was a whole new ball game for Jayaraman, but he seems to have held his own. “My seniors and team members have guided and supported me to understand the systems and procedures, helping me to perform better in my new fabrication planning role,” he says with great gratitude.
A native of Govindapuram, Tamil Nadu, Jayaraman is married to LakshmiBala, a homemaker, and they are blessed with a son, J Dhashvanth, whose birth is his life’s most wonderful moment. He relaxes by listening to music.
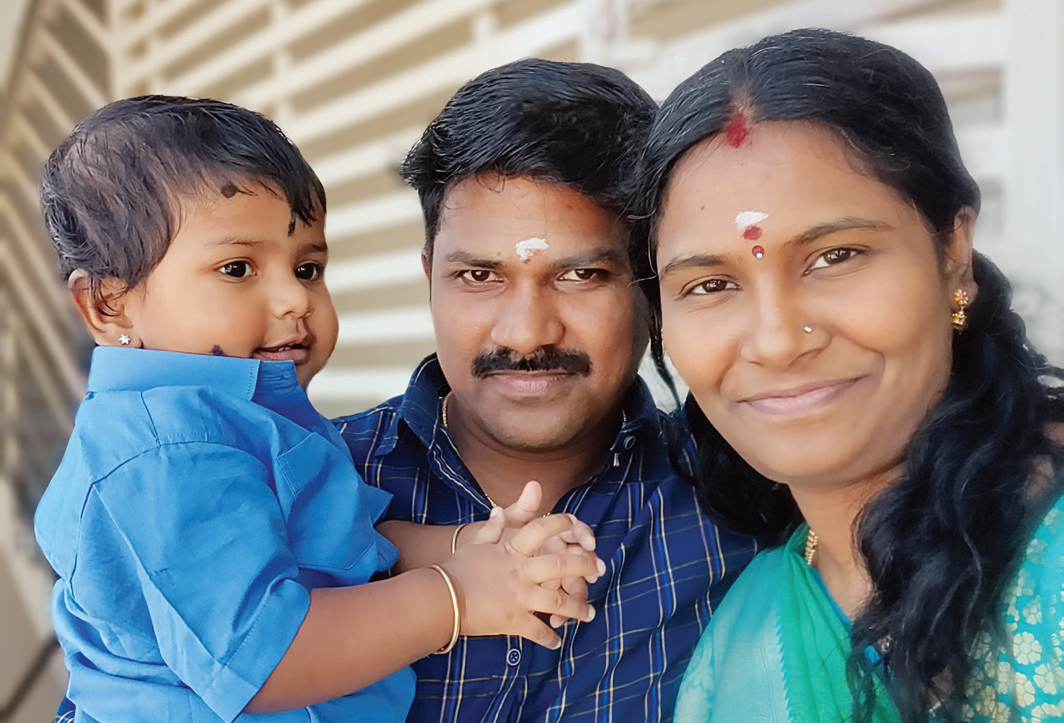
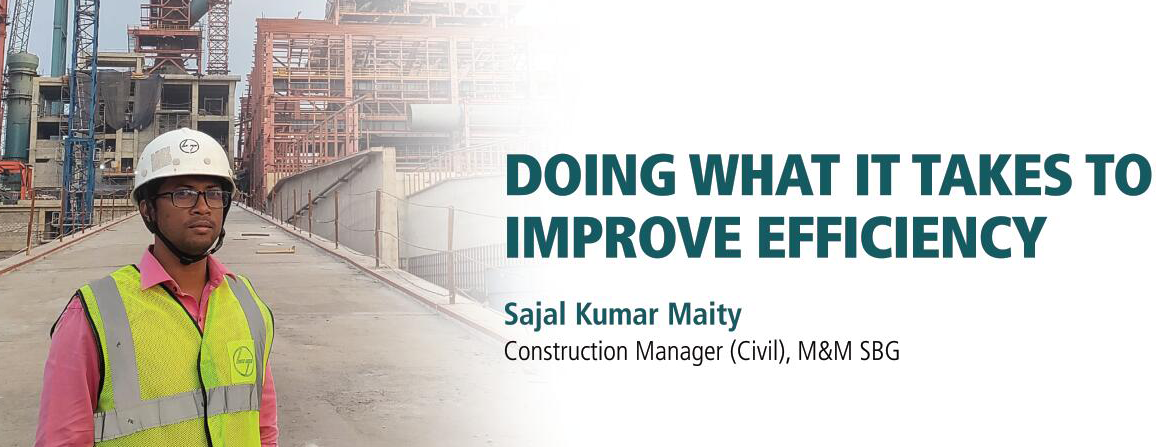
As part of the project team executing the complex and multidimensional JVML BF-5 Project, Sajal Kumar Maity is excited about the various special initiatives they have implemented at the site. “By using prefabricated steel shutters entirely for the three ramps that are circular-shaped piers with pier caps, we reduced shuttering cost, enhanced shuttering productivity and achieved a good aesthetic look,” he enthuses. For the ECR-1 Building, they used plastic shutters (Koehpa Panels) to improve shuttering productivity and reduce plywood consumption and repetitions. “We completed the furnace proper raft (9,000 cum.) sequentially in a cycle time of just 103 hours,” he shares excitedly, which is also his life’s most cherished moment.
Workforce mobilization and development have been perennial headaches for the team, as they are finding it extremely difficult to mobilize workmen, a majority of whom are from Bengal, Bihar, Jharkhand, Odisha, and UP, to come to their site in interior Karnataka. “We therefore concentrate on retaining workmen with additional incentive schemes, a good hygienic habitat, good food facilities, conveyance, outdoor games and entertainment facilities,” shares Sajal. “Since we are not finding adequate skilled manpower, we are developing our workmen by conducting many training sessions for different categories and rewarding them every month to improve our safety and quality culture.”
Sajal points out that, as per their original scope, there were no high-rise RCC structures, but the revised scope includes several superstructures for civil activities. “To address this enhanced scope, we mobilized additional workforce and formwork material and parallelly prepared a route map, to fix milestones for activities in the critical path.” His definition of successful execution is working systematically, department-wise coordination and learning each other’s systems, focusing on completing tasks in time and better interpersonal skills.
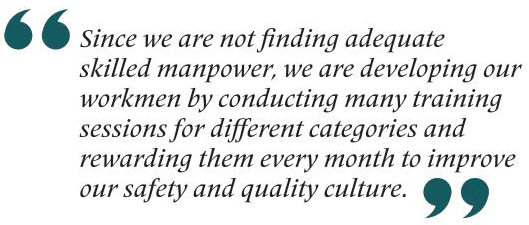
Recalling some successes from his previous projects, Sajal mentions the Coke Oven Project for JSW Dolvi, where the 82-cable support foundation of the Stamping Charging & Pushing Car was completed using the precast method instead of cast-in-situ to reduce the project’s time frame. “Again, at the same project, for the slope slab for two Coke Wharves, we poured self-compaction concrete instead of conventional concrete to reduce execution time,” he shares. He is extremely appreciative of his peers, team members and subordinates who have stood by him to achieve his goals throughout his journey.
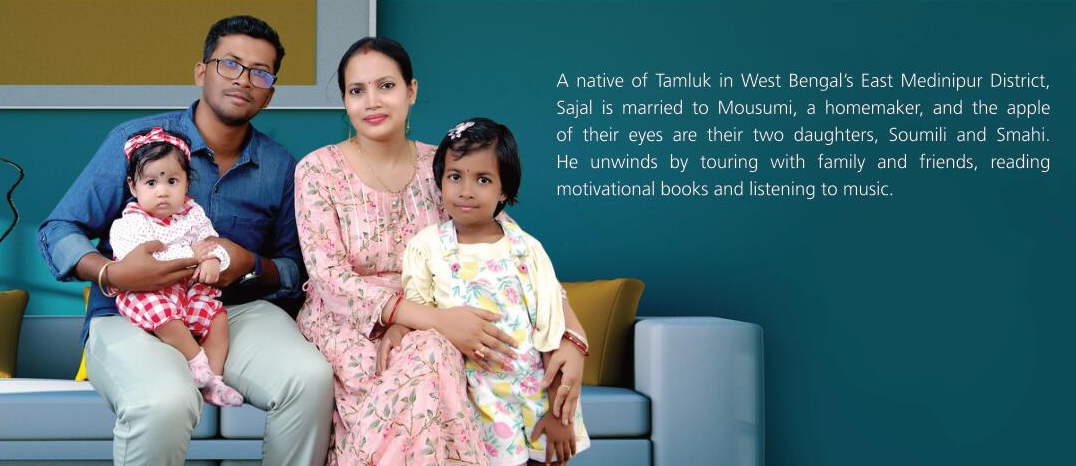
“JOINING L&T IS ONE OF MY LIFE’S MOST MEMORABLE
MOMENTS!”
Nabo Kumar Malik
Assistant Construction Manager (Civil), M&M SBG
For all budding civil engineers, L&T is a dream career destination, and it was no different for Nabo Kumar Malik. His dream came true in 2009 on receiving his appointment letter to be, as he proudly declares, “part of a company that builds nations. Joining L&T as a DET was certainly one of my life’s most memorable moments,” he nods vigorously. Since then, he has been living his dream across projects, starting with the Bhusan Steel Plant (Angul) as Site Execution Engineer and then Planning Engineer, a role he continued to play at his 2nd project, New HSM Rourkela (SAIL). “I was Execution In-charge for the mill and furnace area for a year on the project, before moving to the JSW, Dolvi site as Civil Planning In-charge.” In 2021, he joined the JVML Ballari Project, where he is currently handling MIS and Cost Control.
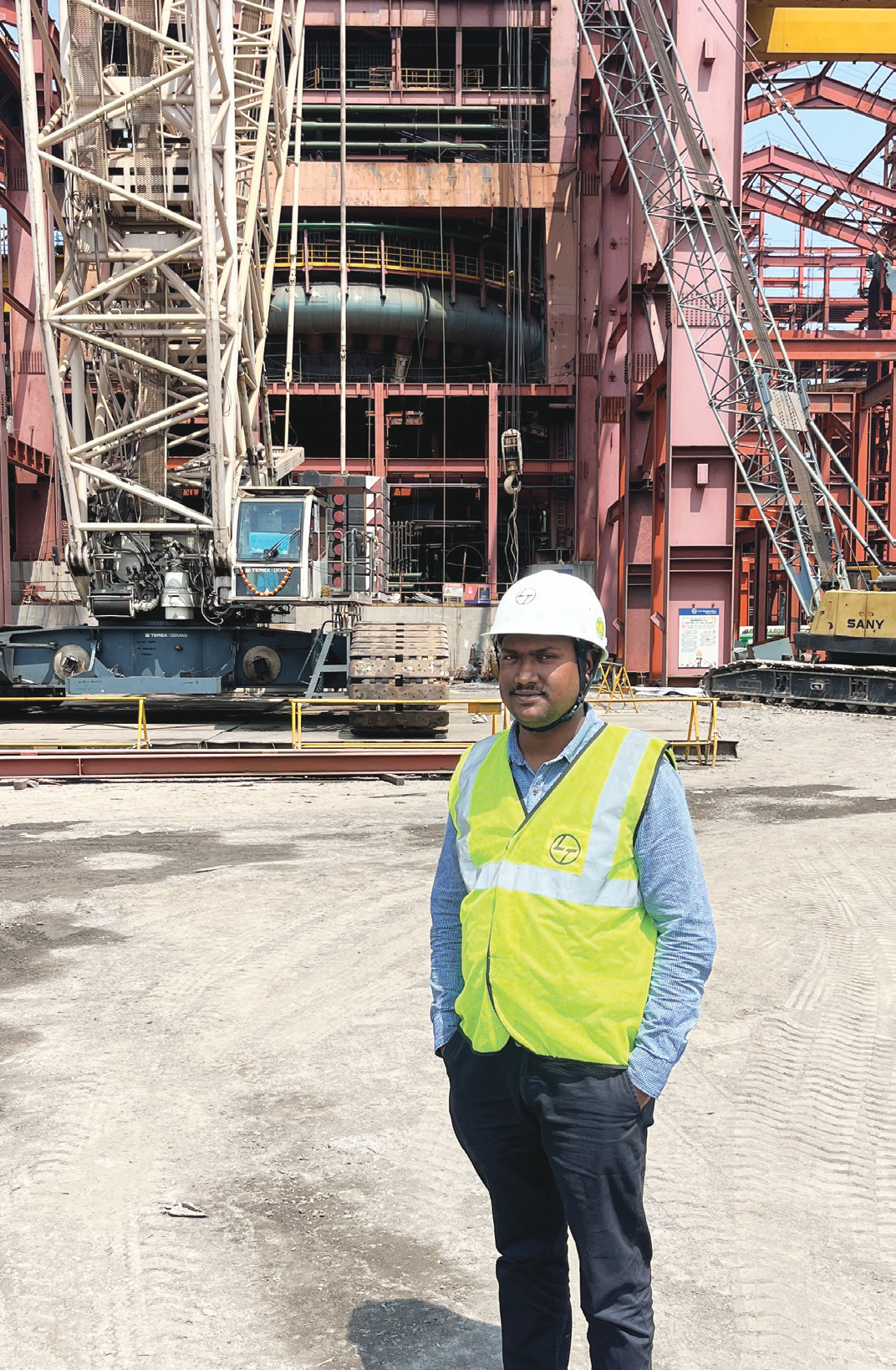
“To start with, the pandemic caused uncertainties because of which we wisely decided to delay the initial mobilization of heavy equipment that saved us two months of idle cost,” he shares, pleased at the team’s call. “All consumables were thoughtfully incorporated into the subcontractors’ scope of work, which increased accountability and promoted greater caution to prevent wastage, again resulting in cost savings on consumables.”
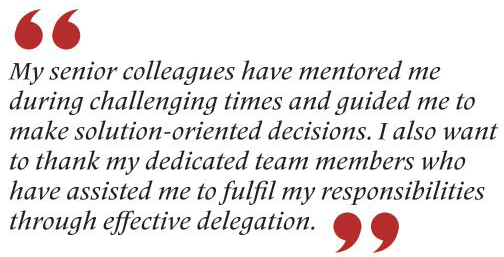
Equipment and labour mobilization have been tough nuts to crack for the team. “To deliver over 52,000 tons of fabricated steel structures within a demanding 24-month schedule while keeping costs at a minimum was a significant challenge,” observes Nabo, “to address which we strategically identified local vendors, to minimize transportation costs and increase the monthly supply rate.” On the labour front, while on one hand they were facing high attrition, on the other was the challenge to retain 6,000 workmen at the site. “We identified more than 100 contractors from across the country, negotiated with them as per our commercial terms and inducted them successfully,” he sits back with the relief of a huge task achieved.
In the face of stern tests, the Ballari team has been standing firm, and Nabo is grateful for the consistent support from all his senior colleagues who have helped him grow in the organization. “My senior colleagues have mentored me during challenging times and guided me to make solution-oriented decisions.” he says. “I also want to thank my dedicated team members who have assisted me to fulfil my responsibilities through effective delegation.”
A native of Dankuni, Hooghly, West Bengal, Nabo is married to Susmita Dutta, a homemaker, and his life’s second most memorable moment is holding their daughter, Ivvanshi, for the first time. He loves to read when away from the rough and tumble of site life.
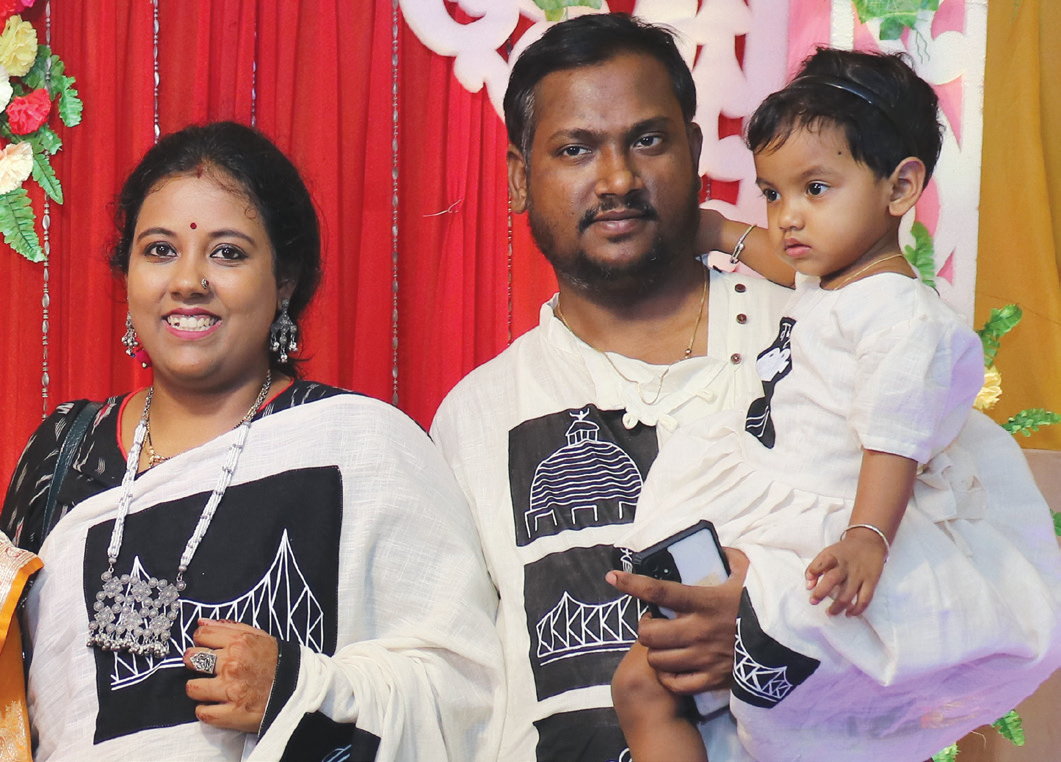
TALENT IS ALWAYS RECOGNIZED AT L&T
Shashank Tripathi
Executive (Stores), M&M SBG
Proud to be working for a company certified as a Great Place to Work, Shashank Tripathi is convinced that every employee’s performance is watched and identified by the senior management. “L&T invests in their employees to help them grow professionally, providing ample opportunities to learn, grow, and advance their careers,” he says. Shashank’s growth bears this out, having started his journey as a GCT at the CHP Amlohri Project and later at the CHP-Block-B, CHP, Khadia, and CHP, Dudhichua, proving his worth in the materials department.
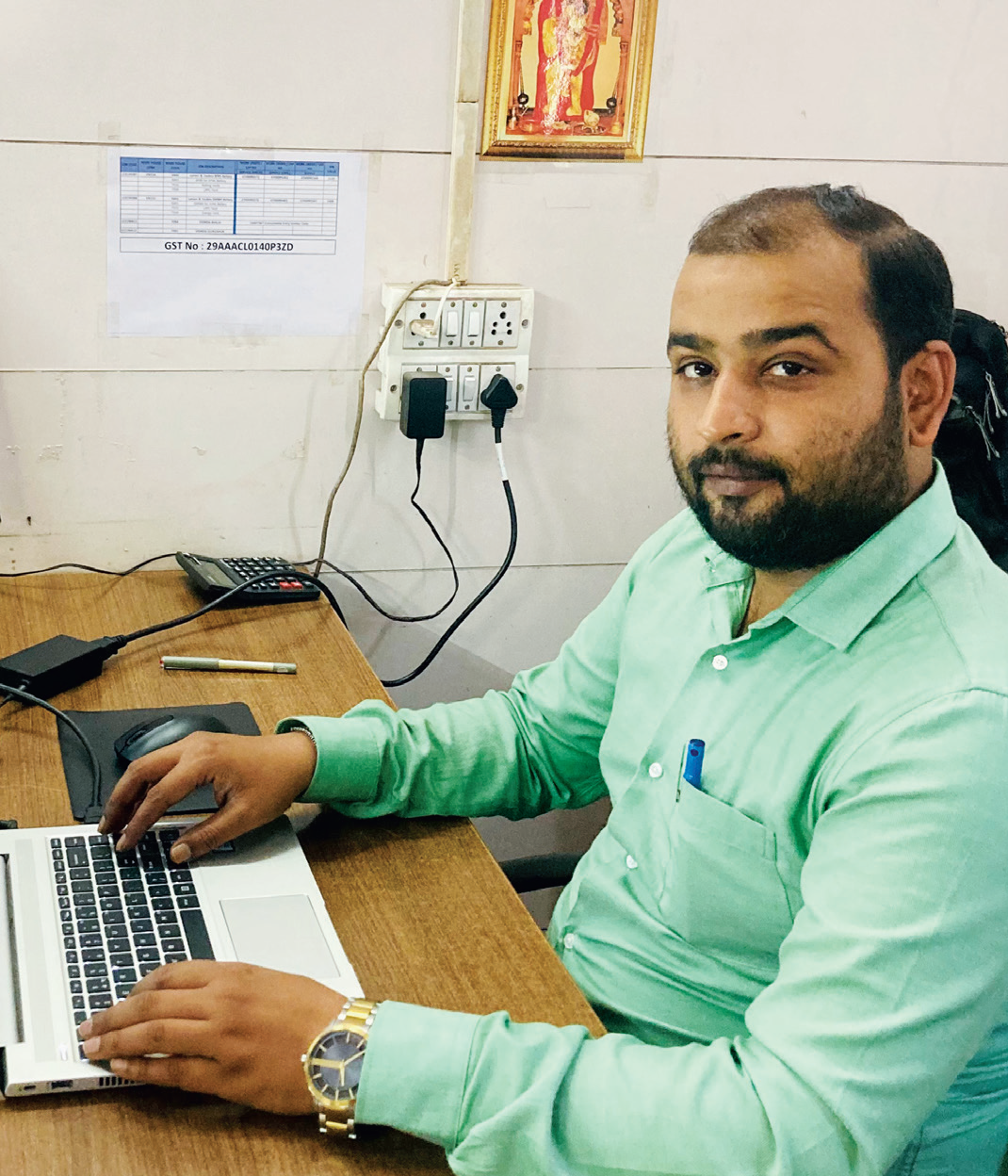
“Presently, with the JVML Ballari Project my key responsibility is catering to the material needs of the BF-5 and SMS-4 Projects with end-to-end responsibility for prefabricated supply materials from yard to erection site,” he informs. From day one, the team’s challenge has been to meet the material needs of a project that must be completed within stringent timelines. “My good rapport with Customers has helped to move materials from yard to the erection site round the clock with invoices and e-way bills,” he smiles.
An issue for the team was handling the huge number of vehicles entering and exiting the site, which involved a lot of formalities at the gate as per JSW’s SOP. “I identified the obstacles in the process and positioned our dedicated personnel at the gate to solve the issue,” he says with josh.

“I took the lead role in making digital stores,” he points out, adding that initially, getting subordinates to implement digital documentation was tough, being habituated to manual documentation. “However, as they realized that digitalization was making their work easier, they actively supported to making the Stores a 100% digital success,” he says with an energetic thumbs-up. Shashank believes in the advantages of digitalization and has been instrumental in linking the Weighbridge with EIP. “We track and monitor the issuance of HSD daily to the Own & Hire Assets through a Fuel Dispensing & Monitoring System installed in HSD Tankers, and fuel is dispensed only against assets having RFID tags that can be tracked live through the FDMS App.”
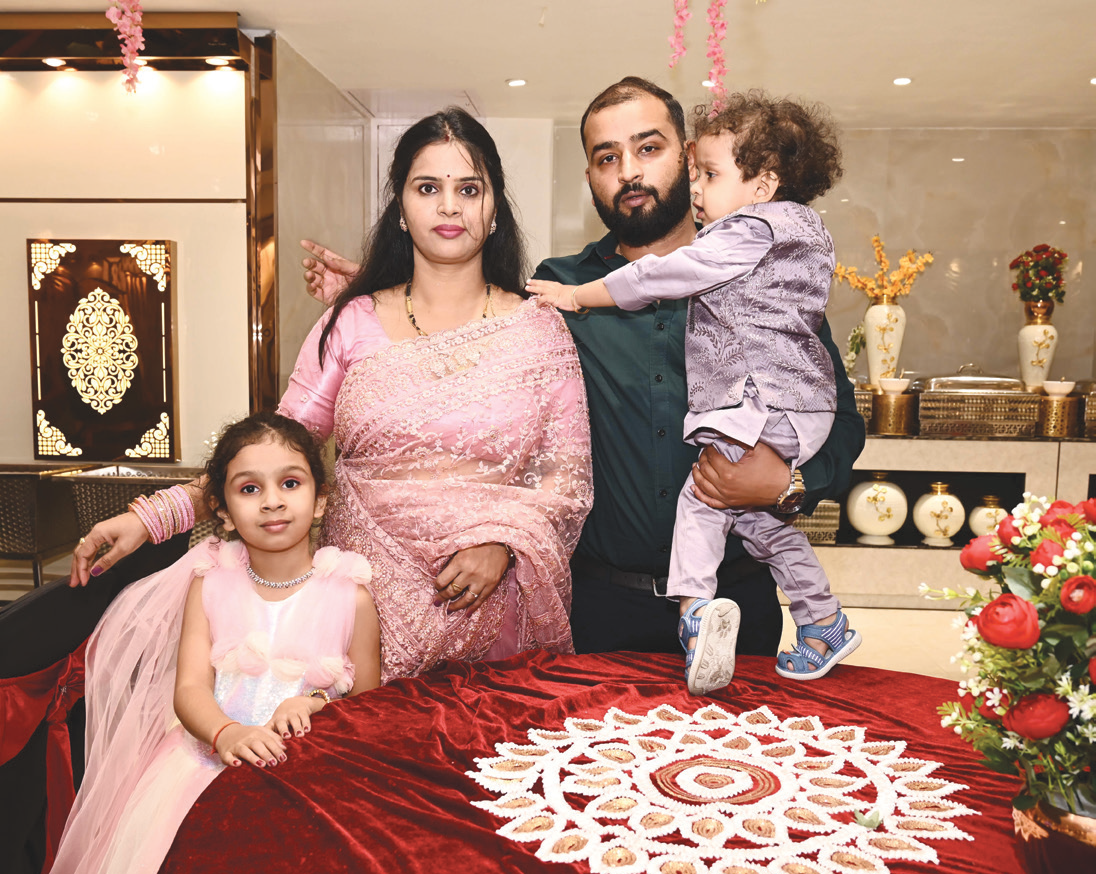
“I thank Project Director Mr. R. Umasathiyan for his mentorship and seniors from the SBG who have been incredibly helpful in developing my skills professionally, which has helped me to push my limits to achieve my targets,” he remarks gratefully.
A ‘Lucknavi’ by birth, Shashank’s better half is Sarita, a homemaker, and they are blessed with a daughter, Shanya, and son, Sarav. His most wonderful moment: “When I became the father of an adorable girl and a notorious son,” he says with a loud laugh. He loves to listen to music and watch web series during his free time.
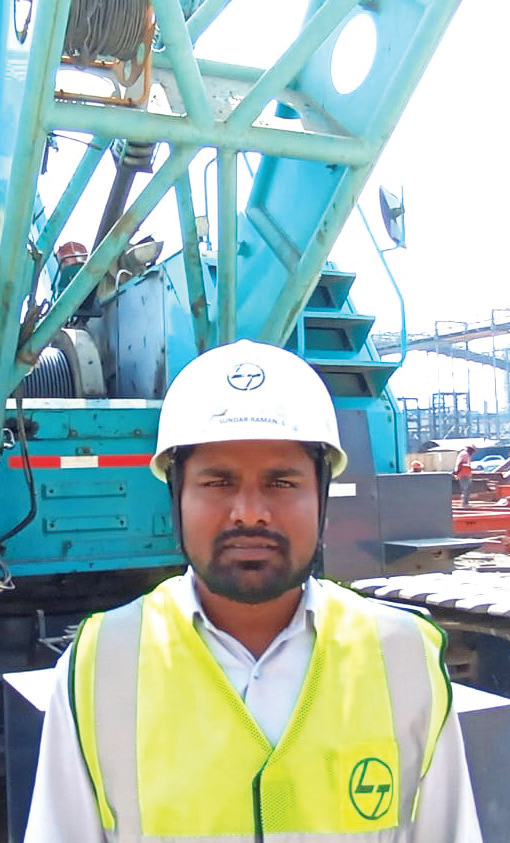
ALWAYS OPEN TO EMBRACE NEW TECHNOLOGIES
Sundar Raman S
Assistant Manager (P&M), M&M SBG
Like a true P&M professional, Sundar Raman S is ever keen to encourage innovation and new ideas to implement in the workplace and supports the associated necessary costs. “I recommend myself for technical and managerial training programmes to keep updated on new technologies and develop my career, and I always appreciate and reward new initiatives and job improvements.” With such a mindset, Sundar is certainly the right Company; he joined as a DET in 2010 at the Bhusan Steel Plant Project in Angul. “L&T encourages innovation at the workplace, which always motivates me to implement innovative ideas, resulting in cost and time benefits at projects,” he says with immense satisfaction.
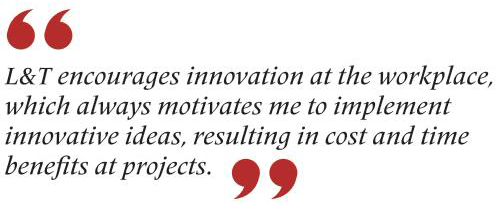
Currently at the JVML Ballari site, Sundar is P&M Site In-charge, taking care of the asset management system for JVML and O&M of the BF#5 plant and machinery. To keep everyone, right from the top management to the operator level, updated about the maintenance requirements, he has implemented multiple maintenance check points for P&M equipment apart from a biometric system installed in the cranes ignition system to avoid unauthorized operations and unsafe work. “We periodically circulate a P&M Digital dashboard to monitor the productivity of all equipment to increase utilization and reduce idle time,” points out Sundar. The MOBA-FDMS System and fuel sensors continuously monitor and control diesel dispensing.
Sundar and his team ensure micro-level planning for maintenance activities, O&M crew management, inventory planning for maximum availability of spares and minimal downtime. “JSW has complicated safety and statutory requirements for the asset base, for which we have developed a dedicated crew to take care of the compliance and entry process, which is resulting in better utilization of resources,” he nods. The team has developed a pan-India vendor base for high cost & critical spares and, through reverse engineering, developed OPMs (Original Parts Manufacturers), which is paying them rich dividends.
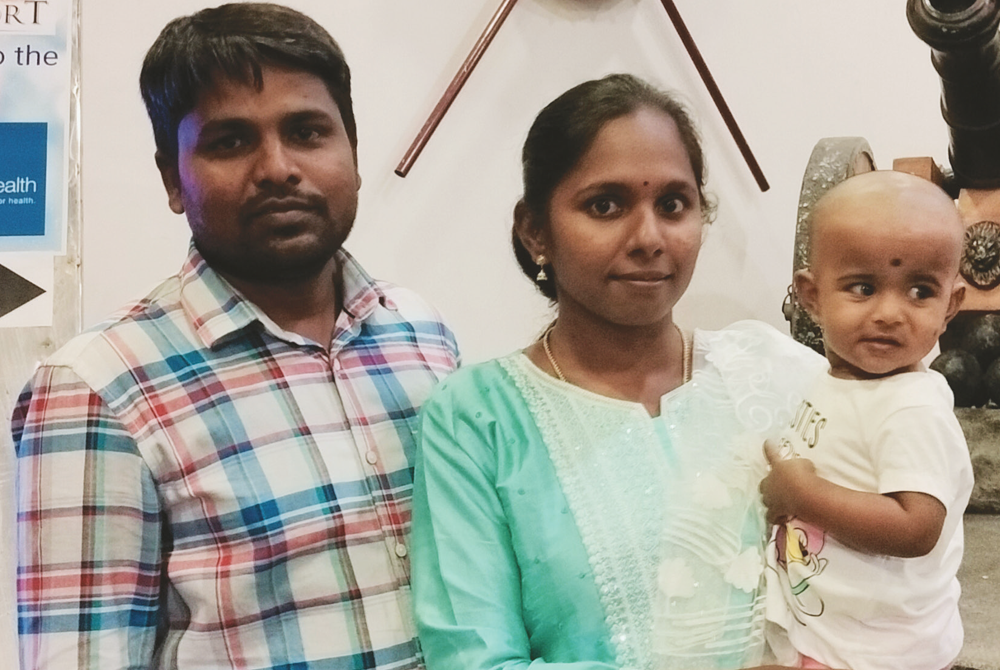
Technology is proving to be their able ally with IoT devices installed in all equipment to monitor asset utilization. The team has also reverse-engineered the TADANO 80T tyre-mounted crane knuckle joint and reeling drum by repairing it locally, resulting in significant cost savings and increased operational efficiency.
On his personal front, Sundar hails from Ranipet, Tamil Nadu, and his better half is Ranjitha, a homemaker. His life’s most precious moment was when their daughter, Sanjana, was born. To chill, he watches movies and plays cricket.