Driving operational efficiency to execute safely!
IKEA Project —
A front runner in out-of-the-box thinking
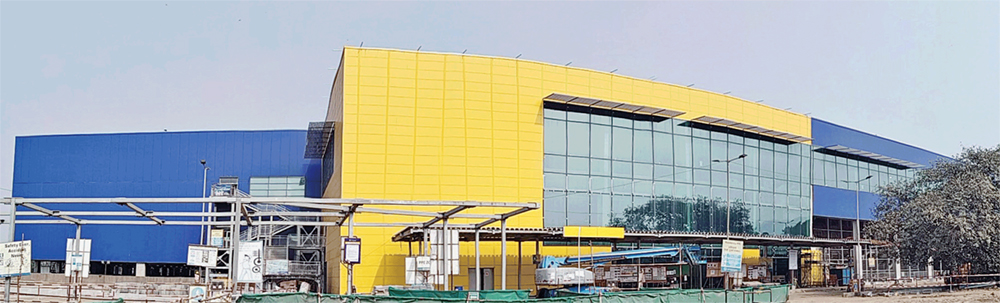
IKEA, a European multinational group that designs and sells ready-to-assemble furniture, kitchen appliances and home accessories, is one of the world’s largest furniture retailers. Having set foot on Indian shores with their first store in Hyderabad, IKEA has mandated L&T to build their second in Navi Mumbai spread over approximately 96,250 sq. m that will feature two levels of retail stores, one level of double height warehouse with a separate section for Food & Beverage, two levels of parking, all of which will sit over a total built-up area of 12.45 lakh sq. feet. “The standards of delivery are set in stone,” shares Project Manager, Rajesh Srinivasan, “and we have to live up to international standards. Our EHS performance, touch wood,” he taps his head, “has been excellent because we have successfully pre-empted hazards by identifying and mitigating them.” Their strategy has paid rich dividends thus far for they have been able to achieve efficiency across a range of operations including handling and erection of structural columns, trusses and connecting members, handling of hollow core panels, facades, table formwork and rebar, lifting, shifting and fixing roof panels.
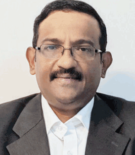
The standards of delivery are set in stone and we have to live up to international standards. Our EHS performance, touch wood, has been excellent because we have successfully pre-empted hazards by identifying and mitigating them.
Rajesh Srinivasan
Project Manager
Collaborate to eliminate
“We collaborate to eliminate,” declares Dr Sanjai Kumar Srivastva, EHS Head – North, B&F IC, who till recently was the EHS Head at the project, having since handed over the mantle to Ventaka Ramaraju Potuuri. “By involving as many people from the project as possible, we evolved an inherently safer thinking that helped us especially during the developmental stage to put together a sound method statement, identify hazards, assess risks and select the right, most convenient and safest method of work.” The question posed to everyone at site was: Can I eliminate risk by adopting the right tools and processes? While sky was the limit to suggest controls, the basic ground rules were that they should be simple, easy to adopt and not impede work progress. Sanjai and his team have successfully eliminated several hazards, in some cases smartly substituting with less hazardous equipment and tools, in others, putting in place well-designed engineering controls to achieve best results.
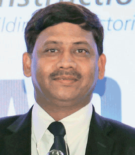
By involving as many people from the project as possible, we evolved an inherently safer thinking that helped us especially during the developmental stage to put together a sound method statement, identify hazards, assess risks and select the right, most convenient and safest method of work.
Dr Sanjai Kumar Srivastva
EHS Head – North, B&F IC
Smart solutions to handle huge and tricky erections
Lifting 3523 MT of heavy, structural steel members is a Herculean task with several attendant dangers. To lift these steel members of different sizes and dimensions, the team designed special lifting brackets. A detailed methodology covers all activities involved, lifting plans are prepared for each lifting sequence and permits are mandatory for all lifting activities. “Apart from the normal checks, we only use boom lifts to fix nuts and bolts or welding work for the structure,” informs Sanjai, “we do not allow tandem lifts and the tower operations are allowed only with an anti-collision device in place while to monitor tower crane activities, a ground monitoring system has been established in the computers of the safety office to see live operations and ensure safe functioning of the devices. It has helped a lot to prevent unsafe practices and promptly notice any unsafe condition during operation,” elaborates Sanjai. The deployment of signalmen with Walky-talky was another administrative control to further reduce the risk.
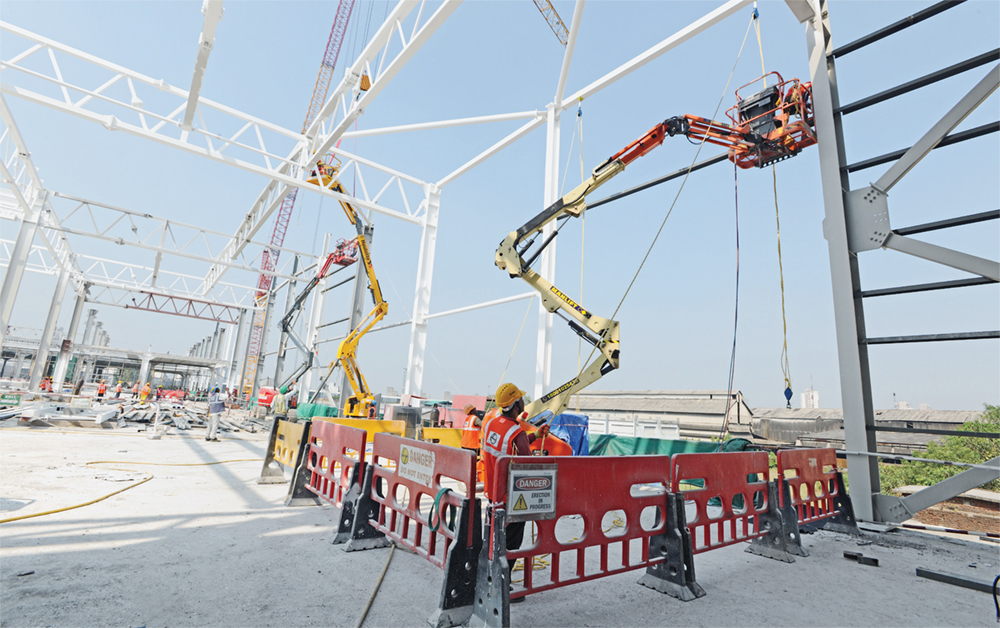
Erection of structural steel
Special lifting brackets were designed to lift, shift and erect 16 span size hollow core slabs, precisely fix them between two beams and place them on a projection of 150 mm. After the erection was complete, the edges were immediately protected by specially designed ‘L’ brackets and handrails to avoid fall from heights.
To fix structural members to support MEP equipment, at a height of approximately 12 m, the team fabricated special arrangements with a provision to rotate 360* mounted on scissor lifts that directly lift and align the members to the required height and location to fix them. Thus, the risk of fall of structural members or workmen from height was eliminated. “This has also helped us to avoid massive use of working platforms or scaffolds that both reduced cost and speeded up work,” Venkata chips in.
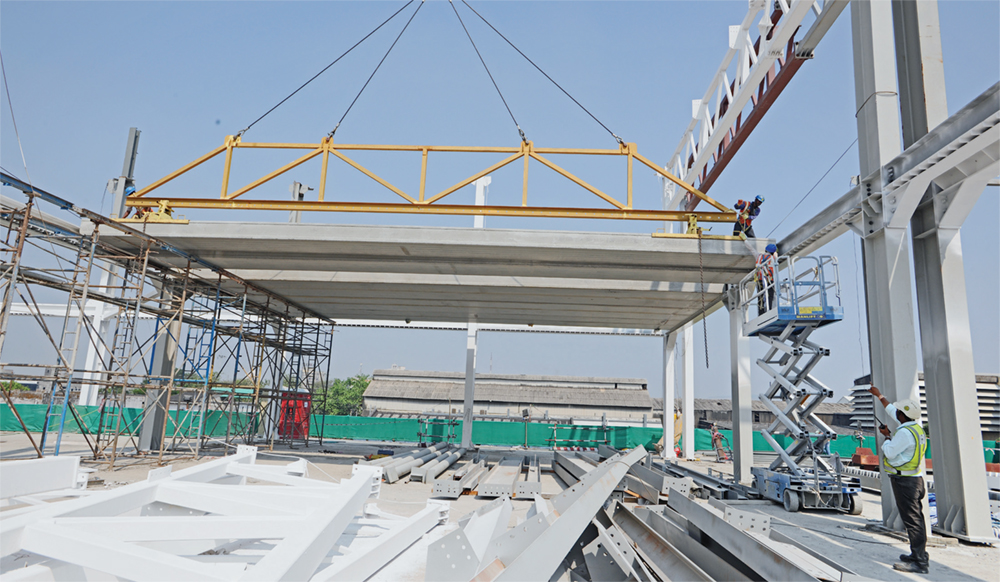
Hollow core erection
Façade erection was another challenge considering the 16 m span size and height of fixing. “The conventional method of tying and lifting the façade with web slings was risky while using scaffoldings was both time-consuming and a drain on our resources,” remarks Sanjai, “so we introduced, ‘Clad Boy’, a special, hydraulically operated lifting tool that once charged, could work for 8 hours at a stretch. The whole process was mechanized, human interaction was minimized resulting in greater efficiency and safety,” beams a satisfied Sanjai. Clad Boy was employed to erect façade panels too with similar excellent results.
The 12 m span size roofing panels posed some challenging questions due to their length, weight and height of fixing. After studying the task, the team decided to carefully lift each sheet, one by one, using a tower crane and web slings with only 3–4 trained workmen allowed to work at heights equipped with retractable fall arrestors and provision of separate wire rope lifelines for each workman based on design calculation to take the load in case of an accidental fall. “We had dedicated supervisors and safety inspectors throughout the activity to closely monitor the movement of the workmen, by adopting access controls at the roof top,” adds Sanjai.
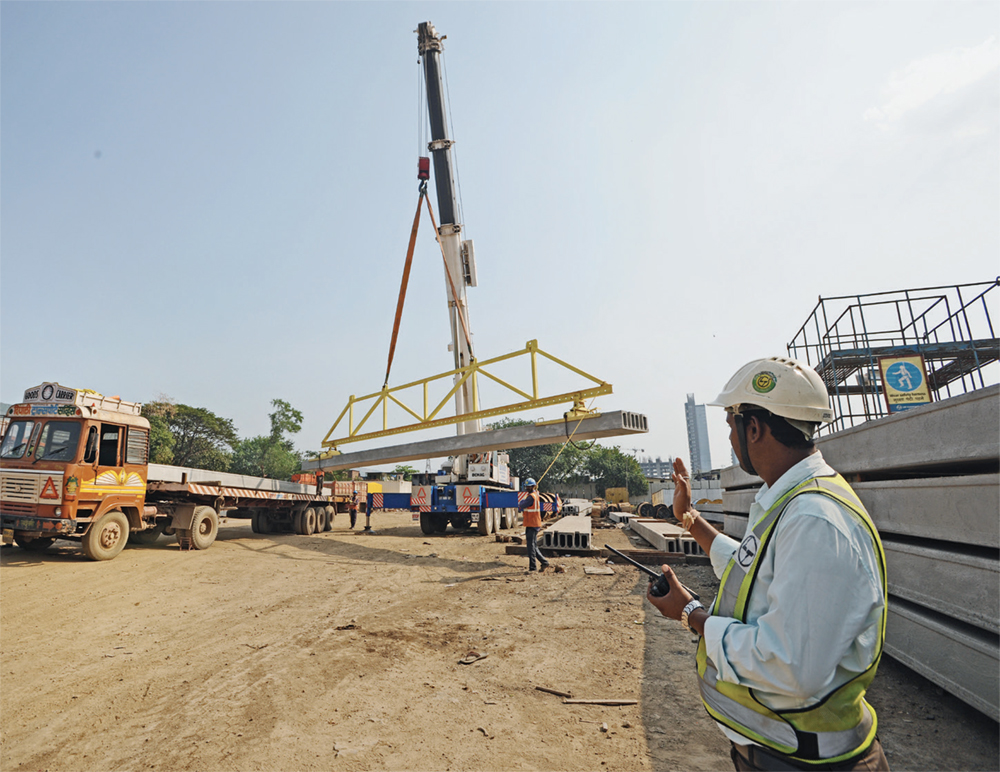
Hollow core handling
Handling table formwork & rebar caze
To address the hazard of both conventional and large area tables toppling while shifting or de-shuttering, Sanjai and team instituted a SOP that ensured that all shuttering works were only carried out as per approved schemes, method statements and HIRA with workmen given on-the-job training. Apart from a host of other regulations, a safety inspection checklist is meticulously followed right through the exercise.
Handling of rebar was another demanding task for as Venkata shares, “not only was there a massive amount of reinforcements for us to handle at site but it is always a fast track job so we have the added pressure to do it a lot quickly and safely which we succeeded by using special lifting brackets to lift the steel caze tied at the ground to reduce massive rebar handling and speed up work. This innovation has not only enhanced productivity but has tremendously reduced agronomical / handling risk to workmen.”
That the site has already clocked 6.5 safe million man hours is obviously a matter of great pride for Rajesh, Sanjai, Venkata and team and also are the several awards the site has won for its impeccable EHS performance. The site was recognized as the ‘Best Commercial Project of the Year 2019’ by National Infrastructure & Construction; it won the Global Safety Award (Platinum — the highest category) from Energy & Environment Foundation for 2019, the CIDC Vishwakarma Award for Construction, Health, Safety & Environment – 2019 (Code 1), the Diamond Award in the Fame Safety Excellence Awards 2019 for ‘Safety Excellence’, the RoSPA Gold Award for Construction, Health, Safety & Environment 2019, the IISSM Security & Safety Excellence Award 2019 in the ‘Construction Safety’ category, the Shreshtha Suraksha Puruskar 2019 (Silver Trophy – National level; construction sector) from the National Safety Council of India (NSCI) and an appreciation award, again from NSCI – Maharashtra Chapter for a ‘meritorious performance in industrial safety.’ “We also won the first prize in the Annual EHS Awards among all CBA projects (medium size category) for 2019–2020,” adds a proud Sanjai.
As the team gallops towards finishing the project to hand over in the next couple of months, here is wishing them all the very best to keep both their efficiency and safety quotients soaring.
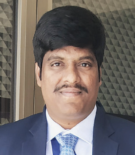
Handling of rebar was another demanding task, not only was there a massive amount of reinforcements for us to handle at site but it is always a fast track job so we have the added pressure to do it a lot quickly and safely which we succeeded by using special lifting brackets to lift the steel caze tied at ground to reduce massive rebar handling and speed up work. This innovation has not only enhanced productivity but has tremendously reduced agronomical / handling risk to workmen.
Venkata
EHS Head – North, B&F IC