Tunnelling to new heights
Surya Water Supply Scheme
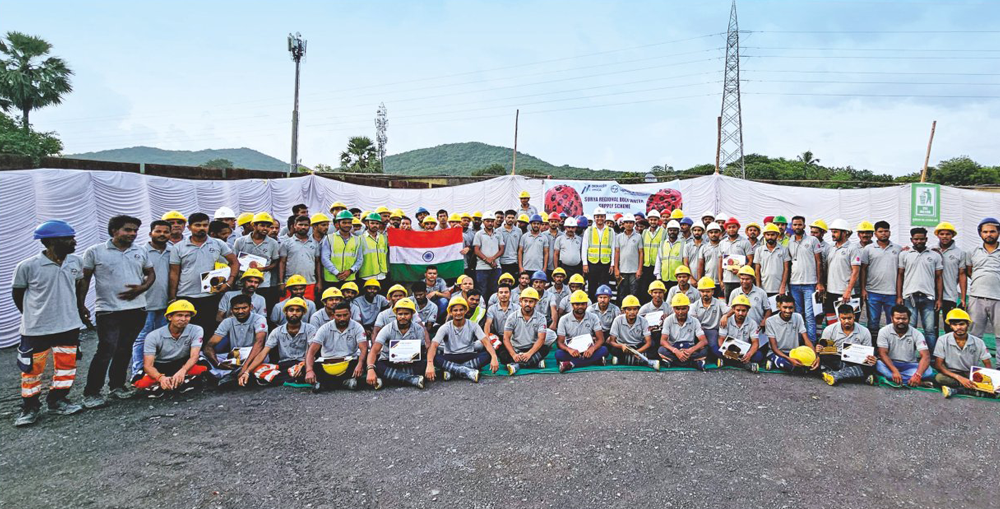
Project Director, Colin Nonis, and his team at the Surya Water Supply Scheme are thrilled at having successfully constructed two tunnels for the first time in WET IC. The 1.7 km long Mendhwankhind and the 4.6 km long Tungareshwar tunnels are both RCC segment–lined water tunnels with a finished internal diameter of 2.85 m and excavation diameter of 3.685 m.
Interestingly, we improved as we went along completing our second drive in 18 and a half months, reflecting a 32% increase in our rate of progress thanks largely to superior planning and the dedicated efforts of the crew, most of whom we had retained from the first drive.
Colin Nonis
Project Director
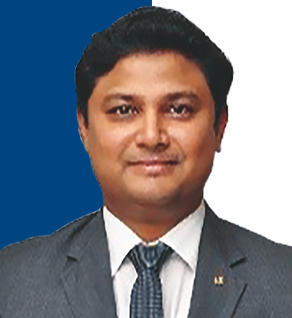
The longest tunnel with TBM constructed by L&T
Tracing their underground journey with TBM Vighnaharta, Engineer (EHS), Yadav Prince Avadhraj, shares, “Our first 1.7 km drive at Mendhwankhind started on March 27th, 2021, after lowering the complete machine in parts into the 34 m deep launch shaft and completed on December 26th, 2021, clocking a peak advance rate of 320 m per month and
20 m per day.”
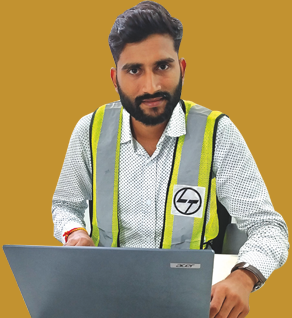
We were monitoring the working environment inside the tunnel by continuously checking the oxygen levels on an hourly basis with multi gas detectors and mini-oximeters, placed inside the TBM machine. Noise, illumination, and temperature levels were also being monitored every hour.
Yadav Prince Avadhraj
Engineer (EHS)
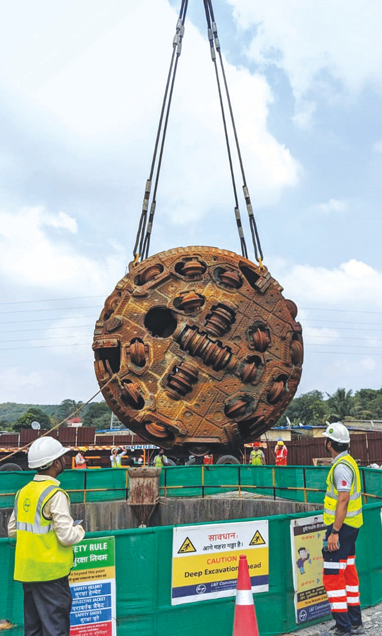
Their second drive at Tungareshwar kicked off on February 25th, 2022, and completed on Engineer’s Day, September 15th, 2023, negotiating a peak overburden of 180 m, clocking a peak advance rate of 319 m per month with an average advance rate of 250 m per month during the 4.6 km course.
“Of course, it was not easy,” Colin shakes his head, what with the various challenges of varying geologies, the dangers of water ingress, equipment reliability, and increased depth and length of the drive. “Interestingly, we improved as we went along completing our second drive in 18 and a half months, reflecting a 32% increase in our rate of progress thanks largely to superior planning and the dedicated efforts of the crew, most of whom we had retained from the first drive.”
Apart from having completed the longest tunnel executed by L&T with a TBM, the team is proud that they constructed a first-of-its-kind pressurized segmental tunnel for treated water in India for MMRDA, which will be key to deliver 218 MLD of potable water to the Mira Bhayandar Municipal Corporation to benefit some
16 lakh people.
A saga of challenges & control measures
To address one the most critical considerations of ensuring a safe and comfortable working environment inside the tunnel, the EHS team designed and deployed a proper ventilation system. “We were monitoring the working environment inside the tunnel by continuously checking the oxygen levels on an hourly basis with multi gas detectors and mini-oximeters, placed inside the TBM machine,” points out Prince. “Noise, illumination, and temperature levels were also being monitored every hour.”
The team controlled the entry and exit of personnel through a tally board that prevented any unauthorized entry into the tunnel. A token handed over at the entry easily identified whether the person was a visitor, staff, workman for the tunnel, or a bottom-shaft workman. A passenger hoist based on a rack-andpinion gear with limit switches was installed, and a man basket, designed as per EDRC-approved drawings, could safely carry up to 10 workmen in case of any emergency.
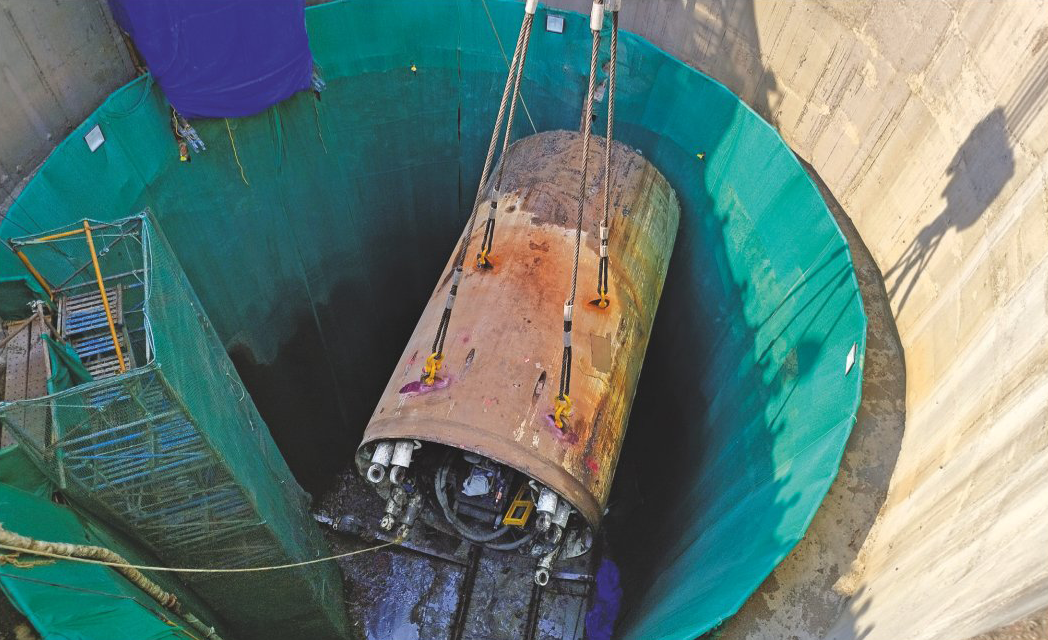
Inspections, maintenance of records, and using findings & learnings are vital to project success, and digitalization has strengthened their hand. “With View EHS, we manage all kinds of inspections, training records, raising UAs/UCs/UBs that gave us a one-point easy access to all records and comprehensive analyses for continuous improvement,” remarks Prince. Even their SEC & work permit systems are being implemented through View EHS.
Getting the right people with the right skill sets
One smart move to appreciably reduce their risk was to engage skilled workmen for tunnelling and train them regularly on a weekly and fortnightly basis on various aspects like EHS Alert training, SST training, & CWT training and through the Safety Ki Baat campaign. External agencies trained the workmen on specific topics. Mock drills were conducted every month about different emergency scenarios, and an Emergency Plan was developed that dealt with issues like flooding, release of hazardous gases, evacuation drills, being hit by a locomotive, medical emergencies, chemical spillage, electrocution, locomotive derailments, and more. “These drills bolstered the confidence of our workforce to deal with any kind of emergency scenario and perform efficiently during emergencies,” mentions Colin with a tight smile.
An IP telephone installed at the tunnel area facilitated easy communication, while walkie talkies with operators and riggers avoided miscommunication during site operations that were monitored from the Control Office through cameras.
Very often, good EHS performance depends on keeping it simple and doing the basics right. The Surya WSS team did so by conducting daily Pep Talks, executive walkthroughs, having dedicated paramedical staff and an ambulance readily available, driving campaigns for better housekeeping, minimizing waste, going green, and organizing occupational health checkups and skill medical tests as per the requirements of the management and IMS.
Apart from tunnelling, several auxiliary activities performed by the team during the initial phase included conducting extensive geotechnical investigations up to a depth of 200 m, preparing inlet shafts at both locations – 34 m deep at Mendhwankhind and 55 m deep at Tungareshwar – using the drill blast method, and erecting and dismantling the gantry crane.
It’s all about proper safety training
Imparting EHS training is a fundamental and non-negotiable aspect of responsible project management that equips workmen and the management with the knowledge and tools necessary to identify and mitigate potential hazards, ensuring the safety of all personnel involved in the project. EHS training not only reduces the risk of incidents, injuries, and costly delays but also helps construction teams stay compliant with rigorous safety regulations. Furthermore, it promotes a culture of responsibility and accountability, fostering an environment where everyone is committed to maintaining a safe workspace. By investing in EHS training, a project not only protects their most valuable asset – their workforce – but also enhances their reputation, reduces costs, and contributes to a sustainable and socially responsible approach.
The staff and workmen at a project are EHS inducted at the initial stage. Activity-specific training schedules are developed, training provided, and certified professionals engaged for tunnel-specific training as and when required. Safe Authorization Procedures pro-actively identify and engage with workmen and staff to comply with the required skill sets for any activity identified as per HIRA & EAISR at the site.
A Workforce Management Centre, EHS induction room, and training van for staff and workmen have been established at site, and on successful completion of the Skill Authorization Procedure, a Skill Authorization Pass (SAP) is issued to the competent workman/staff for identified activities like excavation, working at heights or in confined spaces, electricals, material handling, etc.
WE CARE (Workforce and Environment Protection Programme) is another comprehensive initiative designed to safeguard both workforce and the environment across WET IC projects that integrates strategies and practices prioritizing the well-being of the workforce while minimizing the environmental impact of operations. It includes elements such as thorough implementation of Operational Control Procedures (OCPs) and Zero Tolerance Cards (ZTCs), imparting safety training, the use of protective equipment, health and wellness initiatives, and ergonomics to enhance employee safety and health. Simultaneously, it incorporates eco-friendly practices, waste reduction, resource conservation, and sustainable procedures to reduce the ecological footprint. The programme’s overarching goal is to create a harmonious balance between human welfare and environmental sustainability, promoting a responsible and ethical approach towards operations.
Completing such a critical activity has put Colin, Prince, and the Surya WSS team on the high road to speedy completion of their tough project, but what must have delighted them more is the praise and accolades they have received from their client for their sterling performance.