When the stakes are high, sites rise even higher! WET IC’s IASTW Qatar project wins
Safety Award — 2021
WET IC’s Industrial Area Sewage Treatment Works (IASTW) Phase 3A Expansion Project executed for the Public Works Authority (ASHGHAL) Qatar has clocked more than 4.5 million safe man-hours since start of the project in November 2018. It has won the RoSPA Gold Award and the Annual EHS Trophy for two consecutive years, 2020 & 2021, and therefore it seems almost natural that it emerged as the project that showcased the best safety standards across L&T Construction to be recognized with the Safety Award 2021.
Doubtlessly, the recognition is a matter of great pride and honour for both Project Head, S Vishal and EHS Head — Water International BU, Chandrashekar Keshav Kulkarni (CK), more so as they had to contend with challenging foreign conditions, the uncompromising Qatar construction standards & EHS strictures laid down by the client, the IMS procedures, the unforgiving climatic conditions and, of course, the disruptions caused by the pandemic.
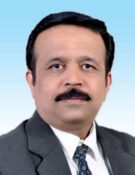
We prepared site-specific method statements to define the scope and methodology of each activity, and risk assessments were conducted for all activities, taking the inputs from the method statement, as per procedure, which were then constantly reviewed and revised as per the requirements.
Chandrashekar Keshav Kulkarni
EHS Head – Water International BU
The project was a Design and Build Contract to create a new sewage treatment facility — IASTW PHASE 3A Expansion — at the existing IASTW to increase the plant’s capacity from 60,000 cubic meters per day to 90,000 cubic meters per day and accommodate the rising demand from the increasing population in the Doha Industrial Area. For Vishal and team, the scope involved designing, constructing, manufacturing, FAT testing, supplying, installing, testing, maintaining the warranty of all items detailed in the project for a 30,000 m³ /d advanced Sequencing Batch Reactor (SBR) activated sludge plant equipped with enhanced mixed liquor recycling process within the biological reactor basin.

CK’s work started in earnest as soon as L&T was awarded the mandate. “We prepared site-specific method statements to define the scope and methodology of each activity, and risk assessments were conducted for all activities, taking the inputs from the method statement, as per procedure, which were then constantly reviewed and revised as per the requirements,” he shares the contours of his tough assignment. Some of the other major challenges the team faced were subcontractor management, employee turnover due to COVID-19, managing night works during pre-commissioning & commissioning stages, working at heights, deep excavations and lifting activities.
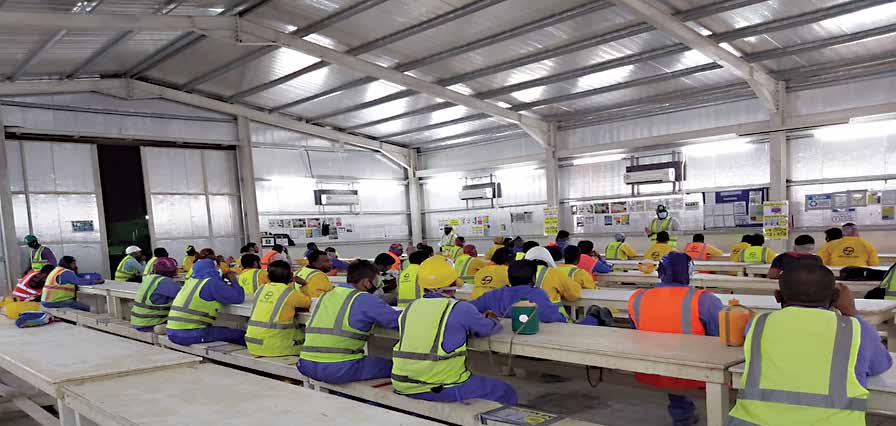
Think safe. Work smart.
“Safety is never an accident,” reminds KS Sudheesh Kumar, Head — EHS, WET IC. “It is the result of a deep understanding of the risks and hazards involved, careful planning followed by meticulous execution enabled by the VIEW EHS digital platform, and taking everyone along with you in the implementation. This is what made the big difference at our IASTW project.”
Due analysis revealed to the team that fall of people and material from height was one of the major safety challenges; hence, approved design drawings were used to erect temporary height work structures. “We ensured adequate working platforms, access/egress, handrails, safety nets, lifelines and full body harnesses,” informs Saif Saeed Bagdadi, Assistant Manager — EHS, who was the Safety In-charge at ground zero. Height work permits & applicable checklists were strictly adhered to, and third-party trainings and height pass tests were mandated for all workmen at heights.
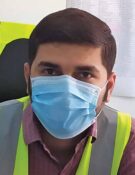
We ensured adequate working platforms, access/egress, handrails, safety nets, lifelines and full body harnesses.
Saif Saeed Bagdadi
Assistant Manager – EHS
Other key EHS challenges were excavation and confined space entry. For all excavation works, apart from HIRA and SOP, EDRC-approved sloping/benching and shoring were implemented across sites. For confined space entry work, third-party training and skill authorisation passes were issued to entrants and attendants. At a defined frequency, mock drills were conducted to ensure effectiveness of work at height, excavation, and confined space entry control measures.
Safety assumes even greater importance at night and the team ensured adequate electrical safety measures, traffic management and permit systems for smooth execution. Illumination levels were monitored with lux meters, and noise levels monitored with adequate control measures to avoid creating a nuisance to the society in the vicinity of the site. With adequate staffing, night shift workers could take breaks and relax during their shift.
Relative humidity gradually increases during the Qatar summer till it reaches stifling levels by August and September. Rainfall doesn’t typically occur during summer; however, humidity levels can touch between 40% and 60%. A heat stress management plan was rolled out to avoid heat-related emergencies like heat cramps, heat exhaustion, and heat/sun strokes. “We continuously monitored the Heat Stress Index, adjusted work timings, air-conditioned the rest areas, and provided ice-making machines & electrolytes for all workmen,” adds Saif, almost wiping the sweat off his brow.
Covering all bases
All workmen at site had to undergo EHS inductions, medical check-ups, and skill pass procedures. A robust access control system restricted all unauthorized entries, and no work began without risk assessments, toolbox talks and SEC Cards.
Prequalification guidelines were set for sub-contractors, with EHS requirements included in the works order which the contractor had to accept on arrival at site. It was the Planning Engineer’s responsibility to share with them the EHS code of practices and inculcate the EHS requirements. CK adds that EHS performances of subcontractors were monitored every month to reward good performers and reprimand poor performance.
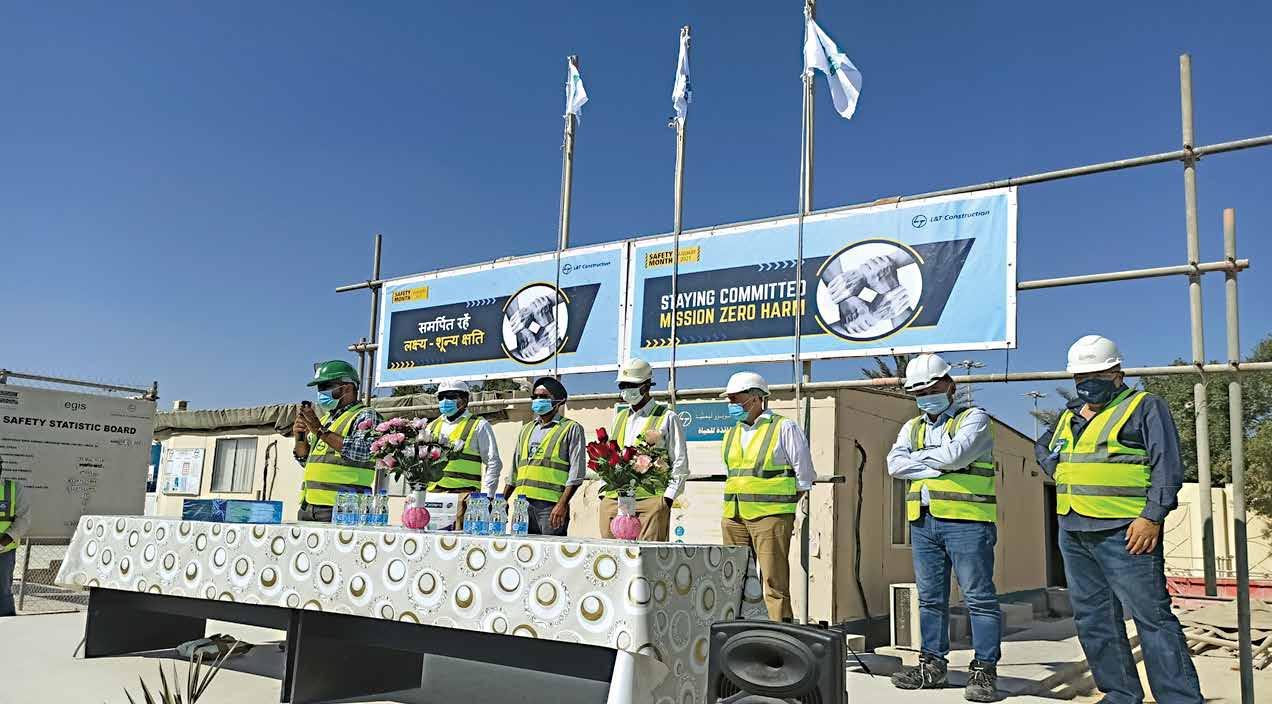
An EHS Committee with members comprising project leaders, workmen representatives and supervisors participated in risk assessments, inspection programmes, incident investigations and met every month to review EHS KPI performances.
“We introduced a training matrix linking competency and capability requirements at the planning stage itself,” shares CK. “Training needs were identified and incorporated into our project EHS Plan.” The project had well-established training facilities with safety posters prominently displayed. In-house and external EHS trainings were organized based on need analysis. “We established a Safety Theme Park, where safety information and various dos and don’ts of safety practices were displayed, and it was an important part of our induction plan,” adds CK, proudly.
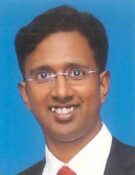
Effective implementation of View-EHS enabled us to adhere to inspection and monitoring programs, observation programs and permit systems without any use of paper or human intervention.
S Vishal
Project Head
EHS rewards and recognition programmes effectively change and/or reinforce safe employee behaviour. As a practice, EHS compliant employees, workmen and sub-contractors were identified and rewarded to enhance safety culture and realise Mission Zero Harm.

Digitalization makes a difference
Digital solutions like View-EHS & MS Teams helped the project maintain EHS requirements despite the impact of the pandemic on EHS functions. “Effective implementation of View-EHS enabled us to adhere to inspection and monitoring programmes, observation programmes and permit systems without any use of paper or human intervention,” points out Vishal. “Further, with the Power BI Dashboard analysis, we were able to visualize data in real time to gain valuable insights and track implementation across sites.” Microsoft Teams came in handy for trainings as well as meetings to bring people together to collaborate, communicate and share content.
Various health awareness programmes and a state-of-the-art health centre within the project premises effectively monitored and controlled employee health.
In the final analysis, WET IC’s Industrial Area Sewage Treatment Works Phase 3A Expansion Project proved that it is not enough to just know about safety, it is imperative to practice it.
Hearty congratulations to the entire team for their wonderful EHS performance that is deserving of the highest Safety Award within the organization.