A HIGHWAY BUILT FOR SPEED, SPEEDILY.
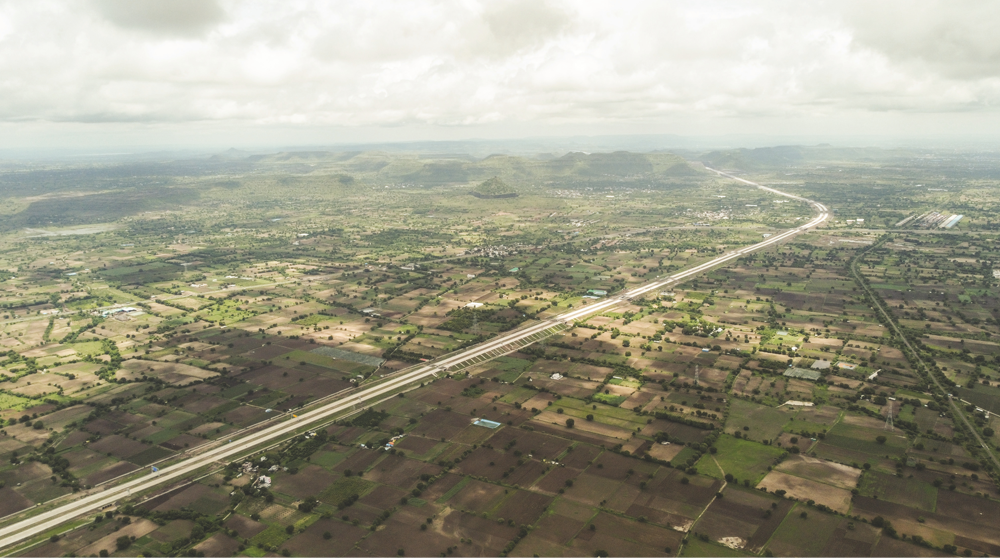
MUMBAI NAGPUR EXPRESSWAY PROJECT
The Mumbai Nagpur Expressway or the Hindu Hridhay Samrat Balasaheb Thackeray Samruddhi Mahamarg is expected to cut the road travel distance between Mumbai to Nagpur by half. RREC’s Road & Bridges BU constructed Package no. 10 of this super communication project from KM 444+845 to KM 502+752, village Fatiyabad to village Surala section in Aurangabad District, in double quick time and won L&T Construction’s Timely Delivery Award 2022 for their efforts. A stretch of the project between Nagpur – Shirdi has already been inaugurated by the Hon’ble Prime Minister Shri Narendra Modi on 11th Dec’ 2022.
An overjoyed Project Director, Rongali Srinivas, when receiving the award from SNS mentioned that “We had decided to complete the project on a fast-track mode on the day of the ‘Kick off’ meeting held at HQ-Mumbai and extending the momentum beyond the meeting room, everyone at project site believed that the project could be completed within the schedule.” And they did.
“We had decided to complete the project on a fast-track mode on the day of the ‘Kick off’ meeting held at HQ-Mumbai and extending the momentum beyond the meeting room, everyone at project site believed that the project could be completed within the schedule.”
Rongali Srinivas
Project Director
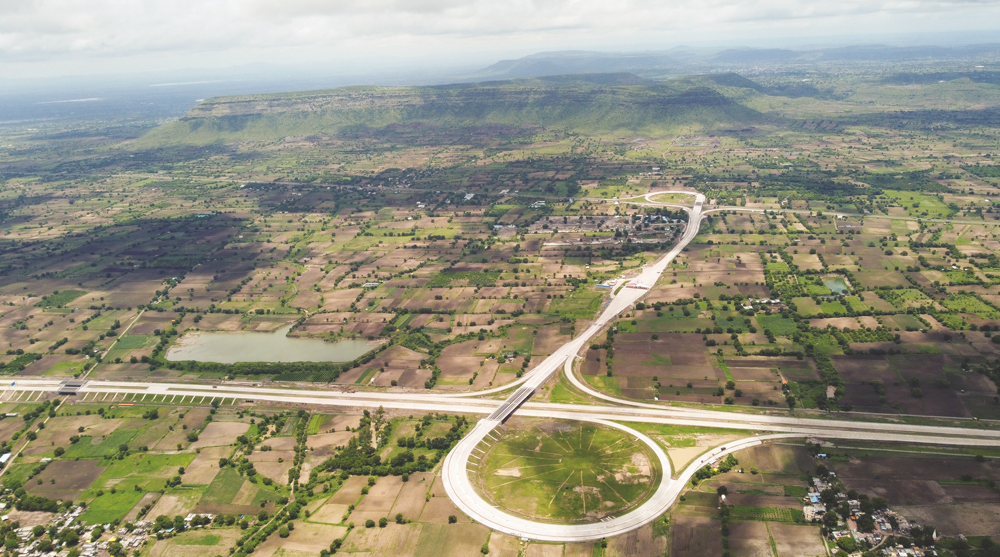
The MNEP in numbers
- 58 km of 6 lane rigid pavement
- 151 structures including
- 83 culverts
- 4 major bridges (including an iconic one)
- 14 minor bridges
- 19 vehicular underpasses
- 20 light vehicular underpasses
- 1 vehicular overpass
- 9 canal bridges
- 3 interchanges
- 1 railway over bridge
- Toll plazas
- 12 km of service roads
- 6 km of cart tracks
- Minor structures
Start running … and keep running till completion
The project team’s sense of urgency is best illustrated by the fact that they utilized the 2-month window they had between LOA & NTP and invoiced in the first month of NTP. While the clearing and grubbing activities were completed before NTP to assess the real availability of land, the team parallelly mobilized the batching plants, camp site, set up crusher plants and identified quarries with all statutory compliances.
We finalized major vendors for the earthwork and quarry crushing to take up works on the first day of NTP while our design team rapidly completed 80% of the plan and profile of the highway,” shares Abhinav Agrawal, DGM-Planning. “Identifying potential earthwork contractors and sourcing 175 lakh cum were huge challenges that kept us awake at night. The alignment of the road passes through extremely undulated topography which is why so much earthwork was involved but thanks to our HQ-Procurement team, we managed by deploying 30+ agencies parallelly along the project stretch and sourcing government borrow areas with the support of the District Collector.”
“We finalized major vendors for the earthwork and quarry crushing to take up works on the first day of NTP while our design team rapidly completed 80% of the plan and profile of the highway.”
Abhinav Agrawal
DGM-Planning
The scope of MNEP
- 175 lakh cum earthwork
- 5.75 lakh cum pavement quality concrete (PQC)
- 6.75 lakh cum of concrete (Dry lean concrete and structural concrete together)
Timely designs and drawings
A pre-requisite to timely completion of a project is the ready availability of design and drawings at site, after which other activities like material sourcing, identifying specialized vendors, sub-contractors, machinery, and other resources can be planned. “Working to a plan, the majority of all designs were completed within 6 months of NTP,” recalls Priyadarshan Shanmugasundaram, Assistant Construction Manager (Design Coordinator). “Then, to fast track the erection works of the ROB, instead of sending the documents via courier, we visited railway officials at Nanded and Hyderabad junctions to sort out the design issues and set the ball rolling.”
“Working to a plan, the majority of all designs were completed within 6 months of NTP. Then, to fast track the erection works of the ROB, instead of sending the documents via courier, we visited railway officials at Nanded and Hyderabad junctions to sort out the design issues and set the ball rolling.”
Priyadarshan Shanmugasundaram
Assistant Construction Manager (Design Coordinator)
Efficiently crushing to speed
To meet the project’s requirement of approximately 45 lakh MT material including 12 lakh MT of granular subbase material and 23 lakh MT of aggregates, the team set up 7 crusher units and completed the scope well within the scheduled timeline. “Liaising with the local villagers and government officials was not as easy as we thought,” frowns Sawant Shrikrishna Bhagwat, Senior Engineer (QMC), “requiring a separate task force team who acted smartly for instant solutions so that crusher operations were running around the clock. At the peak hours, we had nearly 10 lakh MT stock of aggregates,” he mentions.
“Liaising with the local villagers and government officials was not as easy as we thought, requiring a separate task force team who acted smartly for instant solutions so that crusher operations were running around the clock. At the peak hours, we had nearly 10 lakh MT stock of aggregates.”
Sawant Shrikrishna Bhagwat
Senior Engineer (QMC)
With strict and continuous monitoring and control of crushing operations along with the planning department, the team ensured that even fraction wise requirements were readily available as per the project progress plan.
Smart logistics for smart projects
Another challenge for the team was to transport the 45 lakh MT of GSBs and aggregates, and 12.5 lakh cum of concrete from source to destination across a greenfield project to maintain progress. “Identifying stock yards, maintaining enough tippers and trained drivers and operators, handling the issues of the local villagers and controlling the dust were some aspects of logistics management,” remarks Dhiraj Kumar Mishra, Assistant Supervisor. “We multipurposed tipper utilization like transporting aggregates and GSB during the daytime and PQC during the night to retain the subcontractors at project sites as per the project requirements.”
“Identifying stock yards, maintaining enough tippers and trained drivers and operators, handling the issues of the local villagers and controlling the dust were some aspects of logistics management.”
Dhiraj Kumar Mishra
Assistant Supervisor
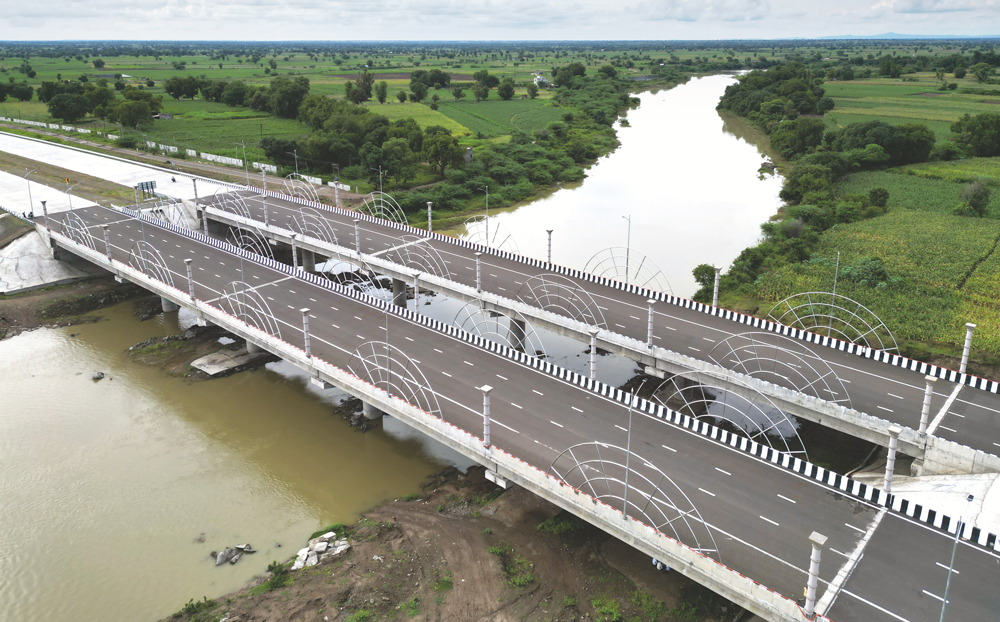
Keeping the P&M up and running right through
The entire P&M department decided to ensure “Zero Breakdown” machine hours to support the fast-track project which was a tough ask considering their huge machinery setup of 10 batching plants, 7 crushers, 2 16 m-width PQC pavers, and 4 Volge pavers along the 56 km stetch. In fact, the 16 m wide, Wirtgen-SP1600 was used for the first time in India. “Scheduled maintenance for all major machinery was carried out as per requirements and predictive maintenance with our rich machinery experience,” informs G Soumen, Manager (ELEC), P&M. “Apart from our own machinery, we consumed 4,000+ machine months for the total project duration, ensuring that project progress was never affected due to machine breakdown.”
“Apart from our own machinery, we consumed 4,000+ machine months for the total project duration, ensuring that project progress was never affected due to machine breakdown.”
G Soumen
Manager (ELEC), P&M
A special team within the P&M department was formed armed with mobile maintenance vans to ensure that assistance was available within 60 minutes. Timely deployment of electrical utility shifting agencies also helped. Finishing activities like highway illumination, electrical connection at the toll plazas, and solar lighting arrangements were executed
within schedule.
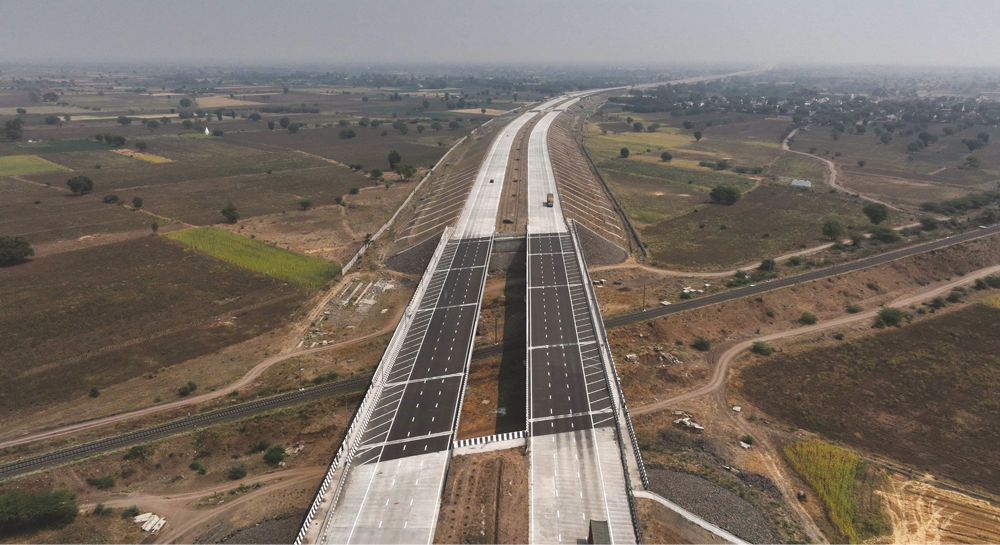
No compromise on quality or safety
The entire project stretch is of PQC and PQC laying conditions are heavily influenced by weather conditions like high ambient temperatures, wind speeds, etc. “First time, first job was mandatory for all,” smiles Pendota Shashi Chandra, Manager (QA/QC). “To ensure the desired quality and zero rework at site, we laid out our total PQC between 20:00Hrs-05:00Hrs with complete tracking and monitoring of the weather during the paving and decisions were taken accordingly.” Pendota is proud that this approach earned high respect from the client and stood them in great stead at other packages too.
“First time, first job was mandatory for all, To ensure the desired quality and zero rework at site, we laid out our total PQC between 20:00Hrs-05:00Hrs with complete tracking and monitoring of the weather during the paving and decisions were taken accordingly”
Pendota Shashi Chandra
Manager (QA/QC)
The team employed a few other initiatives to accelerate construction to achieve the required strength within 24 hours by having precast concrete boundary walls and micro silica in high grade concrete (M50) for precast girders. Geo cell was utilized in RE wall slope protection, geo composite / textile for drainage in the RE wall, structure backfill locations against the filter media and manufactured crushed sand in the PQC mix to prevent cracks.
On the EHS front, the project has won the British Safety Council’s
Safety Award 2020 and a RoSPA Gold to boot.
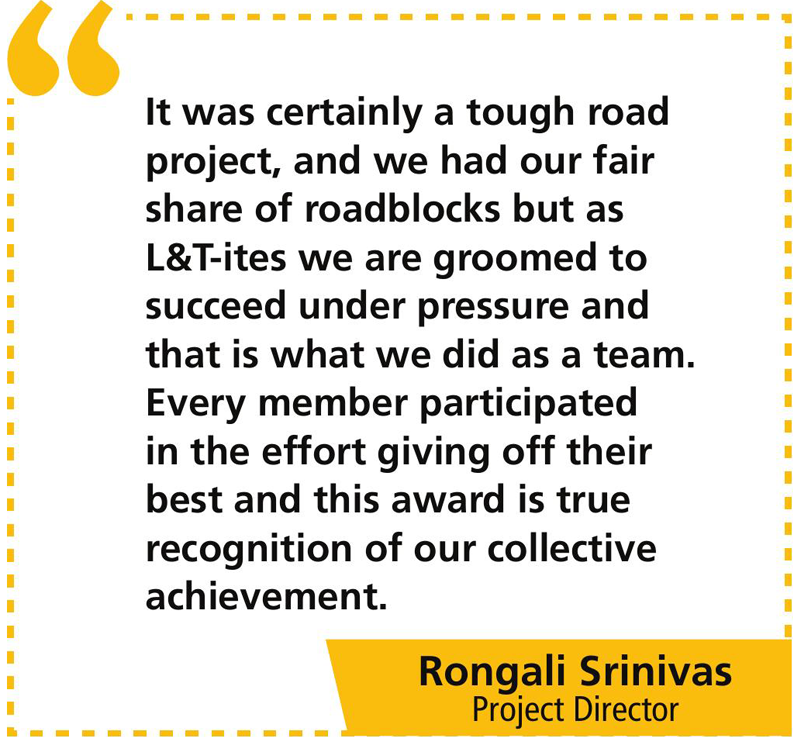
Retaining and remobilizing labour during and post the pandemic were big hurdles that the team had to overcome. “We were very confident that GOI would grant special permissions for remote infrastructure projects to resume the works based on which we retained our workforce at site,” mentions Sathvic S Shetty, Executive (Accounts). This ploy and looking after their welfare helped the project to not lose steam during and post the lockdowns.
“We were very confident that GOI would grant special permissions for remote infrastructure projects to resume the works based on which we retained our workforce at site.”
Sathvic S Shetty
Executive (Accounts)
“It was certainly a tough road project,” grins Srinivas, “and we had our fair share of roadblocks but as L&T-ites we are groomed to succeed under pressure and that is what we did as a team. Every member participated in the effort giving off their best and this award is true recognition of our collective achievement.”