OVERCOMING SOME ‘TALL’ CHALLENGES TO DELIVER A QUALITY PROJECT TO BENEFIT
3 LAKH+ PEOPLE.
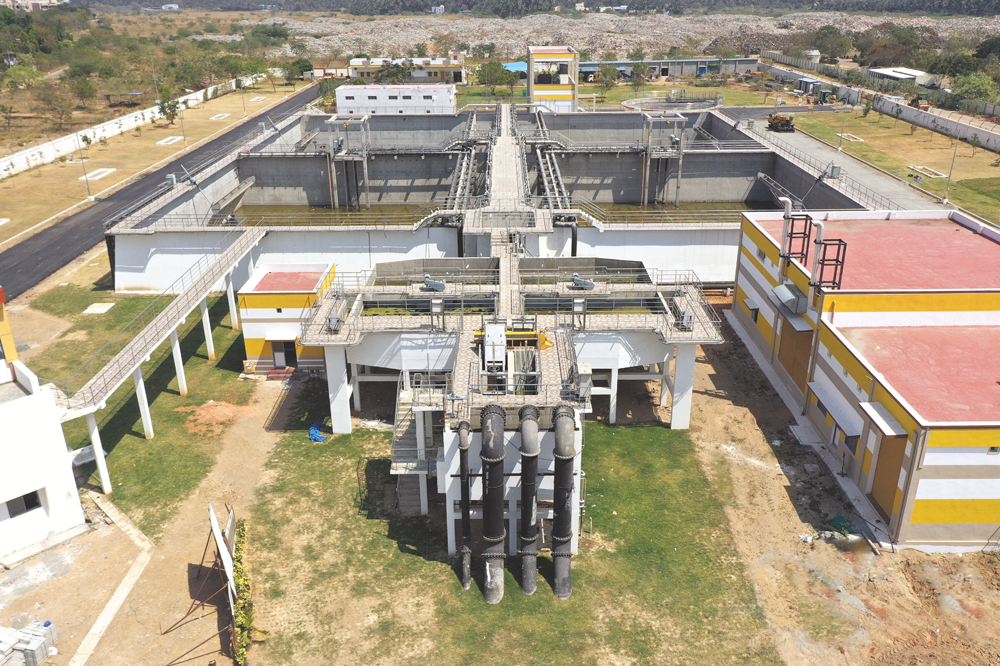
THE COIMBATORE UGSS STP PROJECT
The project aims to provide an Underground Sewerage System (UGSS) to the Kurichi and Kuniyamuthur Area Wards 87 to 100 of Coimbatore Corporation-Phase-II in Coimbatore District, Tamil Nadu, that will play a crucial role to ensure proper sanitation and a clean & hygienic environment for the 3+ lakh residents.
The contours of the project
One of the key components of the UGSS project is the collection system, comprising 434 km of sewer lines to collect all the sewage and wastewater from the houses to be sent to the pumping station. The 49 km pumping main will then take the sewage to the treatment plant where it will be treated and disposed of safely as per the NGT norms set by the Ministry of Environment & Forests, Government of India.
The project involves the construction of 10 pumping stations and 19 lift stations, equipped with pump sets to pump the sewage to the treatment plant. The lift stations will lift the sewage to a level from where it can be pumped efficiently. Manholes are another key component of the project with 17,750 of them, to be placed at various points along the collection system to provide access to the sewerage system for maintenance and repair. 40,000 House Service Connections will connect houses to the sewerage system for the wastewater to be transported to the treatment plant for disposal. In addition to these components, the UGSS project team must construct a 30.53 MLD Sewerage Treatment Plant to treat the sewage before it is disposed of, to reduce the risk of environmental pollution.
“No project is without its fair amount of challenges,” says Project Director, C Rajavel, with a tight smile, “and, rest assured that we have had more than our fair share of challenges, executing in the heart of a bustling city, and facing enormous Right of Way issues. We have, however, taken these in our stride and with several innovations and meaningful initiatives have ensured success, always keeping Quality as our number one priority,” he says, expressing his happiness at the mention that his project received from the awards committee for their Quality performance.
“We have had more than our fair share of challenges, executing in the heart of a bustling city, and facing enormous Right of Way issues. We have, however, taken these in our stride and with several innovations and meaningful initiatives have ensured success, always keeping Quality as our number one priority.”
C Rajavel
Project Director
Tall complexities. Taller solutions.
Single lift concrete wall: One of the most significant challenges the project team had to face was to construct a strong and durable 7.2 m tall concrete wall. “The standard height for such walls is only 1.2 m,” points out a concerned Assistant Manager QA/QC, B Saadath Hussain. “Constructing at a height of 7.2 m involves multiple lifts apart from the danger of leakages and compromising the quality of the wall.” To start with, the team presented a mock-up concrete wall to the client, the Tamil Nadu Water Supply & Drainage Board, and casted the entire structure, panel by panel, in a single lift to prove our point. “Once the client was convinced, we set about constructing the wall in a single lift, attempted for the first time in our Waste Water BU,” shares a determined Saadath.
“Constructing at a height of 7.2 m involves multiple lifts apart from the danger of leakages and compromising the quality of the wall. Once the client was convinced, we set about constructing the wall in a single lift, attempted for the first time in our Waste Water BU.”
B Saadath Hussain
Assistant Manager QA/QC
Another challenge was that the top width of the wall was only 200 mm, while the boom placer mouth was 230 mm, a mismatch that was overcome by using a tremie-like assembly, exclusively fabricated in different heights and used for concreting.
“The entire sequence of activities was clearly worked out and planned considering time and cost optimizations,” remarks Assistant Construction Manager & Planning In-charge, A Ramachandran. “Our quality engineer and the site engineering team were of great support to execute the activities that has helped us to reach where we are now!”
“The entire sequence of activities was clearly worked out and planned considering time and cost optimizations. Our quality engineer and the site engineering team were of great support to execute the activities that has helped us to reach where we are now!”
A Ramachandran
Assistant Construction Manager & Planning In-charge
“Our innovations have given several tangible and intangible benefits,” reveals a delighted Engineer (Civil), Apurba Mondal. “An improved surface finish, a simplified process, time saving, better workmanship, enhanced customer satisfaction, and improved productivity.”
“Our innovations have given several tangible and intangible benefits: an improved surface finish, a simplified process, time saving, better workmanship, enhanced customer satisfaction, and improved productivity.”
Apurba Mondal
Engineer (Civil)
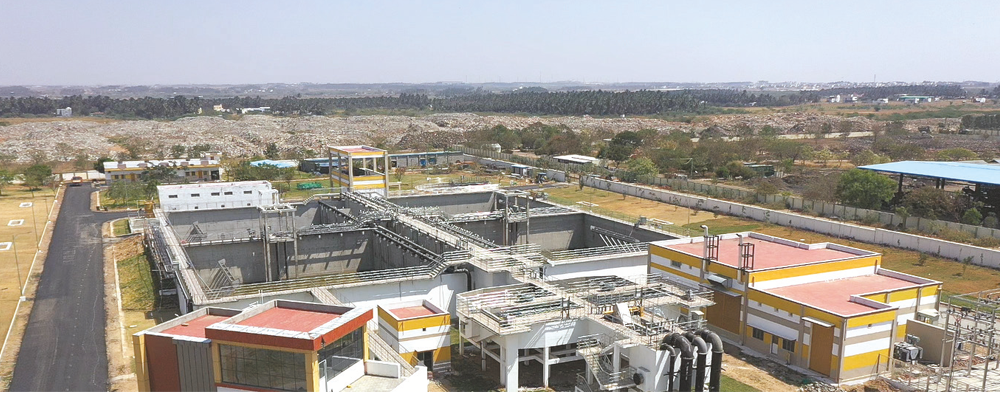
There is always the fear of failure in the face of multiple challenges, but the team has rallied behind Rajavel with a common goal to deliver the project to top Quality. “We meticulously micro-planned before implementation and all departments fully supported the execution team,” says a satisfied Rajavel. “In fact, one of our biggest challenges during implementation has been to convince conventional-minded customers for which, we prepared mock-ups to show the desired results and build their confidence.” A brainstorming session at the site involving all internal stakeholders helped everyone to be on the same page and to clearly understand the responsibilities assigned to each of them. “By recognizing, the efforts to implement new initiatives we are ensuring that they are sustained,” adds Rajavel.
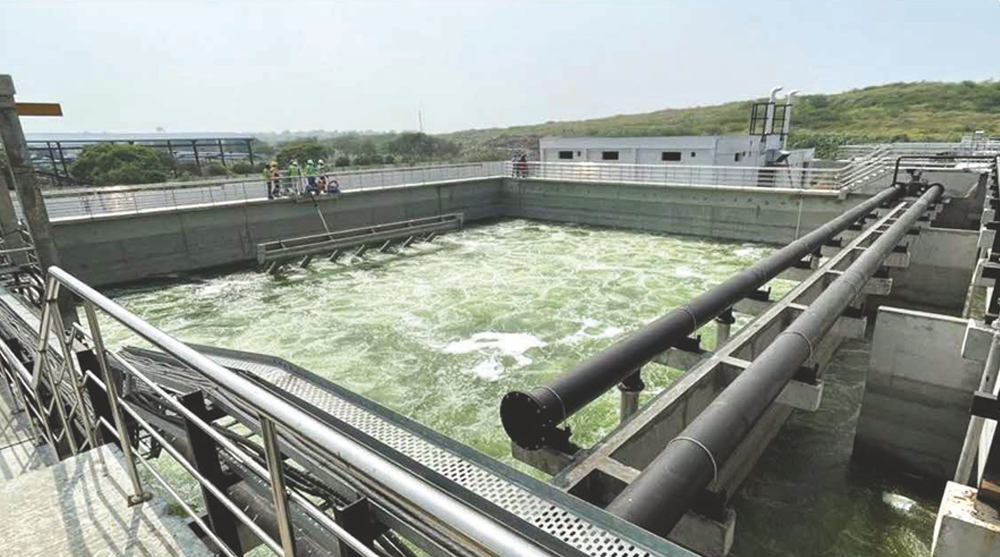
Real-time Kinetic (RTK) Survey: To ensure accurate installation of the sewer line, the team utilized the RTK technology, involving real-time data collection and analysis of project progress. “The survey was completed within a month instead of the conventional 6 months with 2 cm accuracy and faster validation and this was necessary to help us overcome the difficulties posed by the densely populated city and limited ROW issues,” points out Saadath.
Burning the midnight oil: To minimize disruptions to the city’s residents and businesses, the team committed to complete all aspects of the project in a single night. “This was an enormous challenge, as the project required to work around the clock to meet tight deadlines,” says Apurba, “but this helped to reduce cost and time by 2% and 7% respectively.”
Ramachandran is proud of the aggressive progress the project has been making. “One of the classic examples of the team’s success is the highest benchmark of 1.3 km sewer network laying achieved during the pandemic, which was risky, but we turned a challenge into an opportunity to execute the work in the highways where public movement was restricted. Overall, we have carried out around 17 km of dusk-to-dawn activities.”
Monolithic concrete road restoration: Road restoration was a major component of work in the contract involving public management to finalize the land and location for the lifting and pumping station. “It was tough especially during the rainy season amid dense traffic,” moans Assistant Construction Manager, S Mohan Raj, but he is happy that the client accepted their innovation to opt for a single layer of 200 mm of concrete on the road instead of two layers of 100 mm as per the contractual requirements. “After extensive technical discussions and presentations to the higher officials of the TWAD Board, they agreed to our proposal that ensures longevity and durability of the road restoration and for us, significant time saving.”
“After extensive technical discussions and presentations to the higher officials of the TWAD Board, they agreed to our proposal that ensures longevity and durability of the road restoration and for us, significant time saving.”
S Mohan Raj
Assistant Construction Manager
“Digitalization has made us a lot more efficient,” nods Rajavel, mentioning digital solutions like WISA, QIR, View EHS, EIP-Pragati and M-Flow with inbuilt SOP modules that have helped everyone to address site-based issues, rectify them and thereby execute the job as per the contractual requirements. “We monitor project progress in real time, respond to any deviations and take corrective actions. In fact, digitalization is one of the highpoints of our project,” he says emphatically.
Awards & recognition galore
Safety Awards: The project won a RoSPA Gold in 2021 and the British Safety Council Award 2022 for their outstanding EHS performance followed by the Annual EHS Trophy in 2022-23. They have also won the National Safety Council’s Prashansa Patra Award, a 2nd place in EHS Excellence Awards (Construction Sector) and received a 4 Star Rating from the Confederation of Indian Industry (CII) Southern Region.
Environment Awards: The project won the Go Green Champion Award in FY 2020-21 recognizing the team’s efforts to promote environmental sustainability and the NEER Award for the team’s efforts towards balancing nature and environment, employees and people, engineering and digital, and revenue and profits.
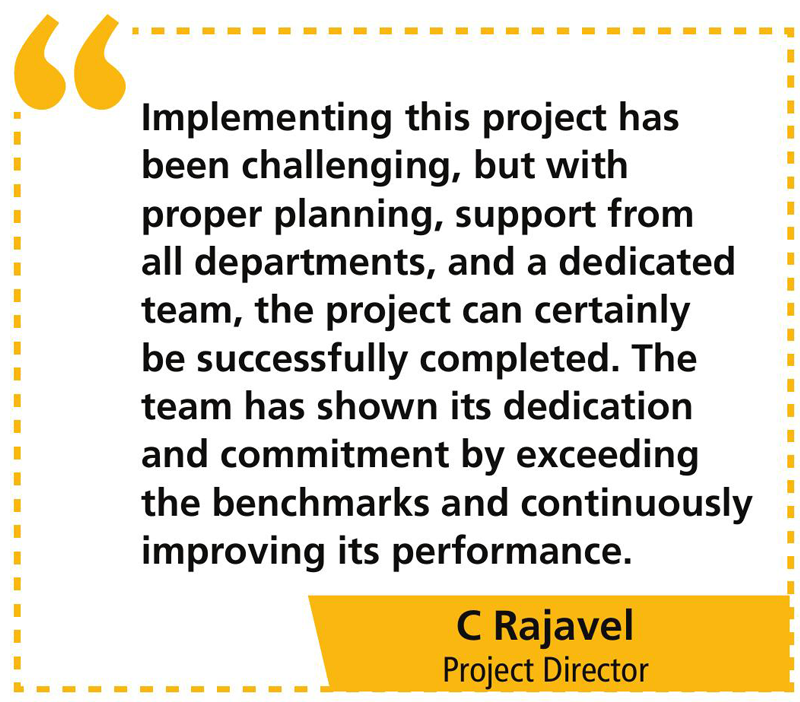
“Implementing this project has been challenging,” sums up Rajavel, “but with proper planning, support from all departments, and a dedicated team, the project can certainly be successfully completed. The team has shown its dedication and commitment by exceeding the benchmarks and continuously improving its performance.”