AN AFRICAN SAFARI THAT HAS BEEN A TOP QUALITY PERFORMANCE.
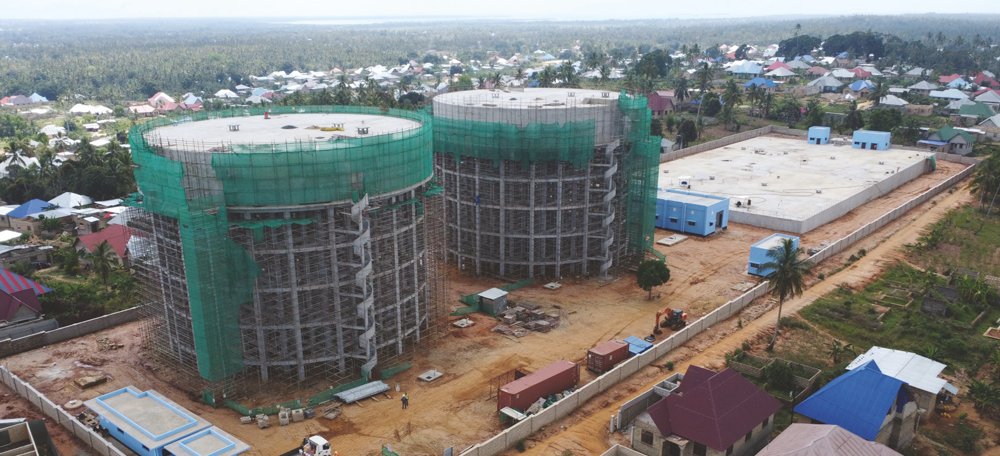
ZANZIBAR WATER SUPPLY SCHEME PROJECT
Zanzibar is an insular autonomous province which united with Tanganyika in 1964 to form the United Republic of Tanzania. An archipelago in the Indian Ocean, 25-50 km off the African mainland, Tanzania consists of several small islands, the two large ones being Unguja (referred to informally as Zanzibar) and Pemba. The capital of Zanzibar is Zanzibar City, located on Unguja and it’s Stone Town is a World Heritage Site, that attracts thousands of tourists all the year round.
The Zanzibar Water Authority awarded WET IC the ‘Rehabilitation and Improvement of Water Supply System in Zanzibar-Lot III’ project, located on Unguja. Work kicked off on March 31st, 2021, under the leadership of Project Director, Hari Prakash Pethakamsetty, who along with a young and energetic project team, hit the high road to progress. “In fact, we received an appreciation from our client for completing 45% of the work within the first 6 months of starting activities,” smiles Hari. He was certainly smiling from ear to ear when ‘virtually’ receiving the Quality Award for L&T Construction from CEO & MD, Mr. S N Subrahmanyan, that recognized a quality execution.
“We received an appreciation from our client for completing 45% of the work within the first 6 months of starting activities.”
Hari Prakash Pethakamsetty
Project Director
The project scope in a nutshell
Funded by the Exim Bank of India, the project scope comprises two major schemes: Kidutani & Masingini and Maji House Office Building (G+4). The Kidutani Scheme involves constructing two 5.5 million liters (ML) capacity Elevated Storage Reservoirs (ESR) with a tank diameter of 36.3 m and staging height of 23 m from ground level making it one of the largest ESRs to be constructed in East Africa. Other deliverables in the Kidutani scheme includes a 32.5 ML capacity Ground Storage Reservoir (GSR) with pump house, a chlorination building, an office room, a guard house, an electrical panel room and associated electro-mechanical works. The Masingini Scheme, on the other hand, involves construction of one 4 ML ESRs, one 14 ML GSR, ancillary structures, with the same electro-mechanical works as for the first scheme. Besides, the scope also includes 125 Kms of DI & HDPE pipelaying to deliver water from the borewells to the reservoirs through a transmission main line and from the reservoirs to the homes of Zanzibaris through distribution lines and house service connections.
Further, the team needs to construct a 5-storey, 4,000 sqm corporate office for the Zanzibar Water Authority, including MEP, façade and external development works to accommodate 270 to 300 personnel. The building will house their hi-tech water testing laboratory and a gymnasium.
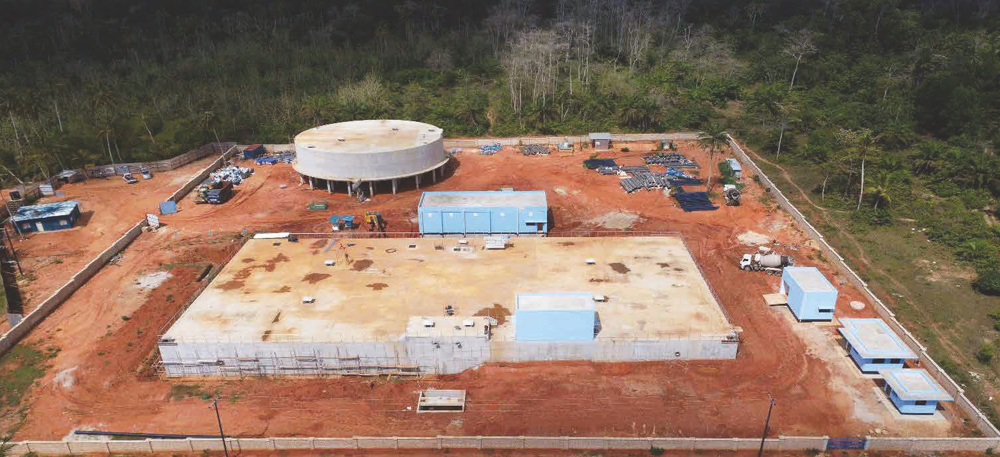
Starting the Quality journey
The first step to successful project execution is a clear understanding of the risks involved and the project team was aware of the challenges of executing on an Island like limited resources, availability of skilled workforce, lack of adequate infrastructure, shipping & logistics and climatic conditions. Zanzibar experiences two rainy seasons – short rain & long rain.
“We prepared a quality road map considering the various risks and opportunities,” informs Firoz Mohamad, Head – QA/ QC, Water International. “The team worked with a motto to ensure that all our deliverables to the client would be in L&T’s trademark style, believing that each and every project executed on field is a value addition for the organization and the brand we operate for!”
“We prepared a quality road map considering the various risks and opportunities. The team worked with a motto to ensure that all our deliverables to the client would be in L&T’s trademark style, believing that each and every project executed on field is a value addition for the organization and the brand we operate for!”
Firoz Mohamad
Head – QA/QC,Water International
Selecting the right partners
Partners can make or break a project and the Zanzibar team carefully chose the right kind of subcontractors to partner them. “Our objectives to select subcontractors were to reduce project risks by drawing on their experience of previously executed projects in Tanzania, maximize quality and strengthen the execution team,” apprises Suresh Kumar K, Assistant Manager (Planning).
“Our objectives to select subcontractors were to reduce project risks by drawing on their experience of previously executed projects in Tanzania, maximize quality and strengthen the execution team.”
Suresh Kumar K
Assistant Manager (Planning)
The credentials and past performance of subcontractors were verified including their specialization, resources, quality of workmanship, degree of quality control in executed projects, flexibility & cooperation when resolving delays, and, most critically, their ability to meet targeted project deadlines. “This identification process began even before project mobilization and various sub-contractors were approached and evaluated,” informs Hari. “To be doubly sure of our choice, we adopted the Multi-Criteria Decision Making method that takes into consideration technology & equipment, management, experience & knowledge of the technical staff, financial stability, quality, familiarity with the area or being domestic, reputation, creativity, innovation and, most importantly, price competitiveness.”
“After such an elaborate process, we finalized reputed and quality conscious subcontractors from Tanzania,” points out Aravind K, Assistant Manager (Mech), QA/QC, “after which they were acquainted with L&T’s Quality Standards & QMS, including the various procedures and processes to be incorporated at various stages of construction adhering to the contract specifications.” Exclusive QA/QC supervisors and assistants from the subcontractors were engaged in a project overview, guided by the L&T QAQC Managers. “By engaging enough skilled workmen, semi-skilled workmen and supervisors, we are monitoring and maintaining quality control at site,” Aravind adds.
“The average Customer Feedback Rating for the project has been maintained at 90%, captured through our QMS formats.”
Aravind K
Assistant Manager (Mech), QA/QC
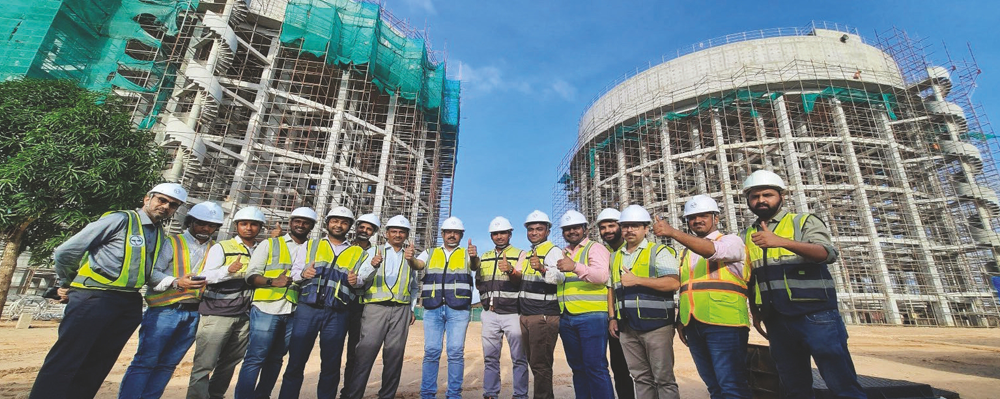
Selecting the right horses for the course
With the right partners on board, Hari’s next task was to put together a team to help him execute the project in sync with their motto. “We are a young and vibrant team with an average age of 34 and a right mix of experienced and young professionals,” he smiles. The team was gradually on boarded even as work was proceeding. While all new joinees are QMS oriented, every new activity starts with the team undergoing in-house project-based training, and introduced to the SOPs and inspection test plans.

Driving quality with the client’s involvement
The QMS for WET IC based on ISO 9001-2015 was adapted, incorporating learnings from previous overseas projects and the project’s contract and technical requirements. The Client and Consultant participate in the QMS process by reviewing the QMS documents and making suggestions. “In fact, we made them co-owners of the project by inviting them to review progress at site,” chuckles Hari. “Their suggestions were immediately addressed with the result there have been Zero customer complaints and non-conformance till date.”
The project Quality Committee conducts bi-monthly quality walkdowns to convey quality assurance & control procedures to all the stakeholders.
Since execution largely entailed concreting and pipelaying, batching plants were strategically placed in proximity to the major structure and concrete pours were carefully planned. “We achieved 6,100 cum of concrete pouring in a single month for 5 different structures and 80% of concrete works were completed within 9 months of starting the activities without any defects, re-work, rejection of materials,” declares a proud Anand Akash (Assistant Manager-Civil Execution). The client’s recognition was an invitation to the Project Director & Deputy Project Manager to the Client’s Board Meeting (ZAWA) to be presented appreciation certificates.
“We achieved 6,100 cum of concrete pouring in a single month for 5 different structures and 80% of concrete works were completed within 9 months of starting the activities without any defects, re-work, rejection of materials.”
Anand Akash
Assistant Manager-Civil Execution
Firoz adds, “The project has received the QMS Certification through the certification body ‘Lloyds Register Quality Assurance’ without any major/minor NCR representing the water projects in Tanzania, thus making it the first water project in Africa to achieve this feat.”
A 3-phase inspection process ensures material quality
In the first phase, materials are inspected as per the approved QAP at the manufacturing premises by an authorized third party assisted and supervised by L&T inspectors from domestic projects in the water business. Additionally, the Client and Consultants travel to the factory location with their technical team for inspections that assures 100% quality.
The second phase involves a Certificate of Conformity inspection under the Pre-shipment Verification of Conformity program. All regulated products are verified and tested in the country of supply and issued a Certificate of Conformity (CoC) to demonstrate that they meet the requirements of the applicable national standards or approved equivalents and technical regulations. This prevents malpractices and ensures that only the inspected materials from the first phase of inspection are packed as per the sea freight requirements under the direct supervision of the third-party inspector.
The 3rd and final stage is receipt after the material travels 3,000 nautical miles to Zanzibar, which has a relatively small port. Incoming material is inspected at project location to confirm that the materials are free from any damages, unloaded and stored as per SOP.
A 3C approach to win client confidence
Ohmae’s 3C – ‘Customer, Competitors, Corporation’ approach is going a long way to help the water business find a firm footing in Africa. Half yearly interactions with the Director General, Zanzibar Water Authority involves a thorough analysis of progress. “The average Customer Feedback Rating for the project has been maintained at 90%, captured through our QMS formats,” shares Aravind and proudly adds, “Our project has received four Customer Appreciation Certificates from the Director General.” The Ministry of Water & the President’s Office also chose the Kidutani Reservoir site to lay the foundation stone for water projects in Zanzibar.
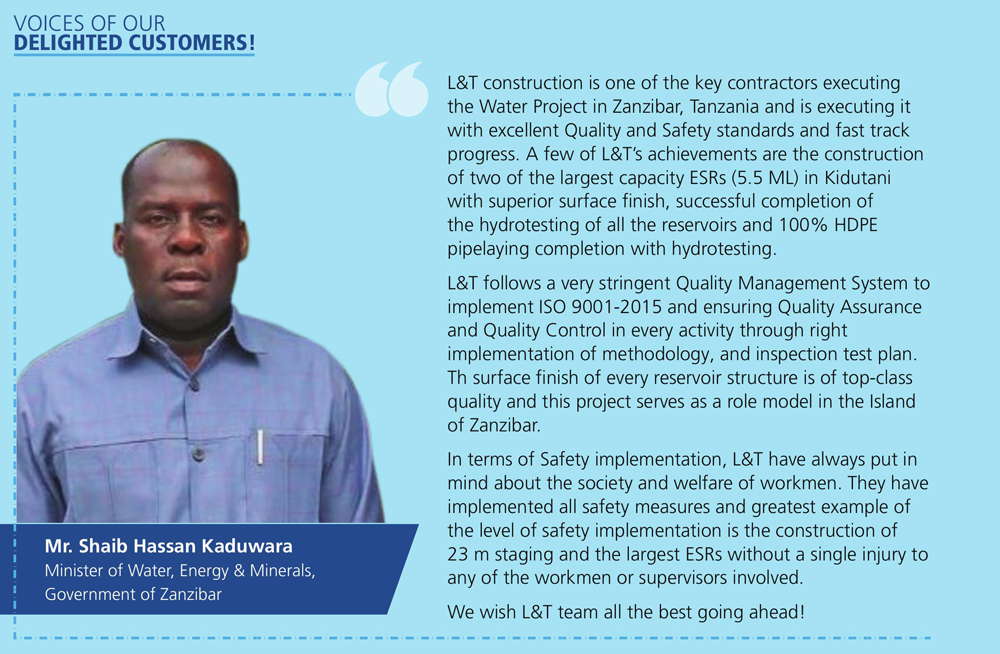
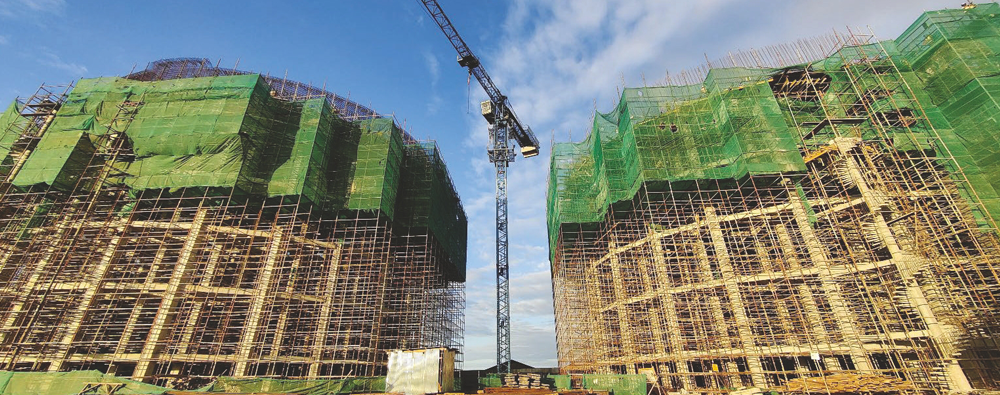
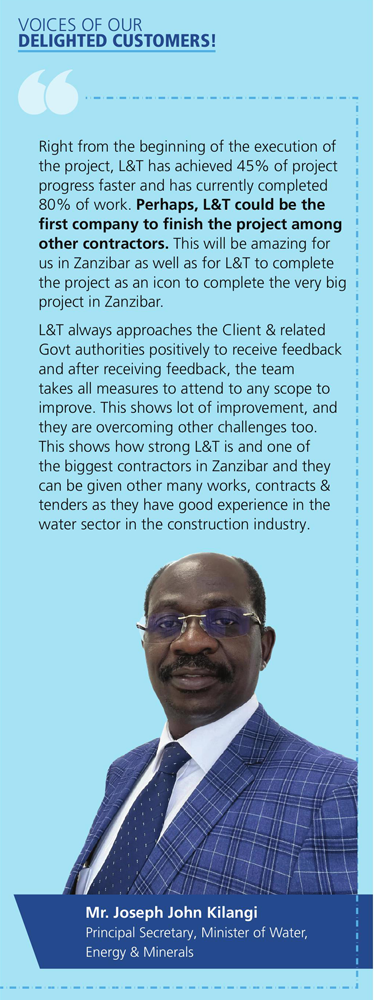
Innovations to the fore
Scraper blade for final levelling work: The project scope involves 2,32,489 cum of earthwork and to achieve the required slope and surface finish, the excavator’s bucket was fixed with a scraper blade instead of manually excavating that saves time and manpower for the final dressing & levelling.
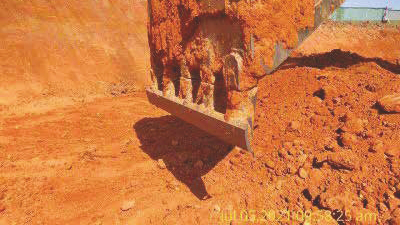
The advantages of this ploy are several as Aravind enumerates. “It completely prevents loose material from falling on the concrete area, ensures an even profile, avoids additional backfilling in the final excavation, does not disturb the hard soil strata and is aesthetically pleasing.”
Monolithic construction of reservoir columns: Constructing 5 different reservoirs involves 224 columns of 6 m height and for monolithic construction, the Fabricated Modular Formwork method was deployed with a single pour of 6 m columns without any construction joints, honeycombing or bulging of concrete. Casting 3 m columns normally take 3 days per lift, a single column in 2 different lifts will take 6 days and totally 134 days to complete 224 full columns. Monolithic construction has reduced that to just 67 days without any construction joints and 50% time savings to boot.
Plastering the interior and exterior surfaces of the reservoirs is part of the Lump sum Quantity awarded in the contract. On showing a superior surface quality in concrete finish, the client waived off the plastering only for L&T thus saving approximately 30 days’ time and associated costs.

Hari is a happy man, with a delighted client by his side and a turbo-charged team behind him to deliver another world-class water project in Africa.