B&F PROJECTS CONTINUE TO CHANGE LANDSCAPES & CITYSCAPES DESPITE
TALL CHALLENGES
Just as project teams were slowly coming to terms with the virus, they were hit broadside by a more virulent second wave, almost without warning, causing even more severe disruptions. For Project Director, K Ravichandran, the Prestige Jindal City residential project in Bengaluru had begun with some inherent restrictions. Located in a dense, residential area, construction activities had to be restricted within a 7 am – 7 pm window with the labour habitat situated elsewhere. “To complete concrete pours of 500 – 750 cum in 12 hours, our equipment had to be at their highest levels of efficiency and availability, with zero breakdowns,” Ravichandran observes. “With a wide variety of properly sequenced structural and finishing activities, we had a large number of skilled workmen and agencies working at site to complete the works in time.”
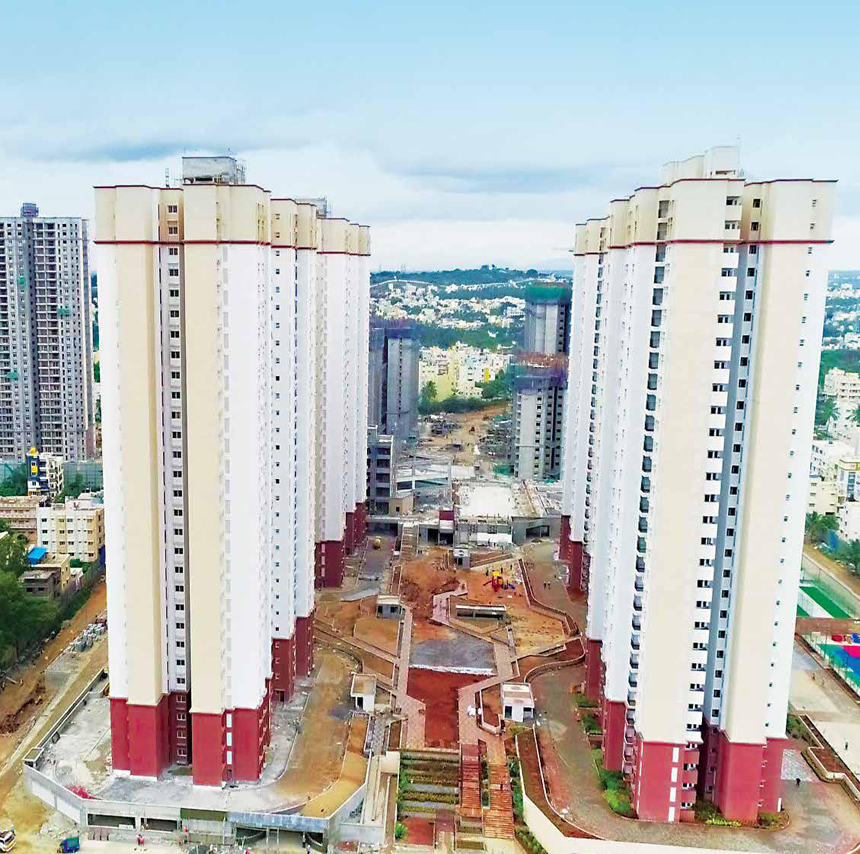
COVID throws progress out of gear
When the first wave struck, Ravichandran and his team found their labour stuck at an external habitat and agitated local villagers clamouring to shut down the labour camp. The team had to literally conduct a door-to-door campaign to appease and assure the locals for it to remain. In addition, they reached out to them with programmes like arranging medical camps and conducting tests. With the labour force dwindling despite their best efforts, the team focused vigorously on remobilization and successfully convinced several workmen to either return to site or come afresh, some of them travelling 2,000 – 3,000 kms.
“To complete concrete pours of 500 – 750 cum in 12 hours, our equipment had to be at their highest levels of efficiency and availability, with zero breakdowns. With a wide variety of properly sequenced structural and finishing activities, we had a large number of skilled workmen and agencies working at site to complete the works in time.”
K Ravichandran
Project Director, Prestige Jindal City Residential Project, Bengaluru
“When work resumed in August 2020, we had achieved only 42% against a completion target of 55%,” remarks Ravichandran. Realizing their shortfall, the team rebounded with renewed energy to close the gap by working on all float areas and exploring analogous activity work areas. “With stringent planning, active resource mobilization & allocation and strict monitoring of site progress, we achieved 66% completion by March 2021 against the target of 67%,” shares Head – Planning, V Ramani, with a rousing thumbs up. Major milestones completed were 19,61,650 sq. feet of the non-tower area, the structure for towers in Clusters 1 – 9 and tiling in 6 towers.
“With stringent planning, active resource mobilization & allocation and strict monitoring of site progress, we achieved 66% completion by March 2021 against the target of 67%.”
V Ramani
Head – Planning, Prestige Jindal City Residential Project, Bengaluru
The project was returning to high gear when the second wave struck. “Despite challenges, we made significant progress,” enthuses Head – Structure, Sivanthillingam. “Several milestones achieved include completing the development works for the club house and ground areas in Cluster 1 which is heading towards inauguration, and 73% of works in Cluster 2.”
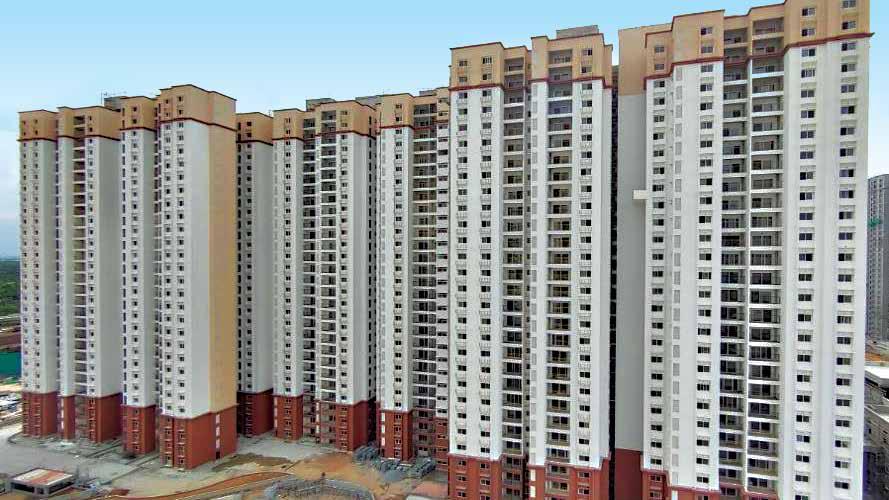
Prestige Jindal City, Bangalore
While Ravichandran is appreciative of the design support from EDRC, the primary task before Head – Finishing, A Subramanian, is to consistently maintain the highest quality for all the 3,571 units with different agencies and workmen. “Sequencing and coordination are the keys to success and our adherence, as a team, to a common goal,” he asserts.
Building a road to recovery
At the 960-bed AIIMS Hospital & Academic Campus project at Guntur, Andhra Pradesh, Project Manager S Vadivazhagan, and team had already handed over 4 of the 8 buildings before the second COVID wave. “Our workmen mobilization was at its peak and as planned, we had successfully managed the critical operating activities, with a precise plan to procure material like glazing when the second wave struck forcing us to change our plans and strategies,” he says, sadly. “We had to maintain cash flows and face decreasing manpower that forced us to tailor our activities not as per our available capabilities but as per the client’s priority.”
“We had to maintain cash flows and face decreasing manpower that forced us to tailor our activities not as per our available capabilities but as per the client’s priority.”
S Vadivazhagan
Project Manager, AIIMS Guntur
To achieve the invoice target, the team planned structural steel works like trusses, but were hit by the lack of industrial oxygen. With fabrication work stalled due to the non-availability of oxygen, workmen started to leave. “Desperate situations require desperate measures,” observes Planning Head, A V Pavan Reddy. “We immediately decided to procure plasma cutting machines to keep work ticking and retain our workmen. Coordinating with our client, we arranged for permission letters from DGPs of States where structural steel for truss was being fabricated, successfully erected the truss and recovered the planned invoice amount.”
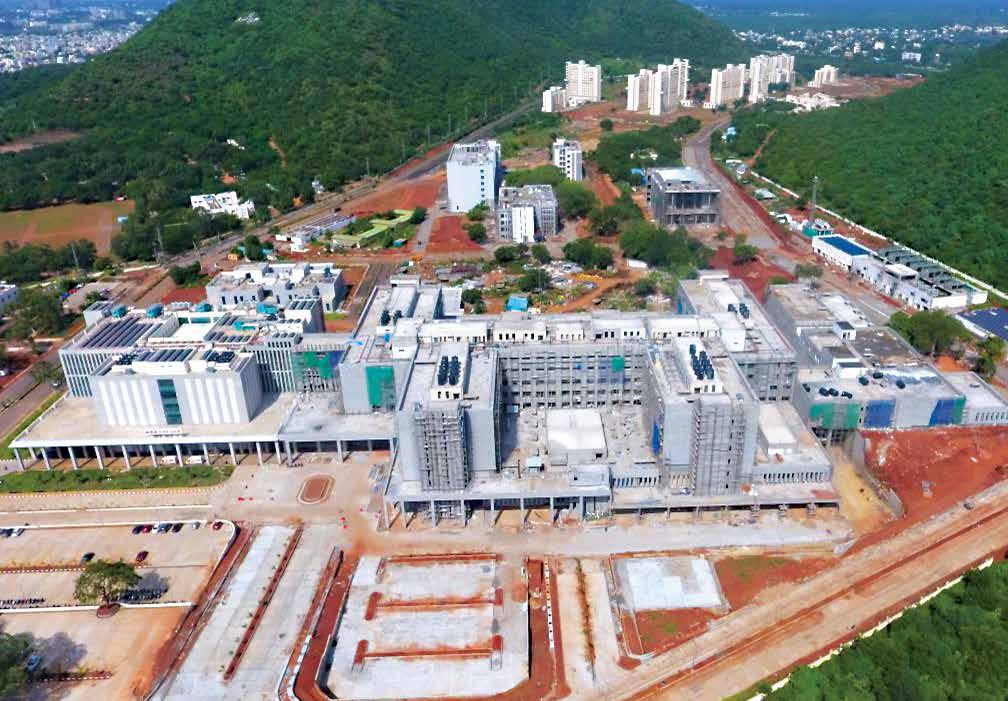
AIIMS Hospital & Academic Campus at Guntur
Although the site was hampered with several of the staff getting infected, the team re-distributed the work and stood firm to complete the work. “As the project was in its completion stage, it was difficult to mobilize new workmen gangs, so we encouraged the existing labour contractors to mobilize their teams apart from retaining 80% of the existing workmen strength,” says Pavan, for whom handing over a 100+-bed building is a big achievement to write home about.
BIAL airport is 21% to take off
The new Terminal 2 of Bengaluru’s Kempegowda International Airport, designed as a ‘Garden Terminal’ is 79% complete and the challenge before Project Director, J K Shivaraj, is to adhere to his timelines despite the pandemic-created disruptions. “A lion’s share of the RCC and envelope works including façade installation, skylights, roofing works, block work, tiling works & screed works have been completed,” he ticks them off on his fingers. “In fact, the entire scope of the bamboo tubes for the internal ceiling system has been delivered and installation is in progress.”
“A lion’s share of the RCC and envelope works including façade installation, skylights, roofing works, block work, tiling works & screed works have been completed. In fact, the entire scope of the bamboo tubes for the internal ceiling system has been delivered and installation is in progress.”
J K Shivaraj
Project Director, Kempegowda International Airport, Bengaluru
He is referring to the bamboo engineered ceiling that will be a key element of the terminal architecture. “After the Madrid International Airport in Spain, this terminal will be the second in the world and the only one in India to have such a ceiling,” shares Deputy Project Director, K P Maheswarappa. The intricate and massive bamboo ceiling construction involving about 1000 km of bamboo tubes, spread over an area equivalent to 11 football fields, will be reminiscent of a forest with bamboo clad structural cruciform columns that mimic tree trunks.
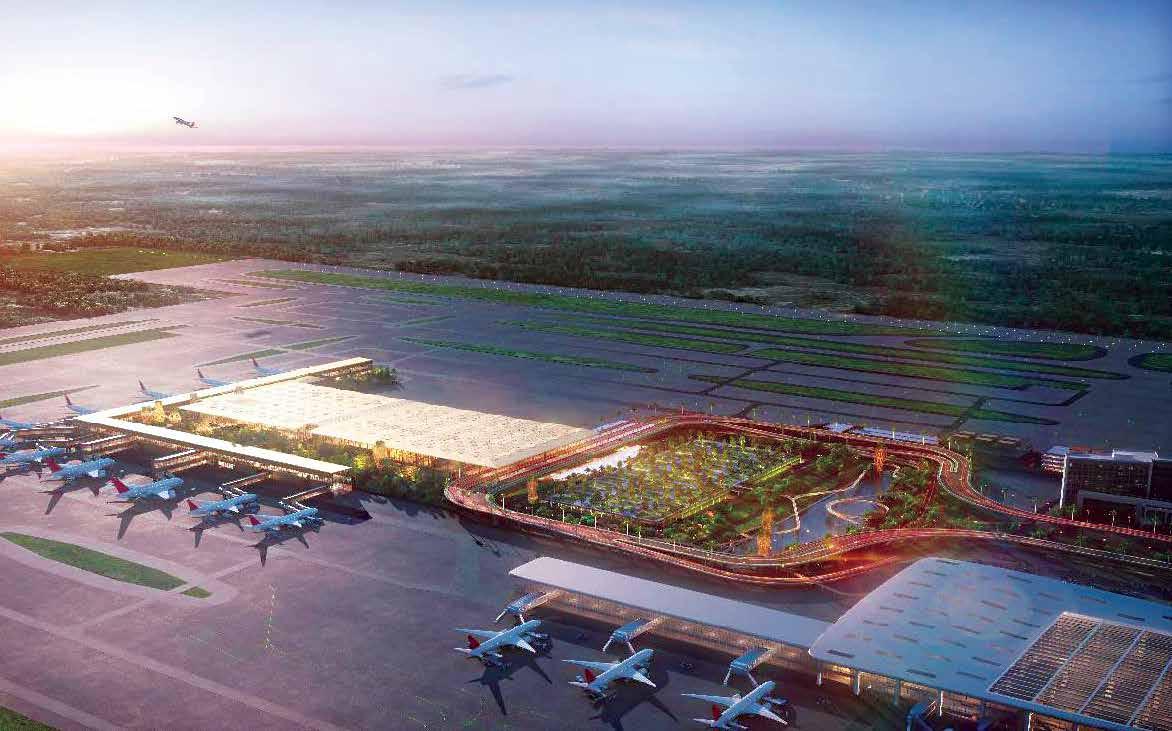
Kempegowda International Airport Terminal 2 at Bengaluru
In addition, the Baggage Handling System (BHS) has been installed and testing is in progress, 12 Passenger Boarding Bridges (PBB) have been installed & another 11 are in the process of being fixed, 90 out of the total 104 VHT systems (elevators, escalators, travelators) are up, and the Master Control Room has been commissioned.
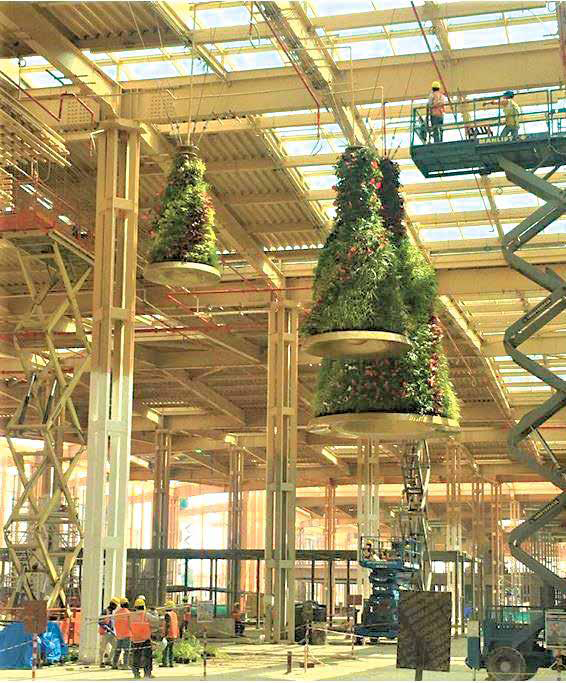
Bells & Veils at the Departure Level
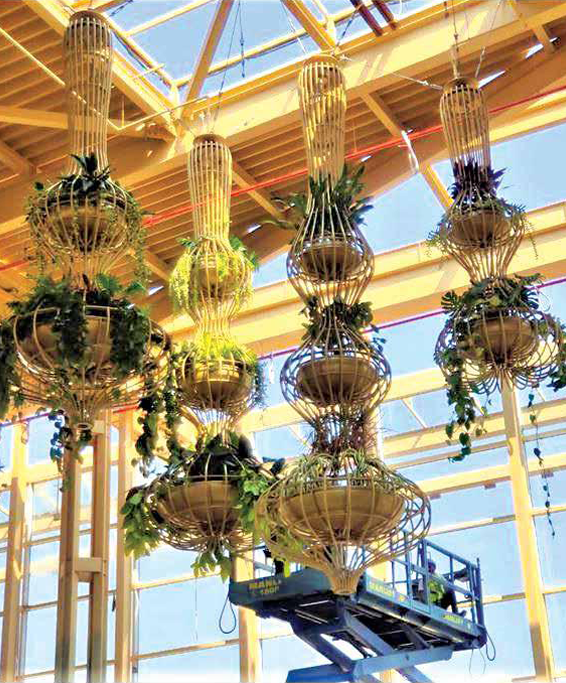
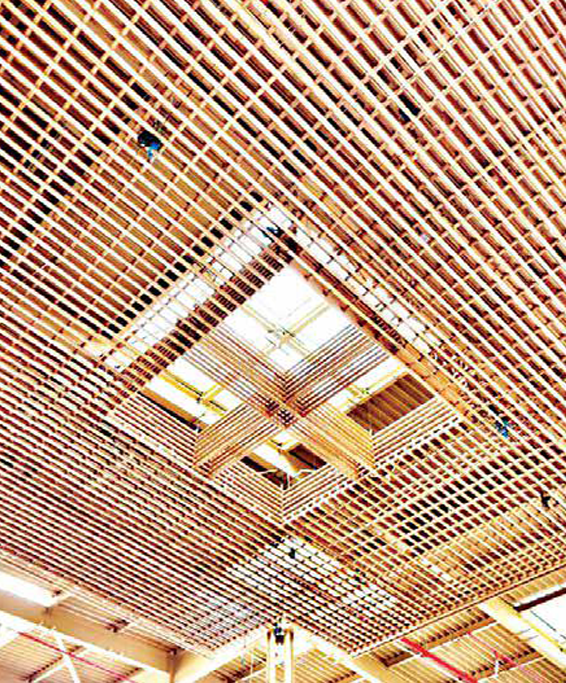
Bamboo Ceiling at the Departure Level
Workmen & procurement travails
From an original strength of 4,000, the first wave reduced the workmen numbers to 900 while the second wave pruned the 5,200-strong force to 3,300 by May 2021. The BIAL T2 site IR team and a specially constituted task force took appropriate steps to either retain workmen or remobilize. “A 200-bed dedicated COVID care centre has been set up in the airport premises and a 24×7 medical centre at the labour camp with dedicated doctors and nurses to keep the force healthy,” informs Head – FA&A, N Sridhar.
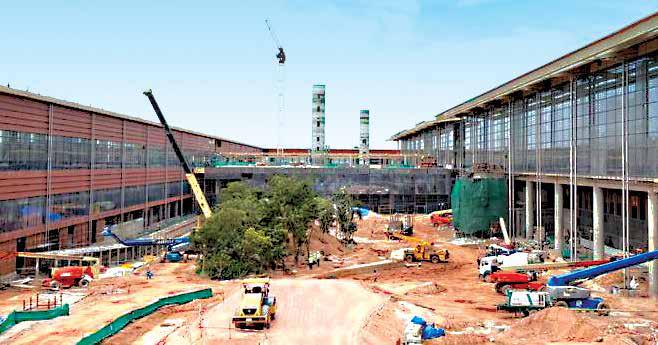
View of Terminal 2 Head House (Right) & North Pier Building (left) from the Forest belt area
Disruptions in supply chains have been a huge stumbling block for the site as major items constituting to 65% like glass, bamboo, BHSs, PBBs, HVAC, VHT equipment, self-baggage drop, light fixtures, cooling towers and the like had to imported from across geographies. The team liaised with the Customs department for seamless clearance of the imported items, rigorously followed up with vendors, coordinated with subcontractors and their efforts bore fruit as 300 containers of various goods & equipment were delivered from different locations during the height of the pandemic.
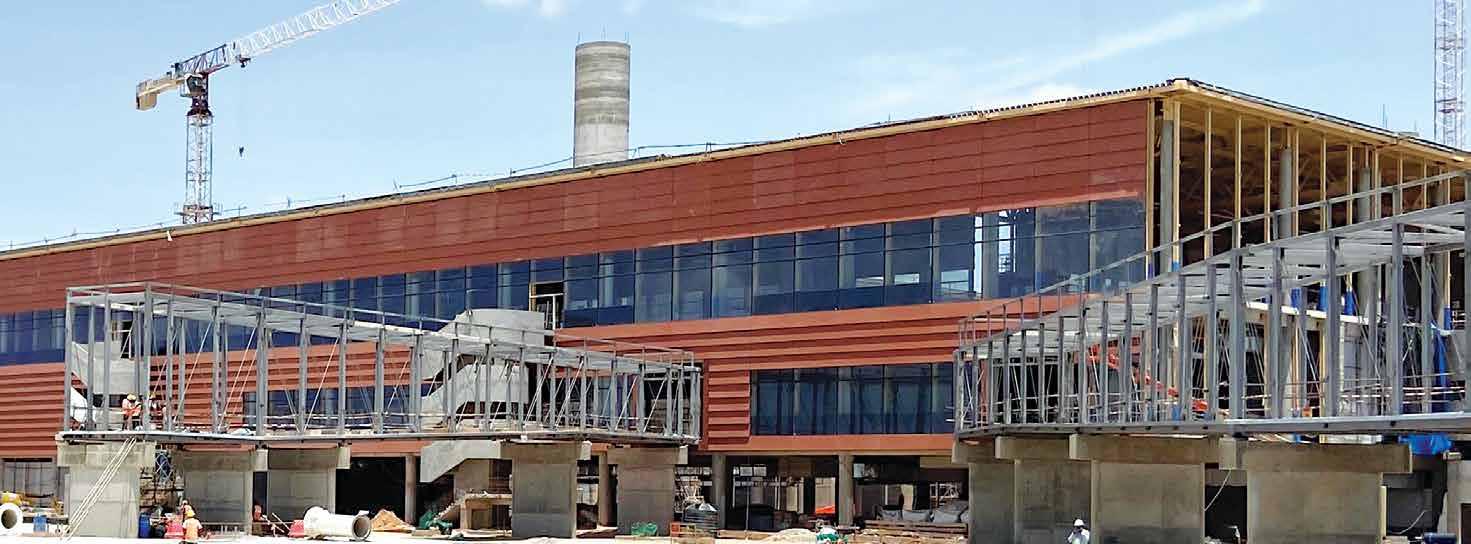
View of East Pier East Elevation & Fixed Link Bridge
“We are conducting FAT (Factory Acceptance Testing) at our laboratory at site, for high/low level controls and simulations for BHS instead of getting it done in Denmark,” remarks Head – MEP, Anne Sriram Kumar. “Our client virtually inspected MEP systems like HT/LT panels, UPSs, HVAC pumps, BUS ducts, ICT liquid cooling systems, ICT racks and more. Even the self-baggage drop FAT was conducted at site instead of at the factory.”
BIAL T2 is a good example of successful adoption of digitalization as Shivaraj proudly shares, “The entire design coordination and preparation of shop drawings are through the BIM 360 platform, wherein around 40 specialized agencies and more than 200 BIM modelers can continue working on the cloud server from their respective locations without having to physically travel to the project site.” All technical submissions & approvals such as method statements, drawings, status reviews, RFIs, inspection requests, material approvals and the like are digital on the Aconex platform, avoiding operational challenges of hard copy submissions.
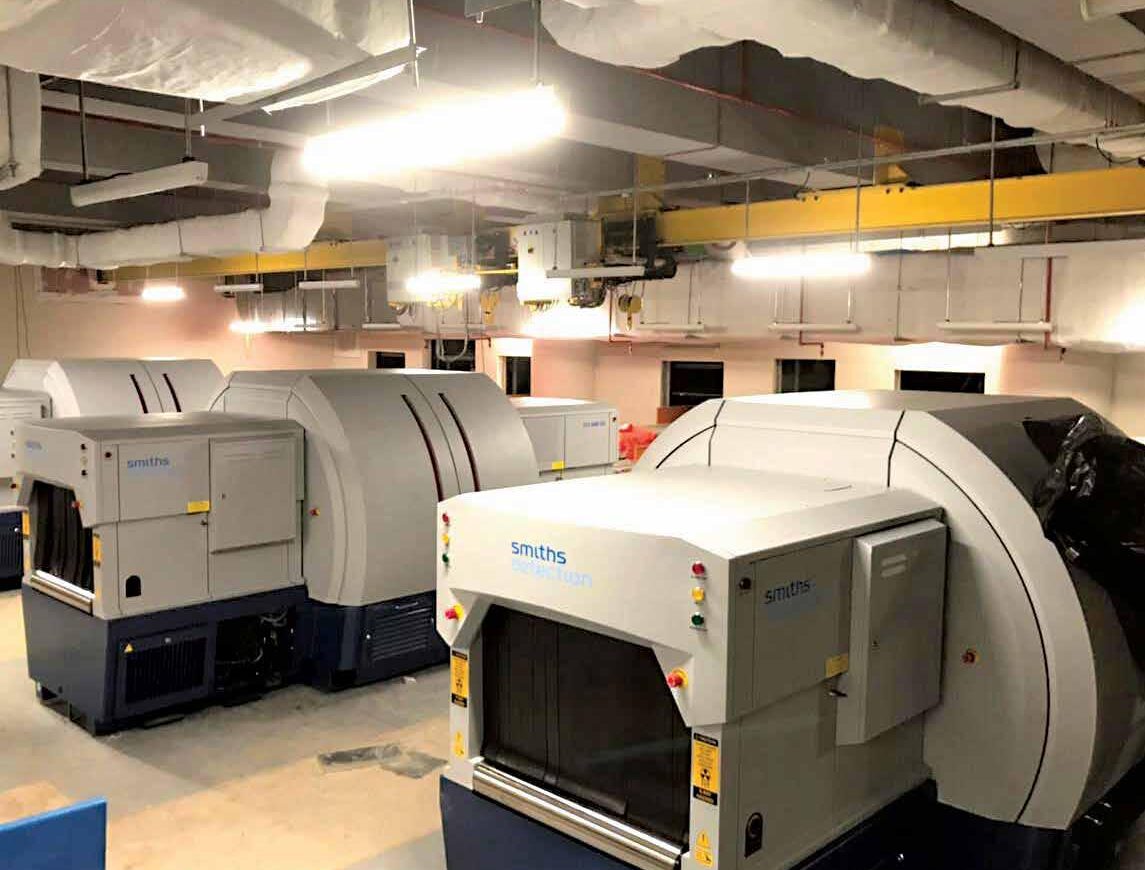
Level three security X-Ray machines
Another striking feature of BIAL T2 is an artificial forest belt located between the Head House and the Pier Buildings that houses 22 artificially created forest mounds of heights ranging from 3m to 12m with two tall pavilion structures of up to 42m housing high-end restaurants and viewing galleries for passengers. For Shivaraj and team it is a race against time and circumstances to bring all this to reality.
IIT, Hyderabad progressing against heavy odds
Workmen attrition and remobilization are sterner issues at the IIT Hyderabad Phase 2 project where Project Director, H S P Shukla must deliver his project in 36 months with intermediate milestones of 18, 20 & 24 months. “Our scope includes construction of 1.6 million sq. feet spanning 46 buildings,” he shares, “though the bigger challenge is to execute buildings with some unique designs like the folded plate with a 3D slope being cast in-situ for the first time in India for the Sports and Cultural Complex. We have developed a BIM model exclusively for this structure for clash detection, better clarity to fabricate truss moulds and avoid last minute surprises during execution.” The Knowledge Centre is another building that involves complicated construction with 82 RCC arches of different heights and radii and 37 with an exposed concrete finish. The roof will be a hyperbolic paraboloid shell, adopted again for the first time in India.
“Though the bigger challenge is to execute buildings with some unique designs like the folded plate with a 3D slope being cast in-situ for the first time in India.”
H S P Shukla
Project Director, Hyderabad Phase 2 Project
“We are at the halfway mark and have handed over one major building (MSME) and two service buildings on August 15th as planned,” Shukla shares his project’s present status with a serious expression though glad of his team’s delivery despite odds. The most productive period for construction from March to May has been hit for a six by the second wave, there are issues of low productivity due to the lack of adequate skilled labour, disruptions in the supply chain, scarce availability of liquid oxygen, and steep rise in material costs with vendors demanding upward revision of their prices that is further hindering progress. Assistant Stores, Leo Stalin A picks up the story. “We had to negotiate hard to procure almost 35,000 solid and AAC Blocks, 28,000 MT of aggregates, 320 MT of steel, 4000 Sqm of tiles and 3100 MT of cement. Despite the vendors demanding an escalated rate, we managed to get the best rates and ensure continuous flow of supply of construction materials to site.”
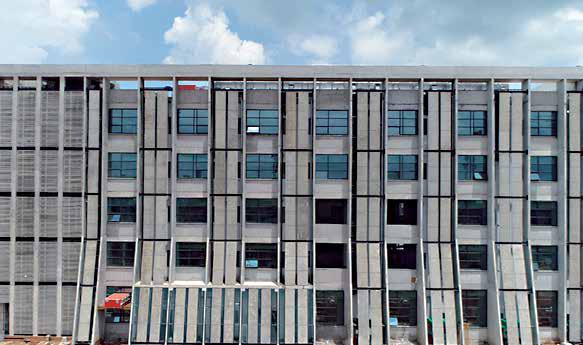
IIT Hyderabad Phase 2
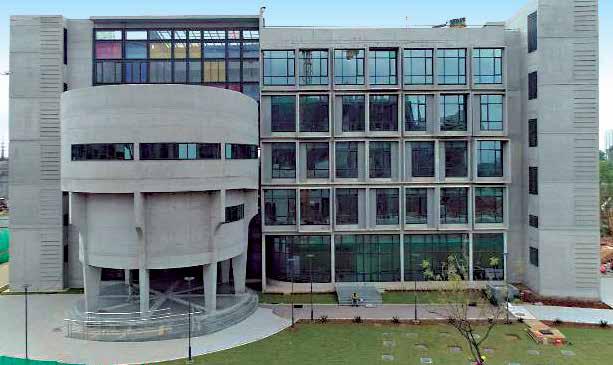
Although the challenges are many, Shukla and his team are manfully pulling things around with fresh strategies and advanced monitoring techniques. They have successfully retained workmen with prior experience of having worked on IIT structures while remobilizations are on in full swing. Senior Manager – Finishes, Ishwar Patil Pandhari, looks happy with the progress. “We have executed almost 2500 Sqm of plastering, 800 Sqm of flooring, 1700 Sqm of terrace tiling, 200 Sqm of waterproofing during May and June 2021,” he shares.
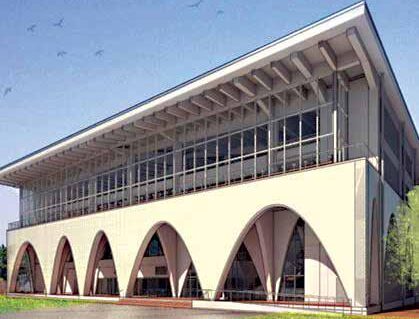
Shukla adds, “We are value engineering various items by proposing alternate items to enhance progress, have bifurcated our scope of works and finalized additional vendors both to avoid monopoly and attack various work fronts simultaneously.” They are also discussing with the client to change the agreed payment terms to enhance cash flows.
L&T Infotech Mahape. A project being built modular, smart, and fast!
The project’s uniqueness is that it comes under the new vertical B&F FAST, identified to fast-track delivery by adopting advanced construction technologies like DfMA (Design for Manufacturing & Assembly), PPVC (Prefabricated, Prefinished Volumetric Construction), Offsite Manufacturing, Structural Steel Construction, and 3D printing. “Our project has been designed with a steel structure that will have unique features like a structural steel core, concrete filled tubes for columns, precast staircases and modular partitions like hollow core walls,” explains Project Director, Rajesh Pachlot.
“Our project has been designed with a steel structure that will have unique features like a structural steel core, concrete filled tubes for columns, precast staircases and modular partitions like hollow core walls.”
Rajesh Pachlot
Project Director, L&T Infotech, Mahape
Having kicked off during the second wave, the project has been striving to mobilize workmen that has touched about 400. The biggest challenge for Pachlot and team is to complete the hard rock excavation to free the front for concreting works and he is delighted with the progress. “We have generated 4 weeks’ buffer in excavation by achieving an average disposal of 1850 cum per day against a historical average of 1000 cum/day thanks to our innovative thinking, meticulous planning and adoption of digital technology.”
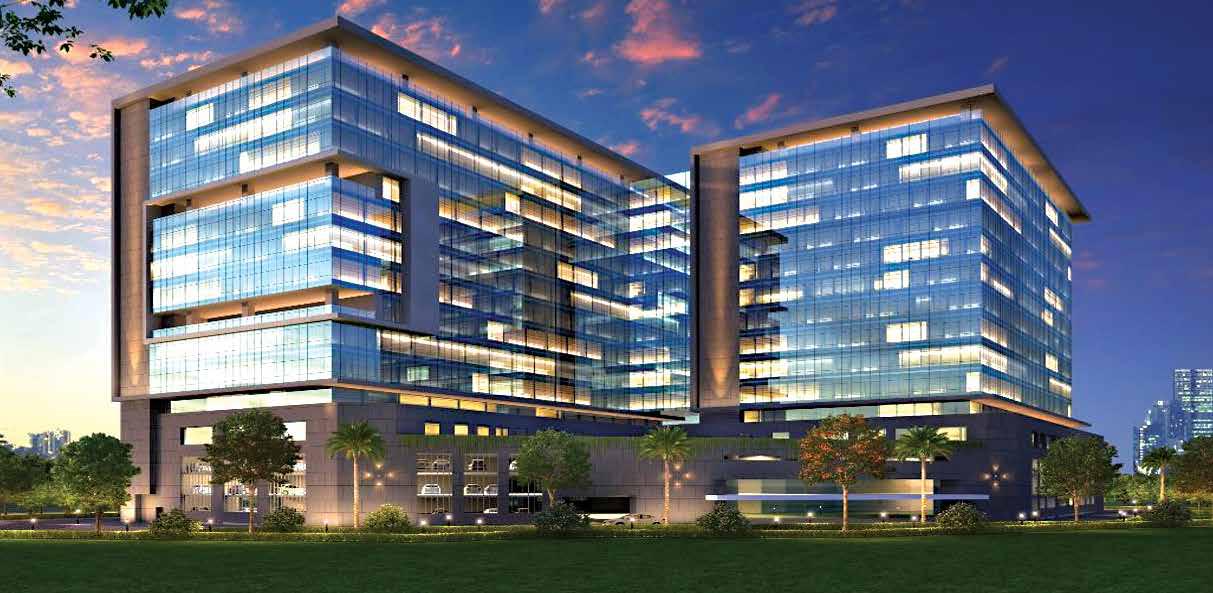
L&T Infotech, Mahape
“Completing 10,000 MT of structural steel design, fabrication and erection in 6 months is an extremely daunting task,” says Head – Structural Steel, J P Navik, “but by using BIM 360 to monitor design and execution progress we are well placed to deliver.” Head of Planning, Rahul Kumar opines that “design defines the speed of a project and by being involved right from the design stage, we have bridged the gap between design and execution that will hold us in good stead to arrest any constructability problems that might arise.”
Executing a project won amid the pandemic
Project Director, Raghuraman and team have the responsibility to build what is proposed to be the largest 2-wheeler factory for OLA Electric in Krishnagar, Tamil Nadu. The first task was to establish two M1 batching plants that were erected in 14 days and 72 hours respectively after completing the foundations to achieve average SFRC cement of 600 cum per day for the flooring works.
“During May & June 2021, we mobilized 300 local workmen and another 300 in 7 days,” says Planning Manager, S Sriram. “They have been provided the essential training and course-corrected to align to our work systems. Our ‘Sathi Engineers’ have played a major role during these times taking care of the workmen and retaining them.” Currently, the work strength is 750, operating in two shifts. Precast In-charge, Thirumalaikumar S is happy with the enhanced demand for precast elements in the project. “With 632 elements to precast the plinth beams, columns, lintel beams, roof beams, parapet walls and hollow core slabs we completed erecting each building including slab in 5 days cycle time.”
“With 632 elements to precast the plinth beams, columns, lintel beams, roof beams, parapet walls and hollow core slabs we completed erecting each building including slab in 5 days cycle time.”
Thirumalaikumar S
Precast In-charge, OLA Electric in Krishnagar, Tamil Nadu
Nallasivam R from CMPC shares that 32 columns and 60 beams had to be precast in 5 days. “Each column and beam erection takes an average of 50 minutes per element with 4.5 m staging required for each column and extending the staging up to the beam and slab levels is a 2-day activity. We have deployed two additional Boom Lifts to eliminate staging for erection and grouting works and two shift operations to optimize element erection in 20 minutes.”
Across B&F sites, project teams are thinking on their feet to lick problems both ‘novel’ and old to ensure that work continues, and milestones are achieved. Hats off to all of them!