CONCEPT TO COMMISSIONING IN
12 MONTHS FLAT!
PT&D’s Qatar project is the second winner of the
Timely Delivery Award
The assignment to construct a 132 kV RAF-1 substation and associated works for the replacement of RAF A 132 kV Switchyard at Qatar for the client, KAHRAMAA, was a brown field, fast track project to be delivered in 12 months. The project team led by J Aravindan conceived, engineered, planned, constructed and commissioned the project right on time, delighting their client and, in the process, won the Timely Delivery Award for L&T Construction.
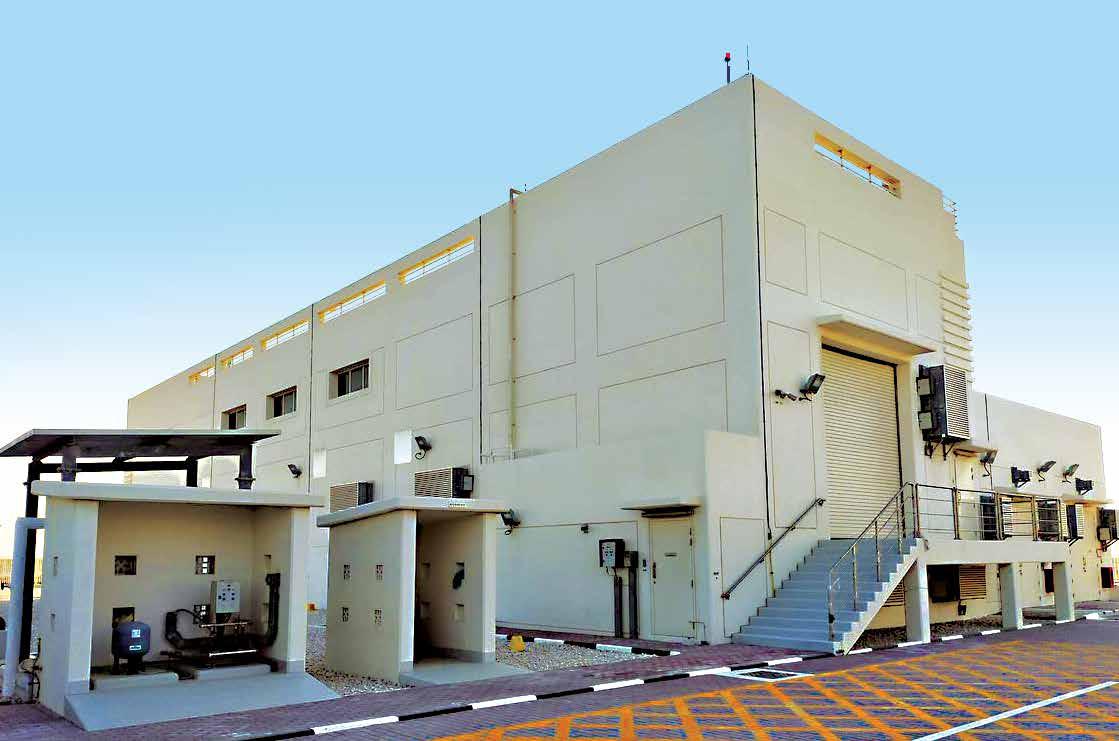
Determining the contours of a tough ask
“It was almost like playing a Twenty20 cricket match chasing a very steep asking rate,” chuckles a visibly proud Aravindan, Project Manager. “The scope was huge and full of challenges.” Their mandate included constructing a new 132 kV RAF1 substation with 30 GIS bays and 15 132 kV & 66 kV EHV cable diversions and associated remote end works at 8 different locations. “Out of these, four remote end substations were owned by Qatar Electricity and Water Corporation, or QEWC,” informs Aravindan, “constructed at different periods of time from the 1980s, undergoing various upgradations at different stages with connections to desalination plants accounting for almost 80% of the water supply to Qatar & connected gas power plants.”
“It was almost like playing a Twenty20 cricket match chasing a very steep asking rate. The scope was huge and full of challenges.”
J Aravindan
Project Manager,
132 kV RAF1 substation at Qatar
In addition, the team had to dismantle power transformers from the existing switchyard and relocate, install and commission them, manage the water RTU modification works at the QEWC desalination plants, and decommission and hand over various panels from the existing control room from RAF A CCR.
Challenges galore: Perhaps, the biggest challenge for the team was to construct and commission 30 GIS bays as a brown field project, having to execute inside a power plant. Along with the construction of the substation, the cable diversions and remote end works had to be executed under three stages of shutdown with meticulous coordination with KAHRAMAA and QEWC.
“We were limited from a design perspective, for we had to operate with only as-built data of the existing plant and utilities,” says Aravindan, “and there were stringent gate pass procedures for each material and manpower movement involving various authorities like the Ministry of Interior, QEWC plant and airport authorities.”
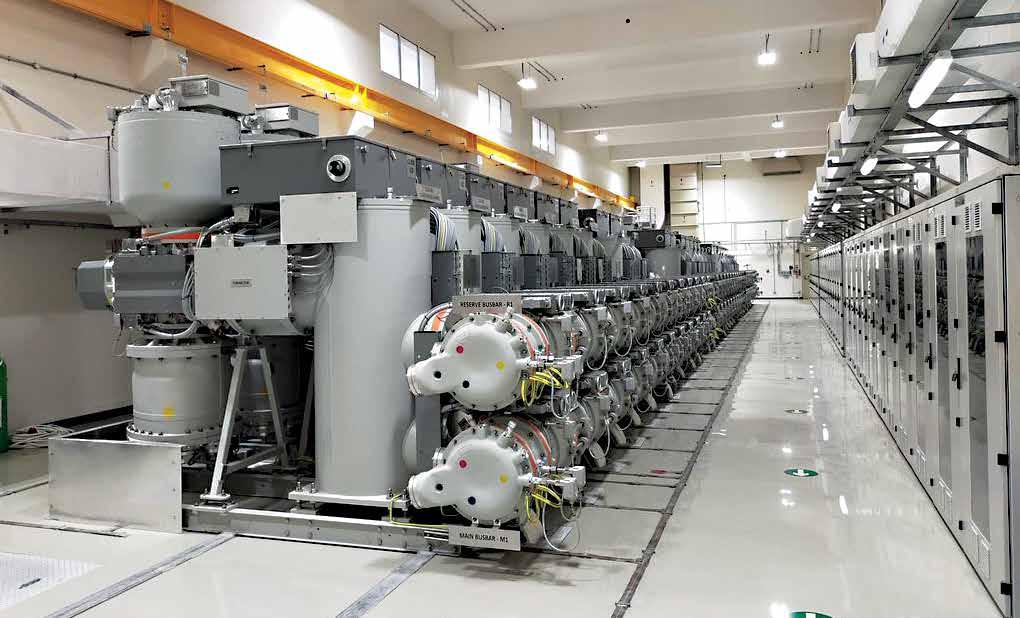
132 kV gas insulated switchgear
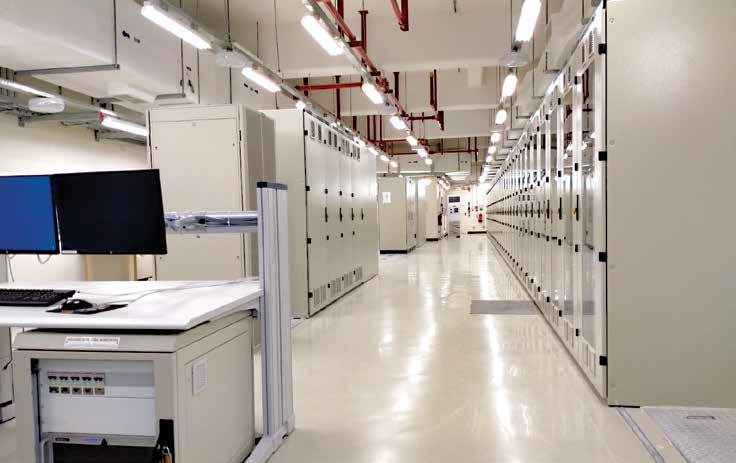
Control room
Planning Manager Muhammad Muhsin continues to add to the list of challenges. “We were dealing with 7-8 different OEMs, and coordinating with all of them was a herculean task,” he shakes his head. “Obtaining shutdowns for the existing desalination and power plants for various remote end and cable diversion works was another huge exercise.”
The first 66 kV EHV cables had to be shifted within the first six months of the project to a new corridor since it was falling within the new substation construction plot, and procuring spares for the existing obsolete systems proved to be extremely difficult.
“Understanding the gate pass system in Qatar is key to achieving physical progress at site for it involves a meticulous and regular review system, and we had a dedicated admin team deployed to coordinate for gate passes and vehicle movement inside the plant.”
Muhammad Muhsin
Planning Manager,
132 kV RAF1 substation at Qatar
To top all these was the mother of all challenges – the pandemic that threw up fresh issues, like difficulty to mobilize labor, problems of mobilizing OEM supervisors from Europe, travel restrictions, stringent site SOPs – the works.
“Let us not forget,” reminds Aravindan, “that while we were executing, we had to face and overcome all the challenges of working in a foreign land.”
A team that made it happen
Often, a clear appreciation and understanding of the challenges involved is half the battle won, and for Aravindan and his team, an awareness of the mountain they had to climb put them in the right frame of mind to climb it. Fully aware of the limited as-built data available with the client, the team went ahead to collect field inputs to fast-track engineering. “Understanding the gate pass system in Qatar is key to achieving physical progress at site,” Muhammad points out, “for it involves a meticulous and regular review system, and we had a dedicated admin team deployed to coordinate for gate passes and vehicle movement inside the plant.” Although there were delays owing to the pandemic, most of the delivery of equipment was made as per a planned schedule with the support of the SCM team.
The team realized that following the conventional sequence of testing each GIS after installation would not work given the constraints for installation, testing and commissioning. Instead, they introduced a partial ECF system that won client approval, wherein the GIS was installed and tested in parallel.
The shutdown delays from the client were minimized by completing the pre-outage works in advance for the following stage of cable diversions, which helped reduce the outage duration once the system was shut down. A pre-outage observation report was maintained for the existing equipment jointly with the client, which helped avoid defect points from the client unrelated to L&T’s scope of works, in turn smoothening the process of obtaining the TOC.
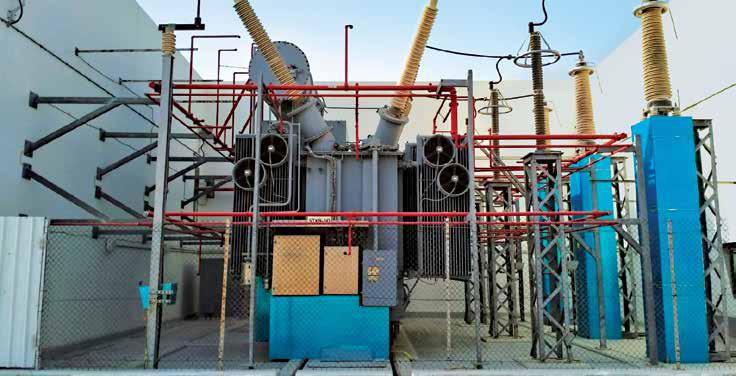
Existing 132 kV RAF A1 Transformer shifted and assembled at new location
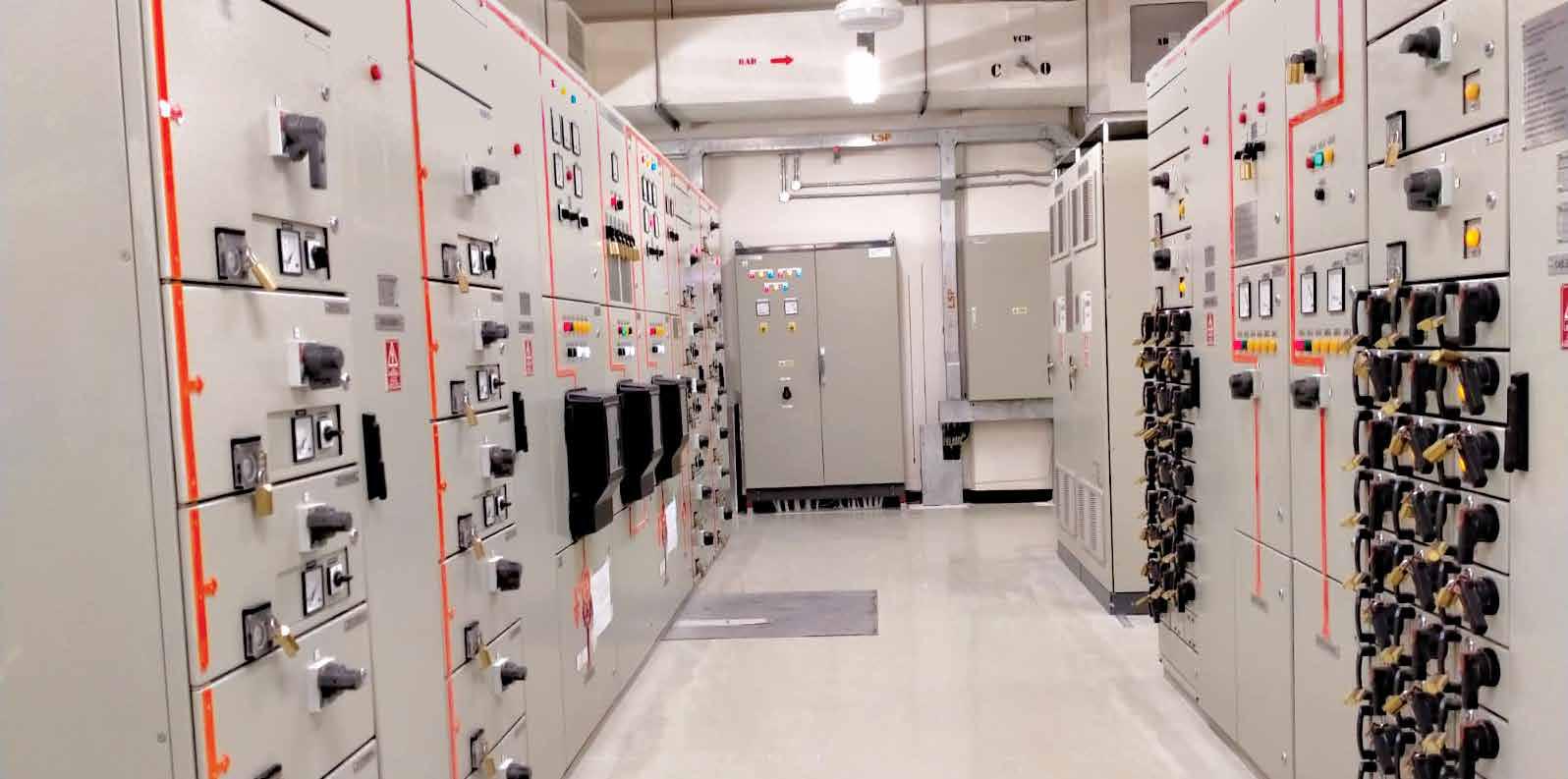
LVAC room
A job well done
“We completed testing and commissioning (NOSP) 30 132 kV GIS bays and associated substations works in just 10 and a half months from the award of the contract, a unique record in the KAHRAMMA network,” Aravindan’s expression is like that of a mountaineer who has scaled Mount Everest. “Our client and consultant both expressed their genuine appreciation when recognizing our timely completion and, more importantly, the quality of our delivery. What’s more, we obtained the Pre-Qualification approval to carry out the EHV cable diversions–related civil works as a benchmark first-time approval from KAHRAMMA.”
From the beginning, the focus of the project team was to obtain cleanroom access for the GIS room. “We did a tremendous job to complete the entire G+1 structure within 80 days from excavation,” observes Aravindan, lavishing praise on his civil team, “and the GIS room was handed over for Electrical and MEP activities within 53 days from the completion of the structure.” Perhaps for the first time in KAHRAMMA projects, the building completion certificate, which normally takes extremely long, was obtained within the taking-over period. Another achievement for the team to be certainly proud of was that all the 132 kV GIS bays were commissioned with less than 20 defect points during energization.
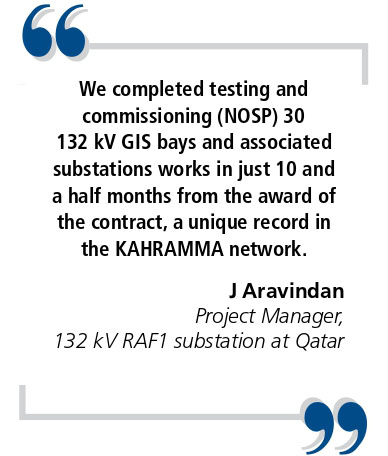
Credit is due to both EHS In-charge A Baskar and Quality In-charge Pankaj Jadeja for maintaining the highest standards, completing the project without a single LTI or NCR. Remote inspections and testing, VR-based safety training for employees & workmen and special training for engineers to manage critical tasks like transformer assembly with remote OEM supervision were some of the digital interventions successfully employed at site.
In the final analysis, Aravindan is a happy man as he not only delivered a tough project in a foreign land ahead of time but ensured that it was a profitable one too! Kudos to the entire team for a sterling on-time performance!