DELIVERING ON PROMISES, THE WET IC WAY
June 16th, 2022, will forever be etched in the minds of Project Manager Rajesh Madhaian and his team as the Hon’ble Chief Minister of Gujarat inaugurated the 100 MLD desalination plant, the first one constructed by L&T in partnership with Tecton, to provide water for industrial use to various industries of the PCPIR region of Dahej in Gujarat’s Bharuch district, apart from providing water to the existing Galenda reservoir. Completed three months ahead of time, which released fronts for electromagnetic works, the Gujarat Industrial Development Corporation is a happy client with their
vision realized.
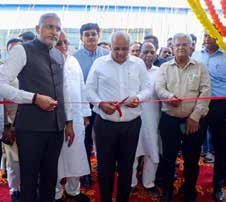
CM inauguration
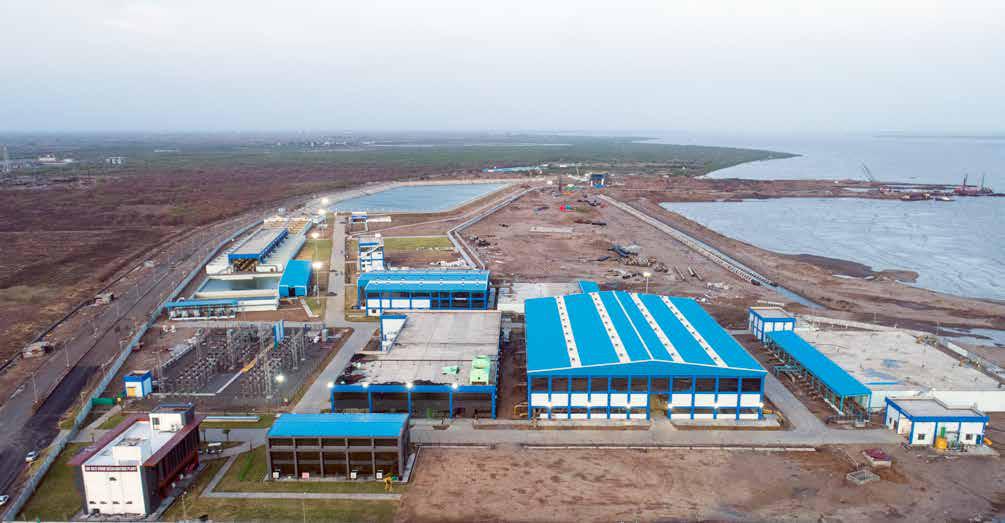
100 MLD WSRO Desalination Plant, Dahej
Realizing a vision
The ‘100 MLD WSRO Desalination Plant’ project was awarded on July 31st, 2019, to the L&T-Tecton JV on an
EPC-DBO (Design Build & Operate) basis with the scope comprising procuring the necessary statutory permissions, constructing and operating the plant for 10 years, located at the confluence of the River Narmada estuary at
Rahiyad village.
“Typical desalination plants handle only salinity (TDS-Total Dissolved Salts) as they draw water from the sea,” points out Rajesh, “but our unique plant draws a mix of river and sea water and has to handle varying tide levels. The project is based on SWRO (Sea Water Reverse Osmosis) membrane technology and houses robust pre-treatment units and the latest filtration technologies.” It has a unique energy recovery device too that salvages the energy of the rejected water to reduce overall power consumption; the resultant lowered power cost directly benefits the industries. Presently,
67 MLD has been booked by 22 industries with an additional 10 MLD reserved for GIDC.
“Typical desalination plants handle only salinity (TDS-Total Dissolved Salts) as they draw water from the sea, but our unique plant draws a mix of river and sea water and has to handle varying tide levels. The project is based on SWRO (Sea Water Reverse Osmosis) membrane technology and houses robust pre-treatment units and the latest filtration technologies.”
Rajesh Madhaian
Project Manager
Some of the project team’s initiatives
External glazing: For building the RO and other structures, high-end external glazing was preferred to Galvalume sheets & masonry walls, which reduced both work at height and manhours by eliminating staging works, quicker release of structure for the subsequent electromechanical works and reduced daylight requirements leading to significant savings in power cost.
Precast cable trenches: Hastened the process and, by shifting the production to factory units, resulted in better product finish and significantly faster execution.
Precast boundary wall: Understanding the project requirements for unhindered access for transit mixers, mechanical equipment, piping works and such activities, the construction of the boundary wall was strategically delayed. However, the idea to process a 3 m boundary wall was a fallback plan to catch up with the schedule and, by fabricating it at a reputed vendor’s premises, ensured that the material was ready while site preparations were underway.
For Planning Manager Madhup Sharma, the novelty was handling a sea-facing project. “Not only for me, but it was also the first time for the entire team,” he grins, though procuring the statutory permissions & CRZ clearances was no laughing matter. “Our initial application was processed through the Gujarat Pollution Control Board, the Gujarat Maritime Board, the Gujarat state-level Technical Advisory Committee and the Gujarat Coastal Zone Management Authority,” he ticks off the bodies involved on his fingers, “and the file was presented at the Ministry of Environment, Forest and Climate Change (MoEF&CC) meeting of August 27th, 2020. The technical proposal required modifications and the entire process had to be redone,” he says, throwing his hands up in the air. In coordination with the Environmental Consultant, MoEF officials and, for several inter-departmental clearances, the design team, the CRZ clearance was finally given on September 30th, 2020.
“Our initial application was processed through the Gujarat Pollution Control Board, the Gujarat Maritime Board, the Gujarat State level Technical Advisory Committee and the Gujarat Coastal Zone Management Authority.”
Madhup Sharma
Planning Manager
All systems go
Rajesh led his team from the front, pushing vigorously for approvals, organizing & coordinating with representatives from the consultants & client for factory visits, optimizing quantity requirements with vendors, selecting premium vendors and, most importantly, adhering to execution requirements. In the process, they had some initiatives to write home about.
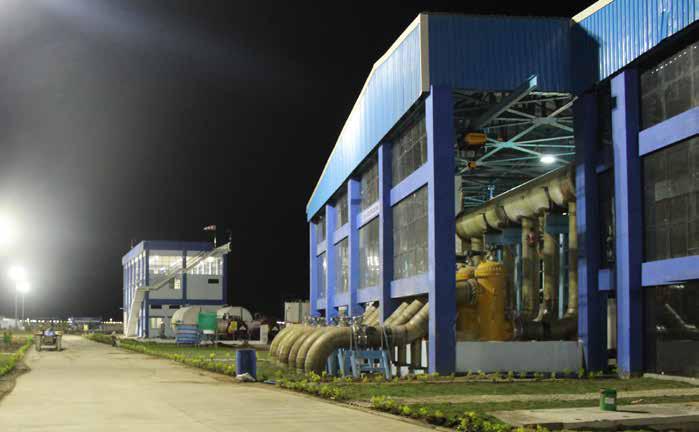
The huge task of handling, joining & laying humongous pipes
Another ‘first’ for the team was to handle the huge intake and outfall pipeline: 1,800 mm (wall thickness 114 mm) and 1,200 mm (wall thickness 49 mm). These were specialized pipes owing to their size with only a select few worldwide capable of manufacturing them. “The pipes delivered at site were approximately 12 m sticks that required to be joined by butt fusion welding,” says Madhup. “Normal working sizes range between 300 and 600 mm, but these were far bigger.” Closely interacting with fusion technology machine vendors and agencies (Mcelroy, Ritmo), by using various international code references and with the help of Vikas Kumar (CQM) and N. Nirapandian, Head QC, the site QC team was able to establish the WPS and PQR requirements for both the pipe sizes. The test pieces were passed and accordingly both the machine and operator were permitted to join the pipes. Both 1,200 mm and 1,800 mm HDPE pipes were hydrotested and passed all consultant evaluations without comments.
Building the critical intake structures
The project’s intake structures were on the critical path with several inherent challenges and risks that called for meticulous planning, engaging specialized agencies, handling heavy reinforcement cage lifts, deep excavations at
39 m, mud excavation through bucket and crane systems and managing huge water ingress requiring continuous dewatering works.
The intake pump house, travelling band screen and the inlet pipe chamber were constructed by the Diaphragm Wall method. Rajesh explains, “Normally, once the side walls are cast, the soil nailing is done to hold the walls in position along with the anchorage. In our case, the proximity to a water body on the southside, an existing ONGC well on the east side, a newly constructed earthen reservoir to the north side and a maintenance bay on the west side necessitated alternate methods for anchorage. The design team proposed interconnecting cross tie beams to hold the walls in position at four different elevations.”
The challenge was that after excavating to a certain depth, one layer of beam had to be concretized and the next stage of excavation could only be started after the first beam achieved its necessary strength and, added to the congestion due to the network of beams, the team was staring at the prospect of five months of construction time for 5 levels that they could ill-afford. Quality Manager Dani Nirmal picks up the story: “The excavation, shuttering, reinforcement works, and concrete placement activities require a minimum duration, but the ‘strength gaining’ or stripping time can be altered; accordingly we decided to try out quick strength concrete.” After discussions with Ultratech’s cement expert team, two variants among OPC Gr 53 type cement were frozen, aptly branded RAPID (48 hours full strength) & FAST (5-7 days M35 strength). “We reduced cycle time by at least 15 days across 5 levels and achieved an overall period reduction of 85 days,” sums up Rajesh jubilantly.
ALIRAJPUR LIFT IRRIGATION SCHEME – ANOTHER WATERSHED PROJECT
“Being an EPC project, we arranged for all the statutory permissions beginning with the environment & forest clearances, land acquisitions for permanent structures, electrical works, Railway, NH & other roads & river crossings to execute the work without local and political hindrances at site,” describes Project Manager Sunil Thakre, giving an overview of the project. In terms of land acquisition, the project team’s biggest challenge was to get 15 Ha at a stretch, which was well-nigh impossible as individual land holdings were often less than 0.5 Ha. “With a clear strategy and a time-bound plan, we completed the process of land acquisition for the factory, storage yards and various permanent structures within 9 months,” says a relieved Sunil.
“With a clear strategy and a time-bound plan, we completed the process of land acquisition for the factory, storage yards and various permanent structures within 9 months.”
Sunil Thakre
Project Manager
Negotiating an uphill struggle
All pump houses and distribution chambers are on hilly terrains ranging from 15 m to 80 m in height.
“The Pumphouse-1 required 40 m deep excavation in weathered and hard rock strata,” informs Planning Manager Abhishek Kumar Pandey.“We completed the earthwork of 72,000 cum. safely within 98 days. Further, being in a submergence zone, we deployed the slipform technique to construct it in 18 months.”
“The Pumphouse-1 required 40 m deep excavation in weathered and hard rock strata. We completed the earthwork of 72,000 cum. safely within 98 days. Further, being in a submergence zone, we deployed the slipform technique to construct it in
18 months.”
Abhishek Kumar Pandey
Planning Manager
The 26 km Rising Mains (of 2,770 mm & 1,860 mm dia.) run through hills, valleys, and forest areas for 8 km, which called for special methods for safe earthwork. “The challenge was to transport the pipes in these hilly terrains, where P&M came in handy by deploying double axle trailers,” remarks Sunil. “On an average, we had to develop new roads for every 500–800 m as the ROU couldn’t be developed across hills.” GPS systems tracked the transport vehicles as breakdowns in such terrains were common, with no proper mobile communication signals.
For the Rising Main Pipeline of 2,770 mm that passes through three hills of 20–30 m height across 650 RM, conventional methods were impossible as the limited ROU was in a forest area. The team therefore developed a Winch & Trolley method to lay the pipe safely without using a crane, which was recognized as the ‘Best Innovative Practice’
for 2019–20.
MS Pipelines of 400–2,770 mm dia. were laid along a 280 km stretch and HDPE ranging from 63 mm to 280 mm along 2,531 km to irrigate 35,000 Ha. Totally, 1,742 OMS boxes have been fixed to cover approximately 20 Ha with PFCMD controllers to control/regulate the water flow, discharge, and pressure and deliver water to eight 2.5 Ha chaks with minimum residual head of 20 m from each OMS box. These OMS boxes have antennas to send and receive signals from the Master Scada room housed at PH3 by means of LORA technology. The electrical 132 kV transmission lines for 30 km and 33 kV for 10 km were laid in hilly terrains to meet the demand of 35 MW to power all the pumphouses to pump water with mammoth pumps and motors of discharges varying from 6,870 cum./hour to 7,560 cum./hour.
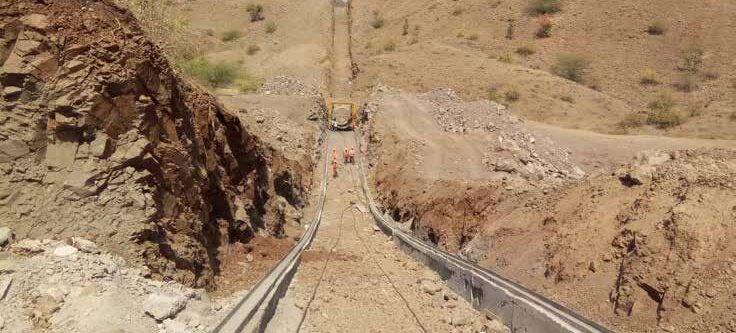
Alirajpur LIS Site
Abhishek is delighted that the project won the ‘Digitally Enabled’ award in 2019 for the slew of digital solutions employed at site including View EHS, QIR, PQI, ePragati, GIS Progress Monitoring, EDMS, BIM Progress for Pump House-1, VPR (Vendor Performance Rating),
P&M IoT & WISA.
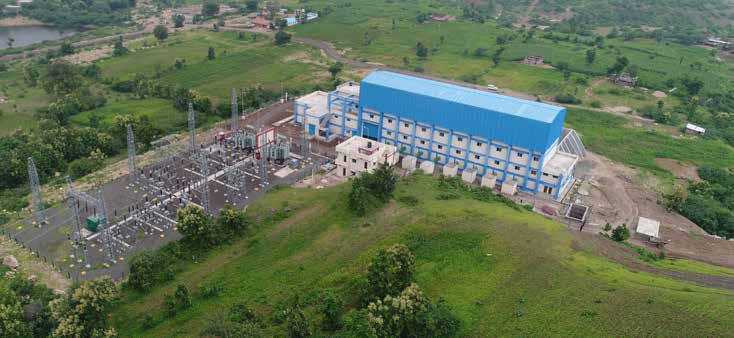
Alirajpur LIS Site 2
For the Rising Main Pipeline of 2,770 mm that passes through three hills of 20–30 m height across 650 RM, conventional methods were impossible as the limited ROU was in a forest area. The team therefore developed a Winch & Trolley method to lay the pipe safely without using a crane, which was recognized as the ‘Best Innovative Practice’
for 2019–20.
Automation to the fore
A major decision the team took was to establish a spiral factory at site that manufactured more than 350,000 RMT of pipeline of thickness varying from 3.15 mm to 7 mm in a span of 22 months, catering to three different projects within a radius of 250 km. Sunil reminds that established spiral mills run by reputed organizations in the country had ruled out the possibility of manufacturing pipes of 3.15 mm thickness. “Our QA/ QC and site teams under the able leadership of
K Prabakaran put up the factory in 4.5 months replete with a BIS license.” Similarly, other processes like painting and guniting were mechanized with the latest technology plants for mass production of finished MS Pipe to meet the laying & joining targets, going a long way in winning the client’s confidence.
The 28,500 MT of MS bare pipes (2,770 mm to 1,300 mm dia.) and around 14,500 MT of MS pipes (1,200 mm to 400 mm dia.) that were fabricated at site required the Gunniting & Epoxy coating before transporting them, for which automated Gunniting & Coating plants were established at site. Other than the pipes, huge pumps & HT motors, transformers, flow meters, butterfly valves, electrical panels, VFD panels, etc. were moved through hilly and uneven routes using heavy duty trailers and expert teams to the pumphouses and erected successfully.
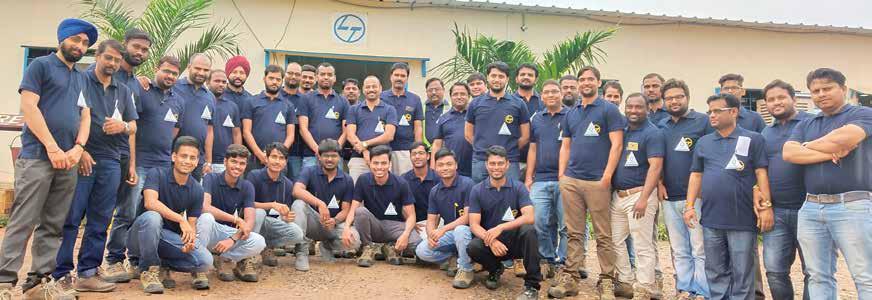
Other challenges included mobilizing manpower & skilled labour in an area like Alirajpur district, with 99% population being tribal adivasis. The team, however, managed to retain 90% of their workforce. More than 200 subcontractors have been engaged at site for different site works and about 20-25 local subcontractors developed for the HDPE Pipeline, inline civil works, etc. All the workmen and employees have been adequately trained in EHS & Quality, and various training sessions on self-development of employees were organized through the segment and HQ for the team to improve their technical and management skills.
16 SCHEMES. 21,300 HA. 115 VILLAGES. 21,684 BENEFICIARIES.
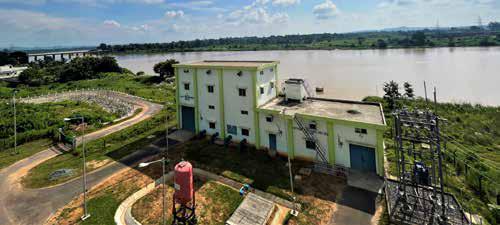
Cluster XII Site
Project Manager S S Mani and his team at the Mega Lift Irrigation Project, Cluster XII, in Odisha have been mandated to construct 16 pumphouses & MCC rooms and eight 33/11 kV substations, lay 260 km of DI pipelines & 909 km of HDPE pipelines, create 5,276 total outlet systems, lay 76 km of transmission lines, and put up 53 VT pumps to achieve a total discharge of 77,737 cum. per hour. Mani’s focus is on the client, and his approach is clear: to keep them on his side. “Anticipate their needs and objectives, communicate regularly, perform exceptional work to their satisfaction, take regular feedback from them and the PMCs, and maintain good relationships to build long-time associations and thereby delight the customer.”
“Anticipate their needs and objectives, communicate regularly, perform exceptional works to their satisfaction, take regular feedback from them and the PMCs and maintain good relationships to build long time associations and thereby delight the customer.”
S S Mani
Project Manager
As with most water infrastructure projects, initial survey, finalizing the cultivable command area, land acquisition and RoW were their initial challenges. “To identify and finalise 21,300 Ha of cultivable area, we conducted a topographical survey for around 1,000 sq. km area covering 115 villages in 7 blocks,” informs Planning Manager T Arulgnanam, “to determine the locations for the pumphouses & substations, route of the pipeline network, and power connectivity.” The survey had to be conducted across various terrains, dense forests, habitations, canals, nallas, the works. Since most of the schemes are in Sundergarh, which is considered a scheduled district, land acquisition involved an SIA
(Social Impact Assessment). Political inferences were addressed with the help of the local district administration.
Automating SCADA – another ‘first’
The Megalift Irrigation Project, Cluster XII is the first project in Odisha to use the SCADA (Supervisory Control and Data Acquisition) and Automation concept. The 21,300 Ha of irrigation land is operated through 5,325 Outlet Management Systems (OMSs) installed at every 4 Ha chak. Network connectivity towers have been strategically installed for seamless communication through the LORA network system from the central control room to the OMS installed on agriculture land. All the 5,325 OMSs are operated and monitored from a central control room situated at one of the Pumphouses, Semina-II, with the help of SCADA to monitor and control the equipment and gather and analyse real-time data for enhancements.
RoW was another thorn in their flesh as the major scope involves DI & HDPE pipeline network of 1,169 km covering 115 villages and 76 km of transmission lines that pass through several villages and reserve forest areas where the team faced severe resistance from the local farmers. The IR team did their bit by procuring approvals from the various District & State headquarters to construct on forest lands.
Supply, resource & contract management
“Optimizing the design and locations of the pumphouse & command area during detailed engineering helped to reduce the distribution network’s HDPE pipe length & electromechanical items, saving cost as compared to the prebid stage,” informs Mani. All the electromechanical items (DI & HDPE pipes, pump, motors, electrical panels, transformers, etc.) were procured efficiently to minimize the working capital cycle for conversion to cash. Resource mobilization of subcontractors, materials and P&M was planned well in advance, and contractors were engaged immediately after the monsoon to achieve maximum progress in the 6-month working season.
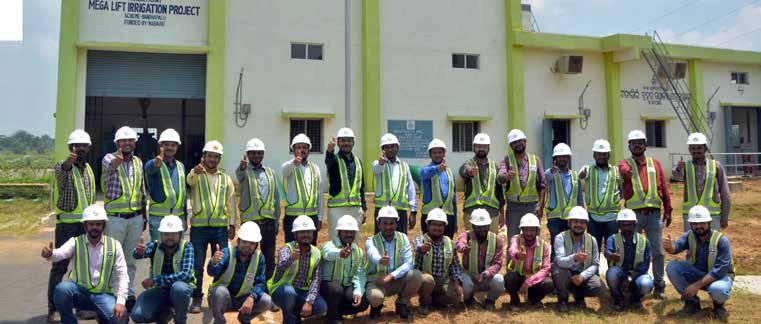
Cluster XII, Prtoject Team
The team strategically focused on submission, certification & collection of running bills from the client within the stipulated time, which helped them maintain a positive cash flow and a negative working capital throughout the project period. Digitalization is through
e-Pragathi, View EHS, Power BI, QIR, P&M IoT & WISA.
IASTW – PHASE 3A: SIMPLY DELIVERED ON TIME
The Industrial Area Sewage Treatment Works (IASTW) project is located in the southwest part of Doha, Qatar’s capital, and the client – the Public Works Authority – popularly known as ASHGHAL, visioned to achieve the world’s highest quality to treat sewage effluent to be used for the city’s irrigation network. L&T was awarded the ‘concept to commissioning’ project in November 2018 and successfully completed it in November 2021, well within the allocated time frame for project execution, clocking around 4 million safe manhours in the process, much to EHS Manager Saif Saeed Bagdadi’s delight.
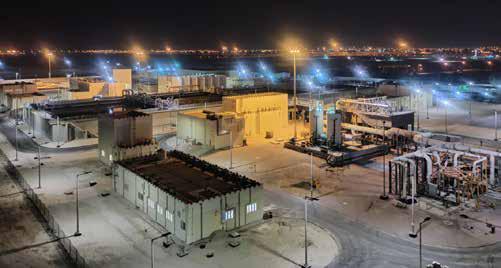
Industrial Area STP, Qatar
The project has modern Sequential Batch Reactor (SBR) technology followed by ultra filtration & UV disinfection, and the sludge generated from the SBR is treated within the plant to achieve the required dry solid content for further disposal. Currently the project is being successfully operated, meeting all the required performance guarantee parameters.
Project Manager, S Vishal is all praise for his team having achieved almost zero solid contamination and using the split backlash concept for ultra-filtration, saving almost 50% of energy in comparison to using conventional methods. “We did zero harm to the environment and to personnel during execution and that is key to our success,” he declares proudly. “A robust design using BioWin software strengthened our TSE standard, which helped us achieve <5 ppm Total Nitrogen, which is unique for sewage treatment plants the world over.”
“We carried out AERMOD, an Odour Disappearance Model, at the beginning of the project, which resulted in zero odour emission from the STP.”
S Vishal
Project Manager
“We carried out AERMOD, an Odour Disappearance Model, at the beginning of the project, which resulted in zero odour emission from the STP,” remarks Planning Manager Hariom Kumar. “And by carrying our CFD (Computational Fluid Dynamic) for the deep inlet pump station, we achieved the best operation efficiency.”
4 projects. 4 jubilant project teams. 4 delighted clients. That’s the way they do it at WET IC!
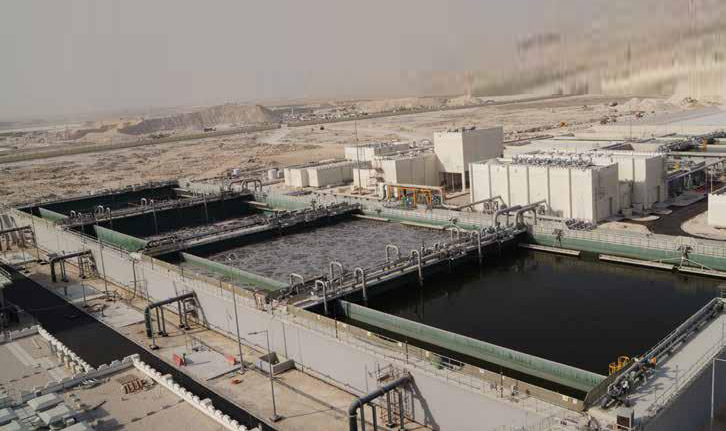
“We did zero harm to the environment and to personnel during execution and that is key to our success.”
Hariom Kumar
Planning Manager