FOR L&T, A WORLD RECORD. FOR THE CLIENT, QUICKER PROGRESS.
In August 2022, the iconic Mumbai Coastal Road project of Heavy Civil IC thrust its way into the record books by setting a world record in tunnel boring. The 12.18 dia Slurry TBM, named ‘Mavala’, the largest deployed in the country at Package 4, excavated 456.72 m in the calendar month of July beating the previous record of 455.4 m set by a Turkish company for monthly tunnelling by a 13 m single shield EPB (Earth Pressure Balance) TBM. While the entire organization is celebrating the record, achieved thanks to an experienced & well-qualified team helped in no small measure by a benign geology, for the client, the Municipal Corporation of Greater Mumbai (MCGM), the pace of boring is good news as it translates into accelerated progress and quicker project completion.
While Project Director, Sandeep Singh, cannot stop smiling, this is sweet respite for the several issues he and his team have had to face starting with the environmental clearances, the pandemic, the Mumbai traffic and monsoon, nature’s fury, the list is seemingly endless.

The 7.87 km stretch that falls within L&T’s ambit of the total 10.58 km long Phase 1 of the project will have four interchanges at Amarsons Garden (Breach Candy), Worli, Haji Ali & Marine Lines.
“The TBM was delivered when the pandemic was at its height,” he recalls, “and neither could the experts travel to help us, nor did we have any knowledge how to assemble it.” Realizing that often the best help is at the end of one’s own hand, the team took it upon themselves to assemble it on the ground. “Lowering a fully assembled TBM, weighing some 2,500 tonnes, into the launching shaft was attempted perhaps for the first time in India and we succeeded but then that’s what you call innovation,” grins Sandeep.
The 7.87 km stretch that falls within L&T’s ambit of the total 10.58 km long Phase 1 of the project will have four interchanges at Amarsons Garden (Breach Candy), Worli, Haji Ali & Marine Lines.
“Lowering a fully assembled TBM, weighing some 2,500 tonnes, into the launching shaft was attempted perhaps for the first time in India and we succeeded but then that’s what you call innovation.”
Sandeep Singh
Project Director
ADDRESSING DISRUPTIONS AND CONVERTING THE SOLUTIONS INTO SOPs
Massive reclamation
“We have reclaimed 111 Ha of land from the Arabian Sea that is as big as 274 football fields,” remarks Planning Head, Raj Kumar, referring to the massive extent of reclamation in the inter-tidal zone that placed extra onus on the team to both keep the environment clean and preserve the marine life in the region. “To diffuse the tidal force, we have used core rocks overlaid with armour rocks that allow for the sea to move in unhindered, under the reclaimed land and also preserves aquatic life,” he points out. “Some corals along the Amarsons Garden ‐ Haji Ali stretch have been relocated to Navy Nagar in Colaba and are doing well,” he smiles, perhaps in relief. The new reclamation will feature a 1 km cantilever promenade from Princess Street to Girgaon Chowpatti for the citizens of Mumbai to enjoy.
“We have reclaimed 111 Ha of land from the Arabian Sea that is as big as 274 football fields.”
Raj Kumar
Planning Head
Monopile technology
Constantly seeking new technologies to speed up construction, the team opted for monopile construction for the bridge pillars that has thus far been used successfully only in Scotland & South Korea. Deployed in India for the first time, with raw material sourced from Europe, the monopiles are environmentally friendly, significantly reduces work, time, and cost and is aesthetically more attractive. “By adopting monopiles that are in a range of 2.5 – 3.2 m in dia, we have reduced the number of piles from 704 to just 176,” flags off Raj. “This also means that we are putting up less piles on the seabed and thus disrupting the marine life less to that extent.”
The pandemic cleared the Mumbai roads for free movement
Considering the strategic importance of the project, MCGM was keen that construction was not disrupted by the pandemic so with special permissions, the project team continued work even during the lockdowns. “The lockdowns were a boon for us,” says Raj, with relief, gesturing towards the road outside the site that is choc-a-bloc with traffic in the early afternoon, that was previously considered a non-peak hour. “With the roads cleared of traffic, we could bring in material, move equipment and take away debris from the reclamation without any hinderances.” The Mavala TBM was delivered at site on 273 vehicles in quick time that would otherwise have taken months to transport on the normal Mumbai roads.
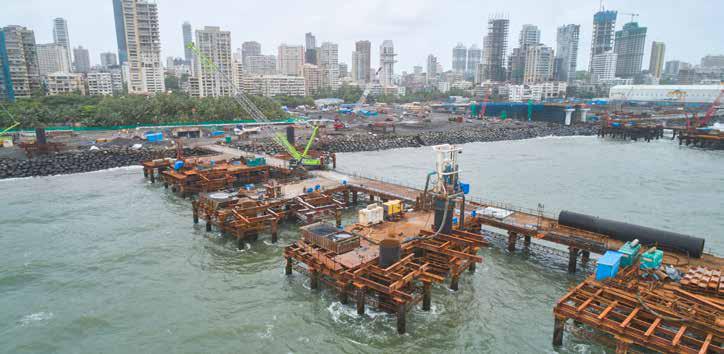
Deployed in India for the first time, with raw material sourced from Europe, the monopiles are environmentally friendly, significantly reduces work, time, and cost and is aesthetically more attractive.
Gasping for oxygen
With oxygen supplies being diverted almost entirely for medical purposes to treat COVID patients, the team switched to plasma cutting that has now been adopted as a SOP even after oxygen supplies have been restored.
Accommodating workmen at site
With Mumbai reeling under the COVID scare, mobilizing workmen was an extremely difficult task and with so many restrictions on movement, transporting them was a nightmare. The team therefore developed a labour camp at site, equipped with all facilities, to address all these issues.
Managing the TBM
The arrival of ‘Mavala’ at site was the opening chapter of an entire saga of first assembling it and then the bold decision to lower the fully assembled TBM to the launch ramp with three backup gantry parts, weighing 350 MT and three freshly assembled shields, weighing 1,500 MT, using a 200-wheel self-propelled modular transporter. The team is using the TBM to construct two 12 m wide tunnels of 2.072 km each running at depths of 5 ‐ 68 m under the Malabar Hills and
25 m below Girgaum Chowpatty between Priyadarshini Park and Marine Drive.
With 11 strategically placed cross passages for fast evacuation, the tunnels will be equipped with heat sensors, CCTV-based advanced traffic controls, Saccrado ventilation systems to pump in fresh air to main air parameters while work is in progress. The 2,072 rings in the tunnel consist of 16,576 precast concrete elements each weighing some 9 tonnes, equivalent to an
empty truck.
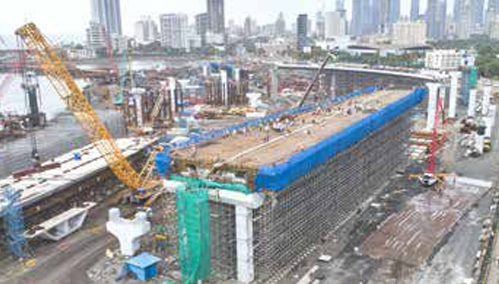
Once work started, the TBM smoothly burrowed its way to the end of the tunnel and then the team was faced with the arduous task of dismantling the TBM underground, lifting it part by part to the surface, transporting it to the new location where the second tunnel was to be launched, reassembling and lowering it to start boring. “All this would have taken several months and that is when our brainstorming gave us an absolutely out-of-this-world idea,” Sandeep pauses, perhaps thinking back to the moment when he had to take that call to go ahead with their plan. Their idea was to rotate the TBM in the tunnel itself and revise the TBM construction sequence. As per the earlier plan the 2nd tunnel was to be constructed from Priyadarshini Park to Girgaon Chowpatty site like the 1st drive which would have involved 6 months of work to dismantle the TBM, transport and re-assemble it at Priyadarshini Park. “We rotated the TBM inside the shaft and started the second tunnel from Girgaon Chowpatty within 3 months and saved us some 6 months of execution time in the process,” says an elated Sandeep. This will not only help in reducing the tunnelling activity but will also facilitate the other successive activities like MEP works to be started earlier.

To execute such a massive project involving so many facets of construction, calls for deep understanding of all the deliverables, meticulous planning, and picture-perfect execution capabilities.
“We are through with almost 75% of the tunneling and should be able to achieve breakthrough by December 2022,” says a confident sounding Pradeep Prasad, Construction Manager (Civil).
“We are through with almost 75% of the tunneling and should be able to achieve breakthrough by December 2022.”
Pradeep Prasad
Construction Manager (Civil)
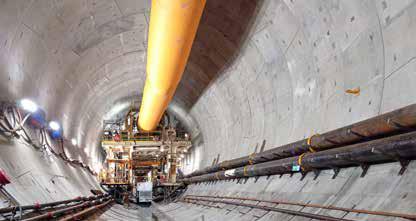
His colleague, Pradeep Kumar Sharma, Assistant Manager, P&M, Heavy Civil IC, reminds us that tunnelling is not only about TBM activity. “There is so much more to tunnelling including the MEP works, electricals, plumbing, ventilation, firefighting systems, live utilities and finally the road itself.” Both are unanimous that perhaps the most difficult aspect of MCRP is having to work and construct in the congested city of Mumbai. “In most places, we have very little space to maneuver,” laments Sharma, “Constructing on Marine Drive is particularly challenging, not just because of the density of traffic but being one of the city’s most important roads, very often our work is disrupted by VIP movement.
This stop-and‐start kind of work plays havoc with our delivery schedules and sometimes we have just 2–3-hour windows to work,” he points out with a long face.
“There is so much more to tunnelling including the MEP works, electricals, plumbing, ventilation, firefighting systems, live utilities and finally the road itself.”
Pradeep Kumar Sharma
Assistant Manager, P&M
Considering its sheer magnitude and complexity, MCRP is a dream project for any civil engineer, opines A H Khan,
Vice President & Head – Operations, Mumbai. “It involves tunnel cut and cover sections, huge reclamation, sea front protection with rocks of various sizes, underpasses, road works, large diameter monopiles, underground car park, viaducts with cast-in-situ, segmental launching involving girders and many more.” To execute such a massive project involving so many facets of construction, calls for deep understanding of all the deliverables, meticulous planning, and picture-perfect execution capabilities. “The teams at both packages have been constantly deliberating with project consultants, designers, and the Employer to improvise upon the deliverables, for them to be aesthetically pleasing and sustainable, with sharp emphasis on digitalization particularly BIM implementation, on-line monitoring of resources and data validation for operation excellence.”
“The teams at both packages have been constantly deliberating with project consultants, designers, and the Employer to improvise upon the deliverables, for them to be aesthetically pleasing and sustainable, with sharp emphasis on digitalization particularly BIM implementation, on-line monitoring of resources and data validation for operation excellence.”
A H Khan
Vice President & Head – Operations
November 2023 is fast approaching for Sandeep Singh and his hardy foot soldiers. They have already completed
a large section of the seawall, almost the entire reclamation and a fair number of the land piles, monopiles and superstructure jobs. There is still a mountain waiting to be climbed but the team is ready and raring to summit it.