HEAVY CIVIL PROJECTS OVERCOME HEAVY ODDS TO PUSH FORWARD
Although its impact on human health has reduced, the disruptions left by the pandemic in its wake are still being felt, more so in the construction industry. With things still only limping back to some degree of normalcy, it is commendable that several projects across businesses and geographies have found ways to push forward despite severe impediments. Here are some Heavy Civil IC projects that have bucked the odds and how.
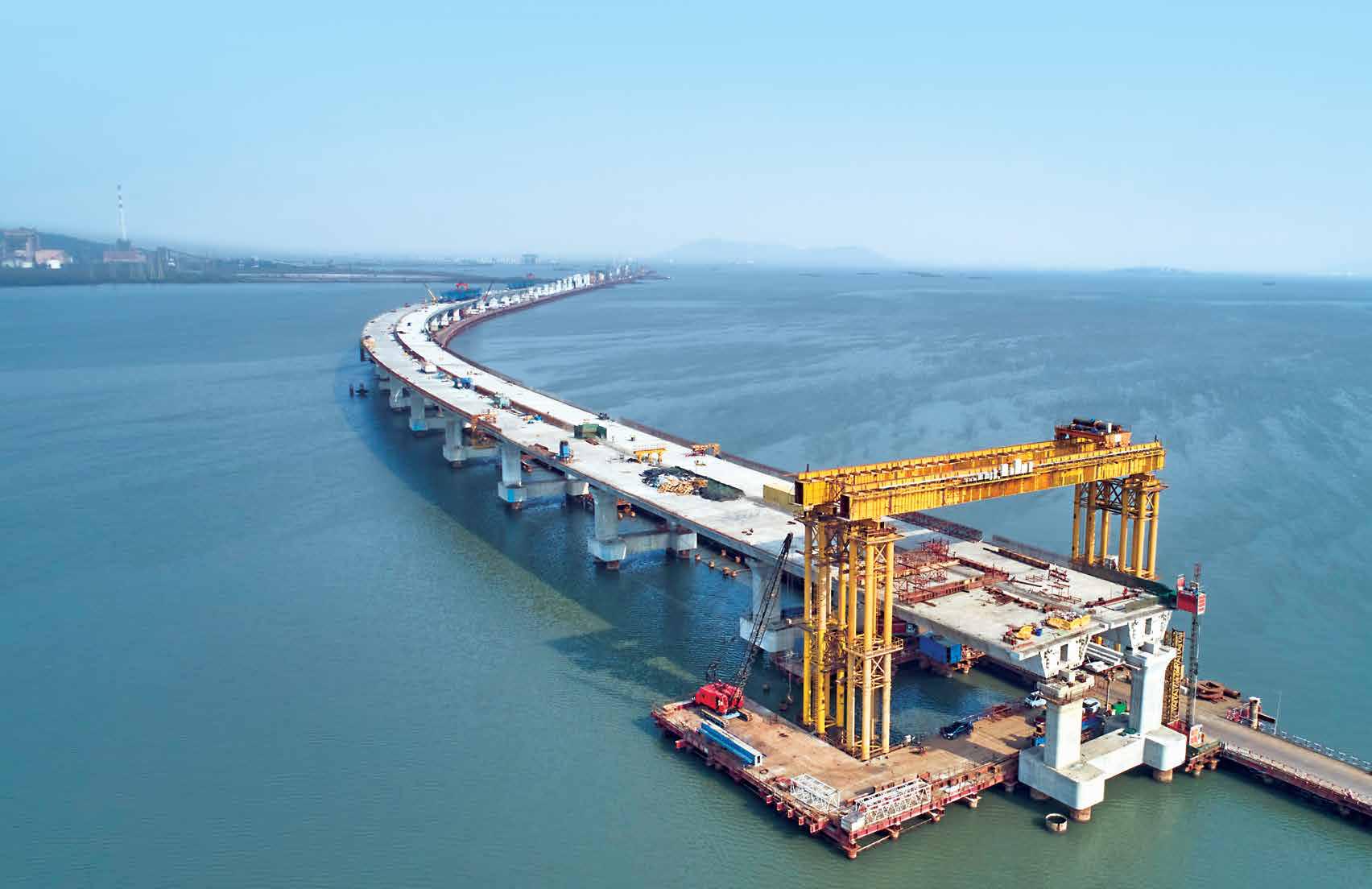
EVOLVING NEW STRATEGIES TO PROGRESS AT MCRP-1
Work began on the Mumbai Coastal Road Project, Package 1, in October 2018, and Project Director Rakesh Sisodia is satisfied that his project has made 60% physical progress and 46% financial progress as of end-January 2022, looking on track to complete on schedule in September 2023. Constructing next to the Arabian Sea, challenges have been rolling in, but the team has been more than up to the task. “To design and construct bridge profiles that include critical interchange loops of up to 70 m radius, we have had to integrate certain special constructability requirements into both the permanent and temporary designs,” shares Rakesh. Designs have been retrofitted to suit site conditions like conventional piling, hydraulic rigs, RCD for foundations, steel shutters & L&T formwork for the substructure, cast in-situ, L&T cup lock system, L&T HD tower system, LG & USG erection systems for the superstructure and sheet piles, stone columns using vibro floats, and geotextiles for shoring and ground stability. The bridge segment moulds have been designed inhouse, with procurement and fabrication carried out within the site premises.
“To design and construct bridge profiles that include critical interchange loops of up to 70 m radius, we have had to integrate certain special constructability requirements into both the permanent and temporary designs.”
Rakesh Sisodia
Project Director,
Mumbai Coastal Road Project,
Package 1
The team is using advanced state-of-the-art methodologies for the crucial tasks of reclamation and seawall construction, reclaiming land through land mode operations with complementary sustainable actions in selecting construction materials. The bridge foundation design is a highly iterative process between the structural and geotechnical engineers due to factors such as stiffness/displacement compatibility, load configuration, and geo constructability. “Constructing bridge foundations (pile cap) in an intertidal, marine and underwater environment poses logistic challenges classifying class A risk activity,” points out Planning Manager K Jayesh, “and therefore we have opted for monopile foundations. This futuristic technology is being used for the first time in the country, and we have cleared its technical feasibility through a technical committee headed by IIT-Bombay.”
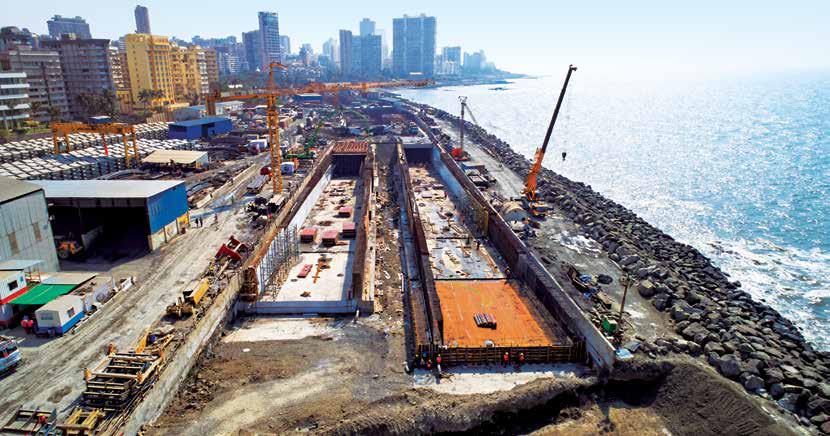
To construct in the heart of Mumbai is to contend with the city’s traffic, and although the team had initially planned for marine mode movement, thanks to the COVID lockdowns and restrictions on movement, they have successfully moved 85 lakh MT of quarried rock and fill materials 100% by road.
On the digitalization front, Digital Officer Mahesh Aithal mentions the use of a custom-made digital app for source-to-destination logistics mapping and E-TAP tagging & mapping throughout the enabling works structure life cycle (15,000 MT). EHS In-charge Gopinath Methanchery is happy that the site has clocked 8 million safe manhours, and his effort is to keep the
safety slate clean.
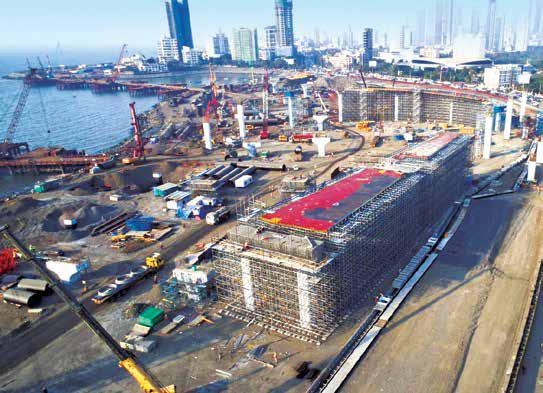
ADDRESSING THE GREEN CHALLENGE
Even before the project team hit the ground, the project was mired in various issues, a major one about protecting the marine biodiversity. “Extremely mindful of the corals in the worksites, we have taken several precautionary measures to protect them,” remarks Quality In-charge (QC) Umesh Kumar Singh. “Through NIO (National Institute of Oceanography) we have relocated some of the corals to Marine Drive and all have survived.” A feather in the site team’s cap is the ‘International Bronze’ Green Apple Environment Award they won for their green performance.
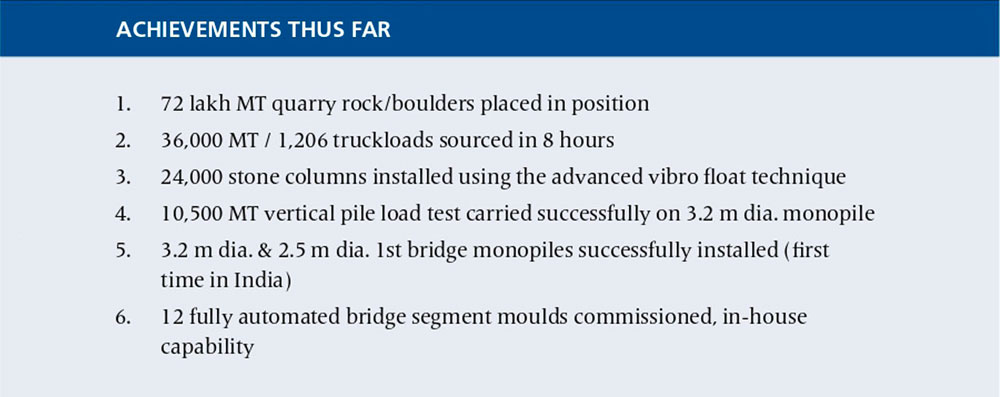
Other steps taken are offsite fabrication of 35,000 MT of structural steel, using 62,000 MT of GGBS as cementitious materials and employing a curing compound over 4.2 lakh sq. m area instead of water. The team has not used any fill for temporary access, and a 2,400 m temporary access bridge (TAB) has been constructed to keep all marine front works independent of waterbased operations. Prefabricated steel has been sourced from local suppliers, onsite fabrication has been avoided, and reinforcements sourced from L&T Panvel.
Looking forward, Rakesh seeks to continue his collaborative approach, applying lean construction concepts, implementing advanced bridge formwork systems for cast in-situ spans, adopting more digital solutions, keeping up the EHS culture, and empowering young engineers to raise the bar.
MCRP-4 IS HALFWAY TO DELIVERY
Given all the roadblocks the site team has had to overcome, Project Manager Sandeep Singh is breathing easy that they have completed 51% of the work and are now moving into top gear with the delivery date of late November 2023 fast approaching. Apart from the court cases that inordinately delayed progress, the pandemic has been playing havoc. “Many of our major equipment like TBMs are imported, and the disruptions in the supply chain, international trade and other commercial activities have impacted us badly,” Sandeep shakes his head. “We have, however, recalibrated our material planning, taking special permissions to transport equipment even during the lockdowns. Since OEM representatives could not visit India due to travel restrictions, we took it on ourselves to complete the TBM assembly and commissioning,” he adds proudly.
“We have, however, recalibrated our material planning, taking special permissions to transport equipment even during the lockdowns. Since OEM representatives could not visit India due to travel restrictions, we took it on ourselves to complete the TBM assembly and commissioning.”
Sandeep Singh
Project Manager, MCRP-4
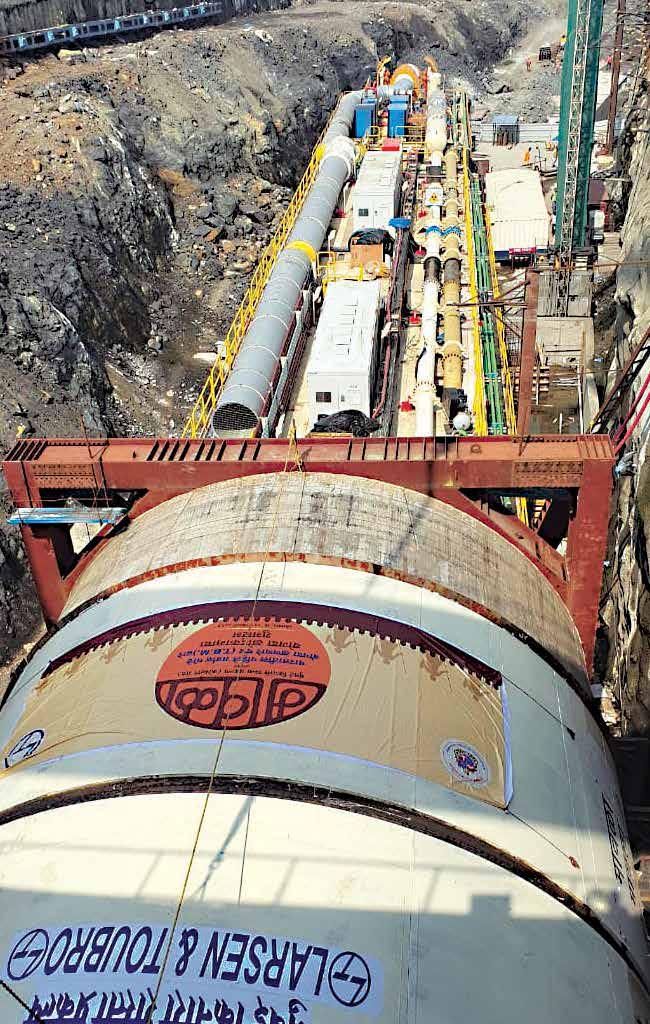
The TBM ‘Mavala’ in action
The 12.19 m dia., 2,400 MT TBM ‘Mavala’, the largest in use in the country, had to be assembled inside the shaft. “Work, however, was stopped for the launching shaft due to the pandemic, so it looked as if the TBM assembly would get delayed,” says Planning Manager
Manik Bhatnagar.
“Therefore we decided to assemble the TBM on the ground.” This created another challenge of lowering such heavyweight components inside the shaft, for which an innovative technique of strand jack was used to lower the TBM components weighing anywhere from 350 to 1600 MT in a single operation. “This reduced the complete operation by 60 days,” smiles Manik.
“The first bored tunnel drive has been successfully completed,” shares Sandeep, ticking off some of his project milestones. “We have achieved tunnel construction of up to 306 rmt/month, cut & cover tunnel construction at Priyadarshini Park has been completed and around 80% of segment casting is also over.”
PUSHING THE PEDAL
“To speed up progress, we have revised the TBM construction sequence,” points out Planning Manager Utkarsh Bhakare. “As per our earlier plan, the 2nd tunnel also had to be constructed from Priyadarshini Park to the Girgaon Chowpatty site, similar to the first drive, but that would have taken around 6 months to complete dismantling, transporting and re-assembling the TBM.” Instead, the project team plans to start the 2nd tunnel construction from the Girgaon Chowpatty site, which will save them some 3 months of execution time. “We have developed a rotation scheme for the TBM inside the shaft to reduce time and cost, which will not only reduce the tunnelling activity but also allow for other successive activities like MEP works to start in advance.”
RVNL-2 PROJECT SUCCESSFULLY DIGS INTO THE HIMALAYAS
Having started their project in January 2020 just before the outbreak of the pandemic, Project Manager Prabhu Kumar and team have been manfully pushing progress, with 30% complete as of end-January 2021. “8 km of tunnel has been completed, progressing 1,000 m in 41 days,” he shares proudly. “We have completed a two-track railway tunnel (15.7 m × 12.9 m) in multiple drifts (7 stages) for the first time in India, 4 months ahead of schedule, and achieved the first breakthrough between the three-track tunnel and single-track tunnel on 31st January 2022.”
“We have completed a two-track railway tunnel (15.7 m × 12.9 m) in multiple drifts (7 stages) for the first time in India, 4 months ahead of schedule, and achieved the first breakthrough between the three-track tunnel and single-track tunnel on 31st January 2022.”
Prabhu Kumar
Project Manager, RVNL-2
It has, however, been tough going. A discrepancy in the Geological Baseline Report to the geology on ground forced the site to start additional tunnel fronts. The pandemic threw up various speed breakers. “We had to change our mobilization strategy,” says Planning Manager Vishva Mohan Srivastava. “Instead of waiting for the main equipment, we mobilized locally available older machines to start the works and modified the work sequence to suit the available resources, which meant largely mobilizing workmen locally.”
“We have back-up options for every activity to ensure timely delivery of materials from multiple vendors, are monitoring the over break and working with experts to optimize blasting patterns to keep over break under 7%, and monitoring shotcrete thickness and rebound to control the wastage and increase progress.”
Vishva Mohan Srivastava
Planning Manager, RVNL-2
PUSHING FORWARD
Strategically, the team opened more tunnel faces and started activity earlier than planned. “Presently we are excavating from 16 tunnel faces against the planned 12 with almost the same set of equipment,” remarks Prabhu. “We have augmented the minor equipment (less costly) to improve the productivity of the major equipment.”
“3-month and 6-month look ahead plans have been prepared for resources, and we continuously monitor to mitigate the dynamic geological changes,” says Vishva. “We have back-up options for every activity to ensure timely delivery of materials from multiple vendors, are monitoring the over break and working with experts to optimize blasting patterns to keep over break under 7%, and monitoring shotcrete thickness and rebound to control the wastage and increase progress.”
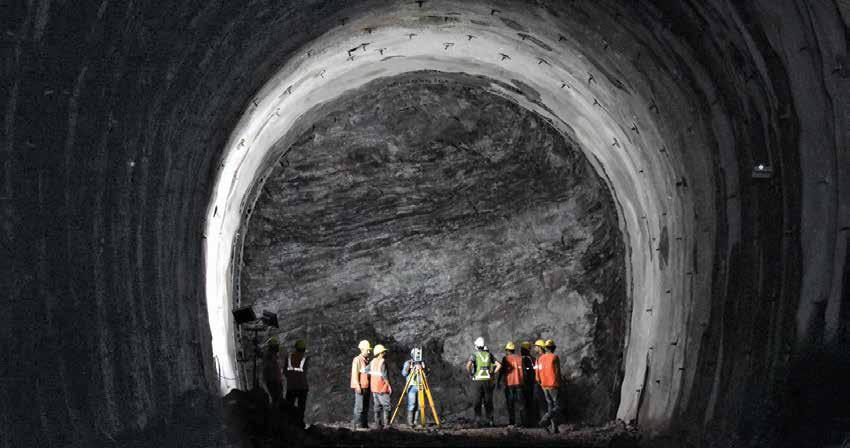
QUALITY TO THE FORE
The team is using Poly Fibre Reinforced Shotcrete (PFRS) in fair class of rock instead of Wiremesh and plain shotcrete to reduce cycle time and speed up progress. Air vent pipes in SDA/SN are bolt grouted to reduce pullout failures and rework. “Rebar cut pieces are being used in lattice girders to control the shotcrete thickness and anti-clog wire meshes in crusher conveyors to avoid clogging due to moisture,” informs Quality In-charge Manoj Kumar. Silt percentage in aggregates has been minimized to less than 10% to reduce the cement content in concrete. Advanced drill jumbos reduce time for navigation and drilling and provide vital drilling data to carry out various analyses to control over break, while the robot arm PLC shotcrete machine gives better reach and rebound control, resulting in better quality, with higher productivity and cost savings.
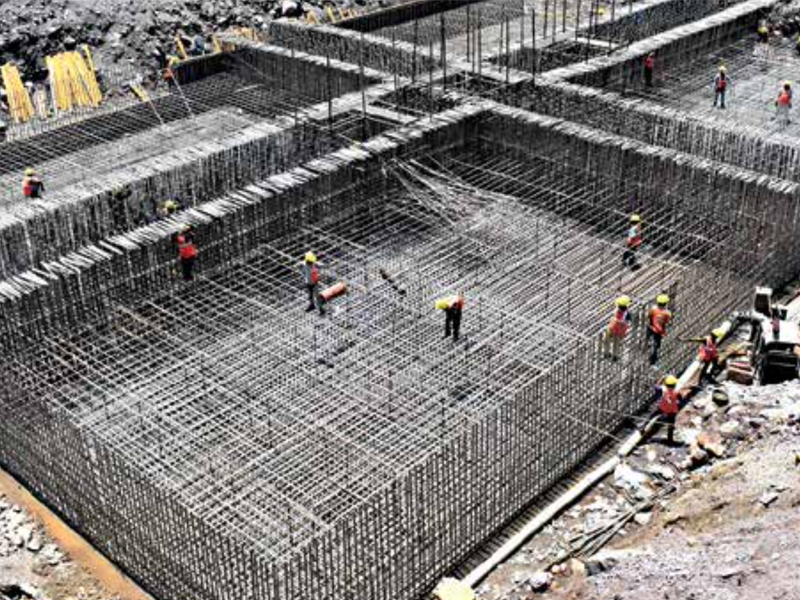
BEING DIGITAL
Video analytics help monitor entries and exits in the tunnel area to keep men and material safe and examine equipment productivity. “Our tunnel communication system, voice and video calling, ensures proper communication within and from/to outside the tunnel,” says Digital Officer Nannapaneni Srimaan. “Internet connectivity has been ensured inside the tunnel. We capture real-time drilling data from the equipment to predict upcoming rock strata and use prediction techniques such as TSP (Tunnel Seismic Prediction) and probe hole drilling.”
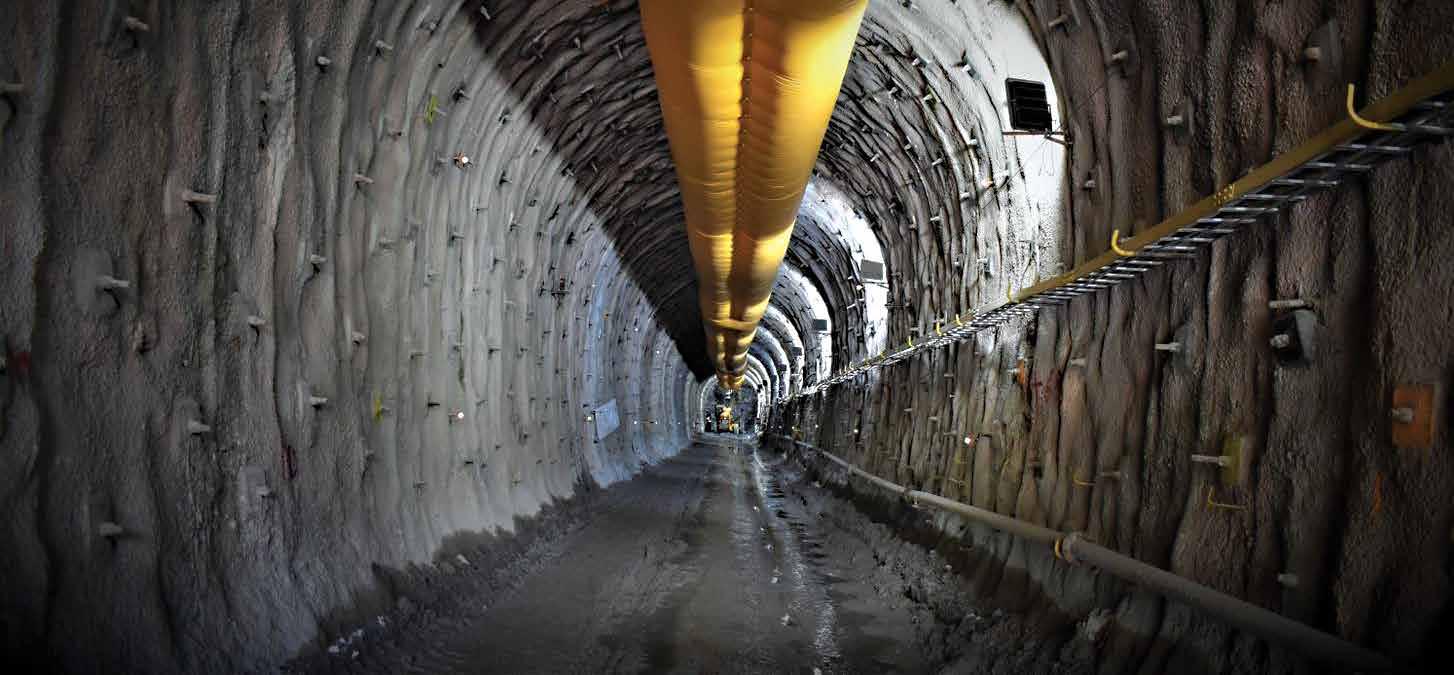
PEOPLE MATTER
Ultimately, it is the people that make the difference, and Prabhu and team are careful to pick key personnel with requisite skills for NATM tunnelling from within L&T and outside. Special simulator training for Drill Jumbo and Shotcrete Machine operators improves productivity and quality of work. “We are building a P&M team to handle various equipment which are being used for the first time not only in the organization but also in the country. With a nice mix of experienced hands and youngsters in various teams, we are pushing forward,” explains Prabhu.
The team has planned tunnel excavation across 17 fronts, concrete lining of tunnels along with the excavation of 14 tunnel lining gantries and micro planning for various activities of concrete lining for kerb concrete, geotextile membrane, PVC waterproofing, reinforcement, movement of lining gantry, concrete lining, and their logistics.
MTHL-3: TARGETING AN AHEAD OF SCHEDULE COMPLETION
The MTHL Package-3 project team under the leadership of Satya Prakash has completed 87% of financial and 70% of physical work to construct India’s longest sea bridge. Set to hand over in March 2023, the scope involves constructing a 3.613 km–long viaduct, entirely over land, with interchanges at SH-54 and NH-4B near Chirle in Navi Mumbai. “We have had our fair share of challenges,” says Satya with a tight smile. “Right of way, local threats, interfacing with the Railways, unexpected demand from the Railways to use stainless steel reinforcements for the railway spans, over-dependence on a single subcontractor for 40% of the initial work and, of course, the pandemic.”
“Our strategy has been to attack all possible available work fronts fully supported by our subcontractor. At the same time, we constantly followed up with our customer and GC to release the balance work fronts to prioritize stretches based on our requirements.”
Satya Prakash
Project Manager, MTHL-3
The project team also has huge deliverables. “Our strategy has been to attack all possible available work fronts fully supported by our subcontractor,” says Satya. “At the same time, we constantly followed up with our customer and GC to release the balance work fronts to prioritize stretches based on our requirements.” The ground reality forced them to change methodologies to ensure delivery. “We changed from an overhead LG to an underslung supporting system for precast segment erection as we didn’t have continuous stretches, which has actually saved us cost and time that we would have otherwise spent erecting and dismantling the LGs,” says Planning Manager S Prasanth. Satya mentions the decision to convert cast in-situ spans to precast, which saved them 3 months, and opting for the quicker rock fill embankment instead of soil fill to ensure filling works even during the rains.
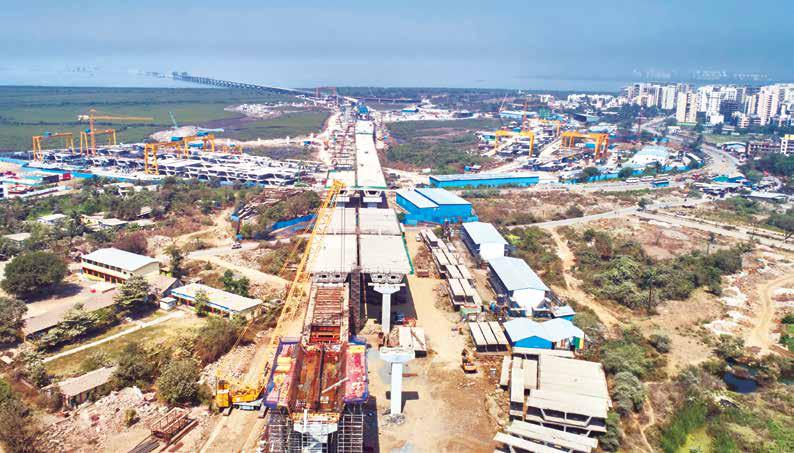
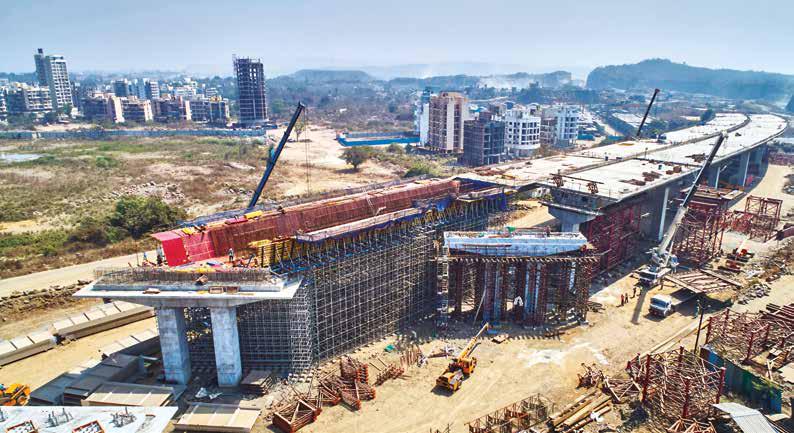
SAVING TIME, EFFORT AND COST
Normally, portal rebars are tied insitu on an erected platform, which is both time-consuming and risky. The team instead opted for prefabricated cages, during which staging and shuttering works could be completed simultaneously. The cage is then crane-lifted on to the erected staging. “This activity takes us about 1–2 hours and saved us 15 days!” smiles Prasanth. Another time-saving innovation was to develop a system to push the inner shutter with a helical gear, which would have otherwise required 45 minutes of hard labor involving 7–8 workmen. By developing a cantilever platform to avoid using cranes during stressing, the team saved about INR 50 lakhs.
“We changed from an overhead LG to an underslung supporting system for precast segment erection as we didn’t have continuous stretches, which has actually saved us cost and time that we would have otherwise spent erecting and dismantling the LGs.”
S Prasanth
Planning Manager, MTHL-3
Life is easier for Digital Officer Shivam Bhansal as drones monitor project progress while he monitors the project through Procube. Other digital tools in use include Conkart, ConPro & P&M IoT. Zero fatality at site is a feather in EHS In-charge Sajay Mishra’s cap. “We give onsite skill training, classroom training on different aspects of safety, and behavior-based training programmes for both employees and workmen.” Workmen are motivated with monthly safety awards; a penalty system pulls up defaulters, and the team follows a rigorous work permit system.
“We have minimal NCRs for the project and none for the Quality department,” declares Quality Incharge Pallab Kulia. “We use a highperformance concrete mix with 60% GGBS replacement and have established rock fill embankment filling and use testing methodology for faster construction.”
CTP-15A: NEARING THE HOME STRETCH
When asked to identify champions who have been chiefly instrumental to drive progress at his project, Project Manager H M Bhadri proudly says, “My entire DFCC-15A team, the Mumbai Cluster and HQ teams.” Truly, it has been wonderful teamwork as the team has completed 77% of this tough assignment to construct 8 OWG steel bridges. “Our expected date of delivery is 31st August 2022, but we expect to hand over by 31st December 2022,” he informs.
“The variation order to finalize the Kopar and Sanjali Bridges was hugely delayed, as was the finalization of designs and drawings for the Ulhas Bridge, to offset which we worked at multiple fronts in parallel and engaged a marine fleet to carry out simultaneous piling at multiple locations.”
Swapnil K Age
Planning Manager, CTP-15A
Spread over 400 km across the States of Maharashtra and Gujarat with an equal number of bridges in both States, the project is being executed through one central office controlling 8 site offices, one major and three site stores. For Bhadri and team, the challenges have been many. “6 out of the 8 bridges are running parallel to existing ‘live’ railway lines, and we have been forced to work in confined workspaces as some of our abutments infringe the existing railway embankment or foundation,” points out Planning Manager Swapnil K Age. “The variation order to finalize the Kopar and Sanjali Bridges was hugely delayed, as was the finalization of designs and drawings for the Ulhas Bridge,” he laments, “to offset which we worked at multiple fronts in parallel and engaged a marine fleet to carry out simultaneous piling at multiple locations.”
“We identified as many as eight fabrication agencies from across India and ordered 17,719 MT of steel fabrication and adopted the push launch technique over the embankment filling with a single truss without nosing girder and multiple trusses with nosing girders. ”
H M Bhadri
Project Manager, CTP-15A
TACKLING NON-STANDARD SUPERSTRUCTURE SPANS
With various span lengths of 79.88 m, 48.5 m, and 71 m to construct, the team identified multiple RDSO-approved agencies for fabrication and finalized an erection scheme that was feasible to the various sites. “We identified as many as eight fabrication agencies from across India and ordered 17,719 MT of steel fabrication,” Bhadri explains, “and adopted the push launch technique over the embankment filling with a single truss without nosing girder and multiple trusses with nosing girders.”
The team also adopted staging, tandem lifting, cantilever and derrick crane erection methods according to the site conditions.
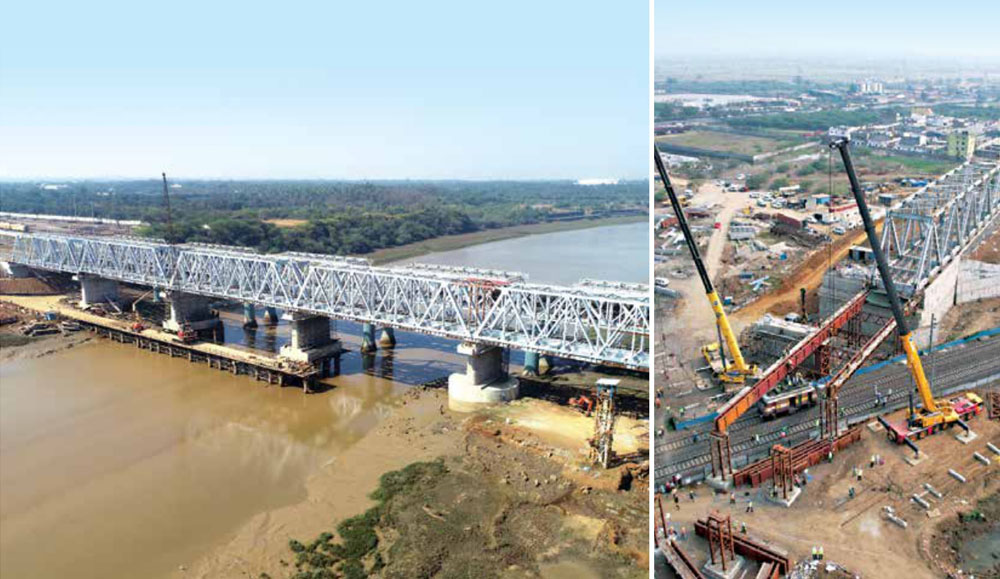
Par Bridge completed with push launch
Girder launching at Sanjali Bridge
TACKLING GEOLOGICAL CHALLENGES
During execution, the team faced variations in the strata other than what was mentioned in the GTI report, with unexpected and excessive settlement while carrying out initial load tests at the Sanjali Bridge. “We engaged excavators for rock breaking and well sinking in the well foundations and lifted the founding level post confirmation from Re-GTI/confirmatory bore hole,” shares QA/QC Manager A Venkatesan. “We changed the type of foundation well to open at the Kamwadi Bridge and adopted the latest IR standards (which increases the limit) to install additional piles within the confined space available at the Sanjali Bridge.”
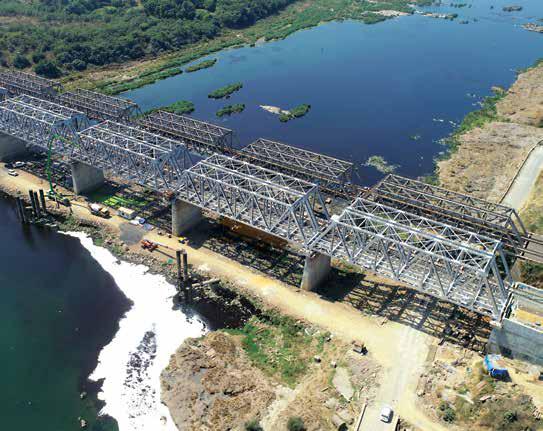
Damanganga Bridge fully erected
ADOPTING INNOVATIVE EXECUTION STRATEGIES
“Apart from the new strategies in well sinking, the team has adopted the latest launching techniques like Push Launching, Modified Derrick, Cantilever Erection with Cranes, using floating walkways instead of single pile ones at the Ulhas and Tapi Bridges, mobile cranes instead of derrick cranes at the Damanganga and Tapi Bridges for cantilever erections, and erecting the upline truss while the derrick crane runs on the downline with the help of CMPC, Mumbai Team & SPCM, HQ Team,” says Erection Incharge C M Fredrick.
SOME SIGNIFICANT ACHIEVEMENTS
The first bridge in 15A, the Par Bridge (downline), was handed over on 24th December 2021, which involved launching five 48.5 m spans weighing 1200 MT in 5 effective shifts using base girder, Hillman roller and nosing girder. The second bridge in 15A, the Sanjali Bridge (downline), was handed over on 5th February 2022, which involved launching a 71 m span truss weighing 610 MT during a 90-minute railway block using base girder and bogiewheel. On the same day, the third bridge in 15A, the Damanganga Bridge (downline), was handed over after completing the erection works of all 12 trusses (upline and downline) using staging, cantilever, and tandem lifting methods. Lastly, all the marine piles at the Ulhas Bridge have been completed in 6 months, involving rock breaking using the conventional method of winches and tripods.
For Bhadri, Satya and their teams, like for all other project teams of Heavy Civil IC, the challenges remain, but they are driven to achieve their milestones and targets in time, so all the best to them!