L&T GEOSTRUCTURE IS DRILLING DEEP FOUNDATIONS FOR THE BULLET TRAIN
The Mumbai-Ahmedabad High Speed Rail corridor or the Bullet Train, as it is popularly referred to, has caught people’s imagination for it represents perhaps the most significant technology leap that the country has attempted in the recent past. For L&T, it is not only the largest EPC order ever awarded in India but also offers scope for various businesses within its fold to contribute to this mega nation building effort.
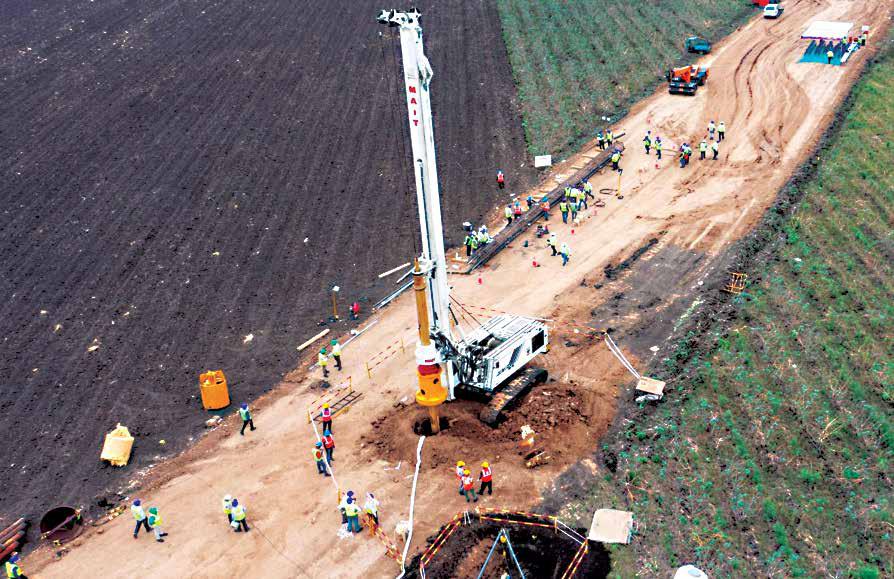
For T Srinivasan (Tsn), Head & Chief Executive, L&T GeoStructure and his team, the scope of work involves conducting soil investigation, pile load tests and piling works for the 236 kms stretch of the C4 package. To monitor progress better they have divided this long stretch into 5 sections, each with a Section Head, and these sections have been further subdivided into 3 km stretches. “Our scope is huge,” nods Tsn, spreading his arms to indicate the massive spread, “and we are mandated to carry out detailed soil investigation works for 2,450 boreholes, approximately 100 running km, with all the necessary tests to evaluate the physical and engineering properties of the soil and rock strata, and then design the foundation systems.” Once the laboratory tests are completed in each segment, investigation reports will be compiled, test pile locations identified and then the Initial Pile Load Test (IPLT) conducted, based on the results of which the working piles drawings will be finalised.
“Our scope is huge and we are mandated to carry out detailed soil investigation works for 2,450 boreholes, approximately 100 running km, with all the necessary tests to evaluate the physical and engineering properties of the soil and rock strata, and then design the foundation systems.”
T Srinivasan
Head & Chief Executive, L&T GeoStructure
The working pile installation involves boring 29,755 piles, approximately 900 running km of diameters varying from 750 mm to 1800 mm using hydraulic rigs in both soil and rocks. Pile boring ranging from 20 m to 50 m is stabilised using eco-friendly polymer fluid and M40 grade concrete is poured into the pile using tremie pipes, involving 1.2 million cum of concrete and 1.2 lakh MT of reinforcement works.
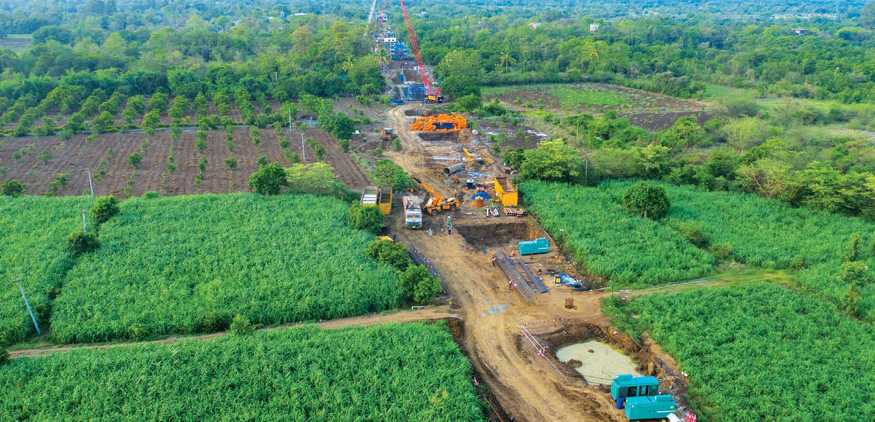
Big project. Bigger challenges.
“We have carefully planned mobilization of the Geotechnical Investigation (GTI) rigs that demand exacting specifications,” mentions, Quality and Investigation Head, S.N Rajan. “Therefore, we purchased imported rigs, modified our own existing rigs and even designed and developed the rigs indigenously from other agencies to meet the specific requirements of the job. In all, we have deployed 50 GTI Rigs.”
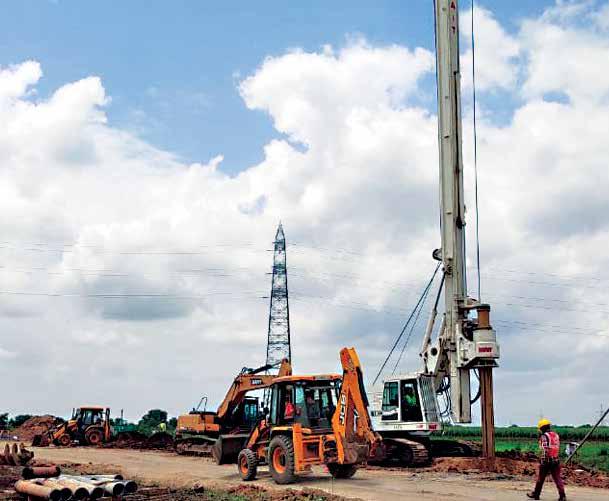
“We have carefully planned mobilization of the Geotechnical Investigation (GTI) rigs that demand exacting specifications. Therefore, we purchased imported rigs, modified our own existing rigs and even designed and developed the rigs indigenously from other agencies to meet the specific requirements of the job. In all, we have deployed 50 GTI Rigs.”
S.N Rajan
Quality and Investigation Head
Another challenge is to test the soil and rock samples collected from the 2,450 boreholes. Engineering property testing procedures are complex, time consuming, requiring highly skilled trained technicians to conduct the tests, and qualified geotechnical engineers to interpret the test results. Secondly, the client, NHSRCL (National HighSpeed Rail Corporation Limited) has mandated that all samples be tested in laboratories accredited by the National Accreditation Board for Calibration and Testing of Laboratories (NABL) to ensure accuracy and reliability of the test results. All the 20+ NABL accredited laboratories in and around the project stretch were identified, scrutinized, and inspected by both the client and L&T and only a handful were found to possess even the right equipment and resource to cater to the testing demand of the project. “While we were required to test about 400 samples a day, these local labs, at best, were only capable to test some 20 samples a day,” points out Tsn, “and therefore considering the quantum of testing and our stringent deadlines the only alternative was to set up our own facilities.”
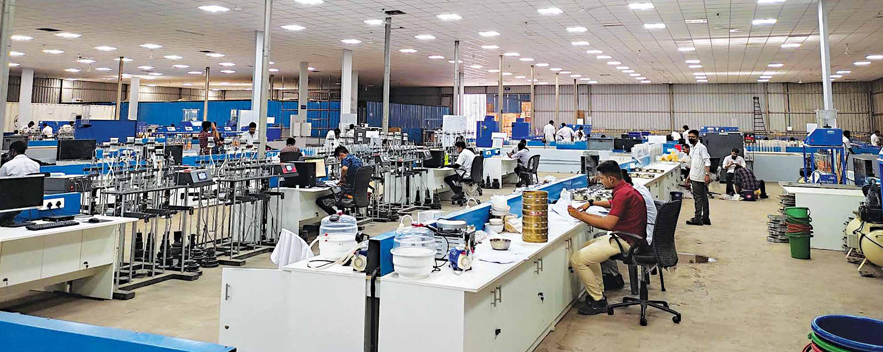
Asia’s largest Geotechnical Lab at Surat
The world’s largest onsite testing facility: The L&T GeoStructure team has thus successfully established a modern, state-of-the-art Geo Technical Testing Laboratory that is the world’s largest such onsite testing facility. Set up over an area of 5,000 sqm at Anthroli in the outskirts of Surat, it is equipped with state-of-the-art automatic and digital testing equipment with accuracies meeting all the codal provisions. Housing 140 automatic triaxial and 350 automatic consolidation equipment, this lab is by far the highest installed capacity of engineering property test equipment in India and about 100 times the capacity of an existing typical geotechnical laboratory. “The lab has been designed and equipped to conduct 3,500 tests a day,” shares a proud Nakkiran, Head – Special Projects, L&T GeoStructure. “It is manned by 180 specially trained technicians to conduct and record test data that is evaluated, interpreted, and reported by 20 qualified and experienced geotechnical engineers to ensure correctness, accuracy and reliability of test results.”
“The lab has been designed and equipped to conduct 3,500 tests a day. It is manned by 180 specially trained technicians to conduct and record test data that is evaluated, interpreted, and reported by 20 qualified and experienced geotechnical engineers to ensure correctness, accuracy and reliability of test results.”
Nakkiran
Head – Special Projects, Mumbai-Ahmedabad High Speed Rail Corridor
50 GTI rigs have been mobilized for on-field investigation, making it one of India’s largest ever on-field geotechnical investigation activity undertaken for any infrastructure project. “To manage such size and scale, we realize that digitalization is certainly the way forward,” adds S.N Rajan. “All the GTI data are captured through a specially developed mobile App while all the data pertaining to each borehole such as drilling depth, samples collected, and testing reports are stored and transmitted digitally.”
Routine load tests are being conducted on 1% of working piles. 25% of the routine load tests are static load tested and the balance 75%, dynamic pile load tested. Further, 100% of the working installed in rock and 40% of working piles installed in soil are subjected to Cross Hole Sonic Logging (CHSL) and Pile Integrity Tests (PIT).
Digging deeper to progress
It is natural for a project of such scale and complexity to throw up challenges. For Project Director, Sanjeevi Perumal, a couple of challenges that are keeping him awake at nights is the inaccessible, marshy areas they must contend with that the 236 km stretch runs through, the difficulty of mobilizing GTI & hydraulic piling rigs and associated equipment and clearing work fronts for both GTI and piling works.
A particularly severe monsoon threatens to wash away three months of their effort, but the team is pushing forward despite many challenges. Allocation, sharing and monitoring resources by ensuring parallel working at all the 5 sections is critical in addition to workmen mobilization and availability, to overcome COVID disruptions.
“By parallelly installing the working piles, we have completed 700 piles till date despite the various challenges. We have already mobilized 35 hydraulic rigs and plan to increase our speed and scale in the coming months post the monsoon to complete the total piling scope of works by August 2022.”
Sanjeevi Perumal
Project Director, Mumbai-Ahmedabad High Speed Rail Corridor
The GTI works kicked off in January 2021 and till date, about 60% of the scope has been covered; the field investigation works are expected to be completed by December 2021 and the laboratory testing works by March 2022. “By parallelly installing the working piles, we have completed 700 piles till date despite the various challenges,” points out Sanjeev, putting up a brave front. “We have already mobilized 35 hydraulic rigs and plan to increase our speed and scale in the coming months post the monsoon to complete the total piling scope of works by August 2022.”
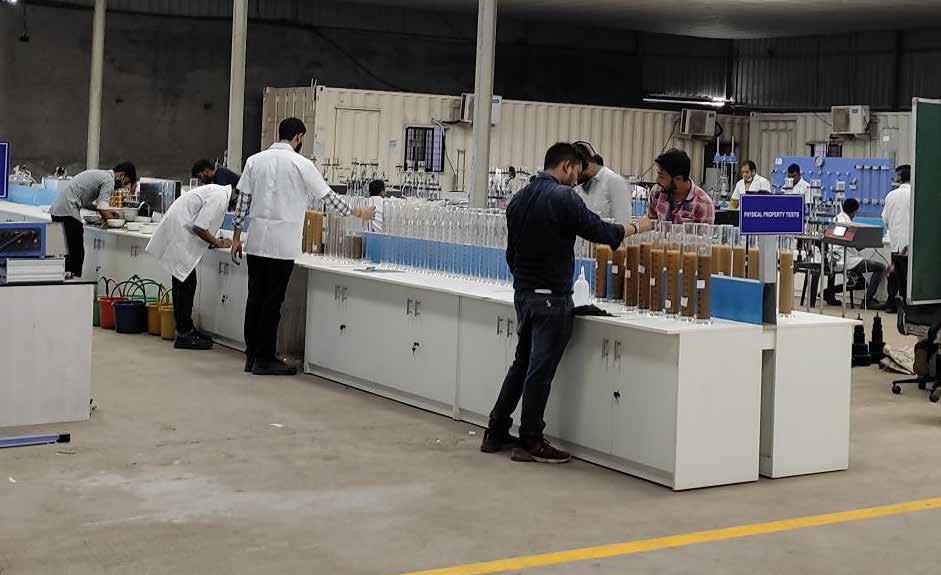
Raising foundations for the Katni Grade Separator
The 34 km-long, Katni Grade Separator project that L&T GeoStructure is executing across the second busiest railway junction in the country, once completed, will be India’s longest railway grade separator, perhaps the longest in Asia too. Comprising two packages upline and downline, of approximately 17 km length each, the project features 687 piled foundation substructures. The elevated grade separator is predominantly structural steel girders of 37,000 MT steel superstructure. 11 piling rigs have been deployed to bore and concrete 4,100 piles. For the concrete structure, four 30- cum-per-hour capacity batching plants are being established to meet the requirements of both the packages.
A state-of-the-art fabrication workshop with a monthly capacity of 2000T is being constructed at site, perhaps for the first time in L&T, to fabricate the structural steel girders while fully automatic CNC machines will fabricate the girders.
Driving progress
“Both packages are two significant projects within a project to be completed in 36 months from pile to rail,” remarks Project Director, T Harmis Jose, who must deliver both the UP and the DOWN Line railway grade separators running over New Katni Junction & Katni Murwara yards, that involve the construction of rail viaducts on pile foundations, composite steel girders & deck slabs, open web girders, retaining walls, minor bridges, earthwork & allied other civil engineering works.
“Both packages are two significant projects within a project to be completed in 36 months from pile to rail.”
T Harmis Jose
Project Director, Katni Grade Separator Project
Harmis and team have already completed 50% of the pile foundation works in Package 1 that is scheduled to be completed by end 2021 while in Package 2, the team has completed 60% of the pile foundations and aim to complete the task by October 2021. While work on the substructure is in progress at both packages, Harmis’s target is to complete the total civil works, excluding the deck slabs, for Package 1 by October 2022. “Half the value of the contract is structural steel works,” he mentions.
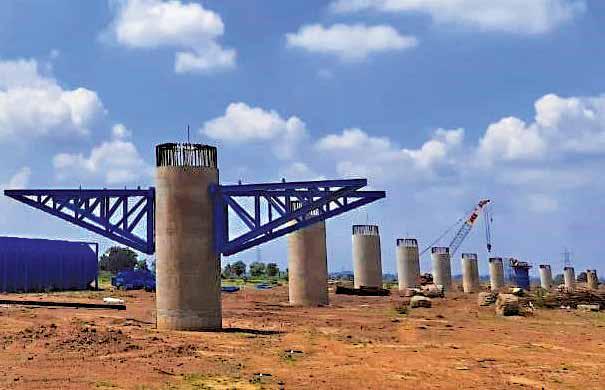
The fabrication of the workshop is in progress and the fabrication work will commence once the team receives the RDSO approval. “With our capacity of 2500T per month and starting from October 2021, we should complete the fabrication work by March 2023 and simultaneously, the erection by April 2023,” informs Soumendra Kishore Roy Choudhury, Lead Fabrication & Erection (for both packages).
“With our capacity of 2500T per month and starting from October 2021, we should complete the fabrication work by March 2023 and simultaneously, the erection by April 2023.”
Soumendra Kishore Roy Choudhury
Lead Fabrication & Erection, Katni Grade Separator Project
“What are construction projects without challenges?” laughs Head Project Planning (for both packages) – Shekhar Keskar. “We have our fair share in the form of existing & unknown and unidentified underground utilities, Signalling & Telecommunication cables, OFC cables, electrical cables and the like, insufficient supply of OPC 53 grade of cement and the required quality of aggregates due to the remoteness of the project location.” Then there is the challenge to negotiate congested and densely populated village roads and railways to move heavy equipment for piling as well as concrete work, the constant hazard of working next to a busy, running railway track, and working in islands between railway tracks to safely construct the rail over bridge spans.
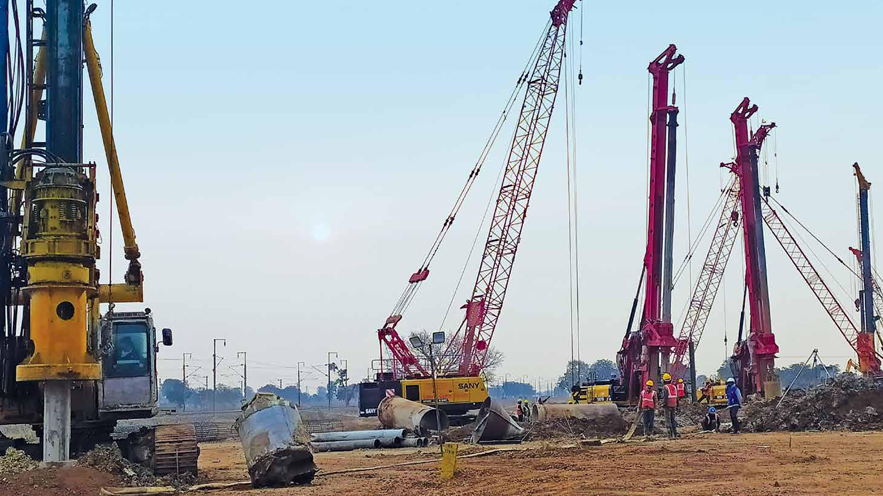
Men at work at Katni
The project team has adopted a wide array of digital solutions to drive efficiencies including IoT for weighbridge transactions, concrete production of the batching plants, GPS on a host of vehicles like transit mixers, mounted cranes, wheel loaders, etc. “39 generators and a BG 25 piling rig are connected through IoT,” mentions Shekhar. “In addition, we also use WISA, Digitance for attendance, IB4U and QIR (Quality Incident Reporting).”
With two very prestigious and massive projects to execute, Tsn and team has a lot on their plate and here is wishing them the very best to deliver handsomely!