MEGA HEAVY CIVIL PROJECTS MAKE PROGRESS DESPITE MEGA CHALLENGES
The Mumbai-Ahmedabad High Speed Rail project, popularly referred to as the Bullet Train project, has caught the imagination of the public not only in India but overseas as a true coming of age of India as a technology leader. While L&T is constructing 63% of the project, the mandate for Heavy Civil Infra IC is to build the 237.1 km long Package 4. “The stretch is so big that we have divided it into 5 sections each headed by a Project Director,” explains Task Force Leader, G Vinod, fresh from his stint as Project Director for the Mauritius Metro project. The beauty and relative calm of Mauritius is but a mere memory for him as he buckles down to meet the huge requirements of the HSR project.
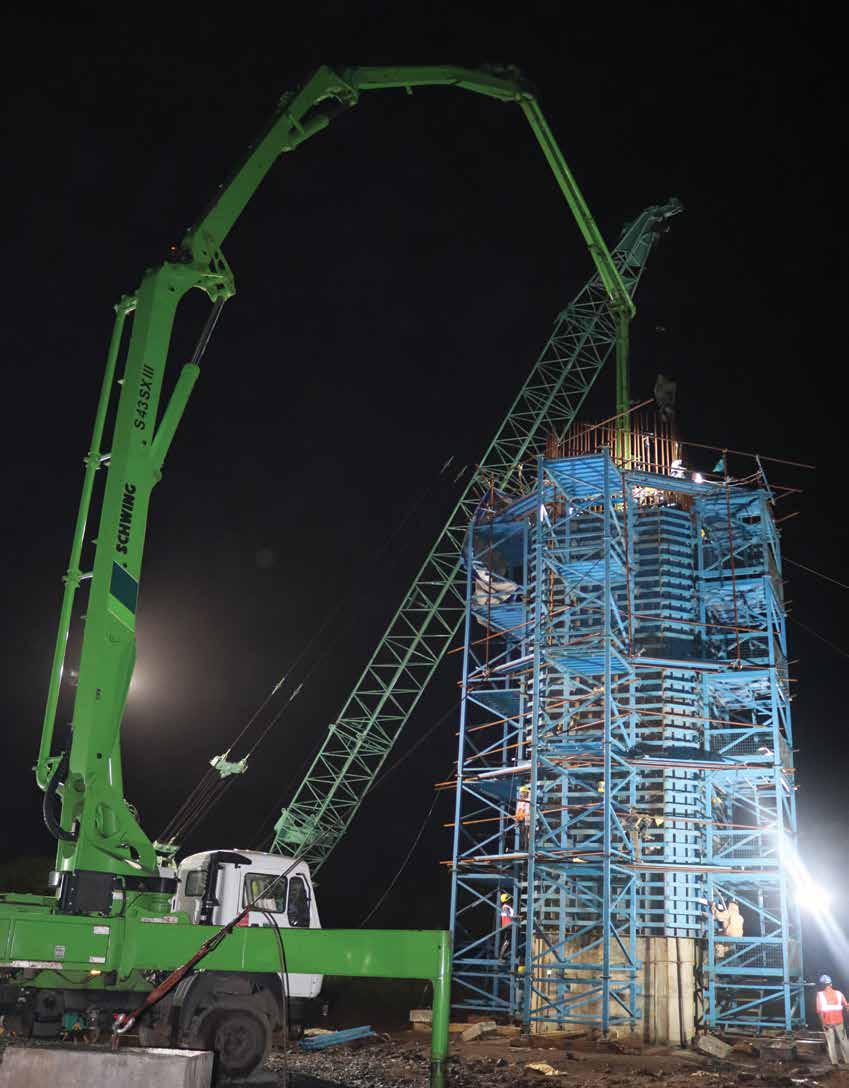
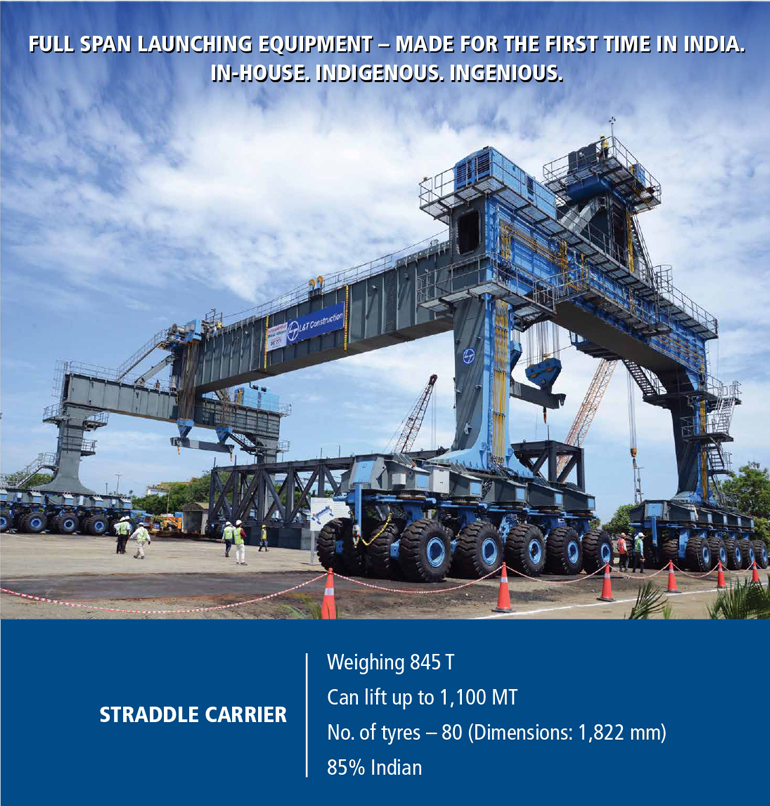
Size & scale of mammoth proportions
A few figures aptly capture the hugeness of the project. Logistically, about 200 cement bulkers are required to make totally some 1,000 trips every day to meet the timeline which is only possible if all the required material reach the different locations along the alignment in time. 85% of the stretch will be executed using the full span launching technique that involves sourcing the right equipment or building it in-house, making moulds, assembling the equipment and spans. The project will require a 17,000-strong labour force, including a large complement of skilled workmen, with the attendant challenges of providing decent habitats, making on time payments, and ensuring that they are retained in these uncertain times of the pandemic. The project requires about 720 acres of leased land in strategic locations to set up casting yards for which the team is almost completely dependent on the client, the National High Speed Rail Corporation Limited.
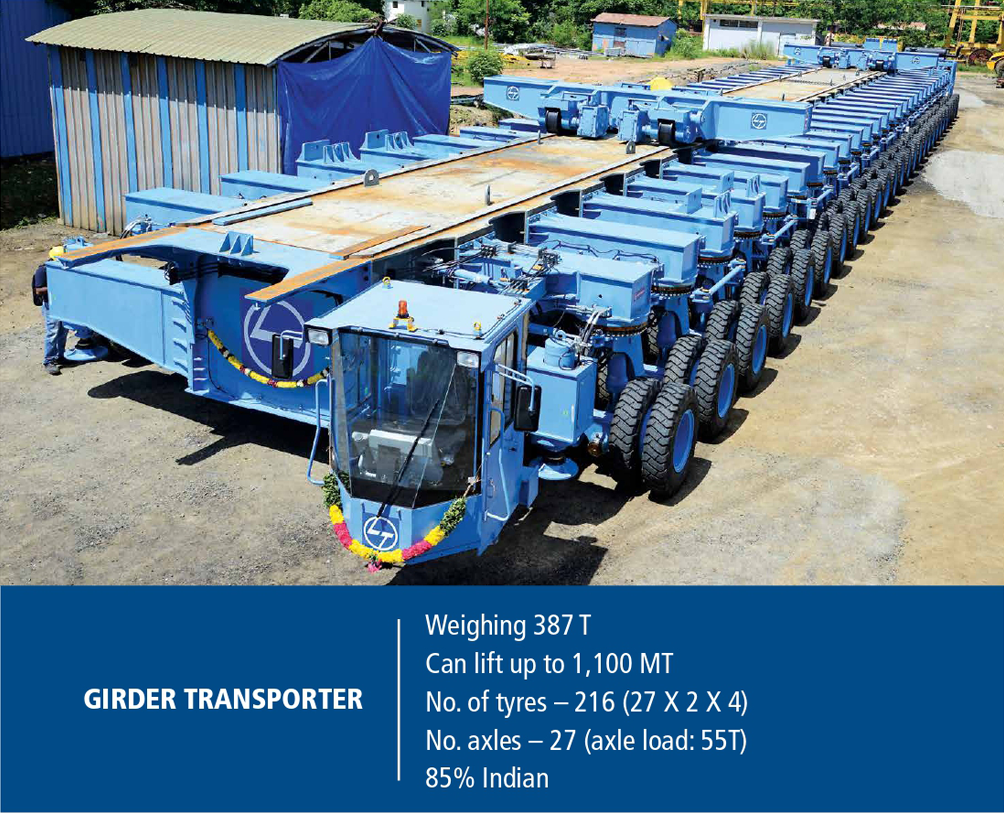
“In normal metro projects, we use smaller precast elements to build the viaduct but when you are talking about building a 237.1 km long viaduct, you have to think big and innovatively to work faster,” says Vinod. The project will thus be using full span launching equipment like high-capacity straddle carriers, girder transporters and launching girders. “The straddle carrier developed at our Kanchipuram manufacturing facility has the capacity to lift girders weighing up to 1,100 MT that is equal to the weight of 20 fully loaded coal BOX-N wagons and its size is almost twice that of a tennis court,” describes Vinod. These huge precast girders will be transported on girder transporters to site for erection. “This mammoth equipment has been entirely designed inhouse, with 85% locally sourced components and made in India for the first time.”
“In normal metro projects, we use smaller precast elements to build the viaduct but when you are talking about building a 237.1 km long viaduct, you have to think big and innovatively to work faster.”
G Vinod
Task Force Leader, Mumbai-Ahmedabad High Speed Rail project
While most of the work on the project presently is confined to design, engineering and geotechnical studies, the team has still achieved a few early milestones. The first full pier at Section 1 has been constructed, client offices at pre-decided locations along the route have been handed over, the state-ofthe-art geotechnical lab – Asia’s largest – is already up and testing and several AI, ML, mobile and web-based digital solutions are already connected and streaming data to drive efficiencies.
The task is huge; the asking rate even bigger and here is wishing the entire HSR team the very best to deliver handsomely.
THE STRADDLE CARRIER DEVELOPED AT OUR KANCHIPURAM
MANUFACTURING FACILITY HAS THE CAPACITY TO LIFT
GIRDERS WEIGHING UP TO 1,100 MT THAT IS EQUAL TO THE
WEIGHT OF 20 FULLY LOADED COAL BOX-N WAGONS AND ITS
SIZE IS ALMOST TWICE THAT OF A TENNIS COURT.
Mumbai Metro project makes significant headway underground
The first underground metro line termed as the ‘Aqua Line’ of the Mumbai Metro is 33.5 km long connecting Cuffe Parade to SEEPZ with 26 underground stations and one at-grade station. The civil contract for the tunnels and underground stations for this stretch has been divided into 7 packages by the Mumbai Metro Rail Corporation (MMRC) of which L&T, with JV partner, STEC, are executing two packages, UGC01 and UGC07.
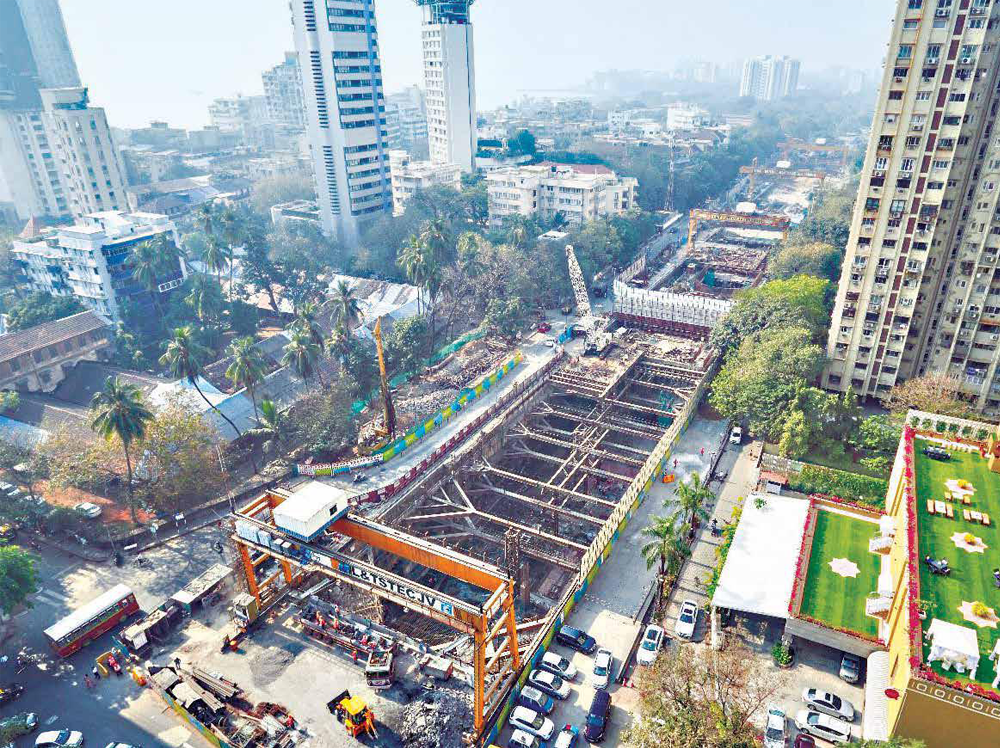
Station at Cuffe Parade
Apart from the challenges of working in one of the world’s most densely populated cities, the project team under the leadership of Project Directors, A K Dey and H Jayarama, have had to contend with the limitations induced by the pandemic, more so because Mumbai was, till recently, the most severely affected region in the country. With the requirement for medical oxygen suddenly skyrocketing, and the government issuing orders prohibiting the supply of oxygen for non-medical purposes, the project was hit by the lack of industrial oxygen. “This shortage could not have come at a worse time,” Jayarama shakes his head. “At UGC01 we were at a critical stake of retrieving the TBM and excavating for the entry and exit. So, we had to quickly modify our methodology to keep moving forward by resorting to the plasma cutting machine,” informs A K Dey. Night curfews cut into the hours of work available for the team resulting in further lower productivity.
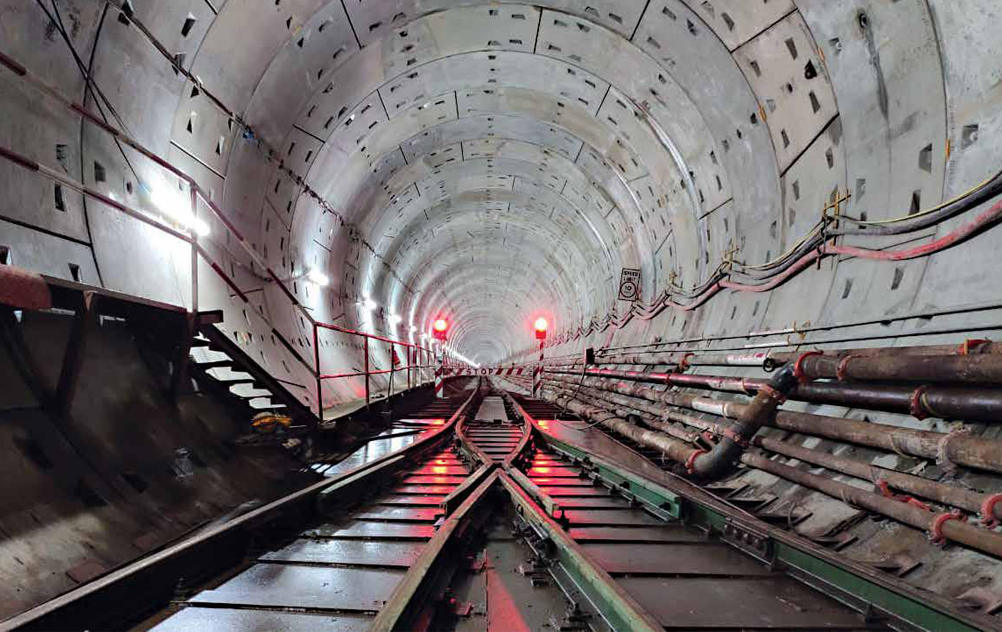
Mumbai metro tunnel
Labour was the other major problem that had to be tackled: first, with the exodus immediately post the lockdowns, then the difficult task of remobilizing since workmen were not ready to return to Mumbai. The COVID Response Team focused on testing, tracking, treating infections and driving vaccinations for both the staff and workmen. “Presently, 95% of our staff and 85% of the labour and RSW workmen have taken the jab,” informs Admin & IR Manager, L C Tripathi.
From engineering and construction perspectives, “Our challenges are largely threefold,” says A H Khan (AHK), Vice President & Head Operations (Mumbai). “The first has been Mumbai’s unpredictable geology, the difficulty of logistics in a cramped and congested environment and, last but certainly not the least, managing the underground utilities.”
“Our challenges are largely threefold. The first has been Mumbai’s unpredictable geology, the difficulty of logistics in a cramped and congested environment and, last but certainly not the least, managing the underground utilities.”
A H Khan
Vice President & Head Operations, Mumbai Metro Project
“Ours is not so much a design-and-build project but rather a ‘design as you build’ project,” remarks Nilesh Jain, Head- Stations, referring to the customized formwork systems developed and deployed by his team including A -Frames L- Frames, perhaps for the first time at L&T. To erect the Over Track Exhaust (OTE) Duct at each station, they have fabricated and assembled tackle & trolley systems to replace the standard separate scissor lifts that has saved the project hugely on costs.
“At the Hutatma Chowk station, the benching of the NATM (New Austrian Tunnelling Method) Platform Tunnel was carried out using a TBM that required fine control on the operational parameters of the TBM as only 25% of cutter head was excavating the rock mass,” shares Project Manager, Palwinder Singh. “We relaunched the TBM without using the reaction frame by taking reaction from half segments erected during the benching of the NATM Platform Tunnel. This innovative way of benching the NATM Platform Tunnel having basalt rock mass using a TBM and relaunching the TBM in hard rock has been accomplished for the first time in India,” he exults.
“We relaunched the TBM without using the reaction frame by taking reaction from half segments erected during the benching of the NATM Platform Tunnel. This innovative way of benching the NATM Platform Tunnel having basalt rock mass using a TBM and relaunching the TBM in hard rock has been accomplished for the first time in India.”
Palwinder Singh
Project Manager, Mumbai Metro Project
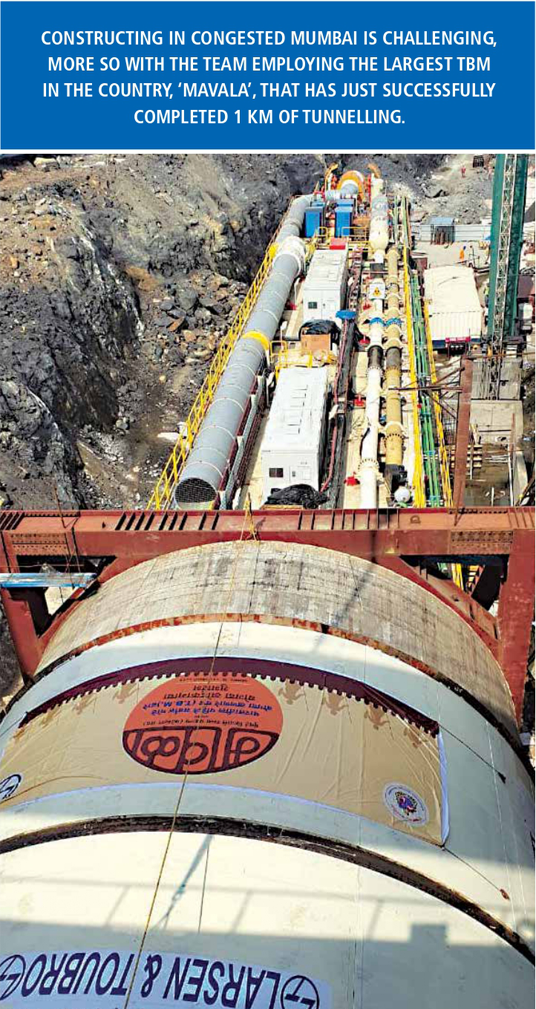
Mavala TBM in use at the Mumbai Coastal Road Project
Despite the several challenges, AHK is happy with the progress both packages have made thus far. “In UGC01, we have completed 100% of the tunnel boring and have successfully retrieved the TBM, while for the stations, we have completed 99% of station box structure, 95% of piling and 40% of excavation for entry and exit. In UGC07, we have completed the NATM excavation, station box, and pling works for entry and exits while we are almost done with the excavation for the entry and exits.” MEP and architectural works are presently under progress across both packages.
Mumbai Coastal Road Project –a potential game-changer
It has the potential to reduce a 2-hour city commute from north to south Mumbai to just 20 minutes; it can reduce fuel consumption by a whopping 34% valued at approximately US $ 100 million annually; it will dramatically change the way the city of Mumbai commutes. It is the Mumbai Coastal Road Project, a 29.8 km long freeway that will run along Mumbai’s western coastline connecting the Princess Street Flyover in South Bombay to Kandivali in the northern suburbs. Divided into two phases of 10.58 km and 19.22 km respectively, and scheduled to be completed by July 2023, the project at present has completed totally about 36% of the work against a target of 40%.
Describing the nature of Packages 1 & 4 that L&T is constructing, AHK says, “We are constructing a sea bridge of 1.5 km, a 1.5 km sea wall and with all the interchanges it will be around 9 kms.” Constructing in congested Mumbai is challenging, more so with the team employing the largest TBM in the country, ‘Mavala’, that has just successfully completed 1 Km of tunnelling. Working close to the sea has been a challenge and several times work has had to stopped to pump out the water that rushed in. “We have opted for the slurry type TBM to suit Mumbai’s heterogenous geological profile,” remarks AHK. “It is complex engineering, requiring technical expertise and the right people to operate.” He mentions the use of mono-piles instead of groups of piles that has speeded construction and improved aesthetics. Once completed, the project will boast off India’s first sea road tunnel.
A civil engineer’s dream project involving roads, bridges, tunnels, reclamation, highways, crossovers, underpasses, sea walls, the task before Rakesh Singh Sisodia, Project Director – Package 1 and Sandeep Singh, Project Manager, Package 4 is to keep things rolling to deliver on time to quality.
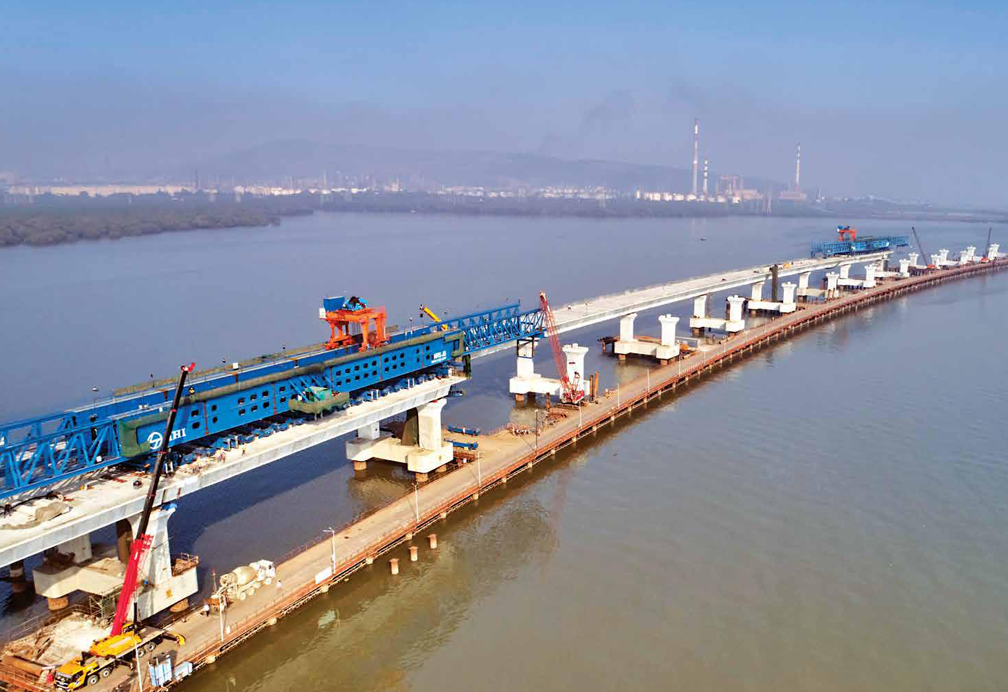
Mumbai Trans Harbour Link
Work on India’s longest sea bridge proceeds
Deputy Project Director, Sanjay Digambar Patil’s face has a slight smile as he triumphantly declares that his Mumbai Trans Harbour Link project has cumulatively made 43% of physical progress, 30% of which during the height of the pandemic. “We have completed the marine piling scope and a substantial portion of the foundation works for the main bridge, erected seven launching girders and commissioned six of them out of a total of eight,” he updates. The team has completed 4.6 km of the permanent bridge that constitutes to about 17% of the work, the mobilization of the Orthotropic Steel Deck (OSD), the largest in India and the size of a football field and the assembly of five of its spans have commenced.
Sanjay and his team are aggressively pushing ahead come pandemic or high water – the Cyclone Tauktae.