MMH PROJECTS CONTINUE TO SURGE AHEAD FUELLED BY THE POWER OF DIGITALIZATION
MMH SBG’s Utkal Alumina International Limited (UAIL) project at Kucheipadar, near Tikiri in Odisha’s Rayagada district, some 200 km from Visakhapatnam and 75 km from the main town in the district, has several inherent challenges like remoteness due to which sourcing material, spares, manpower, skilled labour are all huge issues. Severe and prolonged monsoons are another headache and with COVID-19 adding to the mix in early 2020, Project Manager, Prasanta Tikadar must have wondered what more would he and his team have to face. Yet, he puts up a resolute and cheerful front. “We have made significant progress since the lockdowns,” he says, reeling off the several milestones the team has achieved. They have erected 850 MT critical / heavy equipment, 1,380 MT of structure, 14 tank top structures, completed 4,500 cum of concreting, electrical panels & transformers, and integrated trials in the PDS, PPT and digestion areas.
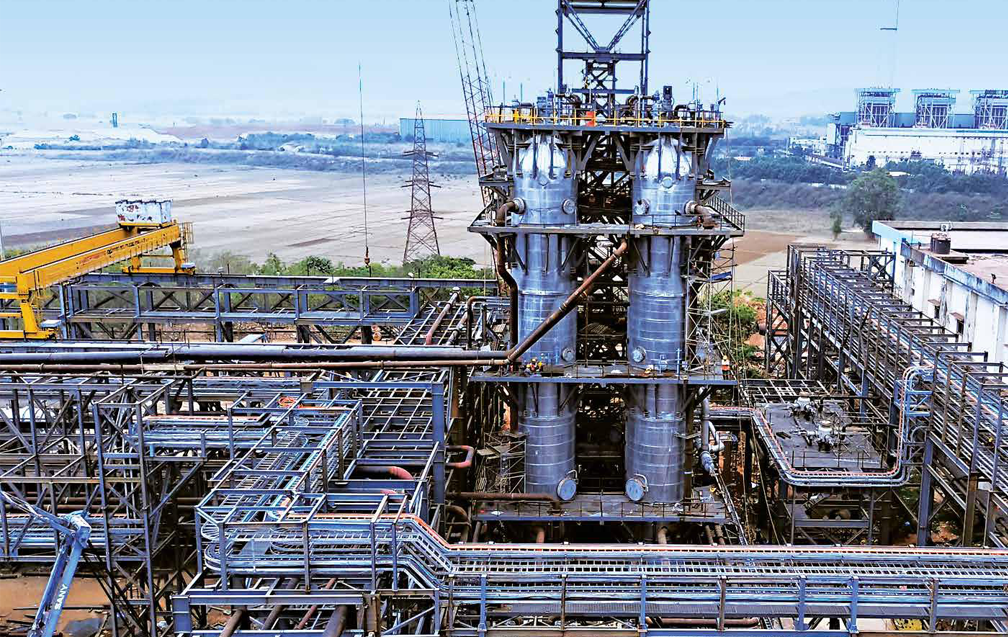
“Though about 1,500 workmen were retained during the lockdown, most of them fled the site when the restrictions were lifted, so progress depended a lot on implementing automation, mechanization and digitalization solutions.”
Prasanta Tikadar
Project Manager, Utkal Alumina International Limited (UAIL) Project, Kucheipadar
Automation, mechanization & digitalization winning the day
“Though about 1,500 workmen were retained during the lockdown, most of them fled the site when the restrictions were lifted, so progress depended a lot on implementing automation, mechanization and digitalization solutions,” informs Prasanta. The 3D modelling software of Navisworks has fast-tracked unit piping by managing interfaces and easily identifying lines with specifications and processes. “By adopting modular erection specially for heavy & critical structural lifts like tank top structures at heights of 35 m and conveyors, we made big savings in labour, time, improved quality and safety,” enthuses Planning Manager, Sudip Sen. Their discipline in stacking fabricated structural materials like pipes of various diameters, pipe fittings, cable drums and the like has reduced workmen engagement and quickened progress.
“By adopting modular erection specially for heavy & critical structural lifts like tank top structures at heights of 35 m and conveyors, we made big savings in labour, time, improved quality and safety.”
Sudip Sen
Planning Manager,
Utkal Alumina International Limited (UAIL) Project, Kucheipadar
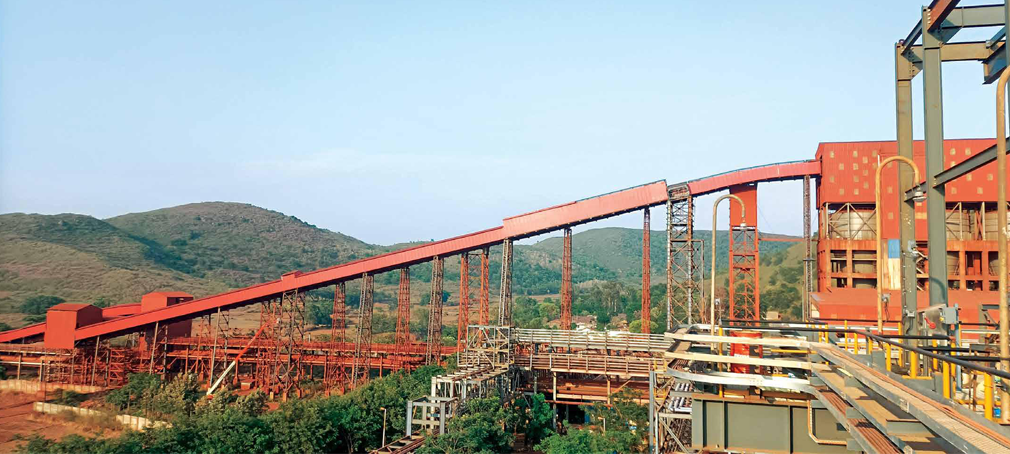
Bauxite handling area – Conveyor 6B
Area wise and line wise colour-coded pipes & spools have improved the team’s logistic planning, orbit pipe cutting & welding machines for pipes of larger diameter have reduced time for pipe fabrication, automatic plastering machines have reduced the requirement of masonry groups and space climbers for mechanical work inside tanks have speeded up progress.
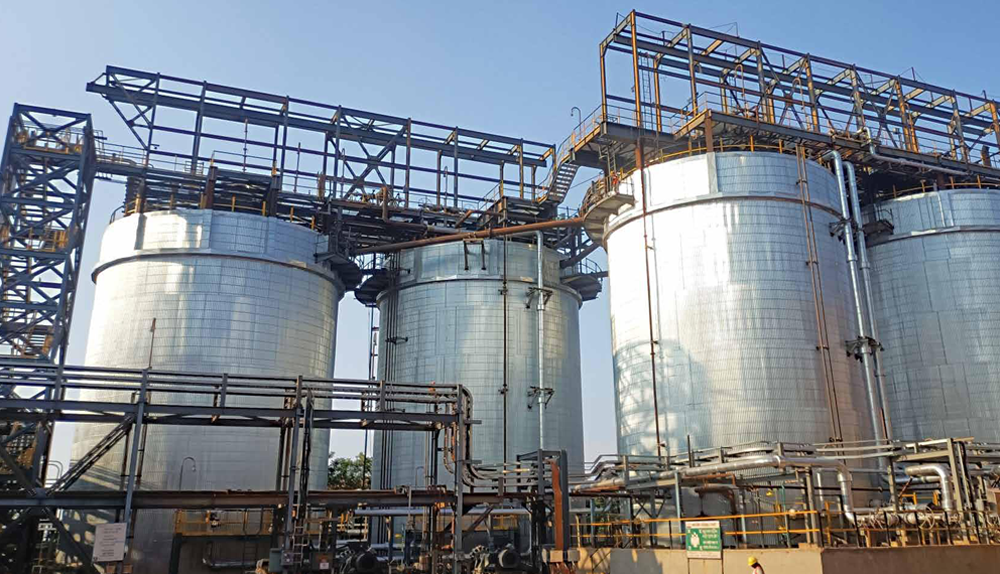
PDS tank insulation
At the JSW project in Dolvi, Maharashtra, where MMH SBG is executing India’s biggest blast furnace, largest steel melt shop and tallest coke oven battery to double the capacity of the facilities from 5MTPA to 10MTPA, Project Manager – CDQ Project, R Sivanesan has a similar story to share. “Adopting digitalization at an early stage has proved to be a strategically sound decision for we are reaping its benefits when most needed,” he smiles. “Thanks to WISA, workmen details are available at the click of a button for quick remobilization and were it not for ‘QR Codes’, material retrieval would have been a nightmare given the acute shortage of the storage space available at the project. Chatbots & Asset Insights are helping us track project progress and the productivity of our P&M assets.”
“Adopting digitalization at an early stage has proved to be a strategically sound decision for we are reaping its benefits when most needed.”
R Sivanesan
Project Manager, CDQ Project
T S Muraleedharan (Project Manager, SMS#2 project) adds, “As soon as we faced the workmen crisis after the 2nd wave and prescient about having to extend into the monsoon season, we rationalized our resources to make our project sites monsoon-ready. We prioritized civil works & roof works so that when we remobilized the workmen in sufficient numbers, we had fronts ready inside the plants to deploy them to avoid idling of the manpower and P&M resources. Strategy and timely action have paid dividends,” he emphasizes.
“We prioritized civil works & roof works so that when we remobilized the workmen in sufficient numbers, we had fronts ready inside the plants to deploy them to avoid idling of the manpower and P&M resources. Strategy and timely action have paid dividends.”
T S Muraleedharan
Project Manager, SMS#2 Project
Having a mandate to execute 1,78,000 cum of concreting, 24,000 MT of structural and 15,000 MT of equipment, Project Manager, Sanjay Saha at the Lanjigarh site where MMH is constructing and erecting a 3MTPA aluminium refinery, is facing a tall order but again digital solutions for planning, safety and quality are going a long way to improve his efficiencies. “We have rolled out the Wrench smart project management tool with Chatbot for progress monitoring, Primavera for project scheduling & tracking and the Conquer app for reporting and tracking quality related observations to ensure timely compliance.” By recording their activities, EHS managers are addressing unsafe acts through the SOSC app. Other forms of mechanization adopted to modernise its operational capability include the use of PAUT (Phased Array Ultrasonic Testing) using robotic crawlers and rope suspended platforms, telehandlers, and scissor-lifts, that have ushered in improved efficiency of time and greater accuracy.
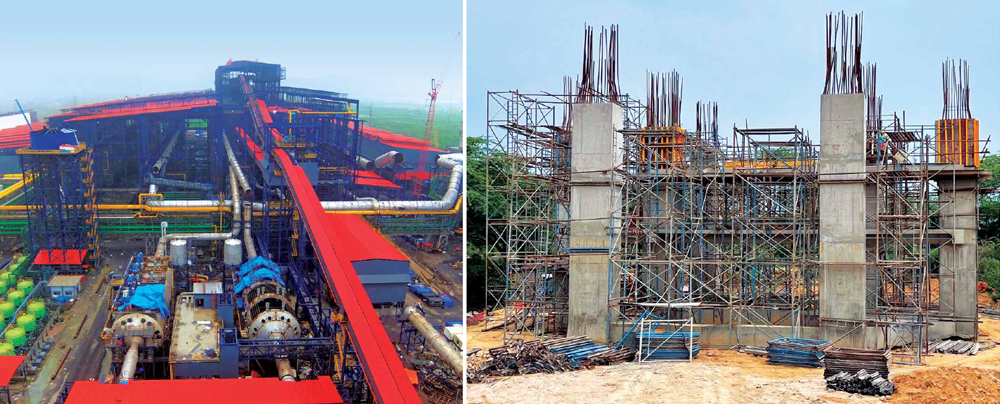
Dolvi Steel Melt Shop#2 site
Rapid Loading System for Despatch of Coal through Railway Wagons, Dudhichua
At the Northern Coal Fields, Dudhichua Coal Handling Project, a breakthrough package for MMH bagged in 2019-2020, Project Manager, Matta Satyanarayan, says, “Strategy, innovation and timeliness are the keys to success and to succeed in such a competitive environment. We have implemented several digital solutions like BIM for 3D Modelling, Primavera for project scheduling & tracking and ChatBot to regularly report progress to drive efficient progress.” In addition, the team has adopted modular rebar cages, precast civil elements, folding shuttering and the like that are ensuring proper reporting, improving productivity, minimizing mistakes, for timely delivery.
“Strategy, innovation and timeliness are the keys to success and to succeed in such a competitive environment. We have implemented several digital solutions like BIM for 3D Modelling, Primavera for project scheduling & tracking and ChatBot to regularly report progress to drive efficient progress.”
Matta Satyanarayan
Project Manager, Dudhichua Coal Handling Project
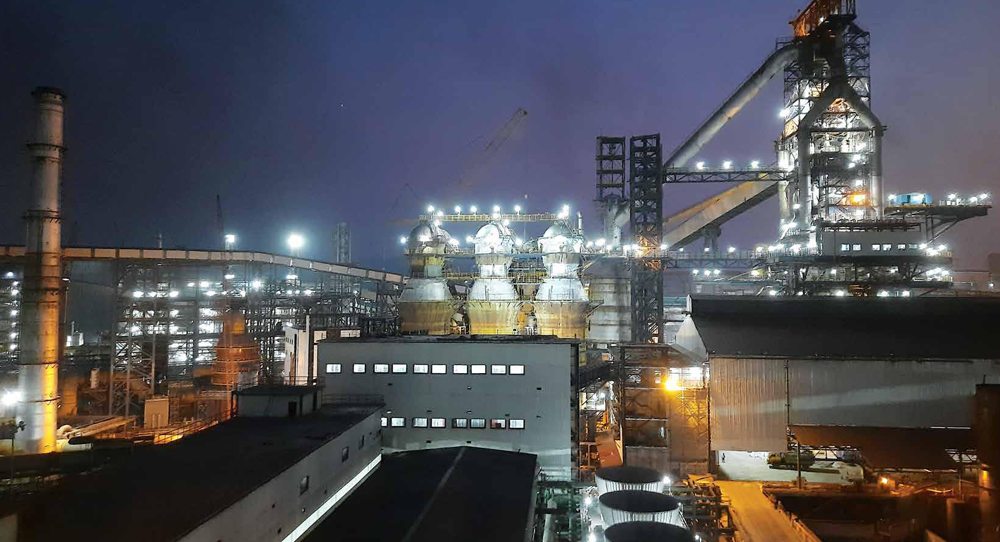
Dolvi blast furnace
Enduring labour pains
Labour has been one of the two biggest disruptions for the construction industry due to the pandemic other than supply chain issues, yet project teams, in true L&T style, have taken these problems in their stride, evolving strategies and methodologies to push forward. Reverse migration reduced labour force strength from 8,000 levels to less than half by May 2021 at the JSW, Dolvi site necessitating quick action from Project Manager – Civil Works, A K Ray. “The goodwill we maintained with our subcontractors by promptly processing their bills and addressing their grievances empathetically was a huge advantage for they were willing to mobilize manpower even in very trying circumstances.” The site office then geared up to handle this influx.
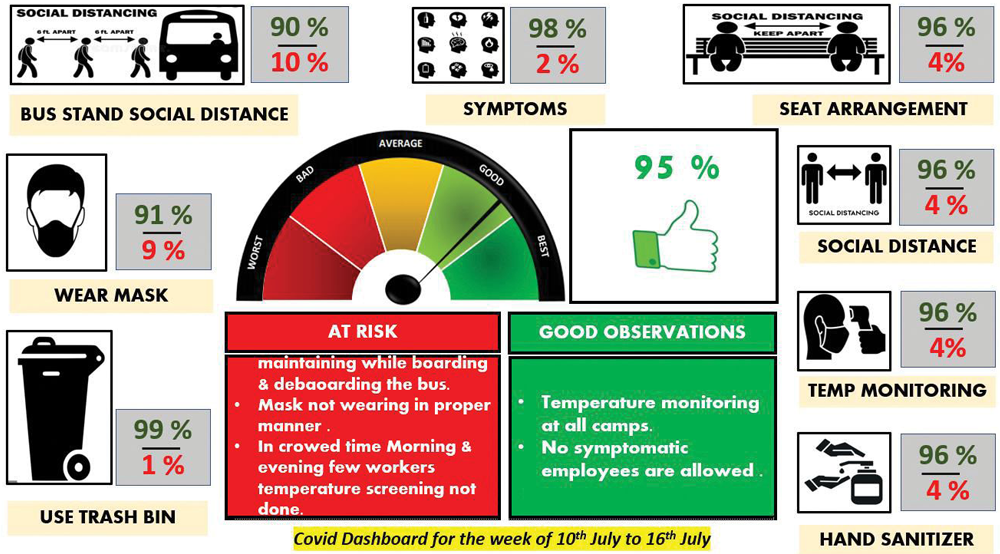
Weekly COVID watcher dashboard
“Staff crunch was a major issue as more than 40% of our staff fell ill at some of our sites and the remaining ‘fit’ staff had to take up the slack going beyond their normal job routines,” recalls A Dhanasekar (Project Manager, BF#2 project). “The strength of our organization lies in our resilience, perseverance and commitment to perform and deliver because of which we successfully mobilized more than 2000 workmen in 2 months, sufficient to complete the finishing activities of our project.”
“We conducted daily ‘War Room’ meetings, regular virtual meetings with the top management of the client, consultant, medical and project to review matters with continuous and regular monitoring of systems as a proactive preventive measure.”
Hare Ram
Project Director, Maa’den, Saudi Arabia
While Accounts & Admin Head, Pradeep Kumar Das at the Lanjigarh project site took several steps to ensure the safety of the labour force by insisting on negative RT-PCR tests before reporting to site, compulsory 7-day quarantines for those coming from outside and getting 95% of the workmen vaccinated, at the Maa’den site in Saudi Arabia, Project Director, Hare Ram adopted a ‘right decision at the right time’ approach to mitigate risks. “We conducted daily ‘War Room’ meetings, regular virtual meetings with the top management of the client, consultant, medical and project to review matters with continuous and regular monitoring of systems as a proactive preventive measure.” Daily COVID and weekly COVID Watcher dashboards, the latter a part of the site’s ‘COVID Watcher’ initiative, kept all at site updated and on the same page in their concerted war against the pandemic.
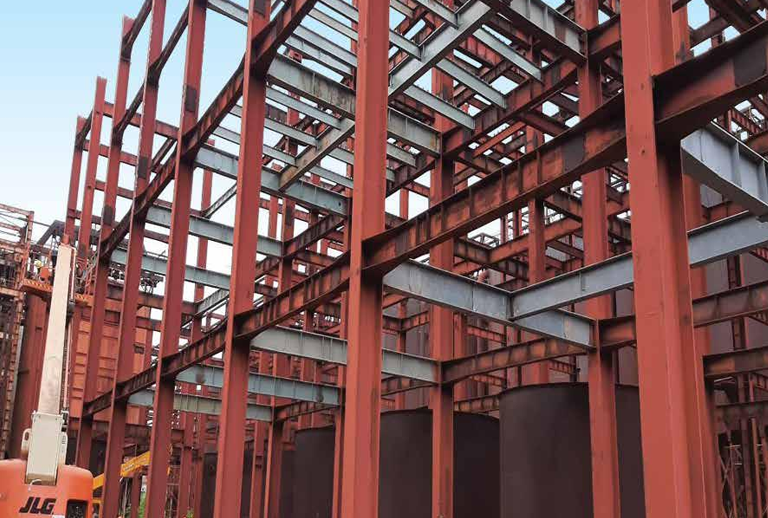
Security filtration
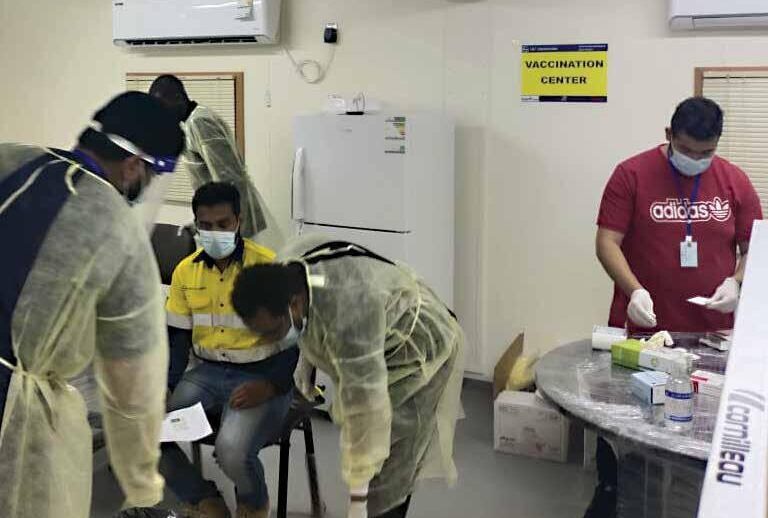
Mass vaccination
Overcoming a variety of other challenges to drive progress
MMH’s coal mining project for NTPC Limited at Kerandari is one fraught with steep challenges but Project Manager, Paramhans Singh has already achieved 2,400 cum of concreting out of a total scope of 28,500 cum, and still has 13,586 MT and 4,780 MT of structural and equipment erection to go. “We have been struggling with the non-availability of fronts and are constantly liaising with the customer and the local administration to explore possibilities of encumbrance free land to commence construction activities in the balance areas.” This assumes greater relevance as 65% of the pipe conveyor corridor runs through government forests. The overall terrain is largely rough and hilly with an extreme elevation difference of 110 m, and restricted operating space is making movement of men, material & resources extremely difficult. “This is a Naxal area too so the sooner we complete the project the better it is,” shares a worried Project Schedular, Santosh Anand.
“Our site has two outstanding features,” points out Site In-charge – Civil, Rajendra Kumar. “One, is that we are constructing some of the largest pipe conveyors comprising two stage crushing systems along with 9.4 km dual stream pipe conveyors each of 2,500 TPH rated capacity. The other is the 490 trestles along the pipe conveyor corridor, with a maximum base width of around 6 x 2.5 m, maximum height and span of 30 m and 24 m respectively.”
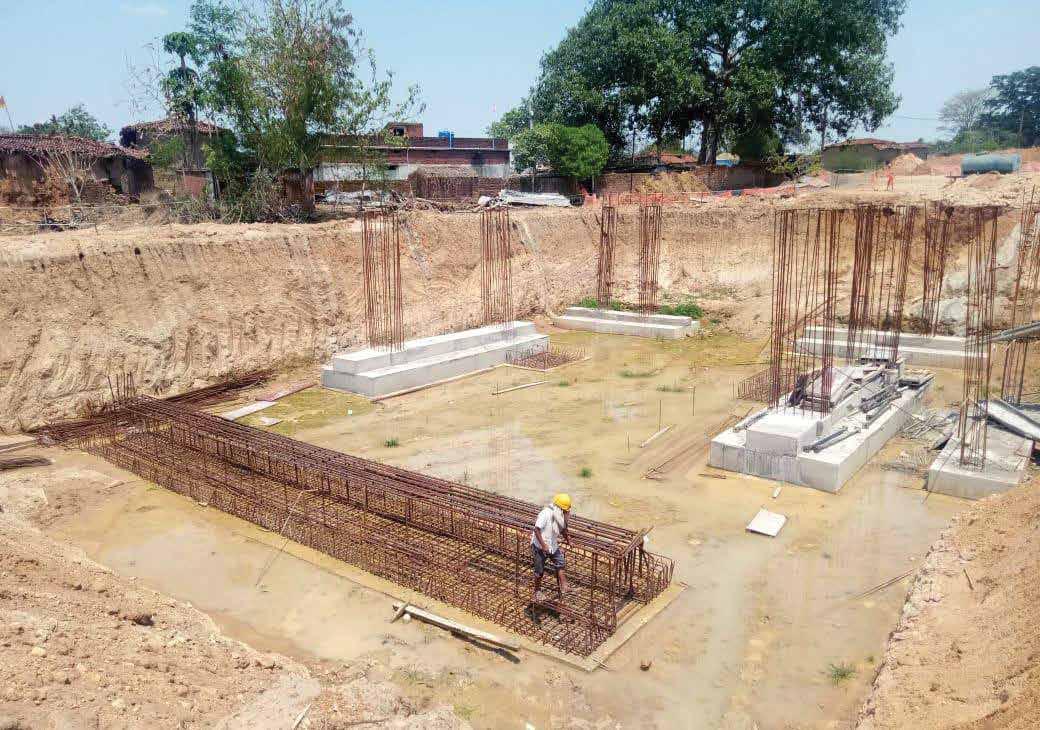
Surge hopper building at Kerandari
The UAIL project team encountered very hard rock that could not be dismantled with the conventional rock breaking methods and since chemical blasting was not allowed, they had to resort to the diamond cutting method. “We executed 23,600 cum against a contractual BOQ quantity of 3,000 cum which has thrown our scheduling right out of gear,” laments Planning Manager, Sudip. “Even our structural quantity has increased by 50% and these huge changes in scope quantities are resulting in increased execution time, more deployment of erection cranes and other material handling equipment leading to cost overruns.” The team also frequently faces disruptions in work due to interference from the local villagers.
Supply chain disruptions haunt all project sites as at the Lanjigarh site where its location and poor connectivity are hindering delivery of several key consignments.
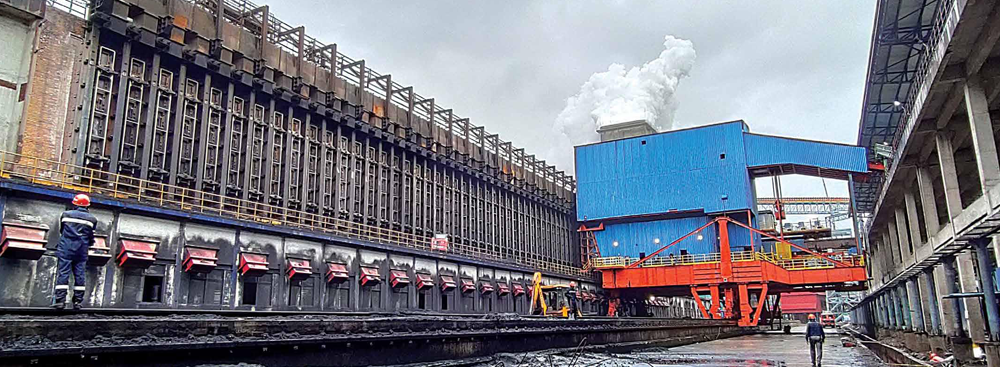
Dolvi coke oven battery
“To streamline the supply chain processes, orders from multiple vendors of a given location are being grouped together to reduce delivery lead time and to take advantage of economies of scale,” explains Planning Manager, K Durgamadhaba Patro. “We maintain a catalogue of vendors of different specialisations operating at major locations to ensure better coordination and smoother supply.”
“To address the situation, a tripartite arrangement between JSW, the oxygen bottling plants, and L&T stipulated that the liquid oxygen would be supplied by JSW directly to oxygen bottling plants who in turn would supply adequate oxygen cylinders to L&T as per site requirements.”
Surendra Singh
Project Manager, COB Project
With industrial oxygen being diverted for medical purposes, the shortage of oxygen cylinders threatened to derail progress at the JSW, Dolvi site. “To address the situation, a tripartite arrangement between JSW, the oxygen bottling plants, and L&T stipulated that the liquid oxygen would be supplied by JSW directly to oxygen bottling plants who in turn would supply adequate oxygen cylinders to L&T as per site requirements,” explains Surendra Singh (Project Manager, COB Project). To remove the bottlenecks in supply chain logistics, cylinders were transported partly on the vehicles of vendors and partly on L&T vehicles. “Although site progress suffered for few days due to the nonavailability of oxygen cylinders, our innovative approach to the problem and good relationship with the customer came to our rescue,” sums up Surendra.
Challenges and uncertainty are part and parcel of construction though MMH sites have been facing more than their fair share during these tough and unprecedented times. By adopting an ‘expect the unexpected’ approach, thinking and acting innovatively, projects are driving progress and we wish them all the very best to continue doing so.