MMH PROJECTS PROGRESS FUELLED BY DIGITALIZATION
The Mansourah Massarah Gold Project (MMGP) is one of MMH SBG’s iconic projects currently being executed in the Kingdom of Saudi Arabia involving engineering, procurement, construction, pre-commissioning, commissioning, and start-up of what will be the largest ever gold project producing an average of 250,000 ounces of gold per year over its lifetime. The good news is that the project is being executed in an entirely 3D environment with the intelligent P&ID’s prepared by Aveva Diagram, linked with multiple other deliverables like equipment lists, pipeline lists, valve lists, isometric diagrams, and a 3D model for the entire plant.
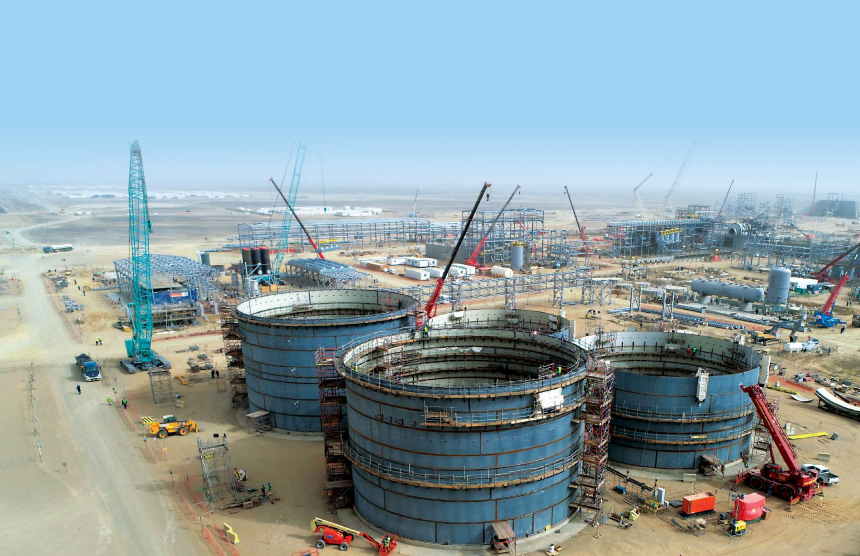
3D modelling is taking execution to a new level
“Visualization with 3D models improves communication between stakeholders,” shares Project Director, Hare Ram. “2D drawings, including fabrication drawings, are being generated directly from 3D models reducing man-hours, enhancing accuracy and quality.” There are manifold benefits for Hare Ram and his team from 3D modelling: it helps to arrive at complex solutions, enables visual communication, constructability, clash detection to reduce rework in both the engineering and construction phases, and unique work planning with maximum safety. “We have divided the project’s 3D model into 8 zones that reflect the actual working site so that individual zone in-charges are using their particular zones to plan construction through the cloud,” explains Hare Ram.
“Visualization with 3D models improves communication between stakeholders. 2D drawings, including fabrication drawings, are being generated directly from 3D models reducing man-hours, enhancing accuracy and quality.”
Hare Ram
Project Director, Mansourah Massarah Gold Project
Equipment lists, developed in Aveva Engineering, are simultaneously updated based on the changes in the process during engineering while the project’s entire piping has been modelled in Aveva E3D from which isometrics have been prepared that have enhanced productivity and improved quality. Engineering Lead for the Maaden Gold Project, Nirmalya Burman, elaborates “All the structures and foundations are modelled in Tekla and imported into the Aveva E3D platform to reflect the actual plant configurations to check for possible clashes between the structures, piping, cabling etc. in real time to eliminate interferences during the modelling itself resulting in no or minimal rework at site.” In addition, all structural manufacturing drawings are prepared from Tekla models resulting in higher productivity and error-free detailed manufacturing drawings.
“All the structures and foundations are modelled in Tekla and imported into the Aveva E3D platform to reflect the actual plant configurations to check for possible clashes between the structures, piping, cabling etc. in real time to eliminate interferences during the modelling itself resulting in no or minimal rework at site.”
Nirmalya Burman
Engineering Lead, Maaden Gold Project
Etihad Rail project rides on digitalization too
The Etihad Rail project is a proposed railway network, linking freight facilities and passenger stations to form a part of the planned Gulf Cooperation Council (GCC) railway network. MMH’s scope of works includes detailed design, procurement, construction, testing and commissioning of all elements of freight facilities at 5 locations. “Our project has interfaces with four packages other than L&T’s 2F2 package,” informs Senior Project Director, Ranjan Roy, “and we are storing our 3D models in ProjectWise cloud along with vendors of other packages to check for clashes without any physical intervention and avoid clashes with internal or external parties during construction.” 3D models for the five stations are available that can be accessed using different devices.
“Our project has interfaces with four packages other than L&T’s 2F2 package and we are storing our 3D models in ProjectWise cloud along with vendors of other packages to check for clashes without any physical intervention and avoid clashes with internal or external parties during construction.”
Ranjan Roy
Senior Project Director, Etihad Rail Project
In both the Etihad Rail and Ma’aden Gold projects, 3D models are Digital Twins with respect to construction. The Digital Twin is a representation of the physical object in terms of data and information; an organized collection of design data developed from the detailed engineering 3D model along with final vendor data which the client can access by clicking on a particular object on the 3D model for all relevant documentations like P&ID, GA Drawings, Data Sheets, O&M Manuals, and the like. The entire actual engineering, asset and construction details are incorporated in 3D models which will be useful digital information for the Client to operate and maintain the plants in future.
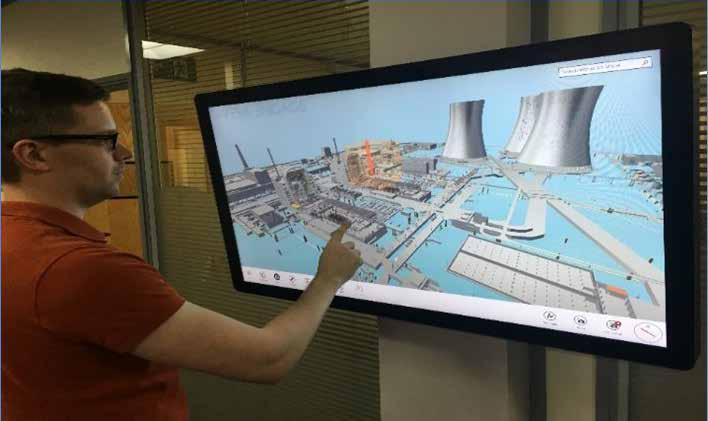
Digital Twin – an organized collection of data
4D BIM and Common Data Environment
At both these projects, since data is processed in a 4D model (3D model + Project Schedule) and available on the cloud, it is visible to multiple stakeholders saving time, cost, and effort. All the information is from a single source that addresses all communication issues, it is easier to monitor interfacing with 4D models, enables logistics & site utilization planning and real time risk & impact analysis. “4D BIM improves construction planning and management to help us understand project milestones better,” says BIM Manager, Antara Roy. “It enhances competency, safety and site space utilization, we can monitor actual vs planned in real time and actual vs look ahead for future project progress planning.” With the pandemic disrupting scheduled project deliveries, the MMGP team appropriately reconciled the actual vs planned and actual vs look ahead project schedule with the 4D model that threw up the missing activities. Apart from proper construction sequencing, the complexity of the structure can be visualized, and resources planned accordingly.
“4D BIM improves construction planning and management to help us understand project milestones better. It enhances competency, safety and site space utilization, we can monitor actual vs planned in real time and planned vs look ahead project progress.”
Antara Roy
BIM Manager
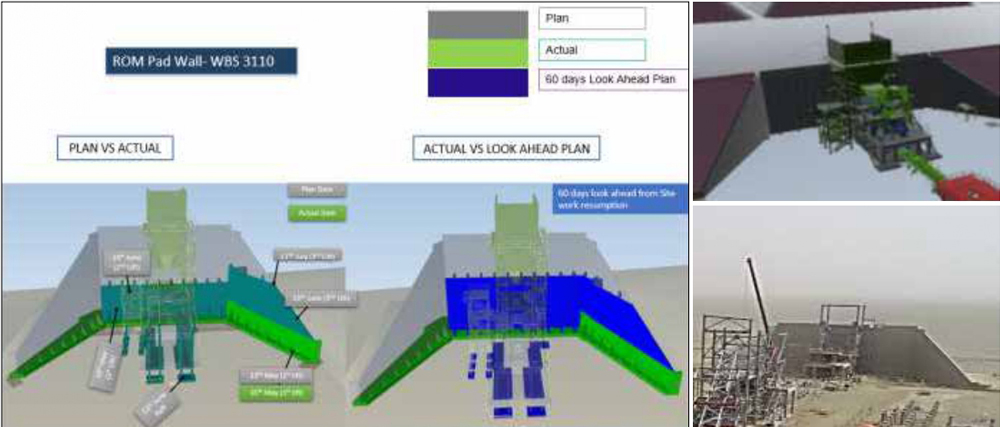
4D Model Plan Vs Actual comparison
The benefits of digitalization
“By using the 3D platform in complex EPC projects across the entire value chain of design, manufacturing, material management and site construction and integrating them with scheduling has helped us create a robust 4D project platform,” says Amit Swarnkar, Head – MENA BU. “We have witnessed this platform bringing enormous control to interdisciplinary interface management, construction planning, risk management with utmost ease and visually impactful understanding of the project. In the EPC project business space, it is not any more a desire but a necessity to stay ahead in the global race.”
“By using the 3D platform in complex EPC projects across the entire value chain of design, manufacturing, material management and site construction and integrating them with scheduling has helped us create a robust 4D project platform. In the EPC project business space, it is not any more a desire but a necessity to stay ahead in the global race.”
Amit Swarnkar
Head – MENA BU
As many as 3,776 hard clashes were discovered at MMGP that were all resolved prior to construction. 3D models open easy avenues of communication between the various stakeholders, enable process and engineering specification reviews with the client on a single platform that keeps the client updated on progress.
“BIM has led to enhanced collaboration and coordination among the stakeholders,” says Ranjit Ghosh, Head – EDRC, MMH SBG. “This is primarily the reason why our engineering deliverables have been error free and on time for the Maaden Project.” Real time project monitoring, analysis of delay and critical paths, construction review meetings and virtual walkthroughs with VR are all possible.
“BIM has led to enhanced collaboration and coordination among the stakeholders. This is primarily the reason why our engineering deliverables have been error free and on time for the Maaden Project.”
Ranjit Ghosh
Head – EDRC, MMH SBG
3D scanning hastens progress
For the brownfield Birla Copper project at Dahej that involves structural upgradation, the team did not have As-Built drawings of the existing plant. 3D scanning came to their rescue with which the As-Built drawings were extracted. “The conventional method of making 2D drawings would have taken a lot of time, that could have been inaccurate and not representing the entire project,” observes Project Manager, Sumit Kumar Jena.
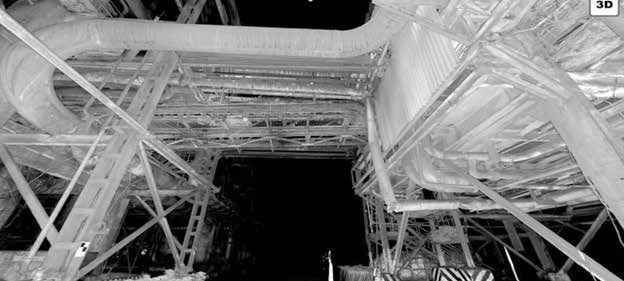
Point Cloud Modelling & Model Output
Areas across the project were identified where the 3D scanning equipment was placed and point cloud data generated. The point cloud data of multiple scans were then stitched together using the FARO Scene Software, rescanning any insufficient or incomplete data. The point cloud data was then uploaded to a server in the office. “Post this, plant wise 3D models were generated with EDRC helping us to extract and deliver the required 2D drawings,” says Sumit. “The entire operation was completed in just 7 months from initial scan to structural 2D drawings that entailed some 6900 scans across 7 plants.”
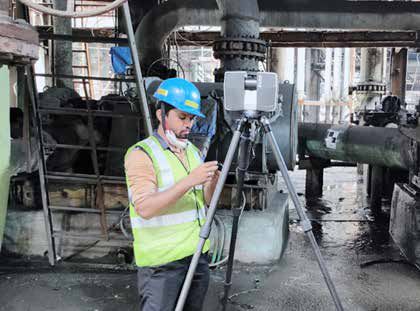
Scanning and Modelling
Geospatial technologies drive efficiency
The greenfield project Coal Handling Plant at Dudichua has a unique topology with a geographically dispersed area and natural obstructions along the way which would have made conventional surveying extremely time-consuming and arduous. “Instead, we used drone based topographic survey with DGNSS (Differential Global Navigation Satellite System) that was so much faster and more efficient,” enthuses Project Manager, Matta Satyanarayan. “The presence of hills, forests, rivers, etc. did not pose a problem for drones and with the reports generated, we could accurately identify the elevation, excavation areas, land levelling etc.” The entire scanning operation was conducted, and the contour survey generated in 4 days flat that would normally have taken nothing less than 15 days.
CHATBOT is making a telling difference
Accurate progress monitoring is key to efficient project delivery and the typical process involves the Site Engineer updating progress on WhatsApp or some App which the Planning Engineer aggregates to generate the report. “We wanted to leverage the reach and coverage of Apps like WhatsApp and Telegram to bring the entire project monitoring on to an App of choice for easier use and better compliance,” says S Sundarrajan, Digital Officer – MMH, who along with Nikhil Sunil Kunnuthottiyil developed the solution. “Now, at the end of a day, our site engineers open and say “Hi” to our CHATBOT and complete the DPR entry within minutes,” smiles Project Manager, Sivanesan Ramanujan, CDQ, Dolvi. The DPR entered gets aggregated in the database and Daily Progress Reports are generated automatically. “To further improve its functionality, we have now successfully integrated the CHATBOT with WRENCH to avail off its powerful functionalities,” adds an excited Nikhil. Seeing its success, MMH has expanded this feature to all the three CDQ jobs of Dolvi, Birla Copper -Structural Upgradation, SHPS (Solid Pitch Handling System) Vizag and CHP (Coal Handling Plant) Kerandari.
“We wanted to leverage the reach and coverage of Apps like WhatsApp and Telegram to bring the entire project monitoring on to an App of choice for easier use and better compliance.”
S Sundarrajan
Digital Officer – MMH
Along similar lines, a CHATBOT has been designed and deployed across 20 projects in response to a request by the EHS team led by Dr K N Sen, EHS Head – MMH SBG, through which users can make Safety Observations on the go in 30-40 seconds via Telegram or WhatsApp. Till date, roughly 2,300 observations have been noted.
Immediately post the unlock, though sites were hungry for new labour, the process of on-boarding was long-winded, difficult, offline with the added danger of COVID infections. CHATBOT-WISA proved to be the ready answer at Dolvi for five projects – Civil Works SMS II, Supply and Erection work for SMS II, Civil works for BFII, Supply & Erection work for BFII, Construction and Erection of 3 MTPA Coke Oven Plant. In the new feature, the workmen themselves provide all their necessary details on WhatsApp which is aggregated into an Excel file and shared with the Time Office. Using WISA’s bulk upload feature, the file is directly added to the system saving time, increasing the number of workmen onboarded and raising the efficiency of the Time Office personnel. Around 870-odd workmen have provided their information using the CHATBOT much to the delight of the Dolvi IR team of Senthilkumar Mani and Umesh Kumar, who took the lead to drive its implementation.
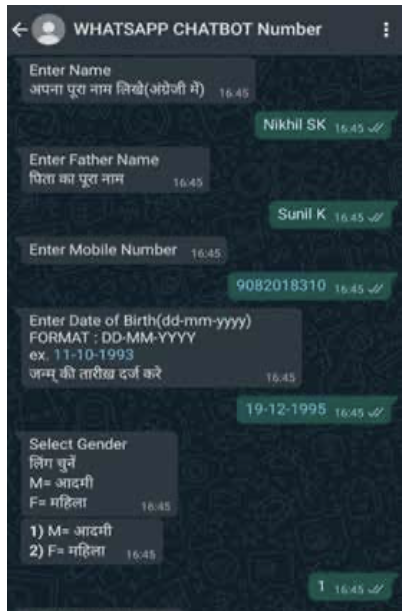
The telling difference that CHATBOT is making
CHATBOT has come in handy even to vaccinate MMH personnel, by digitizing the entire process from data collection to hospital intimation with minimal human intervention. The HR department now gathers, arranges, and shares the data with the respective hospitals daily using a CHATBOT. It is user-friendly, data collection is easier as is sending automatic Emails and can be accessed anytime, anywhere.
PDSS- Android based QR app captures production hours
The Kansbahal Works operates on a three-shift basis and the production hours of 200 direct workmen and approximately 30 machines must be captured by the concerned shop supervisors in PDSS at the end of the shift the same day. For Dalveer Singh Panesar (Head -Machine and Assembly Shop) and P K Sinha (Head – Fabrication Shop), the process was manual, time-consuming, not in real time and prone to human errors. By digitalizing the process, they are breathing a lot easier.
Each part of the BOM is processed through a document called Route Card (RC), available online in PDSS, which has an inbuilt QR code that defines the part. At the start of the shift, the shop supervisor scans the QR codes of all the parts required for that day through an Android scanning device which is, in turn, integrated with PDSS. The user then gets the details of the RC on the 6” in-built screen of the Android device and records the quantity completed, start time and end time as per the requirement of the job progressively. “The data is now in real time, accurate with errors reduced drastically,” smiles a satisfied Sumanta Kumar Mohapatra, Manager IT.
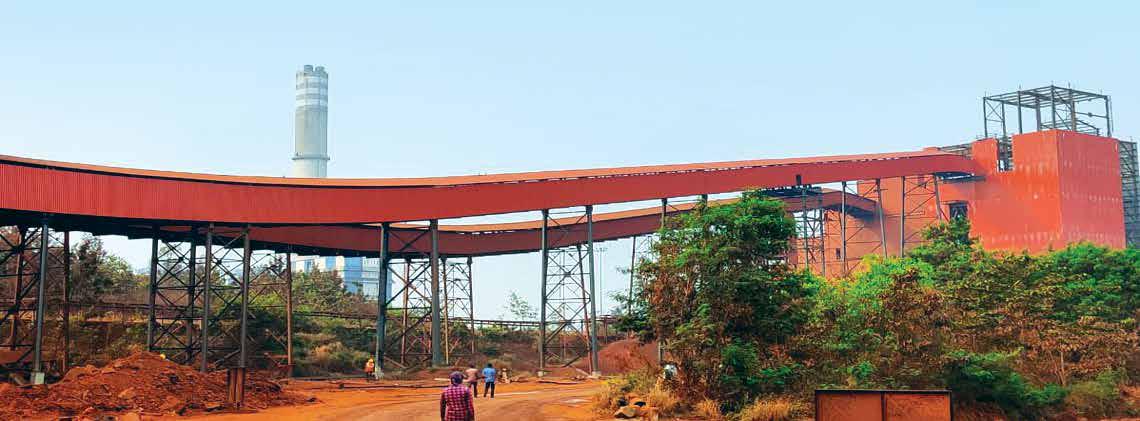
Bauxite Handling Converyor – UTKAL
QR Code based Material Tracking
Material tracking at the Kansbahal Works posed a similar problem with about 15,000+ materials kept at different locations inside the factory under the custody of the Central Stores Department. The materials are issued based on indents given to the Stores department and the Stores personnel locate the materials either based on their experience or by following a manual tagging system. This was an arduous manual process, prone to errors and delays. “We have created an in-house system to generate QR codes against each material code that is printed and pasted on the material,” informs Arun Kumar Mishra, Senior DGM (IT). “It is now easier and faster for both the end users and the Stores personnel to locate and issue the material, it is more accurate and helps users to plan further procurement of the same looking at the physical availability,” informs Srinivasu Malladi (Senior Manager – Manufacturing), who along with Narendra Kumar Tiwari (Manager, Stores), are driving this initiative. Digitalization has again proven to be a winner!
Wrenching out more efficiency
All operating projects of MMH SBG are managed through WRENCH that encompasses scheduling and auto-progress updation with varied monitoring and control reports and contract management through communication and document management. An intelligent cloud-based platform to collaborate, plan, monitor, and control the lifecycle of projects, WRENCH acts as an integrating central platform enabling data-driven process enforcement and real time collaboration between stakeholders.
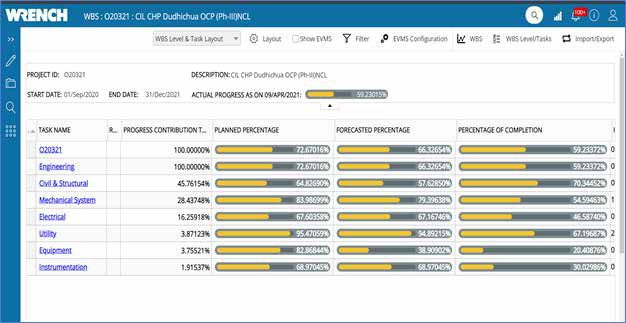
How WRENCH is driving efficiency
With seamless bi-directional integration capabilities with Primavera and MS Project, the entire project schedule can be transferred to WRENCH wherein each individual stakeholder can operate in his/her domain and the progress will be captured automatically and reflected in their respective schedule without manual intervention. The progress of workflow-based activity can be monitored in fine granular level, enabling to do lists for every user and a step-by-step Rule of Credit at each stage. With central data management, the entire data repository is maintained at a single location for easy data access, removal of dependency on dynamic user groups, revision control and tracking for engineering documents and is confidential.
MMH – EDRC has fully enabled and implemented WRENCH for all its EDMS and Engineering Management processes with active involvement of all users. Ms. Subarna Mazumdar is at the forefront of the change management efforts with her team, involved in reconfiguring a new system, training all 350 staff in more than 20 sessions and continuously handholding even during the pandemic disruptions. “I am very happy that all the Engineering Data is available at the click of a button,” exults Subarna, “and deliverables are tracked on a real time basis pushing progress.”
Pushing quick progress
For Project Manager, Prasanta Tikadar at his Utkal Alumina International Limited project site in the remote Rayagada district of Odisha, the challenges to restart operations after the lockdown were several. He was facing a substantial loss of manpower, especially from out of the State, limited railway connectivity, non-availability of local suppliers for materials and spares, lean skill level of local workers and, to add to them all, a prolonged and heavy monsoon. “When we restarted, every employee at site worked like a frontline worker to push progress and despite the challenges we have made good ground,” declares Prasanta and his numbers back his claim. Since the unlock, in Q1 they completed erecting 850 MT of critical & heavy equipment, 1,380 MT of structural erection, 4,500 cum of concreting and all the electrical panels and transformers in all the substations.
“When we restarted, every employee at site worked like a frontline worker to push progress and despite the challenges we have made good ground.”
Prasanta Tikadar
Project Manager, Utkal Alumina International Limited Project
Though the team had initially succeeded to retain 1,500 workmen at site, many left as soon as the restrictions were lifted that forced them to shuffle the remaining skilled workmen and change the crew composition based on discussions with the subcontractors. “To push progress, we gradually shifted from the conventional execution style to focus on automation and digital tools to achieve the desired progress with limited resources,” shares Planning Manager, Sudip Sen. They are planning their piping work using 3D model (Navisworks) software that has made execution easier by addressing the interfaces and identifying the specification lines.
“To push progress, we gradually shifted from the conventional execution style to focus on automation and digital tools to achieve the desired progress with limited resources.”
Sudip Sen
Planning Manager, Utkal Alumina International Limited Project
“We have introduced modular erection specially for heavy & critical structural lifts like tank top structures at heights of 35 m from ground level and conveyors that are saving hugely on labour time with superior quality and safety,” informs C Muthuraj, Construction Manager – Structural. Disciplined stacking of fabricated structural materials, area wise and line wise colour coding of pipes and spools, using orbit pipe cutting & welding machines, automatic plastering machines and space climbers have enormously improved efficiency.
Digitalisation of e7 Sand plants
Digitalization of e7 Sand Plants takes care of collecting, storing, computing and dynamically representing both historical and live data to users. Available on a computer or a mobile device, one can view major operational and technical data collected from the Sand Plants such as feed material quantity, product quantity, production hours, yield, motor winding and bearing temperature, equipment vibration, etc. In addition to the data capture, digitalization helps to take the machine’s PLC control remotely for troubleshooting. After the lockdown, five sand plants have been commissioned remotely.
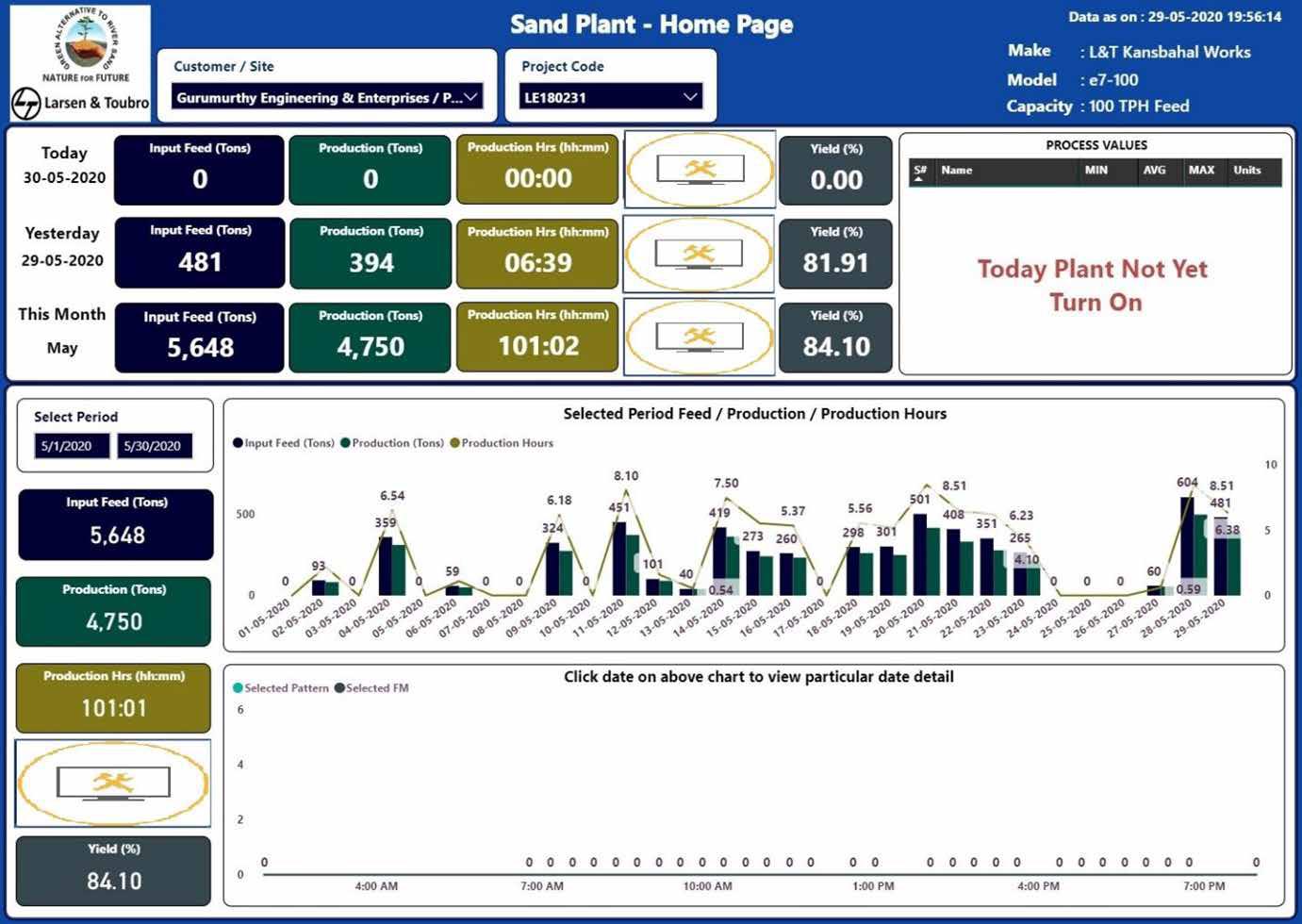
A dashboard showing the digitalization of sand plants
Smruti Ranjan Purusti and Omkar Prasad Patra from the Engineering team of the Product BU who are driving this initiative point out that they can now monitor the operational status of a plant from their office, analyse plant performance, production, faults, and service support. “We can even optimize or improvise future design,” they chorus excitedly.
The challenges remain but MMH project sites have evolved their unique strategies to keep their noses ahead. Here is wishing them the very best!