PT&D IC PROJECTS ARE POWERING
THE PUSH FORWARD
Every project has its share of obstacles, but what characterizes each is the will and grit to make the final push. The PT&D IC projects featured in this story have all showcased their strength and determination to overcome challenges, as they look to make the final push to completion.
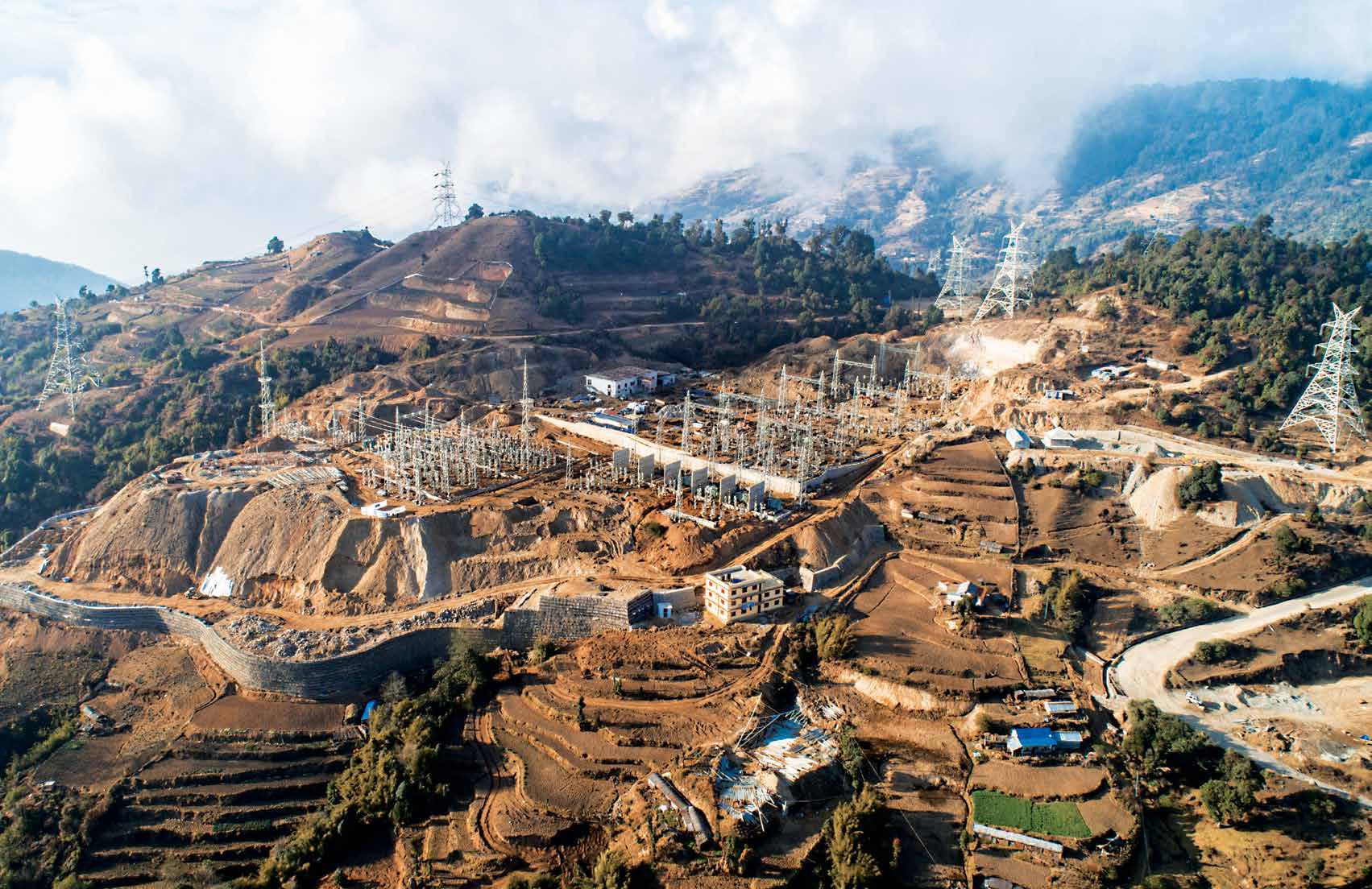
765 kV S/C GHATAMPUR–HAPUR TL
READY FOR CHARGING
Ghatampur–Hapur being one of the longest 765 kV Single Circuit Transmission Lines constructed in India to date, with its 411 km line length and 1,053 locations, the high stakes were evident to Project Manager Raghu Potla from the beginning. “It was a lumpsum turnkey contract with statutory and regulatory approvals under L&T’s scope, including the completion of 63 powerline crossings and the foundation with a unique inclined trapezoidal base,” explains Raghu. Apart from the unexpected outbreak of COVID-19, and the challenge of retaining and deploying manpower, the project faced several other trials. “Obtaining ROW was critical as we were in a region where transmission line works had been held up previously. Payment terms were also stringent.” To add to the problems, the site location was a theftprone area. “Birds had pecked at some of our strung insulators, damaging them,” Raghu adds, with the hint of an
exasperated smile.
“It was a lumpsum turnkey contract with statutory and regulatory approvals under L&T’s scope, including the completion of 63 powerline crossings and the foundation with a unique inclined trapezoidal base. Obtaining ROW was critical as we were in a region where transmission line works had been held up previously. Payment terms were also stringent. ”
Raghu Potla
Project Manager,
765 kV S/C Ghatampur–Hapur TL
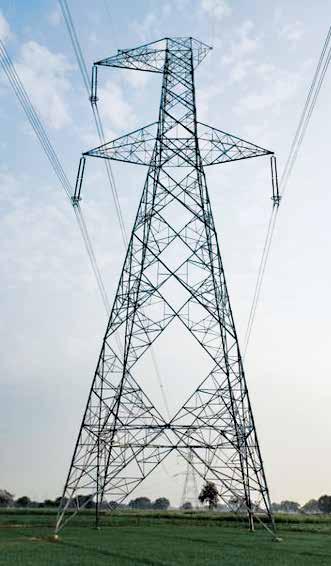
765 kV S/C Transmission Lines, Ghatampur–Hapur
Thanks to systematic and strategized planning, the project team jumped over the hurdles. With consistent followups with the concerned authorities, 135 statutory approvals were obtained within the targeted time. Planning Manager Bezawada Ravi Simon reveals how they tackled the issues: “For the 63 powerline crossings, we adopted the hotline stringing methodology, which significantly reduced execution time, and procured fresh insulators on priority to replace the damaged ones. With a prompt invoicing strategy, we reduced working capital and pursued the client in advance to avoid idling of resources.” There was a huge requirement of materials, which was met through inhouse manufacturing and outsourcing from quality suppliers. The project team had to safeguard uncharged strung conductors from miscreants by posting gunmen at critical locations along with frequent night patrolling.
Being a cross-country job, Quality In-charge Shylesh Hariharan says that using the right people for the right job was the team’s motto. “Frontline supervisors were given frequent training backed with photographic evidence, which helped bring the points across clearly. We even introduced a mobile training van,” he adds. “A one-of-its-kind solution for a cross-country job, this greatly improved job awareness among the workmen.”
For the work required at heights, medical tests were duly conducted beforehand. “We tested the workmen for vertigo to ensure their safety,” says EHS In-charge Manoj Kumar, “and ECGs were made mandatory. For the final sagging, we implemented a Sag Bridge, which greatly reduced the hazard of falling from a height.”
The project implemented the SPEED 2.0 concept, which, explains Digital Officer Rohan Tyagi, “stands for Site Productivity Efficiency & Excellence by Digital, a digital initiative focusing on monitoring & improving key parameters pertaining to workmen productivity.” Drones helped to complete the hotline stringing work where it crossed power lines, railway lines or National Highways. Drones are used to survey the towers too and resolve access-related issues.
Despite the impact of the pandemic, packages were completed within the agreed extended schedule. “We faced numerous challenges during the project lifecycle,” Raghu concludes. “But I am happy to say that we have overcome them through sheer team effort and executed our strategies. The line is now ready for charging!” he declares
with a flourish.
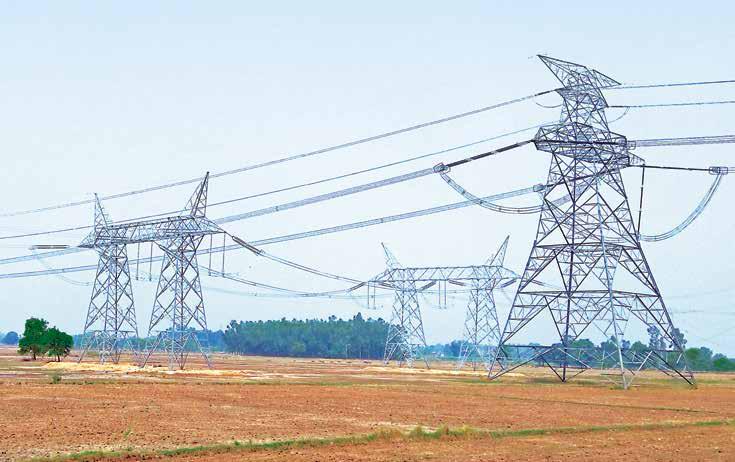
220/66/11 kV KPTCL GIS SUBSTATION
AT HBR LAYOUT
LIMITED IN SPACE BUT NOT IN HEART
A true artist creates a masterpiece regardless of what’s on his/her palette. It is no different with Satyajit Parija, Project Manager for the HBR Layout project. “We had limited space available,” he says, “to accommodate 220 kV and 66 kV GIS buildings, of 13 m and 17 m height, respectively.” The allotted space was pre-occupied with an existing 66 kV tower and a 66 kV terminal bay that were fouling with the proposed 220 kV and 66 kV GIS buildings. “To commence the civil building work, we had to design, supply and modify the existing terminal bay and the diversion of the existing 66 kV OH transmission lines through 66 kV UG cable under line clearance (LC).”
With the site premises in the vicinity of a hospital zone and domestic area, there were time restrictions for work. The UG cabling had to pass through crowded Bengaluru roads, with a substation to be constructed at the heart of the city. “Laying the UG cable amid the dense traffic was tricky,” admits Satyajit, “and roads and bridges were constructed simultaneously by other agencies. The movement of heavy equipment was challenging during the daytime because of the traffic. We had to store bulk materials away from the location due to space constraints. However,” he adds, holding up a finger for emphasis, “we commissioned both the line diversion and the bay modification works in a very short span of 20 days.”
“We had limited space available to accommodate 220 kV and 66 kV GIS buildings, of 13 m and 17 m height, respectively. To commence the civil building work, we had to design, supply and modify the existing terminal bay and the diversion of the existing 66 kV OH transmission lines through 66 kV UG cable under line clearance (LC).”
Satyajit Parija
Project Manager,
220/66/11kV KPTCL GIS Substation
at HBR Layout
Work at the HBR Layout project continued even amid the pandemic lockdowns. “We were going at full pace during both first and second waves as we had obtained special permissions,” reveals Satyajit. Cable supply was completed by the end of FY 2019–20, but the pandemic reared its head just at the time of bill processing. “We followed up vigorously with KPTCL officials and obtained the certification for cable supply of INR 34 crore net value, helping us maintain positive cash flow and less working capital.”
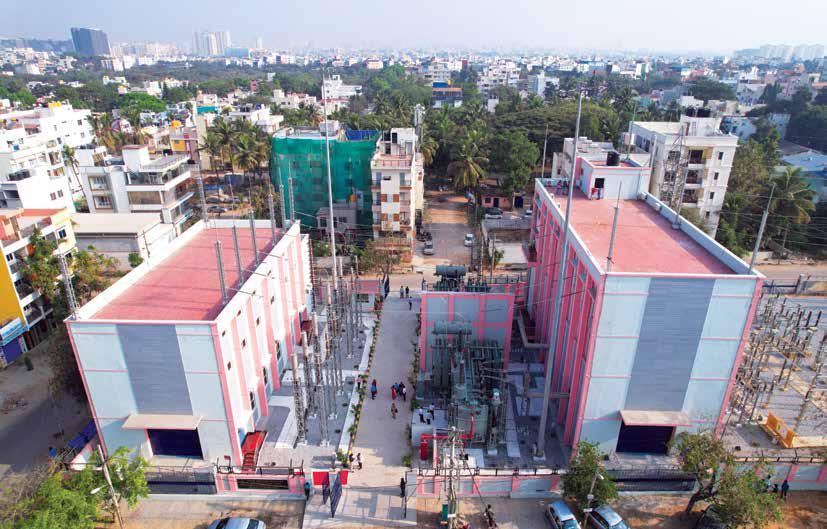
220/66/11 kV KPTCL GIS Substation
Before the substation work could begin, the bus PT bay shifting, 66 kV line bay shifting, and 66 kV transmission line conversion to UG cable had to be completed, for which obtaining LCs was crucial to get the ball rolling. “Bay modification works were not in our original scope of contract,” informs Planning Manager D Saravana Prabhu. “But we planned to complete the design approval, procurement and execution under LC to start civil construction activities. Timely permission obtained from the authorities helped facilitate the cable laying on the planned date.”
The project site was digitally equipped to meet the objectives with WISA, Opticvyu cameras, webcams in public areas with EHV cable jointing to monitor theft, Align for progress monitoring and VR-based safety training for workmen. “All quality compliances were monitored in real time using the L&T QIR App,” says Quality In-charge Rajesh Gupta.
The Hoody–Manyatha line had to be connected through the HBR GIS. “We identified the team who had worked at the Hoody–Manyatha circuit and engaging them helped us to identify the correct circuit and smoothen the completion of LC works,” explains Rajesh.
Installation of the 220 kV GIS (with 5 bays) and 66 kV GIS (with 11 bays) was completed within 3 months. “We have completed HV testing of both stations and confirmed the healthiness of the installation,” informs Satyajit with pride. Kudos to the project team for a commendable completion!
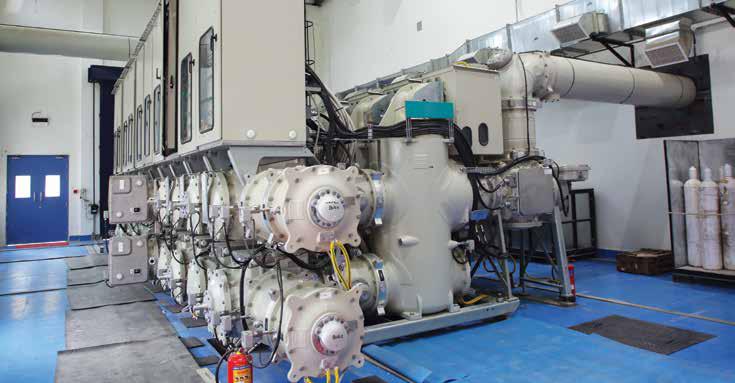
NEPAL KC-2 PROJECT
AN UPHILL CLIMB
For Project Manager Ramakrishnan E, it’s all about making for the final push, as the KC-2 package – Procurement of Plant Design, Supply, Installation, Testing & Commissioning of 220 kV Substations at Inaruwa, Basantapur, Baneswar, and Tumlingtar – nears completion. Three of the four locations are completed, and the fourth, the Basantapur substation, stands at 82% completion, with the civil and electrical works concluded.
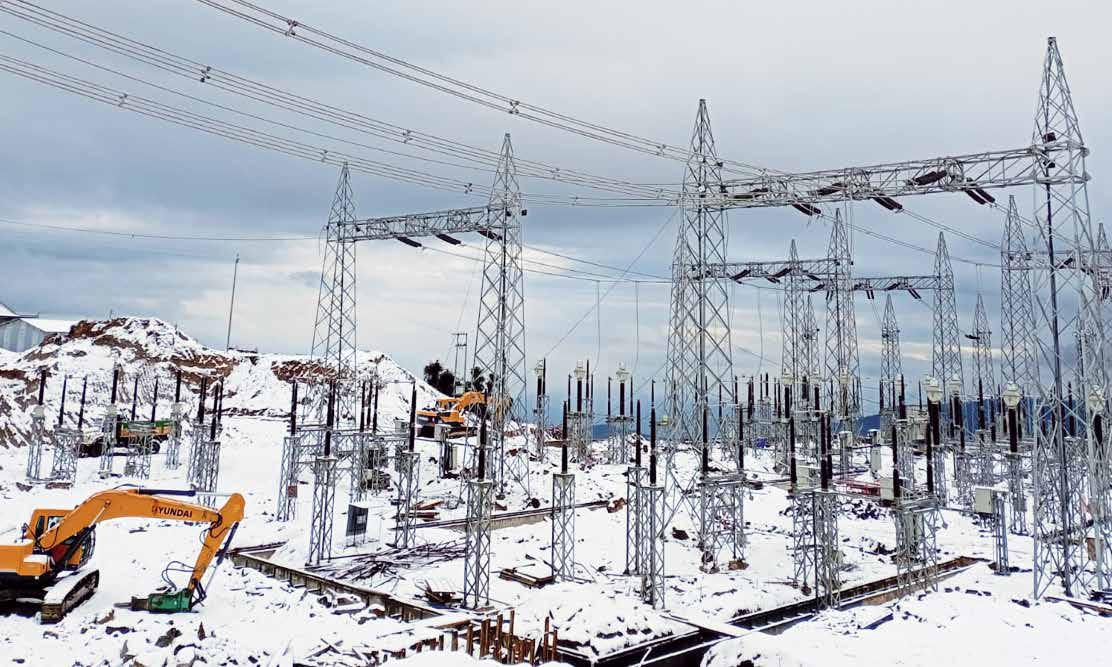
KC-2 Project, Nepal
“At an altitude of +2,480 m from the mean sea level, Basantapur is a particularly challenging area where the maximum temperature roams near 10°C and the minimum dips to as low as −8°C in winters, and located in a region prone to heavy rainfall,” Ramakrishnan states. With the monsoon spread across May– September, the effective working period is practically reduced to about 5–6 months in a year.
“At an altitude of +2,480 m from the mean sea level, Basantapur is a particularly challenging area where the maximum temperature roams near 10°C and the minimum dips to as low as − 8°C in winters, and located in a region prone to heavy rainfall.”
Ramakrishnan E
Project Manager, Nepal KC-2 Project
With such demanding conditions, one can imagine the difficulty in retaining a skilled workforce. “In Nepal, skilled workmen are not available for specific work like stone masonry, gabion, and drain-related works,” Ramakrishnan states. “To maintain quality, we had to mobilize workmen from India, but due to the climatic conditions, they are not willing to stay long at the site. We have, however, worked hard to motivate them, ensuring and fulfilling their basic needs and our efforts have helped maintain the manpower strength.”
The uphill climb did not stop with the weather challenges. Due to poor condition of roads and hilly terrain/slope area, the transportation of supply items and bulk materials was severely affected. “In due course, we identified a specialized logistic agency from India for the transformers while the other equipments were locally procured,” reveals Planning Manager and Digital Officer Rahul Routh. To mitigate the scarcity of bulk materials nearby, the project team set up their own crusher at the site to feed the aggregate requirement of 4,900 cum., thus saving both time and cost.
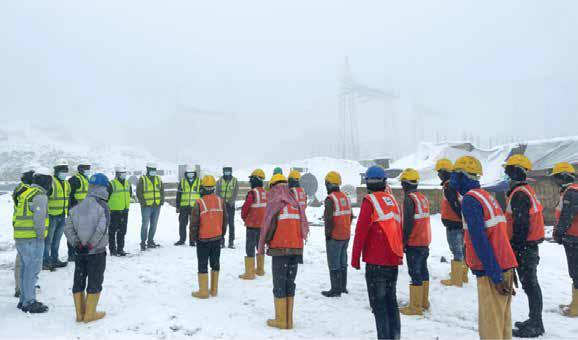
Site grading work at Basantapur involved 7.39L cum. of earthwork, with cutting up to 25 m and filling up to 35 m. “During its execution, we encountered approximately 1L cum. of hard rock,” says Rahul. “Since the Nepal government does not allow blasting, the entire hard rock had to be broken using rock breakers fitted to excavators, a time-consuming activity.”
Digital initiatives at the project have smoothened the push. “The workmen screening and vendor assessment forms are all QR-based,” explains Rahul. “As the online forms can be easily filled from any smartphone, the whole process becomes contactless.” It is commendable that this system was fully developed by the site team without incurring any additional costs.
The KC-2 project is the first in L&T to implement the Mechanically Stabilized Earth (MSE) Wall Technology for the Nepal Electricity Authority. Also called a gabion wall, this US-based technology decreases the usage of stones and aggregates and reduces construction area, time, and cost. “We saved 8 months by using MSE walls and it is ideal for projects where there is a necessity for a soilretaining system, a scarcity of stones, and space constraints, especially for multiple terrace or bench formations,” Rahul explains.
Developing links with local vendors, contractors, and workmen in line with L&T’s standards for safety and quality was crucial. Quality In-charge T S K Viswanath and EHS In-charge Gopinath K wield proud smiles as they list several milestones and achievements of the project. “The client has commended us for our strong EHS performance,” beams Gopinath, “such as achieving 2 million safe manhours with zero LTI and receiving the ‘Distinction’ Award from the British Safety Council, the Special Award for Consistent Performance in FY2021 and the Annual EHS Trophy Award in FY2020 under the SS BU.”
“We have received Appreciation Certificates for Timely Resumption of Works with proper implementation of SOPs and for continuous team work to achieve good product quality throughout the project,” Viswanath remarks proudly. “We also successfully transported 11 transformers from the Indo–Nepal border to respective site locations by making a bypass road arrangement over the Philuwa Khola and Sabha Khola Rivers after obtaining approvals from local authorities and sorting out ROW issues.”
With project completion close at hand, the handover of mandatory spares, bill preparations, and submissions of material reconciliation, as-built drawings, and O&M are some of the activities still on Satyajit’s plate. “We plan to complete the minor works and close the remaining punch-points duly signed by the client. Once we obtain the statutory requirements and clearances from the Government of Nepal, we should be good to go.” Scheduled to be completed by 31 March 2022, we wish the KC-2 project all the best for summiting the peak!
QATAR POWER TRANSMISSION SYSTEM
EXPANSION PHASE-13 – 132/11 kV UMM
BESHER & 132/11 kV WAKRAH-4 SUBSTATIONS
FAST-TRACKING TO THE FINISH LINE ON SCHEDULE
When it comes to sticking to one’s plans, the Umm Besher and Wakrah-4 project has hit the bull’s eye. “As per the planned schedule, the project should be 84% complete at this stage,” says Project Manager Gaurav Gaur. “And we’re right on the money. The agreed date of delivery is 20 March 2022, and we fully expect to meet it.”
A fast-track project linked with the accommodation facilities for the FIFA World Cup 2022 in Qatar, it is being monitored at the highest level by the client, KAHRAMAA. “We have displayed tremendous civil work progress, especially in Q3,” Gaurav comments with a smile. The erection and testing works were fast-tracked, with the component testing of GIS bays started along with the installation works.
“As per the planned schedule, the project should be 84% complete at this stage. And we’re right on the money. The agreed date of delivery is 20 March 2022, and we fully expect to meet it.”
Gaurav Gaur
Project Manager,
Qatar Power Transmission System
Expansion Phase-13
“All civil, erection, and testing works took place in two shifts, and end-user inspections were organized in two stages,” reveals Planning Manager Amandeep Singh, “one for the 11 kV voltage level and another for the 132 kV level. We arranged for early telecom connectivity to complete the 11 kV DCC testing and provided additional SCS workstations to perform activities in parallel.” After discussions with the client, the team agreed to carry out relay final settings along with component testing.
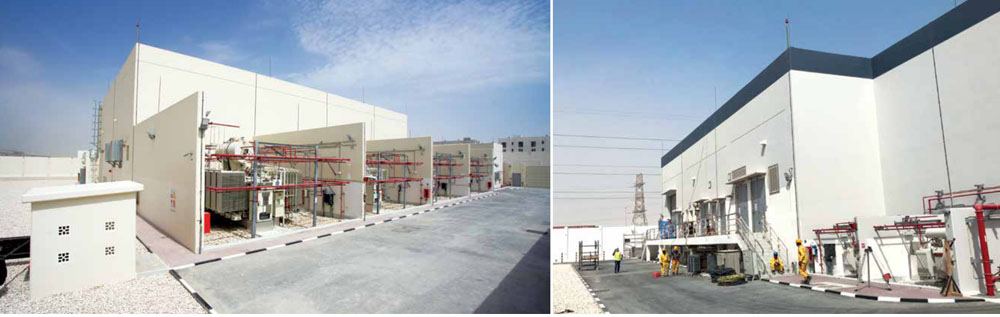
132/11 kV Substation, Umm Besher
132/11 kV Substation, Wakrah-4
Digital initiatives are pushing the project’s progress. “The pandemic has taught us that the ‘new normal’ is the way forward,” remarks Digital Officer Susanta Chattopadhyay. “Initiatives like Align are helping us track real-time progress, and Hilti OnTrack provides information for the required material. With a connected P&M and a GPS-based vehicle tracking system, we have optimized our resources.”
The project faced a delay in procuring the GIS, as the manufacturer had shifted their factory from Germany to Switzerland. Delivery of other major equipment was held up as well due to the pandemic. “However,” emphasizes Quality In-charge Al Jaseem, “we have already made up for the delay in GIS delivery for Umm Besher. The substation will be energized as per schedule. The client had approved to carry out the testing work during the installation phase.” With the fasttracking and crashing approach used for execution and by working in two shifts, the team is on track.
The entire duration of the project has been LTI-free. “Since the project’s inception in January 2021, we have not recorded any lost time injury or first aid case on both sites,” reveals EHS In-charge Proloy Kumar Das. “The challenging fact is that both substations’ overall completion schedule is only 14 months to energization, whereas the normal schedule for KAHRAMAA is between 22 and 24 months.”
All room access work for equipment installation was done within 7 months from the start of the project. “Moreover, we completed the GIS HV test at the Umm Besher substation in 12 months,” says Gaurav proudly. For the Wakrah-4 substation, the team is looking to make up for the delay in the delivery of equipment by continuing to work in two shifts. Coupled with the fast-tracking mode for installation and testing of the GIS, we are sure that the project will reach the finish line in time!
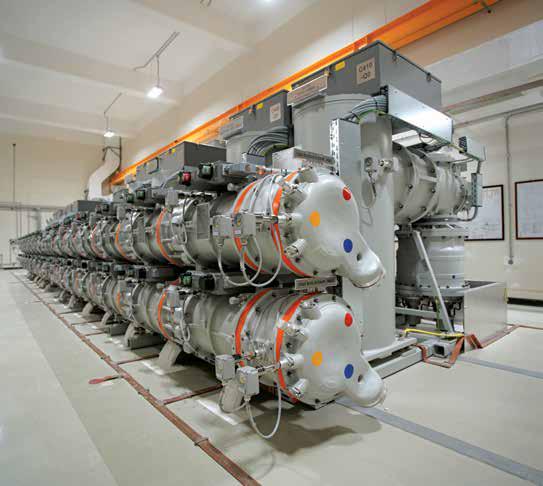
SITC OF BANIYAS SQUARE 132/11 kV SUBSTATION AND ASSOCIATED 132 kV CABLE WORKS AND ALL OTHER ASSOCIATED WORKS
HITTING OBSTACLES OUT OF THE PARK
The team knew the challenges posed by the project right from the time it was awarded, with the scope of demolition of the existing substation and construction of a new substation, along with connecting to the existing network through UG cable. “Proactive risk management was imperative to see the project through to completion,” remarks Project Manager A Sajith with a serious look. “Located in a constrained space within the city, with the metro running nearby, there were uncommon risks to tackle. But we at the project believe in the adage ‘Adversity causes some to break, others to break records’.”
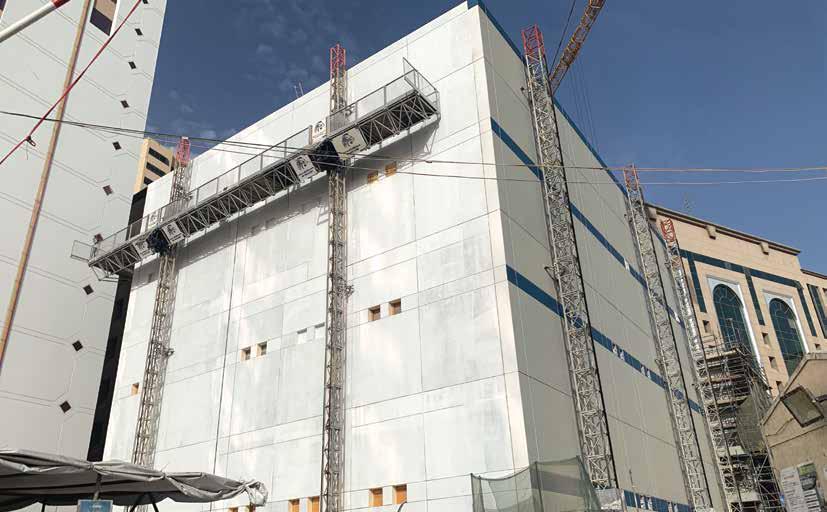
132/11 kV Substation, Baniyas Square
The project plot was in the middle of a commercial-residential complex surrounded by private parking zones and a graveyard. “That accessibility to the plot was constrained would be a gross understatement,” says Sajith in earnest. Further, the plot was just half the size (50×27) of a typical substation plot (50×60). With design and engineering playing a pivotal role in alleviating executional struggles, the project would go on to claim many firsts in the client
(DEWA) network.
“Proactive risk management was imperative to see the project through to completion. Located in a constrained space within the city, with the metro running nearby, there were uncommon risks to tackle. But we at the project believe in the adage ‘Adversity causes some to break, others to break records.”
A Sajith
Project Manager,
SITC of Baniyas Square
The existing substation, located in Deira, Dubai, catered to a highly congested business and residential load, with the remote ends operating at full load. “Load redistribution became complicated,” reveals Planning Manager and Digital Officer P Vadivelu, “eating away 10 months from the awarded contract duration of 36 months, leaving us with just 26 months to execute.”
To accommodate the fire pump room, the transformer design had to be modified. The team approached KONČAR with the proposed solution. “They gracefully accepted,” says Quality In-charge Mohd. Azimali with reassured smile. “With this, we achieved a known Overall Equipment Layout (OEL) and saved almost 4 months of construction time while avoiding deep UG structures.”
Following the OEL approval, the team, armed with a detailed execution study, conveyed to the client the constraints of casting in-situ. They fervently demonstrated that with the available plot access, scaffolding and material logistics would be impossible. “The clearance with the neighbouring complex was at a dangerous minimum and concreting would have risked property damage,” Safety In-charge Gokul Unnithan remarks with a serious look. After several rounds of deliberation, the design was cleared by the client. “The idea of precast panels was appealing at several levels as it reduced execution risks and improved timelines by 6 months, against 10 months for the average cast in-situ structure,” elaborates Gokul. As it averted the need for block walls, electrical access was available two months in advance, helping crunch the electrical schedule from 8 months to a mere 4 months.
While the prefinished panels brought the advantage of moving directly to the painting phase, they required highercapacity cranes for installation. “The space constraints meant that only a tower crane would provide complete access to the plot,” explains Vadivelu. “We sourced a special high-capacity tower crane with a monumental height of 70 m to clear the surrounding buildings.”
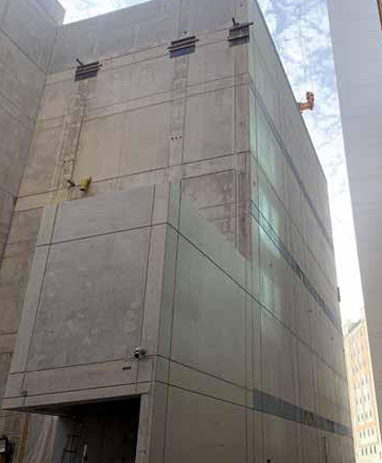
All challenges were met with creative solutions from the project team, such as using an acoustic layer during demolition to keep the residents free from disturbance, introducing a nonvibro method for stone columns to limit drilling vibrations, and more. The plot had to be dewatered, for which a sensor-and-alarm technology ensured water-level monitoring. “BIM played a huge role for clash analysis,” reveals Gokul, “and we adopted stage-wise execution planning to minimize risks.”
Currently in the electrical installation/ testing phase, with the High Voltage test for the 132 kV GIS and 11 kV AIS completed, the team is gearing up for protection testing and remote end modifications. Despite a 10-month delay in plot handover, the project looks well set to commission in a jawdropping 11-month period from raft casting, 6 months in advance of the contractual completion.
OH–UG CABLING WORK, PHASE-III,
E9 SUB-DIVISION, SHIVAJINAGAR DIVISION,
BESCOM, BANGALORE
PRIMED TO FACE CHALLENGES FROM THE START
With the project awarded during the peak of the pandemic, the starting line might not have been the most ideal for the Shivajinagar project. However, the project team did not let the lockdown periods go idly. “Even as the first wave was progressing, we were obtaining drawing approvals,” explains Project Manager Anand M R. “50% of material requirement as per the survey quantity was also ordered during this period.” Staff mobilization began in June 2020, with survey work immediately following, as it did not require any subcontractor deployment. “Within 3 months, the client approved the survey of routes, and we were ready for execution once the government relaxed the lockdown.”
“400 km of cable survey was done in 2 months with just six staff members. Work order and BBMP approvals were taken within 1 month, in one go, for all 20 feeders. 100 km of HDD work was completed within 2 months from the start of execution, and this average of 50 km/month is the highest in the Bengaluru region.”
Anand M R
Project Manager,
OH–UG Cabling Work, BESCOM,
Bangalore
With support from the client, BESCOM, the project team ensured that neither did their UG cabling interfere with the existing utilities nor were the lines damaged in any way. “We formed a group with all the agencies involved (GAIL, BWSSB, BSNL, and KPTCL) and conducted physical surveys with our subcontractors,” informs Planning Manager Amir Hussain. The team also procured the utility tracker ‘Pathfinder’ to identify the existing lines, resulting in early completion and minimum rework.
Before work had begun, the team identified subcontractors and proceeded with their rate approval during the lockdown. “We deployed local subcontractors, clearing ROW issues quicker,” Amir says. “By keeping the number of subcontractors to a minimum, with more manpower under each, we avoided idling of workmen and the reconciliation and billing process became easy.” The store yard and guest house were finalized in two months’ time, while section-wise completion of feeders was planned during execution. This helped the project achieve higher productivity.
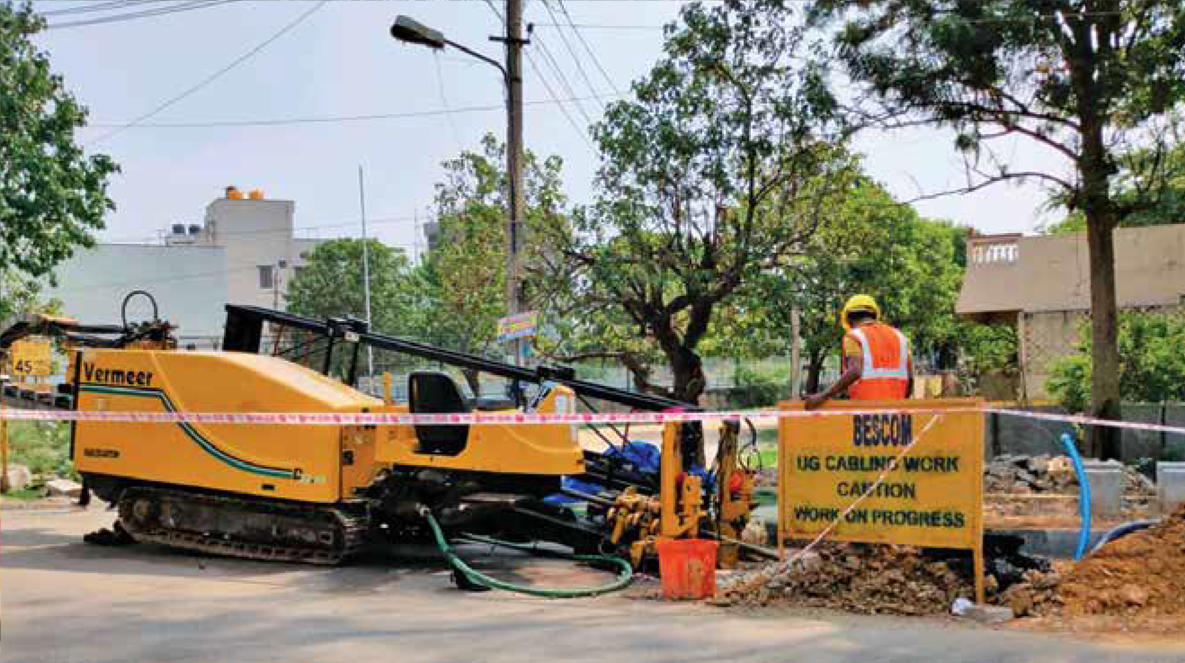
UG cabling work, Bescom
On the digital front, the project has implemented Em-Power to save time in the issuance of material. BODHI tools are used to track progress biweekly to identify and mitigate any delays on time. “Regular monitoring through the QIR app resulted in minimum reworks at site,” conveys Quality In-charge Bala Brahmam. “Any new subcontractors deployed at the site were asked to execute a sample to ensure quality, which helped avoid repeated mistakes.”
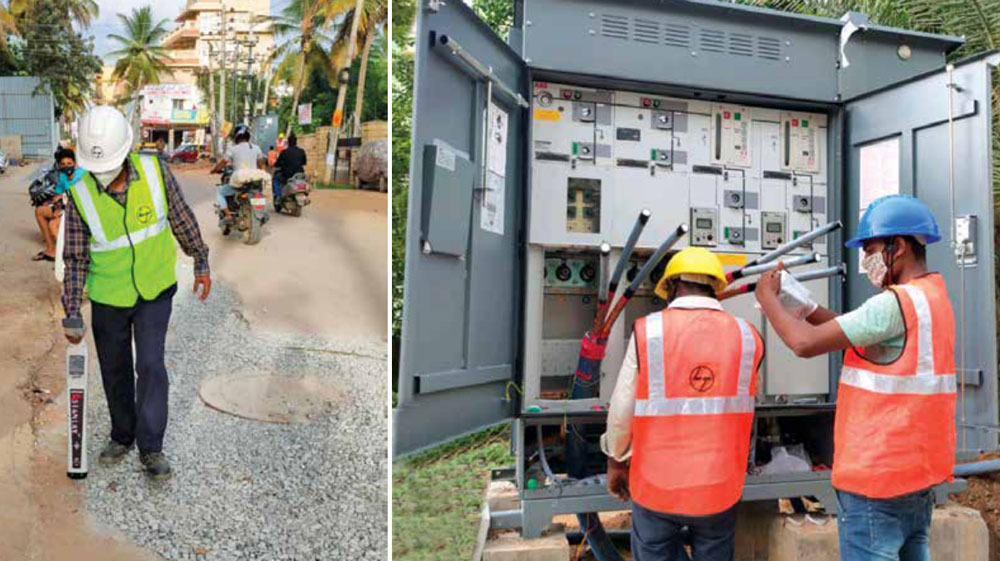
UG Utility Sensors
Cable Termination
Regular visits to the site by EHS In-charge Anand Raj along with the Project Manager and Section In-charge helped ensure no lapses in safety. “With the Shield app’s regular monitoring, we ensured nil accidents,” says Anand. “Regular training programmes were conducted for the subcontractors’ workmen, with ‘Best Workman’ rewards to motivate others to follow.”
The project has achieved some significant milestones along the way. “400 km of cable survey was done in 2 months with just six staff members,” Anand elaborates, checking off their achievements one by one. “Work order and BBMP approvals were taken within 1 month, in one go, for all 20 feeders. 100 km of HDD work was completed within 2 months from the start of execution, and this average of 50 km/month is the highest in the Bengaluru region. 1,500 sets of GOS were executed during peak months of work, involving purely shutdown activities. With timely invoicing and collection, the project is operating with a negative working capital,” he signs off proudly.
The project is 75% complete, with 12 of the 20 feeders done. By assigning site engineers as one point of contact for each O&M section, the team is focusing on handing over the commissioned feeders through continuous follow-ups with the customer.
GURUGRAM UG CABLING/11 kV UPGRADATION
PACKAGE – DHBVN-HARYANA
METHODICALLY PUSHING AHEAD
“The motto ‘Be enthusiastic, be positive’ is infectious,” comments Project Manager Praveen Kumar K V. “We at the project look to motivate our team members by empowering them with sufficient decision-making authority to achieve objectives and goals, while following proper execution methods.” With roles and responsibilities clearly defined, the project is about two-thirds of the way through, scheduled to be completed by the end of June 2022.
“We plan to collaborate with the DHBVN smart grid’s operation teams and statutory bodies. To meet the scheduled target, we are continuously augmenting the P&M and manpower, with an average of 300+ workmen at the site. Day and night work permits are being arranged, and cable laying and major equipment erection will be done using mechanised methods.”
Praveen Kumar K V
Project Manager,
Gurugram UG Cabling, DHBVN-Haryana
The project team’s strategy involved whole-to-part and part-to-whole based renovation/modernisation of the OH line to UG cable (smart grid). They have a dedicated in-house team for load flow study, network design changes if any, supervision, and testing & commissioning. “For interrupted supply, major equipment orders for RMUs, cables, feeder panels, DTs, etc. were finalized post bid. To save cost and time, we have set up a pre-cast foundation yard instead of cast in-situ,” Planning Manager Ranjit Sen explains. “To keep activities free from physical contact as much as possible, virtual factory inspections are conducted remotely and the Em-Power app is used for material indenting, authorization, and updating DC generation and consumption.”
With the National Green Tribunal ban in place, the team took careful steps in making sure not to harm nature. “We have executed the project with the necessary precautions as a part of the Go Green initiative to protect the surrounding environment,” says EHS In-charge Partho Kumar Poddar. “We also obtained the client’s permission to shift major equipment at night.”
Speaking of permissions, ROW was obtained in time from the statutory bodies (GMDA, GTPL, NHAI and MCG) with continuous follow-ups. “Further, the crossing of 48 feeders involved collaboration with the GAIL authority, as there were Gurgaon city’s gas and water supply pipelines,” Ranjit explains. “At a depth of 6 m and below from the natural ground level, we executed the crossings within the targeted schedule.”
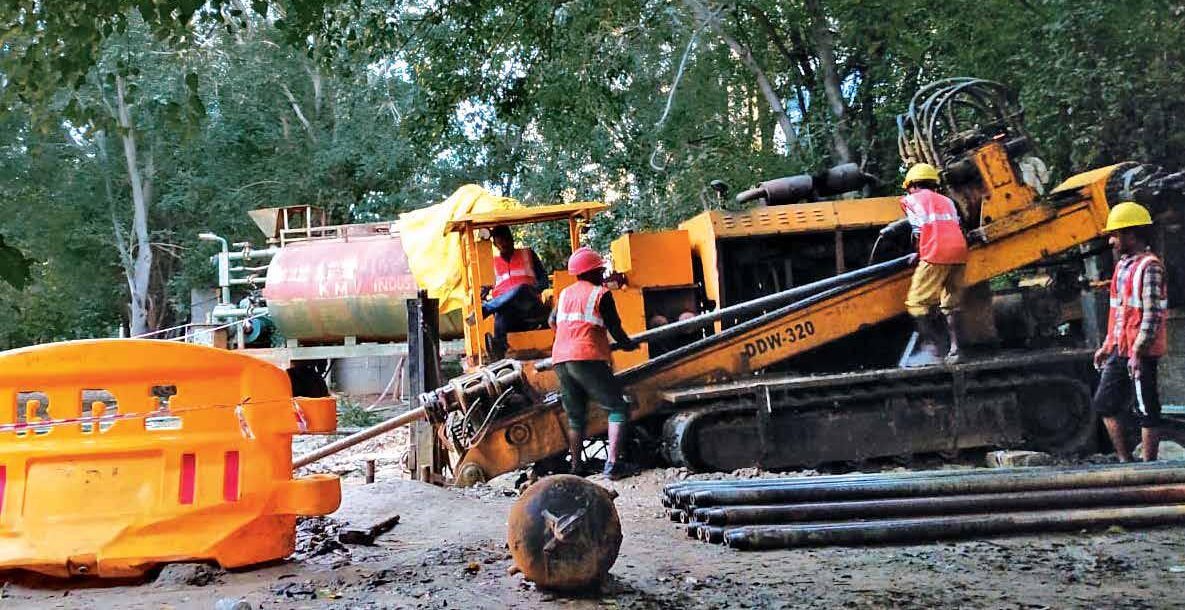
UG cabling work, Gurugram
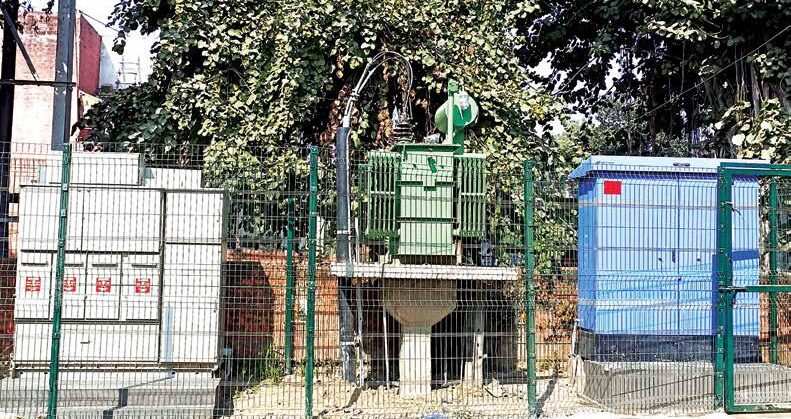
RMU work
All staff, supervisors, electricians, and linemen receive continuous training, informs Quality In-charge Brijmohan Sharma. “We have implemented digital solutions such as the QIR, Shield, and Live Location apps, CCTV towers, GPS tracking, GPR Survey, EmPower, BODHI, ERM, WISA, biometric attendance, and more,” he says. These solutions, along with specific checklists maintained based on the type and category of activity, have gone a long way in ensuring quality at the site.
Receiving the Digital Award in 2020 and the Special Merit Award 2021 under the EHS category are some of the project team’s milestone achievements. With the final third of the project still on hand, Praveen and team’s focus is on the feeder commissioning. “We plan to collaborate with the DHBVN smart grid’s operation teams and statutory bodies. To meet the scheduled target, we are continuously augmenting the P&M and manpower, with an average of 300+ workmen at the site. Day and night work permits are being arranged, and cable laying and major equipment erection will be done using mechanised methods,” signs off Praveen with a thumbs-up.